Intelligente Vernetzung für die Fräsbearbeitung
Im Forschungsprojekt „TensorMill“ wird die Umsetzung einer intelligent vernetzten autonomen Fertigung von sicherheitsrelevanten Bauteilen in der Luftfahrtindustrie angestrebt. Dabei soll mithilfe von Künstlicher Intelligenz (KI) auf möglichst viele Situationen im Fertigungsprozess reagiert werden. Dies dient dem Ziel, die Produktivität und Prozesssicherheit bei der Herstellung der sicherheitsrelevanten Integralbauteile zu erhöhen.
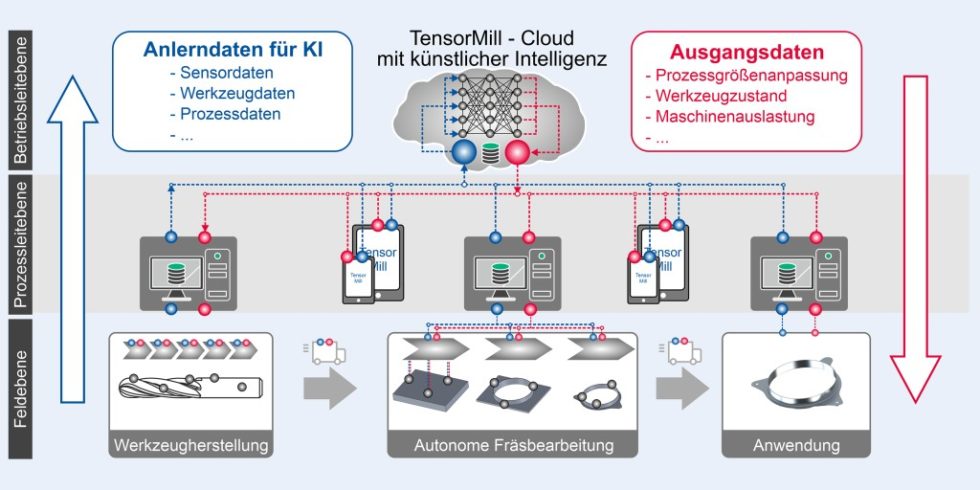
Bild 1. Der Aufbau der Prozesskette und der Datentransfer im Forschungsvorhaben „TensorMill“. Bild: IFW Hannover
Ausgabe 1/2-2021, S. 14
1 Einleitung
Mit einer Bruttowertschöpfung von über 660 Milliarden Euro weist das verarbeitende Gewerbe für die deutsche Wirtschaft eine hohe Bedeutung auf [1]. Durch Entwicklungen im Rahmen von Industrie 4.0 wird zusätzlich eine kumulierte Produktivitätssteigerung von 23 % bis zum Jahr 2025 erwartet. Dies liegt insbesondere an der Umsetzung von dezentralen Lösungen, welche eine Echtzeit-Auswertung von Prozessen mit zunehmender Komplexität ermöglichen [2]. Von dieser Entwicklung können besonders Unternehmen profitieren, die sich auf die Fertigung von sicherheitsrelevanten Integralbauteilen für die Luft- und Raumfahrtbranche spezialisiert haben. Hintergrund ist, dass die Herstellung dieser Integralbauteile mit hohen Anforderungen verbunden ist. Diese Anforderungen basieren auf der stetig wachsenden Bauteilkomplexität, den geringen Stückzahlen und einer hohen Wertschöpfung im Rahmen des Zerspanprozesses. Die Vermeidung von Ausschuss bei einer gleichzeitig hohen Produktivität dieser anspruchsvollen Werkstücke stellt eine wesentliche Herausforderung für die Herstellung dar. Um dieser Herausforderung zu begegnen, besteht insbesondere bei der spanenden Bearbeitung Handlungsbedarf. Dies betrifft Maßnahmen zur Umsetzung von Prozess- und Zustandsüberwachung sowie eine zunehmende Etablierung bedienerloser Prozesse zur Sicherstellung prozesssicherer und produktiver Zerspanprozesse. Dafür sind zunehmend vernetzte und intelligente Werkzeugmaschinen und Produktionsanlagen entlang der gesamten Wertschöpfungskette notwendig. Hier knüpft der Forschungsvorhaben TensorMill an. Im Rahmen dieses Beitrags wird das Gesamtkonzept dieses Forschungsvorhabens beschrieben. Ferner werden Methoden zur Umsetzung von Prozess- und Zustandsüberwachung durch eine maschinen- sowie werkstückseitige Überwachungseinheit vorgestellt.
2 Gesamtkonzept und Zielstellung
Das Forschungsvorhaben verfolgt mit seiner angestrebten intelligenten Vernetzung der gesamten Wertschöpfungskette das Ziel, die Produktivität und Prozesssicherheit bei der Fertigung von sicherheitsrelevanten Strukturbauteilen zu erhöhen. Dabei wird unter Verwendung von Methoden der KI die Robustheit der Fertigungsprozesse gesteigert. Der grundlegende Aufbau der ganzheitlich digitalisierten Prozesskette ist in Bild 1 dargestellt.
Die Prozesskette umfasst die Teilprozesse Werkzeugherstellung, autonome Fräsbearbeitung und Anwendung. Auf der Feldebene werden entlang der einzelnen Teilprozessschritte Daten generiert. Die Daten umfassen prozessspezifische Informationen zum Werkzeug (zum Beispiel Durchmesser und Drallwinkel), zum Zerpanprozess (zum Beispiel Prozesskräfte und Werkzeugposition) sowie zum Werkstück (zum Beispiel Maß- und Formabweichungen). Die Daten werden in der Prozessleitebene von Edge-Computern und anderen Endgeräten gesammelt und an die TensorMill-Cloud in der Betriebsleitebene gesendet. Dort werden die Daten verwendet, um KI-basierte Modelle anzulernen. Der Abgleich der Daten der Überwachungssysteme mit den angelernten KI-Modellen erlaubt es, Fehler während des Zerspanprozesses frühzeitig zu erkennen und darauf zu reagieren. Zusätzlich ermöglichen Daten aus vorgelagerten Prozessen bereits dort entstandene Abweichungen zu identifizieren und nachgelagerte Handlungsmaßnahmen zu ergreifen. Die von den KI-basierten Modellen abgeleiteten Handlungsempfehlungen werden an die Prozessleit- und Feldebene gesendet. Dort werden diese von den Benutzern oder direkt von den Werkzeugmaschinen weiterverarbeitet.
Während bei der Werkzeugherstellung und der Anwendung auf Daten aus der Qualitätssicherung zurückgegriffen werden kann, stellt die Generierung von prozessrelevanten Daten in der autonomen Fräsbearbeitung eine besondere Herausforderung dar. Grund hierfür ist zum einen, dass sich Datenquellen, die zum Beispiel Informationen zu den Prozesskräften und dem Werkzeugverschleißzustand liefern, möglichst nah am Werkzeugeingriff befinden müssen. Nur durch die Nähe zur Wirkstelle gelingt es, Daten zum realen Prozessverhalten mit hinreichender Sensitivität aufzunehmen. Zum anderen erfordert die Dynamik der Fräsbearbeitung eine hohe Abtastrate zum Auslesen eingesetzter Sensoren. Grund hierfür ist, dass die Detektion dynamischer Merkmale, wie zum Beispiel das Auflösen einzelner Zahneingriffe nach dem Nyquist-Shannon-Abtasttheorem, hohe Abtastraten erfordern.
