3D-Metalldruck und Carbonbeton: Reif fürs Museum
Zwei High-Tech-Objekte sind durch die Aufnahme ins Deutsche Museum geadelt worden: Eine Carbonbetonbrücke, die gerade in Oslo mit zwei Preisen ausgezeichnet wurde, und ein Tensegrity-Turm, der den Stahlbau mit additiv gefertigten Verbindungselementen voranbringt.
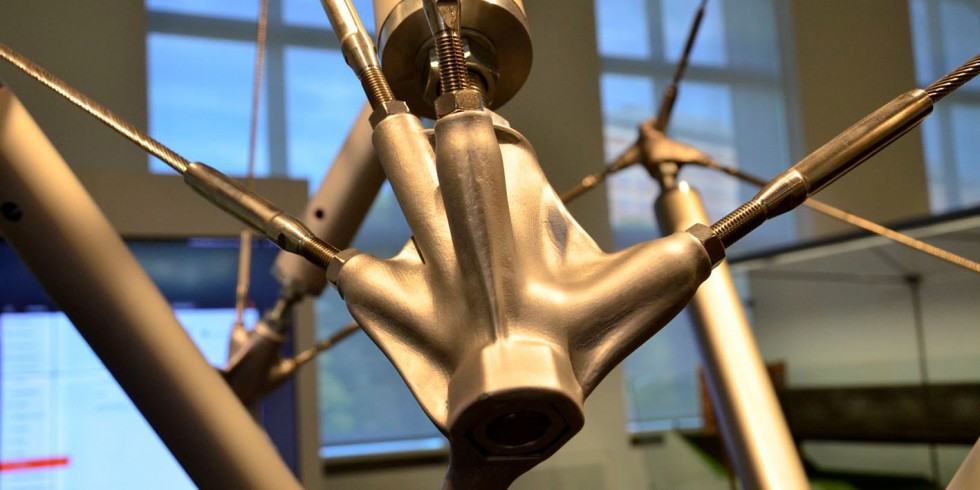
Die 3D-gedruckten Verbindungsknoten des Tensegrity-Turms müssen enorme Kräfte aufnehmen. Formoptimierung spart bis zu 28 Prozent Material ein.
Foto: VDI Fachmedien / Karlhorst Klotz
Der sogenannte Tensegrity-Turm ist ein fünf Meter hohes Gebilde aus Rohren und Seilen, das scheinbar schwerelos im Raum steht. Er zeigt, wie Strukturen sich allein durch Spannung stabilisieren lassen (siehe Kasten). Ein technischer Leckerbissen bei der Realisierung – und interessant für die Weiterentwicklung des Stahlbaus – sind die Verbindungselemente, die von der Technischen Universität München kamen.
3D-Metalldruck für extrem belastbare Verbindungsknoten
Denn egal ob Brücke, Hochhaus oder Lagerhalle – Bauwerke, deren Grundstruktur aus Aluminium oder Stahl besteht, brauchen Verbindungselemente, die Profile, Seile oder Bleche zusammenhalten. „Bisher werden solche Verbindungsknoten gefräst, geschweißt oder gegossen“, erklärt Florian Oberhaidinger vom Lehrstuhl für Metallbau der TUM. „Mit additiven Fertigungsverfahren könnte man wesentlich materialsparender arbeiten. Doch der 3D-Druck hat sich im Metallbau noch nicht etabliert.“
Im Projekt Tensegrity-Turm konnte der Ingenieur zusammen mit seinem Team zeigen, dass sich auch Bauteile, die hohen Belastungen ausgesetzt sind, mit Drucktechnik formoptimiert und ressourcenschonend fertigen lassen. „Es war daher eine besondere Herausforderung, diese Verbindungsknoten zu designen und mit unserem 3D-Drucker zu fertigen“, erläutert der Projektleiter.
Mit Hilfe von Computermodellen und Formfindungsmethoden wurde zunächst die Geometrie des Turmes ermittelt. Jeder Knotenpunkt musste dann unter Berücksichtigung dieser Geometrie entworfen, bemessen und formoptimiert werden. Durch die Formoptimierung, an der auch der TUM-Lehrstuhl für Statik beteiligt war, konnten die Ingenieure und Ingenieurinnen nach eigenen Angaben bis zu 28 Prozent Material einsparen.
Additive Fertigung mit pulverbettbasiertem Laserstrahlschmelzen
Für die Herstellung der Knoten nutzten sie den 3D-Drucker des Lehrstuhls für Metallbau. Beim pulverbettbasierten Laserstrahlschmelzen wird eine dünne Aluminiumpulver-Schicht an den Stellen, an denen festes Material entstehen soll, durch einen Laserstrahl Punkt für Punkt erhitzt und verschmolzen. Dann folgt die nächste Schicht.
Die Qualität des Werkstücks lässt sich dabei über die Laserleistung, Pulverschichtdicke, Scangeschwindigkeit und den Spurabstand steuern, erklärt Johannes Diller, der Spezialist im Team für additive Fertigung: „Unser Ziel war es, mit einem minimalen Einsatz von Ressourcen ein leichtes Bauteil mit hoher Festigkeit und Dichte herzustellen.“
3D-gedruckte Knoten durch Messungen überprüft
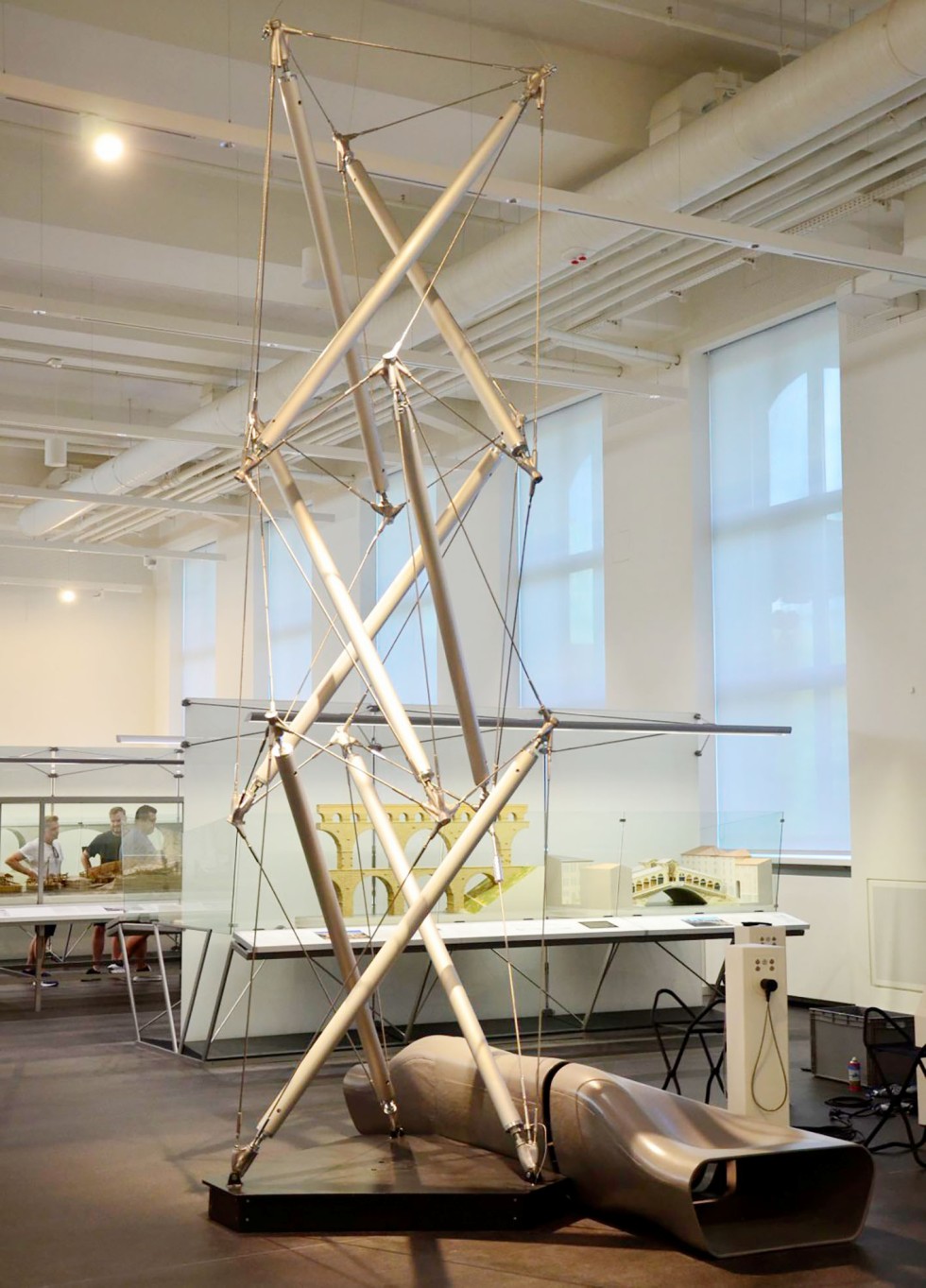
Der fast raumhohe Tensegrity-Turm hat bereits einen Platz im Deutschen Museum zwischen den schon länger vorhandenen Vitrinen der Ausstellung „Brücken und Wasserbau“ bekommen; an Erläuterungen wird noch gearbeitet.
Foto: VDI Fachmedien / Karlhorst Klotz
Messungen, die am TUM-Lehrstuhl für Metallbau durchgeführt wurden, haben bestätigt, dass die gedruckten Aluminiumknoten den Zugkräften und der dynamischen Belastung standhalten, denen sie im Tensegrity-Turm ausgesetzt sind. Mit dem Design, Druck und der anschließenden Prüfung der Bauteile haben die Forschenden der TUM die Grundlage geschaffen für weitere Entwicklungen. Die möglichen Anwendungen der additiven Fertigung im Metallbau sind vielfältig – Verbindungen werden überall gebraucht, wo aus Stützen, Trägern und Seilen Brücken oder Gebäude konstruiert werden.
Ästhetische Struktur
„So eine Tensegrity-Turm-Struktur aus scheinbar schwebenden Stäben ist sehr ästhetisch und lockt die Besucherinnen und Besucher an“, ist sich Kurator Moritz Heber sicher, der im Deutschen Museum für das Bauwesen zuständig ist. Das Besondere ist, dass jedes seiner Elemente entweder unter reiner Druckbelastung oder reiner Zugbelastung steht und der Turm aufgrund der hohen Vorspannung der Seile äußerst stabil ist. „Davon können sich die Besucherinnen und Besucher selbst überzeugen, da das Exponat angefasst werden soll – dafür gibt es extra massive Griffe an den Seilen“, erläutert Heber die Rolle des Exponats, an dem bei unserem Besuch im Museum Mitte Juli immerhin schon der erste der vorgesehenen Griffe montiert war.
Damit lässt sich das Tensegrity-Modell zur Einführung in das Thema Tragwerke nutzen, da die Ausstellung im Deutschen Museum nach statischen Gesichtspunkten gegliedert ist in Bogenbrücken (Druck), seilverspannte Brücke (Zug) und Balkenbrücken (Biegung, also Druck und Zug). Künftig – zu dem Exponat gibt es derzeit noch keine Erläuterungen – soll der Tensegrity-Turm dank eines Sensors und einer Echtzeitdarstellung des Rütteleffekts am Bildschirm fundamentale Grundlagen aufzeigen, nämlich wie Druck- und Zugkräfte in einer solchen Struktur sich dynamisch verhalten.
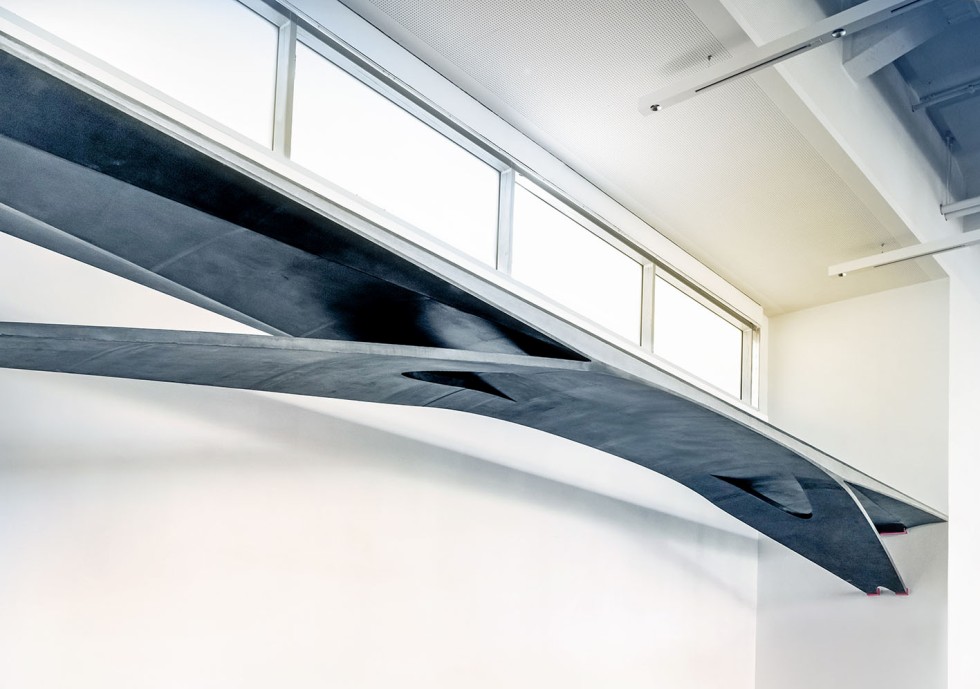
Die Carbonbetonbrücke im Deutschen Museum München, unmittelbar nachdem sie 2021 ihren Platz dort eingenommen hatte.
Foto: Ansgar Pudenz
Eine Brücke aus Carbon- und Infraleichtbeton
Ebenfalls in der am 7. Juli 2022 nach einer Sanierung wiedereröffneten Abteilung „Brücken und Wasserbau“, die abgesehen von diesen Exponaten im Wesentlichen auf dem Stand von 1998 verharrt, gehört seit 2021 auch eine Brücke, die schlankes Design mit Ressourceneinsparung vereint. Angefertigt und konzipiert wurde die Brücke aus Carbonbeton und Infraleichtbeton speziell für das Deutsche Museum durch Forschende des Instituts für Massivbau der TU Dresden.
Die Brücke präsentiert die Vorteile der neuartigen Materialkombination eindrucksvoll, kann allerdings trotz ihrer Spannweite von 9,5 Meter und ihrer Breite von etwa einem Meter nicht begangen werden, obwohl sie kein Funktionsmodell, sondern ein „Original in Lebensgröße“ ist. Der Grund: Sie ist in einer Nische in etwa vier Meter Höhe installiert, weder direkt zum Anfassen noch sehr augenfällig.
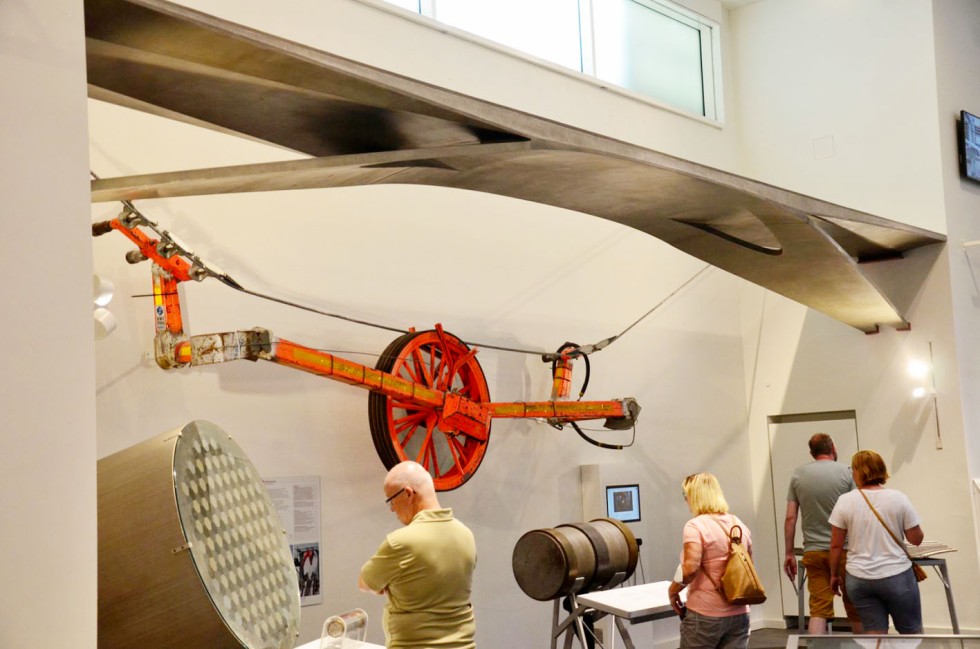
Die oben in einer Nische angebrachte CarboLight Bridge im Deutschen Museum in München ist inzwischen leicht zu übersehen, da darunter andere sehenswerte Exponate angebracht wurden, auf die der Blick von Besucherinnen und Besuchern leichter fällt.
Foto: VDI Fachmedien / Karlhorst Klotz
Auszeichnung für die „CarboLight Bridge“ beim fib-Kongress in Oslo
Viel beachtet wird sie jedoch in der Fach-Community. So kam die „CarboLight Bridge“ Mitte Juni 2022 im Rahmen des fib-Kongresses in Oslo zu Ehren. Die Tagung gilt als wichtiges Zusammentreffen von Betonforscherinnen und -forschern. Dort erhielt die Brücke gleich zwei Auszeichnungen: den Sonderpreis „Exceptional Recognition“ im Wettbewerb „Award for Outstanding Concrete Structures“ sowie den „Innovation Award 2022“ in der Kategorie „Structures“ für das Paper „An ultra-light Carbon Concrete Bridge: From Design to Realisation“ der Autoren Marc Koschemann, Iurii Vakaliuk und Manfred Curbach.
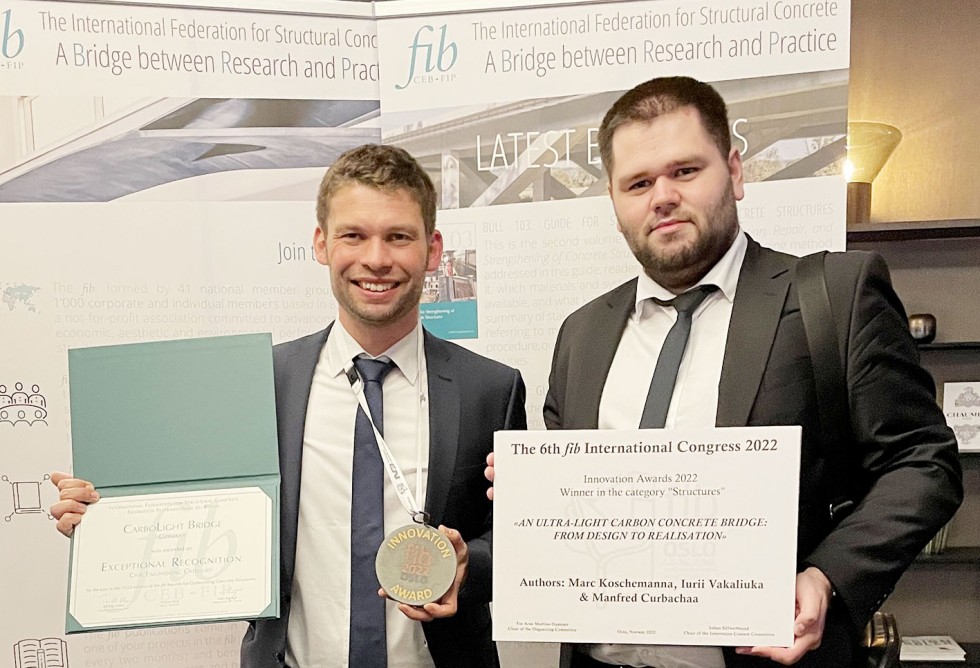
Marc Koschemann (links) und Iurii Vakaliuk präsentieren im Juni 2022 beim fib-Kongress in Oslo die Urkunden.
Foto: Michael Frenzel
„Die Baubranche muss sich wesentlich verändern, damit wir künftig ressourcenschonend bauen und gleichzeitig CO2-Emissionen reduzieren können. Der Einsatz innovativer Baustoffe und deren Kombination sowie die Optimierung von Bauwerken im Hinblick auf den Kraftfluss sind wesentliche Bestandteile, um dieses Ziel zu erreichen“, sagt der Bauingenieur Marc Koschemann, der den Bau der Brücke geplant und begleitet hat.
Die CarboLight Bridge wurde als filigranes Bauwerk aus zwei leicht geneigten V-Stützen, einem dreiteiligen Überbau und einem Konstruktionsgewicht von nur 2,1 Tonnen konzipiert. Die kraftflussoptimierte Form und der Sandwichaufbau des Überbaus spielen dabei eine wesentliche Rolle. Die biaxial gekrümmte Unterseite und die flache Deckschicht bestehen aus Carbonbeton, während die Schicht dazwischen aus Infraleichtbeton gefertigt wurde. Somit konnte Material eingespart und das Gewicht reduziert werden.
Optimiert: Lastabtragung und Design
Mit Hilfe einer parametrisierten 3D-Modellierung wurde die Geometrie hinsichtlich der Lastabtragung und des Designs optimiert. Durch Verknüpfung des 3D-Modells mit einem Statikprogramm war es möglich, die Brücke hinsichtlich Materialeinsatz und Lastabtrag quasi gleichzeitig zu optimieren, betont der für die 3D-Modellierung zuständige Architekt und Wissenschaftler am Institut für Massivbau Iurii Vakaliuk. „Dazu wurde eine Schnittstelle zu einer FEM-Software programmiert, die es ermöglicht, die Auswirkungen einer Geometrieänderung auf den Lastabtrag quasi zeitgleich zu ermitteln.“
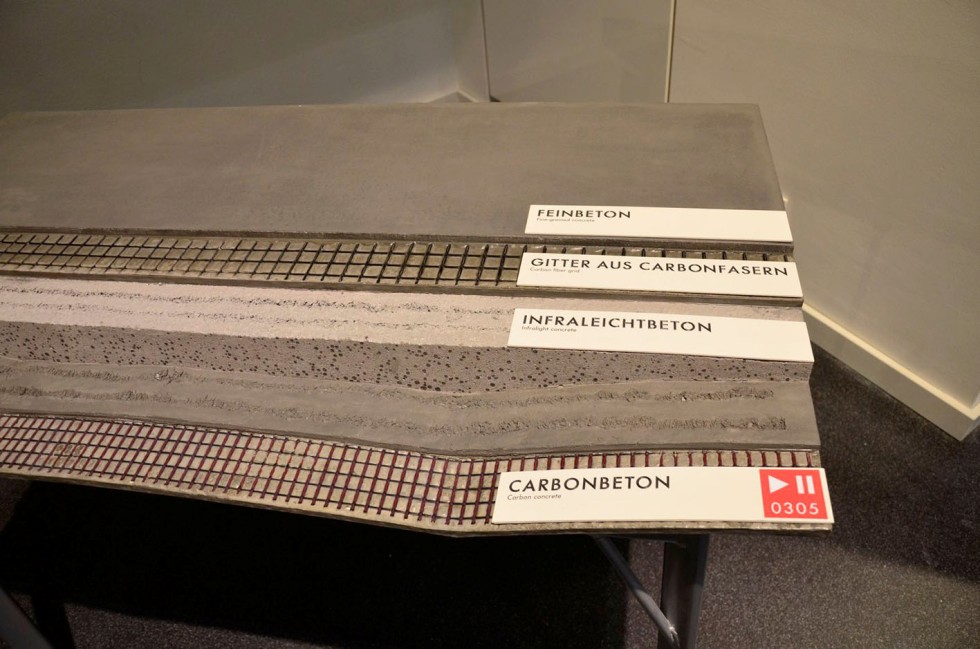
Darstellung des Aufbaus der CarboLight Bridge im Deutschen Museum München.
Foto: VDI Fachmedien / Karlhorst Klotz
Auf der Grundlage des endgültigen 3D-Modells wurde die Schalung aus gefrästem Sperrholz hergestellt. Um den Zusammenbau, das Aussehen und die Tragfähigkeit der Brücke und der einzelnen Segmente zu testen, wurde ein Testmuster der Brücke im Otto-Mohr-Laboratorium der TU Dresden hergestellt und geprüft.
Die Carbonbetonbrücke wurde als ein Demonstrator für das Schwerpunktprogramm 1542 „Leicht Bauen mit Beton – Grundlagen für das Bauen der Zukunft mit bionischen und mathematischen Entwurfsprinzipien“ erstellt, das durch die Deutsche Forschungsgemeinschaft (DFG) gefördert wurde. Unterstützt wurde das Vorhaben zudem durch die Firmen Heidelberger Beton GmbH und Hiconform – Freitaler Modellwerkstätten eG sowie dem Institut für Baustoffe der TU Dresden und dem Institut für Massivbau der TU München.
Deutscher Zukunftspreis als Initialzündung
Ins Deutsche Museum passt das Exponat umso besser, als dort auch eine Ausstellung über den Preis des Bundespräsidenten für Technik und Innovation zu sehen ist. Mit den Deutschen Zukunftspreis werden die Wissenschaftlerinnen und Wissenschaftler geehrt, die hervorragende technische, ingenieur- oder naturwissenschaftliche Innovationen hervorgebracht haben. Zur Riege der geehrten gehört seit 2016 für seine Arbeiten zu Carbonbeton auch Prof. Manfred Curbach von der TU Dresden.