Simulationsgestützte Prozessauslegung reduziert Bauteilverzug während der Fräsbearbeitung
Bauteilverzug ist ein großer Kostenfaktor in der Fertigung von Metallbauteilen, besonders bei großen, dünnwandigen Werkstücken, wie sie im Leichtbau und der Luftfahrt eine wichtige Rolle spielen. Das Fraunhofer-Institut für Produktionstechnologie IPT in Aachen hat gemeinsam mit Partnern ein System zur Reduzierung eigenspannungsbedingter Bauteilverzüge entwickelt: Mit simulationsgestützter Prozessauslegung und einem neuartigen Spannsystem kann es Unternehmen künftig gelingen, den Bauteilverzug bei der Fräsbearbeitung deutlich zu reduzieren.
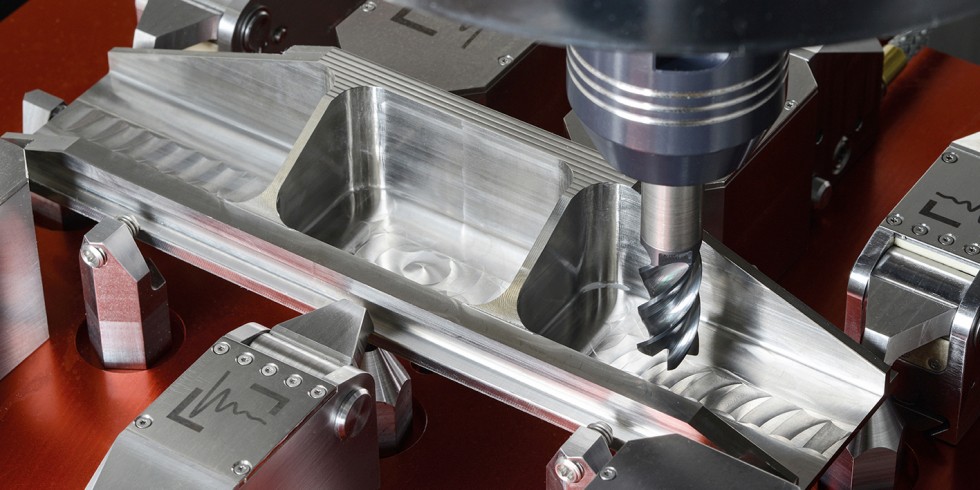
Im Forschungsprojekt „VoKoEs“ entwickelte das Projektteam eine Simulationssoftware zur Vorhersage und Reduzierung von Bauteilverzügen sowie ein adaptives, hydraulisches Spannsystem für die Fräsbearbeitung von Luftfahrtstrukturbauteilen.
Foto: Fraunhofer IPT
Fraunhofer IPT reduces part distortion during milling
Abstract: Part distortion is a major cost factor in the production of metal components, especially for large, thin-walled workpieces such as those that are important in lightweight construction and aviation. Together with partners, the Fraunhofer Institute for Production Technology IPT in Aachen has developed a system for reducing part distortion caused by residual stress: With simulation-based process design and a new clamping system, companies will be able to significantly reduce part distortion during milling operations in the future.
Bei der Herstellung und anschließenden Wärmebehandlung von Rohlingen aus Metall entstehen Eigenspannungen, die bei der Zerspanung zu Form- und Maßabweichungen des Bauteils führen. Vor allem nach dem Abspannen, wenn das Werkstück aus dem Spannsystem gelöst wird, kommt es häufig zu deutlichem Verzug des Bauteils. Solche Bauteilverzüge führen dazu, dass Fertigungstoleranzen nicht eingehalten werden können und das Bauteil aufwendig nachbearbeitet werden muss. Ein Report des Luftfahrt-Unternehmens Boeing aus dem Jahr 2001 bezifferte die jährlichen Kosten des Unternehmens für eigenspannungsbedingte Nachbearbeitungen und Ausschuss auf rund 290 Millionen US-Dollar.
Finite Cell Method zur Simulation eigenspannungsbedingter Bauteilverzüge
Ein Team des Fraunhofer IPT entwickelte gemeinsam mit Partnern im Forschungsprojekt „VoKoES“ ein Konzept bestehend aus einer Simulationssoftware und einer neuartigen Spannvorrichtung, mit dem der Bauteilverzug gewalzter und wärmebehandelter Halbzeuge prognostiziert und reduziert werden kann. Am Beispiel eines Luftfahrtstrukturbauteils aus der Titanlegierung Ti-6AI-4V konnte das Projektteam nachweisen, dass die entwickelten Lösungen den Verzug um bis zu 94 % reduzieren.
Die Forscherinnen und Forscher des Fraunhofer IPT programmierten im ersten Schritt gemeinsam mit dem Partner Access e.V. eine thermomechanische Simulation zur Bestimmung von Eigenspannungszuständen in wärmebehandelten Halbzeugen. Anhand einer numerischen Verzugssimulation gelang es im Projekt VoKoEs erstmals, den eigenspannungsbedingten Bauteilverzug für beliebige Zeitpunkte entlang der gesamten Fräsprozesskette zu simulieren. Die Simulation programmierten die Forscherinnen und Forscher des Fraunhofer IPT anschließend gemeinsam mit dem Institut für Strukturmechanik und Leichtbau (SLA) der RWTH Aachen University auf Basis der Finite Cell Method (FCM).
Erfolgreiche Integration der Simulation in CAM-System
Das Forscherteam integrierte gemeinsam mit dem Partner Module Works GmbH die Simulationssoftware erfolgreich in ein CAM-System zur Werkzeugbahnplanung. Auf der Basis der Verzugs-Vorhersagen testete das Team verschiedene Kompensationsmethoden, etwa die Variation der Bearbeitungsreihenfolge oder der Position des Soll-Bauteils innerhalb des Rohlings. Die Ergebnisse der Kompensationsmaßnahmen werden direkt in dem CAM-System visualisiert. Die Integration in das CAM-System hat den Vorteil, dass keine zusätzliche Software erforderlich ist. Ein weiterer Vorteil des Verfahrens ist, dass es sich grundsätzlich auf alle Werkstückgeometrien sowie subtraktiven Fertigungsverfahren anwenden lässt.
Adaptives, hydraulisches Spannsystem zur verzugsreduzierten Fräsbearbeitung
Zusätzlich zu den digitalen Lösungen zur Vorhersage und Reduzierung der Bauteilverzüge entwickelte der Projektpartner Innoclamp GmbH aus Aachen ein adaptives, hydraulisches Spannsystem für die Fräsbearbeitung von Luftfahrtstrukturbauteilen. Mit dem neuen Spannsystem können Eigenspannungen der eingespannten Werkstücke während der Bearbeitung kontrolliert freigesetzt werden; die spannungsfreien Werkstücke werden dann weiterbearbeitet. So lassen sich die gewünschten Geometrien herstellen, ohne dass sich das Werkstück beim Ausspannen nochmals verzieht. Der Bauteilverzug zwischen den Bearbeitungsschritten wird also zugelassen, ohne dass die Referenzen des Bauteils verloren gehen und das Bauteil erneut eingemessen werden muss. Die entwickelten Lösungen wurden in der letzten Projektphase am Beispiel eines Luftfahrtstrukturbauteil aus der Titanlegierung Ti-6AI-4V sowohl am Fraunhofer IPT als auch beim Projektpartner BoTech GmbH erfolgreich demonstriert.
Ausblick
Das Forscherteam plant, die Simulationssoftware in Folgeprojekten um zusätzliche physikalische Kenngrößen, etwa die Werkstück- und Werkzeugabdrängung, zu erweitern. Zudem könnte sich die Methodik künftig auch auf additive Fertigungsverfahren anwenden lassen, denn bei der additiven Fertigung treten ebenfalls häufig Bauteilverzüge auf, für die angepasste Kompensationsstrategien entwickelt werden müssen. Eine Weiterentwickung des adaptiven Spannsystems ist ebenfalls bereits in der Planung.
Förderung: Das Forschungsprojekt „VoKoES – Vorhersage und Kompensation von Bauteilverzügen durch Eigenspannungen während der 5-Achs-Fräsbearbeitung“ wurde durch Mittel des Europäischen Fonds für regionale Entwicklung (EFRE) 2014–2020 gefördert. Projektpartner sind: Fraunhofer-Institut für Produktionstechnologie IPT, Aachen (Koordination); Access e. V., Aachen; RWTH Aachen, Institut für Strukturmechanik und Leichtbau (SLA); Innoclamp GmbH, Aachen; Module Works GmbH, Aachen; BoTech GmbH, Mönchengladbach.
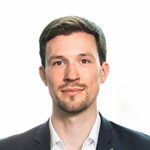
Philipp Ganser, M. Sc.
Foto: projektelf
Fraunhofer-Institut für Produktionstechnologie IPT
Abteilungsleiter Hochleistungszerspanung
Steinbachstr. 17, 52074 Aachen
Tel. +49 241 8904-425
philipp.ganser@ipt.fraunhofer.de
www.ipt.fraunhofer.de