AR-Assistenz für die modulare Spannmittelmontage
In der CNC-Bearbeitung ist es zur Kollisionsvermeidung sehr wichtig, dass real aufgebaute Spannsysteme exakt der Vorgabe aus der CAD/CAM-Simulation entsprechen. In diesem Beitrag wird ein industrietaugliches Assistenzsystem präsentiert, mit dem per Augmented Reality (AR) die manuelle Montage von modularen Spannsystemen unterstützt wird und so Fehler vermieden werden können. Es wird aufgezeigt, dass die Kamera-Monitor-basierte AR geeignet ist, um unter rauen Bedingungen intuitive Montageanleitungen zu visualisieren. Dadurch lassen sich Bearbeitungszeiten in der CNC-Maschine verkürzen und die Montage beschleunigen.
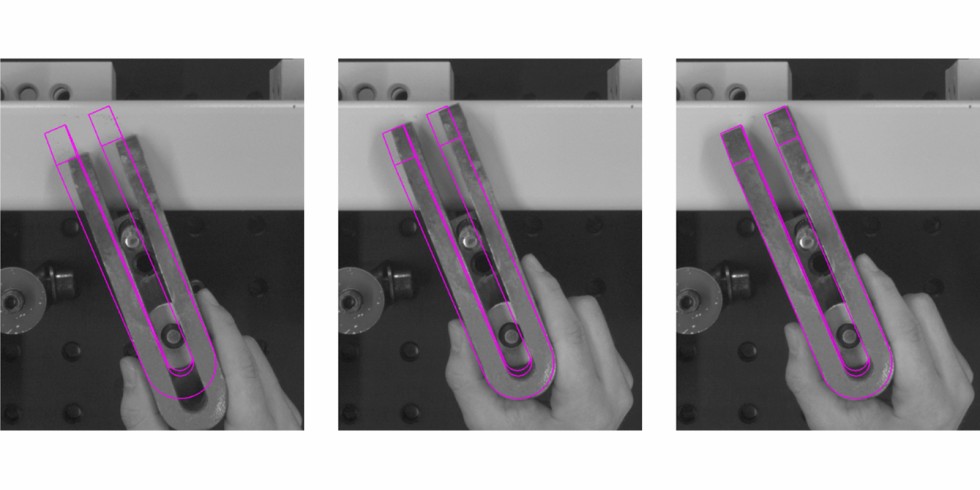
Bild 1. Assistierte Ausrichtung eines Spanneisens mittels Augmented Reality.
Foto: IFF / FMA
Ausgabe 10-2022, S. 591
Error-free Assembly of Clamping Systems – Assembly Assistance for Modular Clamping Systems
Abstract: In CNC machining, the similarity of real assembled clamping systems compared to the constructed clampings in CAD/CAM is of critical importance. If differences are present, unintentional collisions between tool and clamping system can occur, which may lead to total breakdown. In this work we present an Augmented Reality (AR) industry-ready assistance solution, which helps workers to reduce the error rate when clamping systems are assembled manually. We will show that camera-screen-based AR is well suited to present assembly instructions in harsh environmental conditions and that by using this solution machining times can be reduced and the assembly itself can be accelerated significantly.
1 Motivation
Im Sondermaschinenbau werden verstärkt Kleinserien gefertigt. Die dafür notwendigen Einzelteile fallen daher zum Teil mit einer hohen Variantenvielfalt bei vergleichsweise geringer Losgröße aus. Daher stellen Fertigung und Montage der Teile aufgrund der sich stetig ändernden Bedingungen eine große Herausforderung für den Menschen dar.
Ein wichtiger Schritt in der Fertigung ist die spanende Verarbeitung von Rohteilen zu Fertigteilen mittels CNC-Maschinen. Hier werden die zu bearbeitenden Bauteile in Spannvorrichtungen fixiert, damit diese automatisiert spanend bearbeitet werden können. Für den Kleinserienbereich existieren Baukastensysteme mit einer Vielzahl von Komponenten, aus denen diese Spannvorrichtungen manuell zusammengesetzt werden können. Hierbei ist es von enormer Wichtigkeit, dass die Spannvorrichtungen exakt nach Vorgabe aufgebaut werden. Werden dabei falsche Komponenten verwendet oder diese nicht lagerichtig montiert, kann es zu ungewollten Kollisionen in der Bearbeitungsmaschine kommen, wenn das Werkzeug oder die Spindel mit der Spannvorrichtung oder einem falsch fixierten Bauteil kollidiert.
