Monitoring von Schraubverbindungselementen
Ein Verbindungselement dient zum Zusammenhalten von Bauteilen. Die Dimensionierung wird in Abhängigkeit der zu erwartenden Belastung vorgenommen. Basis ist oft die Finite Elemente Methode. Werden hohe Sicherheitsanforderungen an die Festigkeit, bei gleichzeitiger Berücksichtigung von Gewicht und Kosten gestellt, sind ausgiebige Funktions- und Belastungstests unter den definierten Randbedingungen erforderlich. Die Testanordnungen beinhalten oft Sensoren, die die Belastungen an exponierten Positionen bis zum Versagen der Struktur misst.
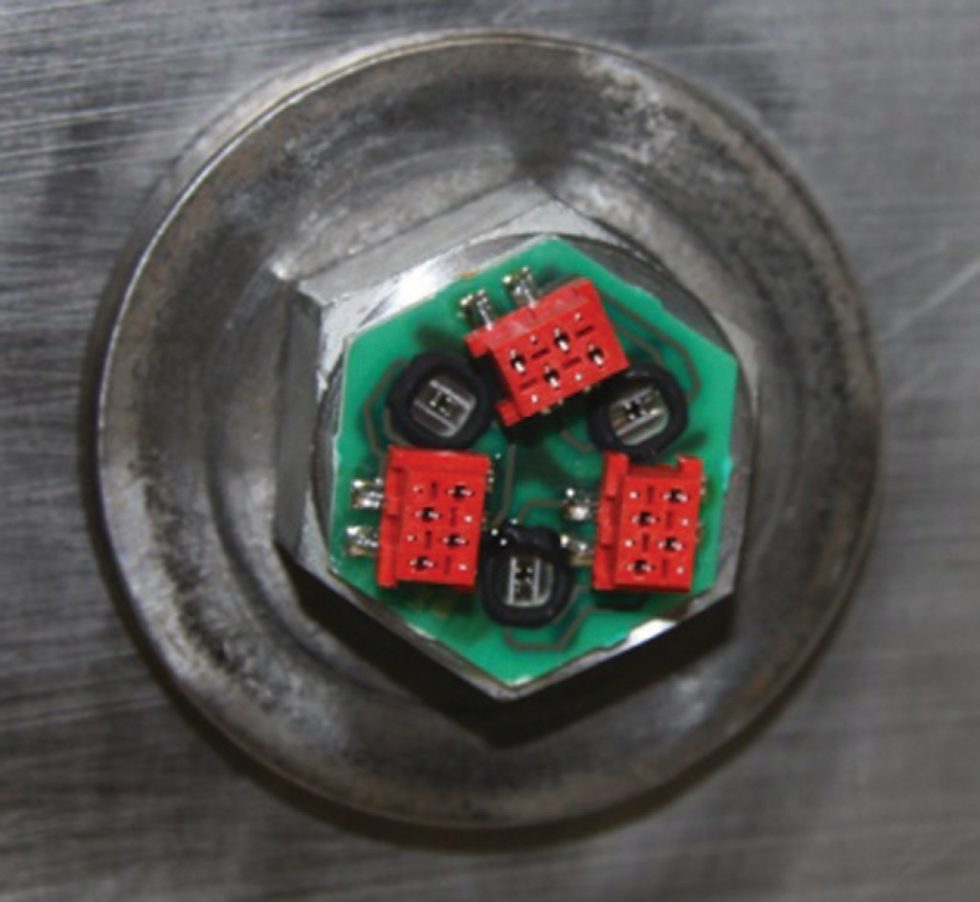
Quelle: CIS
Bei sicherheitsrelevanten Verbindungselementen ist es wünschenswert, dass die Funktion und die Belastung ständig überwacht werden. Aus der mechanischen Belastung ergibt sich die Messgröße Dehnung. Diese lässt sich nach Kalibrierung in die belastende Kraft umrechnen. Verwendet werden können alle Dehnungssensoren, Foliendehnmessstreifen (DMS), Faseroptische Dehnungssensoren oder Halbleiter-DMS.
Ziel ist es, die Verbindungselemente mit sensorischen Eigenschaften auszurüsten. Diese Verbindungselemente eignen sich jedoch nur bedingt für die Integration herkömmlicher Sensoren, da sie einen erheblichen Eingriff in die Konstruktion und in den Kraftfluss erfordern.
Handelsübliche Kraftsensoren bestehen vorwiegend aus hochfestem Stahl oder Aluminium, versehen mit Folien-DMS. Die Einbausituation und die geometrische Form dieser Kraftsensoren sind derart gewählt, dass insbesondere die Querkräfte das Messsignal nicht verfälschen. Die Konstruktion der Federkörper ist derart gestaltet, dass in dem Bereich der Folien-DMS eine wesentlich größere Dehnung erreicht wird, z. B. durch gezielte Verjüngung im Kraftfluss einer Parallelfederführung.
Sollen Sensoren zur Überwachung der mechanischen Belastung in Verbindungselementen integriert werden, um Struktur und Design nur minimal zu beeinflussen, wird ein extrem miniaturisierter Aufbau benötigt. Zusätzlich ist zu berücksichtigen, dass die Belastungsrichtung nur eingeschränkt bekannt ist und dass plastische Verformungen nicht ausgeschlossen werden können. Durch alternierende Belastungen liegt die Dauerfestigkeit weit unter der statischen Belastungsgrenze. Es besteht die Gefahr der plastischen Verformung der Verbindungselemente. Aufgrund der zu erwartenden geringeren Dehnung sind empfindlichere DMS erforderlich. Silizium-DMS (Si-DMS) erfüllen diese Eigenschaften. Sie sind bis zu 50-mal empfindlicher als Folien-DMS [2].
Für diese Anwendungen wurden daher eine Reihe verschiedener Silizium-Dehnmessstreifen-Chips entwickelt, die
- einen Einzelmesswiderstand,
- eine Messbrücke und
- querdehnungsunempfindliche Messwiderstände enthalten. Diese Silizium-DMS werden verwendet um die Vorspannkraft einer Schraubenverbindung zu bestimmen.
Die Schraube als Verbindungselement
Eine Schraube ist ein Maschinenelement zur kraftschlüssigen Verbindung von zwei oder mehr Bauteilen. Durch das Anzugsmoment wird zwischen Schraubenkopf und Muttergewinde die Montagevorspannkraft aufgebaut. Die maximale zulässige Vorspannkraft wird durch den Bolzendurchmesser und die Festigkeitsklasse der Schraube definiert. Für eine dauerhaft sichere und funktionsfähige Verbindung ist zu gewährleisten, dass die Vorspannkraft über die gesamte Lebensdauer in einem definierten Toleranzbereich liegt. Für Standardanwendungen mit bekannten Belastungen, ist die Einhaltung des Anzugsmomentes und der Richtlinie VDI 2230 ausreichend. Besonders sicherheitsrelevante Verbindungen bedürfen jedoch regelmäßiger Kontrollen. Die nachträgliche Kontrolle der Montagevorspannkraft ist ohne spezielle Zusatzmaßnahmen nicht möglich. Standardgemäß wird das Anzugsmoment manuell überprüft. Es ist zudem auszuschließen, dass Korrosion und Verschmutzung durch Erhöhung der Reibung ein korrektes Anzugsmoment vortäuschen. Vorteilhaft ist das Monitoring der Montagevorspannkraft. Die vorgeschlagene Anordnung nutzt aus, dass die Vorspannkraft alle beteiligten Komponenten beeinflusst. Die Vorspannkraft dehnt den Schraubenschaft, staucht die zu fügenden Elemente und deformiert sowohl den Schraubenkopf als auch die Mutter. In der Deformation des Schraubenkopfes, bzw. der Mutter sind damit alle Informationen über die Vorspannkraft enthalten. Besonders der Schraubenkopf ist für die Integration von Sensoren aufgrund des guten Zugangs gut geeignet.
Für die Messung haben sich Dehnmessstreifen als vorteilhaft erwiesen. Sie bilden die Deformation präzise ab. Wie bereits erwähnt sind die herkömmlichen FolienDMS aufgrund ihrer geometrischen Größe ungeeignet. Die Alternative sind Halbleiter-DMS, welche in verschiedenen Formen verfügbar sind.
Silizium-DMS
Für die Bestimmung der Deformation des Schraubenkopfes infolge der Vorspannkraft, wurde ein mit Hilfe von MEMS-Technologien hergestellter Silizium-DMS verwendet. In Bild 1 ist das Layout und die Schaltung der Messbrücke dargestellt.
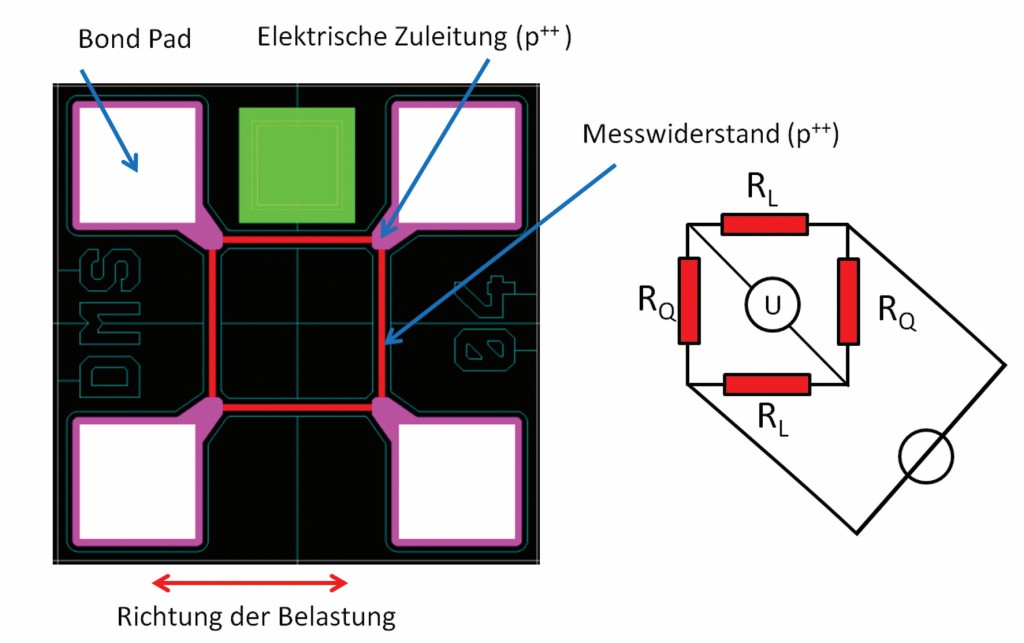
Bild 1 Komplette Messbrücke mit zwei Widerständen für Längseffekt (RL)- und Quereffekt (RQ).
Foto: CiS Forschungsinstitut für Mikrosensorik GmbH
Die vier Messwiderstände bilden eine Vollbrücke. Entsprechend der Beschaltung und der Belastungsrichtung werden die Messwiderstände paarweise quer und längs zur Stromrichtung belastet. Durch die piezoresistiven Eigenschaften des verwendeten Siliziums verhalten sich die Paare, bezogen auf die Änderung des Widerstands, gegensätzlich. So das auf kleinstem Raum eine Vollbrücke ausgebildet wird. Dies bedeutet aber auch, dass dieser Silizium-DMS nur auf anisotrope mechanische Spannungen sensitiv ist. Isotrope Spannungen werden durch die Messbrücke kompensiert.
Die Chipfläche des Silizium-DMS beträgt 500 x 500 μm2. Die Implantationsparameter sind für einen Flächenwiderstand des piezoresistiven Widerstandes von ca. 200 mit einem Temperaturkoeffizienten von ca. 0,8 ‰ / K ausgelegt. Dies ergibt einen Brückenwiderstand von 5000 . Die piezoresistiven Widerstände sind durch hoch implantierte Leitungen verbunden (Bild 1).
Für die verschiedenen Anwendungen können die Sensoren bis zu 5 μm abgedünnt werden.
Um diese Silizium-DMS optimal anzuwenden, werden sie auf den zu untersuchenden Federkörper gefügt. Im Gegensatz zu Folien-DMS konnten mit Epoxy- und Acrylatklebstoff optimale Ergebnisse erzielt werden. Hauptgrund sind die großen Unterschiede im Elastizitätsmodul der Klebstoffe und dem Silizium bzw. dem Stahl. Der Unterschied bewirkt eine unzureichende Übertragung der Dehnung des Federkörpers in den Silizium-DMS. Ein weiterer Grund ist die Langzeitstabilität der Verbindung, welche sich aufgrund der hohen Sensitivität des Silizium-DMS entsprechend negativ auswirkt. Das Fügeverfahren der Wahl ist daher die Verbindung mit Glaslot.
Montage Silizium-DMS auf Stahl
Die Silizium-DMS können auf verschiedenen Federkörpern mittels Glasfritte bei einer Verarbeitungstemperatur von ca. 450 °C montiert werden.
Aufgrund der hohen Unterschiede in der thermischen Ausdehnung zwischen metallischen Federkörpern und dem Silizium steht der DMS unter starken lateralen Druckspannungen. Diese beeinflussen natürlich auch die Messwiderstände, die zu einer Messbrücke verbunden sind. Die Vollbrücke kompensiert diese isotrope Belastung nahezu vollständig. Voraussetzung sind identische Bedingungen an allen Messwiderständen. Dies wird durch ein völlig symmetrisches Design erreicht.
