Bohren statt rammen
Großrohre gelten als die wirtschaftlichste Fundamentlösung für Windparks auf See. Ein Problem bleibt aber der Rammschall. Der Tunnelbauer Herrenknecht und Hochtief Solutions wollen in Zukunft das Rammgeschirr gegen einen Bohrkopf tauschen. Das Errichten der Fundamente soll so schneller, preiswerter und umweltverträglicher werden.
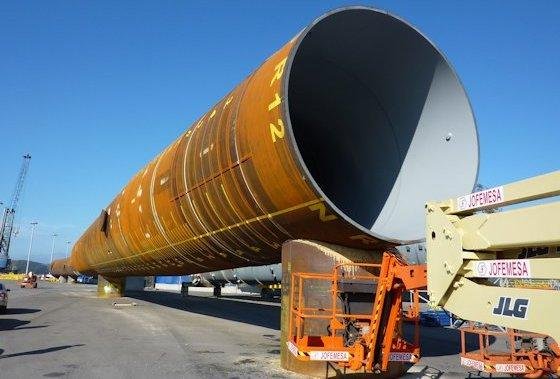
Monopile für Offshore-Windkraftanlage: Großrohre erreichen inzwischen Durchmesser von über 6 m und Längen von 70 m.
Foto: EWE
Monopiles, Fundamente mit nur einem Rohr als Fuß, rangieren in der Gunst ganz oben, wenn es darum geht, Windkraftanlagen auf See zu errichten. Erlauben es die Wassertiefen und Bodenverhältnisse, dann sind Großrohre erste Wahl bei Betreibern. Sie lassen sich weitgehend automatisiert herstellen, in beträchtlichen Stückzahlen produzieren und wie am Fließband rammen.
Allerdings war ihr Einsatzradius bisher auf Wassertiefen von 20 m limitiert, da es kaum vorstellbar war, große Rammrohre herzustellen, auf denen sich Multimegawatt-Anlagen in großen Wassertiefen errichten lassen. Dieses Feld sollten bisher aufwendigere und teure Speziallösungen wie die zweifüßigen Jackets oder die dreifüßigen Tripods bestellen.
Einsatzradius erweitert
Inzwischen wendet sich das Blatt, die Hersteller von Monopiles legen ordentlich nach. Üblich sind 800 t schwere und 70 m lange Piles mit Durchmessern von bis zu 6,5 m. Solche Kaliber – Gesamtgewicht rund 70 000 t – lässt zurzeit Vattenfall im Nordseewindpark Dan Thysk in den Boden rammen. Die Wassertiefen liegen dort schon bei bis zu 32 m.
„Es gibt für Monopiles noch Spielraum und leistungsfähige Kranschiffe, die mit solchen Rammpfählen umgehen können. So etwas hätte man vor ein paar Jahren kaum für möglich gehalten. Jetzt sind in Abhängigkeit von der Geologie des Meeresbodens Wassertiefen von vielleicht 35 m drin, bevor man auf Jackets oder Tripods zurückgreift“, sagt Christoph Mertens, Geschäftsführer von Dong Energy Renewables Germany.
Dillinger Hütte baut Tochterunternehmen Steelwind auf
Wo die Reise hingeht, machen die Hersteller klar. Sie wollen gegenüber aufgelösten Strukturen kostenneutral sein oder durch Automation sogar billiger werden. Als neuer Player für XXL-Piles empfiehlt sich die Dillinger Hütte am Markt. Zurzeit baut der Stahlkocher das Tochterunternehmen Steelwind im niedersächsischen Nordenham auf.
„Solche Rohre fertigt noch niemand. Wir richten uns in der Nordsee auf Wassertiefen von 30 m bis 35 m ein. Das wären dann Rammrohre mit Wandstärken von 120 mm bis 130 mm und Stückgewichten von gut 1000 t. Der Durchmesser kann mit maximal 8,5 m perspektivisch so groß sein, dass Piles auch Windenergieanlagen mit 6 MW oder 7,5 MW tragen“, sagt Dieter Sichau, Geschäftsführer von Steelwind.
Derlei mächtiger Stahl stelle weder die Walzenbiegemaschinen noch die Schweißtechnik vor Probleme, so Stahlfachmann Sichau. Die gibt es bei den Durchmessern aber mit dem Rammgerät und vor allem mit dem enormen Schallpegel beim Rammen.
Enormer Schallpegel beim Rammen
Bisher mühen sich die Akteure mehr schlecht als recht, die Vorgaben des Bundesamtes für Seeschifffahrt und Hydrographie (BSH) aus Hamburg einzuhalten. Andernfalls – so befürchten Behörden, Wissenschaftler und Umweltverbände – könnte der Schalldruck Auswirkungen auf die marine Tierwelt und vor allem auf die lärmempfindlichen Schweinswale haben.
