Forschungsprojekt „Patch2 Patient“
Im Verbundforschungsprojekt „Patch2Patient“ wurden die notwendigen Basistechnologien für eine digitale, flexible und weitgehend automatisierbare Wertschöpfungskette untersucht. Dazu gehören die für die Produktion notwendigen Module der Fiber Patch Placement (FPP)-Technologie als Testaufbau sowie ein Planungsworkflow mit angepassten digitalen Werkzeugen, die patientenspezifische Daten in die FPP-Fertigung integrieren können. Eine Besonderheit ist die Untersuchung einer geschlossenen digitalen Prozesskette für die Einzel-, Kleinserien- und Serienfertigung von medizintechnischen Bauteilen und -Komponenten aus Faser-Kunststoff-Verbund (FKV). Mit der Realisierung der Grundlagen für einen automatisierbaren Produktionsprozess unter Beachtung des Medizinproduktegesetzes (MPG) und der einschlägigen Normen [1–4] wird die automatisierte Produktion von FKV-Fertigungsprozessen in der Medizintechnik ermöglicht.Abstract: In the joint R&D-project “Patch2Patient”, we investigated the necessary basic technologies for a digital, flexible and largely automatable value chain. These include modules of the Fiber Patch Placement (FPP) technology required for production as a test setup as well as a planning workflow with adjusted digital tools that can integrate patient-specific data into FPP manufacturing. A special feature is the investigation of a closed-loop digital process chain for the individual, small series and series production of medical technology composite (i.e. fiber reinforced) parts and components. With the realization of the basics for an automatable production process in compliance with the Medical Devices Act (MPG) and the relevant standards [1–4] the automated production of composite production processes in medical technology is made possible.
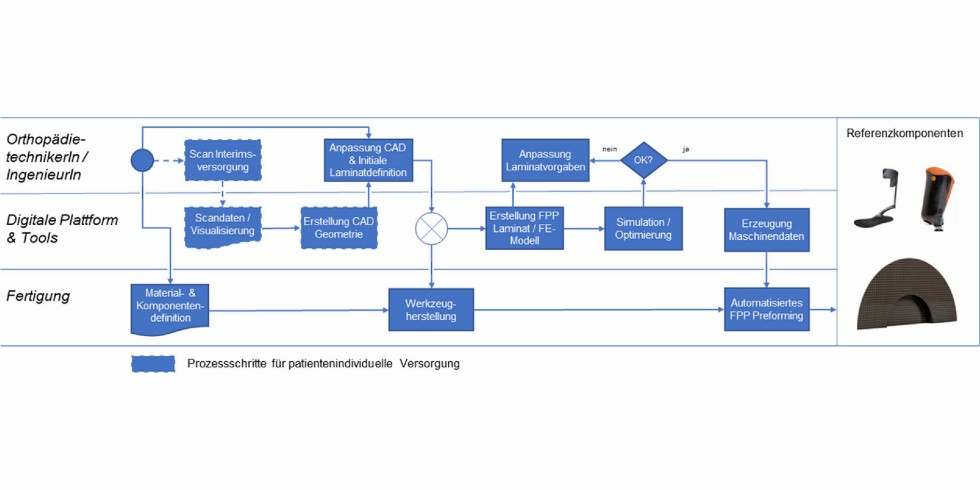
Bild 1. Angestrebte Prozesskette (vereinfacht). Grafik: Cevotec GmbH
Efficient process chain for the design and manufacture of composite components in medical applications
1 Einleitung
Die Produktion von Komponenten aus Composites, also Faser-Kunststoff-Verbunden (FKV), für die Medizintechnik erfolgt noch weitgehend in Handarbeit und wurde aus Kostengründen von vielen Herstellern ins Ausland, bevorzugt nach Asien, verlagert. Eine Automatisierung bei der Produktion von FKV-Komponenten würde in vielen Bereichen eine erh ebliche Steigerung der Produktivität ermöglichen, eine wesentlich verbesserte Rückverfolgbarkeit und Qualitätssicherung im Herstellungsprozess erlauben und damit neue Marktchancen eröffnen. Mit den heute üblichen Verfahren ist eine weitere Verbesserung aber nur sehr begrenzt möglich.
