Düsentriebwerk aus dem Drucker
Einem Forscher- und Entwicklerteam gelang es, ein komplettes Mikrostrahltriebwerk auszudrucken, das funktionsfähig sein soll. Wir haben mit den Machern gesprochen und sagen, warum die Luftfahrtbranche darin die Zukunft sieht.
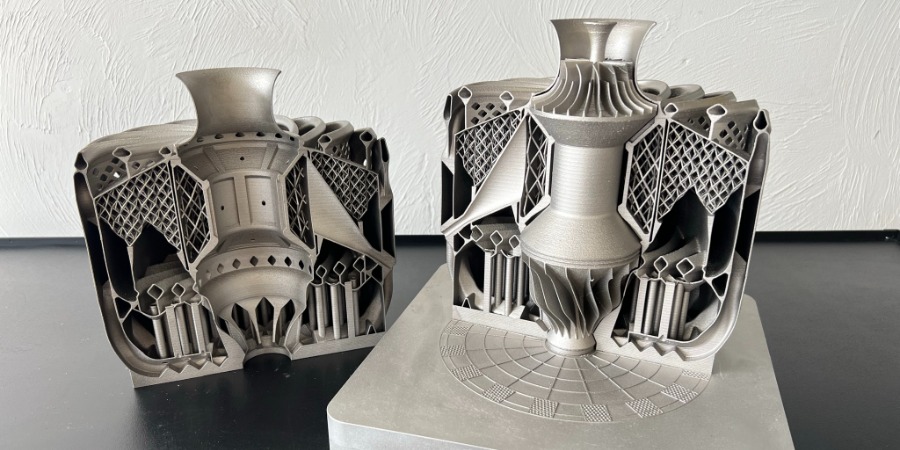
PTC hat auf der LiveWorx 2023 das weltweit erste vollständig in 3D gedruckte Triebwerk vorgestellt.
Foto: PTC
Hochbelastet, viele bewegliche Teile, die bis zu 50.000 Umdrehungen pro Minute absolvieren: Eine Turbine ist ein komplexes Zusammenspiel aus etlichen Einzelteilen. Doch das muss einfacher gehen, dachten sich Dr. Ronen Ben Horin, Vizepräsident für Technologie beim US-Unternehmen PTC und Senior Research Fellow am Technion – Israel Institute of Technology, sowie Beni Cukurel, Professor für Luft- und Raumfahrt am Technion.
Horin ist Experte für additive Fertigung und verfügt über mehr als 25 Jahre Branchenerfahrung im Design komplexer Luft- und Raumfahrt- sowie Verteidigungssysteme. Cukurel ist bekannt dafür, das Thema Strahltriebwerke weiter zu denken. Also haben die Beiden in Zusammenarbeit mit weiteren Instituten und Unternehmen, das nach eigener Aussage weltweit erste Mikrostrahltriebwerk entwickelt, das sich aus einem Guss, samt sämtlicher beweglicher Komponenten, ausdrucken lässt.
Mit dem kürzlich auf der Konferenz LiveWorx in Boston erstmals präsentierten Mikroturbostrahltriebwerk sollen künftig unbemannte Luftfahrzeuge mit einem Gewicht von bis zu 200 Kilogramm ausgestattet werden, erläuterte Cukurel im Gespräch mit ingenieur.de.
So sieht das innovative Konzept aus
Dabei handelt es sich um eine neuartige Turbomaschinenarchitektur, erklärt Cukurel: „Die Gasturbine besteht nur aus zwei Hauptteilen – einem statischen Gehäuse mit einer eingebetteten Brennkammer und einer rotierenden Schalenstruktur.“ Das rotierende Bauteil dreht sich mit einer Geschwindigkeit von 40.000 U/min und besteht aus Kompressor- und Turbinenlaufrädern, die durch eine Hohlwelle verbunden sind. Der Rotor dient auch als kraftstoffbetriebenes hydrostatisches Lager.
Der Kraftstoff wird durch perforierte Medien in Richtung Kompressor-Diffusor-Bereich evakuiert und vermischt sich als Aerosol mit dem einströmenden Luftstrom. „Um die Motorgröße zu minimieren, wird eine Brennkammer mit porösem Medium verwendet, um das vorgemischte Kraftstoff-Luft-Gemisch zu verbrennen, was wiederum den Einsatzbereich der Brennkammer erhöht“, erläutert der Professor. Der Proof-of-Concept-Demonstrator liegt kompakt in der Hand und wiegt nur gut zwei Kilogramm.
In der Luft- und Raumfahrtindustrie wird schon länger mit additiver Fertigung experimentiert. So hat ein Forscherteam des Fraunhofer IWS zusammen mit dem Institut für Luft- und Raumfahrttechnik der TU Dresden gezeigt, dass sich Triebwerke für Mikrolauncher, eine Alternative zu herkömmlichen Trägerraketen, zumindest teilweise additiv herstellen lassen.
Die mittelgroßen Transportsysteme können Nutzlasten bis zu 350 Kilogramm befördern und sollen künftig kleine Satelliten in den Weltraum bringen. Treibstoffinjektor, Brennkammer und Düse werden per Laser Powder Bed Fusion (L-PBF) Schicht für Schicht hergestellt. Die Düse selbst besteht aus einem stachelförmigen Zentralkörper, über den die Verbrennungsgase beschleunigt werden.
