Leichtbau: Datenvernetzung für additive Fertigung
Additive Fertigung (AM) bietet aufgrund großer Designfreiheiten ein enormes Leichtbaupotenzial. Vom Rohmaterial bis zum fertigen Bauteil durchlaufen Zwischenprodukte meist mehrere Wertschöpfungsstufen und Unternehmen. Wissensverluste zwischen den Wertschöpfungsstufen müssen verhindert werden, um durchgängig eine genaue Kenntnis des Werkstoffs, des Bauteils und des Fertigungsprozesses zu erhalten. So lassen sich Design und Produktion in wirtschaftlicher sowie ökologischer Hinsicht optimieren.
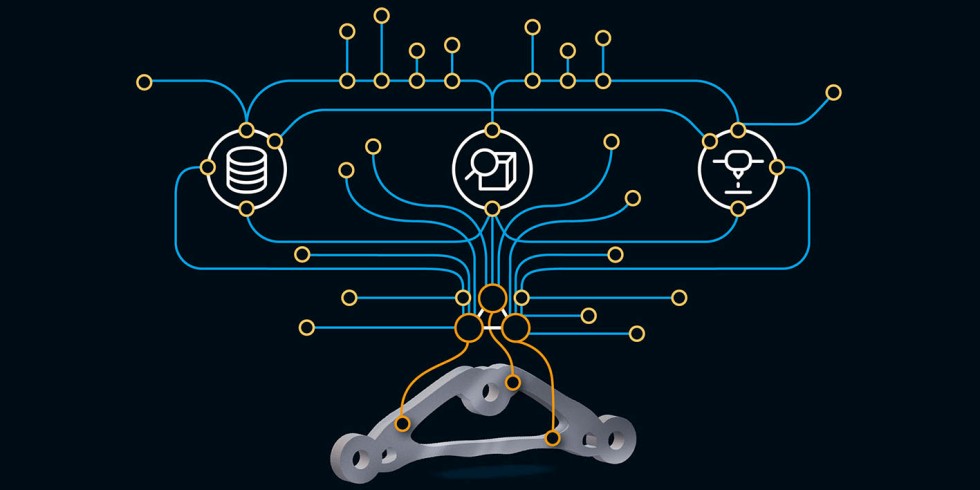
Bild 1. Verknüpfung von Daten- und Wissensinseln zu Bauteilanforderungen, Werkstoffeigenschaften und AM-Prozess für das Leichtbaudesign. Grafik: Fraunhofer EMI
Ausgabe 6-2022, S. 372
Digitization of the process chain for additively manufactured aluminum lightweight components – Data fabric for lightweight design with AM
Abstract: Additive manufacturing (AM) offers enormous lightweight potential due to great design freedom. From the raw material to the finished component, the intermediate products usually pass through several companies. For lightweight design, knowledge losses in the value chain must be prevented in order to obtain the most accurate possible knowledge of the material, the component and the manufacturing process. In this way, design and production can be further optimized in economic and ecological terms.
1 Zielsetzung und Anwendungsfall: Designoptimierung von AM-Leicht- baukomponenten
Ziel des vom Ministerium für Wirtschaft, Arbeit und Tourismus Baden-Württemberg geförderten Forschungsprojekts „AluTrace“ war es, die über Produktentwicklungs- und Produktherstellungszyklen entstehenden Daten- und Wissensinseln digital zu verknüpfen (Bild 1). Das Projektkonsortium, bestehend aus dem Fraunhofer-Institut für Kurzzeitdynamik, Ernst-Mach-Institut, EMI, Fraunhofer-Institut für Werkstoffmechanik IWM und dem fem Forschungsinstitut Edelmetalle + Metallchemie, entwarf zu diesem Zweck einen realistischen Anwendungsfall in Rücksprache mit Fachleuten aus Forschung und Industrie.
Der Anwendungsfall hat zum Ziel, die Geometrie eines für das Gießverfahren ausgelegten Bauteils aus der Aluminiumlegierung AlSi10Mg zu optimieren und bei gleichbleibender mechanischer Performance 20 % Gewichtseinsparung zu ermöglichen. Unter Nutzung der Möglichkeiten der additiven Fertigung (AM) soll ein neues Leichtbaudesign entwickelt werden.
Hierfür wurde im Projekt eine automatisierte Konstruktionssoftware mit einem neuen Algorithmus für eine prozessspezifische Topologieoptimierung (PSTO) entwickelt. Sie nutzt verteilt vorliegende Daten, interpretiert diese Datenbasis selbstständig und unterstützt damit das Konstruktionsbüro unabhängig von dessen Fähigkeiten bei der Auslegung eines Leichtbauteils. Die Auswahl des bestgeeigneten Laser-Powder-Bed-Fusion(LPBF)-Fertigungssystems, der Bauteilorientierung im Bauraum und der passenden Bauteilnachbehandlung erfolgt ebenso automatisiert wie die Optimierung der Bauteilfunktion, die des Einsatzes von Stützstrukturen und die der Oberflächenqualität (Bild 2).
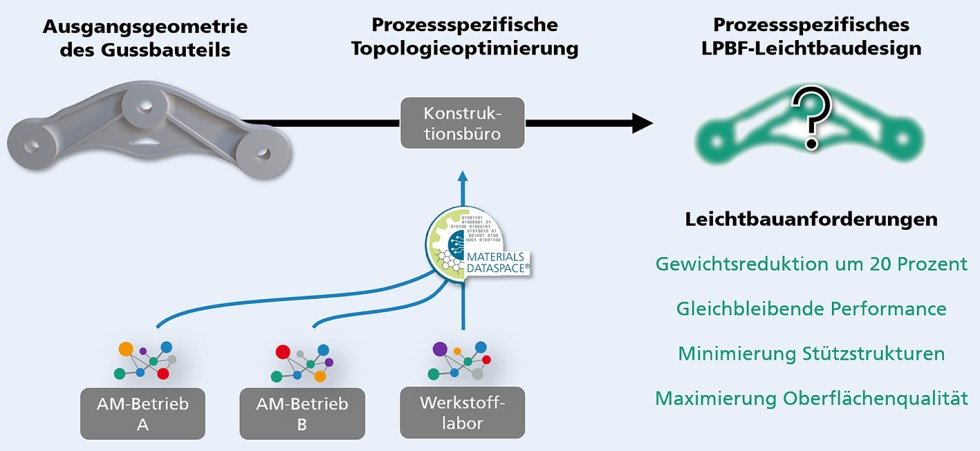
Bild 2. Ziel des AluTrace-Anwendungsfalls ist es, ein Konstruktionsbüro dazu zu befähigen, eine Gussbauteilgeometrie mittels prozessspezifischer Topologieoptimierung für den Leichtbau mit AM unter Nutzung der automatisierten PSTO-Konstruktionssoftware zu optimieren. Grafik: Fraunhofer EMI
Darüber hinaus wurden für die unternehmensübergreifende Datenvernetzung eine vertrauenswürdige und sichere IT-Infrastruktur sowie rückverfolgbare und interoperable Datenstrukturen nutzbar gemacht.
Folgende in unterschiedlichen Unternehmen verortete Beteiligte agieren im AluTrace Anwendungsfall:
- Konstruktionsbüro Führt die Designoptimierung der Ausgangsgeometrie und den Entwurf eines Leichtbauteils für LPBF unter Nutzung der neuen PSTO-Konstruktionssoftware durch. Ist offen gegenüber der Wahl eines spezifischen AM-Betriebs und macht die Entscheidung abhängig von der besten zu erreichenden Bauteilqualität.
- AM-Betrieb A Betreibt das LPBF-Fertigungssystem A und stellt AM-Prozessdaten für auf diesem System additiv gefertigte Bauteile inklusive der durchgeführten Bauteilnachbehandlungen bereit.
- AM-Betrieb B Betreibt ein weiteres LPBF-Fertigungssystem B und stellt AM-Prozessdaten für auf diesem System additiv gefertigte Bauteile bereit.
- Werkstofflabor Führt Bauteilnachbehandlungen durch, prüft AM-Bauteile und untersucht Werkstoffe experimentell. Stellt erhobene Werkstoffdaten bereit.
2 Erheben von Werkstoff- und Prozessdaten aus der LPBF-Fertigung
Im Projekt AluTrace wurden existierende Datensätze aus vergangenen Vorhaben der Konsortialpartner herangezogen und gezielt um weitere AM-Prozess- und Werkstoffdaten aus der LPBF-Fertigung von AlSi10Mg-Probekörpern ergänzt. Für die Umsetzung des Anwendungsfalls fungieren die Konsortialpartner Fraunhofer EMI, Fraunhofer IWM und fem als Beteiligte. Folgende Daten liegen dezentral bei den Beteiligten vor oder wurden im Projekt erhoben.
2.1 Ausgangsgeometrie des Konstruktionsbüros
Dem Konstruktionsbüro, hier Fraunhofer EMI, liegt die Ausgangsgeometrie des Gussbauteils [1] vor (Bild 2 links), die für AlSi10Mg auf Zugbelastung ausgelegt wurde.
2.2 LPBF-Prozessdaten des AM-Betriebs A
Die Prozessdaten des AM-Betriebs A, hier ebenso Fraunhofer EMI, wurden für die LPBF-Fertigung von Probekörpern (Bild 3) an einem „EOS-M-400“-System erhoben [2].
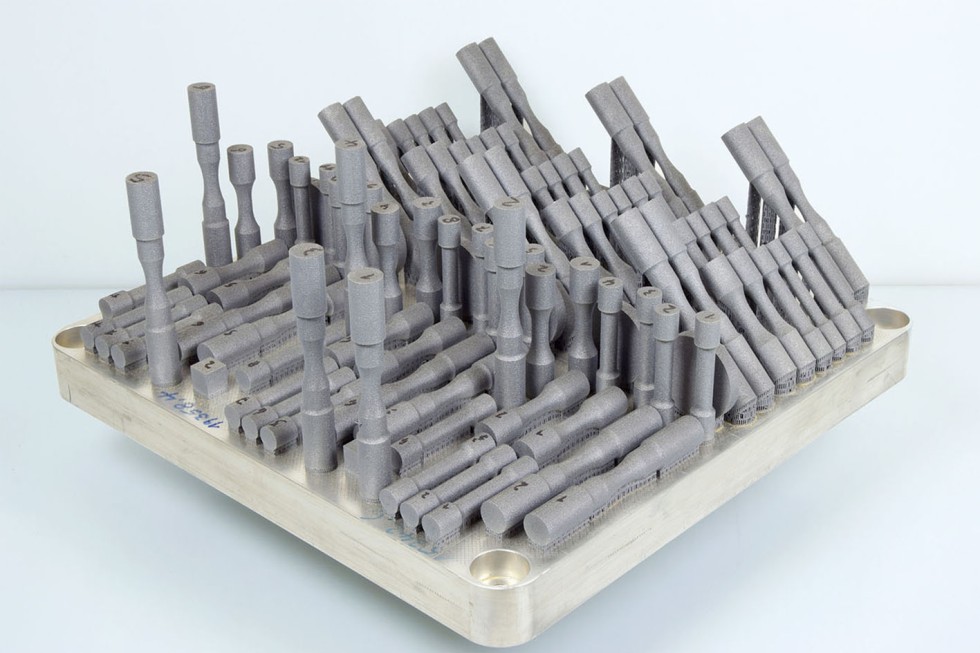
Bild 3. In einem EOS-M-400-System des AM-Betriebs A gefertigte Probekörper auf Bauplattform. Variation der Bauteilorientierungen und -positionen im Fertigungsdurchlauf A1.
Foto: Fraunhofer EMI
Die erhobenen Prozessdaten enthalten strukturierte Informationen zu den Variationen im AM-Prozess beim AM-Betrieb A (Tabelle 1).
2.3 LPBF-Prozessdaten des AM-Betriebs B
Die Prozessdaten des AM-Betriebs B, hier fem, wurden im Projekt AluTrace bei der additiven Fertigung von Probekörpern auf einem Aconity-MINI-System gezielt erzeugt (Bild 4).
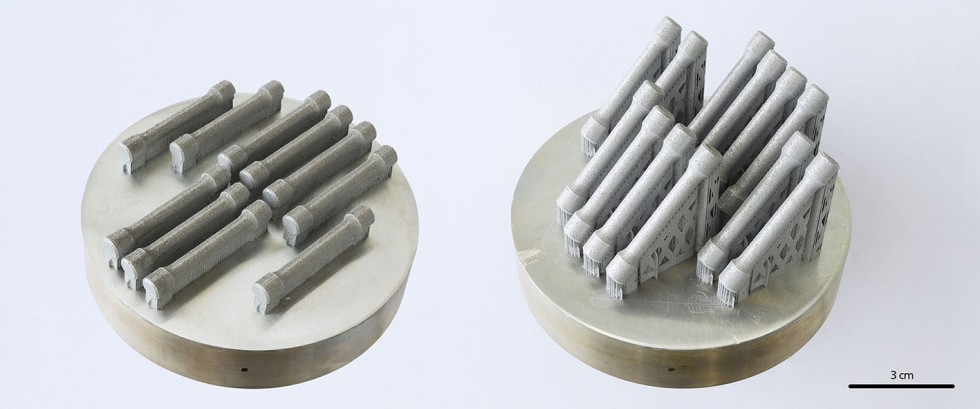
Bild 4. In einem Aconity-MINI-System des AM-Betriebs B gefertigte Probekörper auf Bauplattform. Variation der Probekörperorientierung 0° (links B4) und 45° (rechts B5).
Foto: fem
Die erhobenen Prozessdaten des AM-Betriebs B enthalten ebenso strukturierte Informationen zu den Variationen im AM-Prozess (Tabelle 2).
2.4 Werkstoffdaten des Werkstofflabors
Dem Werkstofflabor liegen Probekörper aus den Anlagen der AM-Betriebe A und B vor. Diese Probekörper wurden durch das Werkstofflabor teilweise mittels Wärme- oder Oberflächennachbehandlungen verarbeitet, um deren Einfluss auf die mechanische Leistung beurteilen zu können (Tabelle 3). Die dabei entstandenen Untersuchungsergebnisse stellen die Werkstoffdaten des Werkstofflabors dar.
Es ist festzustellen, dass verschiedene AM-Prozessparameter und Nachbehandlungsschritte bei unterschiedlichen Beteiligten variiert beziehungsweise durchgeführt wurden. Zugehörige Daten wurden projektübergreifend erhoben, sind heterogen und liegen dezentral bei den Beteiligten vor. Weiterhin bieten die unterschiedlichen Systeme der AM-Betriebe verschiedene Vor- und Nachteile hinsichtlich fertigungsbedingter Toleranzen oder Art und Qualität der bereitgestellten Daten. Es ist von einem starken Einfluss der Prozessvariationen auf die werkstoffmechanischen Eigenschaften auszugehen, deshalb müssen die Untersuchungsergebnisse einzelner Probekörper (W1 bis W3) unternehmensübergreifend zu ihren Fertigungsbedingungen (A1 bis A3; B1 bis B6) zugeordnet und gemeinsam ausgewertet werden. Um die Konstruktionssoftware zu dieser automatisierten Auswertung zu befähigen, wurde eine Datenraumarchitektur entwickelt, die sich durch ihren hohen Anspruch an Datensouveränität sowie Interoperabilität auszeichnet.
3 Unternehmensübergreifendes Teilen und Vernetzen von Werkstoff- und Prozessdaten
Werden unterschiedliche Daten automatisiert von den Beteiligten geteilt, ist die Einhaltung der FAIR-Datengrundsätze (findable, accessible, interoperable, reusable) [3] von größter Bedeutung. Um diesem Bedarf gerecht zu werden, wurde vom Fraunhofer EMI eine Datenraumarchitektur auf der Grundlage des International-Data-Spaces(IDS)-Referenzarchitekturmodells [4] entworfen und implementiert (Bild 5). Auf diese Weise schaffen die Autoren die allererste Instanz des „Materials Data Space“ (MDS) [5].
![Bild 5. Unternehmensübergreifende Datenraumarchitektur, basierend auf den IDS-Standards [4]. Der Business Layer zeigt die Beteiligten, ihre IDS-Rollen und IDS-Interaktionen. Die technische Implementierung stellt den Materials Data Space [5] dar. Grafik: Fraunhofer EMI](https://www.ingenieur.de/wp-content/uploads/2022/07/W_Fraunhofer-AluTrace_Bild-5.jpg)
Bild 5. Unternehmensübergreifende Datenraumarchitektur, basierend auf den IDS-Standards [4]. Der Business Layer zeigt die Beteiligten, ihre IDS-Rollen und IDS-Interaktionen. Die technische Implementierung stellt den Materials Data Space [5] dar. Grafik: Fraunhofer EMI
- die Auffindbarkeit (F – findable) der Daten und deren Eigentümer durch die Nutzung eines virtuellen Marktplatzes,
- den sicheren und automatisierten Zugriff (A – accessible) auf die Daten aus den IT-Infrastrukturen der Institutionen,
- die Interoperabilität (I – interoperable) beim Datenaustausch unter voller Gewährleistung der Datensouveränität durch die Nutzung des Dataspace Connectors [6] sowie
- die Wiederverwendbarkeit (R – reusable) der Daten aufgrund maschinen- und menschverständlicher Metadaten in Form von Wissensgraphen.
- Die Wissensgraphen beschreiben die gesamte Prozesskette von der additiven Fertigung bis hin zur mechanischen Prüfung und betten die dabei anfallenden Daten durch ein ontologiebasiertes Prozessmodell in ihren Kontext ein (Bild 6). Diese rückverfolgbaren und interoperablen Prozessmetadaten werden von den Datenanbietern bereitgestellt und erlauben die automatisierte Vernetzung ihrer Daten auf Basis von Domänenkonzepten, was dem Konstruktionsbüro als Datenkonsument die intelligente Datenanalyse und den automatisierten Entwurf eines LPBF-Leichtbaudesigns mittels PSTO-Konstruktionssoftware gestattet.
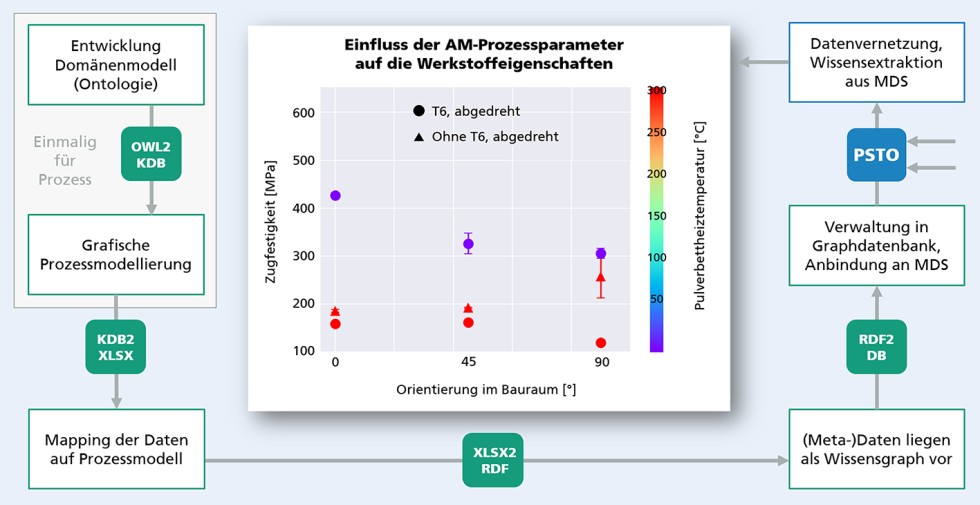
Bild 6. Arbeitsablauf zur Generierung semantischer Prozessmetadaten durch den Datenanbieter (grün) mithilfe der Werkzeugkette des Fraunhofer IWM. Die Abfrage der Daten mehrerer Datenanbieter geschieht durch den Datenkonsumenten mittels PSTO-Konstruktionssoftware (blau). Grafik: Fraunhofer IWM, Fraunhofer EMI
4 Ausschöpfen des Leichtbaupotenzials durch prozessspezifische Topologie – optimierung
Es wurde ein neuer Algorithmus für eine prozessspezifische Topologieoptimierung entwickelt, der die effiziente Ausnutzung der unternehmensübergreifend vernetzten Prozess- und Werkstoffdaten ermöglicht. Dieser neue Algorithmus läuft innerhalb einer Konstruktionssoftware, die sich aktuell noch in Entwicklung befindet. Hierdurch können real gemessene Werkstoffkennwerte, die sich auf die spezifischen Fertigungsanlagen und Prozessparameter beziehen, automatisiert durch die Software für das Design genutzt werden. Dadurch wird im Vergleich zur Verwendung unspezifischer Quellen, zum Beispiel aus Materialdatenbanken, die Unsicherheit der Materialeigenschaften stark reduziert und dadurch zusätzliches Leichtbaupotenzial geschaffen.
Der Algorithmus für die PSTO-Konstruktionssoftware ist vollständig automatisiert und unabhängig von den Fähigkeiten des Konstruktionsbüros. Basierend auf einer Gewichtung mehrerer Zielkriterien für Bauteilfunktion und Fertigungsprozess wird innerhalb des zur Verfügung stehenden Volumens (Designraum) ein optimiertes Design inklusive der Bauteilorientierung im Bauraum generiert. Hierzu fragt die Software die Prozessparameter der beiden AM-Betriebe, die zugehörigen Werkstoffdaten des Werkstofflabors sowie die Bauteilnachbehandlungsinformationen aus dem Datenraum ab. Damit wird in Abhängigkeit der Kennwerte eine adaptierte Modellbildung der Materialeigenschaften vorgenommen. Elastische als auch Plastizitätseigenschaften sowie Streugrößen und Datenqualität, beispielsweise die Anzahl der Messungen, werden durch die Software in der Modellierung mit berücksichtigt.
Die PSTO-Konstruktionssoftware verwendet ein multimodales Verfahren, um mehrere Modelle der Strukturmechanik und der Vorhersage von AM-Prozessgrößen wie Stützstrukturen und Oberflächeneigenschaften in einer multikriteriellen Formulierung zu berücksichtigen. Auf diese Weise wird es möglich, nicht nur die mechanische Bauteilfunktion, sondern auch AM-Prozessgrößen in Abhängigkeit der Bauteilorientierung automatisiert zu optimieren. Die prozessspezifischen Messdaten ermöglichen dem Algorithmus, die mechanische Funktion des Leichtbauteils und damit die elastische Steifigkeit sowie die Sicherheit der Struktur bei Überbelastung zu berücksichtigen.
Im vorliegenden Anwendungsfall wird das Konstruktionsbüro durch die Nutzung der PSTO-Konstruktionssoftware mit Anbindung an den MDS dazu befähigt, automatisiert ein optimiertes Leichtbaudesign inklusive der dortigen Bauteilorientierung im Bauraum sowie der Empfehlung für das System eines spezifischen AM-Betriebs und für die Bauteilnachbehandlung zu finden (Bild 7).
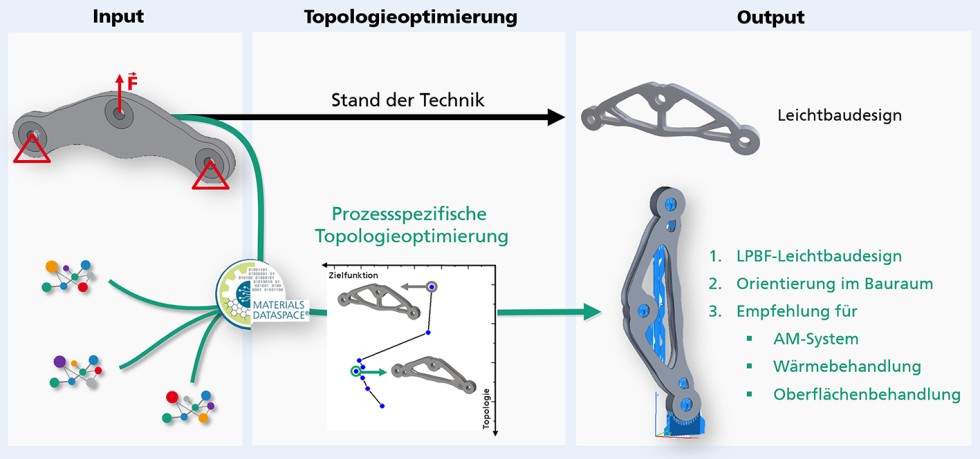
Bild 7. Ablauf der automatisierten prozessspezifischen Topologieoptimierung mit Darstellung von In- und Output sowie Vergleich zum Stand der Technik. Grafik: Fraunhofer EMI, fem
Mittels der PSTO-Konstruktionssoftware wurde ein optimiertes Leichtbauteil entworfen, das im vorliegenden Anwendungsfall im AM-Betrieb B, in einer Orientierung von 96 Grad gefertigt und ohne Oberflächennachbehandlung in den T6-Zustand überführt werden sollte. Dieses prozessspezifische LPBF-Leichtbaudesign zeigt gegenüber dem Gussbauteil ein um 20 % reduziertes Gewicht. Außerdem weist das LPBF-Leichtbaudesign verbesserte Eigenschaften gegenüber einer Bauteilgeometrie auf, die nach dem bisherigen Stand der Technik der Topologieoptimierung ausgelegt wurde:
- Höhere Sicherheit bei Überbelastung um +15 %
- Stark verbesserte AM-Prozessgrößen:
- -66 % Stützstrukturen,
- +16 % Oberflächenqualität
5 Zusammenfassung und Ausblick
Mit AluTrace konnte an einem realistischen Anwendungsfall demonstriert werden, dass die Anbindung eines unternehmensübergreifenden Datenraums an eine Konstruktionssoftware für prozessspezifische Topologieoptimierung zur weiteren Ausschöpfung des AM-Leichtbaupotenzials beiträgt. Im Rahmen des Projekts wurden weitere Prozess- und Werkstoffdaten erhoben, zum Beispiel die Emissivität des AM-Schmelzbades, die Porosität der Bauteile oder metallografische Bruchflächenanalysen. Mit dem Materials Data Space als skalierbarem Datenraum wird es zukünftig weiteren Datenanbietern und -konsumenten möglich sein, das Leichtbaupotenzial in vielen Anwendungen zu maximieren.
Das Projektkonsortium bedankt sich beim Ministerium für Wirtschaft, Arbeit und Tourismus Baden-Württemberg für die finanzielle Förderung. Ein besonderer Dank gilt außerdem dem projektbegleitenden Industriebeirat für den regen Austausch und insbesondere für die aktive Beteiligung. Weiterhin ist der LeichtbauBW GmbH zu danken, die wesentlich zur Zusammenstellung des Projektkonsortiums und des Projektbeirats beigetragen hat.
Literatur
- Internet: https://www.materialdigital-bw.de/. Zugriff am 24.2.2022
- Pfaff, A.; Jäcklein, M.; Hoschke, K. et al.: Designed Materials by Additive Manufacturing – Impact of Exposure Strategies and Parameters on Material Characteristics of AlSi10Mg Processed by Laser Beam Melting. Metals 8 (2018) 7, S. 491
- Wilkinson, M. D.; Dumontier, M.; Aalbersberg, I. J. et al.: The FAIR Guiding Principles for scientific data management and stewardship. Scientific data 3 (2016)
- Otto, B.; Steinbuß, S.; Teuscher, A. et al.: Reference Architecture Model. Version 3.0, International Data Spaces Association, 2019
- Internet: https://www.fraunhofer-materials-data-space.de. Zugriff am 22.2.2022
- Internet: https://github.com/International-Data-Spaces-Association/DataspaceConnector. Zugriff am 22.2.2022
Martin Huschka, M. Sc.
Dipl.-Ing. (TUM) Klaus Hoschke
Dr.-Ing. Michael Dlugosch
Sankalp Patil, M. Sc.
Fraunhofer-Institut für Kurzzeitdynamik
Ernst-Mach-Institut EMI
Ernst-Zermelo-Str. 4, 79104 Freiburg
Tel. +49 761 / 2714-458
martin.huschka@emi.fraunhofer.de
www.emi.fraunhofer.de
Dr.-Ing. Christoph Schweizer Dr.-Ing. Valerie Friedmann Dr. Elena Garcia Trelles Dr.-Ing. Johannes Preußner
Fraunhofer-Institut für Werkstoffmechanik IWM
Wöhlerstr. 11, 79108 Freiburg
Tel. +49 761 / 5142-382
christoph.schweizer@iwm.fraunhofer.de
www.iwm.fraunhofer.de
Dr. Ulrich Klotz
Dario Tiberto, B. Sc.
fem Forschungsinstitut Edelmetalle + Metallchemie
Katharinenstr. 17, 73525 Schwäbisch Gmünd
Tel. +49 7171 / 1006-700
klotz@fem-online.de
www.fem-online.de