Smart Tools: intelligente Werkzeuge
Werkzeugprozesskosten haben einen signifikanten Anteil an den Fertigungskosten in der zerspanenden Fertigung. Diese Kosten zu senken und die Produktion zu optimieren, waren die Forschungsschwerpunkte des vom BMBF geförderten Projektes „Smart Tool – Intelligente Werkzeuge für die vernetzte Fertigung von morgen“. Smart Tool vernetzt mithilfe eines cyber-physischen Systems (CPS) den gesamten Werkzeugkreislauf. So ist eine lückenlose und durchgängige Nachverfolgung der Werkzeuge gegeben. In den Werkzeughalter integrierte Sensoren lassen darüber hinaus Rückschlüsse auf den Zustand des Werkzeugs zu.
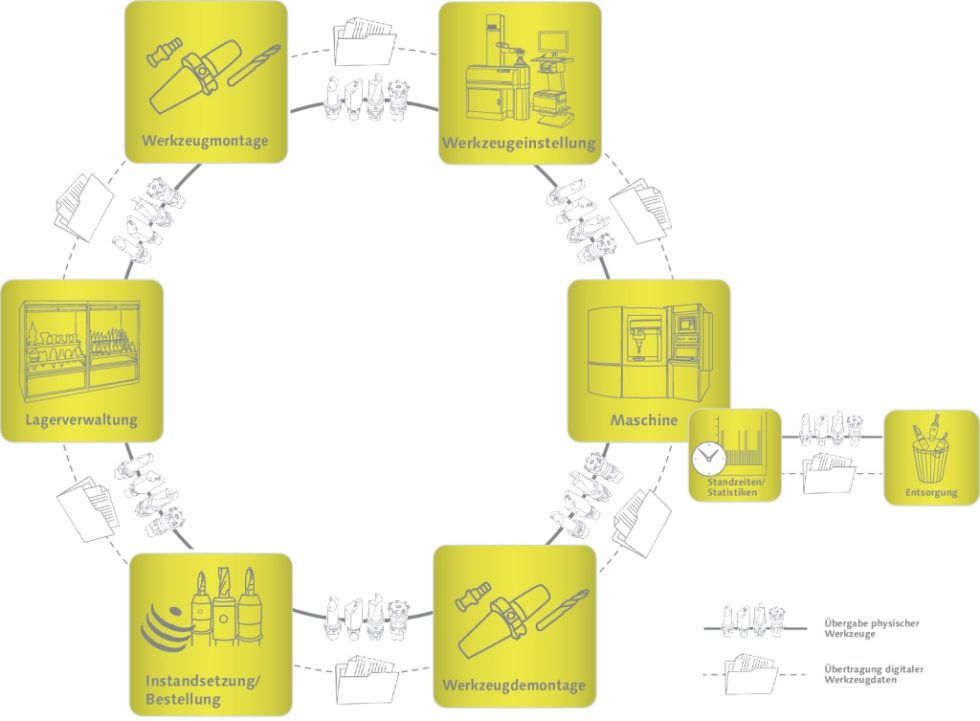
Was wäre, wenn Werkzeuge einfach ihren Standort mitteilten, statt sich suchen zu lassen? Wenn sie beim Überschreiten von Grenzwerten Alarm schlügen, bevor es zum Crash kommt? Oder mit den Bearbeitungs- und Einstellmaschinen kommunizieren könnten, damit überall die gleichen Daten vorhanden wären und die Abläufe optimiert würden? Das wäre ganz schön „clever“.
Diese Zukunftsvision wurde im Rahmen des Forschungsprojektes bereits Realität. Kerninnovation ist ein cyber-physisches System (CPS), in dem nicht nur jedes Werkzeug jederzeit seinen Platz und seinen Zustand kennt, sondern auch mit den für den Fertigungsverlauf relevanten Maschinen und Anlagen kommuniziert und sich über dessen Zustand austauscht.
Ein CPS verbindet reale physikalische Objekte und Prozesse mit virtuellen Objekten und Prozessen – und zwar in Echtzeit über das Internet. Dazu muss ein Datentransfer zwischen Werkzeugen und Maschinen sowie Planung und Logistik jederzeit gegeben sein.
1 Das typische Bild im Werkzeugmanagement
Je komplexer die Fertigung aufgebaut ist, desto heterogener sind auch die verschiedenen Komponenten, Maschinen und Anwendungen im Werkzeugkreislauf. Oftmals gibt es innerhalb der Produktion gar keine oder nur eine rudimentäre Vernetzung; zur Verfügung stehende Daten aus den verschiedenen Abteilungen oder Funktionsbereichen auch nur eines einzelnen Unternehmens sind intransparent und können zwischen den verschiedenen Bereichen häufig nicht transferiert werden. Eine mangelhafte und unterschiedliche Datenerhebung, ungleiche Schnittstellen und unterschiedliche Anforderungen an die Datenformate machen einen Datentransfer in der Fertigung nahezu unmöglich. Damit kann es keine ereignisbasierte, automatisierte Unterstützung der Fertigungsprozesse geben.
Insbesondere bei verschleißbehafteten Werkzeugen, wie sie in der zerspanenden Fertigung zum Einsatz kommen, ist das Wissen um das „Wie“ und „Wo“, also um den Aufenthaltsort eines Werkzeugs und seines Zustandes, wesentlich für die Fertigung. Bei bis zu 30 % Werkzeugprozesskosten – diese setzen sich zusammen aus der Werkzeuglagerung, der Werkzeugbereitstellung, der Werkzeugmontage, der Werkzeugeinstellung, der Aufbereitung oder Entsorgung sowie der Demontage – bedeutet jede Optimierung im Kreislauf gespartes Geld.
Als Smart Tool wird jedes Werkzeug von seiner Umwelt wahrgenommen. Seine Daten sind erfasst und können übertragen werden. Damit erhält der gesamte Werkzeugkreislauf eine durchgängige Datentransparenz, welche die Grundlage für selbst-organisierende Prozesse ist.
2 Der Werkzeugkreislauf
Ausgehend von dem Fertigungsprozess des Werkstücks in der Maschine, wird das Werkzeug nach der Bearbeitung wieder demontiert, gegebenenfalls aufbereitet und eingelagert oder entsorgt.
Der Lagerbestand wird üblicherweise mithilfe eines Toolmanagement-Systems erfasst. In diesem ist das Werkzeug mit seinen Materialstammdaten hinterlegt. Wird das Werkzeug für einen weiteren Auftrag angefragt, wird es montiert, eingestellt und abschließend an der Maschine bereitgestellt. Damit schließt sich der physische Werkzeugkreislauf.
Parallel zu dem physischen Kreislauf sind für jedes Werkzeug und für jede Komponente auch digitale Daten im Toolmanagement-System hinterlegt und verfügbar. Somit besitzt jedes physikalische Werkzeug einen „digitalen Zwilling“ in der Datenbank. Dort sind sämtliche Stammdaten aber auch Zustandsdaten, aus denen Verschleiß, Toleranzen und Reststandzeit hervorgeht, hinterlegt und für jedes Werkzeug jederzeit aktuell abrufbar.
Je umfangreicher die Produktvielfalt, desto größer ist die Anzahl der eingesetzten Werkzeuge und desto häufiger kommt es zu einem Werkzeugwechsel und damit zu dem beschriebenen Werkzeugkreislauf mit den entsprechenden Kosten. Eine Kostenoptimierung des Werkzeugkreislaufs besitzt ein enormes Einsparpotenzial. Somit kommt dem Werkzeug eine Schlüsselrolle bei der Betriebsmittelplanung zu. Ist jederzeit sein Zustand und sein physischer Ort bekannt, kann das enorme Kosten einsparen. Das Werkzeug wird nicht gesucht, sondern ist verfügbar, sein Zustand und seine Qualität sind direkt abrufbar. Damit ist zum einen die Logistik optimiert und das Werkzeug kann auf direktem und kürzestem Weg dorthin transportiert werden, wo es benötigt wird. Zudem ist jederzeit der Zustand des Werkzeugs bekannt, sodass auch das interne Bestellwesen für die Bereitstellung von Werkzeugen entsprechend vereinfacht ist.
