Qualitätssicherung von Flanschverbindungen
Die Anforderungen an die Dichtheit in Störfallanlagen und somit an die Montagequalität steigen kontinuierlich. Die konsequente Umsetzung von Best-Practice-Erfahrungen soll hier entgegenwirken. Eine Verbesserung der Montagequalität führt zwangsläufig zu einer schnelleren und sicheren Anfahrt bzw. einem sicheren Betrieb ohne Leckagen. Eine Standardisierung der Planung und klare Montagevorgaben sind neben einer guten Flanschmonteurschulung die Voraussetzung für eine fehlerfreie Montage. Der Monteur wird, ähnlich wie bei einer Schweißverbindung, in die Verantwortung genommen, aber auch in seinen Rechten gestärkt. Die Praxis zeigt jedoch, dass eine umfassende Qualitätsüberwachung im gesamten Herstellungs- und Montageprozess unerlässlich zur Zielerreichung sind. Hierzu gehören insbesondere eine Überprüfung der Flanschgüte, eine spannungsfreie Montage unter Verwendung einer korrekten und geschmierten Schraubverbindung und selbstverständlich eine Dichtheitsprüfung vor Inbetriebnahme. Sämtliche Qualitätssicherungsmaßnahmen sollten durch den Betreiber, unabhängig vom Monteur, gesteuert und kontrolliert werden. Die Ergebnisse in der Praxis zeigen, dass die Qualität von Flanschmontagen dauerhaft und signifikant durch die konsequente Anwendung eines Montageworkflows gesteigert wird. Leckageraten kleiner 1 x 10–4 mbar . l/s und eine Absenkung der Fehlerquote von größer 2 % auf kleiner als 0,5 % sind erreichbar.
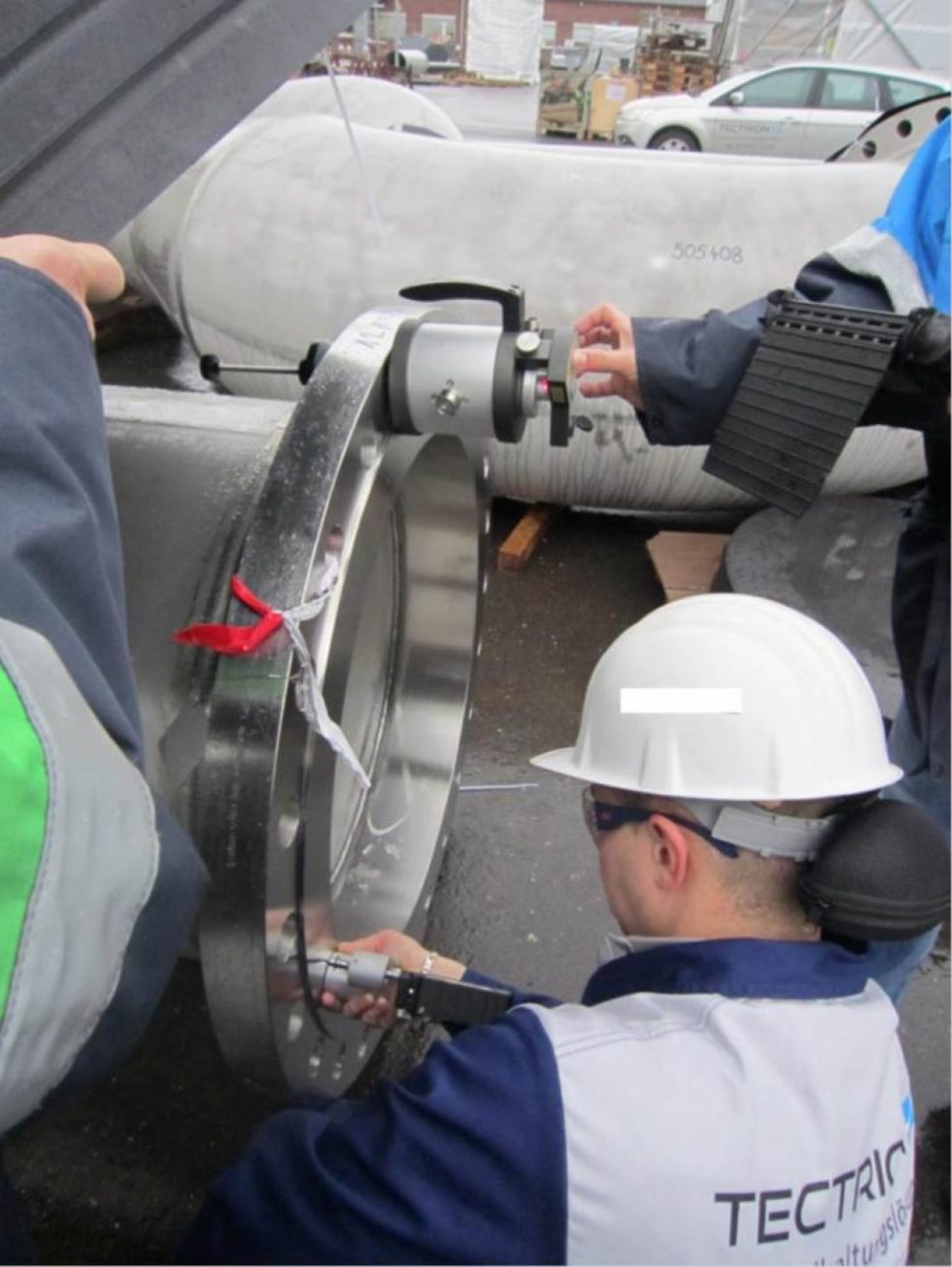
Quelle: Tectrion
Neben steigenden gesetzlichen Anforderungen und den berechtigten Erwartungen der Nachbarschaft nach einem sicheren Betrieb von Chemieanlagen, haben die eigenen hohen Ansprüche von Bayer MaterialScience (BMS) bezüglich Dichtheit von Equipment und Rohrleitungen zur Entwicklung des sog. Workflow Rohr geführt. Die Sicherheit in Störfallanlagen bei BMS soll nicht nur auf dem bereits hohen Niveau stagnieren, sondern weiter gesteigert werden. Diese Überlegungen führten dazu, eine von Praktikern erarbeitete Best Practice unter Berücksichtigung des „VCI-Leitfaden zur Montage in verfahrenstechnischen Anlagen“ [1] zu etablieren, die für alle BMS-Betriebe Gültigkeit hat.
Nachweis der gesetzlichen Rahmenbedingungen
Eine Verbesserung der Montagequalität führt zwangsläufig zu einer schnelleren und sicheren Anfahrt bzw. zu einem sicheren Betrieb ohne Leckagen. Fehlerhafte Montagen sind sofort bei der Abnahme zu bemängeln. Hierdurch können nicht nur allfällige Regressansprüche durchgesetzt, sondern vor allem die Verfügbarkeit der verfahrenstechnischen Anlage und somit die Produktion sichergestellt werden. Für Instandhalter und Anlagenbauer ergibt sich somit zum einen das Ziel, eine Flanschverbindung derart herzustellen, dass sie dauerhaft technisch dicht ist und somit die Ziele des Arbeitsschutzes, des Umweltschutzes und der Ökonomie sicherstellt, und zum anderen die gesetzlichen Anforderungen sicher zu erfüllen. Das bedeutet, dass mindestens die Leckageklasse L = 0,01 zu erzielen ist, um die VDI 2290 [2] und somit im Sinne die TA-Luft [3] einzuhalten. Ein bewährter Weg, um dieses Ziel zu erreichen, ist durch geeignete Montagevorgaben und Kontrollmechanismen die Dichtheit über die Montagegüte sicherzustellen. Der Nachweis kann z. B. durch einen Montageworkflow, der Abnahmeprotokolle und Stichprobenkontrollen beinhaltet, erreicht werden. Die Einhaltung der TA-Luft [3] und somit der gesetzlichen Rahmenbedingungen lässt sich also über eine nachgewiesen qualifizierte Montage belegen. Der VCI-Leitfaden [1] definiert Mindestanforderungen an die Montage, die Grundvoraussetzung sind, um dieses Ziel zu erreichen.
Die Best Practice bei BMS umfasst die Schritte:
- Planung, unter Berücksichtigung von genormten Rohrklassen und ggf. einer Stressberechnung (abhängig von den Betriebsbedingungen und dem Rohrleitungsverlauf).
- Fertigungsüberwachung, insbesondere sind hier die Überwachung der Schweißgüte und der eingesetzten Materialien zu erwähnen.
- Schulung des Montagepersonals durch eine qualifizierte, vom Kontraktor unabhängige Ausbildungsstätte in Anlehnung an DIN-EN 1591-4. [4].
- Festlegung von klaren und eindeutigen Montageregeln unter Anwendung eines leicht verschärften VCI-Leitfadens [1].
- Qualifizierte Überwachung und Abnahme unabhängig von der Werkstatt bzw. dem Kontraktor.
Vorteil durch definierte Planung
Basis einer Rohrleitungsplanung ist es, unter Bezug auf die Stoffkennzahl, die das Medium und dessen Eigenschaften näher spezifiziert, eine geeignete Rohr-, Dichtungs-, und Armaturenklasse festzulegen. Genormte Rohrklassen (i. d. R. Werknormen der Betreiber unter Bezug auf weitere Normen, z. B. DIN-EN), berücksichtigen i. Allg. auch Flansche, Schrauben und Unterlegscheiben. Eine komplette Flanschverbindung wiederum ist ein System aus Flansch, Schraube, Unterlegscheibe, Fett und Dichtung. Die Hauptkomponenten sind also mithilfe der Rohrklasse definiert und somit bereits in den dort genannten Einsatzgrenzen auf ihre Eignung berechnet. Die Verwendung von genormten Rohrklassen ermöglicht den großen Vorteil, dass auf einen Einzelnachweis der Flanschverbindung verzichtet werden kann. Dies gilt natürlich nur, sofern die äußeren Lasten, die auf die Flanschverbindung wirken, den zulässigen Bereich der Rohrklasse bzw. der Flanschverbindung unterschreiten. Bei einer Neuplanung oder einer wesentlichen Änderung muss eine Überprüfung unter Berücksichtigung der normalen und maximalen Betriebsbedingungen einschließlich der statischen und dynamischen Lasten und dem Rohrleitungsverlauf erfolgen. Sonderbauteile wie z. B. Flanschanschlüsse an Maschinen mit geringeren zulässigen Stutzenlasten müssen gesondert betrachtet werden. Gegebenenfalls sind Stressberechnungen durchzuführen, die die Verwendung von Federhängern/ -stützen und/oder Kompensatoren aufzeigen.
Die Aufgabenstellung verlangt die Anwendung von geprüften und zugelassenen Dichtungen. Der Dichtungshersteller stellt die TA-Luft-Eignung sicher und hat diese zu zertifizieren. Wesentlich für die Betrachtung der Flanschverbindung ist die Angabe der Flächenpressung, die zur Erreichung einer gewünschten Leckageklasse erforderlich ist. Hieraus ergibt sich das Drehmoment als wesentliche Angabe für den Monteur. Der VCI-Leitfaden [1] schafft hier Klarheit. Für einige häufig verwendete Dichtungstypen sind die Berechnungen der Drehmomente exemplarisch durchgeführt worden und in einer einfach zu handhabenden Tabelle, in der der Bolzendurchmesser der Schraube als Bezugsgröße verwendet wird, abgebildet. Darüber hinaus müssen Dichtungen selbstverständlich auch gegenüber den chemischen Angriffen der verwendeten Medien resistent sein. Um allen Anforderungen der Planung und der Instandhaltung gerecht zu werden, ist die Verwendung von Dichtungsklassen empfehlenswert.
Ein besonderes Augenmerk muss auf das verwendete Fett gelegt werden. Oft wird dieses ausschließlich in Bezug auf die Produktverträglichkeit und die Eignung bezüglich der Prozesstemperaturen ausgewählt. Unbedingt zu beachten ist jedoch auch der Einfluss auf die Reibwerte der Schraubverbindungen. Die meisten Drehmomentberechnungen erfolgen mit Standardreibwerten von = 0,12 bis 0,13. Mit Hochleistungsfetten können deutlich kleinere Reibwerte erzielt werden. In solchen Fällen sind die Berechnungen mit den realen Reibwerten zu korrigieren, da ansonsten eine Überlastung der Flanschverbindung nicht ausgeschlossen werden kann.
Auf die verwendeten Armaturen sei hier nur insofern eingegangen, dass die dort verwendeten Flansche der jeweiligen Rohrklasse entsprechen müssen.
Fertigungsüberwachung stellt Eignung für die Montage sicher
Eine korrekte Planung ist die Basis für eine dichte Flanschverbindung, jedoch allein nicht ausreichend. Die Fertigungsüberwachung soll u. a. eine konstant hohe Schweißgüte sicherstellen. Stichprobenkontrollen nach der Nahtvorbereitung, während der Schweißung als auch durch Röntgenaufnahmen nach der Fertigstellung stellen sicher, dass der Betreiber seinen Verpflichtungen gerecht wird. Insbesondere der untere und mittlere Nennweitenbereich, der aufgrund seines Druckinhaltsprodukts nicht durch eine zertifizierte Stelle überwacht wird, sollte hier im Fokus liegen. Sofern der Betreiber nicht über eigene Schweißrevisoren verfügt, sollten diese Leistungen extern und unabhängig vom Hersteller zugekauft werden. Bei BMS werden im Rahmen der Schweißüberwachung begleitend die eingesetzten Materialien geprüft. Somit wird eine Vermischung alter DIN-Rohrklassen und neuer DIN-EN-Rohrklassen vermieden. Empfehlenswert ist eine Festlegung geeigneter Vorlieferanten.
Eine begleitende werkstofftechnische Untersuchung ist ebenso empfehlenswert wie eine Maßhaltigkeitskontrolle der fertigen Rohrleitung, aber auch der Bauteile in Stichproben. Dadurch kann sichergestellt werden, dass es bei der Montage keine Abweichungen gibt. Besonders zu erwähnen ist in diesem Zusammenhang die Vermessung der Flanschebenheiten. Erfahrungen und Messungen zeigen, dass durch Welligkeiten die Toleranzen, die durch die Dichtung ausgeglichen werden können, teilweise deutlich überschritten werden. Trotz fehlerfreier Schweißung mit Gegenflansch ist bei Flanschen > DN400 ein Verzug festzustellen, der oft ein Überdrehen notwendig macht. Unzulässige Flanschebenheiten führen, auch bei fehlerfreier Montage, in der Folge zu Leckagen. Um dieses Risiko zu minimieren, hat BMS in Zusammenarbeit mit dem Chemieparkdienstleister Tectrion eine Laservermessung entwickelt. Die Messung kann in der Werkstatt oder vor Ort durchgeführt werden (Bild 1) und ermöglicht eine schnelle und sichere Aussage über die Eignung des Flansches (Bild 2).
Monteur als entscheidendes Qualitätskriterium
Korrekt ausgewähltes und gefertigtes Material sind keine Garantie für eine dichte Flanschverbindung. Erst eine korrekte Montage stellt die dauerhafte Dichtheit her. Somit rückt der Mensch in den Mittelpunkt der Qualität. Der Monteur steht dabei im Widerspruch zwischen den Interessen des Anlagenbetreibers und des ausführenden Kontraktors, also seines Arbeitgebers. Anlagenbetreiber haben ein Interesse an hoher Qualität (also dauerhaft technisch dicht) zu günstigen Konditionen. Kontraktoren haben Interesse an einer möglichst kostengünstigen Montage. Da oft über ein Standardleistungsverzeichnis abgerechnet wird, ist eine schnelle Montage für den Kontraktor gewinnmaximierend. Dies geht jedoch schnell zulasten der Qualität. Um diesen Widerspruch aufzulösen, ist es notwendig, beim Monteur das Bewusstsein für seine herausragende Stellung in Bezug auf eine dichte Flanschverbindung zu schaffen bzw. zu schärfen. Elementar ist der Aufbau eines Vertrauensverhältnisses. Unzureichende Montagebedingungen und Fehler müssen rechtzeitig gemeldet werden. Der Monteur, von dem selbstverständlich eine fehlerfreie und fachgerechte Montage erwartet wird, kann bezüglich der Montagevoraussetzungen seinen Vorarbeiter und den Betreiber in die Verantwortung nehmen. Erfahrungsgemäß funktioniert dies in partnerschaftlichen Arbeitsverhältnissen am besten. Deshalb empfiehlt es sich, den Kontraktor wenn möglich zeitlich zu binden.
Eine Schulung des Montagepersonals durch eine qualifizierte Ausbildungsstätte in Anlehnung an DIN-EN 1591-4 [4] sollte Standard sein. Ein entsprechender Schulungsnachweis stellt die fachliche Eignung des Monteurs sicher. Neben den allgemeinen Schulungsinhalten, wie sie in der DIN beschrieben sind, sollten insbesondere folgende Punkte Bestandteil einer qualifizierten Schulung sein:
- eine Erklärung, was für Konsequenzen eine fehlerhafte Montage haben kann (Personen-, Umwelt-, und Sachschäden), auch wenn der Schlosser in der Regel nicht persönlich haftet,
- ein praktischer Teil mit eingebauten Fehlern und Visulisierung, z. B. über Druckmessdosen,
- die Festlegung von klaren und eindeutigen Montageregeln und Erklärung der Folgen einer Nichtbeachtung von z. B.:
– Verwendung von Montagedornen,
– korrektes Schmieren,
– korrekte Schraubverbindung einschließlich U-Scheiben,
– fehlerfreier Umgang mit Dichtungen,
– korrekte Anzugsmomente.
