Selbstlernende Industrieanlage optimiert Prozesse
Industrieanlagen sind heute bereits so komplex, dass diese kaum von einzelnen Menschen überwacht werden können. Die mehrfach voneinander abhängigen Verfahren und Prozesse in einer solchen Anlage werden auch in Zukunft eher komplexer als simpler. Forschern der Technischen Universität Wien und am AIT im Center for Energy ist es nun gelungen, Modelle zu entwickeln, mit denen sich diese Anlagen in Zukunft selbst überwachen und Fehler identifizieren können. Das könnte den Markt revolutionieren und für technische Innovationen und vor allem Optimierungen in Fabriken sorgen.
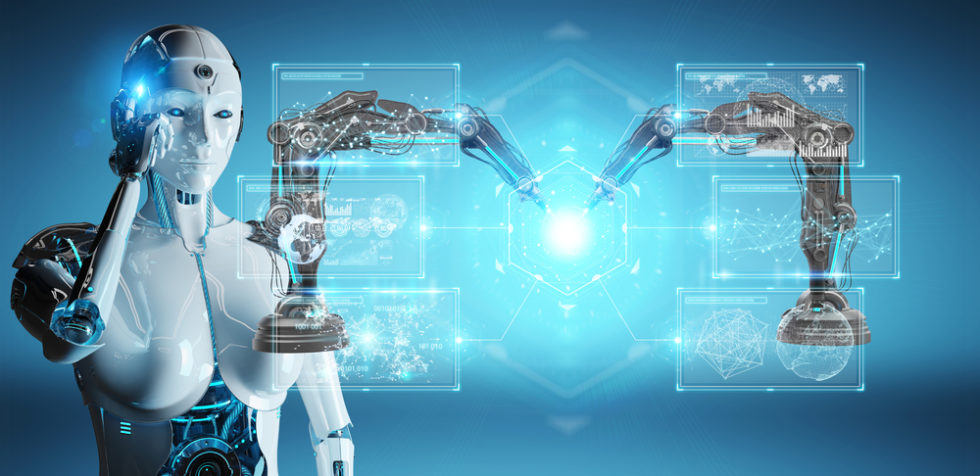
Foto: panthermedia.net/sdecoret
Erstes Ziel der Forscher: Die Effizienz von Industrieanlagen optimieren
Eines der wichtigsten Ziele in der heutigen Zeit für die Industrie ist die Einsparung von Energie und CO2 und die Nutzung der möglichen Synergieeffekte bei den verschiedenen Produktionsschritten. Und genau in diesen Bereichen können in Zukunft dank der Forschung deutliche Fortschritte möglich werden. Denn die industrielle Energieprozesstechnik ist so komplex geworden, dass ohne mathematische Modelle bereits jetzt kein Überblick mehr möglich wäre. Das Problem liegt dabei vor allem an den vielen Variablen. Wenn beispielsweise verschiedene Methoden zur Energiegewinnung zur Verfügung stehen, muss die Anlage immer unter optimalen Bedingungen betrieben werden. Dieses Optimum zu entwickeln, stellt die Forscher vor ein enormes Problem, da es manuell nicht möglich ist, die vielen unterschiedlichen Variablen effektiv zu berechnen. Daher gibt es verschiedene Ansätze, um dieses Problem zu lösen.
KI und maschinelles Lernen als Lösungsansatz
Eine Form der künstlichen Intelligenz wird bereits jetzt von einigen Forschern eingesetzt und überzeugt durch erste, sehr gute Ergebnisse. Auf der Basis neuronaler Netze haben die Forscher beispielsweise ein Modell eines thermischen Energiespeichers simulieren lassen. Dabei handelt es sich um einen Energiespeicher, welcher die thermische Energie von heißem Gas auf festes Material und zurück überträgt. Ein enorm komplexes Verfahren. Für die physikalische Simulation des Verfahrens wäre viel Zeit und ein erheblicher Rechenaufwand notwendig gewesen. Die künstliche Intelligenz hingegen konnte mit erheblich geringerem Aufwand vorhersagen, wie sich das System verhalten würde. Die Forscher gehen aktuell davon aus, dass genau diese Leistungen in den kommenden Jahren enorme Auswirkungen auf die Industrie haben werden, da sich immer mehr Betriebe durch die fortschreitende Digitalisierung mit diesen Themen beschäftigen. Es wird in Zukunft somit möglich sein, dass sich industrielle Anlagen nicht nur kompakter, sparsamer und leistungsfähiger aufbauen lassen, sondern dass diese sich auch selbst überwachen und Fehler direkt identifizieren. Der für diesen Prozess wichtige Begriff lautet „Digitaler Zwilling“.
Was ist ein „Digitaler Zwilling“ überhaupt?
Digitale Zwillinge können in verschiedenen Varianten und Größenordnungen genutzt werden. Es handelt sich um ein digitales Computermodell, welches einzelne Prozesse, Prozessabschnitte oder auch ganze Industrieanlagen simulieren kann. Dabei wird das Modell durch Echtzeitdaten versorgt. Dies erlaubt es dem Nutzer, durch die Berechnung verschiedener möglichen Veränderungen, einen Blick auf die mögliche Zukunft der Anlage zu werfen. Zudem können die vorhandenen Messdaten evaluiert und angepasst werden. Ein solches System bleibt aufgrund der Verbindung mit den Echtzeit-Messdaten immer exakt an die Anlage gekoppelt.
Welche digitalen Zwillinge die Industrie 4.0 noch vorantreiben, lesen Sie hier.
Vorteile digitaler Zwillinge im Detail
Ein Vorteil zeigt sich beispielsweise bei der Planung neuer Anlagen oder bei der Optimierung bestehender Industrieanlagen. Denn ein digitaler Zwilling der gesamten Anlage erlaubt es den Planern, zu simulieren, welche Lösung das effizienteste und beste Resultat bietet und somit planerische Entscheidungen auf Basis von Fakten zu evaluieren. Das senkt in vielen Bereichen nicht nur die Baukosten der Anlage, sondern vor allem deren Betriebskosten und sorgt für eine höchstmögliche Effizienz im Betrieb.
Wie kann eine Anlage nun die eigenen Fehler finden?
Auch hier spielt der digitale Zwilling eine wichtige Rolle. Denn ein digitaler Zwilling der Anlage kann auch als direkter Abgleich gelten. Da die Anlage ihn mit Echtzeitdaten versorgt, kann der digitale Zwilling sofort bemerken, wenn die Daten zu stark von den erwarteten Daten der Simulation abweichen. In einem solchen Fall kann der digitale Zwilling anhand der unterschiedlichen Abweichungen und Parameter genau bestimmen, welcher Fehler vorliegt. Ein Schaden an einer Dämmung kann einen anderen Effekt auslösen als ein offenes Ventil. Durch Simulation können all diesen Problemen unterschiedliche Parameter zugewiesen werden. Es fällt der Anlage also leicht die abweichenden physikalischen Werte zu vergleichen und einen präzisen Fehlerbericht auszugeben. Das kürzt nicht nur die Fehlersuche deutlich ab, sondern erlaubt auch frühzeitige Reparaturen, da bereits kleine Fehler frühzeitig bemerkt werden können.
Die digitalisierte Industrie bleibt spannend
Insgesamt muss man sagen, dass die aktuelle Forschung gerade erst einmal die Grundlagen entwickelt und die einzelnen Modelle und Möglichkeiten aktuell verfeinert. Es ist aber abzusehen, dass viele dieser Forschungen von der Industrie weiter adaptiert werden und in Zukunft viele industrielle Anlagen weit stärker durch Simulationen und KI ergänzt sein werden, als es heute bereits der Fall ist.
Lesen Sie auch:
Ein Beitrag von: