Neues Verfahren im Feinschliff halbiert Energieverbrauch
Statt großer Mengen an Kühlmittel verbraucht ein neues Feinschliffverfahren im Maschinenbau genau dosierten Schmierstoff. Im VW-Motorenwerk in Salzgitter ist diese Minimalmengenschmierung jetzt erstmals erfolgreich erprobt worden. Fast 300.000 Euro an Stromkosten lassen sich damit jährlich einsparen.
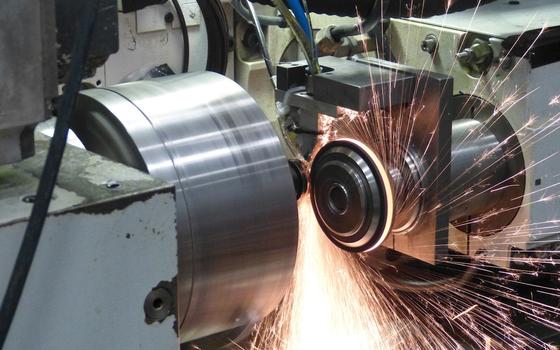
Forscher polieren Nockenwellen mit nur einem Bruchteil der üblichen Kühl- und Schmierstoffmenge und erzielen 50 Prozent Energieeinsparung.
Foto: Volkswagen AG
Zwei Millionen Dieselnockenwellen aus induktionsgehärtetem Chromstahl stellt die Volkswagen AG im Werk Salzgitter pro Jahr her. Höchste Präzision ist dabei gefragt, besonders bei der Feinbearbeitung der Werkstücke. Bei der bisher verwendeten Überflutungskühlung und –schmierung ist der Aufwand jedoch erheblich. Zwischen 5.000 und 7.000 Liter Kühlmittel werden pro Stunde im Umlauf benötigt. Die Energie, die man allein für das Zuführen, Aufbereiten und Kühlen der Schmierstoffe braucht, kann bis zu 80 Prozent des Gesamtbedarfs ausmachen.
Extrem hohe Reibungswärme beim Schleifvorgang war bisher ein Problem
Nun hat ein Forscherteam die Schleifmaschine, den Schleifkörper und die Schmierstoffzufuhr derart optimiert, dass der Stromverbrauch bei der Produktion um bis zu 50 Prozent gesenkt wird. Wenn man pro Nockenwelle einen durchschnittlichen Verbrauch von 2,4 Kilowattstunden für die Ver- und Entsorgung von Kühlschmiermitteln ansetzt, könnte das eine Energieeinsparung von 2,4 Millionen Kilowattstunden pro Jahr ergeben. Das, so rechnen die Ingenieure vor, bedeute eine Einsparung von fast 300.000 Euro.
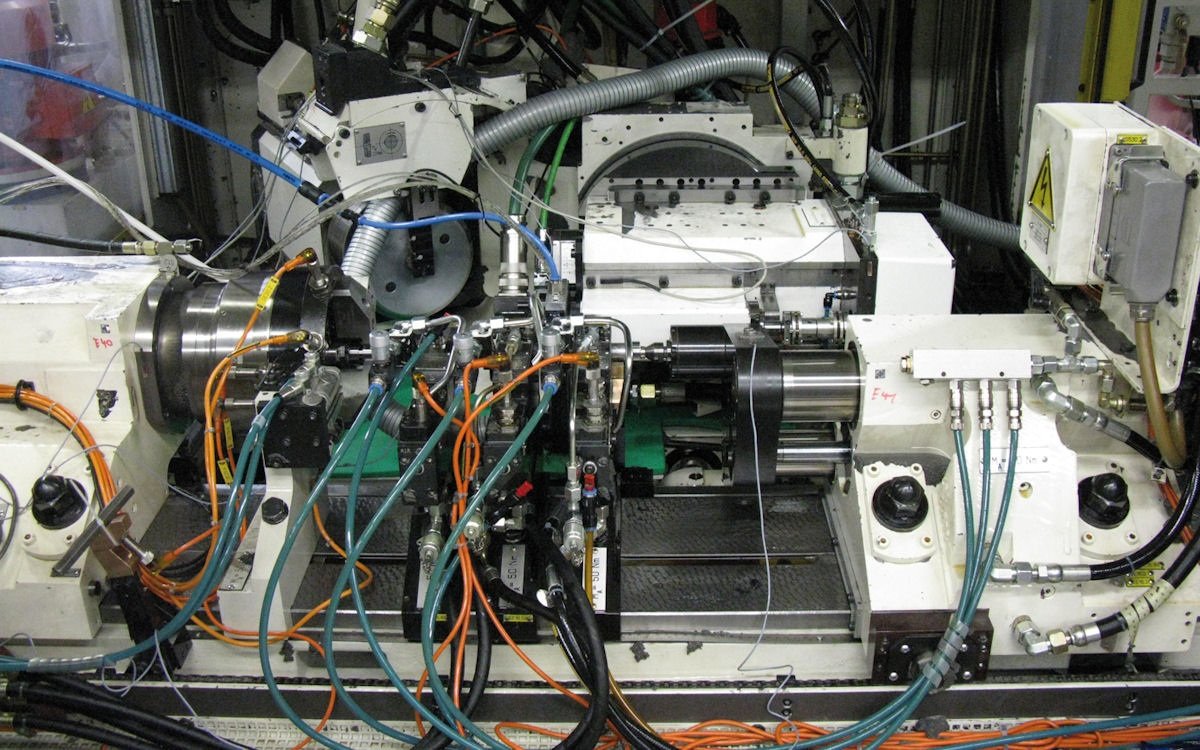
Versuchsaufbau: Schleifen mit Minimalmengenschmierung.
Quelle: Volkswagen AG
Die Minimalmengenschmierung ist nicht neu. Sie wird bereits jetzt schon beim Bohren und Fräsen verwendet. In Schleifprozessen war dies bislang noch nicht möglich, weil hier durch die Schleifkörner enorm viel Reibungswärme entsteht. Diese Wärme, die das abgetragene Metall zum Schmelzen bringen kann, muss sicher abgeführt werden, damit es nicht zu Überhitzungen kommt. Deshalb kam beim Schleifen bisher nur die Überflutungskühlung zum Einsatz, weil hier mehr als die Hälfte der Wärme durch das Kühlmittel aufgenommen wird.
Damit man nun auch bei Schleifprozessen die Menge des Kühlschmiermittels auf wenige Milliliter pro Stunde reduzieren kann, mussten die Forscher die Reibungswärme stark reduzieren, den Funkenflug in der Maschine verhindern und sicherstellen, dass die Späne vollständig abgesaugt werden.
Fokus der Kostenreduzierung liegt auf den Energiekosten
Als Schleifmittel verwendeten die Forscher Bornitrid (CBN), das keramisch im Schleifbelag gebunden ist. Bei der Oberflächenstruktur fand man heraus, dass Poren im Belag einerseits das Kühlmittel besser befördern und andererseits die Späne besser abtransportiert werden. Mit einer gelaserten Lochstruktur erhielt man die gewünschte Oberfläche. Außerdem wurde der Schmierstoff über ein Zweikanal-Düsensystem dosiert zugeführt. Dies ermöglicht ein optimales Mischungsverhältnis von Druckluft und Schmierstoff.
Nach ausgiebigen Tests an Werkstück-Dummys rüsteten die Forscher eine serienmäßige Nockenschleifmaschine nach dem neuen Verfahren um und installierten eine umfangreiche Messtechnik sowie eine Hochgeschwindigkeitskamera. Mithilfe der gelieferten Prozessdaten wie Temperatur, Wirkleistung der Spindel oder Bilder von den Strömungsverhältnissen im Bereich des Düsenkopfes wurde der Schleifvorgang genauestens analysiert. Danach wurde das Werkstück auf mögliche thermische Schädigungen untersucht. Derzeit gilt es, die Langzeittauglichkeit des neuen Verfahrens nachzuweisen.
In den letzten Jahren hat sich VW wie auch in anderen industriellen Fertigungsbereichen der Fokus der Kostenreduzierung von den Werkzeug- auf die Energiekosten verschoben. In Deutschland benötigt die Industrie etwa 25 Prozent des gesamten Endenergieverbrauches. Die in den letzten Jahren stark gestiegenen Energiepreise haben zu einer deutlich wahrnehmbaren Kopplung der Produktionskosten und der CO2-Emissionen geführt. Bei Volkswagen Salzgitter überstiegen beispielsweise im Jahr 2006 die Aufwendungen für die elektrische Energie bei Zerspanungsprozessen erstmals die Aufwendungen für die Werkzeuge. Dieser Trend setzt sich bis heute fort.
Ein Beitrag von: