Design von Druckentlastungssystemen
Die Konzeption von Druckentlastungssystemen zählt zu den großen Herausforderungen in der chemischen Industrie, insbesondere wenn Behälter unter hohem Druck oder mit permanenter Energieversorgung betrieben werden. In der Vergangenheit griffen Planer dazu auf Heuristiken zurück, um die Systeme zu dimensionieren, da die Berechnung über die vorhandenen Softwarelösungen einen oft unvertretbaren Zeitaufwand erforderte. In den letzten Jahren sind die Software-Tools für modellgestützte Sicherheitsrechnungen jedoch deutlich leistungsfähiger geworden. Dadurch lassen sich nun Druckentlastungssysteme in einem überschaubaren Zeitrahmen genauer berechnen. Die präzise Ermittlung der notwendigen Inputgrößen kann dabei die Kosten für das Druckentlastungssystem deutlich senken.

Quelle: PantherMedia/mulderphoto
Ob der Ausfall des Kühlmediums, eine falsche Rezeptur oder ein defekter Regler – die Gründe für Störungen im Betrieb einer Anlage sind vielfältig. Gerade Reaktionen mit exothermen Verlauf, unter hohem Druck oder mit permanenter Energieversorgung bergen jedoch das Risiko, dass ein sicheres Verfahren durch eine Betriebsstörung unkontrollierbar wird. Produktionsanlagen verfügen daher über komplexe Druckentlastungssysteme. Deren Berechnung ist aufwendig, müssen doch eine Vielzahl von Faktoren berücksichtigt werden, die sich zudem im Zeitverlauf ändern. Zu den Standards bei der Berechnung von Druckentlastungssystemen gehören seit vielen Jahren heuristische Verfahren. Erst in den letzten Jahren lohnt es sich, Druckentlastungssysteme über eine detaillierte Prozessmodellierung und Simulation auszulegen. Bis dahin war eine solche Berechnung zu aufwendig und damit zu teuer. Kommerzielle Tools, wie Aspen Plus, CHEMCAD und Aspen FlareNet, aber auch von professionellen Planern selbst entwickelte Ansätze zur spezifischen Prozessmodellierung, haben jedoch nun eine Reife erreicht, die solche Berechnungen wirtschaftlich machen. Dabei bietet die Simulation nicht nur wirtschaftliche Vorteile. So lassen sich Druckentlastungssysteme über eine detaillierte Prozessmodellierung deutlich genauer auslegen. Das reduziert einerseits die Kosten für die benötigten Behälter, Rohrleitungen und Geräte bei Neuanlagen sowie deren Montage. Es sorgt andererseits bei bestehenden Anlagen dafür, dass nicht größeres Equipment als nötig in vorhandene Gebäude integriert werden muss.
Doch wie lässt sich ein möglichst genaues Design eines komplexen Druckentlastungssystems mit seinen vielfältigen Sicherheitseinrichtungen erstellen? In einem ersten Schritt gilt es zunächst, die Szenarien möglicher Betriebsstörungen zu ermitteln. Dies kann beispielsweise der Ausfall von Kühlmitteln bei Reaktoren mit stark exothermen Umwandlungsprozessen sein. Solche Szenarien betrachten Planer in der Regel gemeinsam mit dem Betriebspersonal einer Anlage – beispielsweise über den API Standard 521 – und ermitteln ihre Auswirkungen im konkreten Prozess. Dabei liegt ein besonderes Augenmerk auf einem möglichen Druckanstieg. Für den typischen Fall eines Brandes sind dagegen feste Heuristiken für den Energieeintrag vorhanden, aus dem dann die Konsequenzen berechnet werden.
Zusammenhängende Prozessabschnitte im Blick
Gerade bei kontinuierlichen Verfahren, beispielsweise bei aufeinanderfolgenden Reaktionen in Reaktorkaskaden mit Recycle-Strom und angeschlossener Destillation (s. Beispiel in Bild 1), wie sie in der chemischen Industrie häufig vorkommen, können Störungen Auswirkungen auf mehr als nur einen Apparat haben. Denn die dynamischen Prozessverläufe der einzelnen Apparate sind unlösbar miteinander verknüpft. So kann zum Beispiel der Ausfall des Katalysatorzuflusses dazu führen, dass die Reaktionsrate im Reaktor abfällt und die Reaktivität in den folgenden Reaktoren erst verzögert zunimmt. Die Planer haben deshalb nicht nur einzelne Geräte, sondern auch zusammenhängende Prozessabschnitte mithilfe einer detaillierten dynamischen Prozesssimulation im Blick. Ziel ist es, zunächst mögliche kritische Stellen anhand von Worst-Case-Szenarien im Prozess zu ermitteln. Zu diesem Zweck werden alle möglichen Szenarien von Betriebsstörungen einzeln untersucht. Die ermittelten Worst-Case-Szenarien dienen als Grundlage für die Auslegung der Sicherheitseinrichtungen, wie Ventile und Berstscheiben, sowie der Zulauf- und Abblaseleitungen. Dafür müssen die zeitlichen Verläufe von Druck, Temperatur und Energieeintrag genau untersucht werden. Diese zeitlichen Verlaufskurven bilden letztendlich eine wichtige Entscheidungsgrundlage für die Festlegung des Ansprechdrucks der Sicherheitseinrichtung für alle Einzelapparate.
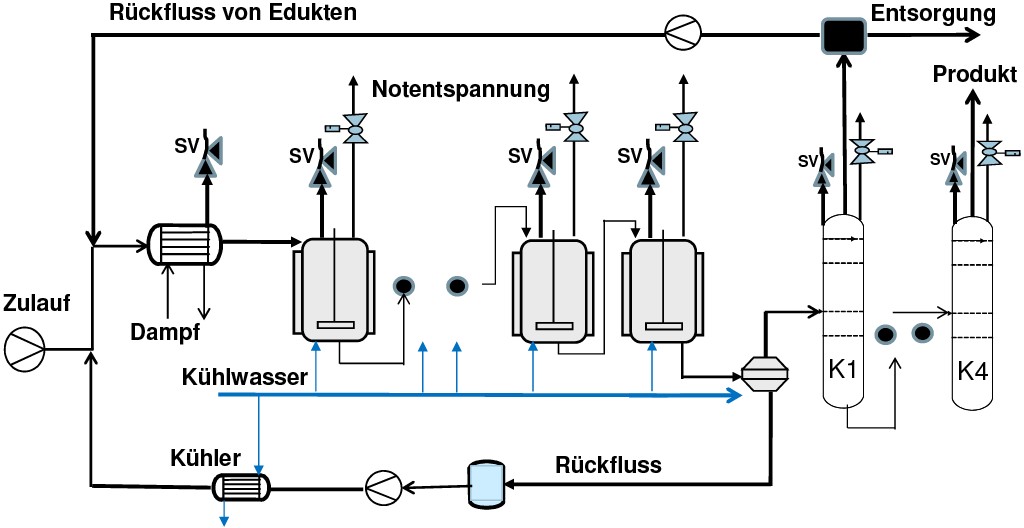
Bild 1 Interaktion verschiedener Prozesseinheiten im kontinuierlichen Verfahren.
Foto: Infraserv GmbH&Co. KG
Festlegung des Ansprechdrucks der Sicherheitseinrichtungen
Basierend auf den Ergebnissen aus der Betrachtung der verschiedenen Prozessabschnitte untersuchen die Planer dann die einzelnen Apparate und legen u. a. den Ansprechdruck der Sicherheitseinrichtungen fest. Der festgelegte Ansprechdruck darf dabei durchaus auch unter dem – vom Hersteller ausgewiesenen – Maximaldruck des Behälters liegen, wenn dadurch der Energieeintrag geringer ist (s. Bild 2).

Bild 2 Grundlagen zur Festlegung der Ansprechbedingungen von Sicherheitseinrichtungen.
Foto: Infraserv GmbH&Co. KG
Denn dies kann zu niedrigeren Abblaseströmen führen und damit zu niedrigeren Baukosten der Anschlussleitungen.
Durch die dynamische Simulation der Szenarien lassen sich nicht nur die Zeitpunkte des Erreichens der Ansprechdrücke bestimmen, sondern auch die zu diesen Zeitpunkten herrschenden Energieeinträge sowie die Temperaturen, die Zusammensetzungen und die anderen Zustandsgrößen der Flüssig- und Gasphasen in den Einzelapparaten. Aus den Zustandsgrößen können dann die maximal abzuführenden Mengenströme und deren Zustände, wie deren Gas- bzw. Flüssiganteil, berechnet werden.
Für deren zuverlässige dynamische Berechnung ist eine hohe Genauigkeit bei der Definition des Prozesszustands der zu betrachtenden Apparate und Behälter zu Beginn der Betriebsstörung erforderlich. Es muss vermieden werden, dass sich mögliche Fehler in der darauffolgenden dynamischen Simulation des Prozessverlaufs fortpflanzen. Schließlich sind bis zum Zeitpunkt des Ansprechens der Sicherheitseinrichtungen zum Teil drastische Zustandsänderungen zu erwarten. Die exakte Kenntnis des Prozesszustands wird vor allem für den Zeitpunkt des Ansprechens der Sicherheitseinrichtungen und des nachfolgenden Abblaseverlaufs zur Druckentlastung benötigt, da dies die Basis für die Auslegung und Dimensionierung der Sicherheitsapparaturen sowie der Zulauf- und Abblaseleitungen bildet. Neben Druck und Temperatur benötigen Planer darüber hinaus genaue Informationen über die Zusammensetzung der flüssigen und dampfförmigen Phase, aber auch über den Energieeintrag zu diesem Zeitpunkt. Die Berechnung der Phasen erfolgt über eine detaillierte dynamische Simulation vom bekannten Anfangszeitpunkt – zumeist der stationäre Normalbetrieb – bis hin zum Zeitpunkt des Erreichens des Ansprechdrucks. Durch die Analyse von möglichen Betriebsstörungsszenarien ergeben sich zudem Fälle, bei denen Einzelbehälter isoliert vom Gesamtprozess zu betrachten sind, wie etwa bei blockierten Ausflussleitungen oder im Brandfall. In diesen Fällen wird der Zustand im Behälter vom Anfangszeitpunkt bis zum Erreichen des Ansprechdrucks wie bei einem Batchbetrieb dynamisch berechnet. Anschließend gleichen die Planer ihre Ergebnisse mit den anderen Szenarien ab und beurteilen, welches Szenario als Worst-Case gelten soll. In der Regel reicht es dazu aus, den Energieeintrag bei Erreichen des Ansprechdrucks zu vergleichen. Ein Sonderfall stellt dabei der Brandfall dar. Hier ist es nötig, nicht nur die Sicherheitsarmaturen sowie deren Zulauf- und Abblaseleitungen zu dimensionieren, sondern auch Einrichtungen zur Notentspannung zu berücksichtigen. Leitungen und Ventile zur Notentspannung, die im Brandfall zum Einsatz kommen, werden dabei separat von den anderen Sicherheitseinrichtungen betrachtet. Denn bei einem Brand kann das Material der Behälter überhitzen und soweit aufweichen, dass sich Betreiber nicht mehr auf die Angabe des Maximaldrucks verlassen können. Leitungen im Anschluss an Notentspannungsventile müssen daher so groß ausgelegt werden, dass sich der Druck im Behälter innerhalb von 15 min – in Sonderfällen auch in kürzerer Zeit – halbiert. Für die Notfallentlastung im Brandfall lässt sich der normale Betriebsdruck als Anfangswert für die dynamische Rechnung heranziehen. Die Ventilöffnung ist dabei so zu dimensionieren, dass die genannte Zeitspanne eingehalten wird. Daraus ergibt sich ein zeitlicher Verlauf des austretenden Massenstroms (Bild 3).
Für die Auslegung der Zulaufleitungen, des Ventils sowie des gesamten Leitungsnetzes hinter dem Ventil nutzen die Planer den Maximalwert, der meistens zu Beginn der Ventilöffnung erreicht wird. Auch die Notentspannungsleitungen werden am Ende mit den Ausblaseleitungen der anderen Behälter zusammengeführt und somit in die Gesamtbetrachtung integriert.
Ermittlung des Zustands des Abblasestroms
Nach Festlegung des Ansprechdrucks und den daraus resultierenden Zuständen für die Gas- und Flüssigphase in den Einzelbehältern gilt es, die essenzielle Frage nach dem Zustand des abzuführenden Abblasestroms zu beantworten. Denn ob der austretende Strom ein- oder zweiphasig ist, hat sowohl für die anschließende Bestimmung des maximalen Mengenstroms als auch für die Dimensionierung der Sicherheitsapparaturen und Rohrleitungen des angeschlossenen Abblasesystems einen signifikanten Einfluss. Insbesondere der Füllstand der Flüssigphase und die vom Energieeintrag abhängige Höhe der Sprudelschicht bestimmen maßgeblich, ob der austretende Strom rein flüssig, rein gasförmig oder zweiphasig erfolgt (Bild 4).
Zur Beantwortung dieser Frage sind in der Norm ISO 4126-10 heuristische Regeln zusammengefasst. Um diese effektiver zu nutzen, haben einzelne Engineering-Experten diese in eigene Tools implementiert.
Bei einem rein gasförmigen Austritt lässt sich der Mengenstrom direkt über die Dampfbildungsrate ermitteln, die sich aus dem Energieeintrag und der Verdampfungsenthalpie bei bereits bekannter Temperatur ergibt. Bei einem zweiphasigen Strom wird zur Berechnung des Mengenstroms in der Regel von einer Homogenität zwischen Behälterinhalt und austretenden Strom ausgegangen. Hier wird der Volumenstrom aus der Dampfbildungsrate bestimmt. Bei einphasigen Abblaseströmen erfolgen die weiteren Berechnungen mit nun bekannten Mengenströmen zur Dimensionierung von Sicherheitsarmaturen, Zu- und Ausblaseleitungen u. a. über das Tool CONVAL. Bei zweiphasigen Strömungen dienen wiederum die Heuristiken in der ISO 4126-10 zur Dimensionierung der Sicherheitsarmaturen.
Integration des nachfolgenden Equipments
Nach der Dimensionierung der Ventile und Einzelleitungen der einzelnen Apparate sind die ermittelten Strömungsbedingungen und Massenströme für die Integration des nachfolgenden Equipments von Bedeutung. Auf der Basis dieser Daten dimensionieren Planer im Anschluss sowohl die Sicherheitseinrichtungen als auch das Rohrleitungsnetz, das Blow-Down-System, den Tauchbehälter und die Fackelleitung. Die Berechnung dieses gesamten Leitungsnetzes von den Ventilausgängen einschließlich der Notentspannungsleitungen bis hin zur Fackelleitung erfolgt mit speziellen Tools wie Aspen FlareNet. Bei der Simulation des gesamten Leitungsnetzes muss berücksichtigt werden, dass mehrere Sicherheitseinrichtungen gleichzeitig ansprechen können. Welche Einrichtungen zeitgleich ansprechen, hängt sowohl vom Einflussbereich des zu betrachtenden Szenarios als auch von der Positionierung der einzelnen Behälter ab. Bei der Berechnung des Druckprofils im gesamten Leitungsnetz ist außerdem zu beachten, dass an den Ventilenden der maximal zulässige Gegendruck nicht überschritten wird. Dabei gilt für Sicherheitsventile meist eine Obergrenze von etwa 30 % des Vordrucks. Gleichzeitig müssen Planer die maximale Durchströmungsgeschwindigkeit im Auge behalten, um eine zu hohe Lärmbelastung zu vermeiden. Häufig werden dazu rund 60 % der Machzahl als Grenzwert der Strömungsgeschwindigkeit angesetzt.
Die genaue Berechnung des Strömungs- und Druckprofils von Strömen, die im zweiphasigen Zustand aus dem Ventil austreten, stellt besondere Anforderungen an die Simulation. Zu berücksichtigen ist dabei, dass sich mit stetig zunehmendem Druckabfall entlang der Leitung der Dampfanteil erhöht. Dadurch reduziert sich die mittlere Dichte, was zu einer stetig höheren Strömungsgeschwindigkeit führt. Die ansteigende Strömungsgeschwindigkeit bedingt wiederum einen steileren Druckabfall, was im Endresultat meist ein hoch nichtlineares Druckprofil entlang der Leitung zur Folge hat. Die korrekte Berechnung des Strömungs- und Druckprofils erfordert daher eine extrafeine Diskretisierung in kleine Leitungssegmente. Einhergehend mit der Erhöhung des Dampfanteils ist auch ein starker Temperaturabfall bis hin zu Werten möglich, die unter dem Gefrierpunkt von Wasser liegen. Auch dies muss bei der späteren Auslegung des Tauchbehälters bedacht werden.
In einem der letzten Schritte wird der Blow-Down-Behälter dimensioniert. Er dient in erster Linie der Abscheidung von Flüssigpartikeln in einem Zweiphasenstrom. Aus den vorhergehenden Berechnungen sind bereits die eingehenden Maximalströme sowohl von Gas als auch von Flüssigkeit und damit auch der maximale Gesamteingangsstrom in den Behälter bekannt. Der benötigte Durchmesser des Behälters ergibt sich überwiegend aus dem maximalen Gaseintritt. Dabei wählen die Experten einen Durchmesser, der die Strömungsgeschwindigkeit und damit den Impuls soweit absenkt, dass Flüssigpartikel ab einer bestimmten Größe nicht mehr mitgerissen werden können. Ein allgemein anerkannter Grenzwert liegt hier bei einer Größe von 300 m. Die maximale Strömungsgeschwindigkeit und damit der Mindestdurchmesser des Behälters lässt sich – basierend auf Heuristiken aus der Fachliteratur – in Abhängigkeit vom Durchmesser der Flüssigpartikel berechnen. Die Festlegung der Behälterhöhe wird im Wesentlichen vom maximalen Flüssigkeitseintritt bestimmt. Weitere Einflussgrößen sind die Durchmesser der angesetzten Einlaufrohre.
Um sicherzustellen, dass durch einen von der Fackel ausgehenden Gegendruck kein Rückstoßeffekt über den Blow-Down-Behälter zur Anlage erfolgt, werden in vielen Anlagen Tauchbehälter zwischengeschaltet. Die Auslegung des Tauchbehälters basiert im Wesentlichen auf dem maximalen Ausgangsstrom des Blow-Down-Behälters sowie auf Regelwerken, beschrieben in API 521 und ISO 23251. Auch bei einem Tauchbehälter wird ein ausreichend hoher Durchmesser benötigt, um einen zu starken Mitriss von wässrigen Flüssigpartikeln zu vermeiden. Gleichzeitig muss die Tauchtiefe dem maximal möglichen Gegendruck der Fackel entsprechen (s. o.). Außerdem sollte die als Tauchflüssigkeit verwendete Wassermenge ausreichen, damit eventuelle Gefrierungen durch kalte Gaseintrittsströme von vornherein ausgeschlossen werden können. Dabei setzt sich der Ausgangsstrom zur Fackel zusammen aus dem eintretenden Gasstrom zuzüglich der mitgerissenen Wasserpartikel und des im Gasstrom gelösten Wasserdampfs. Dies entspricht etwa 60 % des temperaturabhängigen Sättigungsdrucks. Mit der Auslegung von Tauchbehälter und Fackel ist dann das gesamte Druckentlastungssystem definiert. TS 494
Dipl.-Ing. Michael Strack, Leiter Engineering und Mitglied der Unternehmensleitung, InfraServ GmbH & Co. Knapsack KG, Hürth.
Dr. Moritz Wendt, Mitarbeiter im Engineering der InfraSerV GmbH & Co. Knapsack KG.