Wie ein Cobot bei Thales nachts die Produktion forciert
In der Nacht, wenn die Produktionsmitarbeiter von Thales Deutschland längst in ihren Betten liegen, herrscht rege Betriebsamkeit im Fertigungswerk: Dann hat ein kollaborierender Roboter die dritte Schicht an einer CNC-Maschine des Weltmarktführers für Wanderfeldröhren-Verstärker übernommen.
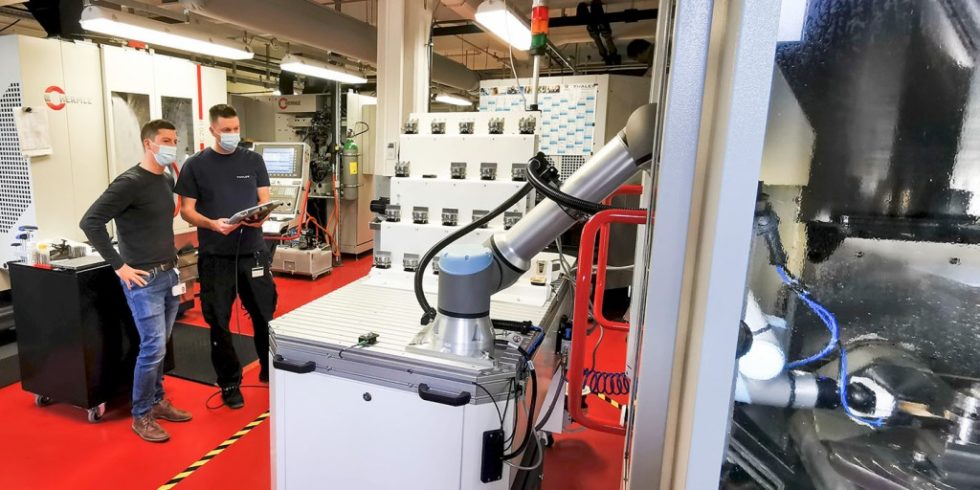
Thales in Ulm nutzt ein mobiles System mit einem Cobot, um eine Fräsmaschine automatisch zu beladen.
Foto: Thales
Dabei handelt es sich um einen Cobot „UR10e“, der an einem hochproduktiven Bearbeitungszentrum „Hermle C 20 U“ stationiert ist. „Automatisierung war für uns die einzige Lösung.“ So lautet das Statement von Marc Prestele, verantwortlich für die mechanische Fertigung bei Thales Deutschland in Ulm. Er spricht aus, was viele seiner Berufskollegen in seiner Branche umtreibt: Der Fachkräftemangel bleibt eine der größten Herausforderungen in der produzierenden Industrie.
Nächtliches Duo: Cobot und Fräsmaschine
„Es ist fast unmöglich, neue Mitarbeiterinnen oder Mitarbeiter für die Bedienung von Fräsmaschinen zu finden“, so Prestele. Dies ist mittlerweile ein Dauerzustand, der beim internationalen Thales-Kompetenzzentrum für Raumfahrtkomponenten und Subsysteme im Laufe der Zeit zum Umdenken geführt hatte: Um die anhaltend hohe Nachfrage nach Wanderfeldröhren-Verstärkern für den Einsatz in Raumfahrtanwendungen wie geostationären Satelliten befriedigen zu können, musste sich Thales nach Alternativen umsehen.
Gemeinsam mit dem Systemintegrator für Robotikanwendungen, der Firma Voith Robotics, entstand eine ganz besondere Idee: „Ein Cobot sollte die Fräsmaschine in der Nacht automatisch bedienerlos beladen.“ Anstatt die CNC-Maschine – wie bisher – mit Mitarbeitern im Zwei-Schicht-Betrieb beschicken zu lassen, sollte das Fräsen künftig mithilfe eines Cobots im Drei-Schicht-Betrieb ablaufen. Die Vorgehensweise ist folgende: In den Tagesschichten entfernen die Bediener das System vom Bearbeitungszentrum, um sie manuell zu beladen. Nach Feierabend wird an der Söflinger Straße 100 in Ulm der Cobot wieder aktiv.
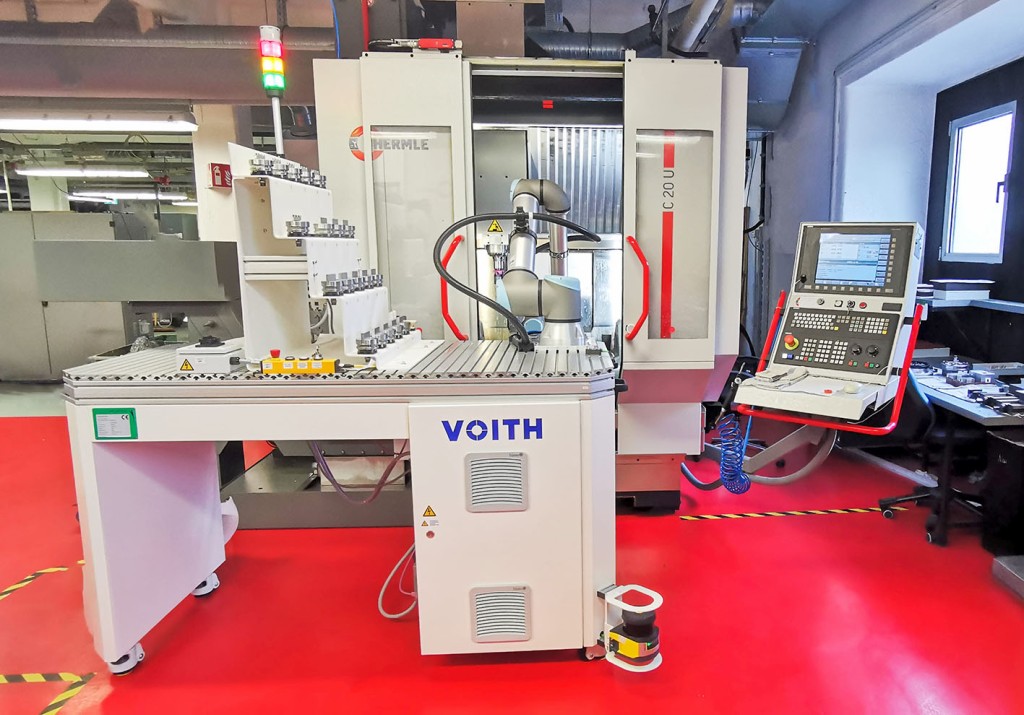
Das mobile System mit einem Cobot von UR übernimmt am Bearbeitungszentrum statt der menschlichen Mitarbeiter die dritte Schicht.
Foto: Thales
Der für das Projekt gewählte Partner – Voith Robotics – ist ein zertifizierter Systemintegrator des Cobot-Anbieters und ein globaler Spezialist für die Analyse und Integration von Robotersystemen sowie für die Planung von intelligenten Automatisierungslösungen. Neben dem gebündelten Know-how in den Bereichen Prozessberatung, künstliche Intelligenz, digitale Apps und Servicelösungen liegen 150 Jahre Erfahrung aus den etablierten Konzernbereichen der Voith Group vor, die verschiedene Zielmärkte wie Metallverarbeitung, Maschinenbau und Elektronik betreffen. Die Muttergesellschaft ist ein weltweit agierender Technologiekonzern. Gegründet 1867, ist Voith heute mit mehr als 20.000 Mitarbeitern, 4,2 Milliarden Euro Umsatz und Standorten in über 60 Ländern der Welt eines der großen Familienunternehmen Europas.
Traglast und Reichweite passen zum Bauteilspektrum
„Wir haben den Markt sondiert und uns schließlich für einen kollaborierenden Roboter von Universal Robots (UR) entschieden“, erinnert sich der Thales-Verantwortliche. „Die Cobots des dänischen Weltmarktführers sind für ihre Leistungsfähigkeit bekannt und haben sich in der Praxis bewiesen“, so Prestele weiter. „Wir haben uns für einen UR10e ausgesprochen: Er bot in Sachen Traglast und Reichweite das beste Leistungsverhältnis, denn die Reichweite war für den Einsatz besonders wichtig.“
Der Cobot-Hersteller UR wurde 2005 gegründet, um Robotertechnologie durch die Entwicklung leichter, benutzungsfreundlicher sowie preisgünstiger und flexibler Industrieroboter allen Interessenten zugänglich zu machen. Seit der erste Roboter 2008 auf den Markt kam, hat das Unternehmen ein beträchtliches Wachstum erfahren und verkauft seine benutzungsfreundlichen Roboterarme mittlerweile weltweit. Der Spezialist hat seinen Unternehmenssitz im dänischen Odense und verfügt weltweit über zahlreiche regionale Niederlassungen. 2019 wurde ein Umsatz von rund 248 Millionen US-Dollar erzielt (www.universal-robots.com/de).
Mit den Erkenntnissen aus der Marktsondierung im Gepäck, implementierte Thales gemeinsam mit dem Integrator ein mobiles System aus Cobot und dem Greifer „Hand-E“ von Robotiq mit Kraftmessung vor der Fräsmaschine. Thomas Meier, Verantwortlicher für die Integration bei Voith Robotics, geht ins Detail: „Die hohe Sensitivität des UR10e und eine spezielle Führung am Greifer erlauben es, dass sich das Robotersystem eigenständig kalibriert und die Beladeposition in der Maschine erkennt.“
Flexibilität in der Produktion dank Roboterbeladung verbessert
Der Greifer des Cobots öffnet und schließt die Türen der Fräsmaschine, während eine Greifer-Eweiterung den Werkzeugträger spannt, entspannt und positioniert. Die zusätzliche Kraftmessung erlaubt dabei das Greifen der Spanner sowie der Teile und erkennt, wann ein Platz für ein Werkstück leer ist. In dem Moment, in dem die Spanner aufgenommen werden, bewegt sich der Roboter nicht. Daher kann die Torsion in den Roboter-Achsen, die durch den integrierten Kraft-Momenten-Sensor gemessen wird, für diese Anwendung nicht genutzt werden. Weil das mobile System nur knapp 33 Kilogramm wiegt, lässt es sich Meier zufolge „problemlos beiseitestellen, wenn der menschliche Bediener seine Tagesschicht beginnt“.
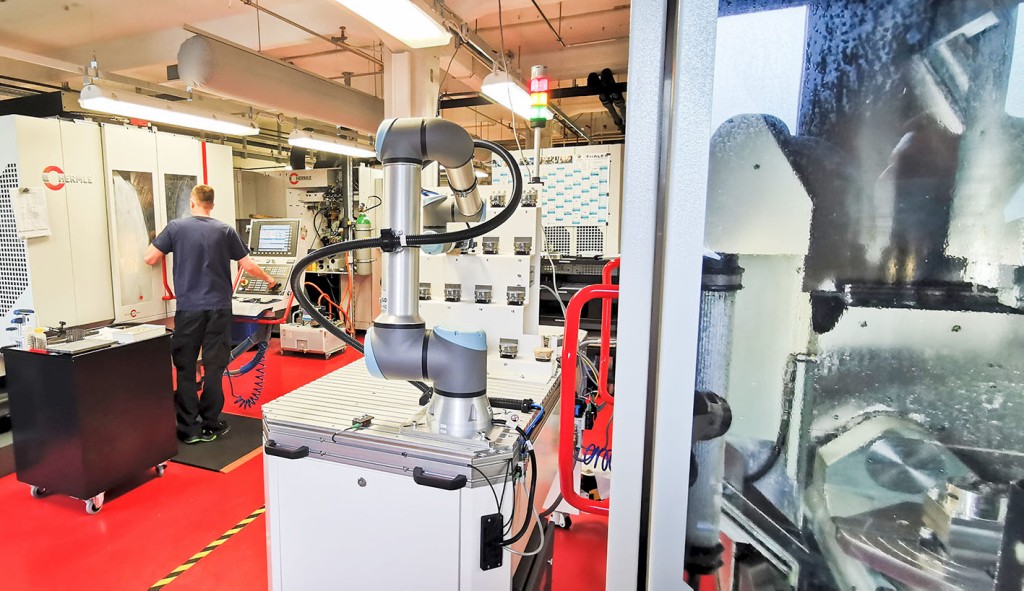
„Der Dreischichtbetrieb lastet die Maschine um 50 Prozent mehr aus. Damit konnten wir die Stückkosten senken“, sagt Marc Prestele, verantwortlich für die mechanische Fertigung am Thales-Standort in Ulm. Bild: Thales
Thales-Manager Prestele sieht indes den wirtschaftlichen Aspekt der Implementierung. So habe man mit dem Cobot das Kunststück fertiggebracht, die Produktivität trotz fehlender Fachkräfte deutlich zu erhöhen: „Mit dem UR10e konnten wir das Produktionsvolumen der Fräsmaschine ausweiten. Durch den Drei-Schicht-Betrieb ist die Maschine um 50 Prozent stärker ausgelastet. Gleichzeitig haben wir die Stückkosten gesenkt und die Flexibilität enorm erhöht.“
Hinzu kam, dass ein ursprünglicher Plan nun der Vergangenheit angehört: Aus Kapazitätsgründen war eigentlich vorgesehen, eine weitere Maschine anschaffen zu müssen, ohne zu wissen, woher man die Bediener bekommen sollte.
Fazit: Ein gelungenes Projekt
Rund zwölf Monate nach dem Projektstart verfügte der Anbieter von Satellitentechnik über ein Robotersystem, das sich laut Prestele „bereits nach zehn Monaten amortisiert hatte“. Dies sind Gründe genug, weshalb Thales nun bereits an die nächsten Schritte denkt. Konkret geplant ist bereits heute eine Investition in weitere Spannmittel. Dadurch erweitert sich das von der Fräsmaschine zu bearbeitende Spektrum an Teilen laut Prestele von sechs auf zehn. Und auch bei künftigen, neuen Anwendungen ist eine Investition in weitere Cobots von Universal Robots nicht mehr weit: Weil der Fachkräftemangel voraussichtlich auch die nächsten Jahre anhalten wird, wird nunmehr an eine Unterstützung für den Krankheitsfall und für neue Bereiche in der Produktion gedacht. Der Fertigungsleiter: „Wir überlegen, den UR10e auch an anderen Arbeitsstationen einzusetzen, wenn zum Beispiel mal ein Mitarbeiter krank ist, oder um die maschinelle Hilfe beim Reinigen und der Montage in Anspruch zu nehmen.“
Über Thales
Thales (Euronext Paris: HO) ist ein weltweit führendes High-Tech-Unternehmen, das in digitale und „Deep-Tech“-Innovationen – Konnektivität, Big Data, künstliche Intelligenz, Cybersicherheit und Quantentechnologie – investiert. Ziel ist, eine Zukunft zu gewährleisten, die für die Entwicklung der Gesellschaft von entscheidender Bedeutung ist. Das Unternehmen bietet Lösungen, Dienstleistungen und Produkte an, die seinen Kunden – Unternehmen, Organisationen und Staaten – in den Bereichen Verteidigung, Luft- und Raumfahrt, Transport sowie digitale Identität und Sicherheit helfen, ihre „kritischen Aufgaben“ zu erfüllen und Menschen in den Mittelpunkt des Entscheidungsprozesses zu stellen. Mit 81.000 Mitarbeitern in 68 Ländern erwirtschaftete Thales im Jahr 2020 einen Umsatz von 17 Milliarden Euro.
Das könnte Sie auch interessieren:
Sensorik und KI optimieren Fertigung von Trägerraketen
Andrea Alboni ist General Manager Western Europe bei Universal Robots.