Bereits vor Jahren wurde an der australischen Monash University ein Flugzeugtriebwerk mit dem 3D-Drucker hergestellt. Allerdings nicht aus einem Stück. Insgesamt wurden 14 Hauptkomponenten, unter anderem aus Titan, Aluminium und Nickel-Legierungen, gedruckt und dann montiert.
Warum die Triebwerkproduktion künftig sehr einfach werden könnte
Das US-israelische Team hat hingegen nur ein Material verwendet: Inconel 718. Das ist der Markenname für eine Reihe von extrem belastbaren und druckfähigen Nickelbasislegierungen, genauer: eine Nickel-Chrom-Eisen-Molybdän-Verbindung, die vor allem für Hochtemperatur-Anwendungen verwendet wird. Die Australier benötigten noch einen Monat, bis alle einzeln ausgedruckten Komponenten aus dem Drucker kamen. Cukurel berichtet von einem 5-Tages-Sprint, die eine EOS-Maschine hinlegte, bis das gesamte Aggregat fertig war.
Möglich wurde das letztlich durch moderne Werkzeuge des generativen Designs: „Wir haben unsere Forschungsidee durch digitale Modellierung und simulationsgestütztes Design der gesamten Motortopologie in Creo, einer CAD-Software von PTC, umgesetzt“, berichtet Cukurel. Insbesondere die innen liegenden Kühlkanäle mit feinen, verschlungenen Strukturen stellen hohe Anforderungen an das Design und lassen sich konventionell nicht fräsen oder gießen.
Hierbei leistete die Software einen wesentlichen Beitrag: „Creo erwies sich als leistungsstarke Lösung, die es ermöglicht, innovatives Design vom ersten Konzept über das endgültige Modell bis hin zum 3D-Druck zu übertragen“, berichtet Ronen Ben Horin. Insbesondere was die Gittermodellierung anbelangt und die Möglichkeit so generativ zu designen, dass möglichst viel Material und damit Gewicht eingespart werden konnte, ohne dass darunter die Festigkeit, Leistung sowie Lebensdauer leiden.
Außerdem half die Software durch Funktionen des additiven Fertigens unter anderem dabei, Gitterstrukturen des Triebwerkes so zu optimieren, dass diese problemlos gedruckt werden können. Nachdem Creo mit den meisten 3D-Druckern auf dem Markt kompatibel ist, gelingen sozusagen Konstruktion und Produktion aus einem Guss: So können die Entwickler ihre am Rechner entworfenen 3D-Modelle direkt an verschiedene Druckerendgeräte senden und fertigen lassen.
Diese Kombination aus fortschrittlichen Tools für generatives Design mit erweiterten Geometrie-, Simulations- und Bauvorbereitungsfunktionen sowie 3D-Druck eröffnet neue Möglichkeiten für Ingenieure. Der Designprozess beschleunigt sich, letztlich sinkt der Materialverbrauch, etwa von Titan, weil bereits die Konstruktion daraufhin optimiert ist und beim 3D-Druck kein Abfall anfällt. Kein Wunder also, dass Flugzeugbauer wie Airbus und Boeing ein hohes Interesse am additiven Fertigen von Triebwerken haben.
Warum 3D-Druckdüsen ein echter Gamechanger sind
Und es gibt noch eine Reihe weiterer Gründe: Triebwerke aus einem Guss verringern drastisch die Abhängigkeit von Zulieferern. Was angesichts löchriger Lieferketten nicht unwesentlich ist. Außerdem ersparen sich Flugzeugbauer personal- und arbeitsintensive Montageprozesse. „Das senkt die Kosten, reduziert die Anforderungen an einen Metall-3D-Drucker und eröffnet die Möglichkeit einer On-Demand-Fertigung direkt beim Kunden“, unterstreicht Horin.
Insbesondere bei modernen, unbemannten Luftfahrzeugen, etwa für Verteidigungszwecke, sei dies ein großer Vorteil, ergänzt Cukurel, denn noch seien die Kosten für dort eingesetzte Mikrogasturbinen unverhältnismäßig hoch.
„Trotz der relativ einfachen Topologie herkömmlicher Mikroturbostrahltriebwerke erfordert ihre traditionelle Produktion eine komplexe Planung langer Prozesse aufgrund zahlreicher Teile und unterschiedlicher Herstellungsverfahren, darunter Turbinenguss, Verdichterfräsen, Wellendrehen und -schleifen sowie Brennkammerblechbearbeitung“, führt der Wissenschaftler aus. Anschließend würden alle diese Teile gemeinsam mit den Beschichtungs- und Lageranbietern von qualifiziertem Personal montiert.
„Unser Konzept setzt hingegen auf die Entwicklung eines unkonventionellen Motors, der für die additive Fertigung konzipiert ist“, so Cukurel, „Da nur ein Laser-Pulverbett-Schmelzdrucker und ein Bediener erforderlich sind, reduzieren sich die Kosten für den Motor auf die Abschreibung von Investitionsgütern und Rohmaterial.“
Wann könnte der Micromotor marktreif sein?
Doch bis etwa eine Drohne mit der Mikrostrahlturbine abhebt, dürfte noch einige Zeit vergehen: „Wir rechnen mit weiteren zwei bis drei Jahren Entwicklungszeit“, sagt Cukurel. In der Simulation am Rechner funktioniert das ausgedruckte Triebwerk, nun folgen erste Live-Tests im Labor. Die hier gewonnenen Erfahrungen dürften auch andere Entwicklerteams weiterbringen, die mit ihren 3D-Druck-Triebwerken in Zukunft große Jets und Raketen abheben lassen möchten.
Ein Beitrag von: