Die Forschungsplattform von morgen
Das FlexCAR besteht aus einer autonom gesteuerten Fahrzeugplattform für die Mobilität von morgen, welche UseCase – gesteuert als Forschungsdemonstrator fungiert, um neue technologische Features unmittelbar aus dem Forschungsstadium nach dem Plug-and-Play – Prinzip gezielt zu implementieren. Damit kann eine frühzeitige Validierung im Hinblick auf ein künftiges Anwendungspotential ermöglicht werden. Offene Soft- und Hardwareschnittstellen sind hier berücksichtigt, beziehungsweise werden weiterentwickelt.
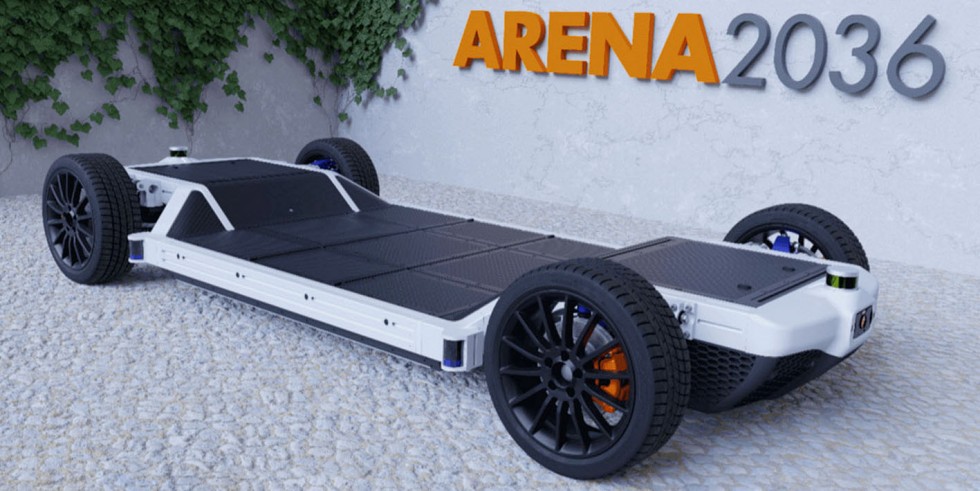
Bild 1. Rolling Chassis.
Foto: www.arena2036.de
FlexCAR – the Research Platform of Tomorrow
Abstract: FlexCAR exists of an autonomous driven vehicle platform for the mobility of tomorrow. Usecase-guided as a research platform, it enables to implement new technological features after the plug-and-play principle. Therefore, an early validation can be setup concerning potential future application. Open software and hardware interfaces are included and will be developed further.
1 Einleitung und Motivation
Smartphones haben unsere Nutzung der Telefonie grundlegend geändert. Umfangreiche Büro- und Datenkommunikation ist von jedem Ort und zu jeder Zeit möglich. Standardisierte und offene Softwareschnittstellen (API) ermöglichen Drittanbietern, neue Applikationen auf Basis der bestehenden Hardware anzubieten. Hier setzt das durch das Bundesministerium für Forschung und Bildung finanzierte Förderprojekt „FlexCAR“ an, in dem mit einer standardisierten autonomen Fahrzeugplattform ein Forschungsdemonstrator entwickelt wurde, der neue technologische Features unmittelbar aus dem Forschungsstadium nach dem Plug-and-Play-Prinzip gezielt implementieren lässt und eine Validierung im Hinblick auf ein künftiges Anwendungspotenzial ermöglicht.
Im Förderprojekt arbeiten 12 Verbundpartner aus Industrie und Wissenschaft zusammen mit einer Projektlaufzeit von fünf Jahren (10/18 – 09/23).
Offene Soft- und Hardwareschnittstellen erlauben hier die Wandlung starrer Lieferketten hin zu flexiblen Lieferantennetzwerken. Weiterhin lässt sich mit dieser standardisierten FlexCAR-Plattform eine Vielzahl an Anwendungszwecken cyberphysisch entwickeln. Die Projektarbeiten finden auf der Technikumsfläche der ARENA2036 auf dem Campus der Universität Stuttgart statt.
In diesem Veröffentlichungsbeitrag Teil II werden in Fortsetzung zu den bereits im Teil I veröffentlichten fachlichen Schwerpunkten (wt Werkstattstechnik online, Band 112 (2022), Nr. 9; S. 601 – 606) weitere fachliche Schwerpunkte aus dem Projekt FlexCAR im Detail vorgestellt.
1.2 Struktur Verbundprojekt
Vier Themenbereiche bilden den inhaltlichen Projektrahmen des FlexCAR-Projektes.
Im Themenbereich 1 – „Rolling Chassis“ wird eine elektrisch angetriebene und über 5G angesteuerte Forschungsplattform mit zugänglicher und offener Soft- und Hardware entwickelt. Diese Plattform dient als gemeinsame Basis für die FlexCAR-Einzeltechnologien. Erweitert wurde diese durch eine modular aufsetzbare Bodenplatte, welche die Schnittstelle zum Interieur herstellt und dem Themenbereich 2 für verschiedene Anwendungsfälle und Interieurstudien zur Verfügung steht.
Der Schwerpunkt des Themenbereichs 2 – „Interieur und cyberphysischer Einstieg“ baut auf den Themen des Themenbereichs 1 auf. So werden hier verschiedene interieurbezogene Use Cases betrachtet, wie zum Beispiel „Working during driving autonomous“ und „Relaxing during driving autonomous“ sind. Bucht beispielsweise ein Kunde oder eine Kundin eine Fahrt über eine App, wird diese Anfrage über 5G/6G oder GPS gesendet und verarbeitet. Entsprechend der Kundenanforderungen wird ein FlexCAR-Fahrzeug zugewiesen und dem Kunden beziehungsweise der Kundin die genauen Angaben über Ort und Zeit übermittelt. Das Fahrzeug trifft zum vereinbarten Zeitpunkt am vereinbarten Ort ein und hält Ausschau nach dem Kunden oder der Kundin. Über nach außen gerichtete Kameras kann mit dem Fahrzeug Kontakt aufgenommen werden. Es wird nur berechtigten Personen über Smartphone, Fingerabdruck oder Eyetracking Zutritt gewährt und die Fahrt kann entsprechend abgerechnet werden.
Im Themenbereich 3 – „Flexible Produkt- und Produktionskonzepte“ wird das Produktionskonzept von FlexCAR betrachtet. Die beiden Drivemodule und das Energymodul vom FlexCAR sollen hier in den Fokus der produktionstechnischen Betrachtung rücken: zum Beispiel die Fragestellungen nach passenden Blech- oder Strukturprofilierungen im Rahmen des Chassis. Mithilfe standardisierter Schnittstellen wird das FlexCAR-Chassis Teil eines cyberphysischen Produktionssystems und kann als weiterer Use Case während der Fertigung beispielsweise als fahrerloses Transportsystem eingesetzt werden und somit heutige Transport- und Fördertechnik im Werk ersetzen.
Der Themenbereich 4 – „Offener Entwicklungsprozess modularer Fahrzeuge“ beschäftigt sich mit der Umsetzung eines der wesentlichen Kriterien vom FlexCAR: dem offenen Entwicklungsprozess. Ziel ist es, offene Schnittstellen bei Hard- und Software zu entwickeln und umzusetzen, wodurch neue Geschäftsmodelle etabliert werden können. FlexCAR ist damit viel mehr als nur ein neues Fahrzeugkonzept. Es bietet eine Forschungsplattform für die zentrale Entwicklung und Fertigung modularer autonomer Fahrzeugsysteme Indoor und Outdoor.
1.3 Ausgewählte inhaltliche Projektschwerpunkte
1.3.1 Neue Profilstrukturen für das FlexCAR-Chassis
Motivation
Das im FlexCAR-Projekt entwickelte Rolling Chassis stellt eine fahrbare, upgrade-fähige sowie modulare Fahrzeugplattform dar, die rein elektrisch oder mittels Brennstoffzelle betrieben werden kann. Der aktuelle FlexCAR-Prototyp folgt einem hoch integrativen Konzeptansatz, der in einem zweiten Schritt durch flexible, bedarfsorientierte Produktionskonzepte optimiert wird. Der Fokus liegt hierbei auf der Weiterentwicklung des Energiespeichermoduls (Energy-Modul), welches die Rahmenstruktur für das Hochvoltspeichersystem beziehungsweise für die Brennstoffzelle mit Wasserstoff-Tanks bildet. Neuartige Anforderungen werden dabei berücksichtigt, die aus dem Strukturwandel in der Automobilindustrie hin zu einer nachhaltigen, elektrischen Mobilität sowie aus kürzeren Entwicklungs- und Produktlebenszyklen resultieren. Die hier entwickelten Profilstrukturen sollen möglichst gewichtsoptimiert, gut rezyklierbar, bedarfsgerecht gestaltet und einfach anpassbar sein.
Vorgehen
Im Projekt werden zwei verschiedene Ansätze zur Umsetzung einer flexiblen Rahmenstruktur für die Wechselspeicherkonzepte untersucht. Der Projektpartner Constellium entwickelt eine modulare Bauweise aus Aluminium-Strangpressprofilen sowie eine intelligente Auswahl von nachhaltigen Legierungen. Alternativ wird vom Projektpartner Trumpf eine reine Aluminium-Blechbauweise mit innovativen Fügekonzepten untersucht. Die hierbei eingesetzte werkzeugarme Fertigung aus Laserschneiden, Biegen, Laserschweißen und Laserauftragschweißen (LMD) ermöglicht eine bedarfsorientierte Funktionalisierung und eine einfache Anpassung an geänderte Rahmenbedingungen.
Aktueller Stand
Die simulative Optimierung des Energy-Moduls aus Aluminium-Strangpressprofilen hinsichtlich einer modularen Bauweise bei gleichzeitiger Erfüllung von zulassungsrelevanten Crashanforderungen, insbesondere des Seitenpfahltests, zeigt, dass durch die Einbringung lokaler Verstärkungsstrukturen eine Gewichtsreduktion des Schwellers bei verbessertem Crashverhalten realisiert werden kann. Die intelligente Kombination von Aluminium-Legierungen sorgt nicht nur für die erforderlichen Eigenschaften der Bauteile zwischen Duktilität und Extrudierbarkeit, auch das Schwellerprofil selbst muss bei massiven Deformationen die Systemintegrität garantieren. Die beiden Einlegerprofile im Schweller, die je nach Konfiguration modular in den Schweller integriert werden, bestehen aus einer hoch-performanten HSA6 Aluminiumlegierung mit sehr guter Rezyklierbarkeit und leisten damit einen erheblichen Beitrag zur Gewichtsreduktion und zur Nachhaltigkeit. Der Extrusionsknoten im Eckbereich des Energy-Moduls sorgt für die reversible Anbindung des Drive-Moduls an das Energy-Modul und ist bezüglich der Eigensteifigkeit dahingehend optimiert, dass in relevanten Crashfällen ein Versagen der Verbindung verhindert wird. Die eingesetzten Fügeverfahren sorgen für die Möglichkeit einer sortenreinen Trennung beziehungsweise für die Upgrade-Fähigkeit des Legierungs-Mixes.
Um die Crashanforderungen auch in reiner Blechbauweise zu erfüllen, wurden die crashrelevanten Profile aus mehreren gebogenen Blechen mittels Laserstrahlschweißen zu einem Mehrkammerprofil zusammengefügt. Durch den Einsatz der neuartigen Trumpf Multifokus-Technologie kann hierbei die Porenentstehung in der Schweißnaht weitestgehend vermieden werden, was gasdichte Schweißnähte ermöglicht [1]. Teilweise werden die Bleche mithilfe von Steckverbindungen positioniert. Dies erlaubt ein flexibles und vorrichtungsarmes Fügen. Der Wegfall des Flansches spart zusätzlich Gewicht ein.
In der herkömmlichen Fertigung wird der Eckknoten in der Regel als separates Bauteil, zum Beispiel als Gussteil, hergestellt und muss aufgrund von Passproblemen meist aufwendig nachbearbeitet werden. In diesem Projekt wird der Eckknoten durch intelligente Verschachtelung der Blechprofile sowie einer in diesem Projekt entwickelten neuartigen Klebetechnik realisiert. Hierfür wird eine LMD-Naht, deren Höhe genau dem Spaltmaß zwischen den Profilen entspricht, auf eines der zu verklebenden Profile aufgetragen und die Profile werden anschließend zusammengesteckt. Auf diese Weise können einerseits Toleranzen im Spaltmaß ausgeglichen werden, andererseits wird überall ein konstantes Spaltmaß gewährleistet. Das konstante Spaltmaß und die sichere Positionierung ermöglichen nun eine prozesssichere Klebstoffinjektion und eine zuverlässige Verbindung der Profile ohne kritischen Wärmeeintrag.
Ausblick
Sowohl die Rahmenstruktur aus Strangpressprofilen als auch die Rahmenstruktur in reiner Blechbauweise werden bei den Partnern gefertigt und anschließend als physische Demonstratoren in der ARENA2036 in Stuttgart-Vaihingen ausgestellt.
1.3.2 Sensorintegrationen am FlexCAR
Motivation
Durch die Integration von Sensoren im Rolling Chassis des Projektes FlexCAR soll ein update- und upgradefähiges Fahrzeug realisiert werden. Hierzu zählt einerseits die Sensorik für das autonome Fahren als auch die Verwendung von Sensoren zur Strukturüberwachung und die Integration von Zusatzfunktionen.
Vorgehen
Im FlexCAR Rolling Chassis sind eine Vielzahl unterschiedlicher Sensoren verbaut. Hierzu zählen neben der Umfeldsensorik wie Radar, Lidar, Ultraschall und Kameras auch Sensoren zur Erfassung der Fahrzeugbewegung wie Raddrehzahlsensoren und eine inertiale Messeinheit (IMU). Anhand dieser Sensoren können unter anderem verschiedene Verfahren zur Fahrzustandsschätzung und Lokalisierung implementiert und getestet werden. Zusätzlich wurde vom Institut für Flugzeugbau der Universität Stuttgart die Integration von Sensorik und Zusatzfunktionen in Strukturbauteile dazu genutzt, das autonome Fahren sicherer zu gestalten. Im Allgemeinen ist es essentiell, dass die für das autonome Fahren genutzte Sensorik genau kalibriert ist. Kommt es zu einer geringen Lageänderung der Sensorik durch äußere Einflüsse wie zum Beispiel Parkrempler, kann es leicht zu Unfällen kommen. Daher wurde die konventionelle, metallische Halterung der Radarsensoren ersetzt. Hierzu kam eine Leichtbaulösung aus kohlenstofffaserverstärkten Kunststoff (CFK) zum Einsatz, in dessen Lagenaufbau ein Sensorband mit drei mikroelektromechanischen Systemen (MEMS) integriert wurde (Bild 3). Zusätzlich wurde die Kunststoffmatrix des Verbundwerkstoffs mit reduziertem Graphenoxid (rGO) dotiert, um eine höhere Wärmeleitfähigkeit zu ermöglichen [2, 3] und so ein mögliches Überhitzen der genutzten Radarsensoren im Betrieb zu vermeiden.
Aktueller Stand
In einem Ansatz zur Fahrzustandsschätzung und Lokalisierung wurden die fahrzeuginternen Raddrehzahl- und Lenkwinkelsensoren sowie die IMU verwendet [4]. Die Geschwindigkeits-, Ausrichtungs- und Positionsprädikition aus einem Inertialnavigationssystem wurde hierbei in einem Unscented Kalman Filter (UKF) mit den Beobachtungen aus einem raddrehzahlbasierten Odometriemodell und einer gravitationsbasierten Lageberechnung vereint. Ergänzt werden kann dieses System um die Positionsbeobachtung aus der 5G-Positionierung oder der infrastrukturkamerabasierten Lokalisierung (vgl. Kapitel 1.3.4). Lidar und Kamera finden im FlexCAR Anwendung in der Umfeldmodellierung, der Lokalisierung des Fahrzeugs und der Erkennung von Objekten im näheren Umfeld. Für die Lokalisierung wird ein Algorithmus zur simultanen Lokalisierung und Kartierung (SLAM) verwendet, welcher die Punktewolken-Daten des Lidars oder der Kamera weiterverarbeitet, um die Fahrzeugpose (Position und Ausrichtung des Fahrzeugs) relativ zur erzeugten Karte der Umgebung zu schätzen [5]. Neben der Anwendung im automatisierten Fahren finden diese Sensoren, und speziell dieser Algorithmus zur Lokalisierung und Umfeldmodellierung, in zahlreichen anderen Bereichen Anwendung, wie beispielsweise in der Robotik, der Landschaftsvermessung mittels Drohnen, oder der Verkehrsüberwachung.
Ausblick
Die unterschiedlichen Lokalisierungsmethoden werden in weiteren Schritten für die Trajektorienplanung und -folgeregelung im FlexCAR verwendet [6]. Die Verwendung von CFK mit weiteren Zusatzfunktionen wie zum Beispiel Sensorik, Additiven oder Füllstoffen bietet ein großes Potenzial zur Überwachung von Strukturbauteilen und zur Steigerung der Materialeigenschaften.
1.3.3 Implementierung gedrucktes Bedienelement mit integrierter RFID-Bauteilerkennung
Motivation
Um elektrische Komponenten wie ein Bedienelement für ein Fahrzeug kostengünstig herstellen zu können, müssen diese meist in großen Stückzahlen produziert werden. Gleichzeitig sollen diese Komponenten aber auch optisch möglichst ansprechend hinsichtlich Farbe und Design in das entsprechende Interieur des Fahrzeugs integriert werden können, was in einer entsprechend hohen Variantenvielfalt resultiert. Mithilfe von additiven Fertigungsverfahren können Design, Oberflächen und Farben von Bauteilen bei Fertigung auf der gleichen Maschine frei gestaltet werden. Weiterhin besteht die Möglichkeit, gedruckte Leiterbahnen frei im Bauteil zu platzieren und gedruckte Sensorelemente zu integrieren. Um sicherzustellen, dass bei einer hohen Variantenvielfalt von Bauteilen auch das richtige Bauteil ins jeweilige Fahrzeug eingebaut wird und wurde, ist eine kabellose Überprüfbarkeit wünschenswert.