Selbstverständlich gehört auch ein theoretischer Test, der reale Montagesituationen abfragt, zu einer vollständigen Schulung.
Aufgrund der sich widersprechenden Ziele von Betreiber und Kontraktor ist eine vom Kontraktor unabhängige Ausbildungsstätte dringend zu empfehlen. An dieser Stelle sei darauf hingewiesen, dass sich leider noch kein übergreifender Schulungsstandard durchgesetzt hat. Dadurch wird für den Auftraggeber die Überprüfung und Anerkennung stark erschwert. Teilweise führt das zu Doppelschulungen, im – nicht nur für den Handwerker – schlimmsten Fall mit abweichenden Schulungsinhalten.
Als hilfreich hat sich ein Handout für den Monteur bewährt. Im Brusttaschenformat ausgedruckt und laminiert kann der Monteur so die wichtigsten Regeln nachschlagebereit bei sich führen (Bild 3).
Qualitätssicherung bei BMS
Die langjährigen Erfahrungen bei BMS werden im Workflow Rohr in ein Qualitätssicherungssystem eingebettet, in dem die Maßnahmen aus dem VCI-Leitfaden praxisgerecht konkretisiert werden. Ein wichtiger Bestandteil des QS-Systems ist die oben beschriebene Überprüfung der Flanschebenheit. Für Flansche ab DN200 wird auch diese Überprüfung, wie die meisten anderen Maßnahmen, mit einer Stichprobenvakanz von 10 % durchgeführt. Die Stichprobenvakanz wird selbstverständlich bei Unregelmäßigkeiten erhöht. Des Weiteren wird auch die Rautiefe der Dichtflächen in Stichproben gemessen. Hier werden jedoch wenige Unregelmäßigkeiten festgestellt.
Abweichend zum VCI-Leitfaden wird bereits ab einem Bolzendurchmesser von M20 die Verwendung von drehmomentgesteuerten Werkzeugen gefordert. Ab M30 wird ein hydraulisches Anzugsverfahren gefordert. Aufgrund des ungünstigen Verhältnisses von Flanschblattdicke zu Bolzendurchmesser bei Rohrleitungsflanschen ist ein bolzenlängendes Verfahren ungeeignet. Dieses Verfahren führt zu einer elastischen Flanschkippung, sodass die benötigte Flächenpressung nicht sicher aufgebracht werden kann. Drehende Verfahren haben sich hingegen bewährt. Das geforderte Werkzeug wird farbig im Handout für die Handwerker (Bild 3) dargestellt.
Weiterhin hat sich die Kenntlichmachung des Montage- und Prüfstatus an der Flanschverbindung, z. B. durch Plomben, bewährt. Die erste Markierung erfolgt durch den Monteur, der damit auch die korrekte Montage bestätigt. Weitere Markierungen werden im Rahmen der QS und nach der Dichtheitsprobe angebracht. Alle Markierungen sind personenbezogen zuordenbar, wie es bei Schweißungen bereits seit Jahrzehnten bewährte Praxis ist. Dies stärkt die Pflichten, aber auch die Rechte des Monteurs. Schließlich kann er verweigern, eine unzureichende Montagestelle als korrekt montiert zu kennzeichnen. Unsere Erfahrungen zeigen, dass personenbezogene Markierungen positiv aufgenommen werden, u. a. deshalb, weil der Montagearbeit eine höhere Wertschätzung gezeigt wird.
Die Qualitätssicherung beinhaltet selbstverständlich auch eine Montagekontrolle. Dabei erfolgt die Überprüfung der Montagequalität in Anlehnung an den VCI-Leitfaden [1]. Bewährt hat sich, unabhängig von der Montageklasse, eine Gegenprüfung von mindestens 10 %. Um eine qualifizierte Überwachung und Abnahme sicherzustellen, hat diese durch den Betreiber oder vom Betreiber ernannten Personal mit ausreichender Erfahrung und Qualifikation zu erfolgen. Keinesfalls darf die Montagekontrolle ausschließlich durch den Kontraktor durchgeführt werden.
Die Qualitätssicherung schließt mit einer Dichtheitsprobe ab. Abhängig von der Montageklasse (MK) werden unterschiedliche Qualitäten gefordert:
- Bei MK1 und flüssigen Medien (z. B. Wasser) genügt ein Servicetest.
- Bei MK1 und gasförmigen Medien sowie bei MK2 und MK3 ist vorab ein Nekaltest (0,3 bis 0,5 bar Stickstoff oder Luft) gefordert.
- Je nach Kritikalität des Mediums wird zusätzlich ein Vakuumtest und / oder ein Heliumlecktest oder vergleichbar durchgeführt.
Ergebnisse
Der Erfolg des Montageworkflows kann leicht an der dauerhaften Dichtheit der Flanschverbindungen gemessen werden. So konnte in einem beispielhaften, repräsentativen Projekt bei BMS mit mehr als 5 000 Flanschverbindungen, in dem die Flanschmontage zu 100 % dokumentiert wurde, die Quote der Flansche mit Undichtigkeiten während oder nach der Inbetriebnahme auf << 0,1 % (fast ausschließlich in der MK1) reduziert werden. Dabei wurde die Leckagerate mittels Heliumlecktest mit höchsten 1 x 10-4 mbar l/s, in der Regel mit < 1 x 10-5 mbar l/s oder besser bestimmt.
Anzumerken ist jedoch, dass bei der Übergabe vom Kontraktor die Fehlerquote > 2 % betrug, davon >1 % Fehler durch Leckagen.
FAZIT: Eine qualifizierte Überwachung und Abnahme durch den Betreiber ist unerlässlich.
Eine Fehlerquote von 2 % ist nicht akzeptabel. Als Fehler werden auch eine verspannte Montage, ein ungleichmäßig aufgebrachtes oder falsches Drehmoment, fehlendes Fett, fehlende Unterlegscheibe oder die Verwendung einer falschen Dichtung gewertet. Auch wenn solche Fehler in der Vergangenheit eher toleriert wurden und dadurch die Fehlerquote allein durch die Statistik verschlechtert wird, wird eine Flanschverbindung nur dauerhaft dicht sein, wenn fehlerfrei montiert wird. Im Sinne einer erhöhten Verfügbarkeitsanforderung dürfen die Qualitätsansprüche keinesfalls abgesenkt werden. Wie das in der Tabelle gezeigte Beispiel aus einer kleinen, mehrere Jahrzehnte alten Anlage zeigt, wird durch eine gute Qualitätssicherung bei ansonsten unveränderten Bedingungen der Kontraktor so weit sensibilisiert, dass dies allein schon zu einer Verbesserung führt. Der Kontraktor wurde in diesem Beispiel nicht gewechselt. Die Auswertung wurde im Rahmen von kleineren Stillständen erfasst.
Zusammenfassung
Die Qualität von Flanschmontagen kann dauerhaft signifikant durch die konsequente Anwendung eines Montageworkflows gesteigert werden.
Der Mehrwert für Sicherheit und Umweltschutz liegt auf der Hand. Jede Leckage bedeutet meist auch signifikante finanzielle Einbußen und evtl. auch Imageverluste. Mehraufwendungen für die Qualitätssicherung sind auch finanziell gerechtfertigt. Das QS-Personal muss vom Betreiber gestellt bzw. beauftragt werden und unabhängig vom Kontraktor sein (das gilt auch für eigenes Montagepersonal).
Eine Auswertung der Prüfungen bei der Montageschulung und die Resonanz der Handwerker zeigen, dass eine Schulung sinnhaft und zielführend ist. Es erscheint sinnvoll, die Schulungen anzugleichen und gegenseitig anzuerkennen. Hier ist eine größere Unterstützung durch VDI und VCI wünschenswert. TS 451
Literaturverzeichnis
[1] Leitfaden zur Montage von Flanschverbindungen in verfahrenstechnischen Anlagen. Hrsg.: Verband der Chemischen Industrie e. V. Frankfurt a. M. 2013.
[2] VDI 2290: Kennwerte für dichte Flanschverbindungen. Berlin: Beuth Verlag 2012.
[3] Erste Allgemeine Verwaltungsvorschrift zum Bundes-Immissionsschutzgesetz (Technische Anleitung zur Reinhaltung der Luft – TA Luft) vom 24. Juli 2002. GMBl. (2002) , Heft 25-29, S. 511-605.
[4] DIN EN 1591-4: Flansche und ihre Verbindungen – Teil 4: Qualifizierung der Befähigung von Personal zur Montage von Schraubverbindungen in druckbeaufschlagten Systemen im kritischen Einsatz. Berlin: Beuth Verlag 2013.
Dipl.-Ing. Stefan Giesen, Betriebsingenieur, Bayer MaterialScience AG, Dormagen.