Ganzheitliche Entwicklungsmethodik für Leichtbauansätze
Bei neuen Antriebssystemen für einen treibhausgasneutralen Verkehr der Zukunft spielt der Leichtbau eine bedeutende Rolle. Im vom Bundesministerium für Wirtschaft und Energie (BMWi) geförderten Verbundprojekt „LeiMot – Gewichtsreduzierung eines Verbrennungsmotors durch Strukturoptimierung und Verwendung von Hybrid Metall- und Kunststoff-Komponenten“ wurde unter industrieller Federführung eine ganzheitliche Entwicklungsmethodik zur Umsetzung innovativer Leichtbauansätze für leichte und effiziente Antriebe der Zukunft demonstriert. Auch die Nutzung nicht-fossiler Kraftstoffe, zum Beispiel Wasserstoff, sind durch diese Entwicklung möglich.
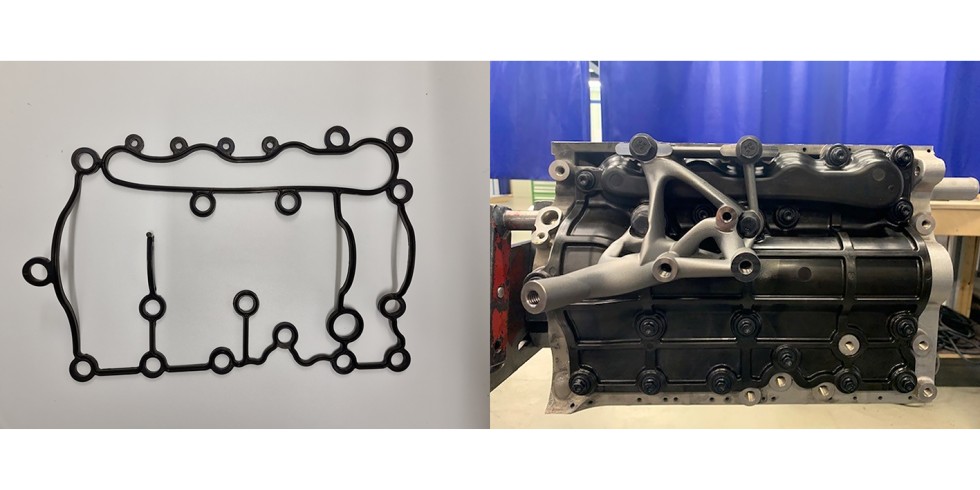
Bild 5. 3D-Dichtung (links), Aluminium-Kurbelgehäuse (rechts), FVK-Cover und Halter der Abgasanlage. Grafik: Fraunhofer ICT
Ausgabe 5-2022, S. 288–291
Significant weight saving in new, mobile drive systems – Holistic development method for lightweight applications in CO2-neutral drive systems, demonstrated with a thermoset-aluminum hybrid crankcase
Abstract: Lightweight construction will play a significant role in new drive systems for the carbon-neutral transportation of the future. In the industry-led LeiMot project, funded by the German Federal Ministry for Economic Affairs and Climate Action (BMWi), a holistic development method for implementing innovative lightweight design approaches for future light and efficient drive systems was demonstrated. The use of non-fossil fuels, such as hydrogen, is also possible through this development.
1 Einleitung und Motivation
Auf dem Weg zu einem treibhausgasneutralen Verkehr müssen alle Register gezogen werden. Neben neuen Antriebsformen wie elektrische oder wasserstoffbetriebene Antriebe werden CO2-neutrale, synthetische Kraftstoffe für Verbrennungsmotoren entwickelt. Allen Antrieben ist gemein, dass das Gewicht eine entscheidende Rolle spielt. Im vom BMWi unter Förderkennzeichen 19/18002C geförderten Verbundprojekt LeiMot wurde unter industrieller Federführung eine ganzheitliche Entwicklungsmethodik zur Umsetzung innovativer Leichtbauansätze für neue Antriebssysteme demonstriert. Die Innovation im Projekt besteht darin, die thermisch und mechanisch hochbelasteten Strukturen des Motors als 3D-gedruckte Aluminium-Bauteile auszuführen und das nach außen offene Kurbelgehäuse mittels im Spritzguß gefertigter Kunststoffseitenwände zu komplettieren. Mit diesem Ansatz können zudem in den Kunststoffseitenwänden weitere Funktionen, wie zum Beispiel die Wasserpumpe oder die Medienkanäle für Öl und Kühlmittel, integriert werden, was zu einer weiteren Gewichts- und Kostenersparnis führt [1]. Die Abteilung „Neue Antriebssysteme“ des Fraunhofer-Instituts für Chemische Technologie ICT hat die passenden Kompetenzen in der Konstruktion, der Simulation sowie der Validierung am Prüfstand, um eine solche Entwicklung zu begleiten.
Die technischen Anforderungen aus dem Lastenheft eines motornahen Bauteils sind anspruchsvoll. Ausreichende mechanische Eigenschaften wie Steifigkeit und Festigkeit der Leichtbau-Kunststoffkomponente müssen auch bei hohen Temperaturen von bis zu 180 °C gegeben sein. Weiterhin werden über die Bauteillebensdauer eine hohe Kriechbeständigkeit sowie die Beständigkeit gegenüber den Medien Wasser und Öl benötigt. Glasfaserverstärkte Phenolharzformmassen erfüllen all diese Anforderungen und können zudem wirtschaftlich mittels Spritzgussverfahren hergestellt werden [2].
2 Herangehensweise
Die Kunststoff-Seitenteile verschließen sowohl das Kurbelgehäuse nach innen und dichten gegen den Blow-By, also dem Mix aus Abgasen, Öl, Wasser und nicht verbrannten Kraftstoffen des Motors, sowie nach außen gegen Schmutz und (Spritz-)Wasser ab. Innerhalb des Kunststoffbauteils wird auf der kalten Ansaug-Seite die Kühlmittelpumpe aufgenommen und das Kühlmittel verteilt.
Zur schwingungstechnischen Entkopplung und Reduzierung von Schallemissionen ist das Kunststoffbauteil auf der heißen Krümmer-Seite entkoppelt. Um das Cover mit dem Zylindergehäuse zu verschrauben und dennoch zu entkoppeln, wurden Verbindungselemente vom Typ Honsel soundFIX M6 eingesetzt. In Bild 1 ist der Aufbau der Entkopplung im Schnitt an einer Verschraubung dargestellt. Beim Anziehen der Schraube wird das Gehäuse über den Elastomer-Puffer, bis zum Anschlag der Stahlhülse über die Dichtung an das Zylinderkurbelgehäuse (ZKG) gepresst.
Die Anforderung einer guten Abdichtung, durch eine hohe Vorspannung des Covers und die Anforderung einer möglichst guten Entkopplung, durch eine möglichst weiche Anbindung stellen einen Zielkonflikt dar. Um beide Anforderungen möglichst gut abzudecken, muss die Vorspannkraft zur Abdichtung des Covers optimal genutzt werden. Simulativ wurden verschiedene E-Module und Abmessungen sowie Formen der Dichtung untersucht. Durch die Gestaltung der Dichtung mit zwei Lippen wird die Verpressung und damit auch die Dichtwirkung erhöht. Durch die doppelte Lippe wird ein Verkippen oder Umknicken der Dichtung verhindert.
Mittels FEM-Simulation wurde die Verpressung der Dichtung zum Kurbelgehäuse hin untersucht. Die Realisierung einer gleichmäßigen und hohen Verpressung ist in den gekrümmten Bereichen der Ausgleichswellen schwierig. Durch Anpassung der Steifigkeitsverteilung des Covers konnte die Verpressung homogenisiert werden. In Bild 2 ist die Pressungsverteilung der Dichtung zum Kurbelgehäuse dargestellt.
Die beiden kritischsten Stellen im Bereich der Krümmungen wurden vergrößert dargestellt. Im oberen Bereich des Covers ist die Verteilung des Kühlmittels erkennbar. Als Anforderungen für die Dichtung ergeben sich im Bereich des Kühlmittels 3 bar Innendruck und für die Abdichtung der restlichen Dichtung 1,3 bar Innendruck gegenüber dem Blow-By des Öl/Luft Gemisches. Die Pressung in der so gestalteten Kontaktfläche unterschreitet in keinem Punkt 0,6 MPa und erfüllt damit diese Bedingungen.
Die entstehenden Spannungen im Cover wurden ebenfalls mittels einer FEM Simulation untersucht. Aufgrund der Materialeigenschaften der Kunststoffkomponente wurden Zug- und Druckspannungen getrennt voneinander betrachtet, da die zulässige Druckspannung bei 130 °C 240 MPa, die zulässige Zugspannung jedoch lediglich 110 MPa beträgt. Die höchsten Bauteilspannungen entstehen dabei beim schnellen Aufheizen, aufgrund der unterschiedlichen Wärmedehnungen und Bauteiltempe- raturen. In Bild 3 ist die Zugspannungsverteilung dargestellt. Besonders in den Bereichen der Krafteinleitungspunkte kommt es dabei auf der Oberseite des Bauteils zu maximalen Zugspannungen von 55 MPa. Da auch die Druckspannungen bei der gewählten Konstruktion deutlich unter den zulässigen Werten lagen, stand der Umsetzung nichts im Wege.
3 Umsetzung
Vor der kostenintensiven Werkzeugfertigung wurden die Simulationsergebnisse mittels Probekörper validiert. In Bild 4 sind die Dichtung, die Entkopplungselemente, das Dummy-Kurbelgehäuse (KGH) und der selbst entwickelte, spritzgegossene Probekörper dargestellt.

Bild 4. Probekörper mit Entkopplungselementen, Dichtungen und Kurbelgehäuse-Dummy. Grafik: Fraunhofer ICT
Nach der Montage wurde die Kavität im KGH im heißen und kalten Zustand mittels Druckwasser beaufschlagt.
Nach dem erfolgreichen Funktionsnachweis des entwickelten Dichtsystems wurden die Werkzeuge für das Cover aus glasfaserverstärktem Phenolharz gefertigt, die Rohteile hergestellt und die Qualität am Fraunhofer ICT, anhand einer optischen Vermessung, überprüft. Aufgrund von Fertigungsrestriktionen, einem Hinterschnitt beim Spritzgießen, wurde das Seitenteil im wasserführenden Bereich aus mehreren Teilen zusammengesetzt. Die einzelnen Bauteile wurden am Fraunhofer ICT zur Gehäusekomponente montiert und die Dichtigkeit anhand von Versuchen erfolgreich nachgewiesen. Mit der vollständigen Validierung ist die Entwicklung des neuen Leichtbauteils abgeschlossen. Im nächsten Schritt wurden die Bauteile an den Konsortialführer FEV versendet, wo alle Komponenten zu einem Gesamtmotor aufgebaut wurden. In Bild 5 sind die im SLM-Verfahren hergestellten Bauteile Kurbelgehäuse und Halter der Abgasanlage sowie das Kunststoffbauteil dargestellt. Nach der abgeschlossenen Montage sind im Rahmen des Projekts umfangreiche Testprogramme auf dem Motorenprüfstand von FEV erfolgreich durchgeführt worden. Das Absolvieren dieser Versuche erbrachte den Funktionsnachweis des Duromer-Aluminium Hybrid-Kurbelgehäuses und stellt den letzten Entwicklungsschritt in diesem Forschungsprojekt dar.
Das Verbundprojekt „LeiMot – Gewichtsreduzierung eines Verbrennungsmotors durch Strukturoptimierung und Verwendung von Hybrid Metall- und Kunststoff-Komponenten“ wurde unter dem Förderkennzeichen 19/18002C vom BMWI aufgrund eines Beschlusses des Deutschen Bundestages gefördert. Verbundpartner sind FEV Europe GmbH, RWTH Aachen University, Fraunhofer-Gesellschaft, FH Aachen, Volkswagen AG, INPECA GmbH und WFS.
Literatur
- Lindemann, B.; Ghetti, S.; Bey, R. et al.: Additive Fertigung bei modernen Verbrennungsmotoren, MTZ – Motortechnische Zeitschrift 81, 40–45 (2020). https://doi.org/10.1007/s35146–020–0321-x
- Berg, L.: Phenolharzspritzgießen – Anwendungen in modernen PKW Antriebsstrangkomponenten. VDI-Konferenz Hochleistungskunststoffe in der Anwendung, Berlin, 2017
Sebastian Bucherer, M. Sc.
Johannes Liebertseder, M. Sc.
Steffen Reuter, M. Sc.
Dipl.-Ing. Stefan Heß
Dr.-Ing. Lars Berg
Fraunhofer-Institut für Chemische Technologie ICT
Neue Antriebssysteme
Rintheimer Querallee 2, 76131 Karlsruhe
sebastian.bucherer@ict.fraunhofer.de
www.ict.fraunhofer.de
Dr.-Ing. Alexander Zabirov
FEV Vehicle GmbH
Leichtbau & Vorentwicklung
Zieglerstr. 15, 52078 Aachen
zabirov@fev.com
www.fev.com