Vorgehen
Zum Aufbau eines additiv gefertigten Bedienelements wurde das Inkjetverfahren ausgewählt, da dieses den parallelen Druck verschiedener Farben und Materialien sowie das Einbetten von Bauteilen ermöglicht. Weiterhin kann durch die Wahl geeigneter Druckparameter die Optik und Haptik von Oberflächen angepasst werden. Als Bedienfunktion werden Taster zum Beispiel zum Ein- und Ausschalten und ein Slider zum Regeln von zum Beispiel der Helligkeit von Licht integriert. Während die Sensorfunktionen und Leiterbahnen durch gedruckte Metallnanopartikel realisiert werden, übernimmt die elektrische Auswertung und Steuerung ein kommerziell erhältlicher „MPR121“ Microcontroller. Die spätere kontaktlose Erkennung des Bauteils soll über ein integriertes beschreibbares RFID-Tag basierend auf UHF-Technologie realisiert werden, welches neben dem Bauteilcode auch noch weitere Informationen beispielsweise Links zur Einbauanleitung oder Hilfestellung zum späteren Recycling enthalten kann.
Aktueller Stand
Mithilfe der Inkjettechnologie konnte ein additiv gefertigter 2D-Demonstrator eines Bedienelements (Abmessung 100 mm³ x 50 mm³ x 1 mm³) mit Taster- und Slider-Funktion aufgebaut werden (Bild 4). Dieses besteht aus einem semitransparenten schwarzen Kunststoff, gedruckten Leiterbahn- und Sensorelementen und einer elektrischen Anbindung an ein 16-poliges Flachbandkabel. Weiterhin konnte durch die Wahl geeigneter Druckparameter und -strategien die Oberfläche optisch und haptisch so weit angepasst werden, dass die Position des Tasters sichtbar, aber auch mit dem Finger erfühlbar ist. In inkjetgedruckte 3D-Objekte konnten erfolgreich RFID-Tags (Abmessung 57,1 mm³ x 5.95 mm³ x 1.3 mm³) integriert und mittels RFID-Lesegerät auf Distanz identifiziert werden. Über eine im Projekt entwickelte Benutzeroberfläche können die Daten auf dem RFID-Tag angezeigt und bei Bedarf neu beschrieben werden (Bild 4).
Ausblick
Zur Demonstration der Technologie wird ein 3D-Bedienelement mit integrierter Tast- und Slider-Funktion, einer haptischen Oberfläche und integrierten RFID-Tag aufgebaut. Während die Integration der haptischen Eigenschaften in die 3D-Geometrie bereits gezeigt werden konnte, muss der Prozess zum Aufdrucken der Sensoren und Leiterbahnen noch final optimiert werden. Das fertig gedruckte 3D-Bedienelement wird zur Demonstration in eine Armlehne integriert und zur Steuerung von Lichtelementen verwendet.
1.3.4 Integrierte onboard- und offboard- Kommunikation über 5G in die ARENA2036
1.3.4.1 Architektur des onboard- und offboard-Netzwerks
Motivation
Anforderungen an zukünftige Fahrzeuge verschieben sich zunehmend von der Hardware hin zu flexiblen Softwareinstanzen, um auf veränderte Anforderungen an Rechenressourcen durch Funktionsanpassungen, Updates oder Hardwareausfälle reagieren zu können. Flexibilität in der Entwicklung spielt dabei eine ebenso große Rolle wie Anpassungen über Updates nach dem Fahrzeug Roll-out. Die Verbesserung bestehender Algorithmen, der Austausch mit Umfeldsensorik oder auch das Einbinden externer Sensorik über die eigene Systemgrenze hinaus fordern ein hohes Maß an Flexibilität, dass mittels einer offenen Entwicklungsplattform und softwareorientierter Architektur erreicht werden kann. Updates erfolgen bereits heutzutage ohne Werkstattbesuche Over-the-Air mittels Fernwartung. Der Fernzugriff ermöglicht neben Steuerungsfunktionen auch das Teilen aller onboard-Daten für Visualisierungen. Die Kommunikation zu externen Geräten stellt zeitgleich die Mindestanforderung für die Vehicle-2-everything Konnektivität (V2X). Eine integrierte, aber flexible onboard- und offboard-Kommunikation über 5G in der Indoor – ARENA2036-Umgebung war für das FlexCAR-Projekt notwendig.
Vorgehen
Die Kommunikationsarchitektur des Rolling Chassis umfasst sowohl die interne Kommunikation (onboard) als auch die externe Kommunikation (offboard). Die onboard-Kommunikation beschreibt den Datenaustausch zwischen allen Geräten und Instanzen, die auf dem Rolling Chassis verbaut und installiert sind. Informationen werden dabei über Ethernet ausgetauscht. Durch Verwendung einer softwareorientierten Architektur (SOA) ist die Software nicht mehr an eine bestimmte Hardware gebunden und kann flexibel im System ausgeführt werden. Die SOA wird im Rolling Chassis über die Middleware Data Distribution Service (DDS) umgesetzt, unter anderem mittels RTI connext. Die Serviceschnittstellen sind im .idl Format standardisiert und werden mit zusätzlicher Information über Quality of Service (QoS) ausgetauscht. Die onboard-Kommunikation erfolgt dadurch interoperabel über Softwareinstanzen, Programmiersprachen und diversen Betriebssysteme hinweg. Eine adaptive Kompatibilität zum „Robot Operating System 2“ (ROS2), oder der „AUTOSAR“ Adaptive Plattform ist dadurch gegeben. Für die offboard-Kommunikation wird eine 5G-Verbindung zum Indoor ARENA2036-Produktionsnetzwerk hergestellt. Die Kommunikation innerhalb des ARENA2036-Netzwerks erfolgt über das Message Queing Telemetry Transport Protokoll (MQTT).
