Wasserstoff-Bagger, MiC-4.0-Bus, kontinuierlicher Tunnelbau, CPC-Bauelemente und Tiefseebergbauprojekt ausgezeichnet
Insgesamt 133 Einreichungen waren diesmal eingegangen, 41 Finalisten schafften es in die nächste Runde. Nun wurden in den fünf Kategorien des Bauma-Innovationspreises die Gewinner ausgezeichnet.
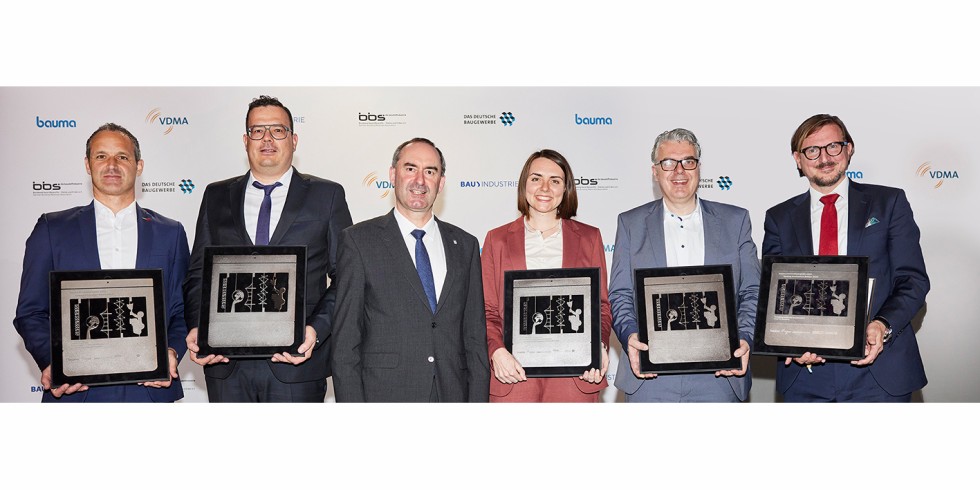
Bayerns Wirtschaftsminister Hubert Aiwanger (ohne Trophäe) zeichnete am Vorabend der Messe Bauma die Gewinner des Bauma-Innovationspreises aus. Auf dem Foto von links Benjamin Künstle (Liebherr France SAS), Prof. Matthias Flora (Herrenknecht), Katharina Schick (Liebherr und als Repräsentantin von MiC 4.0), Thorsten Hahn (Holcim), Prof. Martina Sobczyk (TU Bergakademie Freiberg).
Foto: VDMA
Bereits zum dreizehnten Mal bewarben sich zahlreiche Unternehmen und Institute aus dem In- und Ausland um die Auszeichnung in fünf Kategorien im Rahmen der Weltleitmesse Bauma in München. Nach einem mehrstufigen Auswahlverfahren konnten am 23. Oktober 2022 im Max-Joseph-Saal der Münchner Residenz fünf Sieger ihren Preis in Empfang nehmen.
Die Gewinner des Bauma-Innovationspreises 2022
Hier die Übersicht über die Gewinner der fünf Kategorien. Mehr Details finden Sie in den anschließenden Kapiteln:
- Klimaschutz: Liebherr France SAS mit seinem Raupenbagger mit Wasserstoffmotor.
- Digitalisierung: MiC 4.0 Machines in Construction mit einer einheitlichen digitalen Sprache für Baustellen,
- Maschinentechnik: Herrenknecht AG mit dem kontinuierlichen Vortrieb,
- Bauen: Holcim (Deutschland) GmbH mit vorgespannten CPC-Betonelementen,
- Forschung: TU Freiberg Institut für Maschinenbau mit dem Deep Sea Sampling.
1) Wasserstoff-Raupenbagger mit deutlich reduzierten Schadstoffemissionen
Der R 9H2 ist der erste von einem Wasserstoffverbrennungsmotor angetriebene Liebherr-Bagger. Der Einsatz eines Wasserstoffmotors ermöglicht nach Angaben des Unternehmens eine bedeutende Reduzierung der CO2-Emissionen sowie einfache und schnelle Betankung. Dabei zeigt der Liebherr-Wasserstoffmotor keine Leistungsdifferenz zu einem mit Diesel betriebenen Verbrennungsmotor. Der H2-Antrieb des Raupenbaggers bedarf keiner permanenten Energieversorgung und verursacht nur sehr geringe NOx– und CO2-Emissionen: In Abhängigkeit vom jeweils angewandten Bewertungsverfahren und davon, ob der gesamte Lebenszyklus der Maschine berücksichtigt wird, kann der Wasserstoff-Verbrennungsmotor die CO2-Emissionen bei der Betrachtung „Tank to Wheel“ (vom Tank bis zum Rad) um fast 100 % oder beim „Cradle to Grave“-Prinzip (von der Wiege bis zur Bahre) um 70 % reduzieren.