Bisher setzt man zu deren Schutz auf zusätzliche Hüllrohre, die über das Pile gestülpt werden, und auf Blasenschleier, deren Luftteppiche schallmindernd wirken. Diese Maßnahmen kosten die Betreiber eine Stange Geld und „trotzdem hält keiner dauerhaft den Grenzwert ein“, sagt Christian Dahlke vom BSH. Es werde zwar besser, aber alle Techniken seien nach wie vor zu laut.
„Bei den eher kleineren Rammpfählen für Jackets oder Tripods ist es zwar leiser, aber dafür dauert das Rammen sehr lange. Bei Monopiles ist es genau anders herum. Darum sind sie unser Sorgenkind“, weiß Dahlke. Bei XXL-Piles würde sich die Lage noch verschärfen. Für größere Rohrdurchmesser ist mehr Rammenergie erforderlich und das erhöht wiederum den Schallpegel.
„Die Impulsenergie des Hammers löst starke Biege- und Dehnmomente im Rohr aus und die dabei auftretende Kompression breitet sich unter Wasser mit Schallgeschwindigkeit aus“, erklärt Manfred Schultz-von Glahn, Geschäftsführer des Instituts für technische und angewandte Physik (itap) in Oldenburg.
BMU unterstützt Projekt
Diesen Lärm wollen die Herrenknecht AG und die Hochtief Solution AG mit der Offshore Foundation Drilling Machine (OFD) abstellen. Von den 19 Mio. € Projektkosten tragen beide Unternehmen zusammen 14 Mio. €, den Rest das Bundesumweltministerium. Während Steelwind das erste Großrohr liefern will und Hochtief für die Umsetzung auf See verantwortlich ist, hat Herrenknecht das marine Bohrverfahren ausgetüftelt.
Als Basis der OFD dient die von Herrenknecht entwickelte automatische Schachtabsenkung. „Wir bauen gerade den ersten Prototypen und wollen die OFD Ende des Jahres in Bremerhaven testen. Das aktuelle Design ist auf Pfahldurchmesser von 7,5 m und Wassertiefen von 80 m ausgelegt. Weil diese großen Piles konisch verjüngt sind, lässt sich der maximale Radius des Bohrkopfes auf 4,5 m einfahren“, sagt Marc Peters, Leiter der Forschungs- und Entwicklungsabteilung Tunnelbau bei Herrenknecht.
In der Praxis sollen die Piles zunächst vom Deck aus abgesenkt werden und einige Meter in den Meeresboden eindringen. Danach wird der Bohrkopf in das
Pile eingeführt. Er unterschneidet das Rohr bei jedem Bohrvorgang einmal um 360° und bringt es so scheibchenweise auf Solltiefe. Der dabei entstehende Aushub wird zunächst durch Kreiselpumpen auf ein Schiff gefördert und anschließend wieder zum Verfüllen des
Piles verwendet.
Komplettes Fundament soll in zwei Tagen stehen
In den Simulationen wird davon ausgegangen, dass ein komplettes Fundament in maximal zwei Tagen steht. „Wir mussten das System an die marinen Bedingungen anpassen, es ausfallsicher machen und das Bohrverfahren beschleunigen. Schließlich geht das Rammen sehr schnell und offshore sind die Kosten hoch“, so Peters.
Wenn die Maschine funktioniert, dann hätte das Verfahren mehrere Vorteile. Weil durch den variablen Radius des Bohrkopfes immer unter dem Rohr gebohrt werden kann, stellen dicke Findlinge oder Gesteinsschichten laut Herrenknecht kein Hindernis dar. Damit arbeitet das System unabhängig von geologischen Strukturen und es soll vor allem leise sein.
Erste Simulationen mit dem itap kommen auf Schallwerte für das OFD von 117 dB. Damit würden nicht nur das Rammgeschirr und der aufwendige Schallschutz entfallen, sondern auch die Übergangsstücke zwischen Pile und Anlage. Diese „Transitions Pieces“ genannten Komponenten sind bisher notwendig, um die beim Rammen auftretende Schiefstellung der Rohre auszugleichen. Dafür müssen beide Bauteile zusätzlich mit flüssigem Spezialbeton verklebt werden. „Wir sind sicher, dass die Vertikalmaschine absolut lotrecht bohrt. Dann reicht ein einfacher Verbindungsflansch auf dem Rohr“, ist sich Tunnelbauexperte Peters sicher.
Ein Beitrag von: