Fünf Maßnahmen für den präventiven Schutz von Werkzeugmaschinen
Plötzliche Ausfälle von Werkzeugmaschinen können für Betriebe aufgrund des daraus resultierenden Produktionsstopps gravierende Geldverluste nach sich ziehen. Fünf wertvolle Tipps helfen Fertigungsunternehmen, dies zu vermeiden.
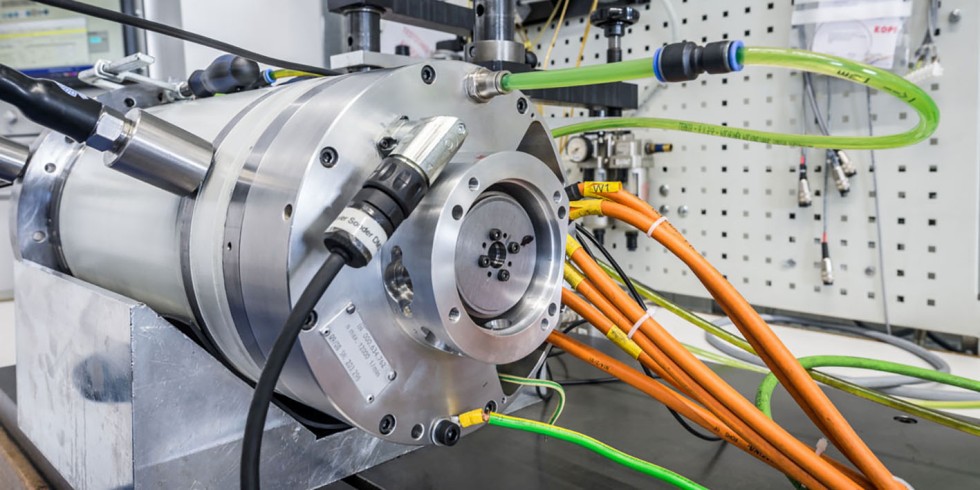
Kommt es aufgrund eines Spindel-Crashs zum Ausfall einer Werkzeugmaschine, so ist dies häufig auf einen Bedienungsfehler zurückzuführen.
Foto: Kern GmbH
Neben dem Zwangs-Stopp und dem Verlust an Produktionszeit kann die Reparatur – je nach Verfügbarkeit von Ersatzteilen – außerdem viel Zeit in Anspruch nehmen. Daher empfiehlt es sich, die Werkzeugmaschinen durch präventive Maßnahmen zu schützen.
„Um Beschädigungen an Werkzeugmaschinen nachhaltig zu verhindern, können die Betriebe selbst tätig werden und verschiedene Maßnahmen umsetzen“, erklärt Maschinenbauexperte Markus Kern. Im folgenden Gastbeitrag verrät er fünf Tipps, die den Verantwortlichen dabei helfen, die Lebensdauer ihrer Werkzeugmaschinen zu maximieren und damit Produktionsstopps zu vermeiden.
Wichtig für hohe Produktivität: Schulung im Umgang mit Werkzeugmaschinen
Kommt es aufgrund eines Spindel-Crashs zum Ausfall einer Werkzeugmaschine, ist hierfür häufig ein Bedienungsfehler verantwortlich. Daher sollte die fachgerechte Ausbildung und regelmäßige Schulung der einzelnen Mitarbeiter höchste Priorität genießen. Zudem bietet es sich an, vornehmlich qualifizierte Fachkräfte zu beschäftigen.
Spindeln von Werkzeugmaschinen bedürfen einer regelmäßigen Überprüfung, um plötzliche Ausfälle zu vermeiden. Dabei gilt es unter anderem, den Öl- und Kühlmitteldruck sowie die Drehzahlen unter die Lupe zu nehmen und bei Bedarf zu korrigieren. Ferner sollten die Sauberkeit der Kühleinheiten sowie die Funktionstüchtigkeit der Hydraulik sichergestellt sein. Zudem sollte alle vier Monate überprüft werden, ob ein Austausch der Drehdurchführung notwendig ist.
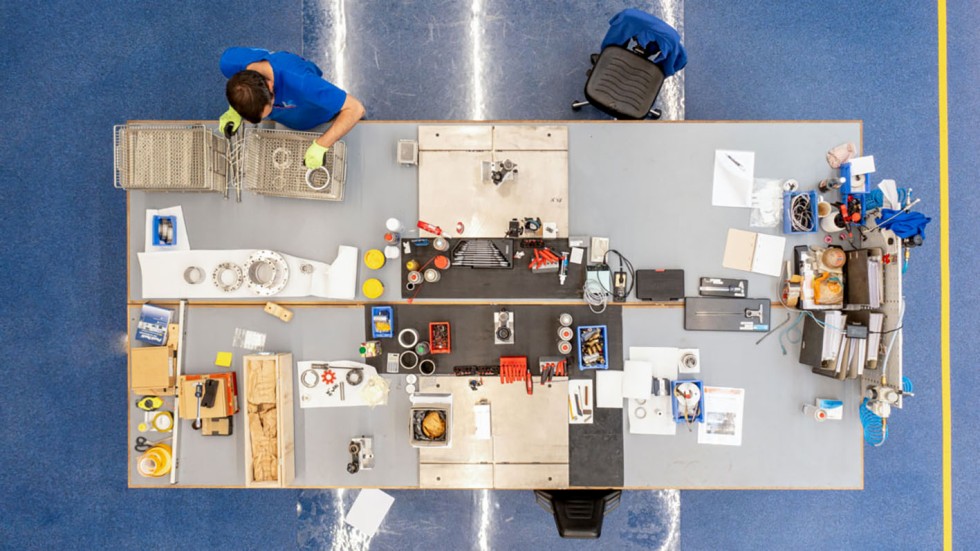
Ein professioneller Vor-Ort-Service ist in der Regel bestens qualifiziert, eventuelle Lagerschäden frühzeitig zu diagnostizieren und eine Flutung der Spindel im Vorfeld zu erkennen.