Sowohl DDS wie auch MQTT arbeiten beide nach dem Publish-Subscribe Prinzip, allerdings auf Basis unterschiedlicher Protokolle. Eine Übersetzung der Protokolle musste deshalb erfolgen. Um volle Kompatibilität zwischen den onboard- und offboard-Systemen herzustellen, wurde vom Institut für Arbeitswissenschaft und Technologiemanagement IAT der Universität Stuttgart in Zusammenarbeit mit dem Fraunhofer-Institut für Arbeitswirtschaft und Organisation IAO eine „DDS2MQTT“-Bridge entwickelt. Beliebige Nachrichten können damit aus und in das Fahrzeug geroutet werden. Zur Anbindung von eingebetteter Hardware unterstützt die Kommunikationsarchitektur neben DDS und MQTT ebenfalls das User Datagramm Protokoll (UDP). Hierdurch konnte zum Beispiel die Kommunikation zum Steuergerät für grundlegende Fahrfunktionen realisiert werden. Auch hierfür wurde eine eigene Software-Bridge entwickelt. Die Regelung der Fahrfunktionen, der Sensorik beziehungsweise Aktorik, der Datenaufbereitung und Verwertung erfolgt jeweils intern über weitere speziell entwickelte Softwareinstanzen. Die notwendige Rechenleistung wird durch vier „Nvidia Jetson AGX Xavier“ Module bereitgestellt. Die Softwarepakete arbeiten verteilt auf den Modulen, wie Bild 5 entnommen werden kann. Aufgrund der gewählten Architektur fungiert die gesamte Netzwerkkommunikation des Rolling Chassis sowohl fahrzeugintern als auch über das Indoor ARENA2036-Netzwerk als eine geschlossene Einheit.
Die Kommunikation des Rolling Chassis mit dem Indoor ARENA2036 Netzwerk erfolgt über das von Nokia installierte „5G Stand Alone“-System (5G SA) der ARENA2036. Mittels zwei Pico Remote Radio Heads die auf dem 5G Radio Interface übertragen, kann somit eine Funkabdeckung von 4000 m² erreicht werden. Eine weitere Micro Basis Station wurde zusätzlich im Outdoorbereich auf dem Parkplatz der ARENA2036 installiert, um einen unterbrechungsfreien Zellwechsel der Funkzellen zu ermöglichen. Das Core Netzwerk wurde zu einem breitbandigem 5G Core Netzwerk ausgebaut. Eine 10 Gbit Glasfaserleitung deckt die hierfür notwendigen Bandreiten ab. Das 5G Netzwerk operiert dabei mit einem Downlink von über 1 Gbit/s und 250 Mbit/s im Uplink, bei optimierten Latenzen (Round-Trip) im Bereich von 8 – 15 ms.
1.3.4.2 Externe Sensorik und offene Entwicklungsplattform
Infrastrukturseitige Sensorik zur Positions- und Hindernisbestimmung spielt eine wichtige Rolle im FlexCAR-Projekt, insbesondere beim Betrieb in Innenräumen, wo kein GPS-Signal zur Verfügung steht. Positionsbestimmung und Ortung des Rolling Chassis erfolgen dabei fahrzeugextern und werden über die 5G-Luftschnittstellen dem Fahrzeug übermittelt.
Für die Ortung mittels Kamerasystem wurden vier in der Halle der ARENA2036 montierte IP-Kameras eingesetzt. Deren Videodaten werden via 5G an einen zentralen Steuerrechner übertragen. Dort sind Perzeptionsalgorithmen implementiert, die die Position und Orientierung des Rolling Chassis sowie die Position etwaiger Hindernisse bestimmen. Dies erfolgt mittels neuronalen Netzen sowie mittels inversem perspektivischen Mapping (IPM). Die genaue Position der Hindernisse wird durch eine „Footprint”-Bestimmung mittels UND-Verknüpfung der Aufnahmen der verschiedenen Kameras ermittelt. Die erkannten Positionen und Hindernisse werden mit einer Genauigkeit von circa 5 cm durch die beschriebene Kommunikationsarchitektur an das Rolling Chassis übertragen.
Für die Lokalisierung mobiler Endgeräte hat Nokia Bell Labs außerdem ein über das 5G-Netz hinausgehendes Prototypen-System in der ARENA2036 – Halle aufgebaut. Es handelt sich dabei um Messempfänger, die 5G-Uplink-Signale empfangen und an einen Server weitergeben. Auf dem Server wird aus den Messungen mittels spezieller Algorithmen die Position des mobilen Endgeräts geschätzt. Die Daten der 5G Positionierung werden in Echtzeit an das Fahrzeug zurückgegeben.
Das Konzept der offenen Entwicklungsplattform und deren Implikation wurde im FlexCAR Projekt von DXC untersucht. Der softwaredefinierte Ansatz einer offenen Entwicklungsplattform fördert die Open-Source- und Crowdkollaboration mit dem einhergehenden inhärenten Innovationspotenzial. Gleichzeitig finden grundlegende Veränderungen des digitalen Lebenszyklusmanagements und der Software-Lieferkette statt. Es werden neue Prozesse wie DevOps in die Fahrzeugindustrie integriert, zusammen mit Over-the-Air-Updates (OTA). Um die technische Machbarkeit zu zeigen, konzipierte DXC eine Pilotanwendung zur OTA-Softwareaktualisierung unter Verwendung der eSync-Technologie der Firma Excelfore. Als Beispiel für eingebettete Funktionen wählte DXC das Objekterkennungssystem aus, das auf dem Rolling Chassis zur Verwendung kam. Über eine neue Version der Objekterkennungssoftware konnte erfolgreich eine Verbesserung der ADAS-Funktionalität durch das OTA-Software-Update getestet werden. In Zusammenarbeit mit der Firma Asvin untersucht DXC die Integrität mit Bezug Cyber-Security im Ökosystem mehrstufiger Zulieferer- und OEM-Softwareketten. Mittels einer automatisierten Ende-zu-Ende Prozesskette hinsichtlich Entwicklung, Bereitstellung/Freigabe und Installation und der Asvin-Blockchain-Dokumentation konnte exemplarisch gezeigt werden, wie eine sichere auditierbare Softwarelieferkette implementiert werden kann.
2 Fazit und Ausblick
Die in diesem Beitrag Teil II ausgewählten Schwerpunktthemen zeigen zusammen mit den Themen aus dem Beitrag Teil I, dass man mit diesen neuen innovativen Ansätzen und Methoden eine zielgerichtete, schnelle und effiziente Auslegung künftiger Mobilitätsformen im Hinblick auf ein automatisiertes beziehungsweise autonomes Fahren mittels der Forschungsplattform FlexCAR darstellen kann. Die entwickelten softwareorientierten Architekturen bieten eine flexible Zuweisung von Programmen an die Hardware FlexCAR und heben damit die Modularität des FlexCAR-Konzeptes auf ein neues Level, was zusammen mit der Breitbandkommunikation einen vollständigen Datenaustausch für eine Nutzung von Edge- oder Cloudcomputing ermöglicht. Die geschaffene offene FlexCAR-Forschungsplattform mit ihren neuen Wechselspeicher- und Fertigungskonzepten bietet mit der Einbettung der VR/AR- Technologie einen idealen Raum für weitergehende Forschungs- und Entwicklungsarbeiten, baureihen- und wettbewerbsunabhängig.
Danksagung: Das Forschungsprojekt „FlexCAR“ wird durch das Bundesministerium für Bildung und Forschung (BMBF) in der Fördermaßnahme „Forschungscampus – öffentlich-private Partnerschaft für Innovationen“ (Förderkennzeichen 02P18Q640 bis 02P18Q649) gefördert und vom Projektträger Karlsruhe (PTKA) betreut. Die Verantwortung für den Inhalt dieser Veröffentlichung liegt bei den Autoren. Die Autoren und involvierten Verbundprojektpartner danken dem Fördergeber sowie dem Projektträger Karlsruhe PTKA für deren freundliche Unterstützung.