Bisher konnte nur die Glaslotverbindung die sehr hohen Anforderungen an Langzeitstabilität und Festigkeit erreichen. Dies bedeutet, dass die mechanische Belastung vom Federkörper auf den Silizium-DMS ohne Dehnungsverluste übertragen wird, Temperaturschwankungen ohne Hysterese überstanden und das Kriechen aufgrund der hohen mechanischen Belastung auszuschließen ist. Als Werkstoff für den Federkörper eignen sich Aluminium, Titan und Stahl [2].
Das Bild 2 und das Bild 3 zeigen eine REM Aufnahme einer Glaslotverbindung mit einem bleihaltigen Glaslot.
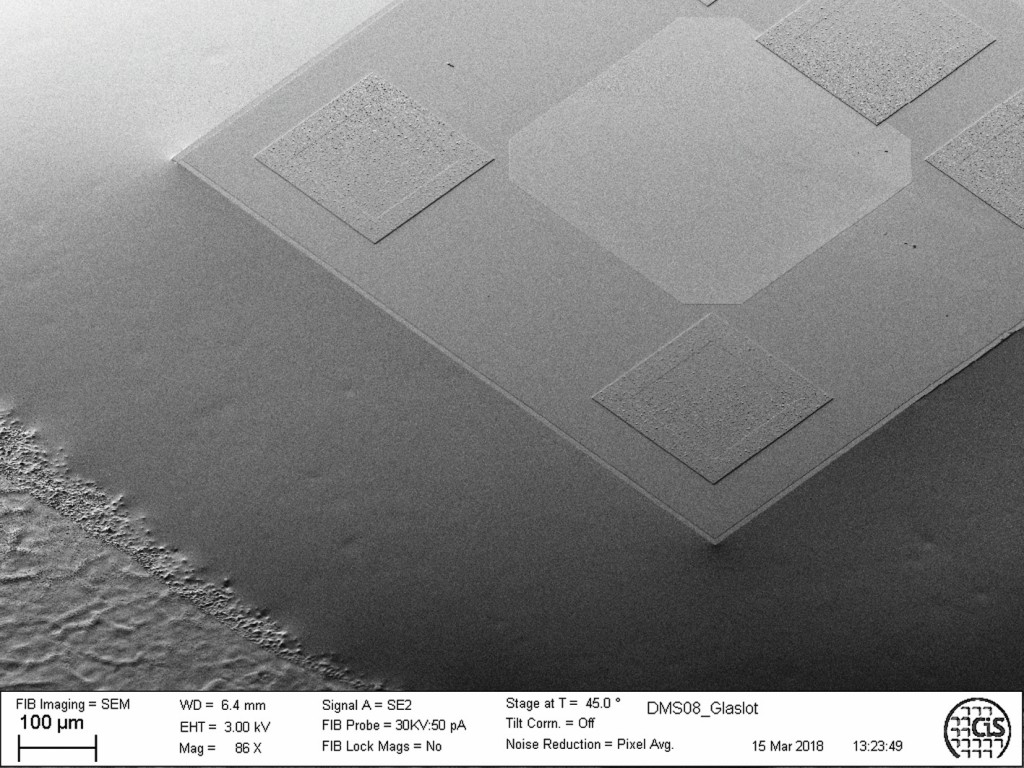
Bild 2 Auf Stahl (1.4542)1) mit Glaslot gefügter Silizium-DMS.
Foto: CiS Forschungsinstitut für Mikrosensorik GmbH
Im Bild 4 ist das Ergebnis einer Langzeituntersuchung zu sehen, bei dem der Offset aufgeglaste Silizium-DMS über einen siebentägigen Temperaturzyklus aufgenommen wurde, 6 mal 2 h bei 30 °C und 22 h bei 120 °C. Die Messwerte bei 30 °C wurden bei der Darstellung ausgeblendet.
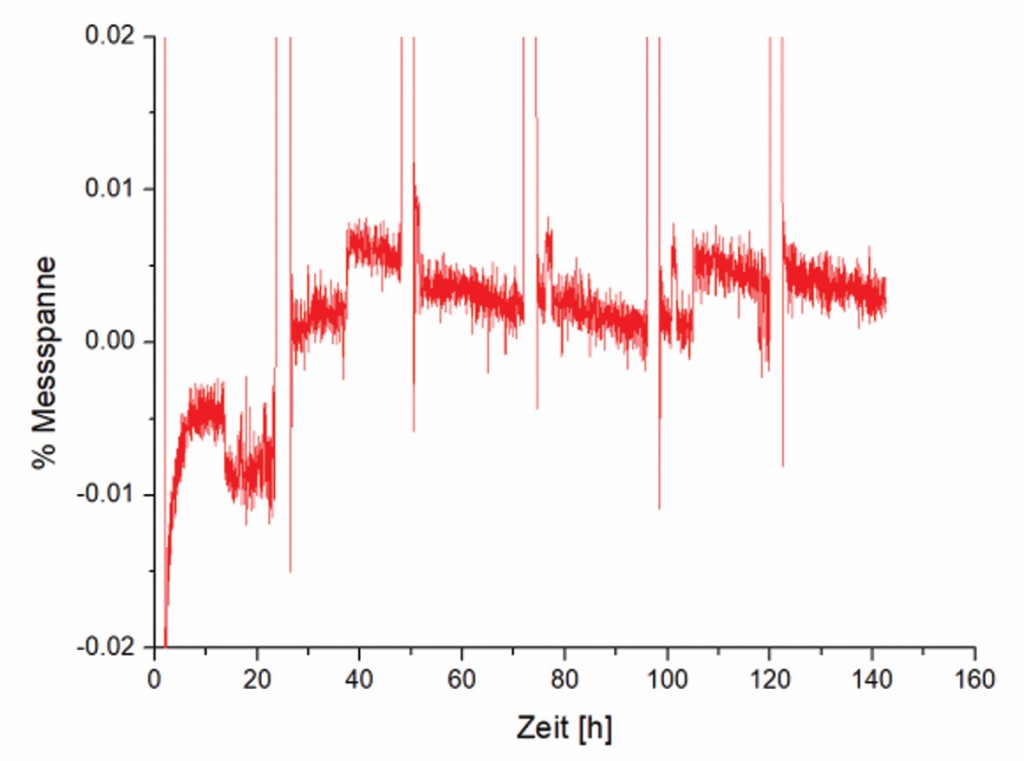
Bild 4 Langzeitstabilität eines durch Glaslot gefügten Si-DMS, 6 mal 2 h 30 °C und 22 h 120 °C, Aufbau wie Bild 2.
Foto: CiS Forschungsinstitut für Mikrosensorik GmbH
Zu sehen ist, dass das Messsignal (Ua0/Messspanne*100 %) der Messbrücke nach 24 h sehr stabil ist. Bezogen ist der Wert auf die Messspanne von 30 mV/V.
Neben der Langzeitstabilität ist das Verhalten der Messbrücken bei Temperaturänderung von Bedeutung. Messbrücken auf Basis von piezoresistiven Messwiderständen besitzen eine höhere Temperaturabhängigkeit als konventionelle Folien-DMS. Eine Anpassung an das Material des Federkörpers sowie eine Verminderung des Temperaturkoeffizienten des Widerstandes sind nicht möglich. Der Temperatureinfluss kann nur mit Hilfe einer elektronischen Signalverarbeitung realisiert werden.
Bild 5 und Bild 6 zeigen die Temperaturabhängigkeit. Die Abhängigkeit des Brückenoffsets von der Temperatur ist, wie bereits erwähnt, auf Asymmetrien im Aufbau, sowohl im Chip als auch in der Montage auf dem Federkörper zurück zu führen.
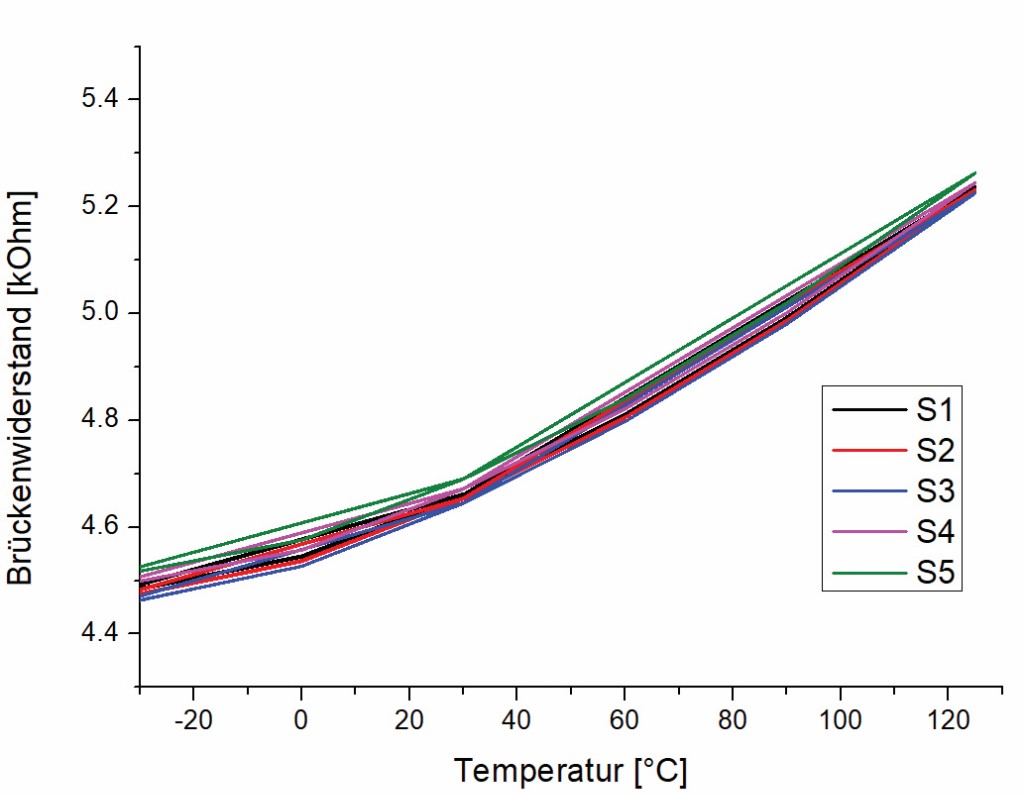
Bild 5 Brückenwiderstand in Abhängigkeit der Temperatur, 5 verschiedene Messbrücken wurden gemessen.
Foto: CiS Forschungsinstitut für Mikrosensorik GmbH
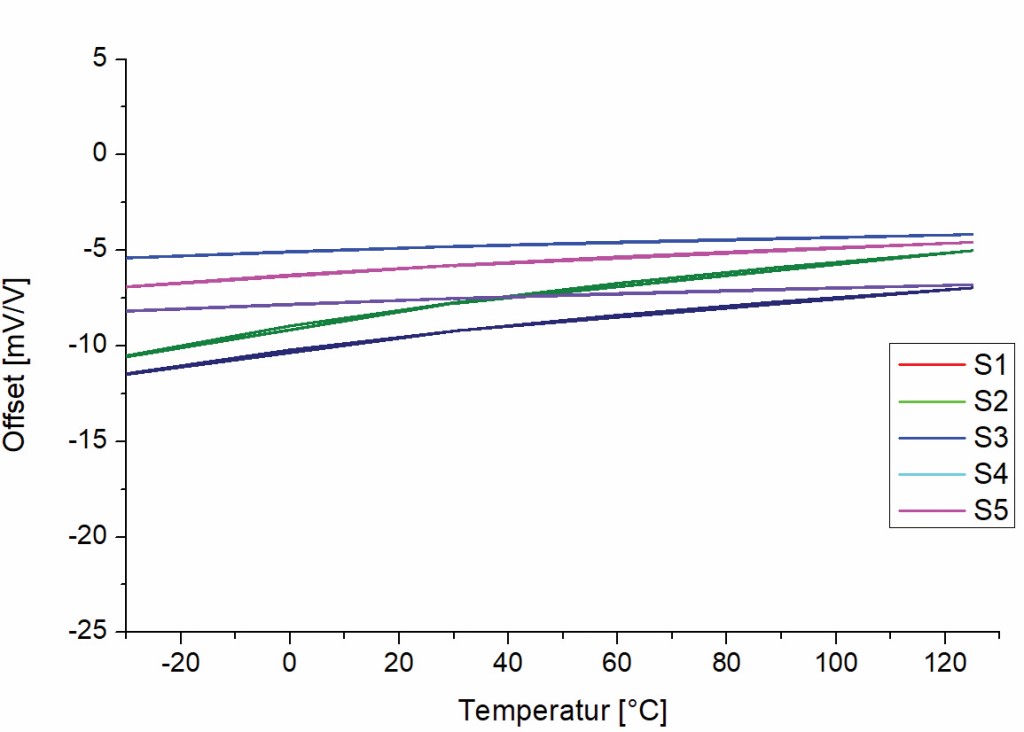
Bild 6 Brückenoffset in Abhängigkeit der Temperatur ohne Belastung, 5 verschiedene Messbrücken wurden gemessen.
