Für effiziente und sichere industrielle Produktion
Im Umfeld von Industrie 4.0 halten die modernen Informationstechnologien immer stärker Einzug. Dabei sind Schlüsseltechnologien wie zum Beispiel künstliche Intelligenz (KI) oder Artificial Reality (AR) für sich allein genommen im industriellen Praxiseinsatz nur sehr bedingt verwendbar. Den Schlüssel zum Erfolg liefert vielmehr die Vernetzung dieser modernen Technologien sowohl untereinander als auch mit dem humanen Bedienpersonal durch Algorithmen und Systeme zur Mensch-Maschine-Kollaboration (MMK).
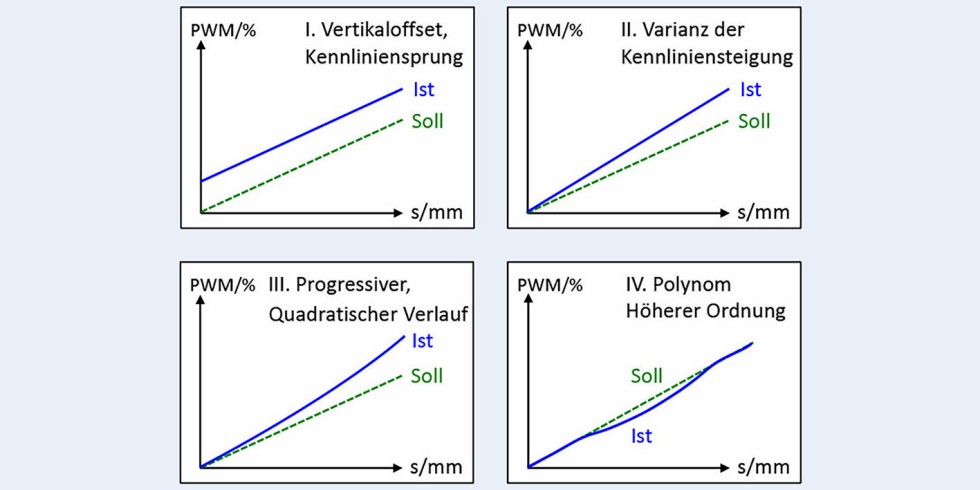
Bild 1. Störszenarien bei der Bewegungserkennung mittels elektromagnetischer Felder. Grafik: Büro für Logistikforschung
Ausgabe 9-2021, S. 607
1 Einleitung und Ausgangslage
Durch die Verwendung von Technologien der Mensch-Maschine-Kollaboration (MMK) beziehungsweise die Vereinigung der Vorteile von Mensch (Intuition, Flexibilität, Entscheiden und Urteilen) und Maschine (schnelle, kraftvolle, ausdauernde und reproduzierbare Bewegungen) ergeben sich erhebliche ökonomische und gesellschaftliche Nutzenpotenziale für produzierende Unternehmen:
- Vereinigung der Vorteile von Mensch (Intuition, Flexibilität, Entscheiden und Urteilen) und Maschine (schnelle, kraftvolle, ausdauernde und reproduzierbare Bewegungen),
- Verbesserung der Arbeitsergonomie durch Übernahme der belastenden Arbeitsteile durch die Maschine beziehungsweise den Roboter,
- effektivere Arbeitsabläufe bei geringerem Platzbedarf im Vergleich zu isolierten Mensch- und Maschinenarbeitsplätzen,
- Möglichkeit zur Verbesserung der Produktivität und Qualität von für eine vollumfängliche Automatisierung nicht geeigneten manuellen Arbeitsplätzen sowie
- Steigerung der Leistungsfähigkeit trotz des demografischen Wandels (vgl. [1, 2]).
