Hutablage aus dem Automaten: Neue Anlage passt Organobleche individuell an
Bauteile aus formbaren Kunststoffen lassen sich jetzt erstmals vollautomatisch herstellen. Die Produktionszeiten sind so kurz, dass sie in den Takt der Autohersteller passen. Fraunhofer Forscher haben die Anlage entwickelt.
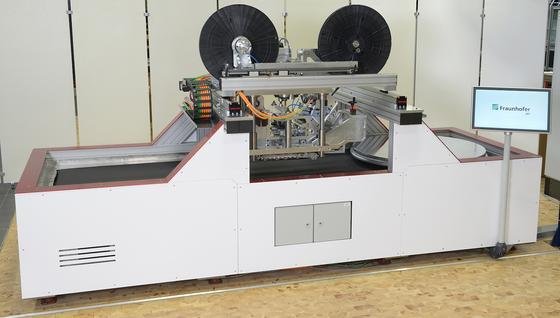
Das System zur automatisierten Herstellung individuell angepasster Organobleche.
Foto: Fraunhofer IPT
Organobleche sind ideal für den Automobilbau, weil sie buchstäblich am Fließband hergestellt werden können. Es handelt sich um Platten, deren Grundgerüst aus Kohlenstoff- oder Glasfasern besteht. Wie Lignin, das Zellstoffasern miteinander verklebt, sodass beispielsweise ein Baumstamm entsteht, werden die technischen Fasern in ein Thermoplast eingebettet. Das ist ein Kunststoff, der sich bei Erwärmung formen lässt, beispielsweise zu einer Hutablage im Auto.
Die Laminate lassen sich durch beliebig einstellbare Faserorientierungen genau an den jeweiligen Anwendungsfall und die gewünschte Belastbarkeit anpassen. Damit, so die Aachener Ingenieure des Fraunhofer-Instituts für Produktionstechnologie IPT, gelinge erstmals „eine vollständig automatisierte Herstellung belastungs- und verschnittoptimierter Organobleche einschließlich Umformung, Funktionalisierung und Kantenbearbeitung“.
Verschnitt wird minimiert
Bisher fällt bei der Produktion von Formteilen aus Organoblechen Verschnitt an, der nicht wiederverwertet werden kann. Das haben die IPT-Forscher geändert. Gemeinsam mit Industriepartnern haben sie in Aachen eine Maschine entwickelt, die derartige Formteile automatisch herstellt.
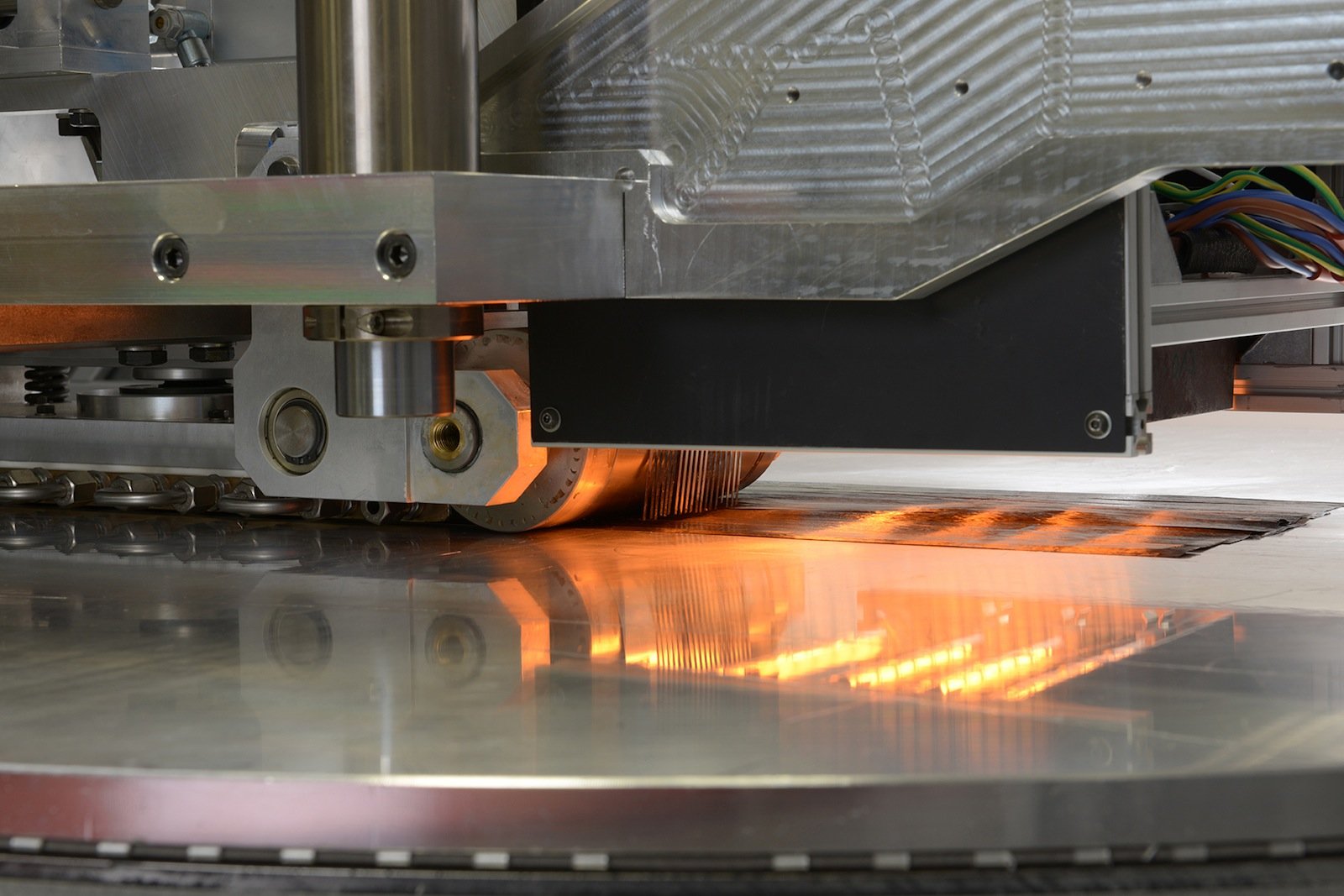