Literatur
- Möller, M.et al.: „Spatially tailored laser energy distribution using innovative optics for gas-tight welding of casted and wrought aluminum alloys in e-mobility“. Journal of Laser Applications 34, 042015 (2022), https://doi.org/10.2351/7.0000735
- Ackermann, A. C.; Fischer, M.; Wick, A.; Carosella, S.; Fox, B. L.; Middendorf, P.: „Mechanical, Thermal and Electrical Properties of Epoxy Nanocomposites with Amine-Functionalized Reduced Graphene Oxide via Plasma Treatment.“ J. Compos. Sci., 2022, 6 (6), 153, doi: 10.3390/jcs6060153
- Ackermann, A. C.; Fischer, M.; Wick, A.; Carosella, S.; Fox, B. L.; Middendorf, P.: „Investigation of the thermal and mechanical properties of composite materials with amine-functionalized reduced graphene oxide inclusions“. In: Vassilopoulos, A.; Michaud, A. (Hrsg.): Proceedings of the 20th European Conference on Composite Materials – Composites Meet Sustainability, 1, 968–975, doi: 10.5075/epfl-298799_978–2–9701614–0–0
- Kiebler, J., et al.: Novel Approach for Vehicle-Self-Localization. In: 22. Internationales Stuttgarter Symposium: Automobil-und Motorentechnik, S. 75–88. Wiesbaden: Springer Fachmedien Wiesbaden, 2022
- Cadena, C.; Carlone, L.; Carrillo, H.; Latif, Y.; Scaramuzza, D.; Neira, J.; Reid, I.; Leonard, J. J.: „Past, present, and future of simultaneous localization and mapping: Toward the robust-perception age,” IEEE Transactions on Robotics, 32 (2016) 6, pp. 1309–1332. https://doi.org/ 10.1109/TRO.2016.2624754 (p. 11), (p. 12)
- Saljanin, M. et al.: A model predictive control approach for highly automated vehicles in urban environments. Automot. Engine Technol. 7, 105–113 (2022). https://doi.org/10.1007/s41104–022–00103-x
Dr. Michael Lahres
Jan Daßler
Mercedes-Benz AG, RD/RTC
Hardware & Digital Technologies
Leibnizstr. 2, 71032 Böblingen
Tel. +49 176 / 309-34786
michael.lahres@mercedes-benz.com
jan.dassler@mercedes-benz.com
www.mercedes-benz.com
Florian Hermann
Dr. Mauritz Möller
Trumpf Laser- und Systemtechnik GmbH
Johann-Maus-Str. 2, 71254 Ditzingen
Tel. +49 7156 303-35600
www.trumpf.com
Dipl.-Ing. Jochen Wiedemann
Constellium Singen GmbH
Alusingen-Platz 1, 78224 Singen
Tel. +49 7731 / 80-2908
jochen.wiedemann@constellium.com
www.constellium.com
Johannes Koppenborg
Nokia Solutions and Networks GmbH & Co. KG
CX Enterprise Digital Industries
Magirusstr. 8, 70469 Stuttgart
Tel. +49 160 909 51051
j ohannes.koppenborg@nokia.com
www.nokia.com
Dr.-Ing. Bernhard Polzinger
Robert Bosch GmbH
Zentrale Forschung und Vorausentwicklung
Robert-Bosch-Campus 1, 71272 Renningen
bernhard.polzinger@de.bosch.com
www.bosch.de
Daniel Kessler, M. Sc.
Balluff GmbH
Innovation
Schurwaldstr. 9, 73765 Neuhausen a. d. F.
daniel.kessler@balluff.de
www.balluff.de
Miralem Saljanin
Institut für Fahrzeugtechnik Stuttgart (IFS)
Universität Stuttgart
Pfaffenwaldring 12, 70569 Stuttgart
Tel. +49 711 / 685-65888
miralem.saljanin@ifs.uni-stuttgart.de
www.ifs.uni-stuttgart.de
Jochen Kiebler
Forschungsinstitut für Kraftfahrwesen und Fahrzeugmotoren Stuttgart (FKFS)
Pfaffenwaldring 12, 70569 Stuttgart
Tel. +49 711 / 685-65888
jochen.kiebler@fkfs.de
www.fkfs.de
Annika Ackermann
Institut für Flugzeugbau (IFB) Universität Stuttgat Pfaffenwandring 31, 70569 Stuttgart Tel. +49 711 / 685-62402 ackermann@ifb.uni-stuttgart.de www.ifb.uni-stuttgart.de
Jens Wizl, M. Sc.
Institut für Arbeitswissenschaft und Technologiemanagement
Universität Stuttgart
Nobelstr. 12, 70569 Stuttgart
Tel. +49 160 8941873
jens.wizl@iat.uni-stuttgart.de
Lukas Block, M. Sc.
Fraunhofer-Institut für Arbeitswirtschaft und Organisation
Nobelstr. 12, 70569 Stuttgart
Tel.+49 711 970 2173
lukas.block@iao.fraunhofer.de
Dipl. Inf. wiss. Jürgen Dettling
DXC Technology
Schickardstr. 32, 71034 Böblingen
juergen.dettling@dxc.com
Dr. Thomas Riemer
Kun Gao, M. Sc.
Dr. Dan Greiner
Forschungsinstitut für Kraftfahrwesen und Fahrzeugmotoren Stuttgart
Pfaffenwaldring 12, 70569 Stuttgart
Tel. +49 711 685-68131 | -61578 | -65743
thomas.riemer@fkfs.de
kun.gao@fkfs.de
dan.greiner@fkfs.de
Nadine Reusch
Ingenieurbüro Reusch
Tel. +49 176 67768952
info@reuschconsulting.de
www.reuschconsulting.de