- Allerdings werden MMK-Technologien in der Praxis bislang noch nicht verbreitet eingesetzt und die oben genannten enormen Nutzenpotenziale daher nicht ausreichend ausgeschöpft. Ein elementarer Grund hierfür sind die in Deutschland vorherrschenden sehr strengen regulatorischen Bestimmungen, die dazu führen, dass MMK-Lösungen im Rahmen klassischer Amortisationsrechnungen in den meisten Fällen an ihre Grenzen stoßen (vgl. [3], S. 21; [1]). Bezüglich des Kriteriums der Arbeitssicherheit gilt es beispielsweise die folgenden vier Schutzprinzipien zu unterscheiden, die nachfolgend näher erläutert werden:
- Handführung,
- Geschwindigkeits- und Abstandsüberwachung,
- Leistungs- und Kraftbegrenzung sowie
- sicherheitsbewerteter, überwachter Halt ([4]; [1]).
- Bei der Handführung handelt es sich um eine Betriebsart, bei der sich Mensch und Roboter einen Arbeitsraum teilen und dabei gleichzeitig mit vorhandenem physischem Kontakt arbeiten. Die Roboterbewegung wird dabei mit einer geeigneten Ausrüstung aktiv vom Mitarbeiter gesteuert. [1] Die elementaren Nachteile dieser Betriebsart sind jedoch die, dass im Vorfeld der Inbetriebnahme eines solchen MMK-Systems eine umfassende und aufwendige Risikobeurteilung zu erfolgen hat und im Rahmen dieser – nach der Norm DIN EN ISO 13849 (Teil 1 und 2) – eine maximale Geschwindigkeit für die Maschinenbewegungen festgelegt wird, die in der Regel negative Auswirkungen auf die Effizienz des gesamten Produktionssystems hat (vgl. [1, 5, 6]).
- Im Zusammenhang mit der Geschwindigkeits- sowie Abstandsüberwachung dürfen sich Robotersystem und Bedienperson gleichzeitig im Kollaborationsraum bewegen, wobei ununterbrochen ein Sicherheitsabstand zwischen der Bedienperson und dem Roboter aufrechterhalten wird, bei dessen Unterschreitung das Robotersystem sicher anhalten muss (vgl. [7], S. 17). Auch bei dieser Betriebsweise ergibt sich der grundlegende Nachteil, dass sich die nach der DIN EN ISO 13849 begrenzte Robotegeschwindigkeit negativ auf einen wirtschaftlichen Einsatz auswirkt (vgl. [4]).
Bei dem Schutzprinzip der Leistungs- und Kraftbegrenzung besteht die Möglichkeit eines physischen Kontakts zwischen dem Robotersystem (einschließlich des Werkstücks) und einer Bedienperson ([7], S. 22). Die Kontaktkräfte zwischen Mitarbeiter und Roboter werden dabei technisch auf ein ungefährliches Maß begrenzt, indem eine sensorische, mechanische und/oder elektronische Begrenzung von Kraft oder Druck bei der Kollision zwischen Mensch und Maschine sichergestellt wird (vgl. [1]). Anzuwenden sind in diesem Zusammenhang die Normen DIN ISO/TS 15066 und DIN EN ISO 10218-2, innerhalb derer die jeweils kritischen Grenzwerte gemäß Risikobeurteilung und Benutzerinformation festgelegt werden (vgl. [7, 8, 1]). Neben der wie bei den Betriebsarten der Handführung und der Geschwindigkeits- und Abstandsüberwachung vorhandenen Begrenzung bezüglich der Maschinen- beziehungsweise Robotergeschwindigkeit ergibt sich bei diesem Schutzprinzip zusätzlich der generelle Nachteil einer erheblichen Gewichtsbegrenzung der zum Einsatz kommenden Maschinen beziehungsweise Robotersysteme, die normativ vorgesehen ist, um hierdurch die potenzielle Kollisionsmasse möglichst gering zu halten (vgl. [1]).
Die Betriebsweise des sicherheitsbewerteten, überwachten Halts ist zum einen für die sogenannte „Koexistenz“ von Mensch und Maschine geeignet, bei der zwar kein Schutzzaun erforderlich ist, jedoch keine Teilung des Arbeitsraums erfolgt. Zum anderen kann sie auch im Rahmen einer „sequenziellen Kooperation“ zwischen Mensch und Maschine eingesetzt werden, bei der sich der Mensch und die Maschine zwar einen Arbeitsraum teilen, dort allerdings nicht gleichzeitig arbeiten [4]. Bei dieser Betriebsart muss die Maschine bei einem Personenzutritt in den Kollaborationsraum sicher anhalten, wobei auch zunächst eine gesteuerte Geschwindigkeitsreduzierung mit anschließendem Stopp der Kategorie 2 mit sicherer Überwachung nach der Norm DIN EN ISO 10218-1 möglich ist (vgl. [1]; [9], S. 16 ff.). Die sichere Trennung zwischen Mensch und Maschine erfolgt hierbei zumeist durch verhältnismäßig kostenintensive optische Sensorsysteme, welche die Arbeitsräume überwachen und dynamische Schutzzonen berechnen. Des Weiteren werden kapazitive Sensoren eingesetzt, die die Annäherung des Menschen an die Maschine im Nahbereich erkennen (vgl. [1]). Der wesentliche Nachteil kapazitiver Näherungssensoren ist wiederum deren sehr hohe Empfindlichkeit gegenüber äußeren Einflüssen wie zum Beispiel Feuchtigkeit oder Verschmutzung (vgl. [10]).
Die zuvor dargestellten Nachteile bestehender MMK-Anwendungen sind die Basis zur Motivation im Rahmen des BMBF-Forschungsvorhabens „MagnOtrop“ die technische Herausforderung zu bewältigen, die Technologie dreidimensionaler, isotroper elektromagnetischer Kugel-Felder zur digitalisierten Bewegungserkennung mittels der Integration von Künstlicher Intelligenz (KI) in Form des Maschinellen Lernens auf die bislang noch nicht erschlossene Anwendung im industriellen Umfeld zu projizieren und damit die wirtschaftliche Anwendung von MMK-Technologien im Rahmen von Produktionsprozessen zu ermöglichen.
Besonders interessant ist diese innovative Technologie als mögliche kostengünstige Alternative für optische Sensorsysteme im Zusammenhang mit dem Schutzprinzip des sicherheitsbewerteten, überwachten Halts. Dieses Schutzprinzip verfügt darüber hinaus – im Vergleich zu den weiteren oben beschriebenen Schutzprinzipien – über den elementaren Vorteil, dass die Maschine hier mit der maximal möglichen Geschwindigkeit arbeiten kann, sofern sich kein Mensch in einem definierten Kollaborationsraum befindet. Zusätzlich zum Kostenvorteil ergeben sich bei der Verwendung von elektromagnetischen Feldern gegenüber optischen Sensorsystemen im Zusammenhang mit der Bewegungserkennung die grundlegenden Vorteile, dass zwischen der Sendeantenne und der mobilen Empfängereinheit kein Sichtkontakt erforderlich ist (eine sichere Detektion kann dementsprechend auch durch störende Objekte hindurch erfolgen) und eine sehr hohe Benutzerfreundlichkeit gewährleistet werden kann (vgl. [11], S. 64). Vorteilhaft im Vergleich zu kapazitiven Näherungssensoren ist vor allem die deutlich geringere Empfindlichkeit gegenüber äußeren Einflüssen wie zum Beispiel Feuchtigkeit oder Verschmutzung, die in industriellen Anwendungen häufig gegeben sind.
2 Projektziele
Das wesentliche Ziel, das innerhalb des Forschungsvorhabens „MagnOtrop“ verfolgt wird, ist die sichere Projizierung der innovativen Technologie dreidimensionaler, isotroper elektromagnetischer Kugel-Felder zur digitalisierten Bewegungserkennung auf das bislang noch nicht erschlossene Anwendungsfeld der Mensch-Maschine-Kollaboration.
Zum Erreichen des Projektziels ist die Integration von KI in Form des Maschinellen Lernens geplant, die es erlauben soll, das zu entwickelnde aus einer 3D-Sende-Antenne und einer 3D-Empfänger-Antenne bestehende neuartige Sensorsystem mithilfe des sukzessiven Anlernens zu erarbeitender Korrekturalgorithmen erstmalig auch unter dem störenden Einfluss metallischer Objekte im Rahmen von Produktionsprozessen zuverlässig einsetzen zu können. Dabei wird die 3D-Sende-Antenne an die zu überwachende Maschine appliziert und bildet um diese ein kugelförmiges elektromagnetisches Feld. Die 3D-Empfänger-Antenne wird in die Arbeitskleidung des zu sichernden Mitarbeiters integriert, dessen Bewegungen innerhalb des Kugel-Feldes millimetergenau erkannt werden.
