Mit neuem Verfahren Batterien effizienter recyceln
Die steigende Zahl von Elektroautos auf deutschen Straßen lässt den Bedarf an Lithium-Ionen-Batterien wachsen. Doch ihre Herstellung erfordert den Abbau seltener Rohstoffe und den Einsatz von viel Energie. Umso wichtiger wird die Wiederverwertung von Batterien. Mit einem neuen Verfahren sollen sich diese schon bald deutlich effizienter recyceln lassen.
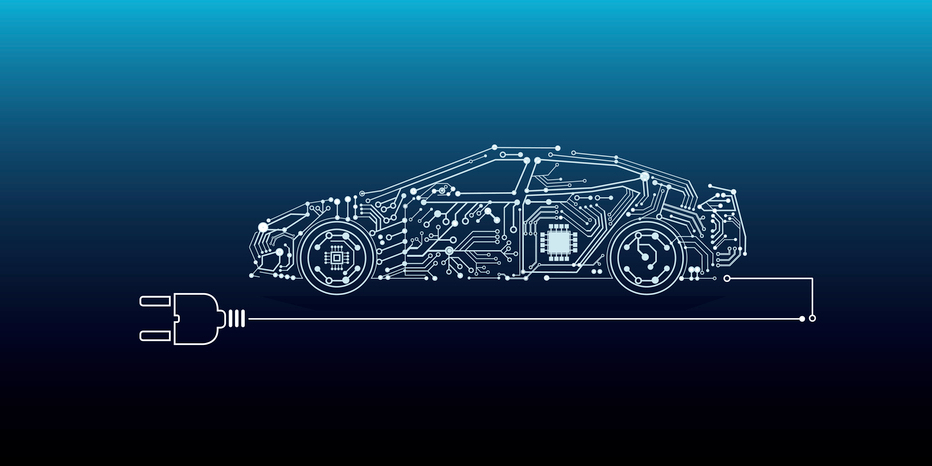
Das Recycling von Lithium-Ionen-Batterien nimmt eine wichtige Rolle für einen nachhaltigen Produktionskreislauf in der Elektromobilität ein.
Foto: PantherMedia / kaptn
Bis 2030 sollen die Treibhausgasemissionen gegenüber 1990 um mindestens 65 Prozent verringert werden. Bis 2040 sollen es 88 Prozent sein und bis zum Jahr 2045 soll Deutschland schließlich die Treibhausneutralität erreicht haben. Für das Gelingen dieser Klimaschutzziele spielt der Ausbau der Elektromobilität eine entscheidende Rolle. Schließlich ist der Verkehrssektor, einschließlich des Straßen-, Schiffs-, und Flugverkehrs einer der größten Verursacher der schädlichen Treibhausgase in Deutschland. Mit dem Umstieg auf Elektromobilität wächst auch der weltweite Bedarf an Lithium-Ionen-Batterien. Diese sind aufgrund ihrer hohen Energiedichte und ihrer geringen Selbstentladung ein wichtiger Baustein für die Ausweitung der Elektromobilität. Doch die Herstellung von Lithium-Ionen-Batterien erfordert den Abbau wertvoller Rohstoffe wie Lithium, Kobalt, Nickel, Mangan und Graphit. Für einzelne Rohstoffe sind in Zukunft temporäre Verknappungen oder Lieferengpässe sowie Preissteigerungen nicht auszuschließen. Zudem kommt es in vielen Abbaugebieten immer häufiger zu sozialen Konflikten. Ebenso zieht der Abbau einiger Rohstoffe negative Umweltauswirkungen nach sich.
Das Recycling von Lithium-Ionen-Batterien spielt daher in Zukunft eine wichtige Rolle. Dieses ermöglicht die Wiederverwendung von bereits vorhandenen Materialien, was Energie und Ressourcen spart. Jedoch sind die meisten Verfahren kompliziert und gelingen oft nur mit dem Einsatz giftiger Chemikalien und viel Energie. Aus diesem Grund entwickeln Forschende des Karlsruher Instituts für Technologie (KIT) und Partner aus verschiedenen Industrieunternehmen in einem groß angelegten Verbundprojekt eine vollständige Prozesskette, um gebrauchte Batterien effizienter zu verwerten und damit die Umwelt zu schonen.
Löst diese kobaltfreie Batterie einige dringende Probleme?
Bisherige Recyclingverfahren von Batterien sind energieintensiv
„Der hohe Bedarf an Lithium-Ionen-Batterien erfordert nachhaltige und geschlossene Materialkreisläufe – von den Batteriematerialien über den gesamten Lebenszyklus bis zum Recycling – sowie eine kreislauffähige Produktion von Batteriezellen“, sagt Marco Gleiß vom Institut für Mechanische Verfahrenstechnik und Mechanik KIT.
Aktuelle Recycling-Verfahren zerkleinern die Batteriezellen und lösen die Aktivmaterialien bis auf die Molekülebene auf. Auf diese Weise können zwar bis zu 90 Prozent der seltenen Materialien wie Nickel, Kobalt oder Mangan wiedergewonnen werden, doch haben diese Verfahren auch Nachteile. Sie benötigen meist Chemikalien und viel Energie. Zusätzlich muss das Batteriematerial komplett neu hergestellt werden. Das erfordert erneut einen hohen Energie- und Rohstoffbedarf.
Neuer Ansatz: Direktes Recyceln von Aktivmaterialien
Neue Verfahren basieren hingegen auf dem direkten Recycling von Aktivmaterialien. „Dabei werden die Aktivmaterialien nicht mehr vollständig aufgelöst. Stattdessen werden sie in die einzelnen Zellbestandteile zerlegt und dann mechanisch getrennt, um sie möglichst rein zurückzugewinnen“, erklärt Gleiß. In der Industrie konnten sich diese Verfahren jedoch noch nicht durchsetzen. Das hat verschiedene Gründe. Zum einen lässt sich noch nicht vorhersagen, wie sich das wiedergewonnene Rezyklat verhält. Hat der Prozess möglicherweise negative Auswirkungen auf die Materialeigenschaften? Zum anderen gibt es keine Kriterien, um die Einsatzfähigkeit des gealterten Materials zu beurteilen. Es stellt sich also die Frage, ob sich die Bestandteile überhaupt für die Wiederverwertung eignen oder gegebenenfalls aussortiert werden müssen. Und zum Schluss fehlt es bisher an praxisorientierten Lösungen, mit denen sich die Batteriekomponenten effizient trennen lassen.
Und genau hier setzt das neue Verfahren der Forschenden an. „Diese kritischen Punkte greift unser Verbundvorhaben auf und beschäftigt sich primär mit der Entwicklung einer agilen Prozesskette für das direkte Recycling von Lithium-Ionen-Batterien sowie der Regeneration der so wiedergewonnenen Aktivmaterialien“, sagt Thomas Dreyer von der Weber Ultrasonics AG.
Kreislauffähige Produktion von Batterien schont die Umwelt
Ein effektives Recyclingverfahren im industriellen Maßstab ist nicht nur aus ökologischen, sondern auch aus wirtschaftlichen Gründen von größter Bedeutung. Es ermöglicht die Rückgewinnung von wertvollen Materialien wie Lithium, Kobalt, Nickel und anderen Metallen aus alten Batterien. Dies reduziert die Abhängigkeit von neuen Rohstoffen und trägt zur Schonung natürlicher Ressourcen bei. Das Verbundprojekt „Agile Prozessketten zum direkten Recycling von Lithium-Ionen-Batterien und Regeneration der Aktivmaterialien“ (DiRecReG) leistet somit einen wichtigen Beitrag für einen effizienten und nachhaltigen Produktionskreislauf, in dem die aktiven Batteriekomponenten funktionserhaltend zurückgewonnen werden. „Ziel ist es zudem, die energieintensiven Prozessschritte der zurzeit eingesetzten Recycling-Verfahren zu ersetzen und nachhaltig recycelte, hochwertige Sekundärmaterialien im Sinne einer Kreislaufwirtschaft zu liefern“, sagt Gleiß.
Das Projekt wird von Bundesforschungsministerium mit 2,95 Millionen Euro gefördert. Seine Laufzeit beträgt insgesamt drei Jahre.
Ein Beitrag von: