Intelligente Fertigungszelle für die Implantatherstellung
Im Rahmen des vom BMBF (Bundesministerium für Bildung und Forschung) geförderten Projekts „TempoPlant“ wird eine teilautonome Fertigungszelle für die Herstellung orthopädischer Implantate erforscht. Dabei wird ein Bearbeitungszentrum mit Messtechnik zur Qualitätskontrolle und Prozessüberwachung ausgestattet. Die gewonnenen Daten werden für die Prozessüberwachung, die Qualitätsregelung und die Dokumentation entsprechend den Richtlinien der Medical Device Regulation (MDR) genutzt.
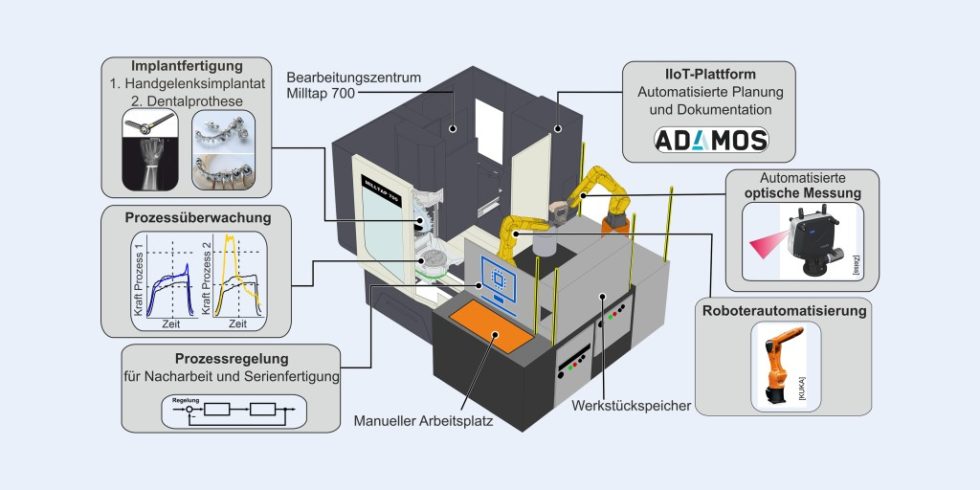
Bild 1. „TempoPlant“ Fertigungszelle. Bild: IFW Hannover
Ausgabe 9-2020 / S. 629
1 Einleitung
Bei Betrachtung der Entwicklung der Weltbevölkerung wird ersichtlich, dass die Anzahl der Menschen, die auf der Erde leben, sowie deren Durchschnittsalter kontinuierlich ansteigen [1, 2]. Bis 2050 werden voraussichtlich nur noch 14 % aller in Deutschland lebenden Menschen unter 18 Jahre und circa 30 % über 65 Jahre alt sein [3, 4]. Aufgrund dieser Entwicklung steigt der Bedarf an medizinischer Versorgung. Bereits heute nimmt die medizinische Versorgung der Bevölkerung mit über 50 % den größten Anteil der industriellen Gesundheitswirtschaft in Deutschland ein [5]. Arzneimittel, Forschung und Entwicklung sowie Medizinprodukte und Medizintechnik machen mit über 20 % den zweitgrößten Anteil der industriellen Gesundheitswirtschaft aus [5]. Experten prognostizieren für die kommenden Jahre einen durchschnittlichen jährlichen Anstieg des Weltmarktes für Medizintechnik in Höhe von rund 5,6 %. Die Marktgröße soll in 2024 einen Wert von 595 Milliarden US Dollar erreichen [6]. Dementsprechend positiv sind damit auch die Aussichten für die Orthopädie, die mit 12,2 % den größten Teil des Medizintechnikmarkts ausmacht [6].
Während sich die marktseitigen Aussichten positiv darstellen, sehen sich die Hersteller orthopädischer Implantate einem zunehmenden Kostendruck ausgesetzt. Eine Umfrage des Bundesverbands Medizintechnologie im Herbst 2019 zeigt eine Veränderung der Entwicklung der Gewinnsituation der Unternehmen in Deutschland aufgrund sinkender Preise und höherer Kosten am Standort Deutschland. Nur noch 12 % erwarten in diesem Jahr eine verbesserte Gewinnsituation (Vorjahr: 24 %). Mittlerweile gehen 43 % der befragten Unternehmen von einer rückläufigen Gewinnentwicklung aus, 42 % von Stagnation [7]. Als Hauptursache für diese Entwicklung sehen die befragten Unternehmen die Einführung der neuen EU-Medizinprodukteverordnung (Medical Device Regulation – MDR). 81 % der Unternehmen bezeichnen die zusätzlichen Anforderungen durch die MDR als größtes Hemmnis für die künftige Entwicklung der Medizintechnologie-Branche. Dabei geht es vor allem um die Pflicht zur umfassenden Speicherung klinischer Daten, Pläne und Berichte gemäß der MDR [7].
Die geforderte hohe Maßhaltigkeit der Implantate, die zunehmende Nachfrage an individuellen, patientenspezifischen Implantaten und die Anforderung an eine möglichst schnelle Lieferung stellen Medizinproduktehersteller, zusätzlich zu den regulatorischen Anforderungen durch die MDR, vor Herausforderungen. So müssen beispielsweise bei der Fertigung von Handgelenksendoprothesen filigrane Einzelteile hergestellt werden, die meist aus schwer zu bearbeitenden Materialien, wie Cobalt-Chrom oder Titanlegierungen bestehen. Ein weiterer Anwendungsfall ist die Herstellung von Implantaten im Dentalbereich. Hier werden neben schnellen Lieferzeiten und sehr engen Fertigungstoleranzen zusätzlich für jeden Patienten individuelle Implantatgeometrien gefordert, was eine produktive Fertigung erheblich erschwert.
Das Projekt TempoPlant möchte die Anforderungen und Chancen durch die Steigerung der Effizienz der Fertigungsprozesse verknüpfen. Innerhalb des Projekts entwickelt das Institut für Fertigungstechnik und Werkzeugmaschinen IFW gemeinsam mit Anwendern aus der Medizintechnikbranche, einem Werkzeugmaschinenhersteller sowie einem Hersteller optischer Mess- und Sensortechnik eine Fertigungszelle zur effizienten, teilautonomen Fertigung orthopädischer Implantate.
2 Gesamtsystem
Die konzipierte Fertigungszelle verfolgt fünf Grundprinzipien, nach denen sich die Produktion von Implantaten richtet:
- Hoher Automatisierungsgrad auch für Einzelteile und Kleinserien
- Automatisierte Qualitätskontrolle aller gefertigten Werkstücke
- Automatisierte Auswertung der Messdaten zur Qualitätsregelung
- Prozessüberwachung während des Fertigungsprozesses
- Bereitstellung und zentrale Sicherung der relevanten Daten zur Dokumentation nach MDR.
Zur Realisierung dieser Grundprinzipien besteht die Fertigungszelle aus mehreren verknüpften Teilsystemen, die in Bild 1 dargestellt sind. Neben dem Bearbeitungszentrum „Milltap 700“ von DMG befindet sich ein mobiler Arbeitsplatz. Darauf befindet sich ein Industrieroboter, der das Bearbeitungszentrum mit Werkstücken be- und entlädt und somit für einen hohen Automatisierungsgrad sorgt. Manuelle Arbeiten, wie beispielsweise Prüf- und Montagearbeiten, können ebenfalls direkt an der Maschine durchgeführt werden. Direkt angrenzend zum Arbeitsplatz befindet sich eine mobile Messstation. Sie besteht aus einem „T-SCAN“ Laserscanner von der Zeiss Optotechnik GmbH, der von einem Roboter geführt wird und dabei die Oberfläche des Messobjekts optisch abtastet. Das Messsystem muss in der Lage sein, die orthopädischen Implantate mit einer Genauigkeit von wenigen Mikrometern zu vermessen, um beispielsweise die Qualität einer Passbohrung D = 10 mm H7 zu bewerten. Dabei sind insbesondere die oft stark spiegelnden Oberflächen und die komplizierte Form der Implantate eine Herausforderung für die Messung. Durch die Entwicklung neuer Messtechniken soll es erlaubt werden, glänzende metallische Oberflächen und Formen mit starken Kavitäten zu vermessen. Durch den Einsatz eines kollaborativen Robotersystems wird eine intuitive Handhabung für den Anwender gewährleistet. Die Messdaten lassen sich zum einen zur Qualitätskontrolle und automatisierter Dokumentation nutzen. Zum anderen ist eine Qualitätsregelung des Fertigungsprozesses möglich. Prozessfehler werden erkannt und nachfolgende Prozesse auf dieser Basis angepasst. Die Grundlage der Qualitätsregelung bilden im CAD-Modell hinterlegte Produktdaten, sogenannte Product and Manufacturing Information (PMI). Darin enthalten sind Toleranz- und Prüfdaten, die zur Bewertung des Fertigungsergebnisses sowie zur Dokumentation herangezogen werden.
3 Prozessüberwachung
Während der spanenden Herstellung von Bauteilen entstehen Prozesskräfte, sobald Werkzeug und Werkstück miteinander in Kontakt geraten. In dem Anwendungsfall der Handgelenksendoprothesen kommen nur Werkzeuge mit einem geringen Durchmesser zwischen 8 mm und 2 mm zum Einsatz. Die Prozesskräfte betragen mit einem Kugelkopffräser (DWz = 2 mm) bei einer Schnitttiefe von maximal 0,25 mm etwa 5 N. Um die geringen Prozesskräfte für eine Prozessüberwachung mit hoher Genauigkeit messen zu können, wurde im Rahmen des Projekts ein sensorisches Spannsystem entwickelt, welches in Bild 2 dargestellt ist.
Dabei werden Dehnungsmessstreifen (DMS) zur Kraftmessung genutzt. Mit diesen lassen sich indirekt über die in Maschinenkomponenten vorliegenden Dehnungen die Prozesskräfte messen [8]. Das sensorische Spannsystem verfügt über Kraftmesselemente, die sich direkt im Kraftfluss befinden. Die Kraftmesselemente sind konstruktiv so aufgebaut, dass sich lokal Spannungsspitzen ausbilden, die sich an den Messpositionen für die Dehnungsmessstreifen befinden. Zusätzlich bilden sich an diesen Positionen nahezu einachsige Dehnungszustände. Durch die konstruktive Ausrichtung der Messgitter in den Dehnungsmessstreifen trägt somit ein Großteil der vorliegenden Dehnung zum Messergebnis bei. Im Bild 2 unten rechts ist dargestellt, dass die normale elastische Dehnung in X-Richtung bei einer Prozesskraft von 5 N etwa 1,3 m/m beträgt, was mit konventionellen Dehnungsmessstreifen messbar ist. Die gesamte notwendige Elektronik ist in das Spannsystem integriert, sodass eine prozessnahe Datenvorverarbeitung möglich ist, was Signalstörungen verhindert. Das Spannsystem kann somit zur Prozessüberwachung genutzt werden, die nachfolgend beschrieben wird.
Das Ziel der Prozessüberwachung ist es, Fehler im Fertigungsprozess zu detektieren und den Prozess zu stoppen bevor irreparable Schäden wie Werkzeugbruch oder Schäden an der Werkzeugmaschine entstehen. Zusätzlich soll durch die Prozessüberwachung sichergestellt werden, dass das zu fertigende Implantat innerhalb aller Fertigungstoleranzen hergestellt wird. Die Grundlage der Prozessüberwachung ist die bereits erwähnte Prozesskraft, die mithilfe des sensorischen Spannsystems erfasst wird. Verlässt diese Kraft während der Fertigung einen vorgegebenen Toleranzbereich, wird der Prozess gestoppt. Im Anschluss daran findet eine Inspektion der aktuellen Bauteilgeometrie statt, um die Maßhaltigkeit zu überprüfen und ggf. in den nachfolgenden Prozess der Weiterbearbeitung einzugreifen. Das Verlassen des Toleranzbereichs kann zum Beispiel durch übermäßigen Werkzeugverschleiß, Werkzeugbruch, fehlerhafte Einspannung des Werkstücks oder ungünstige Temperaturverhältnisse auftreten.
Zur Festlegung des Toleranzbereichs wurde im Rahmen des Projekts ein virtuelles Maschinenmodell, ein sogenannter „Digitaler Zwilling“ (DZ) der Werkzeugmaschine entwickelt, welcher ein hohes Potenzial zur Effizienzsteigerung der Fertigung bietet [9]. Der digitale Zwilling wird durch die Achsdaten der Werkzeugmaschine gesteuert. Hierbei ist ein Industrie-PC von Beckhoff als Profibus-Teilnehmer in die Maschine eingebunden, der damit Zugriff auf die Achsdaten der Maschinensteuerung (Siemens „840 D SL“) hat. Der Simulationsrechner, in den der Digitale Zwilling integriert ist, wird über Ethernet an den Industrie-PC angeschlossen und erhält die Achsdaten der Maschine im Regeltakt von 2 ms. Somit wird jede Achsbewegung der Maschine virtuell gespiegelt. Das Maschinenmodell des Zwillings berechnet auf Grundlage einer Materialabtragssimulation (IFW „CutS“) die theoretisch auftretende Kraft des Zerspanprozesses unter Idealbedingungen und liefert somit zu jedem IST-Kraft-Wert des sensorischen Spannsystems einen zum gleichen Prozessschritt passenden virtuellen Soll-Kraft-Wert. Die Kraftdiskrepanz aus realer IST- und virtueller idealer Soll-Kraft wird zur ständigen Anpassung des erlaubten Toleranzbereichs während des Fertigungsprozesses verwendet.
Diese Vorgehensweise setzt voraus, dass ein initiales Toleranzband bereits vor der eigentlichen Fertigung zur Verfügung steht. Hierzu wurde eine „Vorsimulation“ des Fertigungsprozesses durchgeführt, wobei das digitale Maschinenmodell (DZ) nicht durch die Achsen der realen Werkzeugmaschine angesteuert wird. Stattdessen wird eine sogenannte. virtuelle Maschine (VM) als „Antrieb“ des Digitalen Zwillings verwendet. Die virtuelle Maschine ist ein genaues geometrisches und kinematisches Abbild der realen Maschine. Virtuelle und reale Maschine verwenden die gleiche Steuerung. Somit kann der aus der CAM-Planung generierte NC-Code zusätzlich verlässlich virtuell überprüft werden. Anders als der Digitale Zwilling ist die virtuelle Maschine nicht in der Lage die Eingriffsbedingungen zwischen Werkzeug und Werkstück und somit die Prozesskraft zu berechnen.
Bild 3 zeigt den Ablauf der Vorsimulation.
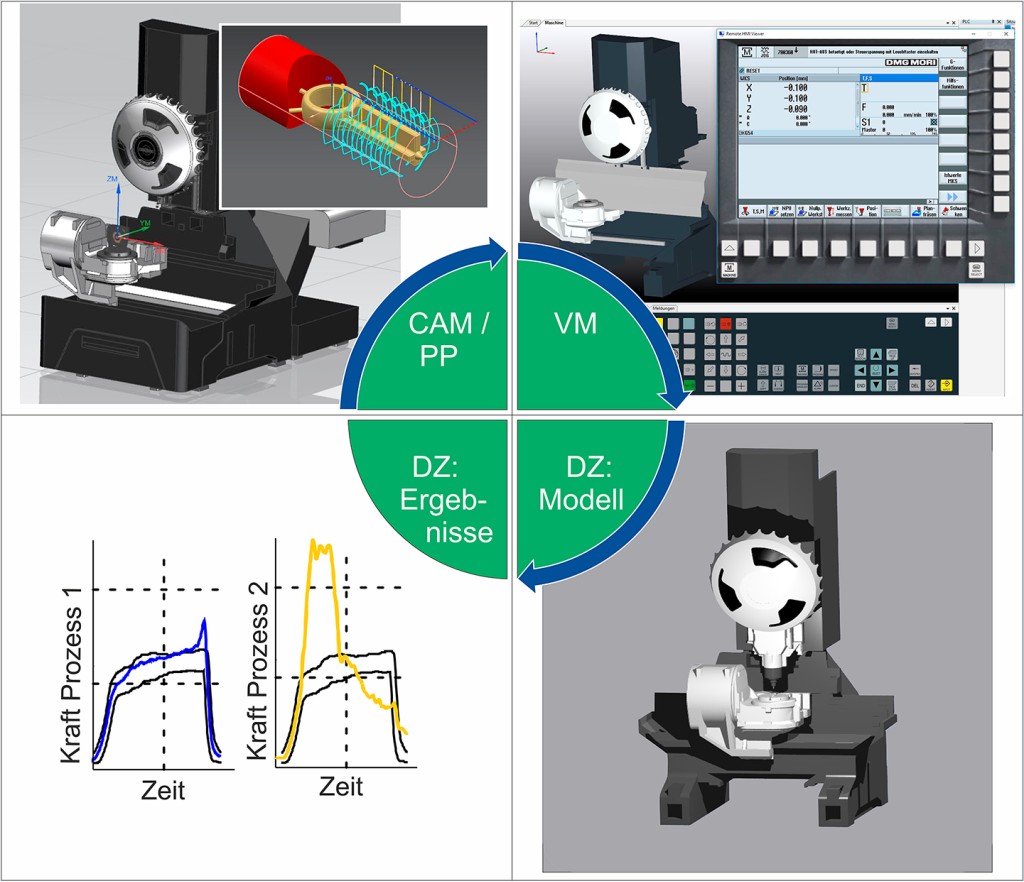
Bild 3. Vorsimulation zur Bestimmung des initialen Toleranzbereichs der Zerspankraft. Bild: IFW Hannover
In der Prozessplanung (CAM) wird mittels Postprozessor (PP) ein maschinenlesbarer NC Code generiert. Dieser wird im Anschluss mithilfe der virtuellen Maschine überprüft. Gleichzeitig liefert die virtuelle Maschine die Achsdaten, die zum Antrieb des Digitalen Zwillings benötigt werden. Der Digitale Zwilling simuliert anschließend den Materialabtrag mithilfe der Materialabtragssoftware IFW CutS und berechnet durch Eingriffsbedingungen die auftretenden Prozesskräfte, die dazu verwendet werden das initiale Toleranzband zur Überwachung der realen Fertigung festzulegen. Die Art und Weise der Festlegung des initialen Toleranzbandes ist Gegenstand aktueller Untersuchungen. Mögliche Ansätze zur Toleranzbanderstellung sind zum Beispiel die Benutzung einer festen Grenze oder eine prozentuale Abweichung des Ist- zum Soll-Signals.
4 Dokumentation nach der Medizinprodukte- Verordnung (MDR)
Durch die neue Medizinprodukte-Verordnung werden nicht nur Anforderungen an das Produkt, sondern auch an die Dokumentation selbst festgelegt. Zwar gab es bereits bei der Medizinprodukte-Richtlinie 93/42/EWG (MDD) Anforderungen an die Dokumentation jedoch waren diese bei weitem nicht so umfangreich und präzise ausgelegt. Die geforderten Anforderungen an die technische Dokumentation eines Medizinproduktes sind:
- Produktbeschreibung: Zweckbestimmung, Varianten, Konfiguration, Zubehör und eindeutige Identifikation des Produkts (Unique Device Identification), Auslegung des Produkts
- Herstellprozesses: Prozessablauf, Maschinennummer, verwendeter NC-Code, Chargennummer, Name des Maschinenbedieners, Fertigungszeitpunkt, Materialspezifikationen, verwendete Hilfsstoffe
- Messprotokolle: Maßhaltigkeit und Toleranzen inklusive der freigegebenen Zeichnungen mit Prüfpunkten
- Begleitinformation: Kennzeichnung, Verpackung, Gebrauchsanweisung
- Hilfsstoffe: Kühlschmierstoffe, validiertes Verfahren zur Reinigung, Laboruntersuchungen
- Risikomanagementakte
- Verifizierung und Validierung des Produkts
- Nachweis, dass die grundlegenden Sicherheits- und Leistungsanforderungen erfüllt sind.
In diesem Projekt soll die Dokumentation der Herstellung von Handgelenksendoprothesen und Zahnimplantaten entsprechend der Richtlinien zentral auf einer Plattform gespeichert werden. Alle digital zur Verfügung stehenden Daten wie beispielsweise die Messdaten und Prozessdaten werden zusätzlich automatisiert gespeichert. Ein Leitstandrechner, der auch zur Steuerung der Teilsysteme genutzt wird, verknüpft alle in Kapitel 2 dargestellten Teilsysteme miteinander. Die Daten der Teilsysteme werden darüber gebündelt und in eine relationale Datenbank gespeichert, die sich auf der Plattform „ADAMOS“ befindet. Dies hat den Vorteil, dass auch anderen Beteiligte der Prozesskette auf die Daten zugreifen und hinzufügen können. Der Dokumentationsaufwand soll somit insgesamt verringert werden. Die gesamte Dokumentation muss mindestens 15 Jahre nach dem jeweiligen Fertigungslos lückenlos nachvollziehbar gespeichert werden.
5 Fazit und Ausblick
Durch die Entwicklung einer teilautonomen Fertigungszelle leistet das Projekt einen Beitrag dazu, die wirtschaftliche Fertigung medizintechnischer Produkte in Deutschland zu ermöglichen. Die Fertigungszelle besteht aus den im Beitrag vorgestellten Teilsystemen. Das Bearbeitungszentrum „Milltap 700“ von DMG und ein danebenstehender Montagearbeitsplatz bilden das Herzstück der Zelle. Ein Industrieroboter zum Be- und Entladen der Zelle und ein Messroboter, der mit optischer Messtechnik der Firma Zeiss ausgestattet ist, vervollständigt die Hardwarekomponenten der Fertigungszelle. Zusätzlich spielen die Qualitätskontrolle und die Prozessüberwachung eine zentrale Rolle. Zum einen wird Messtechnik genutzt und weiterentwickelt, um die Geometrie der hergestellten Implantate zu messen und den Fertigungsprozess zu überwachen. Zum anderen wird virtuell ein Digitaler Zwilling erstellt, der alle Fertigungsdaten enthält und somit die Grundlage zur effizienten Dokumentation des Fertigungsprozesses bereitstellt. Insgesamt wird damit der Ausschuss reduziert, die Produktivität erhöht und der Dokumentationsaufwand verringert. Die Fertigungszelle befindet sich momentan im Aufbau und wird bis zum Projektende (Mai 2022) erforscht.
Literatur
- United Nations, Department of Economic and Social Affairs, Population Division (2019). World Population Prospects 2019, zitiert nach de.statista.com. Internet: https://de.statista.com/statistik/daten/studie/1694/umfrage/entwicklung-der-weltbevoelkerungszahl. Zugriff am 02.04.2020
- United Nations, Department of Economic and Social Affairs, Population Division (2019). World Population Prospects 2019, zitiert nach de.statista.com. Internet: https://de.statista.com/statistik/daten/studie/159834/umfrage/altersmedian-der-weltbevoelkerung. Zugriff am 02.04.2020
- Publications Office of the European Union: Ageing Europe – Looking at the lives of older people in the EU. Luxenbourg 2019
- Statistisches Bundesamt: Bevölkerung Deutschlands bis 2060 – 13. Koordinierte Bevölkerungsvorausberechnung. Wiesbaden 2015
- Bundesministerium für Wirtschaft und Energie (BMWi): Gesundheitswirtschaft – Fakten & Zahlen, Ausgabe 2018. Berlin 2019
- Mallok, J.: Die deutsche Medizintechnik-Industrie: SPECTARIS Jahrbuch 2019/2020. Berlin: Köllen Druck+Verlag 2019
- Bundesverband Medizintechnologie: Branchenbericht Medizintechnologien 2020. Berlin: BVMed 2020
- Brecher, C. et al.: Estimation of the virtual workpiece quality by the use of a spindle-integrated process force measurement. CIRP Annals, Col. 68 (2019) S. 381–384
- Schleich, B. et al.: Shifting value stream patterns along the product lifecycle with digital twins. Procedia CIRP, Vol. 86 (2019) S. 3–11
Prof. Dr.-Ing. Berend Denkena; Dr.-Ing. Marc-André Dittrich; Dipl.-Ing. Martin Winkler; Sebastian Kaiser, M. Eng. – Institut für Fertigungstechnik und Werkzeugmaschinen (IFW) an der Leibniz Universität Hannover, An der Universität 2, 30823 Garbsen, Tel. +49 (0)511 / 762-2533, info@ifw.uni-hannover.de, www.ifw.uni-hannover.de