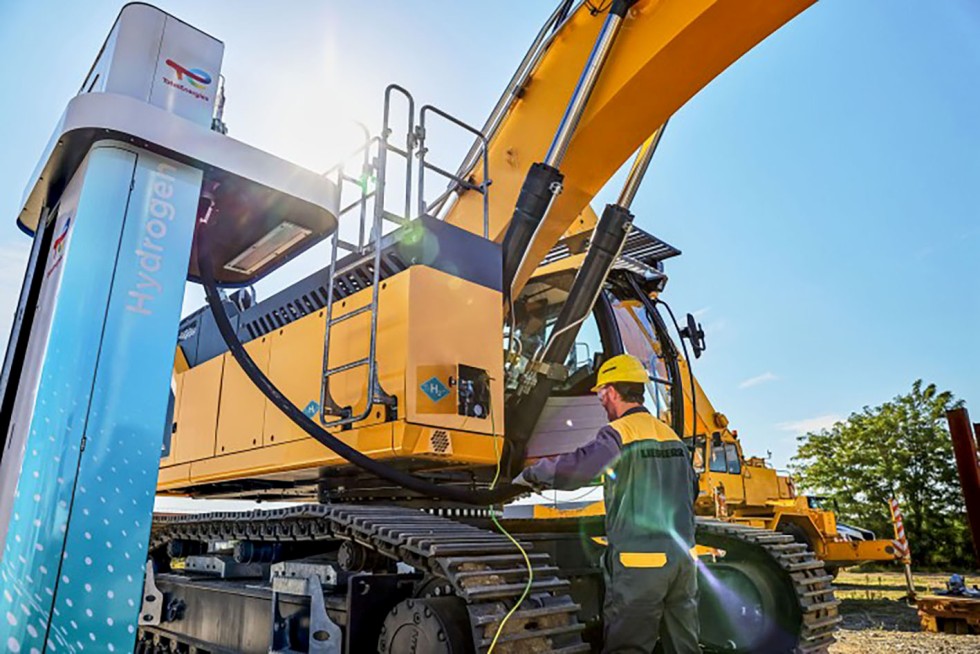
Für eine schnelle und sichere Betankung des Raupenbaggers mit Wasserstoffmotor sorgt eine Infrarotkommunikation zwischen dem Bagger und der Tankstelle über ein standardisiertes Hochgeschwindigkeitsprotokoll.
Foto: Liebherr
2) Der MiC-4.0-Bus: Plug-and-Play-Verbindung für Baumaschinen und ihre Anbaugeräte
Im Cluster 7 – Anbaugeräte – der Arbeitsgemeinschaft Machines in Construction MiC 4.0 wird ein Standard für die herstellerübergreifende Kommunikation zwischen Anbaugerät und Baumaschine entwickelt. Das Ziel ist nicht, die vorhandenen mechanischen, hydraulischen oder elektrischen Schnittstellen zwischen Anbaugerät und Baumaschine zu vereinheitlichen, sondern ein universelles, einheitliches und herstellerunabhängiges Daten-Interface zwischen Baumaschine und Anbaugerät zu schaffen. Durch die Zusammenarbeit von über 25 Anwendern, Maschinen und Werkzeugherstellern wird unter dem Namen „MiC 4.0 Bus“ eine Datenschnittstelle via CAN-Bus definiert, die alle relevanten Anwendungsfälle für die Kommunikation zwischen Werkzeug und Maschine abbilden kann.
Dazu zählt die Identifizierung des Werkzeugs beim Ankoppeln, sodass Informationen wie Seriennummer, Werkzeugtyp und Hersteller an die Maschine übermittelt werden und für Auswertungen zum Einsatz von Maschine und Werkzeug zur Verfügung stehen. Anschließend kann auf Basis der Informationen, wie zum Beispiel dem erforderlichen Hydraulikdruck, die Baumaschine automatisch auf das Werkzeug eingestellt und die Maschinenbediener entlastet sowie Fehlbedienung vermieden werden. Der MiC-4.0-Bus sieht auch die Übertragung von Steuerdaten vor, sodass die Bedienung möglichst einfach und übersichtlich ist. Durch die Übertragung von Geometriedaten können Assistenzsysteme, wie z.B. Arbeitsraumbegrenzung, automatisch mit korrekten Daten arbeiten und die Bediener so bei ihrer Arbeit unterstützen.
Im Rahmen von Proof-of Concept-Tests wurde der MiC-4.0-Bus im April 2022 bereits an Prototypenmaschinen und Anbaugeräten verschiedener Hersteller erprobt. Auf der Bauma 2022 wird ein Demonstrator gezeigt. Im Anschluss an die Messe soll der MiC-4.0-Bus veröffentlicht und so weiteren Unternehmen zur Verfügung gestellt werden, mit dem Ziel zum Standard in der Kommunikation zwischen Werkzeug und Baumaschine zu werden.
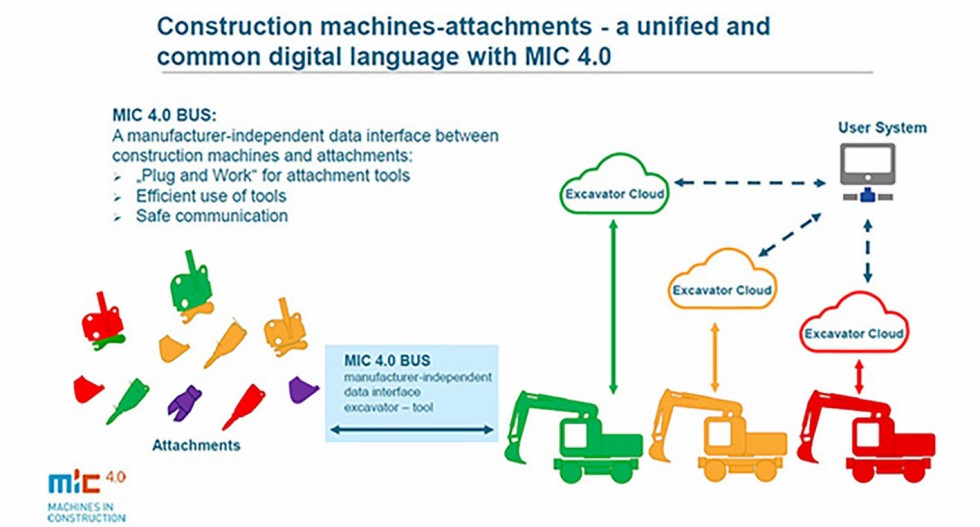
Maschinenbediener werden durch den MiC-4.0-Bus entlastet, da die Ansteuerung der Werkzeuge vereinfacht wird und zusätzliche Bedienelemente und Displays, wie sie heute üblich sind, entfallen können.
Foto: Machines in Construction MiC 4.0
3) Kontinuierlicher Vortrieb beim Tunnelbau
Ein kontinuierlicher Vortriebsprozess, bei dem der Ringbau und das Vorwärtsbohren synchronisiert werden, kann zu einer erheblichen Einsparung von Bauzeit gegenüber dem klassischen Stop-and-Go-Prozess (Vorbohren des Tunnels und der Einbau der Tübbingsegmente) beitragen. Hierfür konzipierten die Ingenieure von Herrenknecht ein für alle gängigen Softground-Konstellationen geeignetes Verfahren, also für weiche Baugrundformationen mit und ohne wasserführende Schichten.
Im kontinuierlichen Vortrieb übernehmen diejenigen Vortriebszylinder, die die Maschine nach vorne zum Bohren schieben, den Kraftanteil derjenigen Zylinder, die für den Ringbau zurückgezogen sind. Damit unter diesen Bedingungen die Maschine ihre Steuerrichtung sicher beibehält, muss der Druckschwerpunkt aus der Summe der vortreibenden Kräfte in seiner Lage unverändert bleiben. Im Mittelpunkt des kontinuierlichen Vortriebs stehen daher eine leistungsfähige Rechnerarchitektur und verfahrensspezifische Software-Programme, die die nötigen Drücke in den Vortriebszylindern präzise kalkulieren. Sie gewährleisten, dass der Maschinenfahrer die Tunnelvortriebsmaschine wie bisher zuverlässig auf der vorgegebenen Trasse steuern kann.
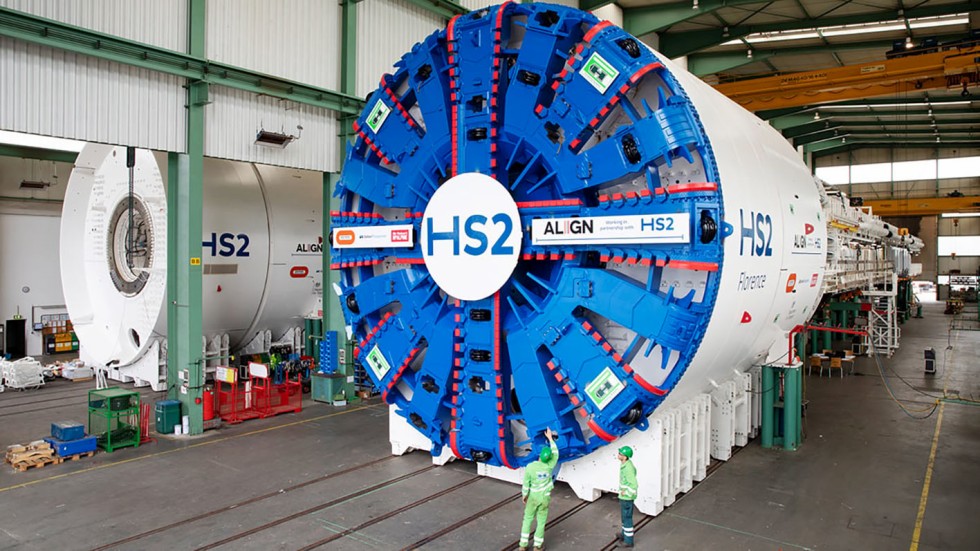
Mit dem Funktionsprinzip des kontinuierlichen Tunnelvortriebs kann gegenüber dem bisherigen diskontinuierlichen Verfahren eine Steigerung der Gesamtvortriebsleistung bis zu einem Faktor von 1,6 erreicht werden. Das Verfahren des kontinuierlichen Vortriebs wird beim Großprojekt High Speed 2 – eine neue Eisenbahnverbindung zwischen London und Birmingham – eingesetzt.
Foto: Herrenknecht
4) Betonbauteile aus CPC (Carbon Prestressed Concrete)
Statt wie gewöhnlich mit Stahl wird der Beton von CPC-Platten ausschließlich mit vorgespannten Carbonfasern bewehrt. Die leistungsfähigen dünnen Betonplatten ermöglichen dadurch je nach Konstruktion Material-Einsparungen von bis zu 80 Prozent und reduzieren den CO2-Fußabdruck des Bauteils um bis zu 75 Prozent. Die geringere Betonmenge reduziert die Eigenlast des Bauwerks massiv und auch der Transportaufwand sinkt deutlich. Die dünnen Elemente lassen sich industriell und großformatig fertigen und anschließend auf Maß zuschneiden. Neben einfachen sind auch frei geformte Zuschnitte, Oberflächenbearbeitungen wie Fräsen und Bürsten, Bohrungen, Schlitzfräsungen oder Taschen möglich.
Entwickelt wurden die CPC-Platten von der Schweizer CPC AG. Holcim Deutschland bzw. das Tochterunternehmen Vetra Betonfertigteilwerke GmbH kooperiert mit dieser bei der Markteinführung und optimiert sie weiter im Design (z.B. über die Betontechnologie und die Zusammensetzung). In Essen bei Oldenburg (Niedersachsen) entsteht eine Großanlage für CPC-Platten, die noch 2022 die Produktion starten wird. Die CPC AG liefert die Technologie und die Carbonfasern, für deren Produktion in der Schweiz ein neues Werk aufgebaut wurde.
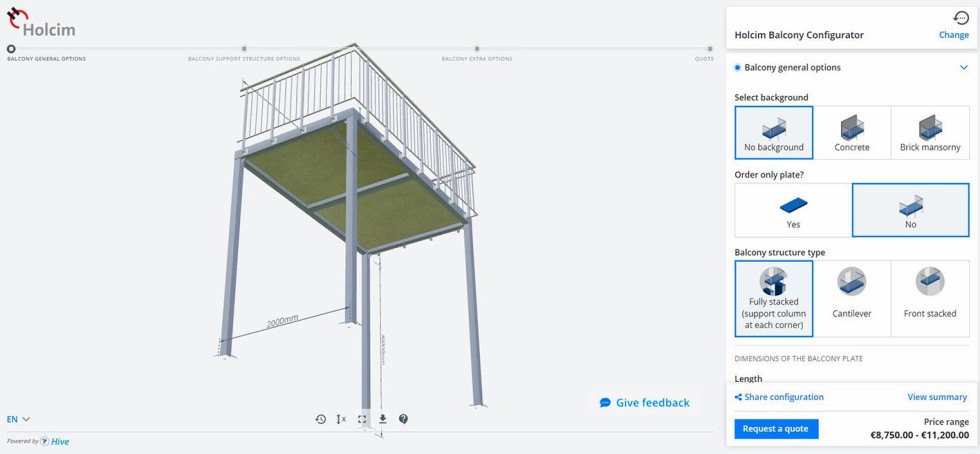
Die Konfiguration der CPC-Bauelemente wird im Internet unterstützt (hivecpqpublic.com/#/codes/AC93BD1B).
Foto: VDI Fachmedien / K. Klotz
5) Exploration und nachhaltiger Abbau von Massivsulfiden
Das vom Bundesministerium für Wirtschaft und Klimaschutz (BMWK) geförderte Verbundprojekt Deep Sea Sampling beschäftigt sich mit dem Erschließen neuer Rohstofflagerstätten in der Tiefsee (ab 2000 m unter dem Meeresspiegel), wo Wasserdrücke von bis zu 400 bar, komplette Dunkelheit und Temperaturen um 1° C herrschen. „Für die Exploration und den späteren nachhaltigen Abbau von Massivsulfiden in der Tiefsee gibt es einen sehr vielversprechenden Ansatz auf Basis der Fräsentechnik, wie sie im Spezialtiefbau schon lange erfolgreich angewandt wird“, erläutert Dr. Matthias Semel, Verbundkoordinator für das Komplettprojekt von der Bauer Maschinen GmbH.
Verbundpartner sind darüber hinaus die TU Bergakademie Freiberg mit ihrem Institut für Aufbereitungsmaschinen und Recyclingsystemtechnik sowie dem Institut für Maschinenbau, die Universität Rostock, die FAU Erlangen-Nürnberg sowie die Krebs & Aulich GmbH. Die Bundesanstalt für Geowissenschaften und Rohstoffe (BGR) wie auch die Deep Sea Mining Alliance (DSMA) sind zudem im projektbegleitenden Ausschuss vertreten.
2021 erfolgte der Startschuss des auf drei Jahre angelegten Forschungsprojekts. Ziel ist es, anstelle eines flächigen Ansatzes zur Gewinnung der Rohstoffe eine kompakte Schlitzwandfräse zu elektrifizieren und zu einer smarten, teilautonomen vertikalen Bergbaueinheit zu transformieren. „Diese Einheit separiert und charakterisiert das gewonnene Material während des Abbauvorgangs direkt am Meeresboden“, so Dr. Semel weiter. Dadurch soll nicht nur ein minimalinvasiver, effizienter Ressourcenabbau sichergestellt, sondern auch entstehende Trübewolken durch das Arbeiten in einem geschlossenen, abgeschirmten Prozess eingefangen werden.
