Für mehr Leistung und Effizienz von E-Motoren
Die zunehmende Elektrifizierung der Mobilität sorgt für einen steigenden Bedarf an elektrischen Maschinen. Künftig führt and der ressourcenschonenden Herstellung, aber auch am effizienteren Betrieb elektrischer Antriebe kein Weg mehr vorbei. Eine wichtige Stellgröße ist dabei die Vergrößerung des sogenannten Nutfüllfaktors. Bei einem erhöhten Kupferanteil in der Nut können Maschinen kleiner dimensioniert oder bei gleicher Baugröße leistungsfähiger und effizienter betrieben werden. Zur Herstellung der Wicklungen mit hohen Nutfüllfaktoren sind mehrere Herstellverfahren bekannt, die jedoch allesamt mit verschiedenen Nachteilen wie geringe Produktivität, hohem Energie- und Ressourcenbedarf verbunden sind sowie dem Konstrukteur Einschränkungen in der geometrischen Gestaltung der Einzelwindungen auferlegen. In diesem Beitrag wird eine mögliche, am Fraunhofer-Institut für Werkzeugmaschinen und Umformtechnik IWU entwickelte Prozesskette zur umformtechnischen Herstellung von Spulen mit trapezförmiger Querschnittsgeometrie im Nutbereich beschrieben.
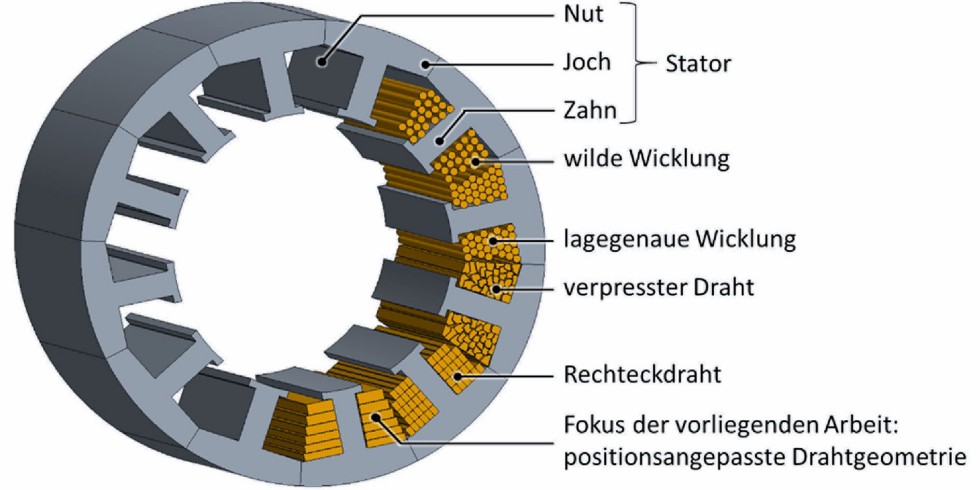
Bild 1. Stator im Schnitt mit ausgewählten Spulenquerschnittsgeometrien. Grafik: Fraunhofer IWU
Process chain for the forming of concentrated windings with trapezoidal cross-section geometry
Abstract: Due to increasing electrification in mobility and the resulting rise in demand for electrical machines, issues relating to resource-saving production and more efficient operation are becoming ever more central. An important parameter here is the increase in the so-called slot fill factor. On the one hand, by increasing the copper content in the slot, machines can be made smaller or operated more powerfully and efficiently with the same size. Various production methods can be used to manufacture windings with high slot fill factors, but they have various disadvantages such as low productivity, high energy and resource requirements, and restrictions in the geometric design freedom of the individual windings. This article describes a possible process chain developed at Fraunhofer IWU for the forming-based production of coils with trapezoidal cross-sectional geometry in the slot area.
1 Stand der Technik: Grenzen…
Bei klassisch hergestellten Elektrospulen aus Runddraht, beispielsweise durch Linear-, Flyer-, Nadel und Ringkernwickeln [1], liegt das Hauptaugenmerk zur Anpassung des Wickelprozesses auf der Optimierung der Drahtlagenanordnung und damit auf der Erhöhung des Kupferanteils in der Nut, beschrieben durch den sogenannten Nutfüllfaktor. Dieser Kennwert stellt vereinfacht das Verhältnis zwischen der tatsächlichen Füllung einer Nut mit Wickelgut und deren verfügbaren Querschnitt dar. Je höher die Nutfüllung, desto höher der maximal mögliche Strom und damit der resultierende magnetische Fluss zur Erzeugung des Drehfeldes in der Maschine. Üblicherweise werden Nuten durch automatisierte Wickelprozesse mit Runddrähten ohne kontrollierte Drahtlagenanordnung (auch bekannt unter dem Begriff „wilde“ Wicklung) oder lagegenau (schraubenförmig oder orthozyklisch) gefüllt (siehe Bild 1). Hier sind unterschiedliche Bewicklungsarten im Schnitt ohne Wicklungsköpfe der Spulen dargestellt. Mit den Runddrahtbewicklungsverfahren sind jedoch nur Füllfaktoren von maximal 50% bis 70 % realisierbar [2, 3]. Um eine grundsätzlich höhere Nutfüllung zu erreichen, ist es notwendig, die Querschnittsform des Wickelgutes an die Nutgeometrie anzupassen. Viele der etablierten Fertigungsverfahren eignen sich aufgrund ihrer Energieintensität beziehungsweise Komplexität nur bedingt für die Drahtquerschnittsanpassung bei mittleren bis großen Stückzahlen und bleiben Nischenanwendungen vorbehalten [4]. Weiterhin weist ein Großteil der Verfahren nicht die notwendige Flexibilität auf, um auf einen geänderten Bauraum in elektrischen Maschinen einfach angepasst werden zu können. Allerdings können verschiedene umformtechnische Herstellungsverfahren wie beispielsweise das mechanische Verdichten der Windungen in der Nut in Betracht gezogen werden [5]. In Bild 1 sind die ausgewählten Leitergeometrien für Wicklungen im Bereich der Nut aus verpresstem Runddraht und Rechteckdraht an einem im Schnitt skizzierten Stator ohne Rotor verdeutlicht. Bei der Umformung des Leiters besteht die Gefahr der Gratbildung, der Beschädigung der Isolation und der mangelhaften Formgenauigkeit der Windungen. Diese Nachteile zu vermeiden ist Hauptmotivation für die vorliegende Prozesskette. Vor dem Hintergrund der Potenziale der Umformtechnik war es Ziel der Untersuchungen, ein kostengünstiges, produktives und flexibles umformtechnisches Fertigungsverfahren für kompakte Zahnspulen hoher Leistungsdichte zu entwickeln. Mit diesem Verfahren ist es möglich, den Nutfüllfaktor einer Wicklung zu vergrößern und das Potenzial zu nutzen, kostengünstigere stromführende Werkstoffe, wie beispielsweise Aluminium, einzusetzen. Die dazu erforderliche positionsangepasste Geometrie der Windungen ist schematisch in Bild 1 erkennbar und Fokus dieses Beitrages.
2 Fertigungsschritte
Meistens wird bei Runddrahtwicklungen eine trapezförmige Querschnittsgeometrie der Nut gewählt [6]. Bei der Gestaltung mit parallelflankigen Nuten können für einen hohen Nutfüllfaktor zwar Spulen mit rechteckigen Einzelwindungen zum Einsatz kommen. Allerdings führt dieses Nutdesign zur Verkleinerung der Querschnittsfläche des Zahns sowie zur inhomogenen Magnetfeldausbildung, was zu dessen Sättigungsmagnetisierung führt. Als Folge kann durch den Zahn nur ein begrenzt starkes Magnetfeld übertragen oder verstärkt werden. Damit wird die Effizienz der Maschine verringert [7]. Mit dem Ziel, eine Spule trapezförmiger Querschnittsform herzustellen, welche geometrisch an ihre Lage in der Nut angepasste Windungen besitzt (unter der Voraussetzung gleicher Querschnittsflächengrößen der Einzelwindungen), wurden im Rahmen der Untersuchungen wesentliche Fertigungsschritte identifiziert. Für die Auslegung von elektrischen Maschinen wird lediglich die Nut im Schnitt betrachtet, der Wicklungskopf hat keinen Einfluss auf die magnetische Wirkung der Spule. Ausgehend von dieser Annahme wird die lokale Formgebung des Drahtes im Bereich der Nut oder die kontinuierliche Umformung des gesamten Halbzeuges im Folgenden Querschnittsbildung genannt. Sie wird mit dem Piktogramm Nr. 1 aus Bild 2, oben links veranschaulicht. Die gestrichelte Linie verdeutlicht dabei den Endzustand nach der Formgebung. Das Ergebnis ist eine Sequenz unterschiedlich gestalteter Bereiche, siehe gleiche Abbildung unten. Die Abschnitte zwischen den geometrisch angepassten Bereichen besitzen die initiale Halbzeuggeometrie, beispielsweise rund (Region des künftigen Wicklungskopfes). Beim Biegen einer angepassten Drahtgeometrie wäre sonst mit Abweichungen von der Sollform zu rechnen. Die Bereiche können einerseits durch individuelles Wicklungskopfdesign oder nachträgliche umformtechnische Bearbeitung angepasst werden. Für das Ziel anschließend einen Spulenkörper aus der Sequenz zu erzeugen, ist ein Biege- oder Wicklungsschritt notwendig. Dieser Prozessschritt wird mit dem Piktogramm Nr. 2 aus Bild 2 verdeutlicht. Die geometrisch angepassten Abschnitte A, B bis Y werden an der entsprechenden Stelle in der Nut mit dort vorherrschenden Platzverhältnissen positioniert, vgl. Bild 2, rechts. Unabhängig davon, ob der Halbzeugquerschnitt kontinuierlich oder im Nutbereich angepasst wird, ist zusätzlich zur Bildung des Wicklungskörpers ein abschließender Kalibrierschritt zur Finalisierung der Sollgeometrie notwendig. Das Kalibrieren wird durch das Piktogramm Nr. 3 aus Bild 2 symbolisiert. Auch hier wird der Endzustand durch die gestrichelte Linie verdeutlicht.
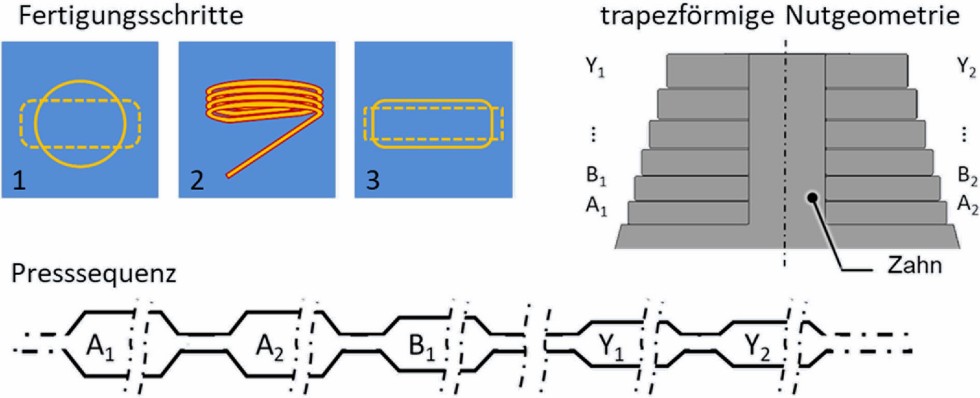
Bild 2. Links: Fertigungsschritte: 1 Sequenzbildung – 2 Wicklung – 3 Kalibrieren; unten: Sequenz mit jeweils unterschiedlichen Leiterabmessungen; rechts: Positionierung der Sequenzbereiche in der Nut. Grafik: Fraunhofer IWU
3 Umsetzung und Charakterisierung
Die Schritte sequenzielle Querschnittsbildung – Erzeugung eines Wicklungskörpers – Kalibrieren sind zunächst mithilfe von FE-Umformsimulationen hinsichtlich des Werkstoffflusses untersucht worden. Dabei sind für einzelne Prozessschritte Herausforderungen ermittelt, Verbesserungsvorschläge erörtert und Werkzeuge abgeleitet worden.
Für den Prozessschritt Querschnittsbildung wurde zunächst ein einfaches Presswerkzeug konzipiert, siehe Bild 3, links. Ober- und Unterwerkzeug werden in einem Gestell zueinander geführt und durch eine Presse mithilfe einstellbarer Aufschlagplatten auf eine bestimmte Presshöhe zusammengefahren. Bei Kontakt mit der Werkzeugoberfläche beginnt der Drahtwerkstoff zu fließen, bis die für die Windungsabmessung festgelegte Höhe und Breite des Leiters erreicht ist. An dieser Stelle wurde neben der Breitung ein ungewollter axialer Werkstofffluss festgestellt. Nach Untersuchungen mithilfe statistischer Versuchsplanung bei Modifikation von Reibwert, Öffnungswinkel und Radius der Werkzeugeinsätze konnte eine verbesserte Geometrie abgeleitet werden, siehe Bild 3, rechts. Mit dieser Anpassung war es möglich, die Längenausdehnung für den Werkstoff Aluminium auf rund ein Drittel des Anfangswertes zu mindern. Die jeweiligen Längenabweichungen flossen in die Bildung einer Fertigungsvorschrift ein. Ziel dabei war es, über gezielte Steuerung des Rollenvorschubes die axiale Längenausdehnung des Leiters in Abhängigkeit zu dessen gepresster Höhe zu kompensieren.

Bild 3. Links: Erstentwurf der Presswerkzeuggeometrie für die Simulation mit gepresster Probe, Seitenansicht; rechts: Modifikation zur Minderung der Presslängung. Grafik: Fraunhofer IWU
Das Ergebnis des sequenziellen Pressvorgangs, eine Presssequenz, wurde für den nachfolgenden Prozessschritt in eine modifizierte Standardrohrbiegemaschine transferiert. Dort wurde der Biegevorgang zur Erzeugung einer vollständigen Wicklung umgesetzt. Eine Herausforderung hierbei war die Implementierung der passenden Vorschubwege für die Realisierung der Biegevorgänge an den richtigen Positionen des initialen Runddrahtes. Außerdem mussten vereinzelt Änderungen an der Gestalt von Halte-, Biege- und Positionierwerkzeugen der Maschine vorgenommen werden, um den Draht mit unterschiedlichen Querschnittsgeometrien zuverlässig greifen und transportieren zu können. Das Ergebnis des Biegevorgangs ist in Bild 4 zu sehen.
![Bild 4. Spulenbiegen; links: im Biegeprozess befindliche Presssequenz; rechts: Zwischenstadium einer gebogenen Presssequenz [8]. Grafik: Fraunhofer IWU](https://www.ingenieur.de/wp-content/uploads/2023/11/W_Fraunhofer_Bach_-0004.jpg)
Bild 4. Spulenbiegen; links: im Biegeprozess befindliche Presssequenz; rechts: Zwischenstadium einer gebogenen Presssequenz [8]. Grafik: Fraunhofer IWU
Aufgrund der verbleibenden runden Geometrie des Drahtes im Bereich des Wicklungskopfes liegen die angepassten Pressbereiche, welche später in der Nut der elektrischen Maschine positioniert werden, nicht aneinander an. Dieser Umstand wäre nachteilig für den Füllgrad der Nut. Daher ist der abschließende Kalibrierschritt notwendig.
Das zum Pressen der Wicklungsköpfe angepasste Kalibrierwerkzeug ist kassettenartig aufgebaut. Wie in Bild 5 (links) dargestellt, besteht es aus einem Ober- und Unterwerkzeug sowie mehreren dazwischen positionierten Pressplatten. Die Anzahl der Pressplatten ist um eins geringer als die Anzahl der Windungen der zu kalibrierenden Spule. Im Fall der in dieser Arbeit gefertigten Demonstratorspule sind zehn Pressplatten eingesetzt. Sie sind übereinander angeordnet, werden durch vier Säulen zueinander geführt und durch Tellerfedern elastisch in Abstand zueinander gehalten. Der Abstand ist erforderlich, um dem anfänglichen Runddraht im Bereich der Wicklungsköpfe ausreichend Raum zu geben, wenn die Spule vor dem Pressen in das Werkzeug geschoben wird. Im Bild 5 ist mittig ein Werkzeugausschnitt mit bereits vollständig gepresster Spule aus Aluminium dargestellt. Das Pressen der beiden Wicklungsköpfe findet nacheinander statt. Es ist gut zu erkennen, dass über den aus dem Werkzeug hinausragenden Wicklungskopf der Spule jeweils der Windungswechsel realisiert wird. Der im Werkzeug befindliche Wicklungskopf erhält die finale Windungsform mit Höhenänderung von links nach rechts.
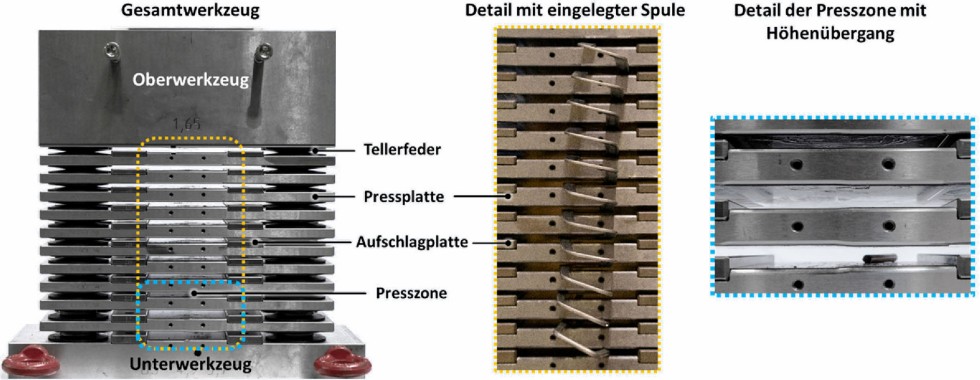
Bild 5. Finales Presswerkzeug für beide Wicklungsköpfe; links: Gesamtwerkzeug; Mitte: Detail mit eingelegter Aluminiumspule; rechts: Detail des Pressbereiches. Grafik: Frauinhofer IWU
Die fertig geformte Demonstratorspule aus Al 99,9 mit trapezförmigem Querschnitt nach der Entnahme aus dem Werkzeug ist in Bild 6, links dargestellt. Unten links ist die Ansicht auf den Wicklungskopf ohne Höhenübergang dargestellt. Mittig ist die Seitenansicht der Spule zu sehen. Rechts ist der zweite Wicklungskopf gezeigt. Der oben dargestellte Ausschnitt Detail A vom zweiten Wicklungskopf zeigt den realisierten Höhenübergang jeweils von der ersten auf die zweite und von der zweiten auf die dritte Windung.
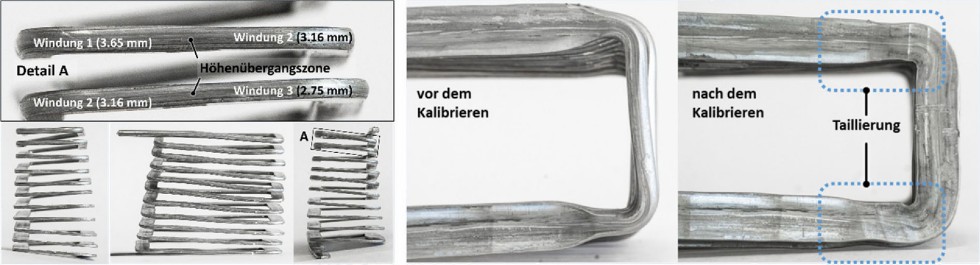
Bild 6. Finale Demonstratorspule mit 11 Windungen und trapezförmiger Querschnittsgeometrie; links: vollständige Spule aus Al 99.9; rechts: Detail der Taillierung im Übergang vom Nutbereich zum Wicklungskopf. Grafik: Fraunhofer IWU
4 Herausforderungen, Fazit und Ausblick
Es gibt an den gefertigten Demonstratoren zwei geometrische Abweichungen von der ausgelegten finalen Geometrie. Zum einen betrifft dies die Knickung in den Nutbereichen, zum anderen die bereits durch die FE-Simulation prognostizierte Taillierung im Übergangsbereich von der Nut zum Wicklungskopf.
Die Knickung befindet sich in dem Bereich der Spule, der beim Kalibrieren des Wicklungskopfes in der Auslaufzone des Werkzeuges liegt. Die Ursache für diese Knickung jeder Windung ist der notwendige Übergang in die nächste Windungslage. Jede aus dem Werkzeug ragende freie halbe Windung der Spule ohne Kontakt zu den Pressplatten muss in die nächste Windungsebene geführt werden. Dies hat zur Folge, dass in Abhängigkeit von der Dicke der Pressplatten und der Länge der Spule die Biegung jeder einzelnen Windung im Nutbereich sehr stark ausgeprägt sein kann. Je kleiner demnach die Plattendicke und je länger die Spule ist, desto geringer ist die Biegung. Allerdings sinkt bei Einsatz von zu dünnen Werkzeugplatten auch deren Festigkeit, was zur Gefahr des Werkzeugbruches bei den hohen Prozesskräften führt.
Die Taillierung der Demonstratorspule ist detailliert in Bild 6, rechts dargestellt. Es wird die unterste Windung der Spule vor und nach dem Kalibrieren des Wicklungskopfes gezeigt. Die Taillierung ist eine Folge des axialen Fließens des Werkstoffes beim ersten Schritt und dem nachfolgenden Kalibrierschritt der hier beschriebenen Prozesskette. Der Effekt der Verringerung der Drahtlängung beim Pressen mit Einsatz der angepassten Werkzeuggeometrie (vgl. Bild 3) wirkt sich positiv auf die Ausbildung der Taillierung aus. Im praktischen Versuch kann nachgewiesen werden, dass die Breite des Leiters im Taillierungsbereich im Durchschnitt um knapp 20 % größer ist als die mit dem Erstentwurfswerkzeug erreichbare Leiterbreite.
Mit den derzeitigen Werkzeugen ist eine weitergehende Verringerung des Effektes beziehungsweise vollständige Vermeidung der Taillierung zunächst nicht möglich. Obwohl das aktuelle Umformergebnis noch nicht allen Anforderungen an die elektromagnetische Leistungsfähigkeit und die geometrische Toleranz entspricht, zeigt es dennoch das hohe Potenzial zur Herstellung von Spulen mit trapezförmiger Querschnittsgeometrie. Die entwickelte Prozesskette zeigt einen Weg auf, einen hohen Nutfüllfaktor durch lageangepasste Windungsgeometrien bei maximaler Werkstoffausnutzung umzusetzen. Bei Einsatz der beschriebenen Technologie ist ein großes Potenzial zur Werkstoff- und Energieeinsparung bei der Fertigung und im Betrieb elektrischer Maschinen zu erwarten.
Literatur
- Hagedorn, J.; Sell-Le Blanc, F.; Fleischer, J.: Handbuch der Wickeltechnik für hocheffiziente Spulen und Motoren. Berlin, Heidelberg: Springer 2016
- Bickel, B.; M. Hübner, M.; Franke, J.: Analyse des Optimierungspotenzials zur Erhöhung des Kupferfüllfaktors in elektrischen Maschinen, ant Journal, S. 16–21, 2014, 2014
- Zerbe, J.: Innovative Wickeltechnologien für Statorspulen zur Erhöhung des Füllfaktors und Reduzierung der Beanspruchungen im Wickelprozess. Dissertation, TU Berlin, 2018
- Groninger, M. et al.: Casting production of coils for electrical machines. In: 1st International Electric Drives Production Conference EDPC, Nürnberg, 2011, S. 159–161, doi: 10.1109/EDPC.2011.6085534
- Rau, E.; Shendl, A.: Stator for a polyphase electric machine and method for manufacturing same, US 2010/0295390 A1. USA 12/295,560, Nov 25, 2010
- Müller, G.; Vogt, K.; Ponick, B.: Berechnung elektrischer Maschinen, 6. Aufl. Weinheim: Wiley-VCH, 2011. Internet: http://swbplus.bsz-bw.de/bsz264767756cov.htm
- Halwas, M. et al.: Entwicklung eines parallelen Technologie- und Produktentwicklungsprozesses/Development of a parallel technology and product development process using the example of winding design and manufacture as a part of the NeWwire funded project. wt Werkstattstechnik online (2018) S. 301–306
- Bach, M.; Psyk, V.; Linnemann, M.; Kräusel, V.; Bergmann, M.; Pohl, N.: Towards the Forming of concentrated Windings with trapezoidal cross sections for Increasing the Slot Filling Factor. In: 11th International Electric Drives Production Conference EDPC, Erlangen, 2021, S. 35–39
Dr.-Ing. Mirko Bach
Andreas Hemmerle
Fraunhofer-Institut für Werkzeugmaschinen und Umformtechnik IWU
Reichenhainer Str. 88, 09126 Chemnitz
Tel. +49 371 5397-1244
www.iwu.fraunhofer.de