Industrielle Einführung der additiven Fertigung
Die Einführung der additiven Fertigung als industrielles Fertigungsverfahren stellt Unternehmen aufgrund der weitreichenden Unterschiede zu konventionellen Verfahren vor außergewöhnliche Herausforderungen. Um bei der Bewältigung dieser zu unterstützen und Lösungsmethoden bereitzustellen, forschen seit Beginn 2017 fünf Industrieunternehmen unter Leitung der Krause DiMaTec GmbH und koordiniert durch die Universität Paderborn gemeinsam im BMBF Forschungsprojekt „OptiAMix“.
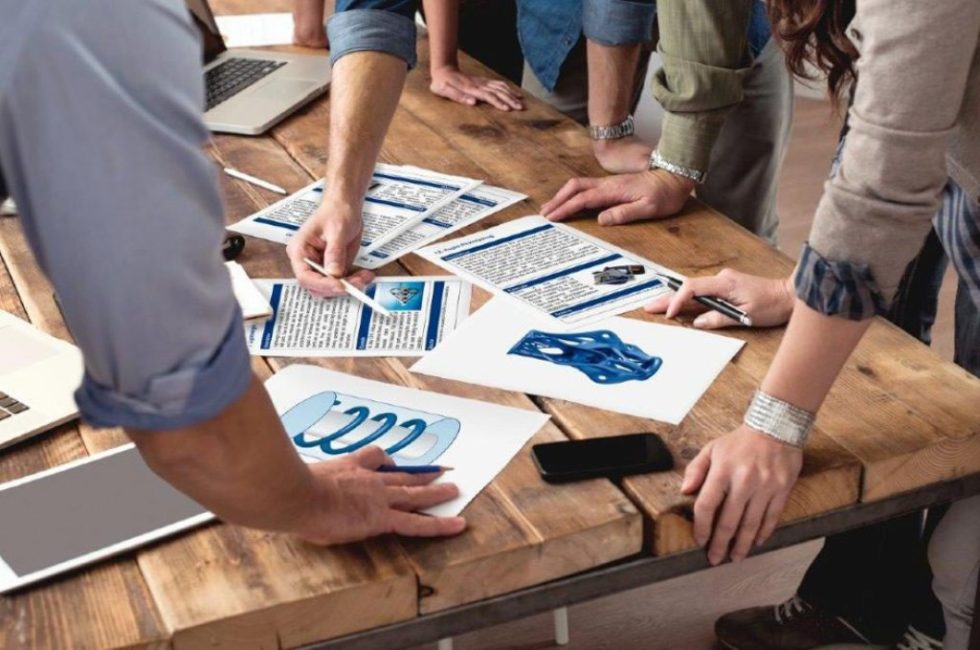
Bauteilauswahl für die additive Fertigung Bild: Krause DiMaTec
Immer mehr Unternehmen wollen die additive Fertigung beziehungsweise Additive Manufacturing (AM) industriell nutzen und die Technologie im eigenen Betrieb integrieren. Hierbei stehen sie Herausforderungen gegenüber, die es bei konventionellen Fertigungsverfahren in dieser Art noch nicht gab. Es herrscht allgemein Unsicherheit bezüglich der Prozesse, der erreichbaren Qualität sowie der allgemeinen Umsetzbarkeit der eigenen Produkte – weiter verstärkt durch fehlende Expertise auf dem Arbeitsmarkt und im eigenen Unternehmen [1]. Um den Ursprung dieser Unsicherheiten besser einordnen zu können, lohnt ein Blick auf die Historie der Produktionstechnik sowie des Qualitäts- und Prozessmanagements.
Produktionsverfahren wie das Schmieden (circa 8000 v. Chr.) oder das Gießen (circa 3000 v. Chr.) entwickelten sich über Jahrtausende zum heute etablierten industriellen Standard. Auch relativ junge Verfahren wie etwa das Fräsen (circa 1820 n. Chr.) oder das industrielle Schweißen (circa 1900 n. Chr.) basieren auf Jahrtausenden alten Prinzipien (Bohren – circa 38 000 v. Chr. und Feuerschweißen – circa 3000 v. Chr.) [2, 3]. Zusätzlich erreichten sie den industriellen Standard noch weit vor der Einführung des Qualitäts- und Prozessmanagements mit Methoden und Normen wie Six Sigma (1987) [4], der ISO 9001 (1987) [5] oder dem EFQM-Modell (European Foundation for Quality Management – 1988) [6]. Mit dem „SLA-1“, einer Anlage zur Fertigung von Bauteilen mittels Stereolithografie, von 3D Systems war erstmals 1987 ein „3D-Drucker“ überhaupt am Markt verfügbar [7]. Das heute im industriellen Kontext hauptsächlich betrachtete Selektive Laserschmelzen wurde erst 1995 entwickelt [8]. Während der Qualitäts- und Prozessbegriff in Bezug auf die Produktentstehung somit hauptsächlich durch den erreichten Stand der Produktionstechnik definiert wurden, stehen Unternehmen heute zum ersten Mal einem Verfahren gegenüber, das standardisierte Qualitätsanforderungen noch vor dem Erreichen eines einheitlichen industriellen Fertigungsstandards erfüllen muss. Durch die teilweise grundlegend neuen Fertigungsansätze der AM-Technologien – die additive Fertigung ist in der DIN 8580 „Fertigungsverfahren“ bis heute keiner Hauptgruppe zugeordnet – sind zur industriellen Nutzung darüber hinaus neben dem Fertigungsprozess auch Herausforderungen in den Bereichen der Produktplanung, der Konstruktion und der Qualitätssicherung zu bewältigen [9]. Erst dann kann die Technologie eine ernsthafte Alternative zu etablierten konventionellen Verfahren darstellen.
1 OptiAMix – Konsortium und Projektziele
Um die Herausforderungen in der Einführung und der industriellen Nutzung der additiven Fertigung besser bewältigen zu können, forschen seit Beginn des Jahres 2017 fünf Industriepartner unter der Leitung von Krause DiMaTec gemeinsam mit der Universität Paderborn im Forschungsprojekt „OptiAMix – Mehrzieloptimierte Produktentwicklung in der additiven Fertigung“. Im Rahmen der BMBF-Fördermaßnahme „Additive Fertigung – Individualisierte Produkte, komplexe Massenprodukte, innovative Materialien (ProMat3D)“ entwickeln sie Integrations- und Anwendungsmethoden sowie verschiedene Tools zur Unterstützung in der Produktentstehungsphase. Das Konsortium verfügt mit den 3D-Druck Dienstleistern Krause DiMaTec und Hirschvogel Tech Solutions, dem Forschungszentrum Direct Manufacturing Research Center der Universität Paderborn sowie dem Entwicklungsdienstleister EDAG Engineering über hohe Expertise im Bereich der additiven Fertigung und wird durch Intes im Bereich der Softwareentwicklung zur Topologieoptimierung sowie WP Kemper als Anwendungspartner aus dem Bereich der Lebensmitteltechnik unterstützt.
Die Ziele des Forschungsprojekts verteilen sich auf zwei Haupt- und vier Teilziele, welche zum Ende des Projekts in drei Demonstratoren validiert werden sollen.
Mit den Methoden zur Erarbeitung mechanischer Kennwerte sowie zur Ableitung von Konstruktionsregeln wird insbesondere das Hauptziel „Werkzeug zur automatisierten und mehrzieloptimierten Bauteilgestaltung“ vorbereitet. Dieses liegt in der Hauptverantwortung des Partners Intes und soll neben bereits am Markt verfügbarer Software zur Topologieoptimierung eine neue Lösung mit zusätzlichen Optimierungsausprägungen darstellen. Während existierende Softwarelösungen bislang lediglich eine belastungsgerechte Auslegung von Bauteilen ermöglicht, wird die avisierte Weiterentwicklung die speziellen Rahmenbedingungen der additiven Fertigung berücksichtigen und zusätzlich die fertigungsgerechte, nachbearbeitungsgerechte und kostengerechte Auslegung von Bauteilen ermöglichen. Weitere Teilziele stellen die Methoden zur strategisch-technischen Bauteilauswahl sowie zur Bauteilkennzeichnung dar. Diese bilden Bestandteile des zweiten Hauptziels, der „Methode zur Integration der additiven Fertigung in bestehende Produktentstehungsprozesse“, und werden im Folgenden näher erläutert.
2 Methode zur Integration der additiven Fertigung im Unternehmen
Mit der Methode zur Integration der additiven Fertigung verfolgt das Konsortium die Entwicklung eines effizienten und beherrschbaren Produktentstehungsprozesses (PEP) für die additive Fertigung. Um im Anschluss an das Forschungsprojekt den Informationstransfer in weitere Unternehmen sicher zu stellen, wurde hierzu eine allgemeine Integrationsmethodik entwickelt, welche im Laufe des Projekts durch weitere Erkenntnisse inhaltlich ausgebaut wird. Die Methodik zur Integration sieht ein Vorgehen in vier Schritten vor, deren Hauptbestandteil die Vereinigung des bestehenden Unternehmensprozesses mit einem idealen AM-orientierten PEP darstellt.
2.1 IST-Analyse des Gesamtprozesses
Bei der IST-Analyse des Gesamtprozesses sind bestehende Prozesse, ähnlich der Einführung nach ISO 9001, auf die Integration vorzubereiten und zu beschreiben [10]. Hierbei werden Prozessbesitzer ernannt, ein Projektteam gebildet und Unternehmensprozesse dokumentiert. In der Integration der additiven Fertigung muss dabei auf drei für den Erfolg der Integration elementar wichtige Rahmenbedingungen geachtet werden: Bei der Bildung des Projektteams und der nachfolgenden Dokumentation sind alle Abteilungen mit direktem Kontakt zur Produktentstehung sowie zukünftig für die additive Fertigung eingeplante Akteure zu berücksichtigen. Auch sollte im Team ein Experte aus dem Bereich der additiven Fertigung mitwirken. Nur so wird gewährleistet, dass Mitarbeiter der Technologieeinführung offen gegenüberstehen und die additive Fertigung nach Abschluss der Integration vollständig im Unternehmen etabliert werden kann. Die Modellierungssprache für die Dokumentation sollte hohe Flexibilität aufweisen und eine klare Darstellung der Prozesse sicherstellen. Mit dem Schwerpunkt auf die grafische Darstellung bieten sich hierzu die „Business Process Modelling and Notation“ oder eine Modellierung nach DIN 66001 an [11]. Wichtigster Aspekt bei der IST-Analyse des bestehenden Prozesses ist allerdings die Wahl des richtigen Detailgrads. Werden Prozesse zu grob dokumentiert, so werden optimale Anknüpfungspunkte des Prozesses später eventuell nicht korrekt gewählt oder gar übersehen. Ist der gewählte Detailgrad zu hoch, wird der zu betreibende Dokumentations- und Analyseaufwand zu groß und die Dokumentation unübersichtlich.
2.2 Definition der PEP-Grenzen
Nach Abschluss der IST-Analyse sind die bestehenden Strukturen für die Integration vorzubereiten. Hierzu werden Schnittstellen des konventionellen PEP definiert, der Prozess von vor- und nachgelagerten Aktivitäten isoliert und aus dem Gesamtprozess entfernt.
Der Wechsel von vorbereitenden Aktivitäten zum konventionellen PEP wird dabei meist durch eine interne Freigabe definiert, ist generell aber vor der Konstruktion anzusiedeln. Der Übergang zu nachfolgenden Arbeitsschritten ist dagegen stärker abhängig von vorhandenen Unternehmensstrukturen. Verfügt das Unternehmen über standardisierte Prozesse zur Qualitätsprüfung in der Produktion, so wird das Ende des PEPs mit dem Übergang in diesen Bereich definiert. Hierbei erfolgt die Anpassung nachgelagerter Prozessaktivitäten erst im vierten Schritt der Einführungsmethodik (vgl. 2.4). Ohne einheitliches Qualitätsmanagement erfolgt die Trennung der Einzelprozesse mit dem Abschluss aller Fertigungs- und Montageaktivitäten. Neben Start und Ende existieren oft Unterbrechungen im PEP (zum Beispiel Konstruktionsfreigabe durch den Kunden). Hier ist durch das Projektteam zu entscheiden, ob diese Prozesswechsel dem spezifischen Fertigungsverfahren zuzuordnen oder generelle Vorgehensweise in der Produktentstehung sind. Gehört eine Unterbrechung zur allgemeinen Produktentstehung, so ist hier ebenfalls eine Trennung vorzunehmen. Um die Definition der PEP-Grenzen abzuschließen, werden die so entstandenen offenen Prozessenden hinsichtlich ihrer Prozesskunden und -lieferanten mit allen Eingangs- und Ausgangsgrößen analysiert und dokumentiert.
2.3 Vereinigung der Prozesse
Die Vereinigung des Gesamtprozesses mit der idealen Produktentstehung der additiven Fertigung stellt den Hauptschritt der Methodik dar. Um hierfür die inhaltlichen Grundlagen bereitzustellen, wird im Rahmen von OptiAMix zunächst ein „idealer AM-PEP“ entwickelt. Dazu wurden im ersten Projektjahr die Produktentstehungsprozesse der Projektpartner Krause DiMaTec, Hirschvogel Tech Solutions und des DMRCs analysiert und dokumentiert. Parallel wurde ein theoretisch idealer Prozess anhand der Vorgaben gängiger Normen und Richtlinien wie der VDI 2221 [12] oder der ISO 9001 [13] entwickelt. Alle Prozesse werden im weiteren Projektverlauf auf Stärken und Schwächen geprüft, in einen einheitlichen Prozess überführt und Ein- sowie Ausgangsgrößen definiert. Mithilfe dieses „idealen AM-PEPs“ werden die bestehenden Prozesse der Partner optimiert und anhand der geplanten Demonstratoren validiert.
Sobald die Entwicklung des idealen AM-PEP abgeschlossen ist, dient dieser als inhaltlicher Bestandteil der Integrationsmethodik.
Hierzu werden die Schnittstellen des idealen AM-PEP mit denen zum Gesamtprozess verbunden und anschließend die zuvor an der definierten Prozessgrenze dokumentierten Ausgangsgrößen mit den Eingangsgrößen der additiven Produktentstehung abgeglichen. Einzelprozesse, deren Informationen im idealen AM-PEP nicht verwertet werden, werden angepasst oder entfernt. Fehlende Eingangsgrößen werden analysiert und dazugehörige Aktivitäten im vorgelagerten Gesamtprozess integriert. Stimmen alle Ausgabe- und Eingabegrößen überein, wird dieselbe Prozedur am Ende des Prozesses durchgeführt bis ein geschlossener Informationsfluss gewährleistet ist. Final sind die Prozessunterbrechungen einzupflegen. Auch hier werden Ein- und Ausgangsgrößen nach Anbindung an den idealen AM-PEP überprüft und notwendige Änderungen eingepflegt.
2.4 Konsolidierung des Gesamtprozesses
Die additive Fertigung stellt keinen unmittelbaren Ersatz anderer Fertigungsverfahren dar. Nicht alle Eigenschaften konventioneller Fertigungsverfahren können durch die additive Fertigung erfüllt, verschiedene Potentiale dafür zusätzlich ausgeschöpft werden. Dementsprechend reicht die reine Integration der additiven Fertigung im PEP nicht aus. Der neue Gesamtprozess muss vom Projektteam hinsichtlich weiterer Einsatzmöglichkeiten aber auch hinsichtlich vorhandener Schwächen weitergehend analysiert werden. Typische Felder für weitere Anbindungspunkte sind dabei die Etablierung der additiven Fertigung als Notfalltechnologie beispielsweise bei Lieferschwierigkeiten von Zukaufteilen. Schwächen stellen beispielsweise das bislang nicht standardisierte Lieferantenmanagement dar. Hierzu muss das Projektteam jeweils Lösungen finden und im Gesamtprozess berücksichtigen. Weiter ist an dieser Stelle nochmals auf das Qualitätsmanagement einzugehen. Sind hierzu Standardprozesse im Unternehmen definiert, so sind hierin verankerte Aktivitäten neu auf die additive Fertigung anzuwenden oder anzupassen.
3 Methoden und Anwendungen entlang der Prozesskette
Mit der Konsolidierung des Gesamtprozesses ist die Integration auf Prozessebene abgeschlossen. Allerdings bringen die Randbedingungen rund um die additive Fertigung weitere Herausforderungen mit sich, für die in OptiAMix Lösungen entwickelt werden. Diese wurden hauptsächlich in den zuvor genannten Projektzielen identifiziert und werden exemplarisch anhand der strategisch-technischen Bauteilauswahl sowie der Methode zur Bauteilkennzeichnung erläutert.
3.1 Strategisch-technische Bauteilauswahl
Die strategisch-technische Bauteilauswahl in OptiAMix baut auf einer vorhandenen Auswahlmethodik der Universität Paderborn auf und wird im Rahmen des Projekts hinsichtlich ihrer branchenübergreifenden Anwendbarkeit weiterentwickelt. Sie ist, bezogen auf den Gesamtprozess, zu Beginn der Produktentstehung in die Designplanungsphase einzuordnen, soll nach und nach aber zu einem Begleittool der Konstruktion weiterentwickelt werden. Aufbauend auf verschiedenen, auf die Funktionalität und das Design ausgerichteten, Fragen dient die Methodik der Unterstützung von Unternehmen beim Screening und der Auswahl geeigneter Bauteile aus dem eigenen Produktportfolio. Hierbei wird das jeweilige Bauteil zunächst in eine Zielkategorie eingeordnet. Diese Kategorien sind die „Änderung des Fertigungsverfahrens“ ohne beziehungsweise mit geringen Designanpassungen, die Optimierung hinsichtlich „Leichtbau“ oder „Funktionsintegration“ oder die „vollständige Potentialausnutzung“. Im Rahmen von OptiAMix erfolgte bereits die Optimierung der bestehenden Fragen für jede dieser Zielkategorien. So konnten die Zusammenhänge einzelner, sich beeinflussender Fragen besser herausgestellt und der Aufwand bei gleichbleibender Analysequalität reduziert werden.
Ist ein Bauteil in eine Kategorie eingeordnet und sind alle Fragen beantwortet, erfolgt die Bewertung basierend auf der jeweiligen Zielkategorie automatisiert. Hierbei wird unterschieden zwischen K.O.-Kriterien, die dem aktuellen Stand der Technik entsprechend eine Umsetzung verhindern sowie wertende Kriterien, welche die Eignung des Bauteils steigern oder senken. Im weiteren Verlauf des Projektes sollen die Gewichtungen der Kriterien auf die Ziele und Bedürfnisse der unterschiedlichen Branchen weiter angepasst werden. So wird die Einsatzbereitschaft der Auswahlmethodik und auch der Potenziale der additiven Fertigung bei Konstrukteuren gesteigert.
3.2 Methode zur Bauteilkennzeichnung
Additive Fertigungsverfahren ermöglichen durch die flexible Produktion basierend auf digitalen Produktdaten die Fertigung individualisierter Produkte. Eine individuelle Bauteilkennzeichnung beispielsweise in Form einer Wort- und Bildmarke, alphanumerischer Zeichenfolgen oder sogar maschinenlesbarer Codes ist eine besondere Art der Individualisierung. Die Chance in der Nutzung der additiven Fertigung besteht nun darin, derartige Kennzeichnungen produktionsintegriert direkt auf oder in einem Bauteil einzubetten. Die Herausforderung besteht jedoch darin, die gewünschte Markierung bereits in die digitalen Bauteildaten zu integrieren und sie fertigungsgerecht zu gestalten. Im Rahmen des Forschungsvorhabens OptiAMix wird diese Fragestellung durch die methodische Analyse geometrischer Elemente und derer Attribute untersucht: Wie muss die Kennzeichnung in einem digitalen 3D-Modell gestaltet sein um eine robuste Lesbarkeit am gefertigten physischen Bauteil zu gewährleisten. Das Ziel dieser Untersuchungen ist die Ableitung von Handlungsempfehlungen für Produktentwickler zum Beispiel in Form einer minimalen Markierungsgröße. Weiterhin gilt es der Fragestellung nachzugehen, wie und wann die Einbettung der Kennzeichnungen in den industriellen Prozessen abzubilden ist und in welchen Prozessschritten eine Kennzeichnung und deren strukturelle Auswirkungen beispielsweise durch Kerbwirkungen berücksichtigt werden müssen.
Gilt es nun, die Kennzeichnung diesen Handlungsempfehlungen folgend in die digitalen 3D-Modelle einzubetten, bieten sich zwei Alternativen: Entweder die manuelle konstruktive Realisierung (alphanumerische Zeichenfolge oder maschinenlesbarer Code) oder die Umsetzung als teilautomatisierte Lösung. Dass der Aufwand für die manuelle Umsetzung überproportional steigt, sobald jedes einzelne Bauteil individuell gekennzeichnet wird, ist offensichtlich.
Daher wird das Projektkonsortium beratend durch die „Additive Marking – Produktionsintegrierte Kennzeichnung GbR“ unterstützt. Als Ausgründung aus der Universität Paderborn bietet Additive Marking eine Softwarelösung zur effizienten Einbettung beliebiger individueller Kennzeichnungen in die digitalen Produktdaten und unterstützt so die Forschungen im Projekt OptiAMix.
3.3 Anwendung der Methoden
Das Potenzial der avisierten Teilziele konnte bereits an einem, durch die Universität in das Projekt eingebrachten, Praxisbeispiel aufgezeigt werden.
Obwohl die konventionell hergestellte Variante der Probenröhrchenstation auf den ersten Blick ungeeignet für die additive Fertigung erscheint, zeigte das methodische Bauteilscreening hohes Potenzial insbesondere in Bezug auf eine mögliche Funktionsintegration. Diese wurde anschließend unter Beachtung AM-spezifischer Konstruktionsregeln im dargestellten Design mit der Integration eines Spülkanals umgesetzt. Durch den eingebrachten Barcode sowie untergeprägte DataMatrix-Codes (Darstellung CT-Scan in Kooperation mit GE Digital Solutions) ist es darüber hinaus nun möglich, Probenröhrchen vollautomatisch einer jeweiligen Station zuzuordnen, wodurch präventiv Mess- und Analysefehler ausgeschlossen werden können.
4 Zusammenfassung und Ausblick
Mit den beschriebenen Methoden und Ausarbeitungen kann der OptiAMix-Verbund bereits heute wichtige Bausteine zur Etablierung der additiven Fertigung liefern. Bereits zu diesem Zeitpunkt des Projektes zeigt sich, dass die Adaption etablierter Vorgehensweisen für die additive Fertigung möglich und die Gesamtprojektziele realistisch und erreichbar sind. Diese werden durch weitere Vertiefung der Methoden zur Bauteilkennzeichnung, Bauteilauswahl und Prozessintegration im weiteren Verlauf des Forschungsprojekts weiterverfolgt und schlussendlich mit der entstehenden Software zur mehrzieloptimierten Bauteilgestaltung zu einem wichtigen Baustein in den Bemühungen der produzierenden Unternehmen, die additive Fertigung optimal in die eigene Produktion zu integrieren.
Literatur
[1] PricewaterhouseCoopers AG: What are the barriers to your company’s inhouse adoption of 3DP?, 3D printing and the new shape of industrial manufacturing, 2014
[2] Spur, G.: Vom Wandel der industriellen Welt durch Werkzeugmaschinen. München: Carl Hanser Verlag 1991
[3] Schulze, F.: Fertigungstechnik. Berlin: Springer Verlag, 8., neu bearbeitete Auflage 2008
[4] Chiarini A.: From Total Quality Control to Lean Six Sigma. Mailand: Springer Verlag 2012
[5] Petrick K.; Graichen F.: Erfolgsweg einer Systemnorm. QZ – Qualität und Zuverlässigkeit (2012) 3, S. 26–28
[6] EFQM Brussels Representative Office: Excellence einführen. Brüssel: EFQM 1999–2003
[7] 3D systems: Unsere Geschichte. Internet: de.3dsystems.com/our-story. Zugriff am 14.03.2018
[8] Meiners W.: Direktes selektives Laser-Sintern einkomponentiger metallischer Werkstoffe. Aachen: Shaker Verlag 1999
[9] DIN 8580: Fertigungsverfahren. Berlin: Beuth Verlag 2003
[10] Füermann T.: Prozessmanagement. München: Carl Hanser Verlag 2014
[11] DIN 66001: Sinnbilder und ihre Anwendung. Berlin: Beuth Verlag 1983
[12] Verein Deutscher Ingenieure: VDI 2221: Methodik zum Entwickeln und Konstruierentechnischer Systeme und Produkte. Berlin: Beuth Verlag 1993
[13] DIN EN ISO 9001: Qualitätsmanagementsysteme – Anforderungen. Berlin: Beuth Verlag 2015
[14] OptiAMix C.I.K.: Internet: http://www.cik.uni-paderborn.de/projekte/industrielle-anwendungen/optiamix/. Zugriff am 20.03.2018
[15] OptiAMix: Internet: http://optiamix.de/projekt/arbeits-paket-8/. Zugriff am 14.03.2018
[16] OptiAMix: Internet: http://optiamix.de/projekt/arbeits-paket-7/. Zugriff am 14.03.2018
[17] Jahnke, U.: Fälschungssichere Produktion: Kennzeichnung zur Rückverfolgbarkeit von additiv gefertigten Bauteilen. In: 3D Printing: Recht, Wirtschaft und Technik des industriellen 3D-Drucks, Hrsg. Andreas Leupold u. Silke Glossner. München: C.H. Beck Verlag 2017
Johannes Büsching, M. Sc. Anne Kruse, M. Sc. Dipl.-Ing. Ulrich Jahnke Prof. Dr.-Ing. Rainer Koch Universität Paderborn / DMRC / C.I.K. Warburger Str. 100, 33098 Paderborn Tel. +49 (0) 5251 / 60-5473 buesching@cik.upb.de www.dmrc.deDr.-Ing. Rinje Brandis Krause DiMaTec GmbH Paul-Schwarze-Str. 5, 33649 Bielefeld Tel. +49 (0) 521 / 4599-06 r.brandis@krause.de www.krause-dimatec.deDas Forschungs- und Entwicklungsprojekt OptiAMix wird mit Mitteln des Bundesministeriums für Bildung und Forschung (BMBF) im Programm „Innovationen für die Produktion, Dienstleistung und Arbeit von morgen“ (Förderkennzeichen 02P15B130 bis 02P15B135) gefördert und vom Projektträger Karlsruhe (PTKA) betreut. Die Verantwortung dieser Veröffentlichung liegt bei den Autoren.