Somit steht diese Technologie neuen, bisher nicht realisierbaren Anwendungsfeldern mit folgenden Optimierungspotenzialen zur Verfügung:
- Geringere Kosten
- Höhere Robustheit und Benutzerfreundlichkeit
- Kein Sichtkontakt zwischen Sendeantenne und mobiler Empfängereinheit erforderlich
- Möglichkeit zur Reduzierung der benötigten Elektronikhardware
- Aufgrund der zuvor genannten wesentlichen Vorteile ist mit einer Steigerung des Verbreitungsgrades von MMK-Technologien sowie der Verbesserung der Arbeitsergonomie im Rahmen der industriellen Produktion zu rechnen.
3 Technischer Lösungsansatz
Zur Umsetzung der geplanten Funktionalität ist zunächst ein Feldgenerator zu entwickeln, der das beziehungsweise die magnetische(n) Kugelfeld(er) erzeugen kann. Dessen 3D-Emitter-Antenne soll dann an der jeweiligen zu sichernden Maschine appliziert werden und um diese ein kugelförmiges elektromagnetisches Feld aufbauen, innerhalb dessen die Bewegungen einer 3D-Receiver-Antenne millimetergenau erkannt werden. Die Receiver-Einheit soll wiederum in Form einer „wearable solution“ anwendungsfallabhängig in die Arbeitskleidung (zum Beispiel in Sicherheitsschuhe beziehungsweise -handschuhe oder entsprechende Armbänder) der zu sichernden Produktionsmitarbeiter integriert werden. Auf diese Weise kann zusätzlich zur sicheren Erkennung des Menschen durch die Maschine auch die Erkennung von Gefahrenbereichen durch den Menschen erreicht werden. So wird der Mitarbeiter ein Feedback seitens der „wearable solution“ erhalten, zum Beispiel durch ein Vibrationssignal, ein visuelles Feedback in Form eines Ampelsystems oder ein akustisches Signal, sobald sie sich in definierten Gefahrenbereichen aufhalten. Hierdurch entsteht indessen ein bidirektionaler Kommunikationskanal zwischen Mensch und Maschine, der es erlaubt, dass die Produktionsmitarbeiter im Falle des Auslösens eines Signals bewusst auf dieses reagieren und damit eventuell unbewusst verursachte, unnötige Maschinenstandzeiten vermeiden beziehungsweise die Produktionseffizienz steigern können.
Zusätzlich zu den zuvor beschriebenen Vorteilen ergibt sich durch den Einsatz eines solchen neuartigen Sensorsystems das mögliche Nutzenpotenzial, ein sogenanntes „Motion-Mining“ auf der Basis aufgezeichneter Sensordaten im Hinblick auf manuelle Bewegungsabläufe im Rahmen von Produktionsprozessen zu vollziehen, welches dazu dienen kann, objektive Prozesskennzahlen bezüglich der Effizienz und Ergonomie von Produktionsabläufen zu errechnen und hieraus Verbesserungspotenziale zuverlässig und anonymisiert aufzudecken (vgl. [12]).
Der Grund dafür, dass das mit der Bewegungserkennung mittels elektromagnetischer Kugel-Felder einhergehende oben beschriebene immense Potenzial im Zusammenhang mit industriellen Anwendungen aktuell noch nicht genutzt wird, ist der bei dieser Technologie zu berücksichtigende störende Einfluss ferromagnetischer Materialien. Diesem Einfluss soll im Rahmen des im Projektvorhaben zu erforschenden und im Folgenden näher beschriebenen innovativen Lösungsansatzes mithilfe einer KI-Integration in Form des Maschinellen Lernens entgegengewirkt werden.