Vor diesem Hintergrund bietet das „Fiber Patch Placement“ (FPP)-Verfahren eine gut geeignete Basis für die automatisierte Herstellung von dreidimensionalen FKV-Bauteilen in der Medizintechnik, da hier über aus der virtuellen Laminatplanung abgeleiteten Maschinendaten die robotergestützte Fertigung komplexer Composite-Bauteile erfolgen kann. Allerdings sind Planungs-Workflow und maschinenseitige Technologien, etwa zur Rohmaterialbereitstellung, nicht auf die Erfordernisse von medizintechnischen Komponenten ausgelegt
Hier setzt das Verbundprojekt „Patch2Patient“, gefördert in der BMBF-Bekanntmachung „Produktion für Medizintechnik – wirtschaftlich und in höchster Qualität (ProMed)“ an. Dabei wurden die notwendigen Basistechnologien für eine digitale, flexible und weitgehend automatisierbare Wertschöpfungskette untersucht und bereitgestellt. Hierzu zählen die zur Fertigung notwendige FPP-Anlagentechnik als Versuchsaufbau sowie ein Planungsworkflow mit abgestimmten digitalen Tools, der patientenspezifische Daten in die FPP-Planung einbinden kann. Eine Besonderheit ist die Verfolgung einer geschlossenen digitalen Prozesskette für die Einzel-, Kleinserien und Serienproduktion medizintechnischer Faserverbund-Bauteile und -Komponenten. Über diese Realisierung der Grundlagen unter Beachtung der einschlägigen Normen [1–4], wird eine Automatisierung der Faserverbund-Produktion in der Medizintechnik im Einklang mit dem Medizinproduktegesetz (MPG) ermöglicht.
2 Physisch-digitale Prozesskette
Der Schlüssel zur Effizienzsteigerung bei der Komponentenfertigung in der Medizintechnik liegt in der Bereitstellung einer ganzheitlichen Prozesskette, bei der die Bauteildefinition nahtlos und mit möglichst wenigen manuellen Prozessschritten in eine automatisierte Fertigung überführt werden kann. Das Konzept einer solchen Prozesskette ist in Bild 1 dargestellt.
Im Rahmen dieses Projekts wurden die Grundlagen eines solchen Prozesses untersucht, Basiselemente prototypisch umgesetzt und erprobt. Zentraler Bestanteil des digitalen Arbeitsablaufs ist die Softwareplattform „MSP“ (Mercuris Solution Platform), in der Daten erfasst, über geeignete angegliederte Softwaretools verarbeitet und schließlich für die Weiterverarbeitung bereitgestellt werden. Ziel ist es dabei, mit Hilfe einer zentralen Benutzeroberfläche den gesamten Prozess von der Datenerfassung bis zur Bauteilproduktion automatisiert zu ermöglichen.
Ausgangspunkt sind erforderliche Geometrien und Bauteilanforderungen, die über entsprechende Schnittstellen einer simulativen Auslegung übergeben werden. Sind die so ermittelten Laminatdaten bestätigt, können über die CAD-CAM Software „Artist Studio“ automatisiert Maschinendaten erzeugt werden, die dann an ein FPP-Fertigungssystem übermittelt werden. Im Projekt wurde dieser Prozess in seinem zentralen Modul, der automatischen Materialzuführ- und Schneideinheit, umgesetzt.
Am Beispiel von Prothesenschäften, einem Blutpumpendeckel und einer WalkOn Orthese als Referenzkomponenten werden unterschiedliche Bauteilklassen (patientenindividuelle Einzelteilfertigung sowie Klein- bis hin zur Großserie) untersucht. So wird hier ein größtmögliches Spektrum produktionstechnischer Anforderungen betrachtet und in die Entwicklung der entsprechenden Software- und Hardware-Funktionsmodule eingebracht.