Die Montage der Spannsysteme erfolgt derzeit überwiegend manuell und anhand von abgeleiteten 2D-Zeichnungen, Screenshots aus dem Konstruktionsprogramm oder Fotos von zuvor bereits montierten Spannsystemen. Zur Bearbeitung wird das Spannsystem in die CNC-Maschine eingefahren und das erste Rohteil einer Serie, das „Erstteil“ fixiert. Da nicht sichergestellt werden kann, dass das Spannsystem fehlerfrei ist, wird die Bearbeitungsgeschwindigkeit der Maschine stark gedrosselt und der Maschinenbediener fährt dieses satzweise, das heißt Punkt für Punkt ab. Wird dabei ein Montagefehler erkannt, muss das Bearbeitungsprogramm abgebrochen, das Spannsystem aus der Maschine entfernt, korrigiert und neu getestet werden.
Der digitale Bruch, der somit bei der manuellen Spannsystemmontage entsteht, verursacht hier eine eklatante Lücke, die zu hohen Belastungen der Mitarbeiter und erhöhtem Zeitaufwand führt und im Fehlerfall zu hohen Kosten durch Maschinenschaden.
In diesem Beitrag wird ein Augmented-Reality-System vorgestellt, mit dem die modulare Spannsystemmontage sicherer und effizienter durchgeführt werden kann, s. Bild 1.
2 Augmented Reality in der Montage
Eine Vielzahl von Studien beschäftigt sich mit der Fragestellung, ob und in welchem Maße AR hilft, die mentale und kognitive Arbeitsbelastung zu senken und dabei die Produktivität der Anwender zu steigern [1]. Abhängig vom Ausgabegerät wird AR mehrere Typen gegliedert, die jeweils Vor- und Nachteile haben:
- Mobile AR: Hier werden Informationen auf tragbaren Endgeräten wie Smartphones oder Tablets ausgegeben. Dabei wird typischerweise der Videostrom der integrierten Kamera mit zusätzlichen Visualisierungen angereichert, die örtlich referenziert sein können [2]. Mobile AR bietet eine hohe Flexibilität bei der Auswahl der Perspektive, jedoch muss das Gerät gehalten werden, wodurch eher für Instandhaltungs- und Wartungsaufgaben geeignet ist.
- Optical See-Trough AR: Bei dieser Variante tragen die Nutzer eine Brille, an dem ein halbtransparentes Display angeschlossen ist (Head Mounted Display, HMD). Die dargestellten Informationen können räumlich referenziert sein und werden direkt in das Sichtfeld des Anwenders eingeblendet. Verschiedene Studien zeigen bisher, dass AR per HMD generell unter Akzeptanzproblemen leidet, die hauptsächlich durch unangenehmes Tragen über einen längeren Zeitraum und das eingeschränkte Sichtfeld hervorgerufen werden [3–5].
- Projektive AR / Spatial AR: Hierbei werden die Informationen mittels eines externen Projektors direkt auf eine Arbeitsfläche oder ein Bauteil projiziert [5]. Die Nutzbarkeit dieser Form hängt stark vom Anwendungsszenario ab. Projektionen sind generell anfällig für Schwankungen in der Umgebungsbeleuchtung und für glänzende Oberflächen. Zudem sind sie bei der Darstellung 3-dimensionaler Inhalte wenig intuitiv, da die meisten Projektoren für eine Darstellung auf ebenen Flächen ausgelegt sind [6].
- Indirekte AR: Hiermit werden Systeme mit fest installierten oder frei beweglichen Kameras bezeichnet, bei denen die Ausgabe auf externen Monitoren erfolgt. Die Kameras sind zum Arbeitsplatz referenziert, wodurch Informationen zeitlich und räumlich korrekt dargestellt werden können [7]. Diese Form der AR ist aus technischer Sicht vergleichsweise einfach, findet in der Forschung aber wenig Beachtung [8]. Dennoch ist sie für Montagetätigkeiten sehr gut geeignet, da der Anwender kein zusätzliches Gerät tragen muss, die Visualisierung auf einem Bildschirm auch für 3D-Objekte geeignet ist und beide Hände stets frei bleiben.
- Eine Übersicht über aktuelle kommerzielle AR-Systeme im Bereich der Montage findet sich in [9]. Hier zeigt sich, dass Assistenzsysteme im industriellen Einsatz derzeit auf projektive und indirekte AR setzen.
3 Augmented Reality zur Montageassistenz unter industriellen Bedingungen
Basierend auf den Einschätzungen aus dem vorhergehenden Abschnitt wurde ein Assistenzsystem entwickelt, das Werker bei der Spannsystemmontage unterstützt. Es handelt sich hierbei um indirekte AR, bei der die augmentierte Ausgabe auf Monitoren erfolgt. Ausschlaggebend für diese Entscheidung war, dass beide Hände bei der Montage frei sein müssen, das System auch unter schwierigen Umgebungsbedingungen im 3-Schichtbetrieb zuverlässig funktionieren muss, der Überlagerungsfehler unter 0,5 mm bleibt und dass eine maximale Mitarbeiterakzeptanz erreicht wird. Das System dient als vollständiger Ersatz für alle bisherigen Montageanleitungen.
3.1. Systemaufbau
Arbeitsplätze für die assistierte, modulare Spannsystemmontage werden mit einer festen Aufnahme ausgerüstet, die für Zapfen der entsprechenden Nullpunktspannsysteme ausgelegt ist. Zur reproduzierbaren lokalen Verankerung werden die Grundplatten dort eingesetzt. Das Assistenzsystem selbst besteht aus mindestens zwei fest angeordneten Kameras, die auf den Arbeitsplatz ausgerichtet sind und kontinuierlich Videobilder aufnehmen. Eine Kamera wird typischerweise senkrecht über dem Arbeitsplatz montiert und deckt in der Aufsicht die horizontale Montageebene ab. Die zweite Kamera wird schräg ausgerichtet und deckt die vertikale Montageebene ab. Als Ausgabe- und Interaktionsgeräte stehen zwei Touch-Screens zur Verfügung, die in ergonomischer Reichweite am Arbeitsplatz montiert sind. Zur Generierung der AR wird das CAD-Modell der zu montierenden Bauteile zum korrekten Zeitpunkt perspektivisch korrekt als Konturdarstellung in das Kamerabild projiziert, s. Bild 2.

Bild 2. Assistenz-GUI zur sicheren Spannmittelmontage. Links: perspektivisch korrekte Überlagerung von Bauteilkonturen, rechts: das zugehörige CAD-‧Modell der gesamten Baugruppe. Grafik: IFF / FMA
Der Mitarbeiter kann dann anhand der visuellen Vorgaben das korrekte Einzelteil dem Lager entnehmen und es exakt und passgenau an der vorgegebenen Position platzieren, ausrichten und fixieren. Durch eine parallele Darstellung von Auf- und Schrägsicht ist sichergestellt, dass das Einzelteil in allen drei Raumachsen korrekt positioniert und orientiert werden kann.
Da Grundplatten von Bearbeitungszentren unterschiedliche Geometrien aufweisen, existieren mehrere Möglichkeiten, eine ergonomische Ansicht auf den Arbeitsplatz zu erreichen. Für Platten mit quadratischem Grundriss eignet sich die beschriebene senkrecht/schräg-Anordnung sehr gut. Um auch Einzelteile, die der schräg ausgerichteten Kamera abgewandt sind, in der Visualisierung darzustellen und um die Ergonomie zu steigern, kann die Grundplatte auf einem Rotationstisch mit Drehgeber abgelegt werden, s. Bild 3.

Bild 3. Rüstplatz mit indirekter AR zur Montage von modularen Spannsystemen mit quadratischen Grundplatten. Links: Grundfläche 900 x 900 mm², rechts: Grundfläche 600 x 600 mm².
Foto: IFF / FMA
Die Winkelstellung des Tischs wird dann ausgewertet und fließt in die AR-Darstellung mit ein. Die Einschränkung der starren Kameraansichten wird dadurch kompensiert und es entsteht eine hochgenaue, lagekorrekte AR-Überlagerung.
Für sehr große Spannsysteme besteht weiterhin die Möglichkeit, eine in sich fest verbundene Kamera-Monitoreinheit auf einer leichtgängigen Linearachse zu bewegen und so die gesamte Arbeitsfläche abzudecken, s. Bild 4.

Bild 4. AR-Assistenzsystem für große modulare Spannsysteme. Links: auf einer Linearachse verschiebbare Touch-Screen-Einheit. Rechts: Gesamtsystem für Grundplatten bis insgesamt 3780 x 500 mm² (zwei von drei Grundplatten aufgelegt).
Foto: IFF / FMA
Hierbei sieht der Anwender die Assistenz für den Teilausschnitt, an dem sich das System gerade befindet. Sollten zu montierende Teile außerhalb des aktuellen Sichtfelds liegen, wird durch einen Pfeil in der AR-Darstellung darauf hingewiesen, und der Mitarbeiter kann intuitiv das System an die erforderliche Position verschieben.
3.2. Datenfluss
Neben einer intuitiven Assistenz-Darstellung ist im Bereich der Augmented Reality auch die Vorbereitung (das Authoring) der Inhalte von entscheidender Bedeutung [10]. Für das hier vorgestellte System wurde daher eine möglichst nahtlose Integration in bestehende Infrastrukturen angestrebt, die keine Programmierkenntnisse für die Arbeitsvorbereitung erfordern.
Als Basis für die AR-Darstellung dient das CAD-Modell des modularen Spannsystems. Es enthält bereits alle notwendigen Geometrieinformationen, um die Konturen lagegerecht und live zu erzeugen: Nachdem für ein Rohteil im CAD/CAM-System ein Spannsystem konfiguriert wurde, wird eine Montagereihenfolge festgelegt. Hierbei handelt es sich um lineare Montagevorranggraphen mit n Arbeitsschritten, denen jeweils nm Einzelteile der Gesamtbaugruppe zugewiesen werden. Jedem Arbeitsschritt lassen sich Hinweise in Textform, wie beispielsweise vorgegebene Drehmomente, hinzufügen. Nachdem die CAM-Simulation erfolgreich abgeschlossen ist, wird die Montagereihenfolge zusammen mit dem CAD-Modell des Spannsystems exportiert und am Rüstplatz als Assistenz für die Montage verwendet. Dort werden dem Monteur jeweils alle Elemente eines Arbeitsschritts gleichzeitig visualisiert. Existiert ein Montagehinweis, wird dieser in das Kamerabild mit eingeblendet. Beginnend mit der Grundplatte im ersten Schritt, kann der Anwender linear in der vorgegebenen Reihenfolge manövrieren und die Einzelteile sicher und entsprechend der Vorgabe verbauen. Der gesamte Datenfluss ist in Bild 5 dargestellt.

Bild 5. Datenfluss zur Vorbereitung und Ausführung der assistierten Spannmittelmontage. Grafik: IFF / FMA
Ein so montiertes Spannsystem ist geometrisch korrekt und entspricht der CAM-Simulation. Damit sind ungewollte Kollisionen in der Bearbeitungsmaschine ausgeschlossen.
4 Ergebnisse in der Anwendung
Die vorgestellte Lösung wird seit mehreren Jahren bei einem Pilotkunden im 3-Schichtbetrieb eingesetzt. Dabei wurden fünf Arbeitsplätze in den zuvor beschriebenen Konfigurationen ausgestattet und als separate Rüstplätze zur Bestückung von zehn Werkzeugmaschinen eingerichtet. Die Umgebungsbedingungen können als rau eingeschätzt werden, da die Maschinen in unmittelbarer Nähe im Einsatz sind.
4.1. Bewertung der Assistenzfunktionalitäten
Die Evaluation der Assistenz misst sich primär daran, ob das Ziel der Kollisionsvermeidung in der Maschine erreicht werden konnte. Seit Einführung der assistierten Montage (zwei bis neun Jahre) ist es zu keinem Zwischenfall gekommen, der auf ein fehlerhaft montiertes Spannsystem zurückgeführt werden kann. Damit wird das Hauptziel erreicht.
In [11] werden acht Richtlinien und Empfehlungen für ergonomische AR-Assistenzsystem im Bereich der Montage formuliert. Angewendet auf die hier vorgestellte Lösung ergeben sich folgende Bewertungen:
- Einfache Darstellung der Information: Es werden Objektkonturen visualisiert. Sie enthalten das Mindestmaß an Informationen, um die Bauteilgeometrie in der Darstellung zu beschreiben.
- Direkte Darstellung der Information: Die Arbeitsplätze sind so gestaltet, dass die zur Ausgabe genutzten Screens vor dem Werker angebracht sind. Nach kurzer Einarbeitung schauen die Mitarbeiter während der Montagetätigkeit direkt auf den Bildschirm. Dass Hände, Werkzeuge und Bauteile nur indirekt betrachtet werden, stellt kein Problem dar.
- Design für Freihandanwendung: Dies ist bei indirekter AR immer gegeben.
- Ausstattung der Umgebung statt des Nutzers: Bei dieser Lösung sind alle Sensoren wie Drehgeber und Linearmesssysteme fest verbaut. Der Anwender trägt kein Equipment.
- Intuitive, natürliche Interaktion: Die Interaktion erfolgt ausschließlich über die Touch-Funktion der Screens. Touch-Bedienung erfordert durch die Verbreitung von Smartphones kein separates Einlernen.
- Personalisierte Informationsdarstellung: Für Menschen, die Farbsinnstörungen leiden, besteht die Möglichkeit die Konturfarbe nach individuellen Bedürfnissen anzupassen.
- Geschwindigkeitsvorgabe durch den Nutzer: Die manuelle Vor- und Rückwärtsnavigation zwischen den Arbeitsschritten erlaubt dem Nutzer, die Geschwindigkeit vollständig selbst kontrollieren.
- Motivierenden Selbstauskünfte: Die Montagesequenz wird tabellarisch dargestellt und der Anwender sieht zu jedem Zeitpunkt den aktuellen und alle folgenden Montageschritte. Damit wird eine Einschätzung über die Restdauer der Montage deutlich erleichtert.
4.2. Ökonomische Betrachtungen
Da durch den Einsatz des Assistenzsystems von einer Kollisionsfreiheit ausgegangen werden kann, können Werkzeuge bei der Bearbeitung deutlich schneller zugestellt werden. Hier wurde eine Einsparung von 3,4 bis 11,1 Minuten pro Programm ermittelt (durchschnittlich 5,8 Minuten).
Für die aufwendige Bearbeitung von Erstteilen ergibt sich ein weiteres Einsparpotenzial: Das satzweise Anfahren eines Neuprogramms kann entfallen und das Erstteil kann mit vollem Vorschub bearbeitet werden. Durch diese Maßnahme kann die Einfahrzeit pro Programm zwischen 15 und 20 Minuten gesenkt werden (Durchschnitt 15,9 Minuten).
Weiterhin wurde die Montagezeiten an den Rüstplätzen verglichen. Die Messungen fanden unter realen Arbeitsbedingungen nach erfolgreicher Einarbeitung statt. Ohne AR wurden als Anleitungen ausgedruckte ISO-Darstellungen, 3D-Screenshots vom Spannsystem, Fotos von bereits erfolgten Aufbauten und zum Teil handschriftliche Notizen verwendet. Es wurde beobachtet, dass mithilfe der AR eine Zeiteinsparung von 17–22 % erreicht werden kann. Die befragten Mitarbeiter hoben hervor, dass es als mental sehr entlastend empfunden wird, anhand einer festen Montagereihenfolge zu arbeiten. Sie führt zu mehr Sicherheit, da den Monteuren bewusst ist, dass ein unter AR-Anleitung montiertes Spannsystem immer kollisionsfrei bearbeitet werden kann. Zeiteinsparungen wurden insbesondere durch die lokal referenzierte Darstellung, weniger Ablenkung und dem Wegfall von Rückbauten im Fehlerfall begründet.
5 Zusammenfassung
In diesem Beitrag wurde gezeigt, dass im Bereich des modularen Spannsystemaufbaus indirekte AR, deren Bilder aus fest angeordneten Kameras stammen und deren Ausgabe auf Touch-Screens stattfindet, sehr gut eignet ist. Es wurden verschiedene Arbeitsplätze mit diesen Systemen ausgestattet. In der praktischen Anwendung sank dadurch die Fehlerrate bei der Montage auf null. Weiterhin konnte nachgewiesen wenden, dass die Montage beschleunigt und insbesondere in der Einzelteil- und Kleinserienfertigung die Bearbeitungszeiten deutlich verkürzt werden können.
Die Autoren danken der Firma Kolbus GmbH & Co. KG für die Bereitstellung der CAD-Daten und des Bildmaterials.
Literatur
- Jeffri, N. F. S.; Awang Rambli, D. R.: A review of augmented reality systems and their effects on mental workload and task performance. Heliyon 7 (2021) 3
- Havard, V.; Baudry, D.; Jeanne, B. et al.: A use case study comparing augmented reality (AR) and electronic document-based maintenance instructions considering tasks complexity and operator competency level. Virtual Reality 25 (2021) 4, S. 999–1014
- Lampen, E.; Teuber, J.; Gaisbauer, F. et al.: Combining Simulation and Augmented Reality Methods for Enhanced Worker Assistance in Manual Assembly. Procedia CIRP 81 (2019), S. 588–593
- Deshpande, A.; Kim, I.: The effects of augmented reality on improving spatial problem solving for object assembly. Advanced Engineering Informatics 38 (2018), S. 760–775
- Bosch, T.; Könemann, R.; Cock, H. de et al.: The effects of projected versus display instructions on productivity, quality and workload in a simulated assembly task. PETRA ‚17: 10th International Conference on PErvasive Technologies Related to Assistive Environments, Island of Rhodes/Greece, 2017, S. 412–415
- Cortes, G.; Marchand, E.; Brincin, G. et al.: MoSART: Mobile Spatial Augmented Reality for 3D Interaction With Tangible Objects. Frontiers in robotics and AI 5 (2018), p. 93
- Loch, F.; Quint, F.; Brishtel, I.: Comparing Video and Augmented Reality Assistance in Manual Assembly. 2016 12th International Conference on Intelligent Environments (IE), London, United Kingdom, 2016, S. 147–150
- Alves, J. B.; Marques, B.; Dias, P. et al.: Using augmented reality for industrial quality assurance: a shop floor user study. The International Journal of Advanced Manufacturing Technology 115 (2021) 1–2, S. 105–116
- Bertram, P.; Birtel, M.; Quint, F. et al.: Intelligent Manual Working Station through Assistive Systems. IFAC-PapersOnLine 51 (2018) 11, S. 170–175
- Evans, G.; Miller, J.; Iglesias Pena, M. et al.: Evaluating the Microsoft HoloLens through an augmented reality assembly application. SPIE Defense + Security, Anaheim, California, United States, 2017, 101970V
- Funk, M.; Kosch, T.; Kettner, R. et al.: motioneap: An overview of 4 years of combining industrial assembly with augmented reality for industry 4.0. 2016
Dipl.-Inf. Steffen Sauer
Dr.-Ing. Dirk Berndt
Fraunhofer Institut für Fabrikbetrieb und -automatisierung IFF
Fertigungsmesstechnik und digitale Assistenzsysteme FMA
Sandtorstr. 22, 39106 Magdeburg
steffen.sauer@iff.fraunhofer.de
www.iff.fraunhofer.de/fma