Foto: CiS Forschungsinstitut für Mikrosensorik GmbH
Anwendungstest
Die gefügten Silizium-DMS werden vorzugsweise mittels Drahtbonden mit der Signalverarbeitungsplatine verbunden. Bei der anvisierten Anwendung treten nun zwei Herausforderungen auf:
- Auf langen Schrauben kann nur unter hohem Aufwand drahtgebondet werden.
- Eine Wärmebehandlung bis 450 °C ist für Stahlkörper von mehreren Kg nicht nur kostspielig sondern kann auch das Gefüge verändern, so dass die angegebene Festigkeitsklasse nicht mehr erreicht wird.
Der im CiS-Forschungsinstitut entwickelte Lösungsansatz ist daher ein dünner metallischer Träger, auf dem ein neu entwickelter Silizium-DMS, ausgeführt als wheatstonesche Messbrücke, dauerfest durch Glaslot gefügt ist. Auf dem Träger kann sich zusätzlich die Signalverarbeitung für die Messbrücke sowie ein RFID-Element zur drahtlosen Datenübertragung befinden. Dieser Träger wird auf die zu untersuchenden Elemente mit einem geeigneten Fügeverfahren gefügt. Möglich sind Klebeverfahren und Lötverfahren für Langzeituntersuchungen.
Als Anwendungsbeispiel wurde eine Schraube nach DIN 933 M16x60 der Festigkeitsklasse 8.8 verwendet. In der FEM Simulation, Bild 7, ist die Belastung des Schraubenkopfes infolge der Vorspannkraft zu sehen.
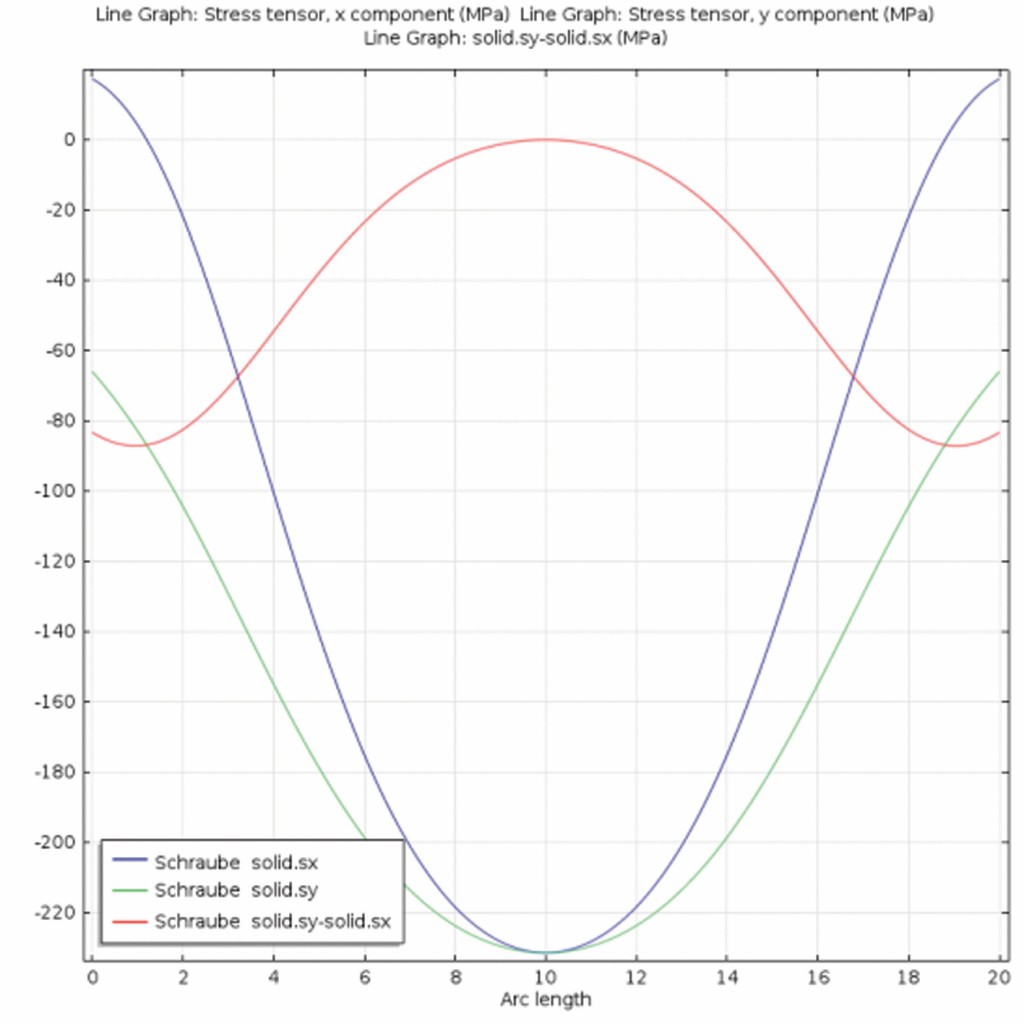
Bild 8 Einzelspannungen in X-Y-Richtung und deren Differenz (Differenz der Druckspannung in X- und Y-Richtung, Rot).
Foto: CiS Forschungsinstitut für Mikrosensorik GmbH
Aufgrund der piezoresistiven Eigenschaften der verwendeten Siliziumorientierung, weist der Silizium-DMS in X- und Y-Richtung eine identische Empfindlichkeit auf. Somit kann dieser nicht in die Mitte des Kopfes gesetzt werden, obwohl hier das Spannungsmaximum ist. Die ideale Position kann aus der Differenz der beiden Spannungskomponenten (rote Linie) abgelesen werden. Es ist das Maximum der Differenz der Druckspannung in X- und Y-Richtung.
Die Schraube ist kein klassischer Federkörper, wie er für Kraftmesszellen verwendet wird, daher ist mit Ungenauigkeiten zu rechnen, wie z. B. eine nicht mittige Belastung. Aus diesem Grund wurde der Kopf mit drei Silizium-DMS (analog Bild 1) versehen (Bild 9).
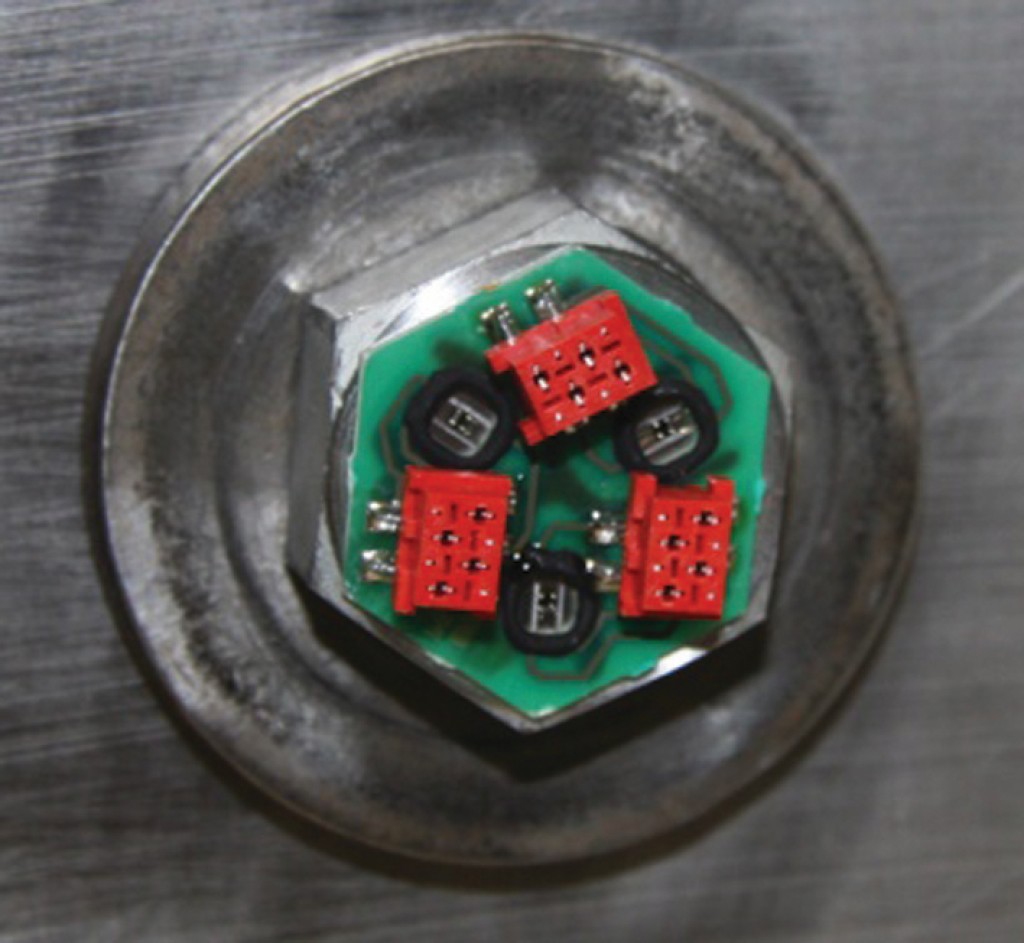
Bild 9 Schraubenkopf mit 3 Si-DMS (A, B, C), mit Leiterkarte auf einem Montageträger.
Foto: CiS Forschungsinstitut für Mikrosensorik GmbH
Diese Drei sind auf einen Montageträger gefügt, an dem zusätzlich die Leiterkarte montiert ist. Dieser Aufbau lässt sich durch die geringe Höhe sehr gut maschinell bearbeiten. Zum Abschluss wird der Montageträger mittels eines geeigneten Verfahrens auf dem Schraubenkopf befestigt. Optional ist ein Lötverfahren möglich. Das Messsignal ist die Summe der drei Silizium-DMS.
Evaluiert wurde das System mit dem Messaufbau aus Bild 10.
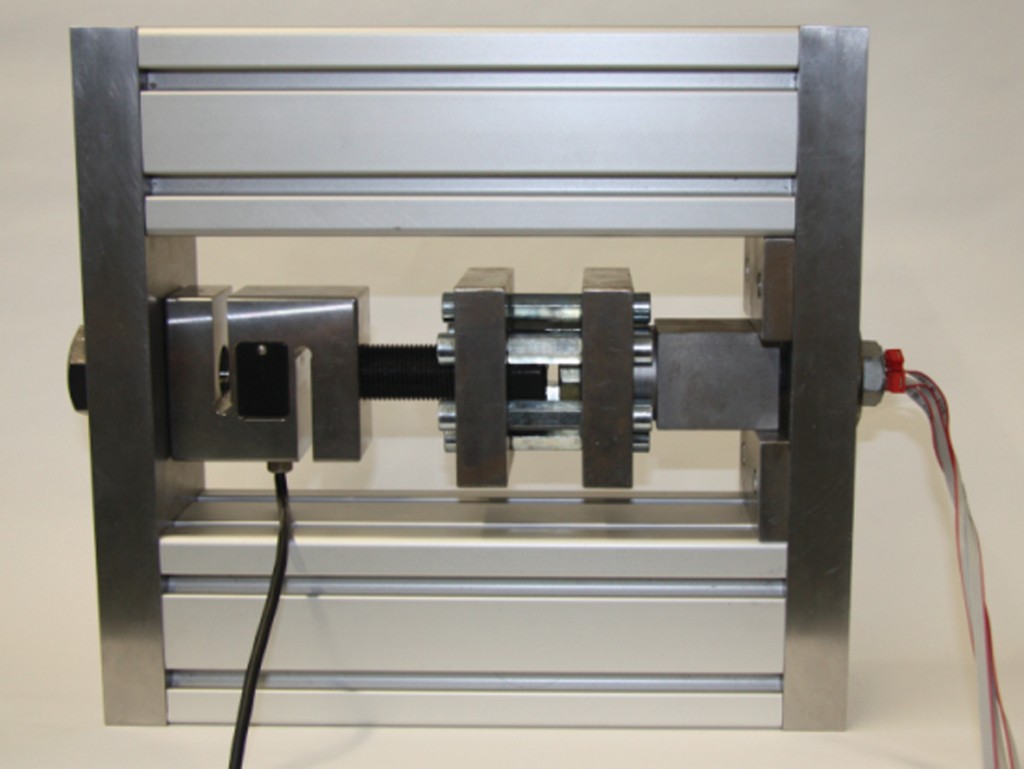
Bild 10 Messaufbau mit einem konventionellen Kraftsensor, Messbereiche 50 kN (Links), Kopplung zur Schraube (Rechts), Ausgleichskupplung (Mitte), Einziehschraube.
Foto: CiS Forschungsinstitut für Mikrosensorik GmbH
Dieser beinhaltet einen konventionellen Kraftsensor, mit einem Messbereich von 50 kN und einer Kopplung zur Schraube. Um Messfehler zu vermeiden, ist der Aufbau derart gestaltet, dass vorwiegend nur Kräfte in Achsrichtung auftreten können.
Zur Evaluierung wurden die Silizium-DMS und der Kraftsensor ausgewertet. Die maximale Belastung betrug 30 kN, der Vorgang wurde 5-mal wiederholt. Zu sehen ist, dass ein Einzelsensor kein verlässliches Ergebnis liefert. Im Gegensatz dazu kann die Summe der Ausgangsspannungen aller drei Silizium-DMS (Bild 11) als verlässliches Signal angesehen werden.
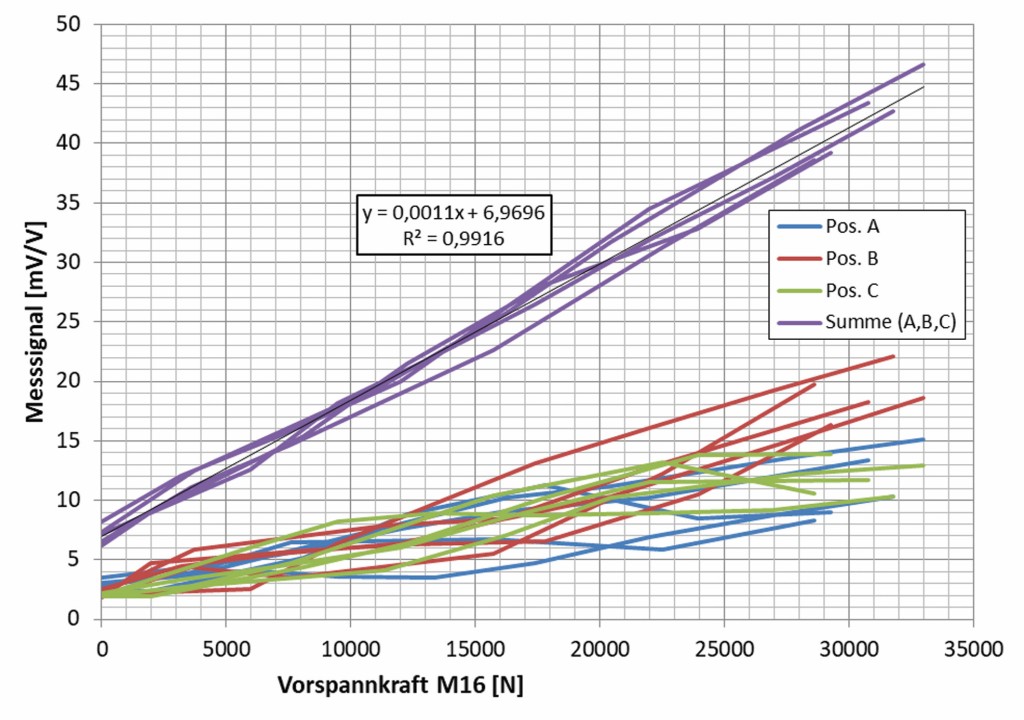
Bild 11a Ausgangsspannung (Ua0) der Si-DMS (A, B, C) und die Summe (A+B+C), Durchsteckschraube.
Foto: CiS Forschungsinstitut für Mikrosensorik GmbH
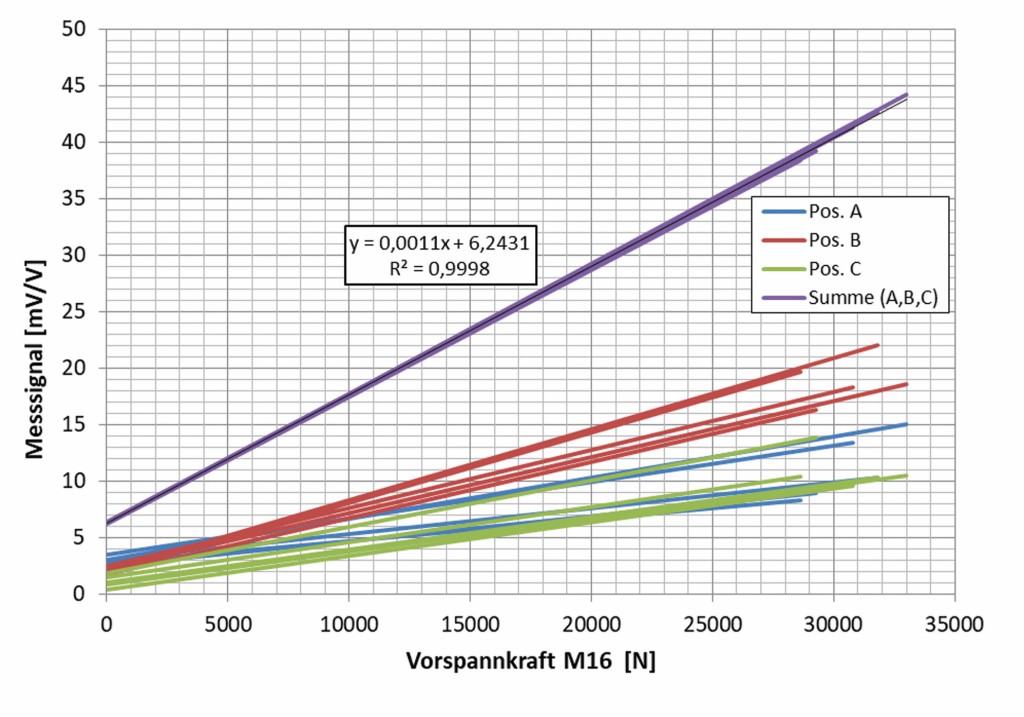
Bild 11b Ausgangsspannung (Ua0) der Si-DMS (A, B, C) und die Summe (A+B+C), Einziehschraube.
Foto: CiS Forschungsinstitut für Mikrosensorik GmbH
Es wurden die Anwendungsfälle Einziehschraube und Durchsteckschraube untersucht. Wie der Vergleich zeigt, liefert der Anwendungsfall Durchsteckschraube ein besseres Resultat siehe Bild 11a. Der Grund ist, dass in diesem Fall die Verbindung über die Mutter angezogen wird. Die Sensoren sind praktisch ortsfest. Bei der Einziehschraube ändert sich durch die Drehung des Kopfes ständig die Lage der Sensoren relativ zur Unterlage. Hinzu kommt ein hoher Verschleiß durch „Fressen“ unter dem Kopf, welcher die Situation ständig verändert und dadurch auch die Spannungszustände im Bereich der Sensoren. Durch die Verwendung von 3 um 120 ° versetzten Sensoren, kann dies ausgeglichen werden, siehe Bild 11b.
Die nächste Frage beschäftigt sich mit dem Langzeitverhalten der Sensoranordnung. Wie Bild 4 zeigte, ist der mit Glaslot gefügte Silizium-DMS hinreichend stabil.
Bild 12 zeigt das Verhalten des Systems auf dem Schraubenkopf.
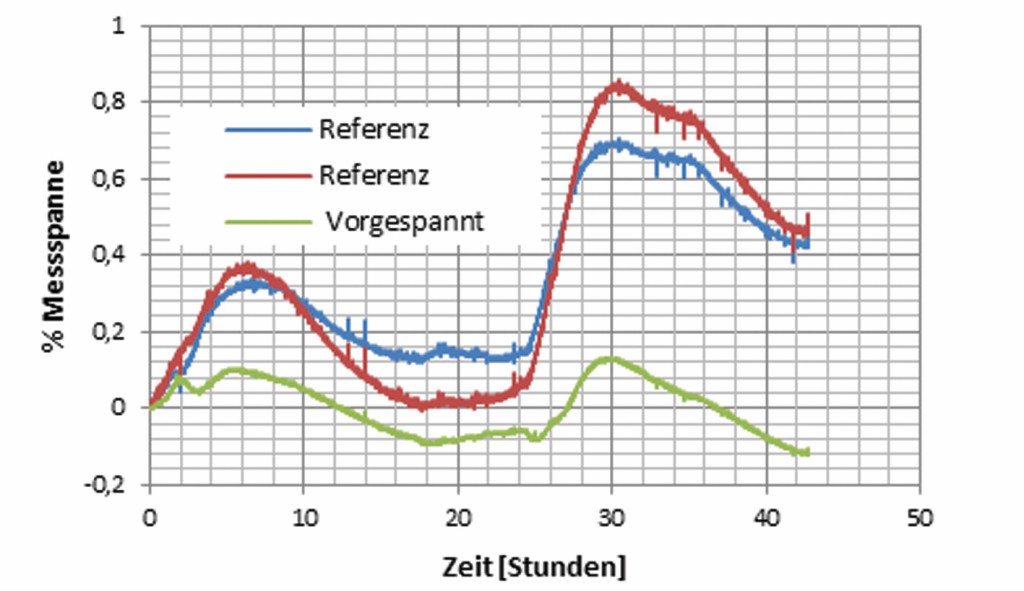
Bild 12 Änderung der Ausgangsspannung bezogen auf die Messspanne von 30 mV/V, Raumtemperatur 22 2 °C.
Foto: CiS Forschungsinstitut für Mikrosensorik GmbH
Zu sehen ist nur die Änderung der Ausgangsspannung bezogen auf die Messspanne von 30 mV/V. Die vorgespannte Schraube wurde zuvor noch 24 h bei 60 °C künstlich gealtert, die Referenz erfuhr keine thermische Behandlung. Zu erkennen ist, dass sich die vorgespannte Schraube (25 kN) durch die Voralterung, bezogen auf die Messspanne, stabiler als die unbehandelten Referenzen verhält. Um die Funktion zu bewerten, ist es wichtig darauf hinzuweisen, dass es sich um eine Standardschraube handelt, welche sich durchaus plastisch verformen kann, und kein Präzisionskraftsensor.
Bild 13 zeigt alle drei Sensoren einer vorgealterten Schraube über 7 Tage. Eine Kompensation des Temperatureinflusses wurde nicht durchgeführt.
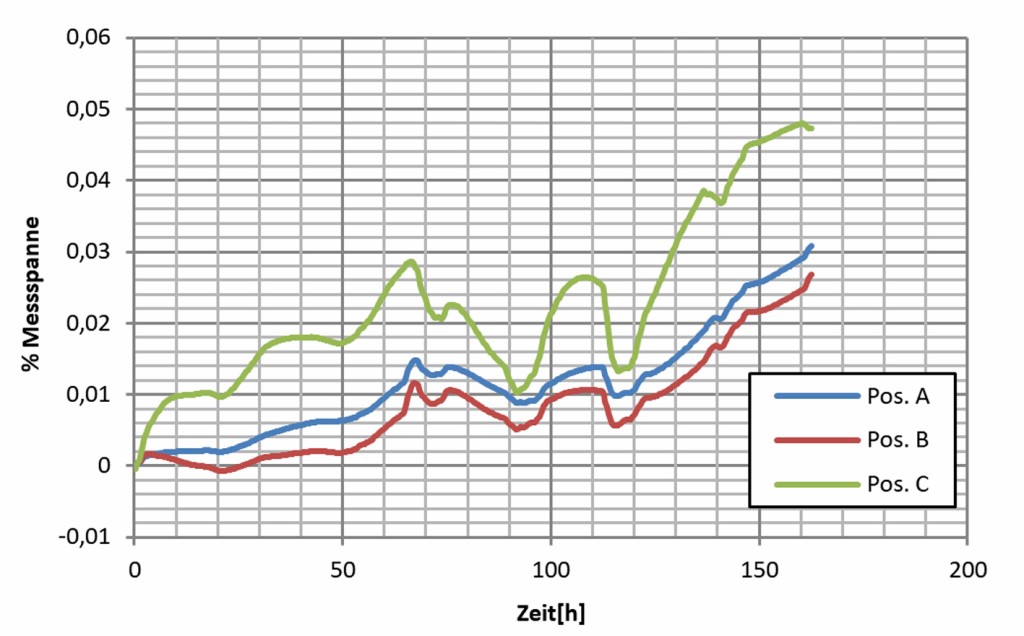
Bild 13 Änderung der Ausgangsspannung bezogen auf die Messspanne von 30 mV/V, Raumtemperatur 20 4 °C.
Foto: CiS Forschungsinstitut für Mikrosensorik GmbH
Es konnte gezeigt werden, dass mit der Anordnung von Sensoren auf dem Schraubenkopf die Vorspannkraft verlässlich bestimmt werden kann. Ein weitgehend kalibrierfreier Aufbau kann realisiert werden, wenn die Position der Sensoren auf dem Schraubenkopf exakt eingestellt werden. In diesem Fall wird es ausreichen nur den Nullpunkt zu kalibrieren, die Empfindlichkeit der untersuchten Sensoren lag in einer sehr engen Bandbreite. Die Langzeitstabilität konnte nur in Stunden untersucht werden, erforderlich sind aber Jahre, dies wird noch weitere Zeit benötigen. TS684
Literatur
[1] Rausch, J. F. K.: Entwicklung und Anwendung miniaturisierter piezoresistiver Dehnungsmesselemente. TU Darmstadt, Inst. für Elektromechan. Konstruktionen, 2012.
[2] Frank, T. Khatri, M. Fiedler, M. Gruen, A. Kermann, M. Cyriax, A. Ortlepp, T.: Miniaturized silicon strain gauge elements to accurately measure mechanical quantities, Germany, AMA Conferences (2015).
Th. Frank, A. Grün, M. Kermann, A. Cyriax, A. Steinke, Th. Ortlepp, K. Ettrich CiS Forschungsinstitut für Mikrosensorik GmbH, Erfurt