Um den Anforderungen gerecht zu werden, wird zur Ermittlung prozessrelevanter Daten im Rahmen der autonomen Fräsbearbeitung eine neuartige maschinen- und werkstückseitige Überwachungseinheit eingesetzt. Die maschinenseitige Überwachungseinheit wird vom Institut für Produktionsmanagement, Technologie und Werkzeugmaschinen (PTW) entwickelt und angewendet. Die Hauptaufgabe dieser Einheit ist das prozessparallele Aufzeichnen und Verarbeiten von Werkzeugmaschinendaten. Hierzu zählen alle Antriebsdaten, wie zum Beispiel Achs- und Spindelströme, Regelabweichungen sowie die Achspositionen. Die wesentliche Komponente dieser Einheit bildet eine Edge Computing-Lösung, die in der Werkzeugmaschine integriert ist. Die Edge Computing-Lösung ermöglicht es, die gewünschten Daten mit einer Abtastfrequenz von f = 500 Hz aufzuzeichnen und zu verarbeiten. Die werkstückseitige Überwachungseinheit hingegen ermöglicht das Erfassen von werkstückseitigen Informationen, die mithilfe der maschinenseitigen Überwachungseinheit nicht in ausreichender Genauigkeit oder unmöglich zu ermitteln sind. Dies betrifft beispielsweise Informationen zum Spannzustand des Werkstücks sowie der Erfassung von Prozesskräften und der daraus resultierenden Werkstückverformung. Um diese Informationen zu extrahieren basiert die werkstückseitige Überwachungseinheit auf einem sensorischen Spannsystem, das vom Institut für Fertigungstechnik und Werkzeugmaschinen (IFW) in Zusammenarbeit mit der Römheld GmbH Friedrichshütte entwickelt und angewendet wird. Die Kombination der Daten der maschinenseitigen und werkstückseitigen Überwachungseinheit auf der Prozessleitebene dient als fundierte Datenbasis zum Anlernen der KI-basierten Modelle. Aufgrund der Bedeutung der maschinenseitigen und werkstückseitigen Überwachungseinheit wird nachfolgend auf deren Anwendung zur Umsetzung von Prozess- und Zustandsüberwachung eingegangen.
3 Maschinenseitige Überwachungseinheit
Der Nutzen der maschinenseitigen Überwachungseinheit lässt sich anhand von zwei Anwendungsbeispielen verdeutlichen. Dies betrifft die Prognose zum Werkzeugzustand sowie zur Werkstückqualität auf Basis der aufgezeichneten Antriebsdaten aus der Werkzeugmaschine im Rahmen des Zerspanprozesses.
3.1 Zustand des Werkzeugs
Für eine umfassende Bewertung des Werkzeugzustands werden Informationen aus der Werkzeugherstellung sowie aus dem Werkzeugeinsatz berücksichtigt. Dies dient der Zustandserfassung des Werkzeugs unter Berücksichtigung des gesamten Werkzeuglebenszyklus innerhalb der Fertigung. Die Daten aus der Werkzeugherstellung, zum Beispiel Abweichungen vom Werkzeugnenndurchmesser und -drallwinkel, ermöglichen vorgelagerte Fehler bei der Prognose des aktuellen Werkzeugzustands mit einfließen zu lassen. Von größerer Bedeutung sind allerdings die Daten zum Belastungszustand im Fräsprozess sowie aus Nachschleifvorgängen von Bedeutung. Grund hierfür ist, dass in diesen Prozessen die größte Gestaltänderung des Werkzeugs hervorgerufen wird. Von den ermittelten Kenntnissen zur Änderung des Verschleißzustands entlang der Prozesskette profitieren neben dem Anwender ebenfalls die Werkzeughersteller. Der Werkzeughersteller bekommt durch die rückgeführten Einsatzdaten des Werkzeugs bisher unbekannte Informationen über das eingesetzte Werkzeug. Dadurch können Nachschleifvorgänge optimiert und die Werkzeugeigenschaften bereits in der Entwicklung verbessert werden.
Zum Ermitteln des Werkzeugzustands in Zerspanprozessen wurden am PTW erste Untersuchungen durchgeführt. Hierfür wurden interne Antriebsdaten bei mehreren Stirnumfangsfräsprozessen eines Titanwerkstücks (TiAl4V6) unter Einsatz verschiedener Werkzeuge mithilfe der maschinenseitigen Überwachungseinheit erfasst. Es wurden gezielt herstellungsbedingte Fehler in den Werkzeugen eingebracht, um deren Auswirkungen auf die Antriebsdaten zu untersuchen. In Bild 2 sind zeitliche Verläufe des gemessenen Stroms in Y-Achse der Maschine dargestellt.
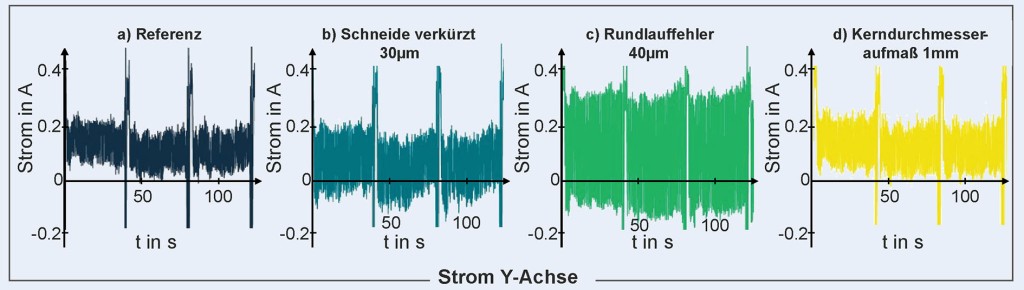
Bild 2. Einfluss von herstellungsbedingten Fehlern auf interne Antriebsdaten am Beispiel eines Schaftfräsprozesses in TiAl4V6. a) Referenzwerkzeug, b) eine radial verkürzte Schneide um 30 µm, c) Rundlauffehler am Werkzeug von 40 µm d) Werkzeug mit erhöhtem Kerndurchmesser um 1 mm. Bild: PTW Darmstadt
Die Auswertung der Antriebsströme verdeutlicht die Unterschiede zwischen dem Referenzwerkzeug und den fehlerbehafteten Werkzeugen. So lassen sich in Bild 2 bei der Betrachtung der rohen Zeitreihen bereits die höheren Schwankungsbreiten der Daten bei einer radial verkürzten Schneide am Werkzeug und bei einem hohen Rundlauffehler des Werkzeugs erkennen. Die Unterschiede sind mithilfe weiterer Datenanalysemethoden für den Zeit, Frequenz und Zeitfrequenzbereich zu detektieren. In zukünftigen Versuchen werden weitere Werkzeugfehler, zum Beispiel unterschiedliche Drallwinkel, Schneidkantenradien, Spanwinkel, Freiwinkel sowie die Beschichtungen, auf die Ausbildung des Werkzeugverschleißes untersucht. Die Auswertung dieser Fehler erlaubt die Bildung umfangreicher KI-Modelle zur genauen Vorhersage des aktuellen Werkzeugzustands. Diese Information ist essentiell zur Erreichung des primären Fertigungsziels, die Realisierung einer hohen Werkstückqualität
3.2 Vorhersage der gefertigten Werkstückqualität
Neben dem Werkzeugzustand existieren allerdings weitere Faktoren, die Einfluss auf die Werkstückqualität nehmen. Dies betrifft zum Beispiel das thermische Ausdehnungsverhalten der Werkzeugmaschine, Werkstoffschwankungen beziehungsweise Inhomogenitäten im Halbzeug oder den Spannzustand des Werkstücks. Diese Einflussfaktoren können allerdings häufig nicht ohne weiteres quantifiziert werden. Zudem bestehen Wechselwirkungseffekte, die eine gezielte manuelle Einflussnahme erschweren. Um diesen Herausforderungen zu begegnen, eignet sich der Einsatz der KI-basierten Modelle. Aufgrund der Fähigkeit der Mustererkennung sind KI-basierte Modelle in der Lage, auch ohne spezifisches Prozesswissen, Aussagen über den Zustand des Werkstücks ableiten zu können. Die Prognosegenauigkeit der Werkstückqualität hängt dabei maßgeblich von den bereitgestellten Daten ab. Um möglichst viele Informationen zu generieren, werden die Daten der maschinen- und werkstückseitigen Überwachungseinheit kombiniert.
Die Vorgehensweise beim Einsatz der maschinenseitigen Überwachungseinheit ist in Bild 3 dargestellt.
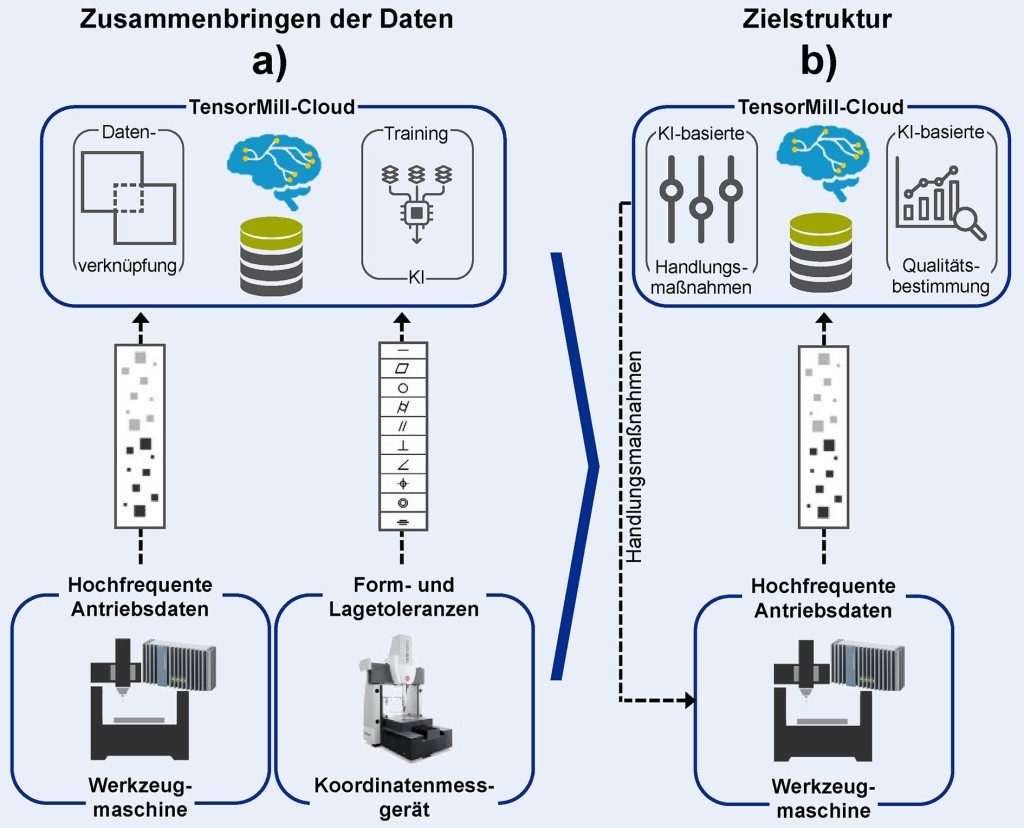
Bild 3. Bestimmung Werkstückqualität auf Basis hochfrequenter Maschinendaten. a) Zusammenbringen der Daten und Training der KI Modelle; b) Zielstruktur für die Nutzung der Maschinendaten für die Qualitätsüberwachung. Bild: PTW Darmstadt
Mithilfe dieser Überwachungseinheit werden im Rahmen des Zerspanprozesses hochfrequent Daten aufgezeichnet. Die Daten umfassen die oben angesprochenen internen Antriebssignale der Werkzeugmaschine. Die aufgezeichneten Signale werden mit den Merkmalen am Werkstück automatisch verknüpft. Als Merkmale werden zum Beispiel Form- und Lagetoleranzen herangezogen. Diese werden mithilfe eines Koordinatenmessgeräts erfasst und in der TensorMill-Cloud mit den Maschinendaten automatisiert verknüpft. Für die Maschinendaten bilden aktuell am Institut für Produktionsmanagement, Technologie und Werkzeugmaschinen (PTW) entwickelte Slicing-Algorithmen die Grundlage für die Zuordnung der Zeitreihendaten zu den geometrischen Merkmalen am Bauteil.
Die Daten der maschinenseitigen Überwachungseinheit liefern wichtige Informationen, um den Werkstückzustand vorhersagen zu können. Allerdings fehlen wesentliche werkstückseitige Informationen, wie zum Beispiel der Spannzustand oder die wirkenden Prozesskräfte, um eine genaue Prognose der Werkstückqualität ableiten zu können. Um diese fehlenden Daten zu generieren, wurde eine werkstückseitige Überwachungseinheit vom IFW entwickelt.
4 Werkstückseitige Überwachungseinheit
Bei der werkstückseitigen Überwachungseinheit handelt es sich um ein Spannsystem, das aus drei sensorischen Schwenkspannern besteht. Die sensorischen Eigenschaften werden durch Applikation von Dehnungsmessstreifen (DMS) hervorgerufen. Aufgrund der Nähe des sensorischen Spannsystems zum Prozess können wichtige Informationen zum Spannzustand und den Prozesskräften ermittelt werden. Die Fähigkeit der Prozesskraftdetektion wurde im Rahmen eines experimentellen Versuchs ermittelt. Hierfür wurde der im Bild 4 dargestellte experimentelle Versuchsaufbau verwendet. Der Versuchsaufbau besteht aus dem sensorischen Spannsystem, das auf dem Spannturm in einer Werkzeugmaschine vom Typ „Heller H5000“ integriert ist.
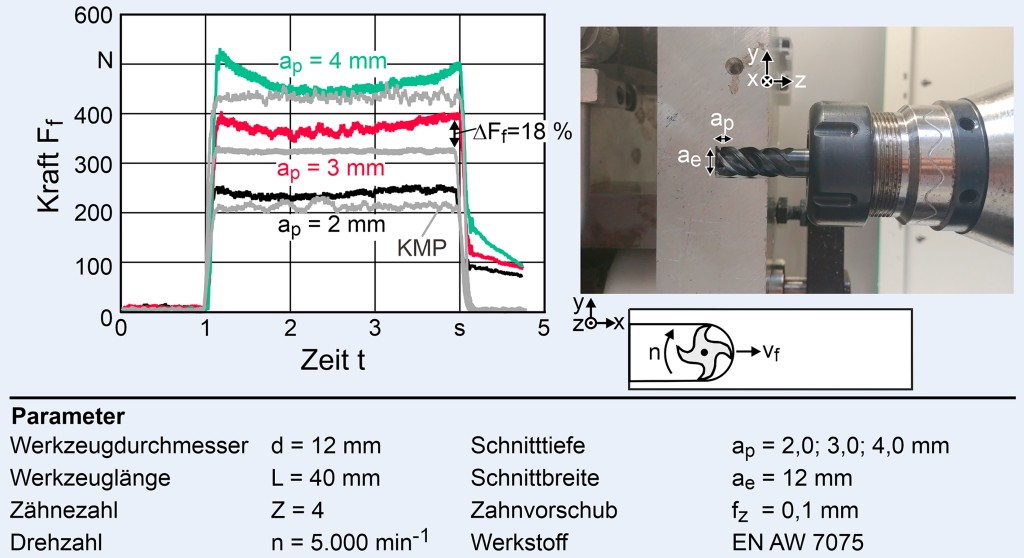
Bild 4. Versuchsaufbau: Sensorisches Spannsystem in der Werkzeugmaschine „Heller H5000“. Bild: IFW Hannover
Mithilfe der sensorischen Schwenkspannern wurde ein Werkstück aus Aluminium EN AW 7075 im Bauraum der Werkzeugmaschine gespannt. Im Rahmen von Zerspanversuchen erfolgte die Messung der Prozesskräfte beim Vollnutenschnitt. Hierfür wurde ein Vollhartmetallwerkzeug mit einem Durchmesser D = 12 mm, einer Auskraglänge von L = 40 mm und einer Zähnezahl z = 4 verwendet. Die für die Vollnutenschnitte verwendeten Schnittparameter sind im unteren Bereich im Bild 5 dargestellt. Es wurde eine Werkzeugdrehzahl von n = 5000 min-1, eine Schnittbreite von ae = 12 mm und ein Zahnvorschub von fz = 0,1 mm mit einer variierenden Schnitttiefe von ap = 2,0 – 4,0 mm angewendet. Als Referenz für die Signale des sensorischen Spannsystems wurde eine Kraftmessplattform (KMP) verwendet. Die Signale, die während verschiedener Vollnutenschnitte aufgezeichnet wurden, sind ebenfalls im Bild 5 dargestellt.
Die im Diagramm dargestellte Kraft Ff beschreibt die vom sensorischen Spannsystem ermittelte Vorschubkraft in x-Richtung. Diese Kraft wurde ausgewertet, weil diese die Hauptkraftkomponente beim Vollnutenschnitt darstellt. Die Vorschubkraft ergibt sich aus der Summe der Einzelkräfte in x-Richtung der einzelnen Schwenkspanner (Fx1, Fx2, Fx3). Der Zusammenhang zwischen der Kraft Ff und den in den DMS ermittelten Dehnungssignalen wurde durch eine statische Kalibrierung des Spannsystems in x-, y- und z-Richtung erreicht. Die statische Kalibrierung erfolgte durch Aufbringen einer definierten Kraft von Fk = 100 N über einen Kraftmessdorn.
Im Bild 5 ist der Vergleich zwischen der vom Spannsystem und von der KMP ermittelten Kraft Ff bei der Fertigung der Vollnuten mit unterschiedlichen Schnitttiefen dargestellt. Den Signalen der KMP kann entnommen werden, dass sich bei der kleinsten untersuchten Schnitttiefe von ap,min = 2,0 mm eine mittlere Vorschubkraft in x-Richtung von Ff = 215 N einstellt. Eine Verdopplung der Schnitttiefe auf ap,max = 4,0 mm führt zu einer Verdopplung der Vorschubkraft in x-Richtung auf Ff = 430 N. Dieses Verhalten kann anhand der Proportionalität der Schnitttiefe ap zur Kraft Ff bei ansonsten gleichen Parametern begründet werden. Die Gesamtkraft der Schwenkspanner in x-Richtung weist ein ähnliches Verhalten auf. Auch hier ist eine Abhängigkeit zwischen dem summierten Schwenkspannerkräften Ff und der Schnitttiefe ap zu beobachten. Im Gegensatz zur KMP weist das Spannsystem allerdings eine Wegabhängigkeit des Kraftsignals auf. So kommt es beispielsweise bei einer Schnitttiefe von ap = 4,0 mm beim Eintritt in das Werkstück zu einem raschen Anstieg der Vorschubkraft von Ff = 520 N. Im Laufe des Fräsprozesses sinkt die gemessene Kraft zunächst in der Mitte der Nut auf Ff = 450 N, bevor sie zum Ende der Nut wieder auf Ff = 500 N. Aufgrund dieses Verhaltens ist eine einfache Ableitung der tatsächlich wirkenden Kraft Ff nicht möglich. Dieses wegabhängige Verhalten lässt sich auf die Änderung der Fräserposition zu den einzelnen stationären Schwenkspannern zurückführen. Dadurch kommt es zu einer Änderung der Lagerreaktionen (Kräfte und Moment) in den sensorischen Schwenkspannern bei einer Änderung der Lage des Fräsers trotz gleichbleibender Kraft Ff. Der maximale Fehler der sich zwischen sensorischem Spannsystem und KMP einstellt, beträgt DFf = 18 %. Trotz der Abweichung wird deutlich, dass durch die Auswertung der Spannsystemsignale, die Kraft Ff in guter Näherung bestimmt werden kann.
Im weiteren Verlauf des Forschungsvorhabens werden die Kraftsignale genutzt, um Maß- und Formabweichungen des Werkstücks vorherzusagen. Zudem können diese Signale verwendet werden, um positionsaufgelöste Informationen über die wirkenden Prozesskräfte zu generieren. Der Nutzen dieser Methode liegt zum einen in der Möglichkeit der Bahnplanoptimierung. Treten im Rahmen des Fräsprozesses erhöhte Prozesskräfte auf, kann das ungünstige Eingriffsbedingungen des Werkzeugs hindeuten. Durch das Auftreten von temporären Kraftüberhöhungen besteht die Gefahr eines vorzeitigen Werkzeugverschleißes beziehungsweise Werkzeugbruchs. Durch Detektion von Lastspitzen kann eine Anpassung der Bahnplanung vorgenommen werden, um die Standzeit der Werkzeuge zu verlängern. Zum anderen ermöglicht die Prozesskrafterfassung durch das Spannsystem die Ableitung des Bauteilverzugs bei der Herstellung der Endkontur. Auf Basis der Kenntnis der Endkonturgeometrie und des E-Modul des Werkstücks kann eine Abdrängung des Werkstücks beziehungsweise des Werkzeugs berechnet werden. Durch Kenntnis über die Abweichung kann eine Abdrängungskompensation umgesetzt werden. Diese erlaubt die Herstellung maßgenauer Bauteile unter dem Einsatz produktiver Prozessparameter.
5 Zusammenfassung
In diesem Beitrag wurde die grundlegende Struktur der ganzheitlich vernetzten Prozesskette des Forschungsvorhabens „TensorMill“ vorgestellt. Wesentliche Bestandteile der vernetzten Prozesskette sind die maschinen- und werkstückseitige Überwachungseinheiten. Diese dienen der Generierung von prozess- und werkstückrelevanten Daten, um eine zuverlässige Prognose des Werkzeug- und Werkstückzustands anhand von KI-basierten Modellen ableiten zu können. Im Rahmen von experimentellen Untersuchungen wurden die Eigenschaften der Überwachungseinheiten analysiert. Die Untersuchungsergebnisse zeigen, dass die maschinenseitige Überwachungseinheit aufgrund der hohen Abtastrate von f = 500 Hz in der Lage ist, beim Zerspanprozess herstellbedingte Werkzeugfehler zu detektieren. Anhand der werkstückseitigen Überwachungseinheit konnten im Rahmen von Fräsuntersuchungen Vorschubkräfte mit einer maximalen Abweichung von DFf = 18 % im Vergleich zur Kraftmessung mit einem Dynamometer ermittelt werden.
Zukünftig werden diese Daten genutzt, um KI-basierte Modelle anzulernen und diese im Rahmen von Zerspanprozessen von Referenzbauteilen für die Prognose der Werkzeug- und Werkstückqualität einzusetzen.
Literatur
- Breitkopf, A.: Verarbeitendes Gewerbe – Bruttowertschöpfung der Metallindustrie in Deutschland bis 2017. Statistisches Bundesamt, 2020
- Bauer, W.; Schlund, S.; Marrenbach, D.; Ganschar, O.: Industrie 4.0 – Volkswirtschaftliches Potenzial für Deutschland. Fraunhofer-Institut für Arbeitswissenschaft und Organisation IAO, 2014
Alexander Fertig, M. Sc., Prof. Dr.-Ing. Matthias Weigold – Institut für Produktionsmanagement, Technologie und Werkzeugmaschinen (PTW), Technische Universität Darmstadt, Otto-Berndt-Str. 2, 64287 Darmstadt, Tel. +49 6151 / 16-29973, a.fertig@ptw.tu-darmstadt.de, www.ptw.tu-darmstadt.de. Christian Teige, M. Sc., Prof. Dr.-Ing. Berend Denkena, Dr.-Ing. Benjamin Bergmann – Institut für Fertigungstechnik und Werkzeugmaschinen (IFW) , Leibniz Universität Hannover Produktionstechnisches Zentrum der Leibniz Universität Hannover / PZH , An der Universität 2, 30823 Garbsen , Tel. +49 511 / 762-18334, teige@ifw.uni-hannover.de, www.ifw.uni-hannover.de