3 Technologie-Elemente der digitalen Prozesskette
3.1 Datenerfassung und -verarbeitung auf einer cloudbasierten Plattform
Um die Datenerfassung und -verarbeitung zentralisiert zu ermöglichen, wurde ein Prototyp der Benutzeroberfläche einer cloudbasierten Plattform entworfen mit dem Ziel, eine zentrale Anlaufstelle für alle Prozessschritte zu bilden.
Ein möglicher Ausgangspunkt ist die Digitalisierung der Stumpfgeometrie durch ein eigens entwickeltes Scanverfahren. Als zentraler Bestandteil der weiteren Datenverarbeitung auf der cloudbasierten Plattform wurde ein Verfahren zur Abbildung der Bauteilkonstruktion auf die Scandaten des Stumpfs entwickelt (vgl. Bild 2).
Im Rahmen des Projektes wurden zwei Schnittstellen implementiert und zu einem späteren Zeitpunkt erprobt:
- Direkter Datentransfer vom Scanner auf die Plattform
- Datenaustausch mit der automatisierten Laminatplanung
- In Punkt 1 können OrthopädietechnikerInnen über eine eigens entwickelte API (Application Programming Interface) die per Scan erfassten Patientendaten direkt auf die Softwareplattform übertragen und dort mit der Modellierung und der Konstruktion des Bauteils beginnen.
In der Folge kann die überarbeitete Scan-Datei sowie relevante Parameter an die Laminatplanung mit einem Klick übergeben werden (Punkt 2). Diese Schnittstelle ist bidirektional ausgeführt, so dass das digitale Modell des Bauteils zurück an die Plattform übergeben werden kann, um im Anschluss an die Produktion übergeben zu werden.
Da es sich bei den erfassten und verarbeiteten Daten um individuelle Patientendaten handelt, war die Sicherstellung der Datensicherheit ein zentraler Aspekt der Entwicklung. Hierfür wurde die Datenspeicherung auf der cloudbasierten Plattform entsprechend der DSGVO entwickelt und eine geeignete Verschlüsselung der Daten mittels eines Master Keys eingeführt. Im Rahmen der Konformität mit dem US Gesetz „Health Insurance Portability and Accountability Act“ (HIPAA) werden die Patientendaten geschützt und entsprechend verarbeitet. Somit wird für die Endnutzer sichergestellt, dass den Vorgaben von Artikel 110 der Medizinprodukteverordnung (MDR) entsprochen wird.
3.1 Simulationsmethoden für patientenindividuelle Komponenten
Die automatisierte Fertigung von Prothesenschäften in Stückzahl 1 braucht zum einen eine Sicherheitsbewertung und zum anderen eine personenspezifische strukturmechanische Auslegung des Schafts. Für diese komplexe Problemstellung wurde ein virtueller personalisierbarer Prothesenschaft-Prüfstand auf der Basis der Finite-Elemente-Methode (FEM) entwickelt, um eine materialeffiziente sichere Faserauslegung von Prothesenschäften aus FKV, in diesem Fall aus kohlenstofffaserverstärktem Kunststoff (CFK), zu ermöglichen (vgl. Bild 3) [5]. Die Krafteinleitung des entwickelten virtuellen Schaftprüfstands ist der ISO10328-Prothesenprüfnorm entnommen, die zur Prüfung von Prothesenpassteilen herangezogen wird. Für Prothesenschäfte existiert derzeit kein Normprüfstand, weil Schäfte immer noch in Handarbeit von OrthopädietechnikerInnen hergestellt werden.
