MIM – höhere Oberflächengüte bei geringeren Rohstoffkosten
In diesem Beitrag wird ein innovatives Verfahren für die Verbesserung des Metallpulverspritzgusses (MIM, Metal Injection Molding) vorgestellt. Die Bauteile werden einem am Fraunhofer IFAM in Zusammenarbeit mit der MUT Advanced Heating GmbH weiterentwickelten elektrochemischen Reduktionsverfahren unterzogen. Infolgedessen konnten feinere Ausgangspulver mit erhöhtem Sauerstoffgehalt eingesetzt werden. Gleichzeitig war es der Firma Element 22 möglich, die Entwicklung des MIM-Feedstocks auf die Bauteilqualität und Verarbeitbarkeit zu optimieren, ohne einen möglichen Sauerstoffeintrag aus dem Prozess berücksichtigen zu müssen. Das Ergebnis sind Titanbauteile höchster Oberflächengüte innerhalb der geforderten Norm.
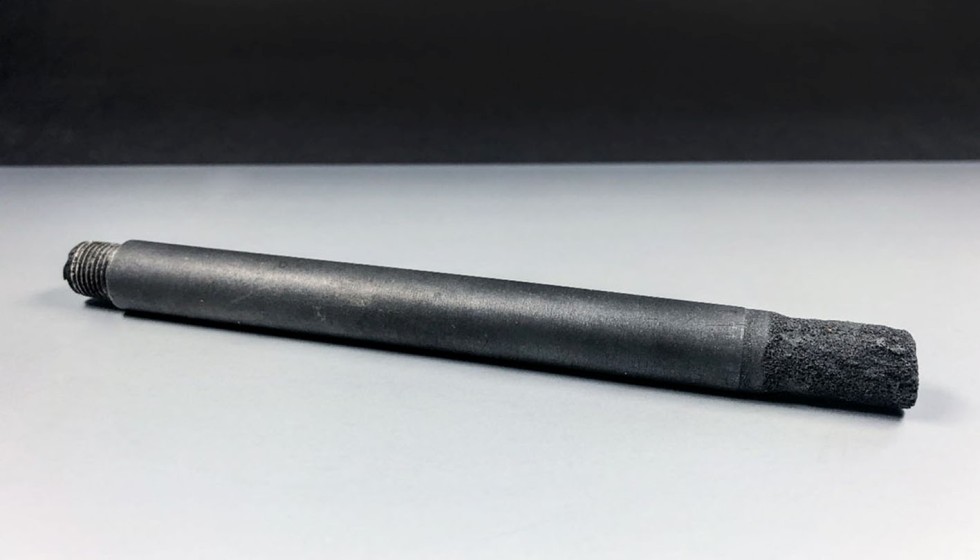
Bild 5. Ursprünglich verwendete Graphitanode zum Einschrauben mit ‧starkem chemischen Angriff des Graphits im Eintauchbereich in das Salz auf der rechten Seite.
Foto: Fraunhofer IFAM
Ausgabe 1/2-2022, S. 103
1 Einführung
Global betrachtet werden medizintechnische Produkte, wie etwa Implantate, zumeist aus dem Vollen zerspant. Damit ist es relativ einfach, den hohen Anforderungen an die Werkstoff- und Oberflächeneigenschaften gerecht zu werden. Werkstoffe wie das Titan und seine Legierungen werden dabei aufgrund ihrer hohen Biokompatibilität und Korrosionsbeständigkeit bevorzugt eingesetzt. Eine alternative Fertigungsmethode, die ohne oder mit minimaler spanender Nachbearbeitung auskommt, ist der Metallpulverspritzguss (MIM, Metal Injection Molding). Dieses Verfahren wird vom Projektpartner Element 22 erfolgreich eingesetzt. Hier bestehen aber, um den hohen Ansprüchen an Medizinprodukte gerecht zu werden, noch weit höhere Ansprüche an das Ausgangsmaterial. Dies betrifft insbesondere den maximalen Sauerstoffgehalt des verwendeten Titanpulvers. Die Folge dieser Anforderungen sind zum einen hohe Kosten und zum anderen eine Mindestpartikelgröße der Pulverteilchen. Ursache dafür ist die dünne Schicht aus Titanoxid auf jedem Pulverteilchen, die zwar ein wesentlicher Grund für die hervorragende Biokompatibilität des Titans ist, gleichzeitig bei pulvermetallurgischen Prozessen im Produkt verbleibt und dort (besonders bei kleinen Partikeln als Ausgangsmaterial und damit in Summe hohem Oxidgehalt, siehe Bild 1) zu nicht akzeptablen Verunreinigungen und in Folge zu Versprödung führt.
![Bild 1. Der Sauerstoffgehalt von pulvermetallurgisch hergestellten Titanbauteilen steigt bei abnehmender Teilchengröße exponentiell an, da die Dicke der Oxidschicht abhängig vom Herstellungsprozess konstant circa 2 – 10 nm beträgt [1]. Grafik: Fraunhofer IFAM](https://www.ingenieur.de/wp-content/uploads/2022/02/WBK-BMBF-Projekt-Spitzentitan-Bild-1-1.jpg)
Bild 1. Der Sauerstoffgehalt von pulvermetallurgisch hergestellten Titanbauteilen steigt bei abnehmender Teilchengröße exponentiell an, da die Dicke der Oxidschicht abhängig vom Herstellungsprozess konstant circa 2 – 10 nm beträgt [1]. Grafik: Fraunhofer IFAM
Gleichzeitig ist ein Prozess für die Herstellung von Titanpulvern aus Titanoxid bekannt (FFC-Cambridge-Prozess [2]). Am Fraunhofer Institut für Fertigungstechnik und angewandte Materialforschung IFAM in Dresden konnte dieses Verfahren auch für fertige Bauteile eingesetzt werden. Entsprechend der Darstellung in Bild 2 reduziert in diesem Prozess Kalzium aus einer Kalziumchloridschmelze das Titanoxid, da das entstehende Kalziumoxid thermodynamisch stabiler ist.
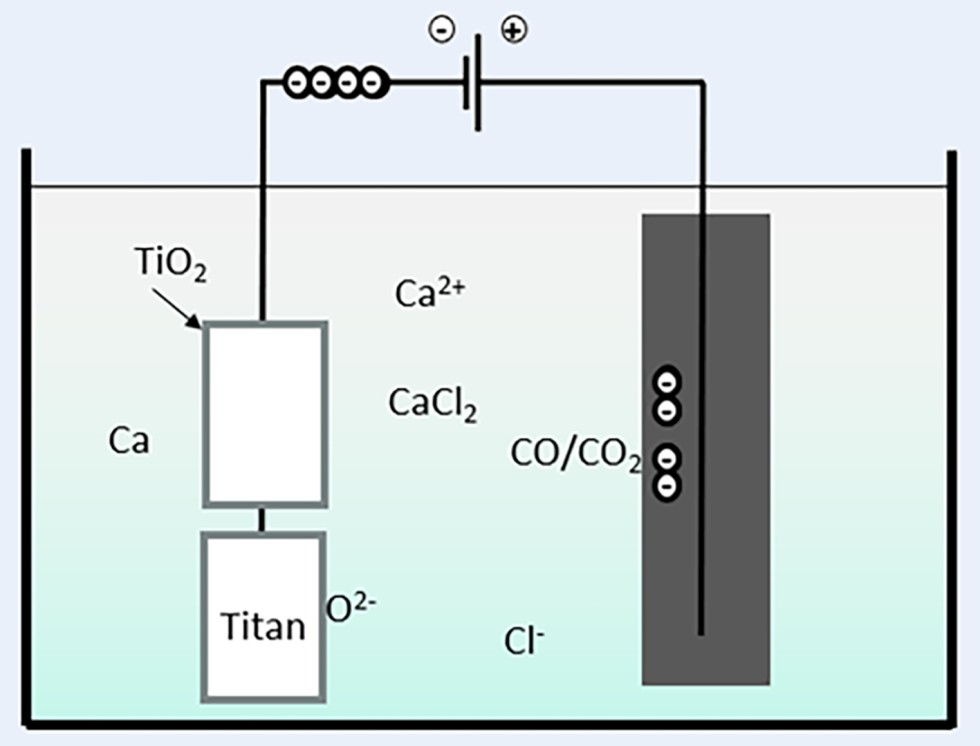
Bild 2. Schematische Darstellung einer Reaktionskammer zur Nachreinigung von Titanbauteilen. Grafik: Fraunhofer IFAM
Letzteres dissoziiert anschließend im angelegten elektrischen Feld und das Sauerstoffion wandert daraufhin zur Anode, wo es als Sauerstoff oder Kohlenstoffdioxid entweicht, nachdem es seine überschüssigen Elektronen an die Anode abgegeben hat. Das Kalzium steht für eine erneute Reduktion weiteren Titanoxids zur Verfügung, sobald das Kalziumion an der Kathode (dem Titanbauteil) zwei Elektronen aufgenommen hat. Mit dieser Methode konnte der Ausgangssauerstoffgehalt der Titanbauteile von 0,5 M% in weniger als 10 Stunden um 90 % reduziert und die Bruchdehnung auf bis zu 19 % gesteigert werden.
Kritisch an dem Prozess ist die potenzielle Aufnahme von Verunreinigungen, vor allem durch Kohlenstoff. Dieser stammt aus den zunächst verwendeten Graphitanoden und diffundiert an die Produkte. Über eine verbesserte Zellanordnung, optimierte Prozessparameter hinsichtlich Temperatur und elektrischer Spannung für den Reduktionsprozess, sowie durch gezielte Auswahl geeigneter Werkstoffe konnten diese Verunreinigen auf Werte innerhalb der Normanforderungen reduziert werden, sodass die Eignung des Verfahrens für die Nachreinigung von Bauteilengezeigt wurde.
2 Ergebnisse
Die Technologieentwicklung wurde in einem experimentellen Laborofen durchgeführt. Dieser erlaubt Prozesstemperaturen bis 1000 °C im Dauerbetrieb und wurde mit Argon-Schutzgas betrieben (Taupunkt < -90 °C). Dabei wurden zunächst Titanbleche mit einer Dicke von 1 mm als Testobjekte verwendet. Die Entwicklung des Sauerstoffgehalts der Bleche ist in Bild 3 dargestellt.
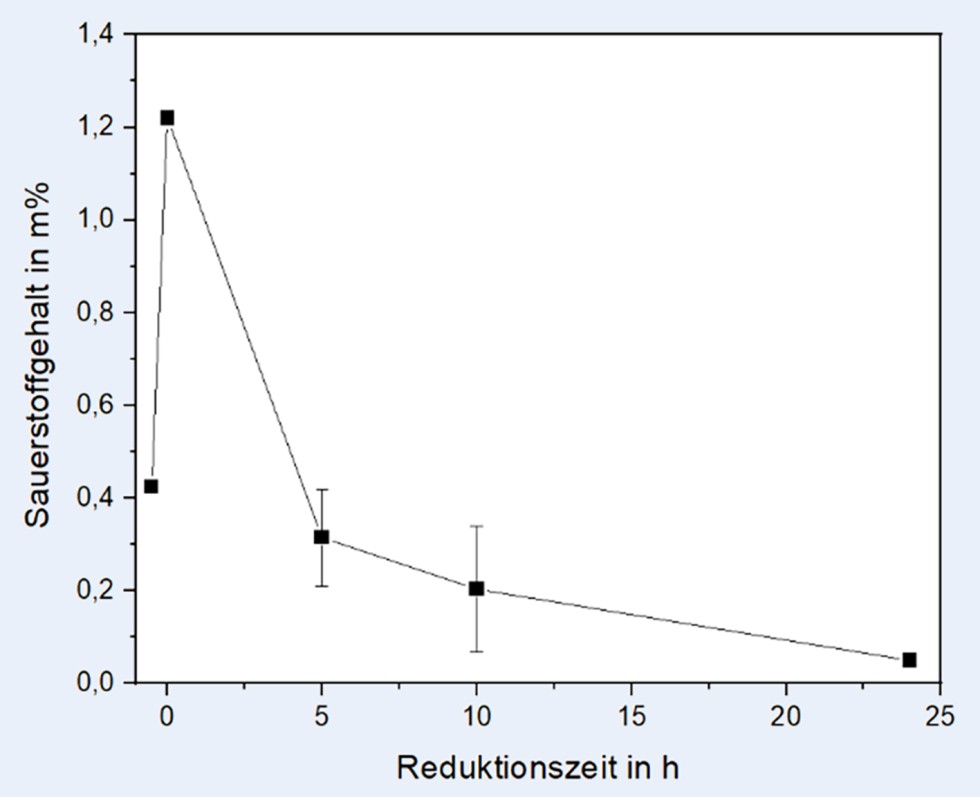
Bild 3. Entwicklung des Sauerstoffgehaltes von Versuchsblechen mit der Prozesszeit. Die anfängliche Steigerung ist auf den experimentellen Aufbau zurückzuführen und tritt in der Industrievariante des Ofens nicht mehr auf. Entsprechend verkürzt sich dann auch die notwendige Gesamtdauer des Prozesses. Grafik: Fraunhofer IFAM
An den Ergebnissen lässt sich erkennen, dass sich der Sauerstoffgehalt der Proben konstruktionsbedingt zunächst stark erhöht, da diese beim Aufheizen trotz Schutzgas den Restsauerstoff der Atmosphäre aufnehmen. Dies wurde in dem für das Projekt von der Firma MUT Advanced Heating entwickelten Industrieofen über eine Kaltzone gelöst, in der sich die Titanteile während des Aufheizvorgangs des Ofens befinden. Anschließend verringert sich der Sauerstoffgehalt nach Anlegen der Spannung und Eintauchen der Proben in die Salzschmelze innerhalb von 24 Stunden auf weniger als 0,06 M%. Auch an Proben aus Titan6Aluminium4Vanadium wurde erfolgreich der Sauerstoffgehalt auf die Anforderungen von „Grade 5“, also unter 0,2 M%, reduziert.
Allerdings bildeten sich zunächst oberflächlich Kohlenstoff oder TiC Schichten, wie es die Aufnahme mit dem Rasterelektronenmikroskop in Bild 4 zeigt [3].
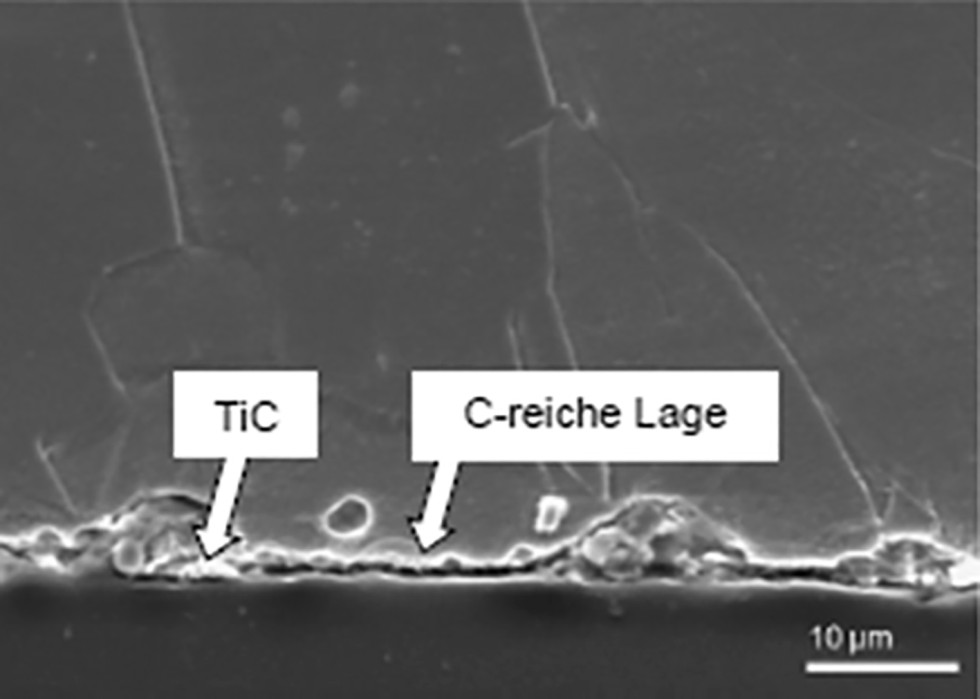
Bild 4. Kohlenstoffreiche Lage und Bildung einer Titankarbidschicht an der Oberfläche der Probenbleche. Grafik: Fraunhofer IFAM
Gelöst wurde das Problem zum einen durch konstruktive Maßnahmen, indem innerhalb der Prozesskammer alle Proben stets einen Mindestabstand von einem Zentimeter zu den Graphitanoden hatten. Damit konnte die Bildung von TiC verhindert werden. Die Reduktion der Verunreinigungen mit Kohlenstoff auf ein Minimum gelang schließlich durch den Ersatz der Graphitanode, die, wie Bild 5 zeigt, durch chemischen Angriff schnell aufgelöst wird. Verwendet wurde nach umfangreichen Versuchen mit Oxiden von Eisen und Nickel verschiedener Zusammensetzungen ein kommerziell erhältlicher Glaskohlenstoff. Dessen dichte, amorphe Struktur widersetzt sich einem Angriff für mehrere hundert Stunden.
Beachtet werden muss bei der vorgestellten Nachreinigungsroute die exakte Einstellung der elektrischen Spannung zwischen den beiden Elektroden. Während bei zu geringer Spannung noch keine anhaltende Reduktion des Sauerstoffgehalts im Titan stattfindet, da Kalziumoxid nicht dissoziiert, ist der Übergangsbereich bis zur Bildung von Chlorgas schmal und durch einen steilen Anstieg der Stromstärke gekennzeichnet.
An Zugversuchsproben aus 2 mm starken Blechen aus Titan6Aluminium4Vanadium wurden die mechanischen Eigenschaften des Materials bestimmt. Die ermittelten Werte der Dehnung 17,5±1,5 % sowie der einer Dehngrenze Rp0,2 von 835±1 MPa liegen ebenfalls innerhalb der Anforderung.
3 Zusammenfassung
Aus den vorgestellten Ergebnissen des vom Bundesministerium für Bildung und Forschung geförderten Projekts „Spitzentitan“ wird ersichtlich, dass die Verwendung von feinem und dennoch günstigem Ausgangspulver für das Metallpulverspritzgießen möglich ist, wenn die so hergestellten Produkte einem nachfolgenden Reduktionsprozess unterzogen werden. Der Sauerstoffgehalt sinkt dabei durch elektrochemische Reduktion von 0,5 M% auf unter 0,2 M% und erfüllt somit die Anforderungen an einen Werkstoff nach Grade 5. Auch die mechanischen Kennwerte liegen innerhalb des Anforderungsbereichs. Kritisch ist hierbei nicht nur die Einstellung der elektrischen Spannung innerhalb eines sehr engen Bereichs, sondern auch die Positionierung der Elektroden innerhalb der Reduktionskammer. Entscheidend ist zudem die Auswahl des Anodenmaterials, um eine unerwünschte Verunreinigung mit Kohlenstoff zu vermeiden.
4 Ausblick
Auch wenn die Ergebnisse bereits vielversprechend für den industriellen Einsatz des Prozesses sind, werden bereits weitergehende Arbeiten geplant. Diese betreffen besonders die Verwendung einer vollständig inerten Anode aus einem keramischen Material. Dies soll nicht nur die Prozessstabilität weiter erhöhen und eine Übertragung auf weitere Materialien mit hohen Anforderungen an den maximalen Sauerstoffgehalt vereinfachen. Die Technologie wird auch für einen Einsatz im Weltraum erprobt, wo auf Langzeitmissionen Sauerstoff aus Mond- oder Marsgestein erzeugt werden soll [4].
Das Forschungs- und Entwicklungsprojekt „Spitzentitan” wird durch das Bundesministerium für Bildung und Forschung (BMBF) in der Fördermaßnahme „KMU-innovativ: Produktionsforschung” (Förderkennzeichen 02P17K510 bis 02P17K512) gefördert und vom Projektträger Karlsruhe (PTKA) betreut. Die Verantwortung für den Inhalt dieser Veröffentlichung liegt bei den Autoren.
Literatur
- Jurisch, M.; Studnitzky, T.; Andersen, O.; Kieback, B.: Proceedings of the World PM2016, Vol. 2016 (Eds: EPMA), EPMA 2016
- Chen, G.; Fray, D. J.; Farthing, T. W.: Nature 407 (2000), (6802), pp. 361–364. DOI: 10.1038/35030069
- Jurisch, M.: Untersuchung der Herstellung von mikrostrukturierten Titanbauteilen mit dem 3D-Siebdruck-Verfahren. Dissertation Technische Universität Dresden
- Airbus Pressemitteilung „ROXY turns Moon dust into oxygen“. Internet: www.airbus.com/newsroom/press-releases/en/2020/10/roxy-turns-moon-dust-into-oxygen.html. Zugriff am 27.10.2021
Dr.-Ing. Johannes Trapp
Marie Franke-Jurisch
Fraunhofer-Institut für Fertigungstechnik
und Angewandte Forschung IFAM
Winterbergstr. 28, 01277 Dresden
Tel. +49 351 / 2537300
info@ifam-dd.fraunhofer.de
www.ifam-dd.fraunhofer.de
Peer Geisenhainer
MUT Advanced Heating GmbH
Fritz-Winkler-Str. 1–2, Jena
Tel. +49 3641 / 56560
mut@mut-jena.de
www.mut-jena.de
Florian Gerdts
Element 22 GmbH
Wischhofstr. 1–3, 24148 Kiel
Tel. +49 431 / 6594610
info@element22.com
www.element22.de