Die elektromagnetische 3D-Positions- und Bewegungserkennung basiert auf stationären magnetischen Wechselfeldern im Frequenzbereich von 10 kHz bis 150 kHz. Die Emitter- und Receiver-Antennen sind dabei isotrop ausgelegt, das heißt sie sind in jeder der drei Raumachsen gleich empfindlich. Durch vektorielle Addition der Signale der drei Empfänger-Achsen ergibt sich der Betrag der Feldstärke im Raum. Die drei räumlichen Achsen-Koordinaten x, y und z sowie die drei Rotationswerte um die drei Raumachsen des Koordinatensystems erhält man wiederum mithilfe der Zuordnung der drei Empfängersignale zu den Signalen der drei räumlich versetzten Spulen der Emitter-Antenne.
Durch eine zeit- oder frequenzdiskrete Überlagerung der Magnetfelder dreier um jeweils 90° räumlich versetzter Antennen-Spulen ergibt sich hierbei ein isotropes Kugelfeld. In Ergänzung der Auswertung der drei ebenfalls räumlich um 90° versetzten Empfängerspulen und eine entsprechende mathematische Zuordnung zu den drei Einzelsignalen des Emitters erhält man auf diese Weise sechs messbare Freiheitsgrade, nämlich drei räumliche Achsenkoordinaten und drei Rotationswinkel. Dadurch ist sowohl die Position als auch die Rotation eines Körpers im Raum eindeutig definiert und somit messbar.
Mit einer einzelnen, aus drei Einzelspulen aufgebauten, isotropen magnetischen 3D-Emitter-Antenne und einer ebenfalls aus drei Einzelspulen aufgebauten, isotropen magnetischen 3D-Receiver-Antenne lässt sich demnach zu moderaten Kosten ein dreidimensionales Positions- und Bewegungserkennungssystem realisieren, welches darüber hinaus über eine sehr hohe Präzision und Zuverlässigkeit auch unter sehr rauen Umgebungsbedingungen verfügt. Der Messbereich eines solchen Systems kann – je nach Antennengröße und Sendeleistung – zwischen etwa 0,5 m und maximal 15 m eingestellt werden, wobei die Messgenauigkeit zum Beispiel bei einem Messbereich von einem Meter bei etwa einem Millimeter liegt.
Allerdings kann die Messgenauigkeit der zuvor beschriebenen Technologie – wie bereits erwähnt – durch sich in der näheren Umgebung des Sensorsystems befindliche ferromagnetische Materialien negativ beeinflusst werden. Aus einer theoretischen Vorbetrachtung heraus, lassen sich hierbei grundlegend die folgenden vier Störszenarien unterscheiden, die es innerhalb des geplanten Forschungsprojektes zu untersuchen gilt:
- Kennliniensprung durch die Annäherung metallischer Objekte in direkter Nähe zum Emitter
- Veränderung der Kennliniensteigung durch metallische Objekte kurz hinter dem Emitter
- Quadratisch ansteigender Messwertfehler durch große metallische Objekte in größerem Abstand hinter dem Emitter
- Einbuchtung der Sensorkennlinie aufgrund der Anordnung metallischer Objekte zwischen Emitter und Receiver
- Zur Veranschaulichung sind die zuvor genannten vier Störszenarien im Rahmen der Bewegungserkennung mittels elektromagnetischer Felder in Bild 1 visuell dargestellt. Bei der Erforschung des neuartigen Lösungsansatzes zur Vermeidung beziehungsweise Verminderung des störenden Einflusses von ferromagnetischen Materialien im Rahmen der Bewegungserkennung mittels elektromagnetischer Kugel-Felder gilt es daher zunächst, den Zusammenhang zwischen Störobjekten unterschiedlicher Größe und Materialien und den daraus resultierenden Messwertabweichungen in umfangreichen Praxismessungen zu untersuchen. Im Anschluss an die messtechnische Erfassung und Validierung des Einflussverhaltens der unterschiedlichen auszuwählenden Störobjekte nach Größe, Abstand, Position und Material sollen entsprechende Algorithmen und Gegenmaßnahmen zur Messwertkorrektur erarbeitet werden. Als Beispiel kann hier die Einbindung von Referenzantennen zur Korrekturberechnung angeführt werden. Die Referenzantenne ist hierbei dort anzubringen, wo die Störgröße beziehungsweise das sich annähernde metallische Objekt in das System eingreift. Mithilfe einer im Bereich des Emitters angebrachten Referenzantenne lassen sich die Störszenarien „Kennliniensprung“ und „Veränderung der Kennliniensteigung“ korrigieren, diesen Zusammenhang gibt beispielhaft das Bild 2 wieder.