Das virtuelle FE-Testsystem besteht aus dem patientenspezifischen Schaft mit der entsprechenden Dummy-Stumpfform, die mit einem steifen ABS-Material modelliert wurde. Die obere und die untere Vorrichtung dienen dazu, die in der ISO10328 [4] festgelegte Prüflasten aus Kraft und Moment auf den Schaft zu übertragen, die in spezifischen Gangphasen (zum Beispiel „heel strike“ und „toe off“) auftreten. Die Vorrichtung ist somit variabel einstellbar, sodass die Prüflast auf die individuelle Stumpfhöhe, Schaftgeometrie und Gangphase angepasst werden kann.
Beide Belastungsszenarien wurden simuliert und die Hauptspannungsverläufe am verformten Prothesenschaft analysiert. Die Hauptzugspannungstrajektorien werden verwendet, um eine optimale Faserausrichtung der CFK-Lagen für eine ideale Materialbeanspruchung zu erreichen. In einem weiteren Schritt kann aus dem Spannungsbild ein Leichtbau-Schaftdesign generiert werden, indem man nicht bzw. wenig belastete Bereiche des Schafts entmaterialisiert und dem Schaft ein neues Design gibt (Bild 4).
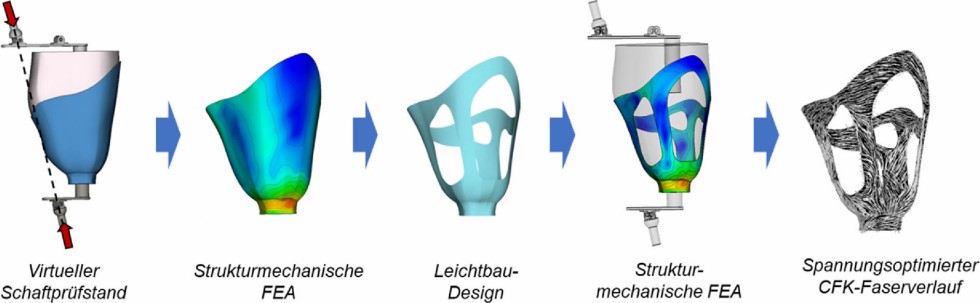
Bild 4. Darstellung eines virtuellen Testlaufs des generischen Prothesenschaftdesigns. Grafik: Cevotec GmbH
Anschließend kann durch Strukturoptimierung das Design weiter verfeinert und gleichzeitig die geforderte Traglast gemäß ISO10328 gegen Bruch sichergestellt werden.
Das virtuelle Prüfsystem kann automatisiert schnell für jedes Material und jede Schaftgeometrie angepasst werden. Damit entstehen große Möglichkeit für Sanitätshäuser individuelle Schaftdesignlösungen schnell und präzise mit definierter Stabilitätssicherheit anzubieten.
3.2 Automatisierte Generierung von Maschinendatensätzen
Die Arbeiten zur Laminatplanung und Maschinendatengenerierung bauen auf der existierenden CAD/CAM-Lösung Artist Studio der Cevotec GmbH und das dort vorhandene Scripting-Interface auf. Insbesondere wurde hier die Unterstützung von Patches mit variabler, auf die Krümmung der Oberfläche angepasster Länge und erweiterte Schnittstellen zu den Projektpartnern neu implementiert.
Ein Nutzer des neu realisierten API sendet eine Anfrage zur Laminatplanung, welche die Bauteilgeometrie in Form eines STL-Netzes und zugehörige Metadaten enthält. Die Metadaten beinhalten unter anderem die Definition eines Referenzpunktes auf der Oberfläche, die gewünschten Materialparameter, sowie Informationen zur sicheren Übertragung der Ergebnisse zurück auf die MSP.
Für die Laminatplanung wird eine zuvor anhand eines Referenzbauteils simulativ validierte Faserarchitektur (vgl. Abschnitt 3.2) auf die konkrete Geometrie angewendet. Hierzu werden zunächst Kurven entlang der gewünschten Faserorientierung auf der Oberfläche erzeugt. Entlang dieser Kurven werden die Patches erzeugt. Mithilfe eines Optimierungsalgorithmus wird darüber hinaus die Überlappung zwischen den Patches optimiert, um die bestmöglichen mechanischen Eigenschaften des Laminats zu gewährleisten. Zudem kann – in Bereichen starker Bauteilkrümmung – ein Laminat mit variabler Patchlänge erzeugt werden, um den Bedeckungsgrad und die Ablagequalität zu verbessern (siehe Bild 5).
Die abschließende Fertigungsplanung und -optimierung, sowie der Export von Maschinendaten erfolgt im Anschluss ebenfalls vollautomatisiert. Die vollständige Laminatgeometrie wird dann zurück an die MSP gesendet, kann dort betrachtet und zur weiteren Verwendung, etwa der Übermittlung von Maschinendatensätzen an das Produktionssystem, freigegeben werden.
4 Technologie-Elemente zur Realisierung der Bauteile
4.1 Automatisierte Multi-Material-Verarbeitung
Composite-Werkstoffe, insbesondere in der gebräuchlichsten Form als vorimprägnierte Verstärkungsfaserhalbzeuge, stellen besondere Anforderungen an die Verarbeitungsmaschinen, da sowohl den Eigenschaften des Matrixmaterials wie Temperaturabhängigkeit und Klebrigkeit, als auch den Eigenschaften der Faserverstärkung wie Schneidbarkeit Rechnung getragen werden muss. Zudem stehen die Halbzeuge auf unterschiedlichen Trägern (Spulentypen) zur Verfügung.
Vor diesem Hintergrund wurde eine vollautomatisierte Zuführ- und Schneideinheit entwickelt, die Patches aus unterschiedlichen Materialtypen auf zwei Transportbändern (Multimaterial-Tauglichkeit) für eine spätere robotergestützte Verarbeitung bereitstellen kann (Bild 6).
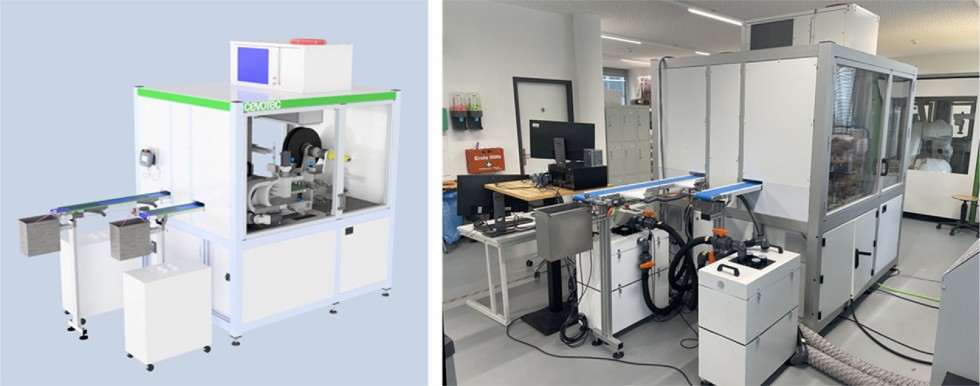
Bild 6. CAD-Entwurf einer auf medizintechnische Anforderungen angepassten Material Zuführ- und Schneideinheit (links) und prototypische Umsetzung (rechts). Grafik: Cevotec GmbH
Ein besonderes Augenmerk gilt der in der Einheit integrierten Qualitätssicherung, so dass eine durchgehende Qualitätskontrolle und -dokumentation der eingesetzten Materialien erfolgt.
Zur Vorbereitung eines automatisierten Produktionsprozesses wurden mehrere verschiedene Werkzeugkonzepte sowohl zum Patchen als auch zum Aushärten untersucht. Hierfür wurden prototypische Werkzeuge aus Aluminium und Stahl gefräst, mit ABS, PLA, PA12 und PETG 3D gedruckt und aus Gips gegossen. Beim Patchen auf diese Werkzeuge zeigte sich, dass die Oberflächenrauigkeit einen sehr großen Einfluss auf den Patchprozess für die erste Lage hat. Hier hat sich gezeigt, dass eine möglichst glatte Kunststoffoberfläche den Ablageprozess begünstigt.
Stahl und Aluminiumwerkzeuge, sowie auch Gipswerkzeuge weisen eine vergleichsweise hohe Masse auf. Da diese Masse durch den Roboter gehandhabt werden muss, haben sich leichte 3D-Werkzeuge, bei denen oberflächlich über ein Vakuum eine PVC-Folie angesaugt wird, als vorteilhaft erwiesen. Zudem sind die Werkzeuge über das 3D-Druck-Verfahren schnell verfügbar. Durch die aufgebrachte PVC-Folie ist die Ablagefläche sehr glatt, wodurch die Patches gut haften. Ein weiterer Vorteil ist, dass die Werkzeuge durch die Folie sauber bleiben und das Patchlaminat sehr leicht vom Werkzeug abgenommen werden kann. Somit ist dieser Werkzeugtyp – unter Beachtung der Temperaturbeständigkeit und der später geforderten Oberflächengüte – die für den betrachteten Prozess bevorzugte Variante.
4.2 Erzeugung von Laminatdaten für Prototypen und Fertigung von Testmustern
Im Rahmen des Projektes wurden unterschiedliche Strukturen mit angepasstem FPP-Laminat entwickelt und prototypisch umgesetzt (Tabelle).
Bei der Fertigung wurden sowohl die bisher zum Einsatz kommenden Materialien als auch im Projekt erarbeitete Alternativmaterialien angewendet.
In der prototypischen Umsetzung zeigen sich auch Limitationen des patchbasierten Ansatzes. Am Beispiel des Blutpumpendeckels zeigt sich bei den sehr kleinen Radien eine Überbrückung von konkaven Bereichen und Fehler wie etwa Lunker, so dass diese Bauteilklasse nicht für die Umsetzung im FPP-Verfahren geeignet ist. In ähnlichen Bereichen, etwa bei der Anbindungsplatte eines Prothesenschafts, kann durch eine konstruktive Änderung eine Verarbeitbarkeit sichergestellt werden.
Ein weiterer begrenzender Effekt sind Bauteilbereiche mit geometrisch filigranen Strukturen, wie sie etwa beim Steg der WalkOn Orthese auftreten. In solchen Bauteilbereichen führt das patchbasierte Preforming zu einem Materialüberstand, der bei der Endbearbeitung des Bauteilrandes wieder entfernt werden muss. Der dabei auftretende Materialverlust verschlechtert die Kostenbilanz dieser Komponente. Hier sind FPP-Technologien in der Erprobung, die diesen Materialüberstand durch Bereitstellung konturangepasster, nicht-rechteckiger Patches verringern oder ganz vermeiden können.
Als relevanteste Bauteilklasse wurde ein Prototyp des FPP-Prothesenschafts einem Patiententest im Vergleich zu einem konventionellen Faserverbund-Schaft unterzogen. Hier kam ein im orthopädischen Bereich etablierter, 12-teiliger Fragebogen zum Einsatz (PLUS-M™). Anhand des Fragebogens lässt sich der Patient individuell und im Vergleich zu einer Vielzahl von Prothesenträgern beurteilen. In beiden Fällen (Referenz- und FPP-Bauteil) wurde dieselbe Bewertungsgröße (T-Score) ermittelt, so dass hier ein direkter Austausch der Fertigungstechnologie erfolgen kann.
5 Fazit und Ausblick
In dem bearbeiteten Forschungsprojekt „Patch2Patient“ wurde eine neuartige Prozesskette zur automatisierten Fertigung von Faserverbund-Bauteilen in der Medizintechnik erarbeitet sowie in ihren Basiselementen umgesetzt. Neben der erarbeiteten Austauschplattform, patientenindividueller Datenerfassung und virtuellen Testmethoden standen auch automatisierte Laminat- und Maschinendatenerzeugung sowie Technologien zur Multimaterial-Verarbeitung im Fokus der Arbeiten. Dabei ist in allen Aspekten (Datensicherheit, Werkstoffe und Prozess) eine Berücksichtigung der medizinprodukterelevanten Normen und Vorgaben erfolgt. Die erarbeiteten Methoden und Technologien wurden an anwendungsrelevanten Fällen, auf Substruktur- und Bauteilebene erprobt. Dabei konnten die Einsatzgrenzen, insbesondere hinsichtlich geometrischer Komplexität, aber auch die Potenziale, insbesondere bei patientenindividuellen Prothesen, aufgezeigt werden. Durch die Bereitstellung eines effizienten Planungs-, Datenverarbeitungs- und Fertigungsworkflows kann die Wertschöpfungskette für solche Bauteile in den Hochlohnländern in Europa gestärkt werden. Zudem sind viele der erarbeiteten Technologien auch in anderen Branchen, etwa der Luft- und Raumfahrttechnik, einsetzbar, so dass ein weiterer Ausbau der Marktposition europäischer Hersteller von Composite-Bauteilen unterstützt werden kann.
Danksagung: Dieses Forschungs- und Entwicklungsprojekt wurde durch das Bundesministerium für Bildung und Forschung (BMBF) im Programm „Innovationen für die Produktion, Dienstleistung und Arbeit von morgen“ (Förderkennzeichen 02P18C090 bis 02P18C096) gefördert und vom Projektträger Karlsruhe (PTKA) betreut. Die Verantwortung für den Inhalt dieser Veröffentlichung liegt bei den Autoren.
Literatur
- EN ISO 13485:2016: Medizinprodukte – Qualitätsmanagementsysteme – Anforderungen für regulatorische Zwecke. Berlin: Beuth-Verlag, 2016
- DIN EN ISO 14971:2019, Medizinprodukte – Anwendung des Risikomanagements auf Medizinprodukte, Beuth-Verlag: Berlin, 2019
- DIN EN 12182:2012 Technische Hilfen für behinderte Menschen – Allgemeine Anforderungen und Prüfverfahren, Beuth-Verlag: Berlin, 2012
- ISO 10328:2016: Prothetik – Prüfung der Struktur von Prothesen der unteren Gliedmaßen – Anforderungen und Prüfverfahren. Berlin: Beuth-Verlag, 2016
- Kneifl, J.; Rosin, D.; Avci, O.; Röhrle, O.; Fehr, J.: Low-dimensional Data-based Surrogate Model of a Continuum-mechanical Musculoskeletal System Based on Non-intrusive Model Order Reduction. Archive of Applied Mechanics (2023)
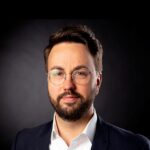
Dr. Florian Lenz
Foto: Cevotec GmbH
Cevotec GmbH
Biberger Str. 93, 82008 Unterhaching
Tel. +49 89 / 2314 165 11
florian.lenz@cevotec.com
www.cevotec.com
Eva Hildsberg
Mecuris GmbH
Lindwurmstr. 11, 80337 München
Tel +49 89 20 00 57-300
eva.hildberg@mecuris.com
www.mecuris.com
Dr. Okan Avci
Fraunhofer-Institut für Produktionstechnik und Automatisierung IPA
Nobelstr. 12, 70569 Stuttgart
Tel. +49 711 / 970-3609
okan.avci@ipa.fraunhofer.de
www.ipa.fraunhofer.de
Robert Bastian
carbovation gmbh
Otto-Lilienthal-Str. 15, 88046 Friedrichshafen
Tel. +49 7541 38890
r.bastian@carbovation.de
Tobias Rusch
Guenther Bionics GmbH
Wiesenweg 1, 39317 Parey
Tel. +49 391 555 68097
t.rusch@guentherbionics.de
www.guentherbionics.de
Johannes Wölper
Otto Bock SE & Co. KGaA
Max-Näder-Straße 15, 37115 Duderstadt
Tel. +49 5527 8481746
johannes.woelper@ottobock.de
www.ottobock.de