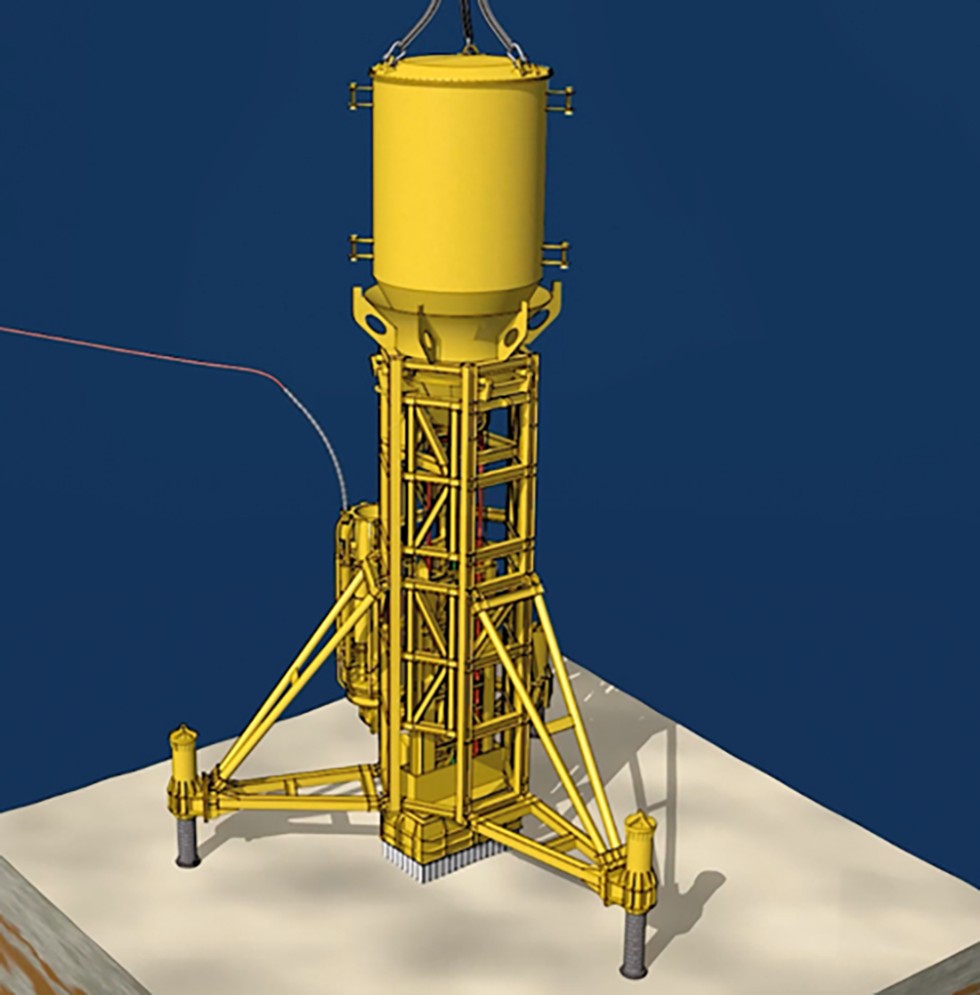
Der Einsatz einer elektrisch betriebenen, vertikalen Bergbaueinheit zielt auf einen minimalinvasiven Ressourcenabbau in der Tiefsee ab.
Foto: Bauer Gruppe
Die Nominierten für den Bauma-Innovationspreis 2022
Für den Bauma-Innovationspreis 2022 nominiert waren – außer den Gewinnern – folgende Bewerbungen:
Kategorie 1: Klimaschutz
- Revoc-System – Katalysator für Asphaltmischanlagen (Benninghoven – Branch of Wirtgen Mineral Technologies GmbH)
- Minus CO2-Baumaterialien – regenerativ, besser, billiger (Carbonauten GmbH)
Kategorie 2: Digitalisierung
- Haptische Kollisionsvermeidung (Bosch Rexroth)
- Mesh-Technologie (Mesh)
Kategorie 3: Maschinentechnik
- Ammann 3D Compactor eAPX 68/95 (Ammann Verdichtung)
- Built Robotics Exosystem (Built Robotics)
Kategorie 4: Bauen
- Prozess-Erfassungssystem b.navigate (Bauer Spezialtiefbau)
- TSB (Transport System Bögl) – Nahverkehr neu gedacht (Max Bögl)
Kategorie 5: Forschung
- Robeton, Individualisierte Bauproduktion (RWTH Aachen University)
- Site Execution System (TU Dresden – Institut für Mechatronischen MaschinenbauDesign)
Empfehlung der Redaktion – das könnte Sie auch interessieren:
- Nichts mehr verpassen: Hier geht‘s zur Anmeldung für den Bauingenieur-Newsletter…
- Wichtige Abkürzungen aus der Baubranche
- Spezialtiefbau: Bauer forciert Digitalisierung der Baustelle – und hofft auf Bauma-Innovationspreis
- Bauma 2022: Wasserstoff- und Elektro-Baumaschinen rollen an
- Deutscher Ingenieurbaupreis 2022: Carbonseilbrücke gewinnt Staatspreis
- Industriebau: Holzbaupreis für Halle mit weltgrößtem Dachtragwerk