Bei der Verarbeitung des Kunststoffs werden Infrarotstrahler als Wärmequelle eingesetzt. So können die Produkte – Kohlenstoff- oder Glasfasertapes – in die endgültige Form gebracht werden.
Quelle: Fraunhofer IPT
Im ersten Schritt werden die Fasern so gelegt, dass sie die später auf sie einwirkenden Kräfte auffangen können, damit das Bauteil nicht schon bei der erste Belastung bricht. Dann folgt der Kunststoff. Nachdem dieser ausgehärtet ist lässt sich die Platte in die endgültige Form bringen. Die nötige Wärme liefern Infrarotstrahler.
Es ist auch möglich mehrlagige Organobleche zu fertigen. Im Gegensatz zu Bauteilen aus duroplastischen Faserverbundwerkstoffen, die in Formen hergestellt werden und nur minimal nachbearbeitet werden können, lässt sich die Produktion von Bauteilen aus Organoblechen an die schnellen Taktzeiten anpassen, die in der Autoindustrie üblich sind.
Komplette Anlage ist in Stuttgart zu sehen
Die Anlage arbeitet mit einer Geschwindigkeit von bis zu einem Meter pro Sekunde. Die maximale Breite der Bauteile liegt bei einem Meter. Sie wurde im Rahmen des Forschungsprojekts „E-Profit – Energieeffiziente Produktion funktionsintegrierter thermoplastischer Faserverbundbauteile“ entwickelt. Das Projekt wurde mit Mitteln des Bundesministeriums für Bildung und Forschung (BMBF) im Rahmenkonzept „Forschung für die Produktion von morgen“ gefördert und vom Projektträger Karlsruhe (PTKA) betreut.
Vom 22. bis 24. September 2015 zeigen die Aachener Ingenieure ihre Maschine erstmals vollständig aufgebaut auf der Sonderfläche „Industry meets Science“ der Fachmesse Composites Europe in Stuttgart.
Ein Beitrag von: