Ressourceneffiziente Fabrikplanung im Mittelstand
Eine innovative und flexible Fabrikplanung ist ein Enabler für die ressourceneffiziente Produktion von Gütern. In einem gemeinsamen Projekt der Bruse GmbH & Co. KG mit dem Fraunhofer-Institut für Materialfluss und Logistik (IML) wurde ein umfassendes Materialfluss- und Standortkonzept entwickelt. Mit der Bündelung weiterer Maßnahmen für die Produktionsversorgung und Auftragssteuerung können erhebliche Ressourcen- sowie Kosteneinsparungen in Wertschöpfung und Logistik erreicht werden.
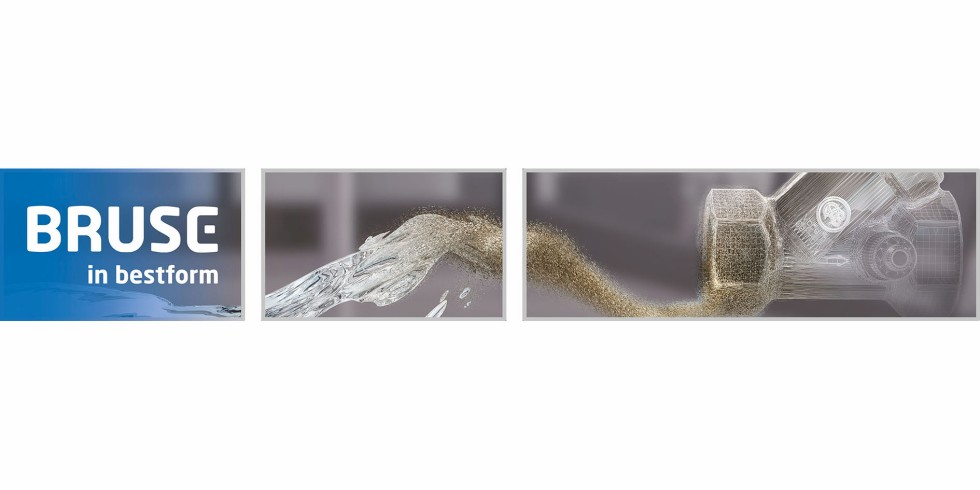
Bild 1. Bruse in Bestform.
Foto: Bruse GmbH & Co. KG
A paradigm shift for an innovative production site – Resource-efficient factory planning in SMEs
Abstract: Innovative and flexible factory planning is an enabler for the resource-efficient production of goods. In a cooperation project between Bruse GmbH & Co. KG and the Fraunhofer Institute for Material Flow and Logistics (IML), a holistic material flow and factory planning concept was developed. By bundling further measures for production supply and order control, considerable resource as well as cost savings in value creation and logistics can be achieved.
1 Einleitung
Die Bruse GmbH & Co. KG (im Folgenden Bruse) ist ein mittelständisches Unternehmen und einer der führenden Hersteller von Pressteilen aus Messing und Aluminium (Bild 1). Am Standort Attendorn produziert Bruse Armaturen mit einer hohen Wertschöpfungstiefe beginnend beim Warmpressen über die spanende Bearbeitung, Oberflächenveredlung bis hin zur kundenauftragsbezogenen Endmontage.
Der Standort Attendorn ist ein gewachsener Standort, an dem die Produktion über ein Hauptwerk und zwei angrenzende Werke verteilt ist. Durch die gewachsenen Strukturen sowie die verteilten Funktionsbereiche ist die Flächennutzung stark fragmentiert und eine Vielzahl redundanter Materialflusstechnik vorhanden. Zusätzlich sind die Funktionsbereiche nicht flussorientiert angeordnet, wodurch kreuzende Materialflüsse entstehen. Derzeit führt eine Vielzahl von möglichen Lagerorten zu einer Mehrfacheinlagerung der Produkte und zu hohen logistischen Aufwänden.
Bruse steht seit jeher für die Fertigung qualitativ hochwertiger Bauteile und verfügt über einen modernen, dem neusten Stand der Technik entsprechenden Maschinenpark. Mit diesem Fertigungsfokus können die beiden Funktionsbereiche Endmontage und Logistik nicht vollumfänglich mithalten. Der Anspruch von Bruse ist es, mit einem systemischen Ansatz für den gesamten Standort die Prozesse in der Auftragsabwicklung von der Fertigung der Bauteile, Lagerung, Logistik, über die Endmontage bis hin zum Fulfillment effizient und zukunftsfähig zu gestalten. Ein Schwerpunkt liegt dabei auf den Montagearbeitsplätzen; diese müssen zukünftig so ausgestattet sein, dass sie ergonomisch, vernetzt und flexibel sind. Die Fertigung der Produkte erfolgt heute nach dem Push-Prinzip. Diese Art der Fertigungssteuerung in Zeiten volatiler, dynamischer und unsicherer Märkte und Lieferketten entspricht nicht dem Puls der Zeit. Das entwickelte Konzept beinhaltet daher auch eine Pull-Steuerung, für die in der Fabrik- und Standortplanung entsprechende Flächen und Prozesse definiert und geplant werden müssen.
2 Maßnahmen
Bruse möchte den gegebenen Herausforderungen begegnen und das Gesamtkonzept auf ein neues, modernes Level heben. „Mit dem neuen Konzept für unseren Standort in Attendorn wollen wir einen großen Innovationssprung machen und unsere Produktion in Zukunft deutlich flexibler, effizienter und schneller machen.“, so der Bruse Geschäftsführer und Inhaber Christian Bruse.
2.1 Umstellung der Produktionssteuerung auf das Pull-Prinzip
Die Umstellung der Produktionssteuerung auf das Pull-Prinzip stellt für Bruse einen tiefgreifenden Paradigmenwechsel dar. Ging es früher um die Maximierung der Kapazitätsauslastung, steht heute der Kundenbedarf und die kurzfristige Reaktion darauf im Fokus. Bruse strebt eine verbrauchsgesteuerte Produktionssteuerung und die Einführung eines Kundenentkopplungspunktes nach der mechanischen Fertigung an. Bestandsgeführte Halbfertigware soll nach dem Verbrauchsprinzip aufgefüllt werden und die Produktion der Fertigware nach Bedarf kurzfristig mit entsprechend kurzen Durchlaufzeiten erfolgen. Dadurch können Verschwendung durch Überproduktion sowie Verschrottung von nicht benötigter Ware massiv reduziert werden. Davon verspricht sich auch Ralf Müller, kaufmännischer Leiter bei Bruse, einen positiven Effekt: „Mit diesem Ansatz wollen wir den Materialeinsatz möglichst effektiv steuern, um nicht nur die Kundenzufriedenheit zu erhöhen, sondern auch einen Beitrag zur Ressourceneffizienz zu leisten.“ Zur Umsetzung dieses Prinzips sind im Gesamtkonzept weitere Maßnahmen wie zum Beispiel die Einführung und Dimensionierung eines Behälterkonzepts oder ein Soll-Prozess für die Materialbereitstellung zu integrieren.
2.2 Neustrukturierung des Standortes
Durch den Anbau einer neuen Halle an das Hauptwerk (Bild 2) können alle Funktionsbereiche räumlich nah beieinander und flussorientiert angeordnet werden. Die heute stark fragmentierte Endmontage wird in Segmente zentral verortet. Die Logistik mit dem Hochregallager und der vorgelagerten Vorzone bekommt durch die Umstellung der Fertigungssteuerung von Push auf Pull einen neuen Stellenwert und dient als zentraler Umschlagsplatz für die Produktionsver- und -entsorgung. Außerdem ist durch die neue Flächennutzung eine Reduzierung von Lärm-, Schmutz- und Wärmeemissionen möglich, da die sauberen Montagebereiche und die schmutzigen Bearbeitungsbereiche voneinander getrennt werden. Die logistische Entkopplung erfolgt dabei über entsprechende Zwischenlagerflächen. Durch das überarbeitete Standortlayout können 66 % der Transportwege für die Materialbereitstellung und der Fertigteile reduziert sowie zusätzliche logistische Aufwände durch den Wegfall mehrerer Lagerorte eliminiert werden.
2.3 Modernisierung der Montage
Die Montage wird in drei Segmente eingeteilt, welche sich in den durchgeführten Tätigkeiten unterscheiden. Außerdem ist die Montage rasterförmig layoutiert, wodurch diese zum Beispiel an veränderte Auftragslagen adaptiert werden kann. Für die Montage wurden außerdem drei neue Standardarbeitsplätze konzeptioniert, die sich durch Skalierbarkeit, Flexibilität, Ergonomie und systemische Vernetzung auszeichnen (Bild 3). Die Mitarbeitenden sollen an den Plätzen zusätzlich durch Werkerassistenzsysteme und Cobots unterstützt werden.
2.4 Entwicklung eines neuen Logistikkonzeptes
Zur weiteren Reduktion des Transportaufkommens sowie der logistischen Aufwände soll ein Routenzug die Ver- und Entsorgung der Montageplätze übernehmen. Der Routenzug beliefert mehrere Arbeitsplätze mit einem gebündelten Warenstrom in definierten Intervallen. Außerdem ist eine Umstellung auf Kleinladungsträger innerhalb der Montage geplant, da diese für ein effizientes Handling und eine effiziente Bereitstellung der Teile am Arbeitsplatz maßgeblich sind.
3 Umsetzung und Ausblick
Bruse hat bereits damit begonnen, das mit dem Fraunhofer IML erarbeitete Konzept umzusetzen. Zunächst steht dabei die Neustrukturierung des Standortes im Vordergrund, welche mit dem Bau der neuen Halle gestartet wurde. Dabei orientiert sich Bruse an dem erarbeiteten Hallenlayout und hat mit der Verlegung des ersten Fertigungsbereichs in die neue Halle begonnen. Diese Verlagerung wird nun in den nächsten Wochen weiter fortgesetzt, bis der Bearbeitungsbereich komplett zusammengeführt ist.
Im zweiten Schritt werden die Montageanlagen erneuert und den aktuellen Erfordernissen im Bereich der Ergonomie, Skalierbarkeit und Flexibilität angepasst. Die in dem Projekt konzipierten Standardarbeitsplätze wurden in Gesprächen mit geeigneten Herstellern konkretisiert. Die Beschaffung erster Arbeitsplätze wurde angestoßen, um mit diesen Prototypen weitere Erfahrungen zu sammeln und ggf. Anpassungen vorzunehmen.
Parallel dazu hat Bruse mit der Einführung eines Behältermanagementsystems begonnen. Dazu wurden zunächst Tests mit verschiedenen Kleinladungsträgern vorgenommen, um die Eignung zu prüfen. Ziel ist eine Umverpackung der Produkte nach der mechanischen Bearbeitung und dem Reinigen der Bauteile. Die nachfolgenden Montage- und Verpackungstätigkeiten werden kundenauftragsbezogen vorgenommen und aus einer vorgelagerten Kommissionierzone versorgt.
Marie Luisa Strehl / Helena Piastowski / Ralf Müller
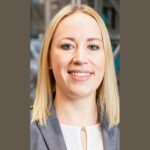
Luisa Marie Strehl, M. Sc.
Foto: Fraunhofer IML
Dipl.-Logistikerin Helena Piastowski
Fraunhofer-Institut für Materialfluss und Logistik
Joseph-von-Fraunhofer-Str. 2–4, 44227 Dortmund
Tel. +49 231 / 9743-373
luisa.marie.strehl@iml.fraunhofer.de
helena.piastowski@iml.fraunhofer.de
www.iml.fraunhofer.de
Ralf Müller
Bruse GmbH & Co. KG
Benzstr. 19, 57439 Attendorn
Tel. +49 2722 / 5509-127
r.mueller@bruse.de
www.bruse.de