Hydraulische Prüfverfahren in der Praxis
Bei der Druckbehälterprüfung kommen verschiedene Verfahren zum Einsatz, von denen einige die Festigkeit des Prüfmusters zerstörend ermitteln sollen. Dies sind aus Gründen der Handhabbarkeit und Sicherheit überwiegend hydraulischen Prüfverfahren. Nach derzeitigem Stand der Regelwerke hängt die Baumusterzulassung von wenigen Ergebnissen aus den hydraulischen Prüfungen ab. Dies bedeutet, dass die Angabe eines Ergebnisses mit einer hohen Verantwortung des durchführenden Prüflabors verbunden ist. Teil 1 des Beitrags erläutert die Notwendigkeit standardisierter Verfahren und gibt einen praxisorientierten Einblick in die Prüftechnik unter Berücksichtigung der Besonderheiten bei der Durchführung der langsamen hydraulischen Berstprüfung aus Sicht des Prüfingenieurs.
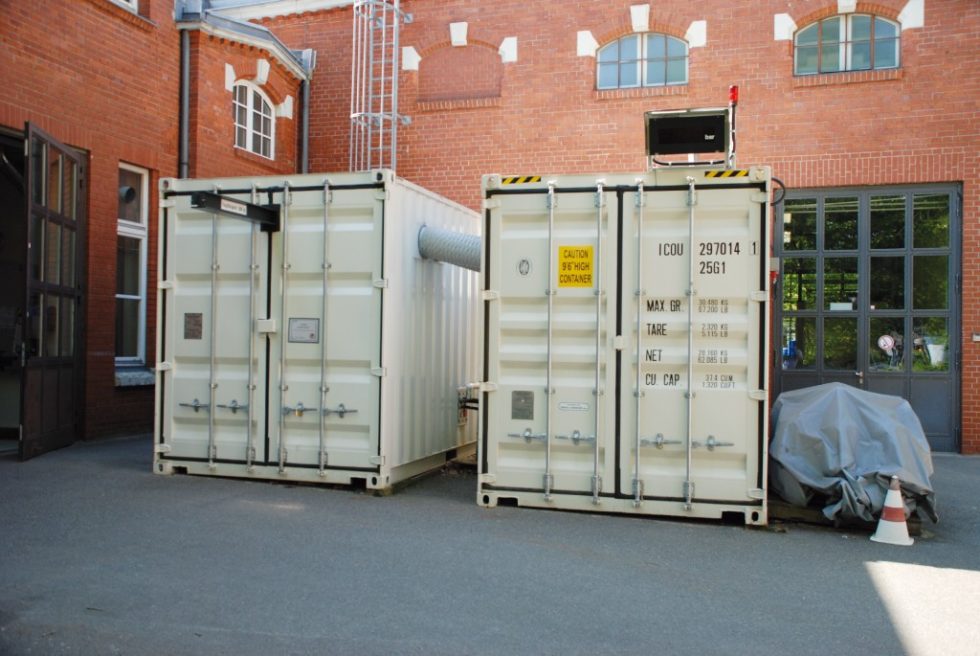
Quelle: BAM
Druckbehälter zur Speicherung von Gasen findet man in allen Bereichen, sei es beim Transport von Gasen, in Fahrzeugen als Treibgas oder auch im Freizeitbereich fürs Grillen oder Kochen mit Flüssiggas.
Bei der Prüfung der für die Speicherung benötigten Druckbehälter kommen unterschiedliche Verfahren zum Einsatz. Die üblichen Verfahren zur Festigkeitsbeurteilung sind verschiedene hydraulische Innendruckprüfungen. „Weit gefasste“ Prüfungsvorgaben in den Normen und Vorschriften bedeuten einen Ermessensspielraum in der Ausführung der Prüfung, der die Prüfergebnisse beeinflusst. Hinzu kommen noch unterschiedliche Anlagenkonzepte in der Nutzung, die die Prüfergebnisse zusätzlich beeinflussen. Kritisch werden solche Einflüsse aber z. B. im Zusammenhang mit dem vom Fachbereich 3.2 der Bundesanstalt für Materialforschung und -prüfung (BAM) angewendeten Verfahren zur Prüffristenfestlegung von Composite-Druckbehältern, das auf statistischen Bewertungen basiert. Um diese Einflüsse zu minimieren, wurden die hydraulischen Prüfverfahren für die Anwendung an der BAM erheblich konkretisiert.
Hydraulische Verfahren in der Druckbehälterprüfung
In den zahlreichen Normen für die Auslegung, den Bau und die Prüfung unterschiedlicher Arten und Einsatzzwecke von (Composite-)Druckbehältern, kommen verschiedene hydraulische Prüfverfahren zum Einsatz. Dabei wird das Prüfmuster, sprich der Druckbehälter, immer mit einer Flüssigkeit befüllt. Das Prüfmuster ist dann über eine Druckleitung mit der entsprechenden hydraulischen Druckerzeugungsanlage zu verbinden, die entweder manuell oder automatisiert das Prüfmedium in das Prüfmuster pumpt. In einem geschlossenen System führt das geförderte Volumen unter Berücksichtigung der Nachgiebigkeit des Prüfmusters und der Kompressibilität des Prüfmediums zu einem Druckanstieg.
Die einfachste Form der Druckerzeugung ist die Verwendung einer Handpumpe mit einem Prüfmedienreservoir, wie sie in Bild 1 schematisch dargestellt ist.
Durch Betätigen der Pumpe wird mit jedem Kolbenhub Prüfmedium aus dem Reservoir in das Prüfmuster gefördert. Der Druck steigt an. Ein Rückschlagventil verhindert das Zurückströmen der Flüssigkeit beim Rückhub der Pumpe.
Zu den hydraulischen Prüfverfahren für Druckbehälter zählen die hydraulische Berstprüfung, die Lastwechselprüfung (auch Druckschwellprüfung oder Ermüdungsprüfung). Von dieser gibt es zwei sehr häufig angewendete Varianten, die bei Raum- und die bei Extremtemperaturen. Hinzu kommt die klassische Zeitstandsprüfung, die ein Auslagern unter Druck bei erhöhter Temperatur bedeutet und meist mit einer Berstprüfung abgeschlossen wird. Die Berstprüfung nimmt demnach eine wesentliche Rolle als eigenständige Prüfung oder als Nachfolgeprüfung zur Ermittlung der Restberstfestigkeit nach Vorschädigung ein.
Notwendigkeit standardisierter Prüfverfahren
In den Bildern 2 bis 4 sind die Druck-Zeit-Diagramme von hydraulischen Berstversuchen dargestellt.
Alle Prüfungen werden entsprechend den geltenden Vorschriften durchgeführt. Vergleicht man den Verlauf des Drucks über der Zeit sind deutliche Unterschiede erkennbar. In Bild 2 ist die Wirkung einer Handpumpe dargestellt. Es zeigt eine unregelmäßige Anstiegskurve des Drucks. Bild 3 zeigt eine Prüfung, die mit einer druckluftbetätigten Hochdruckpumpe durchgeführt wurde. Konzeptbedingt verlangsamt sich hierbei die Hubfrequenz mit Zunahme des Enddrucks. Deshalb ergibt sich ein zwar kontinuierlicher aber nicht linearer Druckanstieg. Ein bis zum Ende linearer Anstieg wird in Bild 4 gezeigt. Hier wird die Berstprüfung mit einer geregelten Druckerzeugungsanlage durchgeführt. Die gewünschte Druckanstiegsrate kann über die Software in einer weiten Spanne ausgewählt werden. Der Istdruck folgt im Rahmen der Leistungsfähigkeit automatisch dem Solldruck bis zum Versagen des Behälters.
Bei allen Prüfungen konnte das Prüfmuster zum Bersten, d. h. zum schlagartigen Versagen bis zur vollständigen Druckentlastung, gebracht werden. Daher konnte für jedes Prüfmuster ein Berstdruck als Ergebnis der zerstörenden hydraulischen Berstprüfung angegeben werden. Bezogen auf die Druck-Zeit-Verläufe während des Druckaufbaus muss man anzweifeln, dass so unterschiedlich erzeugte Prüfergebnisse an ein und demselben Baumuster miteinander vergleichbar sind. Sind die Prüfbedingungen, wie z. B. Temperatur und Feuchte, ebenfalls stark unterschiedlich, wird die Reproduzierbarkeit von Ergebnissen weiter eingeschränkt. Die einzelnen Prüfmuster eines Baumusters selbst unterliegen einer gewissen Streuung, die zum einen material- und konstruktionsbedingt und zum anderen fertigungsbedingt zwangsläufig vorhanden ist. Im Zuge statistischer Auswerteverfahren von Berstergebnissen, (siehe hierzu Verfahren zur Prüffristenfestlegung und zum UN-Service-Life-Test der BAM [1]), müssen alle Einflüsse, die nicht aus dem Prüfmuster kommen, minimiert werden. Dies ist umso wichtiger, da diese Ergebnisse zur Sicherheitsbewertung herangezogen werden. Ziel und Zweck der Konkretisierung von Prüfverfahren ist die Durchführung von hochgradig reproduzierbaren Prüfungen. Diese Modifikationen der Verfahren machen die Bauteilprüfung vergleichbarer und von der Prüfeinrichtung nahezu unabhängig.
Vorbereitung zur hydraulischen Berstprüfung
Das Verfahren der hydraulischen Berstprüfung wird im Folgenden in einer speziellen Form, der langsamen Berstprüfung, gemäß Anlage „Prüfverfahren zur Prüffristenfestlegung“ praxisorientiert vorgestellt [1].
Vor Beginn der Prüfung ist der zu prüfende Druckbehälter zu identifizieren und zu registrieren. Dabei werden alle bekannten Daten des Behälters erfasst sowie eine Fotodokumentation erstellt. Der Prüfer erhält in Form einer vorbereiteten Prüfkarte die detaillierten Angaben zur Durchführung der Prüfung. Gemeint sind damit die Vorgaben für die Prüfparameter sowie die Prüfbedingungen. Das Prüfmuster wird mit dem Prüf- medium möglichst vollständig befüllt, da Luft, die sich im hydraulischen System befindet, erheblichen Einfluss auf das Regelverhalten des Druckerzeugers während der Druckanstiegsphase haben kann. Außerdem bedeutet verdichtete Luft ein energiereicheres Verhalten beim Entspannen im Moment des Berstens, das vom Schutzbehälter der Prüfeinrichtung zusätzlich aufgenommen werden müsste. Bei der Wahl des Prüfmediums (Wasser, Öl, Glykol etc) ist auf die Materialverträglichkeit zu achten. Auch Umwelt-, Entsorgungs- und Arbeitsschutzaspekte sind hier zu berücksichtigen.
Ist das Prüfmuster befüllt, wird ein entsprechender Ventiladapter in das Flaschengewinde montiert. Das Dichtungskonzept zwischen Druckbehälter und Adapter ist individuell auf das Prüfmuster abzustimmen und muss kompatibel und sicher handhabbar sein. Mit einem Zusatzventil in unmittelbarer Nähe des Flaschenadapters oder anderen Möglichkeiten ist ein Entweichen des Prüfmediums nach dem Befüllen zu verhindern. Das Prüfmuster wird anschließend in einen Schutzbehälter eingebracht (oft liegend) und erst dann mit der hydraulischen Druckerzeugungsanlage verbunden. Dafür kommen in der Regel Hochdruckleitungen (Rohre) zum Einsatz. Bevor die Verschraubung festgezogen wird, ist die gesamte Rohrleitung bis zum Prüfmuster zu entlüften. Es wird empfohlen, anschließend einen Drucktest bis max. 20 % des Prüfdrucks PH für unbelastete Prüfmuster oder max. bis PH für schon belastete Prüfmuster durchzuführen [1]. So kann die Dichtigkeit des Aufbaus mit einer hohen Zuverlässigkeit bestätigt werden.
Um die Sicherheit von Mensch und Material bei einer zerstörenden Prüfung zu gewährleisten, wird nun der Schutzbehälter geschlossen und die Umgebung gegen unbefugtes Betreten gesichert. Die Messsensoren in der Prüfkammer für Temperatur und Feuchte bzw. die Temperatursensoren auf der Prüfmusteroberfläche werden online erfasst und mit den Vorgaben verglichen. Die Temperaturen während der Prüfung müssen innerhalb einer bestimmten Spanne liegen. Die Feuchte wird lediglich für eine ggf. Analyse von beeinflussenden Faktoren aufgezeichnet. Das Drucksignal liefert ein nicht in die Druckerzeugungsanlage integrierter Druckaufnehmer (Messbereich auf erwarteten Berstdruck abgestimmt), der sich in der Rohrleitung in der Nähe des Prüfmusters aber außerhalb der Prüfkammer befinden sollte. Dies ist wichtig, um Messfehler durch die zeitliche Verzögerung des Drucks vom Druckerzeuger zum Prüfmuster zu vermeiden. Die Problematik der Verzögerung nimmt mit abnehmendem Rohrleitungsquerschnitt und steigender Rohrlänge zu. Deshalb ist die Verbindung möglichst optimal und einheitlich vom Druckerzeuger zum Prüfmuster zu wählen. Trotz Kalibrierung der verwendeten Messaufnehmer sind weitere Fehler, z. B. in der Einstellung der Messkanäle, möglich.
Um solche Bedienerfehler zu vermeiden, sind Probemessungen hilfreich, um die Plausibilität der Messergebnisse zu überprüfen. Dies könnte unter Umständen schon beim Drucktest mit überprüft werden. Praktisch werden die Druckwerte am externen Messpunkt mit denen im Druckerzeuger zur Regelung integrierten Aufnehmer verglichen. Die Messrate für die Prüfung wird gemäß Prüfvorgaben eingestellt. Minimalforderung in diesem Falle ist ein Druckmesswert je Sekunde. Die Werte für Temperatur und Feuchte sind nur einmal vor und einmal nach der Prüfung zu notieren [1]. Einfachheitshalber sind die Möglichkeiten moderner Messsysteme zu nutzen. Diese bieten eine kontinuierliche Aufzeichnung sämtlicher Sensoren, die für eine Berstprüfung notwendig sind. Somit erhält man anschließend einen zeitsynchronisierten Druck/Temperatur/Feuchte-Verlauf. Mit den in der BAM verwendeten Druckerzeugern ist es zusätzlich möglich, das Signal für den Kolbenweg und daraus berechnet das Fördervolumen aufzuzeichnen. Hierdurch kann man sich anschließend ein umfangreiches Bild über den Prüfungsverlauf und das Materialverhalten machen. Einige Regelwerke für die Druckbehälterprüfung verlangen sogar die Angabe des Gesamtfördervolumens bis zum Bersten.
Durchführung der hydraulischen Berstprüfung
Ist der Prüfaufbau sowie die Messtechnik vorbereitet, werden die prüfungsrelevanten Einstellungen an der Druckerzeugungsanlage vorgenommen. Bei der Durchführung eines SBT (slow burst test) ist die Druckanstiegsrate p ≤ 20%PH/h zu wählen. Die gewählte Druckanstiegsrate ist vor der Prüfkampagne zur Baumusterzulassung festzulegen und über den gesamten Lebenszyklus identisch anzuwenden. Der Soll-Ausgangsdruck liegt bei 0 bar. Praktisch wird ein Anfangswert von maximal 5 % PH akzeptiert [1]. Diese Öffnungsklausel ist bei großen sehr „elastischen“ Behältern, z.B. Typ IV mit Kunststofflinern, nötig. Um überhaupt einen Druck messtechnisch erfassen zu können, muss die Druckerzeugungsanlage eine relativ große Menge Medium in das Prüfmuster fördern. Erst wenn sich der Liner (gasdichter Innenbehälter/Blase eines Druckbehälters) an die Wandung der Composite-Ummantelung angelegt hat und ein Druck messbar wird, ist der Ausgangspunkt der Prüfung erreicht.
Weiterhin ist sicherzustellen, dass die Abschaltgrenzen an der Druckanlage so gewählt werden, dass sie keine unbeabsichtigte Störung auslösen können. Auch die Aufzeichnungsdauer der Messtechnik ist großzügig zu wählen, damit es nicht zu fehlenden Messdaten kommen kann. Hier gilt ggf. das 4-Augen-Prinzip, um Fehlermöglichkeiten zu reduzieren. Es erfolgt der Start der Messtechnik und der Start der Prüfung.
Prüfeinrichtung
Die verwendete Hochdruckanlage in Bild 5 erzeugt einen hydraulischen Druck bis maximal 2 300 bar. Ein Kolben (Plunger), der über eine Kugelumlaufspindel mit einem Getriebe verbunden ist, wird über einen elektrischen Servomotor verfahren.
Dabei komprimiert der Kolben eine hydraulische Flüssigkeit (hier VE-Wasser) und fördert diese in das Prüfmuster, bis es versagt. Die Regelung erfolgt grundsätzlich nach dem gemessenen Druck. Es wird eine Solldruckkurve aufgrund der Eingabe der Druckanstiegsgeschwindigkeit vorgegeben. Der Regler versucht den Istdruck dem Solldruck anzupassen. Wie gut dieses Anpassen funktioniert ist a) vom Regler und der eingestellten Regelparameter und b) vom Prüfmuster (Elastizität, Druckniveau, Volumina) abhängig. Da der Hub des Kolbens bei diesem System begrenzt ist, schließt ein Ventil bei Erreichen der Hubgrenze das Prüfmuster von der Anlage ab. Der Kolben fährt zurück, das Ventil öffnet wieder und der Kolben „schiebt“ die Flüssigkeit wieder zum Prüfmuster. Da dies aber einen kontinuierlichen Druckanstieg stören würde, kann über eine Zusatzfunktion in der Bedienung der Anlage auch ein gleichförmig stufenweiser Druckanstieg realisiert werden. Dabei werden die kurzen, immer gleich langen Haltezeiten der möglichst kleinen Stufen zum Zurückpositionieren des Kolbens genutzt. Somit ist ein quasikontinuierlicher Druckanstieg möglich, der unabhängig vom benötigten Gesamtfördervolumen ist. Die abgebildete Anlage besitzt einen internen Tank für 30 l Prüfmedium, der vor der Prüfung mit VE Wasser bzw. mit einem korrosionshemmenden Mittel gefüllt wird. Bei Prüfungen, die mehr Fördervolumen benötigen, kann ein externes Reservoir angeschlossen werden.
Die Druckerzeugungsanlage in Bild 5 ist in einem 20“-Standardseecontainer untergebracht und damit mobil. Ein weiterer Container gleicher Bauart dient als Prüfraum (Bilder 6 und 7) und bietet Platz für einen großen robusten, mehrteiligen Schutzbehälter aus Stahl mit einem flexiblen Deckelsystem.
Dieser Schutzbehälter nimmt sämtliche Energien beim Bersten der Prüfmuster auf und darf diese bestenfalls in etwas Bewegung umsetzen. Die Wandung des Prüfcontainers, in dem der Schutzbehälter steht, ist zusätzlich von innen mit massiven Vierkantholzbohlen komplett ausgekleidet. Eine Kranbahn im Inneren ermöglicht das Handling von schwerem Equipment und großen Prüfmustern.
Beide Container sind über eine dauerhaft frostgeschützte Hochdruckleitung miteinander verbunden, sodass die Möglichkeit besteht, ganzjährig Berstprüfungen durchzuführen. Zusätzlich ist der Prüfcontainer über vier Luftkonditionierschläuche mit einer Klimaanlage im Anlagencontainer verbunden. Diese hält beide Container auf einer konstanten Prüftemperatur. Sowohl die Prüfanlage als auch sämtliches Messequipment sind vom Anlagencontainer aus zu bedienen. Ein Labornetzwerk ermöglicht den Fernzugriff auf die Anlagensteuerung und Messtechnik. Aufgrund der getrennten Räume sind Mensch und Prüftechnik geschützt. Die Bilder 8 und 9 zeigen den schematischen Aufbau der Prüfeinrichtung sowie die Umsetzung in die Praxis.
Auswertung der Messwerte einer Berstprüfung
Während jeder Berstprüfung werden der Berstdruck, die Zeit bis zum Versagen, eventuell das Gesamtfördervolumen sowie das Versagensverhalten des Behälters dokumentiert. So werden zur Auswertung z. B. die gemessenen Druckwerte (y-Achse) über der Zeit (x-Achse) in einem Diagramm dargestellt. Der Datenpunkt nachdem der Druckwert schlagartig gegen Null geht, ist der Moment des Totalversagens. Mithilfe der Zeitspanne seit Beginn der Prüfung und dem Berstdruck kann die reale Druckanstiegsgeschwindigkeit überprüft werden. Dies gibt die erste Aussage über die Genauigkeit der Prüfung und dient zusätzlich zur Plausibilitätsüberprüfung des Anlagenverhaltens. Ausgehend von der Solldrucklinie wird zusätzlich ein Toleranzband in die Grafik eingezeichnet. Dieses Toleranzband ist für das Verfahren der langsamen Berstprüfung mit p 1 % Prüfdruck (PH) festgelegt [1]. Alle Werte der Istdruckkurve müssen innerhalb dieses Toleranzbandes liegen. Dabei ist zu beachten, dass es technisch bedingt zu einem Unter-und Überschwingen der Solldruckkurve zu Beginn einer Prüfung kommen kann. Eine Abweichung der Kurve bis zu einem Druckniveau von max. 20% PH ist demnach akzeptabel [1]. Danach dürfen die gemessenen Druckwerte die Grenzen des bereits beschriebenen Toleranzbandes nicht überschreiten. Eine akzeptierte Ausnahme ist die kurze Unterschreitung der Solldruckkurve im Falle der spontanen Volumenvergrößerung durch Faserteilversagen. Diese Abweichung ist prüfmusterbedingt und somit auch Teilergebnis der Berstprüfung. Ergebnisse von Prüfungen, die die Anforderungen nicht einhalten, müssen verworfen werden [1].