Die Kompensation des Messfehlers erfolgt dabei rechnerisch: Die Sendeleistung des Emitters wird so eingestellt, dass das Signal an einer ersten Referenzantenne dem erwarteten Wert (Führungsgröße) entspricht. Dadurch wird ein Kennliniensprung korrigiert. Weicht darüber hinaus das Messergebnis von dem an einer zweiten Referenzantenne erwarteten Signal ab, so liegt eine Divergenz hinsichtlich der Kennliniensteilheit vor, die dann rechnerisch von einem Mikro-Rechner korrigiert wird. Analog beziehungsweise auf ähnliche Weise kann auch die Korrektur im Rahmen des Störszenarios „quadratisch ansteigender Messfehler“ erfolgen.
In Bezug auf das Störszenario „Einbuchtung der Sensorkennlinie“, bei dem metallische Objekte zwischen Emitter und Receiver angeordnet sind, ist der Einsatz von Referenzantennen in Kombination mit Algorithmen zur Messwertkorrektur hingegen nicht ausreichend. Tritt in der Praxis ein solches Störszenario auf, bei dem das elektromagnetische Feld durch ein metallisches Objekt zwischen Emitter und Receiver gestört beziehungsweise verändert wird, so ist eine Messwertkorrektur durch eine KI-Integration in Form des Maschinellen Lernens geplant.
Zur sicheren Erkennung der exakten Position einer in einen definierten Gefahrenbereich eintretenden Person muss die neue geometrische Form des elektromagnetischen Feldes für eine entsprechende Korrektur der Messwerte bekannt sein. Um dieses zu gewährleisten, soll im Verlaufe des Projektvorhabens „MagnOtrop“ die Methode des überwachten Lernens (Supervised Learning) zum Einsatz kommen. In diesem Bereich des Maschinellen Lernens werden Datenpaare aus Eingangs- und Ergebnisdaten gebildet. Während des Lernvorgangs werden die Parameter eines neuronalen Netzes so optimiert, dass für alle eingegebenen Daten das korrekte Ergebnis ausgegeben wird und das insbesondere auch dann, wenn die Eingangsdaten nicht Teil der Trainingsdaten waren (vgl. [13]). Hiermit wird angestrebt, erstmalig einen sicheren Betrieb der elektromagnetischen 3D-Positions- und Bewegungserkennung im metallischen Umfeld zu realisieren.
4 Ausblick und Erfolgs aussichten
Der mit dem neuartigen Sensorsystem angezielte Markt für Industriemaschinen verfügt über ein enormes Marktvolumen, haben doch alleine die sieben größten börsennotierten Hersteller von Industriemaschinen im Jahr 2017 einen Umsatz von 388,71 Milliarden US-Dollar erwirtschaftet (vgl. [14]). Vor allem für das für die innerhalb des Projektvorhabens angestrebte Systemlösung besonders relevante Marktsegment der Industrieroboter werden hier bis zum Jahr 2021 jährliche Wachstumsraten von durchschnittlich 14 % prognostiziert (vgl. [3], S. 18) – wodurch sich wiederum ein vielversprechendes Marktpotenzial ergibt.
Das FuE-Projekt „MagnOtrop“ ist ein Kooperationsprojekt der Firmen Scemtec Sensor Technology GmbH und plastec Kunststofftechnikum Oberberg GmbH sowie der Technischen Hochschule Köln mit den Instituten Cologne Institute for Digital Ecosystems (CIDE) und Institut für Allgemeinen Maschinenbau (IAM).
Dieses Forschungs- und Entwicklungsprojekt wird durch das Bundesministerium für Bildung und Forschung (BMBF) im Programm „Zukunft der Wertschöpfung – Forschung zu Produktion, Dienstleistung und Arbeit“ (Förderkennzeichen 02P19K010 bis 02P19K012) gefördert und vom Projektträger Karlsruhe (PTKA) betreut. Die Verantwortung für den Inhalt dieser Veröffentlichung liegt bei den Autoren.
Literatur
- Mensch-Roboter-Kollaboration: So arbeiten Mensch und Maschine sicher zusammen. 2018. Internet: https://www.vde.com/topics-de/industry/aktuelles/mensch-roboter-kollaboration. Zugriff am 23.04.2019
- Institut für angewandte Arbeitswissenschaft e. V. (ifaa): Zahlen / Daten / Fakten – Mensch-Roboter-Kollaboration. 2017. Internet: https://www.arbeitswissenschaft.net/fileadmin/user_upload/Downloads/Factsheet_Mensch_Roboter_Kollaboration.pdf, Zugriff am 23.08.2018
- Maienschein, B.: „Kollege“ Roboter: Freund oder Feind?. In: MM Logistik, 6 (2018), S. 18–21
- Nördinger, S.: 4 Konzepte für eine sichere Mensch-Roboter-Kollaboration. 2017. Internet: https://www.produktion.de/trends-innovationen/id-4-konzepte-fuer-eine-sichere-mensch-roboter-kollaboration-120.html. Zugriff am 24.04.2019
- Deutsches Institut für Normung e. V. (Hrsg.): DIN EN ISO 13849-1 – Sicherheit von Maschinen – Sicherheitsbezogene Teile von Steuerungen – Teil 1: Allgemeine Gestaltungsleitsätze. Berlin: Beuth-Verlag GmbH, 2016
- Deutsches Institut für Normung e. V. (Hrsg.): DIN EN ISO 13849-2 – Sicherheit von Maschinen – Sicherheitsbezogene Teile von Steuerungen – Teil 2: Validierung. Berlin: Beuth-Verlag GmbH, 2013
- Deutsches Institut für Normung e. V. (Hrsg.): DIN ISO/TS 15066 – Roboter und Robotikgeräte – Kollaborierende Roboter. Berlin: Beuth-Verlag GmbH, 2017
- Deutsches Institut für Normung e. V. (Hrsg.): DIN EN ISO 10218-2 – Industrieroboter – Sicherheitsanforderungen – Teil 2: Robotersysteme und Integration. Berlin: Beuth-Verlag GmbH, 2012
- Deutsches Institut für Normung e. V. (Hrsg.): DIN EN ISO 10218-1 – Industrieroboter – Sicherheitsanforderungen – Teil 1: Roboter. Berlin: Beuth-Verlag GmbH, 2012
- Rockwell Automation: Grundbegriffe der Sensorik – Lehrgangs-Handbuch. 2001. Internet: http://www.swibox.ch/fileadmin/user_upload/elektrokomponenten/Diverse_Grundlagen/Grundlagebegriffe_der_ Sensorik.pdf. Zugriff am 23.08.2018
- Rojas Cuevas, A.: AR / VR Technology – Will it change the world? In: Premo S.L. (Hrsg.): VR – EM motion tracking sensors & applications. Málaga, 2017. – ISBN 84–697–8100–5
- MotionMiners GmbH, 2019. Internet: https://www.motionminers.com/index.html. Zugriff am 08.05.2019
- Alpayadin, E.: Introduction to machine learning – third edition. The MIT Press Cambridge, Massachusetts, 2014
- Statista, 2018: Größte Hersteller von Industriemaschinen weltweit nach Umsatz im Jahr 2017 (in Milliarden US-Dollar). Internet: https://de.statista.com/statistik/daten/studie/478377/umfrage/ranking-der-hersteller-von-industriemaschinen-nach-umsatz/. Zugriff am 05.04.2019
Dipl.-Ing. Joachim Uhl
SCEMTEC Sensor Technology GmbH
Wilhelm-Grümer-Weg 20, 51674 Wiehl
Tel. +41 2262 / 9999-615
j.uhl@scemtecsensor.com
www.scemtecsensor.com
Dr. Tim Siebels
Büro für Logistikforschung
Stübbenstr. 6, 44137 Dortmund
Tel. +49 152 / 248 346 40
ts@logistik-innovationen.de