Gedruckte Photopolymere stützen heilende Knochen
Die Technische Universität Wien gründet ein neues Labor. Seine Mission: verschiedene Arbeitsgruppen zu vereinen und künstliches Knochenstützgewebe zu erforschen.
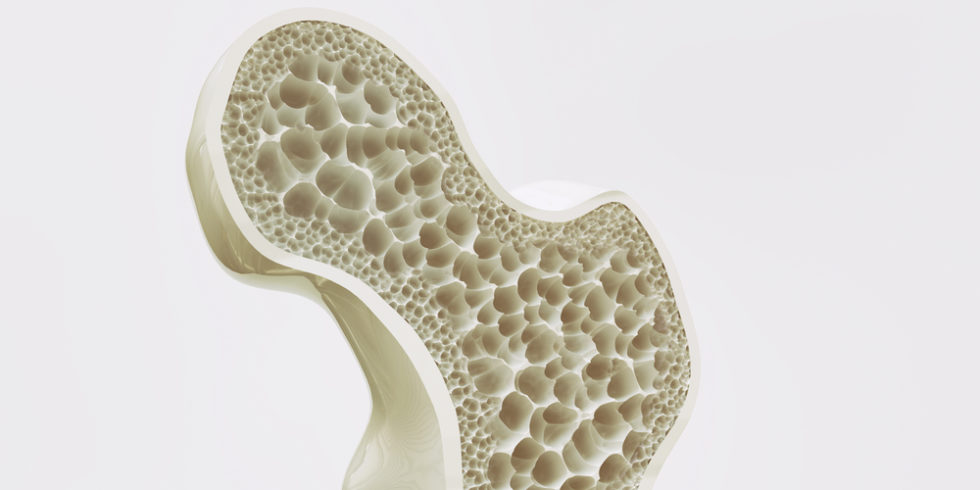
Foto: panthermedia.net/Crevis
Mit der Gründung eines Labors investiert die Technische Universität Wien in die additive Fertigung zu medizinischen Zwecken. Der Fokus liegt dabei auf Knochenersatz-Implantaten, die vom Körper abgebaut werden und über die Zeit hinweg natürlichem Gewebe weichen. Förderung erhält die TU Wien dabei vom österreichischen Bundesministerium für Digitalisierung und Wirtschaftsstandort sowie von Partnern aus der Wirtschaft.
Das neugegründete Christian-Doppler-Labor Advanced Polymers for Biomaterials and 3D Printing vereint mehrere Forschungsgruppen der TU Wien, die gemeinsam an Knochenersatz-Implantaten aus additiver Fertigung arbeiten werden. Diese sollen Unfallopfern schneller wieder auf die Beine helfen. Zu den Beteiligten gehören auch Spezialisten im Bereich der additiven Fertigung, die hauseigene 3D-Druckverfahren entwickeln.
Knochen – ein aktives Material
Doch bevor die Forscher Patienten Stützen einbauen können, müssen sie zunächst die Eigenschaften des menschlichen Knochen berücksichtigen. Bei der Arbeit am menschlichen Skelett stehen die Forscher vor ganz eigenen physiologischen Herausforderungen.
Stefan Baudis vom Institut für Angewandte Synthesechemie der TU Wien und Leiter des neuen Labors, erklärt: „Einen Knochen darf man sich nicht wie ein starres, lebloses Objekt vorstellen. Ununterbrochen werden die Knochen in unserem Körper von bestimmten Zellen abgebaut und von anderen Zellen gleichzeitig wiederaufgebaut. Daher können Knochenbrüche ganz von selbst wieder verheilen.“ Mediziner sprechen in diesem Kontext auch von Knochengeweberemodellierung. Innerhalb von zehn Jahren oder weniger synthetisiert jeder Mensch seine komplette Knochenmasse neu. Essenziell für diese Aufgabe seien auch Blutgefäße, die das „Baumaterial“ anliefern.
Die Materialwissenschaftler beschäftigen sich mit der richtigen Beschaffenheit des Stoffes, der dem Patienten implantiert werden soll. Dieser muss stabil genug sein, um Belastungen standzuhalten, aber gleichzeitig muss er porös sein. Nur so kann sichergestellt werden, dass Zellen des Patienten den Kunstknochen mit der Zeit durchsetzen und an seiner Statt biologische Knochengewebe erstellen. Zusätzlich muss der Werkstoff kurzfristig biologisch abbaubar sein und Kalziumphosphate beinhalten, die Starthilfe geben. Ziel des Implantats ist es, den Knochen des Patienten ein Gerüst zu bieten und nicht dauerhaft als Prothese zu fungieren. Am Ende des Heilungsprozesses soll vom Kunstknochen nichts übrig sein und es soll nur noch Echtknochen bestehen.
Das Skelett aus der 3D-Drucker-Düse
Knochenersatz-Implantate benötigen eine genaue Passform, die sich am individuellen Körperbau des Patienten orientiert. Nach Mustern gefertigte Massenware eignet sich schlichtweg nicht. Die Forscher richten den Blick daher auf die additive Fertigung, die durch moderne Software in der Lage ist, das passende „Bauteil“ maßzuschneidern. Die Fraktur am Knochen des Patienten lasse sich laut Baudis heute sehr genau vermessen. Die TU Wien nutzt bildgebende Verfahren, um exakt zu berechnen, welche Form das synthetische Knochengerüst haben muss. Bei einer Operation müsste der Mediziner das additiv gefertigte Teil dann nur noch anbringen und fixieren.
Um die Knochengerüste zu drucken, gelten wiederum weitere Anforderungen an das Material: Vor dem Einsatz muss es bei Raumtemperatur flüssig sein, nach Bestrahlung durch Licht einer spezifischen Wellenlänge jedoch erhärten – die sogenannte Polymerisation. Baudis und seine Arbeitsgruppe nutzen dazu Photopolymere auf Methacrylat-Basis.
Baudis gibt sich trotz der vielen erschwerenden Faktoren zuversichtlich: „Wir wissen bereits viel über die Chemie der einzelnen Komponenten, die dafür nötig sind. Nun forschen wir an den passenden Materialgemischen, mit denen sich all diese Anforderungen erfüllen lassen.“ Der Fertigungsvorgang selbst dauert einige Stunden.
3D-Druck im medizinischen oder biologischen Sektor ist bereits seit längerem Objekt starker Forschungstätigkeit. Neue Verfahren könnten künftig ganze Organe nachbilden. Die Fraunhofer-Gesellschaft etwa hat auch Knochenstützen additiv gefertigt, jedoch aus Biotinte auf Basis von Biopolymeren wie Gelatine. Die Forscher des Laserzentrums Hannover fertigen Cochlea-Implantate für Hörgeschädigte additiv. Auch Zahnersatz könnte bald vornehmlich aus dem Drucker kommen.
Ein Beitrag von: