Durch den Digitalen Zwilling die Produktion updaten
Ein Forschungsteam am Zentrum für digitalisierte Batteriezellproduktion des Fraunhofer-Instituts für Produktionstechnik und Automatisierung IPA hat untersucht, wie sich durch eine Digitalisierung der Fertigung nicht nur Produktionsprozesse optimieren, Material sowie Energie einsparen lassen, sondern auch die Lebensdauer der Akkus verlängert werden kann.
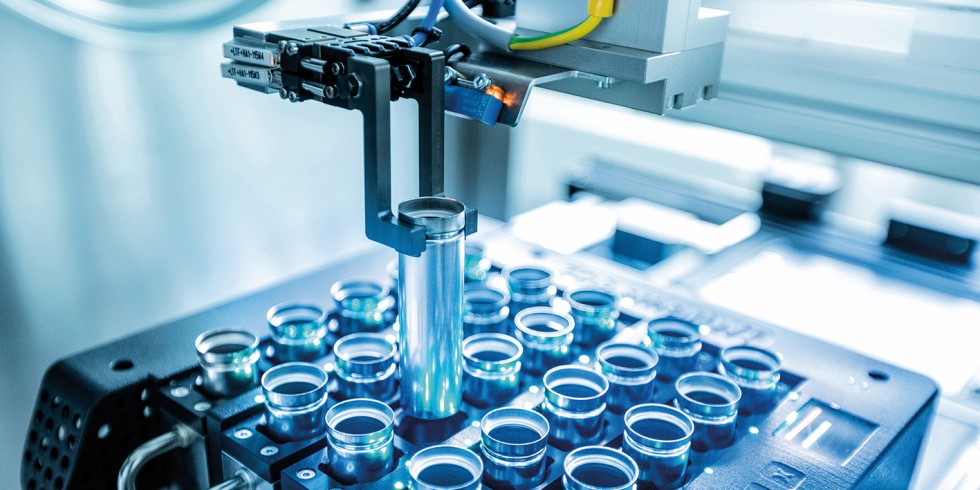
Bild 1. Assemblierung von Batteriezellen mit einem intelligenten Werkstückträger für die digitalisierte Produktion.
Foto: Fraunhofer IPA
Die Anzahl der Neuzulassungen von Elektroautos in Deutschland erreichte im Jahr 2022 einen Rekordwert. Laut Kraftfahrt-Bundesamt wurden 470559 Pkw mit reinem Elektroantrieb neu zugelassen. 2021 waren es mit 355961 Neuzulassungen fast ein Viertel weniger.
Mit der steigenden Nachfrage an E-Autos rückt die Herstellung der Batteriezellen immer stärker in den Vordergrund. Sie ist energie- und ressourcenintensiv. Im Fall eines PKW mit zylindrischen Zellen benötigt man pro Batterie aktuell 7000 bis 10000 Stück. Die Zellen enthalten neben Lithium auch Nickel, Mangan und Cobalt, Graphit, Polymere und Elektrolyte.
Um die Produktion effizient und nachhaltig zu gestalten, muss die Batteriezellenfertigung unbedingt optimiert werden. Ein Forschungsteam am Zentrum für digitalisierte Batteriezellproduktion des Fraunhofer-Instituts für Produktionstechnik und Automatisierung IPA hat im 2022 erschienenen „Handbook on Smart Battery Cell Manufacturing“ dargestellt, wie sich durch eine Digitalisierung der Fertigung nicht nur Produktionsprozesse optimieren, Material sowie Energie einsparen lassen, sondern auch die Lebensdauer der Akkus verlängert werden kann.
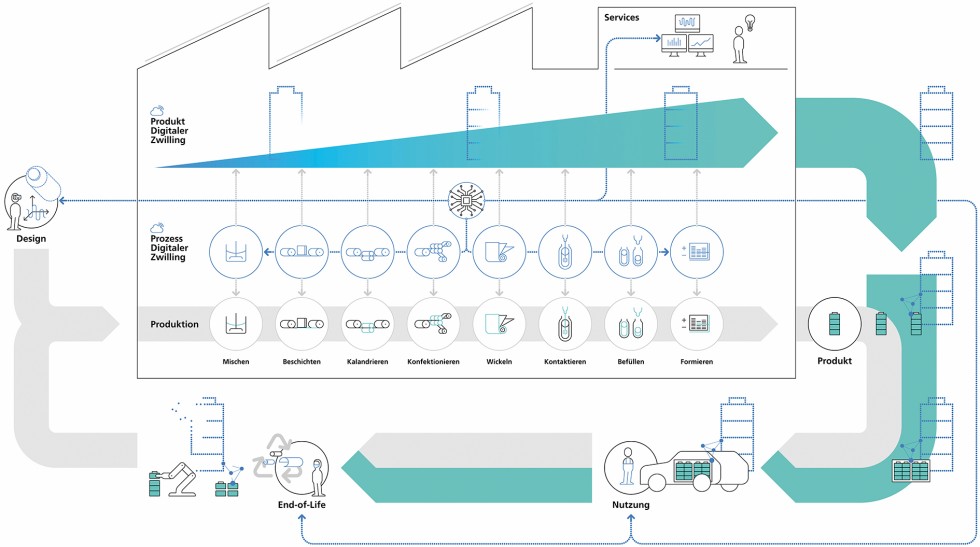
Bild 2. Die Vernetzung über die gesamte Prozesskette hinweg generiert riesige Datenmengen. Diese werden im Zentrum für Digitalisierte Batteriezellenproduktion (ZDB) des Fraunhofer IPA gesammelt, zusammengeführt und ausgewertet. In Zukunft soll die lückenlose Nachverfolgbarkeit der Produktion in Echtzeit geschehen – mit einem sogenannten Digitalen Zwilling. Grafik: Fraunhofer IPA
Mit Digitalen Steckbriefen Einzelzellen auswählen und zu hochqualitativen Akkus verbinden
Durch digitalisierte Produktionssteuerung lassen sich die Fertigungsprozesse beschleunigen und flexibel an Kundenwünsche anpassen und Qualitätsmängel frühzeitig aufspüren: Bauteile, die nicht den Kriterien entsprechen, können aussortiert werden. Durch digitale Fehleranalyse lassen sich außerdem schnell die Ursachen der mangelnden Produktqualität identifizieren und Herstellungsprozesse nachjustieren.
Das spart Zeit, Material und Energie. Die Daten, die während der Produktion gesammelt werden, lassen sich anschließend nutzen, um für jede Zelle einen Steckbrief zu erstellen, der sie ein ganzes Produktleben lang begleitet. Dieser Produktlebenslauf enthält beispielsweise Informationen darüber, aus welchen Materialien die Zelle gefertigt wurde, aus welchen Substanzen die Elektroden bestehen und wie viel Elektrolyt zugegeben wurde.
Wenn die Hersteller von Akkus dank der digitalen Steckbriefe die Kapazitäten jeder Einzelzelle kennen, können sie diese gezielt auswählen und zu hochqualitativen Akkus verbinden. Dadurch würde sich die Lebensdauer der fertigen Akkus verlängern. Denn diese hängt von der Kapazität der Einzelzellen ab – je geringer die Kapazitätsunterschiede sind, desto länger lebt die Batterie. Und im laufenden Betrieb würde der Steckbrief dem Batteriemanagementsystem helfen, den Ladeprozess so zu steuern, dass die einzelnen Zellen möglichst gut ausgelastet werden.
Lebensdauer von Batteriezellen vorhersagen
Die Digitalisierung spielt an einer anderen Stelle noch eine ganz erhebliche Bedeutung. Die Lebensdauer von Batteriezellen vorherzusagen ist entscheidend. Ohne diese wichtige Voraussetzung dürfte man keinen Pkw auf die Straße bringen. Zum einen gilt das für jede neu entwickelte Zellgeneration, zum anderen für jede Zelle im Betrieb in einer Batterie.
Im Falle der Zellgeneration geht es darum, sicher sein zu können, dass die Zelle die garantierte Lebensdauer von zum Beispiel 10 bis 15 Jahren einhält. Das heißt, die Zellen müssen nach dieser Zeit zum Beispiel noch 80 % ihrer Initialkapazität besitzen.
Im Falle des Betriebs spielen individuelle Vorgeschichten wie Temperatur und Betriebsprofile eine erhebliche Rolle. Bei all diesen Szenarien kann man nicht warten, bis man Zellen 10 bis 15 Jahre getestet hat, man muss sich also auf ein Modell, eine Simulation verlassen: Und hier kommt der Digitale Zwilling ins Spiel.
Simulation durch den Digitalen Zwilling
Was unterscheidet nun den Digitalen Zwilling überhaupt von einem Modell der Batteriezelle? Ein elektrisches Ersatzschaltbild einer Batteriezelle, das aus elektrischen Bauteilen wie Widerständen, Kondensatoren etc. besteht, kann beispielsweise dann eine Vorhersagekraft (zum Beispiel für die Zellalterung) entwickeln, wenn es gelingt, die elektrischen Bauteile zu parametrieren. Das bedeutet, die einzelnen Kenngrößen mit konkreten Werten zu versehen, Widerstände, Kondensatoren beispielsweise mit bestimmten Initialwerten und diese abhängig von der Alterung der Batteriezellen anzupassen. Das ist der Stand der Technik.
Ein Digitaler Zwilling kann mehr. Er ist echtzeitfähig und kann durch Kommunikation mit dem Batteriemanagementsystem durch stets aktuelle Daten präziser nachgeführt werden. Man kann sich das wie mit regelmäßigen Updates eines Computerprogramms vorstellen. Je präziser die Vorhersage ausfällt, desto sicherer funktioniert die Batterie. Außerdem können Batterien exakter gebaut werden. Man kann ihnen genau die Kapazität geben, die tatsächlich für eine Anwendung benötigt wird und muss nicht mit Überkapazitäten von 10 % bis 20 % arbeiten, die nur als Sicherheitspuffer eine schlechte Vorhersage des Gesundheitszustands kompensieren. Das spart wiederum Gewicht und Kosten. Außerdem werden auf diese Weise weniger Zellen gebraucht.
Digitale Zwillinge von Batteriezellen könnten eines Tages auch zur Konstruktion von Batterien dienen. Letzen Endes könnte man auch eine ganze Batteriezellfertigung virtuell entwerfen und zunächst im Computer simulieren. Das kann viele teure Schleifen sparen. Im Automobilbau der 1980er Jahre wurden solche Simulationen immer weiterentwickelt. Heute sind sie selbstverständlich. Die Digitalisierung ist also noch weit mehr als eine Optimierung der Produktion von Batteriezellen: Durch den Digitalen Zwilling wird die Produktion selbst immer wieder upgedatet.
Die aktuellen Batteriezellproduktionen immer weiter zu digitalisieren ist aber ein guter und konsequenter Start, da so viel Ausschuss und Kosten gespart und die Langzeitstabilität und Qualität von Batteriezellen noch erheblich gesteigert werden können.
Handbook on Smart Battery Cell Manufacturing. The Power of Digitalization, 488 Seiten. Internet: www.worldscientific.com
Prof. Dr.-Ing. Kai Peter Birke
Julian Grimm
Florian Maier
Joachim Montnacher
Fraunhofer-Institut für Produktionstechnik und Automatisierung IPA
Nobelstr. 12, 70569 Stuttgart
Tel. +49 711 970-3621
kai.peter.birke@ipa.fraunhofer.de
www.ipa.fraunhofer.de