Das linke Diagramm in Bild 10 zeigt das prinzipielle Vorgehen bei der grafischen Auswertung einer Berstprüfung. Im rechten Bereich ist ein Datenausschnitt einer realen Berstprüfung an einer Atemluftflasche mit einem Nennbetriebsdruck (PW) von 300 bar mit dem entsprechenden Toleranzbereich dargestellt.
Die einzelnen Druckwerte liegen im vorgegebenen Bereich. Das Prüfergebnis kann verwendet werden.
Fazit und Ausblick
Um die Resultate aus den hydraulischen Prüfungen statistisch bewerten zu können, benötigt man Prüfergebnisse, die auf reproduzierbaren Prüfverfahren basieren. Dabei geht es nicht nur um ein funktionierendes Qualitätsmanagementsystem im Prüflabor, sondern vornehmlich um die Reduzierung des Einflusses der Prüftechnik und des Prüfverfahrens auf die Streuung der Ergebnisse. Dieser Einfluss kann erst durch ins Detail konkretisierte Prüfungsanforderungen minimiert werden.
Dieser Anforderung entsprechend wurde ein Verfahren beschrieben, das den Spielraum bei der Durchführung der hydraulischen Berstprüfung verringert und somit eine Streuung der Ergebnisse garantiert, die annähernd ausschließlich aus den Prüfmustern kommt. Die Prüfmusterdokumentation spielt dabei eine zentrale Rolle. Zwischen den hydraulischen Prüfungen im Zuge der Zulassung eines Baumusters und den hydraulischen Prüfungen zur Prüffristenfestlegung liegt eine Zeitspanne von mehreren Jahren. Um die Prüfergebnisse auch nach einer längeren Gebrauchsdauer (z. B. zehn Jahre) miteinander vergleichen zu können, müssen die zerstörenden Prüfungen reproduzierbar durchgeführt und vollständig dokumentiert und archiviert werden [1].
Die Prüfung an neuen Materialien oder neuen Produkten erfordert eine moderne Prüftechnik, die sich mit dem Stand der Technik stetig weiterentwickeln muss. Demzufolge ist die zunehmende Automatisierung in der Prüftechnik ein wichtiger Schritt um Prüfungen reproduzierbarer durchzuführen.
Wie ein konkretisiertes Verfahren zur hydraulischen Lastwechselprüfung in der Praxis aussieht, wird in einem nächsten Beitrag betrachtet. Dabei wird ebenfalls Bezug zur verwendeten Prüftechnik genommen, unter dem Hauptgesichtspunkt, welche Anforderungen in der BAM an eine moderne Lastwechselanlage zur Prüfung von Druckbehältern bis 1 200 bar gestellt werden. TS 591
Literaturverzeichnis
[1] Mair, G. W.; Scherer, F.; Saul, H.; Spode, M.; Becker, B.: CAT (Concept Additional Tests): Concept for Assessment of Safe Life Time of Composite Pressure Receptacle by Additional Tests. Berlin 2015. www.bam.de/en/service/amtl_mitteilungen/gefahrgutrecht/gefahrgutrecht_medien/druckgefr_ regulation_on_retest_periods_technical_ appendix_cat_en.pdf
Dipl.-Ing.(FH) André Schoppa, Dipl.-Ing.(FH) Mariusz Szczepaniak, Dr.-Ing. Georg W. Mair, Bundesanstalt für Materialforschung und -prüfung, Berlin, Fachbereich 3.2 Gefahrguttanks und Unfallmechanik, Arbeitsbereich Druckgeräte – Druckgefäße, Treibgasspeichersysteme.