Ein intelligentes Werkzeugsystem kennt nicht nur jederzeit seinen Platz und den Zustand seines Werkzeugs, sondern kommuniziert auch mit den für den Fertigungsverlauf relevanten Maschinen und Anlagen und tauscht sich über dessen Zustand aus.
Ein solches Werkzeug zusammen mit einer durchgängigen Datentransparenz ist die Grundvoraussetzung für die Implementierung selbstorganisierender Prozesse.
3 Intelligentes Werkzeugsystem
Werkzeughalter und Werkzeug bilden als Werkzeugsystem eine Einheit. Ein intelligentes Werkzeugsystem besteht aus einem eindeutig identifizierten Werkzeughalter mit integrierter Sensorik, Logik- und Übertragungseinheit sowie dem Werkzeug selbst mit eindeutiger, integrierter Kennung.
Die eindeutige Identifizierung von Komponenten oder Individuen wie Werkzeuge oder Werkzeughalter erfolgt typischerweise über Data-Matrix-Code (DMC). Diese Kennzeichnung ist sowohl preisgünstig als auch robust und hat sich im industriellen Umfeld bewährt, zumal sie über die gesamte Lebensdauer des Individuums Bestand hat.
Mit dieser Kennzeichnung ist das Werkzeug eindeutig erfasst. Über die Datenbank kann jederzeit auf die hinterlegten Daten zugegriffen werden. Aus diesen sind die Zustandsdaten und die Reststandzeiten ersichtlich. Ändern sich diese Messwerte, beispielsweise durch Verschleiß nach einem Bearbeitungsprozess, ist auch diese Veränderung elektronisch hinterlegt und kann bei der Auswahl des Werkzeugs für die weitere Bearbeitung berücksichtigt werden. Beispielsweise kann ein Werkzeug mit geringer Reststandzeit für einen weniger umfangreichen Auftrag eingesetzt werden; für einen größeren Auftrag würde ein neues Werkzeug oder eines mit entsprechend langer Reststandzeit ausgewählt. So können Werkzeugwechsel und damit Rüstzeiten und Kosten reduziert werden.
4 Track & Trace: Verfolgen des aktuellen Lagerortes
Um auch die Position des gesamten Werkzeugsystems zu identifizieren, sind die Werkzeughalter zusätzlich mit RFID-Technologie (radio frequency identification) ausgerüstet. So können sie mit den Interaktionspartnern kommunizieren. Kommt das Werkzeugsystem an einem Tracking Point vorbei, wird es dort identifiziert und der jeweilige Standort ist damit bekannt. Das Suchen nach dem Werkzeug entfällt.
Die Datenübertragung des RFID erfolgt per UHF-Technologie (ultra high frequence). Sie erlaubt aufgrund der höheren Reichweite auch die Pulkauslesung mehrerer Komplettwerkzeuge auf einmal.
Wird ein Komplettwerkzeug angefordert, werden Werkzeughalter und Werkzeug aus dem Lager entnommen, identifiziert und separat elektronisch gebucht. In der Montage werden sie zu einem Komplettwerkzeug „verheiratet“ und dann an das Einstellgerät gesendet. Die Position des Werkzeugsystems kann per RFID digital abgefragt werden, der Zustand des Werkzeugs ist in den Daten hinterlegt. Auch der Versand von der Montage zum Einstellgerät kann bereits automatisiert ablaufen, beispielsweise durch automatisch angetriebene Flurwagen, die den Empfangsort des Werkzeugsystems bereits kennen. Am Einstell- und Messgerät angekommen, kommuniziert das Werkzeugsystem direkt per RFID. Das Werkzeugsystem wird eindeutig identifiziert und der Einstell- und Messvorgang kann automatisch starten, da die Anforderungen hinterlegt und damit bekannt sind. Der manuelle Aufwand im gesamten Fertigungsprozess wird deutlich reduziert und gleichzeitig sicherer und weniger fehleranfällig. Ebenso lässt sich im weiteren Fertigungsprozess jeder Weg mithilfe des RFID verfolgen: vom Einstellen über die Bearbeitung in der Maschine zurück zum Lager.
5 Datentransfer eines Smart Tools
Gelangt ein Smart Tool in die Nähe der Bearbeitungsmaschine, für die es vorgesehen ist, wird es dort identifiziert. Die Maschine ruft aus dem Smart Tool Center (Cloud) die entsprechenden Daten ab und verfügt somit über sämtliche für sie relevante Werkzeuginformationen. Lediglich das Einlegen des Werkzeugsystems erfolgt noch physisch – manuell oder automatisiert, zum Beispiel per Roboter.
Sämtliche Daten liegen in einer OPC-UA- (Open Platform Communications Unified Architecture) Spezifikation in der Cloud. Nur über dieses offene Datenformat ist es überhaupt möglich, ein übergeordnetes CPS zu entwickeln, das mit sämtlichen Maschinen, Werkzeugen und Komponenten kommunizieren kann – unabhängig vom jeweiligen Datenformat und der jeweiligen Schnittstelle.
Die digitale Kommunikation beim Einlegen des Werkzeugsystems in die Maschine ist sehr viel komplexer als die physikalische und besitzt mehrere Interaktionspartner. Da ist zunächst die Fertigungsmaschine, die einen Magazinplatz für das angelieferte Werkzeugsystem bereitstellen muss und diesen Platz auf der Maschine vorgegeben bekommt. Die Maschine liest die eindeutige Tag-ID des Werkzeugsystems aus und die Maschinensteuerung erhält die relevanten Daten wie die Sachmerkmale des Werkzeugsystems sowie die voreingestellten Prozessdaten über die Cloud. Der Bearbeitungsprozess kann nun starten. Ist der Fertigungsprozess beendet, wird das Werkzeugsystem wieder aus der Maschine herausgenommen, der weitere physische Weg kann ebenfalls digital verfolgt werden. Da sämtliche Daten kontinuierlich aufgezeichnet und nicht überschrieben werden, ist diese Verfolgung auch ein Beitrag zur Qualitätssicherung und zur Rückverfolgbarkeit.
6 Messen prozessinterner Größen
Doch ein Smart Tool kann viel mehr als nur Daten über seine Position und seinen Zustand mit dem Smart Tool Center austauschen. Es kann auch prozessinterne Größen messen, die nutzerspezifisch relevant sein können und beispielsweise Rückschlüsse auf Verschleiß oder sogar einen Werkzeugbruch geben.
Eine zusätzliche Mikroelektronik in Form einer flexiblen Platine ist in die Werkzeughalter integriert. Dafür verfügt der Werkzeughalter über eine zusätzliche Ringnut mit Schraubdeckel, in die die Platine eingelegt wird. Eine zusätzliche Bohrung für das Antennenkabel stellt die Datenübertragung sicher. Ein zusätzlich integriertes und von außen zugängliches Batteriefach gewährleistet die elektrische Energieversorgung.
Die in den Werkzeughalter integrierte Mikroelektronik kann die während des Bearbeitungsprozesses gewonnenen Daten direkt komplett vorverarbeiten und gegebenenfalls über das Smart Tool Center in den Bearbeitungsprozess eingreifen. Ein Beispiel sei der ausgewertete Status für Schwingungssignale, die mithilfe eines integrierten Beschleunigungssensors aufgenommen werden. Läuft der Betrieb normal, wird die Mikroelektronik keine Reaktion einleiten. Wird ein erster Schwellenwert überschritten, der einem gewissen Verschleißgrad zugeordnet wird, wird an die Cloud der Hinweis auf einen anstehenden Werkzeugwechsel ausgegeben. Wird ein zweiter Schwellenwert überschritten, so kommt es zu dem Warnhinweis, dass das Werkzeug sehr stark verschlissen sei. Dieser Warnhinweis kann auch dazu führen, dass der interne Bestellvorgang für ein neues Werkzeug eingeleitet wird, um die Bereitstellung dieses Werkzeugs sicherzustellen.
Kommt es zu einem unerwarteten Signalverlauf, beispielsweise durch einen Werkzeugbruch, so kann dieses Signal einen Vorschubstopp erzwingen: Die Mikroelektronik im Werkzeugsystem detektiert einen untypischen Signalverlauf und sendet diese Fehlermeldung an die Cloud. Diese Daten werden direkt von der Maschine empfangen und die notwendigen Schritte – in diesem Fall der Vorschubstopp – werden eingeleitet und sofort umgesetzt.
Durch zusätzlich integrierte Sensorik lassen sich auch weitere Größen und Parameter aufnehmen, die für den Zustand des Werkzeugsystems wichtig sein können, sich aber aus den ansonsten bekannten Größen über die Steuerung nicht erfassen lassen.
All diese Daten geben Informationen und lassen Rückschlüsse auf den physikalischen Zustand des Werkzeugsystems zu. Die Auswertung und eventuelle Folgerungen ergeben sich aus den Daten. Fließen zusätzlich Erfahrungswerte ein, lassen sich die Standzeiten der Werkzeuge entsprechend optimieren, sodass maximale Werkzeugstandzeiten erreicht werden können und der Austausch so spät wie möglich erfolgt. Auf diese Weise lassen sich die Kosten für die Verschleißteile reduzieren und somit optimieren. Das dient der Ressourcenschonung.
7 Zusammenfassung
Im Rahmen des Projektes wurde sowohl ein Smart Tool entwickelt als auch die Peripherie für den industriellen Einsatz eines Smart Tools geschaffen. Mithilfe von Demonstratoren wurden die ersten Smart Tools bereits unter industriellen Bedingungen getestet und eingesetzt. Track & Trace – die Nachverfolgbarkeit und damit das sichere Auffinden von Werkzeugen – vereinfacht den Werkzeugeinsatz. Ein gezieltes und effektives Werkzeugmanagement spart sowohl Zeit als auch materielle Ressourcen und damit letztlich Kosten. Das Integrieren einer Mikroelektronik in den Werkzeughalter, mit der prozessinterne Größen gemessen und ausgewertet werden, eröffnet darüber hinaus vielfältige neue Möglichkeiten in der Analyse von Werkzeugen.
Dipl. Wirt. Ing. (FH) Bernd Schwennig Dr. Stefanie Jerems E. Zoller GmbH & Co. KG Gottlieb-Daimler-Str. 19, 74385 Pleidelsheim Tel. +49 (0)7144 / 8970-161 schwennig@zoller-d.com www.zoller.infoIm Projekt „Smart Tool – Intelligente Werkzeuge für die vernetzte Fertigung von morgen“ (Smart Tool) kooperieren die folgenden Partner: Heidelberger Druckmaschinen AG, Siemens AG Energy Sector, Haimer GmbH, Gühring KG, E. Zoller GmbH & Co. KG, EINS GmbH, Institut für Integrierte Elektronische Systeme (IES) der Technischen Universität Darmstadt, Institut für Produktionsmanagement, Technologie und Werkzeugmaschinen (PWT) der Technischen Universität Darmstadt. Das Forschungs- und Entwicklungsprojekt Smart Tool wird mit Mitteln des Bundesministeriums für Bildung und Forschung (BMBF) im Programm „Innovationen für die Produktion, Dienstleistung und Arbeit von morgen“ (Förderkennzeichen 02PJ2720–02PJ2726) gefördert und vom Projektträger Karlsruhe (PTKA) betreut. Die Verantwortung für den Inhalt dieser Veröffentlichung liegt bei den Autoren.