Foto: Kern GmbH
Regelmäßige Überprüfung hat Vorrang vor der Reparatur
Arbeiten die Spindeln von Werkzeugmaschinen nach einiger Zeit unpräzise oder verursachen sie „verdächtige“ Geräusche, sollten sie zwingend repariert werden. Nutzt man sie bis zum letzten Moment, kann dies schwerwiegende Folgeschäden nach sich ziehen. Zudem ist eine frühzeitige Reparatur häufig kostengünstiger als ein endgültiger Austausch. Und er schont die Umwelt, da weniger Metallschrott produziert wird. Wird die Wartung fachgerecht und qualitativ hochwertig durchgeführt, stellt sie zudem die bestmögliche Lebensdauer einer Spindel sicher.
Spindeln regelmäßig „unter die Lupe nehmen“
Die Spindeln von Werkzeugmaschinen sollten regelmäßig einer umfassenden Begutachtung unterzogen werden. Mit einer derartigen Überprüfung können die Betriebe einen Vor-Ort-Service beauftragen, der potenzielle Lagerschäden frühzeitig diagnostizieren und die Gefahr auf eine Flutung der Spindel erkennen kann. Den Einbau der Spindel sollten ausnahmslos Profis übernehmen, die sicherstellen, dass alle Einbauparameter eingehalten werden. Auf kostengünstige Alternativen sollten die Unternehmen hierbei verzichten.
Moderne Werkzeugmaschinen sind meist durch Frühwarnsysteme geschützt, die die Spindeln bei einem möglichen Lagerschaden automatisch abschalten. Zudem überwachen sie die Werte der Maschinen und warnen bei Fehleinstellungen das Personal. Sollte es dennoch zu einem Crash kommen, werden die Lager durch Dämpfer vor größeren Folgeschäden bewahrt. Da diese Systeme fehlerhaft sein können, sind zusätzlich menschliche Kontrollen durchzuführen.
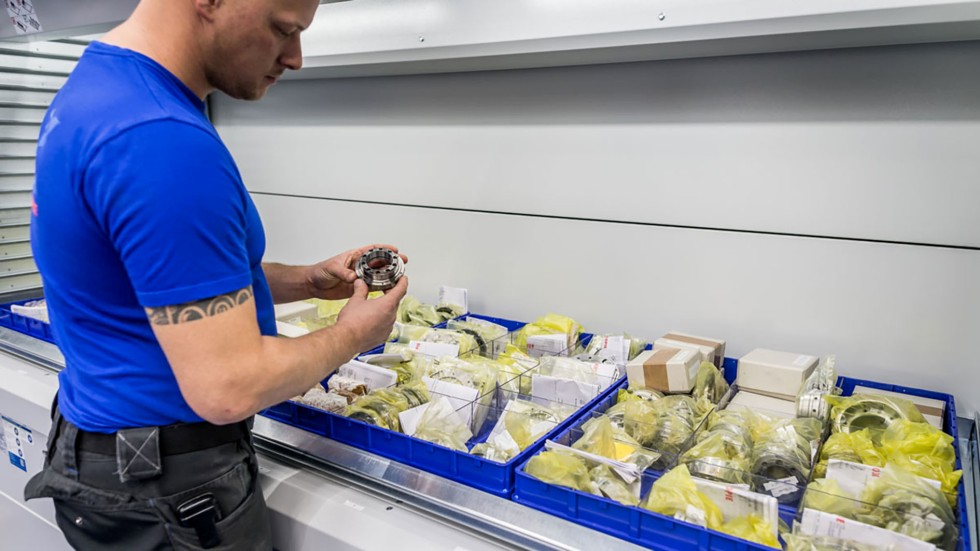
Ein qualifizierter Betrieb arbeitet herstellerunabhängig und hält die wichtigsten Ersatzteile vor. Zum Service gehören die Laufzeitoptimierung der Spindeln und dazu erforderliche tiefgehende Ausfallanalysen.
Foto: Kern GmbH
Werkzeugmaschinen durch neue Technologien schützen – der Experte berät
Als Geschäftsführer und Firmengründer der Kern GmbH hat Markus Kern über 30 Jahre praktische handwerkliche Erfahrung mit der Spindel und ein umfangreiches Wissen über Spindeltechnik (https://spindelfullservice.com). In seinem Betrieb in Burladingen in Baden-Württemberg geht es um eine ganzheitliche Instandsetzung, Optimierung und Modifikation von Spindeln, sodass Kunden sogar gerne von einer „Tuning-Werkstatt“ sprechen. Dabei arbeitet das Unternehmen zu 100 Prozent herstellerunabhängig und kann bereits auf mehr als 14.000 reparierte Spindeleinheiten zurückblicken – von jedem bekannten Hersteller auf dem Markt. Die Laufzeitoptimierung und dazu erforderliche tiefgehende Ausfallanalysen, die zu einer hohen Kostenersparnis führen können, sieht der Betrieb als seinen Schwerpunkt an. So konnte die Ausfallquote bereits bei mehr als 500 Kunden reduziert werden.
Das könnte Sie auch interessieren:
Schneller „Gesundheitscheck“ für die Werkzeugmaschine
Hohe Anlageneffizienz durch intelligent geplante Rüstvorgänge
Oft vernachlässigt: Digitale Identitäten in der Betriebstechnik