Kalksandstein nimmt CO2 auch wieder auf
Baustoffe aus nachwachsenden Rohstoffen gelten in der öffentlichen Wahrnehmung als besonders nachhaltig, auch weil sie Kohlendioxid binden können. Allerdings können das auch Baustoffe wie Kalksandstein durch einen Mechanismus, der über Jahre abläuft. Ihre Klimabilanz lässt sich darüber hinaus durch den Einsatz von erneuerbaren Energien bei der Produktion verbessern und durch Recycling.
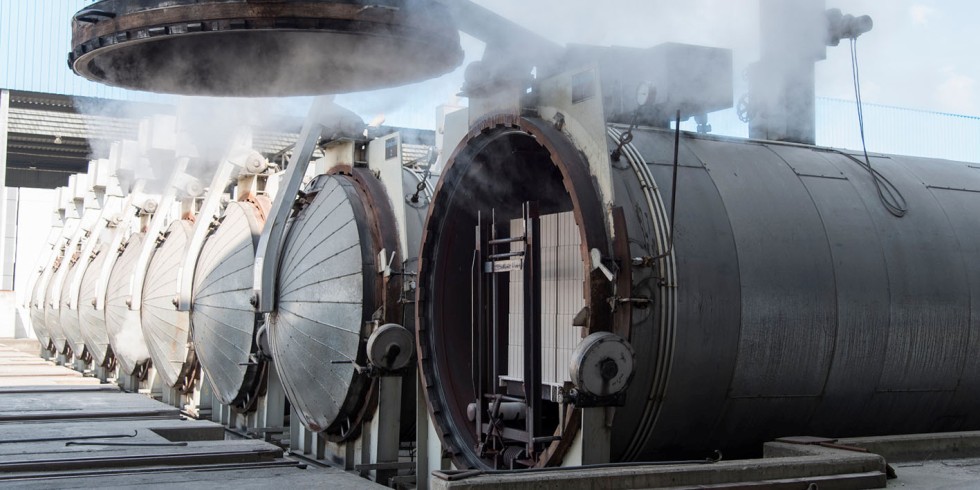
Die Autoklaven zur Dampfhärtung von Erdgas auf grünen Strom umzustellen, ist technisch möglich. Ohne Investitionsförderung wird die Transformation allerdings für die meisten Unternehmen nicht finanzierbar sein.
Foto: Bundesverband Kalksandsteinindustrie
Um die Aufnahmefähigkeit von Kalksandstein für CO2 zu bestimmen, hat Prof. Dr. Bernhard Middendorf, Leiter des Fachgebiets Werkstoffe des Bauwesens und Bauchemie am Fachbereich Bauingenieur- und Umweltingenieurwesen an der Universität Kassel, Zeitraffer-Versuche mit frisch hergestellten Kalksandsteinen und historischen Steinen unternommen. Es zeigte sich, dass die CSH-Phasen (siehe Kasten) des Baustoffs zu ca. 90 Prozent carbonatisiert wurden, indem sie Kohlendioxid aus der Luft aufnahmen.
Das Potenzial der Kalksandsteine schätzt Middendorf auf 50 kg CO2 pro Tonne, also etwa 40 Prozent der etwa 125 kg CO2 pro Tonne, die Kalksandstein laut der aktuellen Umweltdeklaration (EPD) bei seiner Herstellung freisetzt. „Wenn ein Teil der bei der Herstellung entstehenden Kohlendioxid-Emissionen kompensiert wird, verbessert dies die Ökobilanz,“, betont Middendorf, der auch Mitglied im wissenschaftlichen Beirat der Forschungsvereinigung Kalk-Sand e.V. ist.
Es habe sich auch gezeigt, dass das aufgenommene Kohlendioxid chemisch dauerhaft in das kristalline Gefüge der Kalksandsteine eingebunden wird und dabei die Festigkeit von Kalksandstein erhöht.
Die erwähnten 50 kg CO2 pro Tonne nimmt Kalksandstein laut der Forschungsarbeit innerhalb der ersten 50 Jahre auf; danach kann er nur noch marginale Mengen binden. „Anstriche und Putze verlangsamen die natürliche Carbonatisierung, verhindern sie aber nicht gänzlich“, sagt Middendorf. „Es kommt dabei immer auf die Dampfdichtigkeit der Beschichtung an.“
Zusammensetzung des CO2-Fußabdrucks
Nur rund 20 Prozent des CO2-Fußabdrucks von Kalksandstein entsteht in der eigentlichen Produktionsphase und den Lieferketten der Kalksandsteinindustrie. Der restliche Anteil stammt aus der Produktion des Bindemittels Kalk, das für die Herstellung von Kalksandstein essenziell ist. „In den letzten Jahren ist es durch Produktionsoptimierungen gelungen, den Kalkanteil kontinuierlich zu senken“, argumentiert Roland Meißner, seit 2013 Geschäftsführer beim Bundesverband Kalksandsteinindustrie e.V. „Parallel dazu erforschen wir fortlaufend neue Rezepturen mit CO2-ärmeren Kalken und den Einsatz alternativer Bindemittel.“
Mehr erneuerbare Energie für die Produktion
Da ansonsten vor allem die Menge und Art der bei seiner Herstellung eingesetzten Energie die Klimabilanz von Kalksandstein beeinflusst, richtet sich der Blick auf erneuerbare Energien. „Derzeit scheint die Umstellung auf grünen Strom für unsere Branche der sicherste Weg in die klimaneutrale Zukunft zu sein“, sagt Jan Dietrich Radmacher, der Vorstandsvorsitzende des Bundesverbands Kalksandsteinindustrie e.V. „Auch weil wir die notwendige Energie mit Windkraft- oder Photovoltaikanlagen auf unseren Werksgeländen zumindest teilweise selbst erzeugen können.“
Kostspielige Anlagentechnik für Autoklaven
Wasserdampf für die Autoklaven elektrisch zu erzeugen ist im Prinzip machbar, allerdings muss die entsprechende Anlagentechnik erst noch entwickelt werden. „Das wird einige Jahre dauern und sicherlich kostenintensiv sein“, sagt Radmacher. „Ich rechne mit mehreren Millionen Euro pro Anlage. Das könnte vor allem für kleinere Betriebe problematisch werden.“ Ohne eine Investitionsförderung in einer Größenordnung zwischen 30 und 50 Prozent werde das für viele vermutlich nicht zu stemmen sein.
Dass der Weg zur Energieerzeugung auf dem eigenen Werksgelände mühsam sein kann, weiß Radmacher aus eigener Erfahrung: „Seit rund 10 Jahren bemühe ich mich um die Genehmigung für eine Windkraftanlage auf meinem Werksgelände in Wendeburg. Doch laut Raumordnungsverfahren der zuständigen Behörden in Braunschweig sind wir kein Vorranggebiet.“ Mittlerweile setzt er seine Hoffnung auf die nächste Bundesregierung und fordert, dass die Genehmigungsverfahren verschlankt und deutlich beschleunigt werden. „Wenn man sich – wie ich – 10 Jahre um den Bau einer Windkraftanlage auf seinem eigenen Werksgelände bemühen muss, läuft etwas komplett schief in diesem Land“, merkt Radmacher an.
Recyclingquote bei Kalksandstein steigern
Nach Angaben des Bundesverbandes Baustoffe – Steine und Erden e.V. wird Bauschutt aus Kalksandsteinmauerwerk bereits zu 94 Prozent stofflich verwertet. Deklariertes Ziel der Kalksandsteinindustrie ist allerdings eine Recyclingquote von 100 Prozent durch geschlossene Stoffkreisläufe.
„Im Rahmen unserer Forschungsprojekte konnten wir zeigen, dass es selbst für Kalksandsteinmaterial aus dem Rückbau von Bestandsgebäuden viele hochwertige Recyclingwege gibt“, so Dr. Wolfgang Eden, Leiter Forschung und Technologie beim Bundesverband Kalksandsteinindustrie e.V. Bis zu zehn Prozent der Primärrohstoffe können im Regelfall problemlos durch Recycling-Material ersetzt werden. Allerdings muss es sich dabei um sortenreines Material handeln, das völlig frei von Verunreinigungen ist.
Erste Hersteller entwickeln bereits Verfahren zur serienmäßigen Herstellung von Recycling-Kalksandsteinen. „Weder produktions- noch produktseitig weisen die Recyclingsteine irgendeinen Nachteil im Vergleich zu herkömmlichen Steinen auf“, ist sich Dr. Hannes Zapf sicher, Geschäftsführender Gesellschafter der Zapf GmbH & Co. KG. „Wenn das Verfahren Serienreife erreicht hat, werden auch die Produktionskosten nahezu gleich sein.“
Mit Kalksandstein zu emissionsärmerem Beton
Auch bei der Herstellung von Beton kann Kalksandstein-Recycling-Material ein nützlich sein. Ein vielversprechender Ansatz könnte die Zugabe von Füllstoffen aus Kalksandstein-Rezyklaten sein. In einem Forschungsprojekt mit der Universität Kassel konnte die Hypothese bestätigt werden, dass Beton, dem Kalksandstein-Recycling-Material als Füllstoff zugefügt wurde, mit einem reduzierten Zementgehalt herstellbar ist.
Möglich wird dies durch die im während der Dampfhärtung in Autoklaven entstehenden CSH-Phasen (siehe Kasten), die dem Kalksandstein seine Festigkeit verleihen und über ähnliche Stoffeigenschaften wie Zement verfügen. Im Rahmen des Projekts hat sich gezeigt, dass sich die Betonqualität bei einer Zugabe von 10 Prozent Kalksandstein-Rezyklat nicht verändert. Wird der Beton ausschließlich im Innenbereich eingesetzt, wo moderate Festigkeiten ausreichend sind, kann der Anteil auch auf 20 Prozent erhöht werden. Laut DIN EN 4226–101 wären je nach Anwendungsfall sogar bis zu 35 Prozent erlaubt.
Mit Kalksandstein zu weniger schädlichen Deponien
Kalksandstein kann auch in der Abfallwirtschaft nützlich sein. Denn in den 144 in Deutschland auf Siedlungsabfall spezialisierten Deponien entsteht durch den mikrobiellen und chemischen Abbau von organischen Stoffen Methan, das etwa 25-mal klimaschädlicher wirkt als Kohlendioxid.
Selbst stillgelegte Deponien gasen nach Angaben von Prof. Gerhard Rettenberger, dem ehemaligen Leiter des Instituts für Abfallwirtschaft und Materialressourcen an der Fachhochschule Trier, noch mindestens 20 Jahre lang Methan aus. In Laboruntersuchungen und Versuchen auf der Blocklanddeponie in Bremen konnte gezeigt werden, dass Gemische aus Kalksandstein- und Porenbetongranulaten als Träger für methanabbauende Mikroorganismen geeignet sind, die das klimaschädliche Methan in weniger schädliches Kohlendioxid umwandeln.
Das könnte Sie auch interessieren:
Potenzial von Carbonbeton bestätigt
Regelwerk für Ersatzbaustoffe verbesserungsbedürftig
Ressourcenschonende Betonherstellung mit Müllverbrennungsaschen