Kompakte Übersicht aller 3D-Druck-Verfahren
Der 3D-Druck rückt in Alltagsreichweite. Das Verfahren macht es möglich, komplexe 3D-Modelle für nahezu jedes Einsatzgebiet zu erstellen. Neuartige Herstellungstechniken und Rapid Prototyping machen die Technologie zum neuen Allrounder für komplizierte Bauteile.
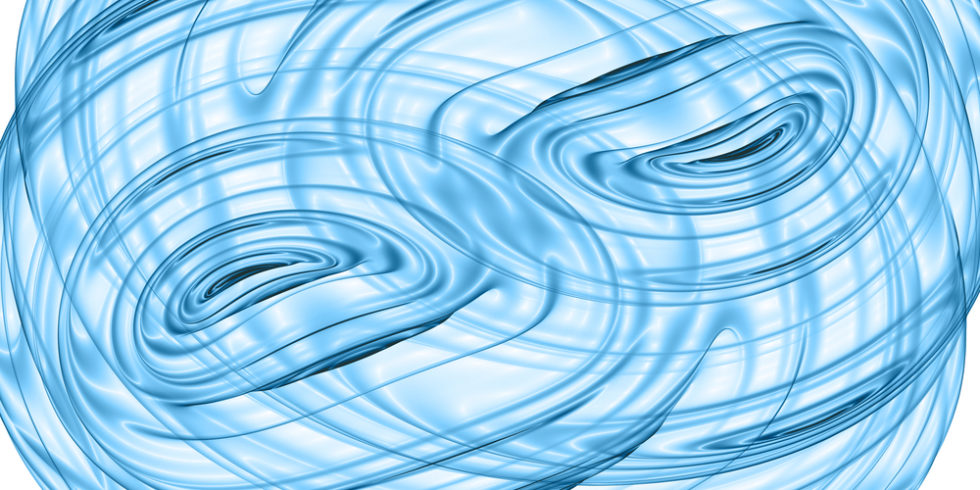
Ein Flüssigmagnet direkt aus dem 3D-Drucker.
Foto: panthermedia.net/yurok.a
Bei der Erstellung von Bauteilen und Prototypen werden verschiedene Methoden praktiziert. Subtraktive Fertigungsverfahren schneiden oder fräsen die gewünschte Form aus einem beliebigen Materialblock heraus. Diese Techniken stoßen jedoch an ihre Grenzen, wenn es um Hohlräume beziehungsweise komplexe sowie filigrane Bauteile geht. Formative Verfahren wie das Gießen ermöglichen zwar die Herstellung solcher Fertigungsteile, die Technik ist jedoch mit hohem Aufwand verbunden. Die Materialauswahl ist auch hier sehr vielseitig. Die Herstellung der Form ist jedoch noch um einiges aufwendiger als subtraktive Verfahren. Gussverfahren sind leider oft unsauber und Materialschwächen sowie Fehler sorgen für Ausschuss.
Mit dem 3D-Druck steht nun ein additives Verfahren zur Verfügung, bei dem ein Gegenstand Schicht für Schicht aufgebaut wird. Der Formgebung werden dabei keine Grenzen gesetzt. Die Materialauswahl ist beinahe dieselbe wie beim Gießverfahren, denn das Material ändert – meist durch die Zufuhr von Wärme – seinen Aggregatzustand von fest zu flüssig. So lassen sich abgesehen von Kunststoff in speziellen Druckern auch Fertigungsteile aus Metall in höchster Präzision drucken. Die Weiterentwicklung des 3D-Drucks erlaubt durch verschiedene Verfahren auch den Einsatz anderer Rohstoffe wie Papier, Keramik und Sandstein.
Dieser Artikel soll die Grundlagen und wichtigsten Begriffe aus der Welt der additiven Fertigungsverfahren vermitteln.
- Anwendungsgebiete und Rapid Prototyping
- Die Geschichte des 3D-Drucks
Anwendungsgebiete und Rapid Prototyping
3D-Drucker sind längst in privaten Haushalten angekommen. Einsteigermodelle und Bausätze können kostengünstig erworben werden. Technikaffine Bastler können beispielsweise komplette Do-It-Yourself-Bausätze (DIY) ordern und Assemblierung, Verkabelung und Programmierung selbst übernehmen. Eine Herausforderung, die sich aber lohnen kann. Die Montage nimmt einige Zeit in Anspruch, dabei werden aber auch gleich die Grundlagen des 3D-Drucks vermittelt. Sie erfordert jedoch Grundkenntnisse in der Elektrotechnik sowie handwerkliches Geschick. Bei fertigen Consumer-Geräten werden die Oberflächen zur Programmierung dagegen immer benutzerfreundlicher und die einzelnen Arbeitsschritte voll- oder teilautomatisiert ausgeführt. Ausgangsmaterial für viele Geräte sind einfache Polymere – aufgewickelt auf einer Rolle, die nur eingefädelt werden muss – oder Systeme, die die genaue Pulverdicke auftragen. Ganz egal, ob Consumer-Gerät oder DIYBausatz, mit beiden Kandidaten können zum Beispiel filigrane Teile für den Modellbau oder kleinste Ersatzteile zu Hause detailgetreu gedruckt werden. Das bietet nicht nur Vorteile für private Anwender.
Die Industrie greift schon lange auf das Verfahren der Prototypenherstellung zurück, um Produkteigenschaften zu testen und für den Endverbraucher zu optimieren. Kleinserien oder Negative für Gussformen aus dem 3D-Drucker erübrigen aufwändige konventionelle Herstellungsverfahren. Hier kommt das Rapid Prototyping zum Einsatz.
Selbst in der Medizin sind additive Verfahren zu einem festen Bestandteil geworden. MRT-Bilder werden im Drucker nachgebildet, um dem behandelnden Arzt die zweidimensionalen Bilder zu veranschaulichen. Kranke Organe oder Gelenke können ebenso repliziert werden. Diese dienen zum Beispiel als Anschauungsmaterial für Studenten, um das Verständnis über den menschlichen Körper zu erweitern. Die Herstellung von individuellen Prothesen mit Hilfe des 3D-Drucks wird bereits seit Jahren praktiziert. Darüber hinaus werden Maßanfertigungen für Brillen, Zahnimplantate, Gehör- Seh- oder Gelenksprothesen mit dem Drucker realisiert. Labore nutzen das 3D-Verfahren, um Proben unter Schutzatmosphäre zu konservieren oder Testreihen ohne Verunreinigungen zu erstellen.
Der künstlerische Bereich profitiert ebenso von der Technik. Modelle und Skulpturen werden gedruckt, statt gemeißelt oder geschnitzt. Durch die vorherige Modellage am Computer kann der Künstler noch Änderungen vornehmen.
Additive Fertigungsverfahren werden zudem für die Baubranche immer interessanter. Portable 3D-Drucker sind mittlerweile in der Lage, ganze Häuser zu errichten. Die Wände werden Schicht für Schicht vom Drucker gebaut, Schalungen, Mörtel und lange Trockenzeiten entfallen. Das Material ist außerdem lange haltbar, steril und feuchtigkeitsresistent.
Vom Küchenexperiment zur Marktreife
Bereits im Jahr 1971 wurde der Grundstein für eine Reihe an Verfahren zur additiven Fertigung gelegt. Ihren Anfang findet die Technologie mit der Anmeldung eines Patentes, welches beschreibt, wie dreidimensionale Objekte aus Photopolymeren (Verbindungen, die im UV-Licht ihre Eigenschaften ändern) entstehen können. Dabei handelt es sich um ein Verfahren, bei dem ein lichtempfindliches Harz mit Hilfe von UV-Strahlen polymerisiert wird – Schicht für Schicht – und sich auf diese Weise ein dreidimensionales Objekt erstellen ließ. Charles Hull meldet schließlich im Jahr 1984 sein Patent für die Stereolithografie an, das zwei Jahre darauf bewilligt wird. Im selben Jahr gründet er das Unternehmen „3D Systems“ (South Carolina, USA) und bringt den 3D-Drucker „SLA-1“ auf den Markt.
Das Interesse an neuen Fertigungsverfahren wächst. 1988 wird auf ein weiteres Druckverfahren Patent angemeldet: Das selektive Lasersintern (SLS). Bei diesem Vorgang werden Pulverkörner mit Hilfe eines Lasers zu Formen verschmolzen. Lediglich ein Jahr später findet die nächste Drucktechnik ihren Weg vom Patent zum Markt. Hierbei handelt es sich um das heute am weitesten verbreitete Fused Deposition Modeling (FDM), bei dem Filamente (Fäden aus Kunststoff) geschmolzen, durch eine Düse extrudiert und Schicht für Schicht aufgetragen werden. Der 3D-Druck ist geboren.
In den frühen 90ern widmen sich zunehmend Unternehmen der Entwicklung von CAD-Software, da für die additive Fertigung noch kaum benutzerfreundliche Programme existieren. Als eines der ersten entsteht Sanders Prototype, heute bekannt als Solidscape. Im Jahr 2000 wird die erste funktionale Niere per 3D-Druck realisiert. Von einer Transplantation in einen Menschen sind Mediziner jedoch noch weit entfernt. Erste Experimente und Forschungen laufen bereits. Kurz darauf folgen Modelle für den Einsatz am Arbeitsplatz, was dem FDM-Verfahren zu größerer Bekanntheit verhilft. Dies führt zu kontinuierlichem Wachstum der Branche. Bereits 2008 werden medizinische Prothesen und Orthesen mit diesem Verfahren hergestellt und eingesetzt.
Der Patentablauf des Fused Deposition Modeling führt schließlich zu einer Revolution in der additiven Fertigung. Der 3D-Druck erobert den Markt und hält im Industriesektor Einzug. Viele kleine und mittlere Unternehmen profitieren seitdem von einer kostengünstigen Methode des 3D-Prototypings.
Additive und subtraktive Fertigungsverfahren im Vergleich
Die Begriffe Additive und Subtraktive Fertigungsverfahren sind sehr unterschiedlich. Beide bieten Vor- und Nachteile, abhängig vom jeweiligen Einsatzgebiet. Deshalb existieren auch Verfahren, die beides miteinander kombinieren.
Subtraktive Fertigungsverfahren finden in erster Linie in der Massenproduktion Anwendung. Das Werkstück entsteht durch Abtragen von Material von einem größeren Materialblock durch Zerspanungsvorgänge wie dem Drehen, Bohren oder Fräsen. Der große Vorteil dieser Fertigung ist die hohe Genauigkeit bei ebenso hoher Produktionsgeschwindigkeit. Erforderliche Toleranzen können bei zerspanenden Verfahren besser eingehalten werden. Außerdem lassen sich feine Gewinde oder genaue Bohrungen herstellen. Stützstrukturen oder Pulverreste entfallen ebenfalls, verglichen mit der additiven Fertigung. Subtraktive Verfahren bringen jedoch auch einige Nachteile mit sich. Beispielsweise erreicht der Materialverlust, beziehungsweise der entstehende Abfall, oftmals enorme Ausmaße. Verwendete Werkzeuge unterliegen ständigem Verschleiß. Zudem gestaltet sich die Programmierung der Fertigungsmaschinen schwieriger. Hier müssen Abmessungen und Lage des Materials mit den Abmessungen und Eigenschaften der Werkzeuge abgeglichen werden. Dazu kommt noch, dass vor dem Produktionsstart die Geschwindigkeit von Spindel (Werkzeugaufnahme) und Arbeitsfläche bestimmt werden müssen, um weder das Werkstück noch das Werkzeug zu hohen Belastungen auszusetzen. Weitaus unkomplizierter ist es, eine 3D-Datei an einen 3D-Drucker zu senden.
Additive Verfahren bieten deshalb eine ganze Reihe an Vorteilen. Angefangen bei der einfachen Handhabung und Bedienung bis hin zur Herstellung von komplexen Werkstücken aus verschiedenen Materialien. Mit dieser Technologie lassen sich Formen realisieren, welche mit subtraktiven Verfahren nur schwer oder gar nicht möglich wären. Komplexe dreidimensionale Strukturen werden Schicht für Schicht aufgebaut – der gesamte Produktionsvorgang in nur einem einzigen Schritt. Selbst die Herstellung hohler Strukturen ist denkbar simpel, beispielsweise die Integration komplexer Kühlkanäle in Turbinenschaufeln von Triebwerken.
Vorteile der additiven Fertigung
- kaum Materialverlust
- komplexe und hohle Formen realisierbar
- einfachere Programmierung gegenüber CNC-Maschinen
- keine Werkzeuge notwendig
- geringe Lagerkosten, da Teile erst bei Bedarf gefertigt werden
Nachteile der additiven Fertigung
- vielfach langsamere Produktionsgeschwindigkeit
- oftmals Stützstrukturen notwendig, die sich schlecht entfernen lassen
- zum Teil thermisch nicht belastbare Materialien
- raue Oberflächen und daher Nachbearbeitung erforderlich
- vergleichsweise höhere Materialkosten
Für jede Anwendung der passende Werkstoff
Materialien beziehungsweise Werkstoffe spielen im 3D-Druck eine große Rolle. Ist im industriellen Bereich die Vielfalt noch größer, beschränkt sich diese im Heim- und Office-Bereich auf eine sehr überschaubare Diversität. Die Gemeinsamkeit der gedruckten Materialien liegt im vergleichsweise geringen Schmelzpunkt des Ausgangswerkstoffs. Bestimmte Stoffe lassen sich auch mit anderen kombinieren. Dadurch werden beispielsweise Stützstrukturen, welche für den einwandfreien Druck von überhängenden oder freistehenden Elementen erforderlich sind, in nur einem Vorgang mit dem eigentlichen Material verarbeitet.
Das wohl bekannteste Verfahren ist das Fused Deposition Modeling (FDM), beziehungsweise Fused Filament Fabrication (FFF). Hierbei handelt es sich um ein Schmelzschichtverfahren aus dem Bereich des Rapid Prototypings. Als Werkstoffe werden in erster Linie thermoplastische Kunststoffe, wie Acrylnitril-Butadien-Styrol (ABS), Polyactide (PLA), Polyethylenterephthalat (PET) oder Polyethylen verwendet. Des Weiteren existieren Druckverfahren, welche mit Metallpulver versehene Filamente verarbeiten und dadurch dem Werkstück eine metallische Struktur verleihen. Dabei wird jedoch nur ein sogenannter Grünling erzeugt, der abschließend noch gesintert werden muss.
Die Zahl der Anwendungsfelder ist ebenso groß wie die Vielfältigkeit der Filamente. So existieren für jedes Einsatzgebiet spezielle Materialien mit ganz spezifischen Eigenschaften. Bei diesen variieren sowohl Schmelzpunkt, Dichte, Löslichkeit mit bestimmten Stoffen und Widerstandsfähigkeit.
Mechanische Bauteile werden in der Regel aus Polycarbonat (PC) hergestellt. Dieses ist widerstandsfähig, steif und kann gebogen werden, ohne zu zerbrechen. Polycarbonat wird auch für die Produktion von CDs und kugelsicherem Glas verwendet. Beim Druck benötigt es hohe Temperaturen von bis zu 280 Grad Celsius und einen beheizten Bauraum. Für weniger beanspruchte Bauteile kann ebenso das Allround-Material PET verwendet werden. Dieses besitzt einen geringeren Schmelzpunkt und ist demnach einfacher zu verarbeiten. Zudem ist das Material schwer entflammbar und resistent gegen eine Vielzahl an Chemikalien. Die Kosten fallen im Vergleich bei PET deutlich geringer aus. Für den Außenbereich eignen sich Filamente aus Acrylester-Styrol-Acrylnitril (ASA), das ursprünglich für das Spritzgussverfahren verwendet wird. Kratzfest, wetter- und UV-beständig, trotzen daraus gedruckte Objekte Sonne und Umwelteinflüssen.
Bei Modellen, Alltagsgegenständen und Spielzeugen findet ABS oder Acrylglas Verwendung. Ersteres ist ein Kompromiss aus Widerstandsfähigkeit und Kostenaufwand und bietet den Vorteil der einfachen Verarbeitung. Zudem lässt sich ABS problemlos einschmelzen und wiederverwenden. Acrylglas beziehungsweise Polymethylmethacrylat (PMMA) ist ein meist transluzenter Kunststoff, welcher dank seiner harten, nahezu kratzfesten Oberfläche vielseitig eingesetzt wird. Die Verarbeitung dieses Materials gestaltet sich etwas komplizierter, da beim Druckvorgang sowohl ein geschlossener, beheizter Bauraum des Druckers als auch eine beheizte Druckplatte vorausgesetzt werden. Andernfalls ist es möglich, dass sich das Werkstück vorzeitig löst oder zum Warping (nach oben gebogene Kanten an der Basis des gedruckten Objekts) neigt. Eine biologische Alternative zu ABS und PMMA ist sogenanntes Green-TEC-Filament. Dieses besteht aus nachwachsenden, natürlichen Rohstoffen und ist biologisch abbaubar sowie CO2-neutral.
Für Gehäuse und Prototypen ist einerseits das einsteigerfreundliche PLA-Filament geeignet, welches kaum unter Warping-Effekten leidet und von nahezu jedem 3D-Drucker verarbeitet werden kann. Andererseits lassen sich für diesen Einsatzzweck thermoplastische, auf Urethan basierende Elastomere (TPE) einsetzen. Diese sind elastisch und weisen eine gummiartige Oberfläche auf. Rutschfeste Werkstücke wie Griffe, Halterungen oder Dichtungen werden auf diese Art und Weise hergestellt.
Fallweise ist es notwendig, das noch nicht ausgehärtete Material während des Druckvorgangs abzustützen, sodass die Form stabil bleibt oder überhängende Bereiche gedruckt werden können. Dabei bedienen sich Drucker einer zweiten Filamentaufnahme, sowie einer zusätzlichen Düse. Als Stütz- beziehungsweise Supportmaterial werden Stoffe verwendet, welche in Wasser oder anderen Flüssigkeiten gelöst werden können. Das sind zum einen PVA, welches wasserlösliche Eigenschaften besitzt und zum anderen High Impact Polystrene (HIPS), welches in Limonenextrakt, einem Nebenprodukt der Orangensaftproduktion, aufgelöst werden kann.
Funktionsweise: Ablaufbeschreibung vom Entwurf bis zum fertig gedruckten Modell
Die Verwandlung von bloßen Gedanken im Kopf zum haptisch fühlbaren dreidimensionalen Modell erfordert ein gewisses Maß an Know-how im Bereich CAD und Fertigungstechnik. Angefangen bei 3D-Modellierung bis hin zur beinahe schon handwerklichen Betätigung, welche dem Objekt die finale, glatte Oberfläche verleiht, gilt es, einige Punkte zu beachten.
Am Anfang war der Gedanke
Der Entwurf eines dreidimensionalen Modells beginnt in der Regel im Kopf, findet dann seinen Weg auf Skizzen und Blaupausen und wird im nächsten Schritt digitalisiert. Mit Hilfe spezieller Software aus dem CAD/CAM-Bereich (Computer Aided Design/Computer Aided Manufacturing) lassen sich Modelle exakt entwerfen und, je nach Software, bearbeiten, weiterentwickeln oder auch für andere Nutzer bereitstellen. Dadurch ist es möglich, dass auch weniger versierte Anwender Zugang zu einer Vielzahl an Modellen durch diverse Online-Datenbanken erhalten. Dreidimensionale Objekte können demnach nicht nur selbst entworfen, sondern unkompliziert heruntergeladen und modifiziert werden.
Abseits der kostenlosen Objektbibliotheken, welche größtenteils Alltagsgegenstände enthalten, müssen Maßanfertigungen, Bauteile oder Modelle meist von Hand erstellt werden. Verschiedene Software, sowohl aus dem kostenfreien als auch kostenpflichtigen Bereich, ermöglicht dies dem Anwender. Grundlegende Funktionen, welche für simple Modelle ausreichen, sind in einer Vielzahl kostenloser Programme enthalten. Werden hingegen komplexe Bauteile benötigt, ist oftmals die Anschaffung teurer CAD-Software notwendig. Einige Hersteller bieten jedoch auch ein Abo-Modell an, sodass sich die Ausgaben in Grenzen halten und der Heimanwender Profi-Anwendungen nutzen kann.
Eines gemein haben diese Softwarepakete: Sie unterstützen verschiedene Dateiformate, um einen reibungslosen Austausch zwischen Computer und Drucker zu ermöglichen – oder, um Modelle in andere Formate konvertieren zu können.
Dateiformate
In der 3D-Druck-Branche hat sich das seit den 1980ern weiterentwickelte STL-Format für generative Fertigungsverfahren etabliert. STL steht hierbei für Surface Tesselation Language – beschränkt sich in seiner Anwendung aber nicht explizit auf diese Fertigungsmethode, sondern wird von den meisten Geräten unterstützt. Das Dateiformat wird dadurch also zur Gemeinsprache, welche zu einer breiten Palette verschiedener Soft- und Hardware kompatibel ist.
Das Dateiformat konvertiert das Modell in eine große Zahl kleiner Dreiecke, welche die Form abbilden. Texturen werden jedoch nicht übernommen, was sich positiv auf die Dateigröße auswirkt. Dateien im STL-Format können dadurch problemlos per E-Mail versandt werden, beziehungsweise lassen sich einfach auf Druckdienstleister-Portale hochladen. Die meisten Maschinen und 3D-Drucker kommen mit Daten dieses Typs zurecht.
Alternativ existieren einige weitere gängige Formate, wie zum Beispiel VRML (Virtual Reality Modeling Language), welches zusätzlich Farbinformationen speichern kann. Die genormten Formate AMF oder 3MF (ISO/ASTM 52915) beinhalten außerdem Materialinformationen und besitzen die Möglichkeit, gekrümmte Flächen zu speichern, sowie relevante Informationen zur Entwicklungsarbeit. Dies kann jedoch aus Gründen der Datensicherheit oftmals zum Problem werden – gerade, wenn es sich hierbei um Prototypen oder medizinische Anfertigungen handelt.
Datenübertragung
Die Übertragung des dreidimensionalen Modells vom Rechner auf den Drucker kann auf verschiedenen Wegen stattfinden. Einerseits lassen sich die meisten Consumer-3D-Drucker per USB direkt am PC anschließen – was den Nachteil mit sich bringt, dass sich dieser ständig im Betrieb befinden muss. Druckzeiten von mehr als einem Tag sind in dieser Branche nicht unüblich – deshalb ist es fallweise sinnvoller, die Daten per SD-Karte auf den Drucker zu kopieren. Im teilautonomen Betrieb kann der Druck am Rechner gestartet und überwacht werden, jedoch dient dieser während des Vorgangs nur als Kontrolleinheit.
Je nach Maschinentyp kommt entweder bereits im Rechner oder im Drucker sogenannte Slicing-Software zum Einsatz. Diese zerlegt die Datei in einzelne zweidimensionale Schichten und konvertiert diese zu Maschinencode (GCode, RS-247). In diesem sind die einzelnen Schritte des gesamten Druckvorgangs enthalten, wie zum Beispiel die Bewegungen der Servomotoren sowie deren Geschwindigkeit auf den drei Achsen.
Ist dieser Vorgang abgeschlossen, wird das zu druckende Objekt in der Druckersoftware auf der Bauplattform ausgerichtet – idealerweise mittig. Diverse Druckoptionen ermöglichen die optimale Verarbeitung verschiedener Materialien. Hier können Parameter wie Geschwindigkeit, Temperatur oder Druckstärke festgelegt werden. Daraufhin wird beim Druck mit Filament der sogenannte Toolpath – der Weg, den das Werkzeug, in diesem Fall der Extruder, zurücklegt, berechnet und der Druck beginnt. Andere Verfahren, wie beispielsweise Stereolithographie oder Digital Light Processing (DLP), starten direkt nach Erzeugung der einzelnen Schichten.
Der Druckvorgang im Detail
Die berechneten Pfade werden im Anschluss abgefahren. Dabei beginnt der Extruder, Material auf die bereits vorgeheizte Druckplatte aufzutragen und mit der untersten Ebene des dreidimensionalen Objekts zu beginnen. Die Basis weist eine etwas höhere Schichtstärke auf, sodass die Stabilität gewährleistet ist und sich das Modell nicht löst. Durch die beheizbare Düse verflüssigt der Extruder das Filament und trägt dieses anhand der festgelegten Pfade auf. Schicht für Schicht entsteht in diesem Vorgang das Modell. Die Volumenkörper sind in der Regel nicht solide, sondern werden mit Stützstrukturen versehen, um einerseits Material einzusparen und andererseits den Druckvorgang schneller abzuschließen. Durch die Erhitzung, nur knapp über den Schmelzpunkt des jeweils eingesetzten Materials, kühlt dieses schnell wieder ab und härtet aus. Nach erfolgtem Druck ist es üblicherweise notwendig, die Stützstrukturen, sofern vorhanden, zu entfernen oder – bei kombinierten Druckverfahren mit zwei oder mehr Werkstoffen – diese in Flüssigkeiten aufzulösen. Die schichtweise Entstehung führt zu einer relativ rauen Oberflächenstruktur, weshalb Objekte oftmals erst durch Schleifen und Lackieren ihr abschließendes Finish erhalten.
Druckverfahren
Das Feld Additive Fertigungsverfahren beziehungsweise Additive Manufacturings (AM) umfasst eine Reihe verschiedener Verfahren, bei denen entweder Material Schicht für Schicht aufgetragen oder Materialpulver durch Laser geschmolzen wird. Dabei entstehen dreidimensionale Werkstücke aus diversen Materialien.
- Fused Deposition Modeling (FDM)
- Stereolithografie (SLA)
- Selektives Lasersintern (SLS)
- Digitale Lichtverarbeitungstechnologie (DLP)
Fused Deposition Modeling (FDM)
Beim Fused Deposition Modeling (FDM) wird ein Kunststofffaden (Filament) erhitzt und durch eine Düse auf die gewünschte Position aufgebracht. Die Schmelztemperaturen liegen bei etwa 200 bis 300 Grad Celsius, wobei manche Materialien zusätzlich einen beheizten Druckraum oder eine beheizte Druckplatte voraussetzen. Das Filament wird nur knapp über den Schmelzpunkt erhitzt und erstarrt dadurch binnen kürzester Zeit wieder. Auf diese Weise sind detailgenaue Werkstücke möglich, die allerdings meist eine raue Oberfläche aufweisen. Eine Nachbearbeitung ist deshalb in der Regel notwendig. Des Weiteren wird beim Druck von überhängenden oder hohlen Strukturen mit Stützmaterial gearbeitet, welches in einem separaten Schritt manuell entfernt werden muss. Die meisten 3D-Drucker für den privaten Bereich nutzen diese Technik.
Stereolithografie (SLA)
Die Stereolithografie (SLA) wurde bereits im Jahre 1983 entwickelt und gilt als das erste Verfahren im Bereich des 3D-Drucks. Dieses Verfahren ermöglicht sehr feine und filigrane Arbeiten und wird deshalb am häufigsten in der Industrie für das Rapid Prototyping verwendet. Die Vorlage des Werkstücks bildet ein zuvor mit CAD entwickeltes digitales Volumenmodell am Computer im STL-Format. Dieses wird dann an den Drucker weitergeleitet. Bei dem Verfahren wird selektiv ein sich im flüssigem Zustand befindlicher Photopolymer, wie zum Beispiel Epoxid- oder Acrylharz, mit einem UV-Laser Schicht für Schicht ausgehärtet. In einem Bad aus Basismonomeren verfestigt sich das Material an der Oberfläche und das Bauteil wird abgesenkt. Die Schichten des Modells sind je nach Verfahren 40 bis 120 Mikrometer hoch.
Selektives Lasersintern (SLS)
Das selektive Lasersintern wird ebenfalls für das Rapid Prototyping verwendet. Beim Sintern wird feinkörniges, keramisches oder metallisches Material bis kurz vor dem Schmelzpunkt des Stoffes erhitzt. Gleiches Prinzip gilt für das selektive Lasersintern. Mit Hilfe einer Walze oder einer Rakel wird ein pulverförmiges Ausgangsmaterial – meistens bestehend aus einem Polyamid, wie zum Beispiel Nylon – auf die Arbeitsplattform des 3D-Druckers aufgetragen und mit dem Laser jede einzelne Schicht in das Material gesintert. Ähnlich wie bei der Stereolithografie wird nach jeder Schicht die Plattform, je nach Einstellung um etwa 100 Mikrometer abgesenkt, sodass sich das Werkstück von unten nach oben langsam aus dem Pulverbett herauskristallisiert. Der wesentliche Vorteil beim SLS-Verfahren ist, dass das Pulver, indem sich das Objekt aufbaut, gleichzeitig als Stabilisator fungiert.
Selektives Laserschmelzen (SLM)
Das selektive Laserschmelzen ähnelt dem selektiven Lasersintern. Doch lassen sich Werkstücke und Bauteile aus Metall fertigen. Dieses Verfahren ermöglicht eine hohe Dichte von bis zu 100 Prozent und liefert dadurch weitestgehend vollwertige mechanische Eigenschaften. Je nach Anwendungsgebiet ist es aber auch möglich spezifische Dichten zu festzulegen. Auf der Arbeitsplatte des Druckers wird pulverförmiges Metall aufgetragen und mit einem Laser erhitzt, bis die Partikel Schicht für Schicht die gewünschte Form erreicht haben. Dabei wird die Grundplatte bei jedem Schritt abgesenkt und neues Pulver aufgetragen, bis alle Schichten zu einem Bauteil zusammengeschmolzen sind. Dieser Prozess findet unter Schutzgasatmosphäre (mit Edelgasen wie Argon oder Stickstoff) statt, um die Kontamination des Ausgangsmaterials mit Sauerstoff zu vermeiden.
Digitale Lichtverarbeitungstechnologie (DLP)
Die Digitale Lichtverarbeitungstechnologie beziehungsweise Digital Light Processing (DLP) ist eine Methode der additiven Fertigung, bei der mit Hilfe eines Projektors Polymer-Harze gehärtet werden. Ähnlich wie beim SLA-Verfahren werden die Werkstücke im Wannenbad entweder eingetaucht oder herausgezogen. Dabei belichtet beim DLP-Verfahren ein Projektor die oberste Schicht des Objekts und bringt diese zum Erhärten. Das Ergebnis wird Schicht für Schicht aufgebaut, jedoch ist diese Fertigungsmethode so genau, dass mit dem freien Auge kaum sichtbare Abstufungen erkennbar sind – verglichen mit FDM oder FFF. Digitale Lichtverarbeitung hat zudem den Vorteil, viel schneller als SLA zu arbeiten. Da hier kein UV-Laser zum Einsatz kommt, welcher Punkt für Punkt bestrahlt, sondern immer die gesamte Einzelschicht als Ganzes projiziert wird. Die beim DLP-Druck verwendeten Harze sind dieselben wie bei SLA. Die Materialien eignen sich deshalb in erster Linie für detaillierte Kunstwerke, Anschauungsmodelle von Prototypen oder Gießformen. Ein Nachteil liegt jedoch in der Auflösung der Projektion. Diese besteht bei DLP aus quadratischen Pixeln, die durch die Materialstärke rechteckige Blöcke (Voxel) entstehen lassen. Zudem hängt die Qualität von der Größe der jeweiligen Projektionsfläche ab – da der Projektor nur eine bestimmte Auflösung darstellen kann. Wird eine höhere Auflösung gewünscht, muss die Projektion verkleinert werden, was auch die maximale Druckgröße der Objekte beeinträchtigt.
3D-Druck mit kombinierten Werkstoffen
Es gibt ein Verfahren mit dem es möglich ist, mehrere Werkstoffe miteinander zu kombinieren. Das Besondere am sogenannten MultiJet Modeling ist, dass dabei Bauteile mit unterschiedlichen mechanischen und physikalischen Eigenschaften gedruckt werden können. Neben photopolymeren Resinen, die vollständig aushärten, können je nach Bedarf, flexible oder gummiartige Ausgangsmaterialien hinzugefügt werden. Dabei kommen auch temperaturbeständige oder transparente Stoffe zum Einsatz.
MultiJet Modeling (MJM)
Multijet Modeling (auch bekannt als Poly-Jet-Modeling) gehört zu den additiven Verfahren und wird häufig für das Rapid Prototyping eingesetzt. Der Aufbau des 3D-Druckers gleicht einem konventionellen Tintenstrahldrucker. Er besteht aus einem Druckkopf, der die gesamte Breite der Bauplattform abdeckt. Ausgestattet ist dieser mit mindestens zwei oder mehr linear angeordneten Düsen. Eine dient als Hauptmaterialzulauf, die andere besitzt die Fähigkeit, an komplexen Stellen Stützkonstruktionen – meist bestehend aus einem Wachs mit niedriger Schmelztemperatur – zu drucken. Das Ausgangsmaterial wird erwärmt in den Druckkopf geleitet und dort ganz fein zerstäubt und Schicht für Schicht mit kleinen Tröpfchen gedruckt. Bei diesem Vorgang senkt sich die Arbeitsplatte, wie bei den meisten additiven Verfahren. Wenn Überhänge gedruckt werden, erstellt der Drucker mit der anderen Düse eine Stützkonstruktion, sodass das Hauptmaterial des Bauteils in der gewünschten Form aushärten kann. Dazu wird UV-Licht verwendet, um die Photopolymere zu vernetzen beziehungsweise die Stoffeigenschaften des Ausgangsmaterials vorübergehend zu verändern, sodass es in der Lage ist, sich zu verbinden. Nach Beendigung des Drucks wird überschüssiges Material durch leichtes Erwärmen einfach entfernt.
Vor- und Nachteile des MultiJet Modelings
Es gibt, wie bei allen anderen Methoden des 3D-Drucks natürlich auch beim MultiJet Modeling Vor- und Nachteile. Zwar ist ein filigranes und detailliertes Ergebnis in vielen Bereichen der größte Vorteil, jedoch eignet sich dieses Verfahren nicht unbedingt für Prototypen, die eine gewisse Funktionalität voraussetzen. Ökonomisch betrachtet ist im Vergleich zu anderen 3D-Druck-Verfahren das MultiJet Modeling wegen der hohen Materialkosten auch nicht zu unterschätzen. Trotz der Eigenschaft, Materialien zu kombinieren, steht eine limitierte Auswahl derer zur Verfügung. Beschränkt ist auch die Größe der Werkstücke, bedingt durch das Volumen des Druckers. Dafür lassen sich die Stützkonstruktionen mit vergleichsweise wenig Aufwand entfernen. Nicht so, wie bei anderen additiven Fertigungsverfahren, bei denen für die Entfernung der überstehenden Ausgangsmaterialien Werkzeuge, wie Zangen, Feilen oder Scheren notwendig sind. Einer der größten Vorteile des MJM ist der Druck in Vollfarbe.
Vorteile | Nachteile |
|
|
|
|
|
|
Überblick der additiven Fertigungsverfahren
Mit der Technologie des 3D-Drucks entwickelten sich stetig neue Verfahren, um diese für bestimmte Anwendungsfelder nutzen zu können. Die einzelnen Methoden unterscheiden sich in ihrer Technik teilweise nur marginal oder gänzlich divergent. Folgende Tabelle soll einen Überblick der einzelnen Verfahren schaffen:
Additive Fertigungsverfahren | Fused Deposition Modeling (FDM) | Stereolithografie (SLA) | Selektives Lasersintern (SLS) | Digitale Lichtverarbeitungs- technologie (DLP) | MultJet Modeling (MJM) |
Häufige Anwendungs-gebiete | – Heimbereich
– Luft-/ Raumfahrt – Medizintechnik |
– Maschinenbau
– Automobilbranche – Medizin |
– Werkzeugbau
– Zahnmedizin – Luft-/Raumfahrt |
– Zahnmedizin
– Juwelierbranche – Modellbau |
– Maschinenbau
– Modellbau – Elektrotechnik |
Genauigkeit | •• | ••••• | •••• | ••••• | ••••• |
Material | – Kunststoff | – Photopolymere | – Pulvermaterialien
(z.B. Alumide, Polyamide, Nylon) |
– Photopolymere | – Photopolymere
– Wachs |
Pro | – sehr robust
– bunte Filamente |
– glatte Oberfläche
– geringer Nachbearbeitungs- aufwand |
– vielfältige Werkstoffe
– hohe Festigkeit |
– sehr schnell
– kompakte Bauform |
– die Kombination mehrerer Werkstoffe ist möglich
– geringer Nachbearbeitungs- aufwand |
Contra | – nicht temperaturbeständig
– raue Oberfläche |
– nicht robust
– nicht lichtbeständig |
– hoher Energiebedarf
– Oberflächen- beschaffenheit materialabhängig |
– aufwändiges Entfernen der Stützkonstruktion
– nicht lichtbeständig |
– hohe Materialkosten
– limitierte Materialvielfalt |
Anwendungsgebiete in der Industrie 4.0
In einer von Digitalisierung geprägten Zeit werden Produktionsprozesse immer effizienter und flexibler. Im „Internet der Dinge“ kommunizieren Maschinen, Werkzeuge und sogar Werkstücke miteinander und optimieren dadurch selbstständig den gesamten Herstellungsvorgang. Die weitgehende Verschmelzung von Fertigungstechnik und IT führt auch zu einem Zusammenwachsen aller beteiligten Parteien – von der Auftragsverwaltung bis hin zur Distribution. Für den Endverbraucher eröffnet diese Technologie ganz neue Möglichkeiten. Individualisierung von Produkten bis hin zur wirtschaftlichen Einzelanfertigung sind Errungenschaften, welche mit Industrie 4.0 einhergehen. Unternehmen sind jedoch angewiesen, die Frage der Fertigungstiefe neu zu überdenken. Produkte, die gegenwärtig noch klassisch, etwa durch CNC-Maschinen entstehen, könnten alternativ möglicherweise bereits additiv hergestellt werden – entweder durch die Investition in 3D-Drucker oder die Nutzung externer Dienstleister.
3D-Drucker, beziehungsweise die additive Fertigungstechnik sind Teil dieser Revolution. Sie vereinen Produktionsgeschwindigkeit und Flexibilität. Mit ihren vielfältigen Möglichkeiten und diversen Vorteilen gegenüber subtraktiven Verfahren halten sie in zahlreichen Branchen Einzug.
Vom 3D-Scan zum medizinischen Implantat
In der Medizin breiten sich 3D-Drucker rasant aus. Wie selbstverständlich der Einsatz in Kliniken wird, berichten wir hier. Passgenaue Zahnkronen oder Hörgeräte sind keine Neuheiten mehr. Implantate und Prothesen lassen sich individuell entwickeln und herstellen. Vor der eigentlichen Entwicklung werden die Bereiche, beispielsweise das Ohr eines Patienten, mit Hilfe eines 3D-Scanners erfasst. Die daraus entstehende Punktwolke enthält hunderttausende einzelne Referenzpunkte, aus denen Software ein dreidimensionales Modell erstellt.
Des Weiteren wird der 3D-Druck dafür eingesetzt, Anschauungs- und Trainingsmodelle für Chirurgen zu erstellen. Diese können an den jeweiligen Patienten angepasst sein und den Chirurgen ermöglichen, den Eingriff noch vor der Operation am Patienten zu trainieren, beziehungsweise sich dadurch auf die Operation vorzubereiten. Übungen am Patienten oder anatomischen Körperteilen von Tieren entfallen und ethische Probleme entstehen erst gar nicht. Zusätzlich können diese anatomischen Modelle dazu dienen, dem Patienten die einzelnen Schritte der Operation zu verdeutlichen und für besseres Verständnis zu sorgen.
Momentan wird an der Herstellung von Zellstrukturen geforscht, welche durch spezielle Druckverfahren organisches Gewebe bilden können. Das längerfristige Ziel liegt in der Möglichkeit, komplette Organe mit Hilfe von sogenanntem Bio-Druck zu schaffen.
Massenware als Einzelstück
Bereits jetzt bieten viele Hersteller dem Kunden an, seine Produkte nach individuellen Wünschen zu personalisieren. Vor kurzem wäre dies noch unwirtschaftlich gewesen, doch lassen sich im 3D-Druck selbst Einzelstücke realisieren. Diese Tatsache eröffnet der Industrie völlig neue Wege. Die Produktdiversifizierung ist kein Kostenkriterium mehr, die Produktzyklen werden kürzer und die Produktion kann dezentral stattfinden. Außerdem können durch eine Just-in-Time-Fertigung sowohl Lager- als auch Transportkosten minimiert werden. Fallweise kann die Herstellung von Objekten sogar direkt beim Kunden erfolgen. Selbst branchenfremde, kleine Unternehmen können mit Technologien aus den additiven Fertigungsverfahren auf den Markt treten.
Anwendungen im Großformat
Bauteile aus Beton werden normalerweise gegossen und sind durch die notwendige Verschalung in ihren Gestaltungsmöglichkeiten sehr begrenzt. Der 3D-Druck vereint in diesem Fall die Vorteile beider Welten. Die hohe Festigkeit des Materials bei gleichzeitiger Flexibilität in der Anwendung. Nach und nach werden dünne Schichten aus Sand aufgeschüttet, welche dann mit Wasser und Zement versetzt, genau an diesen Stellen aushärten. Der überschüssige Sand wird nach dem Druckvorgang entfernt und die gedruckte Betonstruktur kommt zum Vorschein. Eine weitere Methode, Fertigteile oder komplette, wenn auch von den Abmessungen her noch sehr beschränkte, Gebäude aus Beton zu drucken, ist der direkte Druck mit Fertigbeton. Hierbei entstehen die Wände ebenso schichtweise, jedoch mit geringerer Genauigkeit.
Beide Methoden sind jedoch noch kaum praktikabel. Beispielsweise müssen Bewehrungen, Fenster und Türen meist nachträglich eingefügt werden. Aussparungen für Verkabelung und Steckdosen können vom Drucker nicht berücksichtigt werden. Zudem erfordert das Dach eine manuelle Anbringung und der Transport der riesigen Drucker birgt enormen logistischen Aufwand.
Die nächste industrielle Revolution
Der 3D-Druck und die gesamte Palette der additiven Fertigungsverfahren gehen mit der Industrie 4.0 einher und ermöglichen zum einen die Herstellung von detaillierten Objekten aus verschiedensten Materialien. Zum anderen lösen sie teilweise die subtraktive Fertigung ab, weil Werkstücke oftmals einfacher, kostengünstiger und schneller produziert werden können, wenn Material auf- statt abgetragen wird. Bislang führte die gesamte Sparte der additiven Fertigung eher ein Schattendasein und beschränkte sich vorwiegend auf Rapid Prototyping. Sie entwickelt sich aber stetig weiter und kristallisiert sich zu einer Allround-Fertigungstechnik heraus, welche in Bereichen wie Medizin, Baugewerbe, Architektur, bis hin zur Raum- und Luftfahrt Erfolge feiert. Mit einer Diversität an Materialien, angefangen bei Acryl bis hin zu Zellstrukturen aus organischem Gewebe, ergeben sich vielfältige Anwendungsfelder. Ein weiterer Vorteil liegt in der Flexibilität der Maschinen. Diese sind nahezu überall einsetzbar und ermöglichen eine unabhängige Produktion direkt vor Ort. Dadurch werden Lager- und Transportkosten auf ein Minimum reduziert.
In Zukunft wird der 3D-Druck nicht nur Industrie und Privathaushalte mit einfachen und schnellen Lösungen erfreuen. In der Raumfahrt oder an weit abgelegenen Orten könnte er überlebensnotwendig werden. Abgeschnitten von Versorgungsmöglichkeiten wären die ersten Menschen, die den Mars besiedeln, maßgeblich auf diese Technik angewiesen um Station, Raumschiff und Equipment in Schuss zu halten.
Experten sind der Meinung, dass der 3D-Druck in naher Zukunft auch in der Massenfertigung Anwendung findet. Noch verhindern die vergleichsweise längeren Produktionszeiten, die damit einhergehenden höheren Kosten, sowie die teureren Materialien diesen Wandel. Laut Prognosen zufolge soll das Marktvolumen der gesamten Sparte des Additiven Fertigungsverfahrens von aktuell 4,5 Milliarden Euro (Stand 2018) auf bis zu 7,7 Milliarden Euro im Jahr 2023 wachsen.
Andere Herstellungsverfahren wird der additive 3D-Druck noch nicht komplett ersetzen können, aber er stellt eine Bereicherung dar und eröffnet neue Möglichkeiten in der Fertigung. Komplexe Objekte mit Strukturen und Überhängen, sowie Hohlkörper aus verschiedensten Materialien können dank additiver Fertigung problemlos realisiert werden.
Lesen Sie auch:
So werden Sie zum Experten für 3D-Druck
Ein Beitrag von: