ToolRep
Texturierte Spritzgusswerkzeuge sind aus der Kunststoffverarbeitung nicht mehr wegzudenken. Auf die Beschädigung einer Textur folgen Ausfallzeiten, teure Reparaturen bis hin zum Totalausfall des Werkzeugs. Ziel des vom BMBF geförderten Projektes „ToolRep“ war es, die gesamte Reparaturkette in einer prototypischen Anlage abzubilden. Texturfehler werden automatisch erkannt und selektiert, mittels additivem Laserauftrag gefüllt und mittels spezieller Reparaturalgorithmen und Lasergravur wiederhergestellt.
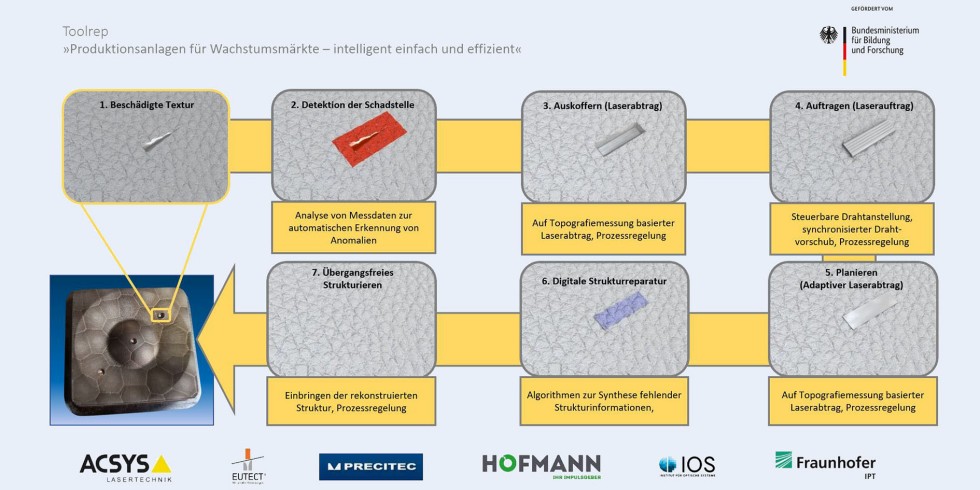
Bild 1. Darstellung der maschinellen Einzelprozesse in der automatisierten laserbasierten Reparatur texturierter Werkzeugeinsätze.
Foto: Acsys Lasertechnik
Toolrep. Development of a system for the automated laser-based repair of structured mould inserts
Textured injection moulding tools have become indispensable in plastics processing. Damage to a texture is followed by downtimes, expensive repairs and even total tool failure. The aim of the BMBF-funded „Toolrep“ project was to map the entire repair chain in a single system. Texture errors are automatically detected and selected, filled by means of additive laser application and restored by means of special repair algorithms and laser engraving.
1 Industrielle Rahmenbedingungen
Kunststoffspritzgießen ist eines der wichtigsten Verfahren zur Serienherstellung von Kunststoffprodukten und stellt weltweit einen hoch-dynamischen Wachstumsmarkt dar, unter anderem wegen der werkzeugseitig stetig verbesserten Möglichkeiten, immer komplexere Oberflächentexturen und Bauteilkonstruktionen abzubilden. Wird jedoch eine Spritzgießform während des Einsatzes beschädigt, hat dies bei einer Just-in-time-Produktion weitreichende Folgen. Die schnelle Reparatur einer beschädigten Form ist daher zwingend erforderlich. Bestehende Reparaturlösungen, die überwiegend auf manuellen Arbeitsschritten beruhen, erreichen oftmals nicht die geforderten Qualitäten und Zeiten. Die Reparatur von oberflächenstrukturierten Spritzgießformen stellt daher eine besondere Herausforderung dar. Es existiert bislang kein Maschinensystem, das eine vollständige Prozesskette zur automatisierten Reparatur solcher Spritzgießformen abbildet und auf dieser Basis die geforderten Bearbeitungszeiten und hohe, versatzfreie Strukturqualitäten erlaubt.
2 Das Projekt „ToolRep“
Bisherige manuelle Arbeitsschritte zur Reparatur eines Spritzgusswerkzeuges beruhen auf der visuellen Inspektion der Werkzeugoberfläche, der Detektion der Schadstelle, dem Ausschleifen und anschließendem Verschließen der Oberfläche sowie, wenn möglich, dem händischen Neutexturieren. Diese Prozesskette (Bild 1) sollte im Ergebnis des Projekts ToolRep vollautomatisiert innerhalb einer Anlage erfolgen. So wurde eine Messtechnik benötigt, welche hochaufgelöst Oberflächendaten des Werkzeugs und der Textur erfassen kann. Außerdem war ein Softwarealgorithmus notwendig, welcher Anomalien in der Oberflächenbeschaffenheit detektiert. Der schadhafte Bereich sollte dann mittels Lasertiefgravur abgetragen werden, um eine definierte ebene Grundfläche zu schaffen. Im Anschluss sollte die Kavität mittels additivem Laserauftrag geschlossen und über die Texturebene hinaus aufgefüllt werden. Ein Erfassen der entstandenen Oberflächengeometrie sowie spezielle Rechenalgorithmik ermöglichen die Bestimmung einer neuen Texturoberfläche, welche folgend mittels Lasergravur erzeugt werden kann. Auf Basis der umliegenden Textur erzeugt dann eine Software Daten, mit denen mittels Laserabtrag eine reparierte Textur erzeugt werden kann.
Für diesen neuen Prozessablauf wurden der Forschungs- und Entwicklungsbedarf in den Bereichen Messtechnik, Maschinenbau, Laserprozessregelung, additiver Fertigung und 3D-Bahnplanung identifiziert und entsprechende Lösungsansätze formuliert. Die Forschungs- und Entwicklungsarbeiten erfolgten in den Jahren 2015 bis 2019 im Verbundvorhaben ToolRep, welches im Rahmen des BMBF-Wettbewerbs „Produktionsanlagen für Wachstumsmärkte – intelligent einfach und effizient“ gefördert wurde.
2.1 Das Projektteam
Das Konsortium des Verbundprojekts ToolRep bestand aus sechs Partnern aus Industrie und Forschung. Jeder Partner konnte in seinem Fachbereich langjährige Expertise vorweisen. Die Acsys Lasertechnik GmbH ist auf dem Markt ein etablierter, in verschiedenen Anwendungsbereichen technologisch führender Hersteller von Laserbearbeitungsanlagen und brachte eine breite anlagen- und laserprozesstechnische Expertise in dieses Vorhaben ein. Daher besetzte das Unternehmen die Funktion des Technologieintegrators und Projektleiters. Darüber hinaus boten die umfangreichen Erfahrungen aus den Bereichen Lasergravur, Laserschweißen und Oberflächenerfassung sehr gute Voraussetzungen für die qualitativ optimale Parametrierung und Abstimmung der Bearbeitungs- und Messprozesse in einer hybriden Laseranlage. Das Unternehmen Euctect GmbH ist spezialisiert auf dem Gebiet der Drahtfördertechnik und brachte eine über 20-jährige Erfahrung im Maschinenbau ein. Seit 1998 werden von Euctect Löt- und Verbindungssysteme entwickelt, gefertigt, montiert, programmiert und bei Kunden weltweit in Betrieb genommen. Das „SWF-AS“-Modul von Euctect dient der kraftgeregelten Drahtzufuhr mit integrierter Begasung für Auftragsschweißanwendungen. Die Precitec Optronik GmbH stellt Sensorik und Komplettsysteme zur Abstands-, Topografie- und Schichtdickenmessung her. Die Messtechnik wird außer in medizintechnischen Anwendungen als integriertes Gesamtsystem auch in vielen produzierenden Unternehmensbereichen verwendet. Die Erfahrung der Werkzeugbau Siegfried Hofmann GmbH bezüglich der Anforderungen an Formeinsatzoberflächen und -qualitäten sowie der Kunststoffprodukte, die mit diesen Formeinsätzen produziert werden, bildet die für die Evaluierung des Reparaturergebnisses erforderliche Basis. Das Institut für optische Systeme der HTWG Konstanz (IOS) hat sich vor allem auf die Bereiche kognitive Systeme, geometrisches Modellieren sowie Bildverarbeitung spezialisiert. Die gleichnamigen Arbeitsgruppen unter der Leitung von Prof. Dr. Matthias Franz und Prof Dr. Georg Umlauf haben in allen für die Textursynthese wichtigen Teilbereichen bereits wissenschaftliche Vorarbeiten geleistet. Im Fraunhofer-Institut für Produktionstechnologie (IPT) entwickeln die Mitarbeiterinnen und Mitarbeiter neue Fertigungsverfahren, innovative Fertigungsmesstechnik sowie entsprechende Anlagen- und Maschinenkonzepte. Die im Vorhaben adressierten Themen Maschinenbau, Messtechnik, die Lasertechnologien „Laserstrukturieren“ und „Laserauftragsschweißen“ sowie Softwareentwicklung mit Schwerpunkt CAM-Entwicklung sind Kompetenzfelder des Fraunhofer IPT.
2.2 Wesentliche Projektergebnisse
Ausgangspunkt für alle Schritte des automatisierten Reparaturprozesses ist die Inspektion der Werkzeugoberfläche. Während sie beim manuellen Prozess klassisch visuell erfolgt, wurde im Projekt eine Möglichkeit geschaffen, die Oberfläche hochaufgelöst zu digitalisieren und die erzeugten Daten für die weitere Bearbeitung zur Verfügung zu stellen.
In diesem Zusammenhang konnte die Precitec Optronik GmbH gemeinsamt mit dem Fraunhofer IPT ein Messgerät auf Basis eines interferometrischen Sensors entwickeln, welches sich mithilfe einer Lichtleitfaser in den Strahlweg des Gravurlasers einkoppeln lässt (Bild 2) und somit durch den Laserbearbeitungskopf die gleiche Oberfläche sieht wie der fokussierte Laserstrahl.
Dies erlaubt eine Oberflächenerfassung an der und um die Defektstelle sowie eine In-situ-Messung der beim Auskoffern und Planieren abgetragenen Oberfläche mit Validierung des Reparaturergebnisses. Aufgrund der Faserkopplung kann der eigentliche Sensor weit entfernt vom geschädigten Werkzeug und der Materialbearbeitung positioniert werden. Somit gibt es kaum geometrische Einschränkungen am Laserbearbeitungskopf sowie keine Bauteil- oder Achsbewegungen zwischen den Gravur- und Messschritten.
Basierend auf den gesammelten Daten kann die Analyse der Oberflächentextur stattfinden. Diese ist Ausgangspunkt für die Defektdetektion und die spätere Textursynthese. Die Textur unterscheidet sich in ihrer Tiefe stark vom eigentlichen Spritzgusswerkzeug. Im Gegensatz zu dessen eher dreidimensional makroskopischen Form, welche sich auf Basisgeometrien, beispielsweise Quadern oder Kugeloberflächen [1] reduzieren lässt, kann die Textur eher als Mikrostruktur betrachtet werden und muss für die weitere digitale Datenverarbeitung von der Makrogeometrie getrennt werden. Während die Makrogeometrie für die spätere Berechnung der Bearbeitungsposition bei der Lasergravur oder der Werkzeugbahnvektoren beim späteren additiven Schweißprozess relevant ist, wird die Mikrostruktur anhand ihrer Strukturmerkmale und deren Anordnung an der Oberfläche analysiert. Diese Strukturmerkmale können geometrisch absolut identisch und künstlichen Ursprungs mit absolut periodischer Anordnung sein oder natürlich mit individuellen Merkmalen gewachsen und absolut zufällig angeordnet sein. Zudem existieren Mischformen. Klassische Beispiele sind Bienenwaben, Ziegelmauern, gewebte Stoffe oder Ledernarbungen (Bild 3).
Die am IOS entwickelte intelligente und selbstlernende Software bewertet die genannten Merkmale sowie deren Ausprägung und erkennt Abweichungen als möglichen Defekt. Bei der Reparatur des Werkzeugeinsatzes werden dann diese Merkmale im defekten Bereich in gleicher Form und Ausprägung wie im gesunden Bereich weitergeführt und in die Oberfläche integriert [2]. Ausgabegrößen sind also final die Defektgeometrie sowie die Zieltextur.
Nachdem die Defektgeometrie bekannt ist, kann eine entsprechende Tasche in die Werkzeugoberfläche graviert werden. Es wird ein Volumenmodell generiert, welches mithilfe eines „Slicers“ in einzelne Schichten zerlegt und nacheinander abgetragen wird. Die Schichtdicken sind abhängig von den verwendeten Laserparametern. Während beim Auskoffern und Planieren das Augenmerk auf maximalem Materialaustrag liegt, werden beim Texturieren deutlich sanftere und damit weniger produktive Laserparameter verwendet. Folglich kann eine deutlich glattere Oberfläche erzeugt werden. Hierfür und auch für die spätere Einbringung der Textur kommt ein klassischer ns-Faserlaser mit einer Leistung von 70 Watt zum Einsatz, welcher mittels Galvanometerscanner über das Material gelenkt wird. Während im Bereich der Gravur auf die jahrelange Erfahrung der Firma Acsys zurückgegriffen werden konnte, musste Acsys zusammen mit der Firma Euctect den kraftgeregelten Drahtvorschub, der für Lötpunkte und Laserschweißungen in der Ebene entwickelt wurde, in die 3D-Fähigkeit überführen und den Laserschweißprozess im Raum etablieren. Um eine fehlerfreie Kraftmessung und gleichbleibende Schweißergebnisse auch auf gewölbten Oberflächen zu gewährleisten, wurde die Vorschubachse mit einem hochauflösenden Lagemesssystem und mit coggingarmen Lineardirektantrieben ausgestattet, der Drahtvorschub vom Drahtlager entkoppelt und eine zyklische Abtastung der Lage der Vorschubeinheit implementiert. Zur Steigerung der Dynamik und Sensitivität war es möglich, das SWF-Modul kompakter und leichter zu gestalten sowie die Ab-tastrate des Kraftsensors deutlich zu erhöhen. Des Weiteren konnte von Acsys ein Modul zur pulssynchronen Laserleistungsregelung entwickelt werden und damit der Wärmeeinfluss und die Spritzerbildung sowie die Schädigung und Umschmelzung der „gesunden“ Textur minimiert werden.
Zum Ende des Projektes wurden die entstandenen Baugruppen in einem Systemdemonstrator (Bild 4) zusammengeführt.
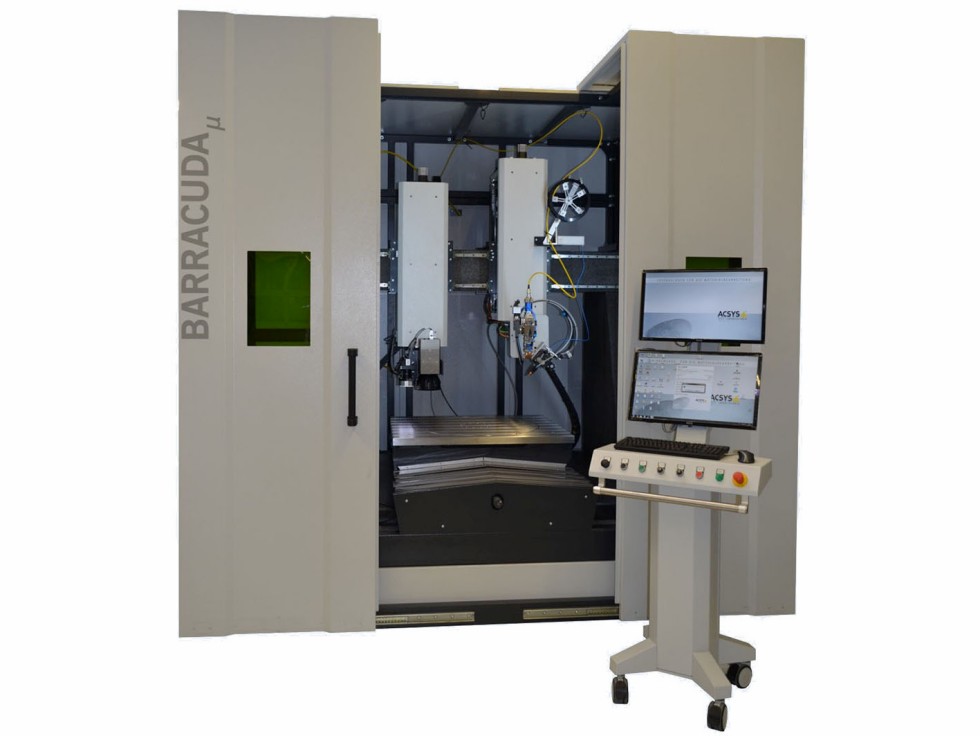
Bild 4. Anlagendemonstrator mit integrierter Messtechnik, Lasergravur‧system, Laserschweißsystem und kraftgeregelter Drahtvorschub.
Foto: Acsys Lasertechnik
Auf einem massiven Granitbett wurden die getrennten Prozesse Lasergravur zusammen mit der optischen Messtechnik und das additive Laserschweißen mit kraftgeregelter Dünndrahtzufuhr in einer 3D-fähigen Präzisionsanlage vereint. Da sich beide Laserprozesse sowohl in der Laserquelle als auch in den Bearbeitungsköpfen unterscheiden, wurden diese Systeme an getrennten Z-Achsen aufgehängt und können unabhängig voneinander über der Bauteiloberfläche positioniert und entlang der Bearbeitungsbahnen interpoliert werden. Alle Linear- und Drehachsen wurden mit hochaufgelösten Lagemesssystemen ausgestattet und haben eine Positioniergenauigkeit von wenigen Mikrometern. Es können Werkzeugeinsätze mit einer Dimension von bis zu 400 x 400 x 300 mm³ und einem Gewicht von bis zu 500 kg bearbeitet werden.
Gesteuert wird die Anlage vom am IPT entwickelten „Calm“-Modul (Computer-aided Laser Manufacturing). Dieses besitzt eine Schnittstelle zur Messtechnik sowie zur Steuerung des Gravurlasers mit Bearbeitungskopf und zur CNC-Achssteuerung sowie zum Schweißlaser mit kraftgeregeltem SWF-Modul. Des Weiteren sind die Defektdetektionsalgorithmen, die Textursynthese und die Kinematik des Demonstrators implementiert. So ist es möglich, auf Basis der Werkzeuggeometrie und der gemessenen Oberfläche die zur Reparatur notwendigen Bahnvektoren zu berechnen und über die Achsen oder den Bearbeitungskopf auszugeben. Zur Sicherstellung der korrekten Abtragtiefe wurde eine Prozessregelung entwickelt, die sich auf Basis der gemessenen Oberflächentopologie Prozessparameter anpasst [3]. Ebenso können zyklische Zwischenmessungen der abgetragenen Oberfläche durchgeführt werden und eventuelle Fehlabträge durch Anpassung der Laser- oder Slicingparameter korrigiert werden. Softwareseitig können also alle Prozesseinzelschritte (Bild 5) abgebildet werden.
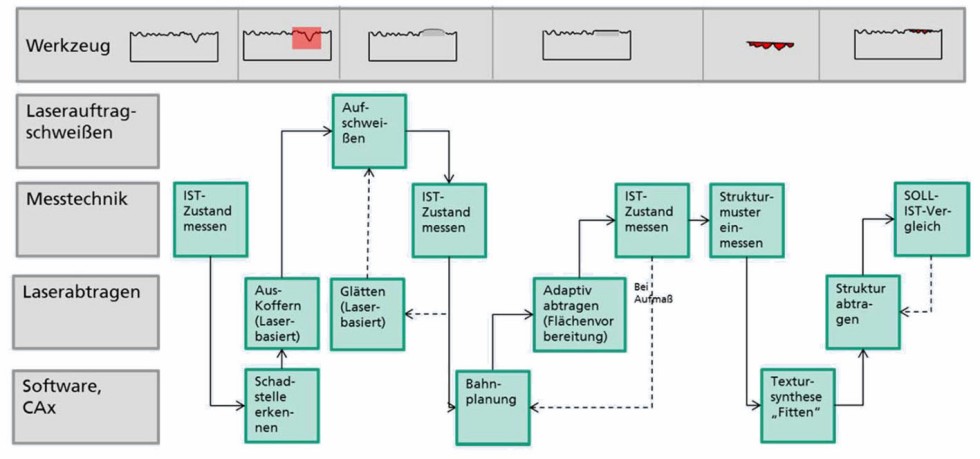
Bild 5. Struktureller Ablauf der automatisierten Werkzeugreparatur innerhalb der „Calm“-Software vom Fraunhofer IPT.
Foto: Acsys Lasertechnik GmbH
3 Fazit und Ausblick
Im Verbundprojekt ToolRep konnte das Konsortium nachweisen, dass die ganzheitlich laserbasierte Reparatur von texturierten Werkzeugeinsätzen in einem komplexen Anlagensystem in seinen einzelnen Prozessschritten abgebildet werden kann. Vor allem die Erzeugung einer neuen Textur in einem geschädigten Oberflächenbereich auf Basis der umgebenden Strukturen mittels intelligenter und selbstlernender Softwarealgorithmen sowie die maschinelle Einbringung in ein Werkzeug bietet in Zeiten von Fachkräftemangel und immer weniger werdenden händischen Prozessen ungeahnte Möglichkeiten. Auch die automatische Erzeugung bionisch funktionaler Oberflächen nach Vorbild „gescannter“ natürlicher Texturen sind denkbar. Die vollständige Automatisierung konnte im Rahmen der Laufzeit des geförderten Vorhabens noch nicht umgesetzt werden. Auf der Basis der vorhandenen Projektergebnisse arbeitet das Konsortium weiter an einer Steigerung der Zuverlässigkeit der gesamten Prozesskette. Hierfür sind umfangreiche Tests an unterschiedlichen Werkzeuggeometrien und Oberflächenstrukturen notwendig. Außerdem soll der Funktionsumfang der Anlage weiter erhöht werden. Weitere realistische Ziele sind zum Beispiel die zusammenhängende Texturierung großformatiger Werkzeugoberflächen oder die Reparatur polierter Werkzeuge. Hier sind aktuell noch Grenzen durch Übersteuerung des optischen Sensors gesetzt sowie die ansatzfreie Laserpolitur limitierend.
Dieses Forschungs- und Entwicklungsprojekt wurde mit Mitteln des Bundesministeriums für Bildung und Forschung (BMBF) im Programm „Innovationen für die Produktion, Dienstleistung und Arbeit von morgen“ (Förderkennzeichen 02P14A030 bis 02P14A035) gefördert und vom Projektträger Karlsruhe (PTKA) betreut. Die Verantwortung für den Inhalt dieser Veröffentlichung liegt beim Autor.
Literatur
- Laube, P.; Franz, O.; Umlauf, G.: Evaluation of features for SVM-based classification of geometric primitives in point clouds, Machine Vision Applications (MVA), 2017 15th IAPR International Conference on: IEEE, pp. 59–62
- Laube, P.; Grunwald, M.; Franz, O. et.al.: Image Inpainting for High-Resolution Textures using CNN Texture Synthesis, Computer Graphics and Visual Computing (CGVC), Swansea UK, Eurographics Association, 2018
- Pothen, M.; Henrichs, O.: Integration of a Smart Measurement Device in the Laser Structuring Process Chain to Ensure High Quality; ICALEO Conference Proceedings; 2017
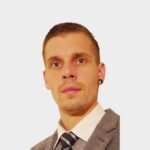
Dipl. Ing. (FH) Christian Kreisel
Foto: Autor
Acsys Lasertechnik GmbH
Leipziger Str. 37, 09648 Mittweida
Tel. +49 (0) 3727 / 996909-24
c.kreisel@acsys.de
www.acsys.de