Verzahnungsherstellung: Das sind die neuesten Trends
Neue Entwicklungen in der Werkzeugtechnologie und moderne 5-Achs-Maschinen mit interpolierenden Achsen machen es möglich, Verzahnungen auch ohne spezialisierte, nur für diesen einen Zweck nutzbare Maschinen herzustellen. Gezeigt wird, welche Verfahren aktuell im Trend liegen und welche Werkzeuge die Wirtschaftlichkeit optimieren.
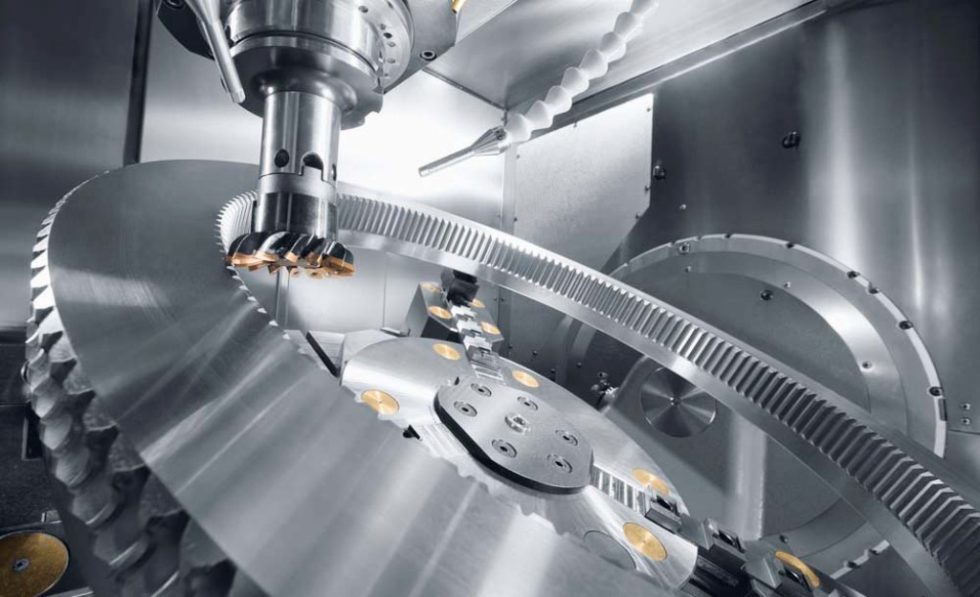
Die Verzahnungsherstellung auf 5-Achs-Bearbeitungszentren liegt voll im Trend. Videos diverser Werkzeugmaschinen- und Werkzeughersteller erläutern die Abläufe.
Foto: Hermle
Viele Fertigungsverfahren führen in der Verzahnungsherstellung zum Ziel. Lange dominierende Techniken wie Stoßen oder Räumen werden durch Wälzschälen bzw. „Skiven“ abgelöst – dank intelligenter Softwareunterstützung und moderner NC-Steuerungen sowie NC-Maschinen wird dies möglich. Eine große Rolle spielen Entwicklungen im Werkzeugbereich wie optimierte Geometrien, neue Hartmetalllegierungen und moderne Beschichtungen. Auch die Wiederaufbereitung der meistens kostenintensiven Hochleistungswerkzeuge ist ein wichtiges Thema. Vor der Erläuterung der relevanten Fertigungstechnologien lohnt sich jedoch ein kurzer Exkurs in die Grundlagen. Teil 1 des Artikels beschreibt Arten und Einsatzgebiete von Verzahnungen sowie die optimale Verfahrensauswahl.
Ohne Verzahnungen läuft in der Antriebstechnik nichts
Zahnräder sind in der Technik nicht wegzudenken: Sie übertragen Drehmomente von einer Welle auf eine andere; können Drehrichtung, Drehmoment und -zahl verändern. Drehbewegungen lassen sich in Kombination mit einer Zahnstange in lineare Bewegungen wandeln und umgekehrt. Nicht nur in Getrieben und Antriebswellen von Kraftfahrzeugen sind Zahnräder unverzichtbare Komponenten. Es gibt sie in sehr variablen Größen für die verschiedensten Einsatzbereiche – von Großteilen für die Windkraftbranche oder für Kraftwerke bis zu filigranen Komponenten für die Uhrenindustrie. Zahnradgetriebe zeichnen sich dadurch aus, dass sie formschlüssig und damit schlupffrei arbeiten.
Automobilindustrie „gibt den Ton an“
Der bedeutendste Einsatzbereich von Zahnrädern ist der Automobil- und der Nutzfahrzeugbau. Nur hochgenau bearbeitete Zahnräder garantieren die optimale Funktion von Getrieben in Fahrzeugen aller Art. Moderne Getriebe verlangen eine zuverlässige Drehmomentübertragung bei hoher Leistungsdichte, niedrigem Gewicht und minimaler Geräuscherzeugung. Aus betriebswirtschaftlicher Sicht stehen möglichst geringe Stück- und Lebenszykluskosten im Zentrum.
Auch der aktuelle Trend zur E-Mobilität ändert daran nichts: Getriebe gelten als Schlüsseltechnologie zur Leistungsoptimierung des Antriebsstrangs. Die Anforderungen an die Zahnrad- und Oberflächenqualität steigen sogar, denn Getriebegeräusche werden nach dem Wegfall des Verbrennungsmotors jetzt viel deutlicher wahrgenommen. Dadurch gewinnen bei der Endbearbeitung Verfahren wie das Verzahnungshonen und das Wälzpolierschleifen an Bedeutung – doch dazu später weitere Details.
Anlagenbau benötigt XXL-Dimensionen
Ganz andere Größenordnungen und Beanspruchungen als im Automobilbau sind im Maschinen- und Anlagenbau an der Tagesordnung. Ein spektakuläres Beispiel ist ein 190 Tonnen schweres Getriebe, an dessen Herstellung die FMCD GmbH, Hattingen, maßgeblich beteiligt war.
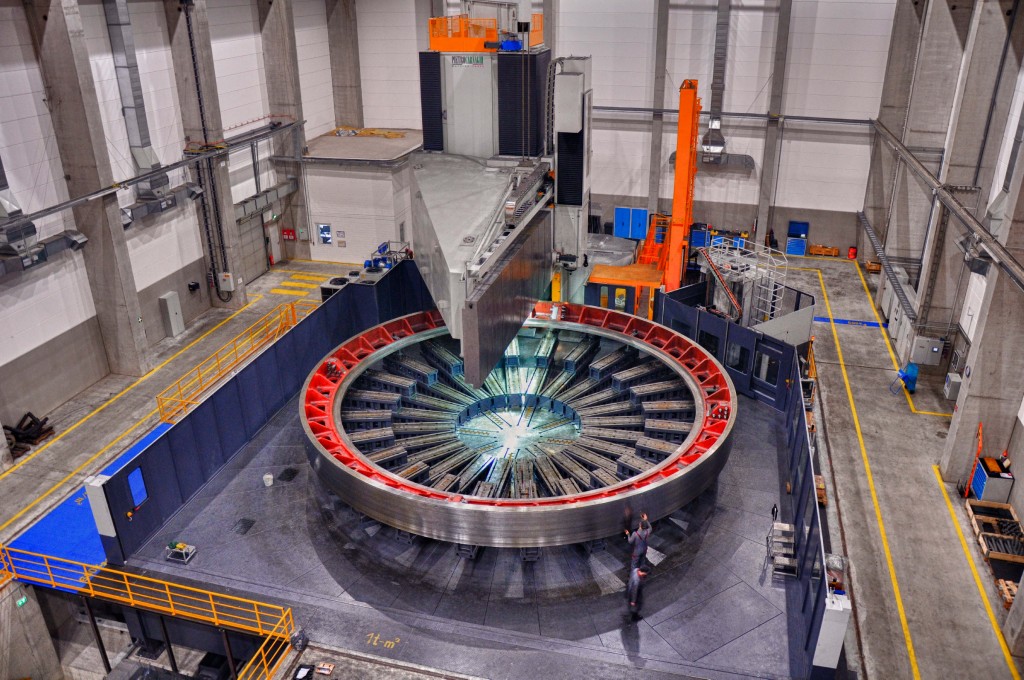
Die Firma FCMD in Hattingen führt selbst Bearbeitungen an Großbauteilen durch. Das Gesamtgetriebe für einWalzwerk entstand aus einer Kooperation mehrerer Firmen in der Groupe CIF.
Foto: FCMD GmbH
Es kommt inzwischen in einem Walzwerk in Südfrankreich zum Einsatz. Auf der Warmbreitbandstraße, die damit angetrieben wird, werden Brammen mehrfach ausgewalzt, um die gewünschte Dicke zu erreichen. Insgesamt sind elf Walzen beteiligt, die für eine Produktion von vier Millionen Tonnen Stahl-Coils im Jahr ausgelegt sind. Gefordert war eine hohe Leistungsdichte, um ausreichend Kraft auf begrenztem Raum zu übertragen. Das imponierende Getriebe erzielt eine Leistung von neun Megawatt, hat eine Länge von fast neun Metern und eine Höhe von annähernd fünf Metern. Auch der Wechsel zwischen den Betriebszuständen war aufgrund der starken Beanspruchung eine Herausforderung: mit Last- und Drehzahländerungen sowie periodischem Aussetzen, was auch Anlauf- und Bremsvorgänge des Getriebes einschließt.
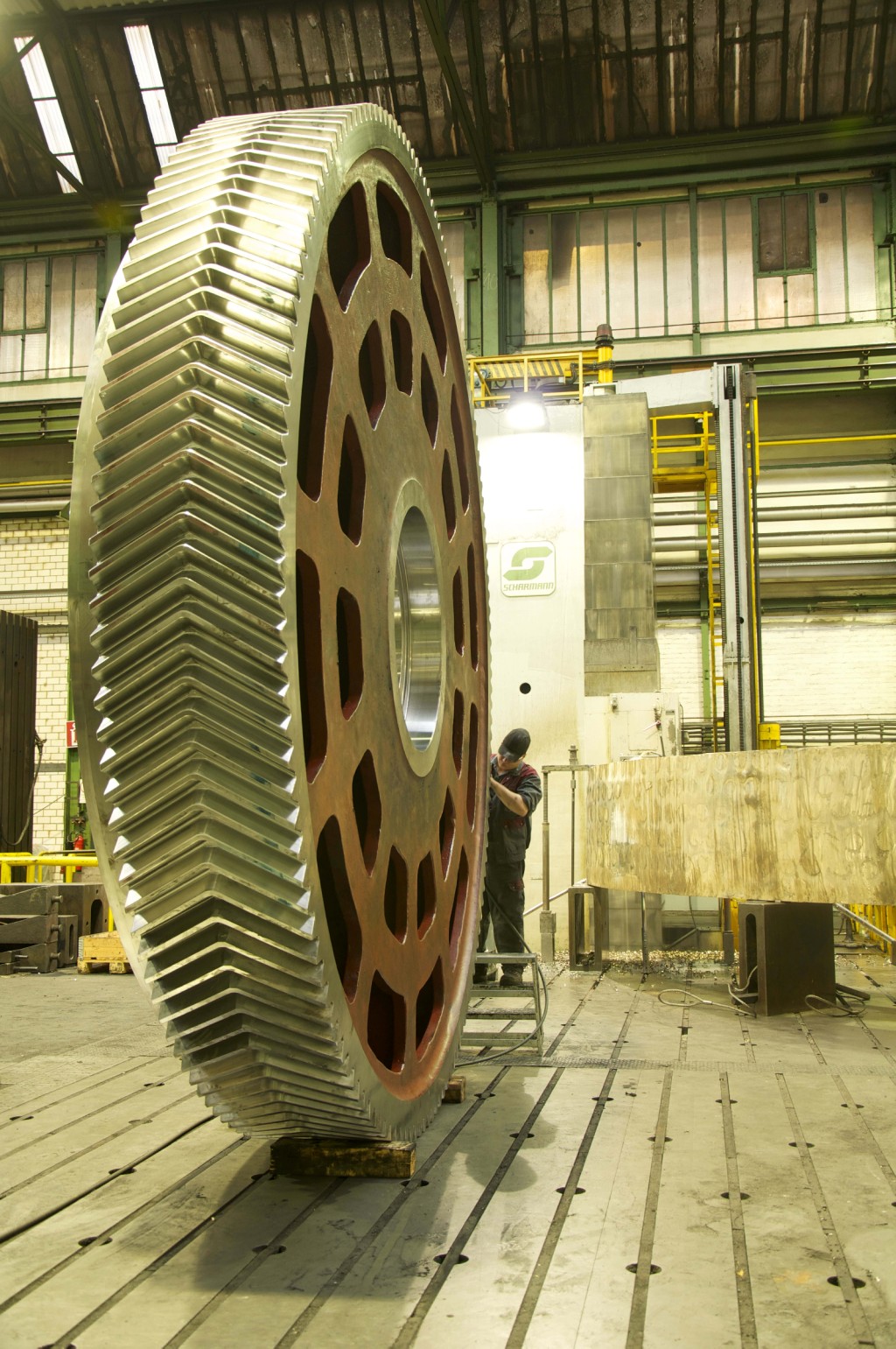
Durch die Größe der eingesetzten Zahnräder sowie eine optimale Kraftumsetzung konnte mit dem Sondergetriebe eine Leistung von 9 MW erreicht werden.
Foto: FCMD GmbH
Arten von Verzahnungen
Zahnräder sind seit etwa 300 Jahre v. Ch. bekannt. Seit dem neunten Jahrhundert n. Ch. wurden sie in Europa in Wassermühlen genutzt. Je nach Bauform lassen sich Außen- und Innenverzahnungen, Gerad- und Schrägverzahnungen, Stirnräder, Kegelräder, Schrauben- oder Hypoidverzahnungen sowie auch Schneckenformen unterscheiden.
Die größte Verbreitung im Maschinenbau hat die Zahnform einer Evolvente. Der Modul (Durchmesserteilung) ist ein Maß für die Größe der Zähne und ergibt sich aus dem Teilkreisdurchmesser, geteilt durch die Zähnezahl. Das Profil entspricht der Form des Werkzeugs, mit dem das Zahnrad hergestellt wird. Das Bezugsprofil heute gebräuchlicher Zahnräder ist in DIN 867 genormt.
Vor- und Fertigbearbeitung von Verzahnungen
Die Verzahnverfahren lassen sich unter Berücksichtigung der Maschinenkinematik in formende und wälzende Verfahren unterteilen. Beim Formverfahren hat das Werkzeug (Formfräser, Schleifscheibe, Umformwerkzeug) die Kontur der zu fertigenden Zahnlücke. In aller Regel wird jede Zahnlücke einzeln gefertigt und dann das „Werkrad“ (das Rohteil, aus dem das Zahnrad entsteht) zur Bearbeitung der nächsten Zahnlücke um den Winkel der Zahnteilung gedreht. Für jede Werkradauslegung, auch bei gleichem Modul, ist ein individuelles Werkzeug erforderlich, das genau dem Zahnlückenprofil entspricht.
Bei den Wälzverfahren wird in der Verzahnmaschine durch die Abwälzbewegung des Werkzeugs auf dem Wälzkreiszylinder des Werkrads die gewünschte Zahnflankenform erzeugt. Der Wälzkreisdurchmesser kann hierbei durch den Eingriffswinkel der Werkzeugschneide variiert werden. Der theoretische Wälzvorschub besteht aus zwei Bewegungsanteilen, die von der Maschine auszuführen sind: Zum einen eine Rotationsbewegung des Werktischs, zum anderen eine translatorische Vorschubbewegung, ausgeführt durch das Werkzeug oder auch das Werkstück.
Spezialisierte Verzahnmaschinen werden durch die Bauart der auf ihnen gefertigten Zahnräder kategorisiert: Zylinderräder, Kegelräder, Schnecken und Schneckenräder erfordern eine jeweils individuelle Maschine.
Nach der Vorverzahnung kann in Abhängigkeit vom Zahnrad-Werkstoff eine Wärmebehandlung stattfinden. Um die jeweils geforderte Qualität zu erreichen, werden die vorverzahnten Zahnräder feinbearbeitet, zum Beispiel durch das Wälz- oder Formschleifen.
Wälzschälen hat sich als effizientes Verfahren bewiesen
Lange Zeit galt es als schwierig, Innenverzahnungen effizient herzustellen. Denn hierfür mussten die wenig wirtschaftlichen Bearbeitungsverfahren Stoßen und Räumen genutzt werden. Als Ausweg setzten sich in der Antriebstechnik zunächst Stirnradgetriebe und Außenverzahnungen durch. Doch mit der Weiterentwicklung der Wälzschäl-Technologie (auch als „Scudding“ oder „Power Skiving“ bezeichnet) änderte sich dies: Im Gegensatz zum Stoßen ist es ein kontinuierlich abwälzendes Verfahren, bei dem der unproduktive Hub und die Abhebebewegung vermieden werden. Die Bearbeitungszeit reduziert sich deutlich, das Zerspanvolumen wird erhöht.
Der Maschinenbediener kann über die NC (Numeric Control) zahlreiche Maße (wie „Zweikugelmaß“, Schrägungswinkel, Flankenform) konfigurieren. Verzahnungen lassen sich mit den Verfahren sowohl außen als auch innen erzeugen – und dies in einer Aufspannung. Zwar wurde der Grundstein zu dieser komplexen Technologie bereits um 1910 gelegt, jedoch erlaubt es erst moderne CNC-Technik, das Potential auszuschöpfen. Beim Wälzschälen werden spezielle Werkzeuge genutzt, welche sich durch eine hohe Standzeit auszeichnen.
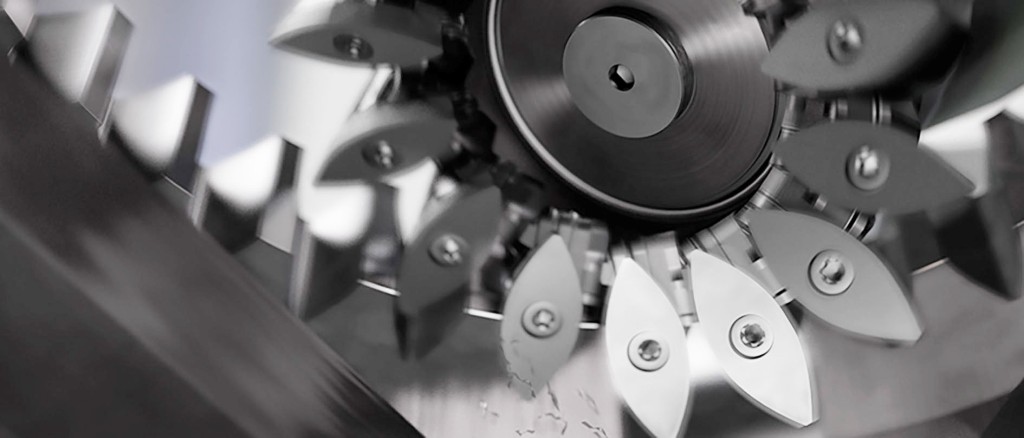
Das „Power Skiving“ mit Bohrungs- und Schaftwerkzeugen sowie Wendeschneidplattenfräsern (im Bild zu sehen) des schwedischen Werkzeugspezialisten hat sich als schnell und flexibel bewährt.
Foto: Sandvik Coromant
Pro und Contra – Skiven oder Stoßen?
Auf das konkrete Bauteil kommt es bei der Auswahl des sinnvollen Verfahrens an, so lautet die Meinung der Experten bei Liebherr-Verzahntechnik, Kempten. „Ein wichtiger Faktor bei der Entscheidung für oder wider Skiving ist die Geometrie des Werkstücks“, sagt Dr.-Ing. Oliver Winkel, Leiter Technologieanwendung. „Bei einem zu sehr begrenzten Werkzeugauslauf ist Schälen nicht mehr möglich. Durch den Achskreuzwinkel benötigen wir einen größeren Werkzeugüberlauf. Diese Werkstücke können nur gestoßen werden.“
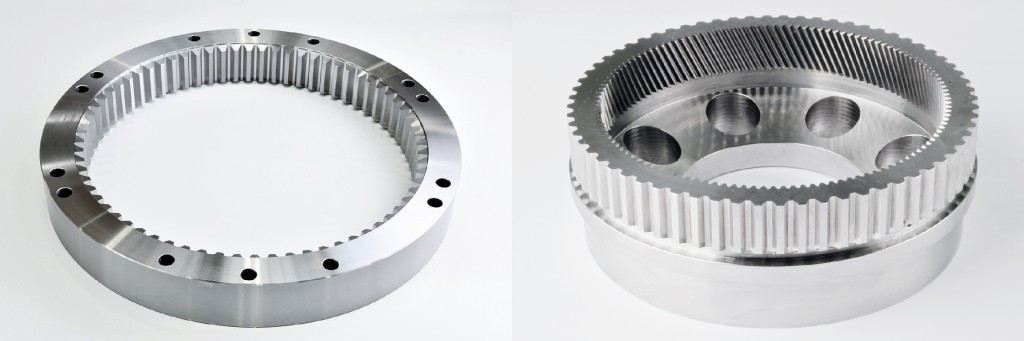
Das rechts gezeigte Werkstück kann wirtschaftlicher gestoßen werden. Ein typisches Werkstück für das Verfahren Wälzschälen ist links zu sehen.
Foto: Liebherr
Ist ein Werkstück grundsätzlich für Skiving oder Stoßen geeignet, entscheiden Losgröße und die geforderte Qualität. Schälen ist deutlich schneller (etwa Faktor drei). „Mit Skiving erreichen wir auch einen besseren RZ-Wert, der die Rauheit der Oberfläche beschreibt“, betont Winkel. Auch die Teilung ist in der Regel gleichmäßiger. Wenn es dagegen um die Flankenqualität geht, ist wiederum das Stoßen besser geeignet, denn hier haben Werkzeugfehler – im Gegensatz zum Wälzschälen – keinen Einfluss auf die erreichbare Qualität. Hinzu kommt, dass die Schneidräder weniger kosten und vielseitiger einsetzbar sind. Kleine Änderungen, zum Beispiel beim Werkstück-Werkstoff, können aber große Auswirkungen haben. Bei hochfesten Werkstoffen über 1100 MPa ist Stoßen aktuell noch etablierter, Wälzschälen „holt aber auf“.
Alles aus einer Hand: Maschine, Werkzeug, Technologie-Know-how
Der Verzahntechnik- und Automatisierungsspezialist Liebherr-Verzahntechnik stellt moderne Wälzschäl-Maschinen her, die mit maschinenintegriertem Werkzeugwechsler, einer integrierten Messeinrichtung für Werkzeuge und der Option zum hauptzeitparallelen Anfasen ausgestattet sind. Damit lassen sich Innenverzahnungen mit definierter Fase produzieren (Modell LK180 / 280). Daneben sind ebenso Wälzfräs- und -Stoßmaschinen im breiten Programm. Auch die Werkzeuge für Schruppen und Schlichten, die im Werk Ettlingen produziert werden, gehören zum Portfolio. So kann die Kinematik des Schälprozesses insbesondere im Grenzbereich genau berücksichtigt werden.
Für das „ChamferCut“-Verfahren zum Anfasen von Wellen oder Rädern mit Störkonturen wurde kürzlich zur „EMO“ 2019 moderne Maschinen- und Werkzeugtechnik vorgestellt. Die ChamferCut CG (Collision Gear)-Technologie erlaubt das Bearbeiten von Schaltgetriebe-Komponenten, bei denen etwa die Hälfte der Räder und Wellen störende Konturen hat. Durch ein Kippen des Werkzeugs und die getrennte Bearbeitung von rechter und linker Flanke mit je einem Tool werden hierfür neue Möglichkeiten erschlossen.
Ein ebenfalls sehr breit aufgestellter, traditionsreicher Anbieter ist die Firma Gleason mit deutschem Sitz in Ludwigsburg. Die Lösungen reichen von der Zahnrad-Auslegungssoftware über Verzahnmaschinen bis zu Messmaschinen und Automatisierungslösungen.
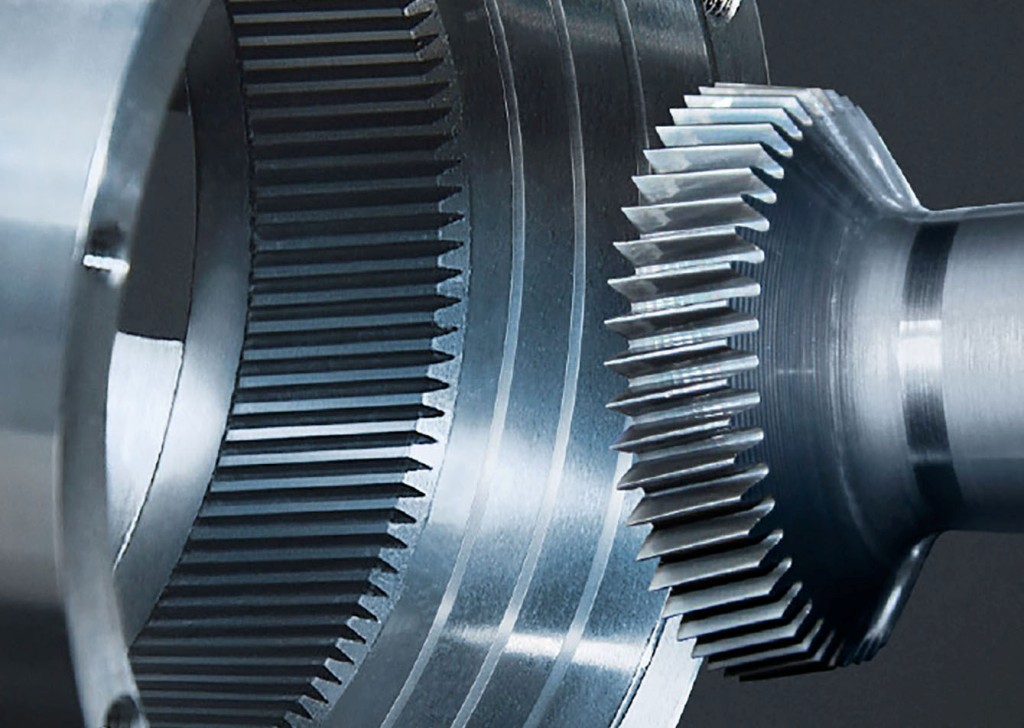
Das „Power Skiving“ von Verzahnungen ist eine moderne Technologie, die sich auf den Wälzschälmaschinen des Traditionsunternehmens umsetzen lässt.
Foto: Gleason
Im Jahr 2015 feierte die Gleason Corporation, gegründet 1865 in Rochester/USA, ihr 150-jähriges Firmenjubiläum. Aktuell macht die Firma mit einer kostenlosen Webinar-Reihe auf sich aufmerksam. Im März 2020 wurde die Fortbildungsreihe zu Verzahnungstechnologie-Themen als kostenloser Kundenservice in „Covid-19“-Zeiten eingeführt. Seit Ende Juni 2020 finden als Fortsetzung „Gear-Trainer-Webinare“ statt: eine Mischung aus Präsentationen, Video-Inhalten und Live-Demonstrationen.. Sie behandeln die Fertigungstechnologien von Kegel- und Zylinderrädern (Weich- und Hartfeinbearbeitung) und schließen Entwicklung/Simulation, Messtechnik, Werkzeuge, Spannmittel sowie Industrie 4.0-Produktionssysteme mit ein.
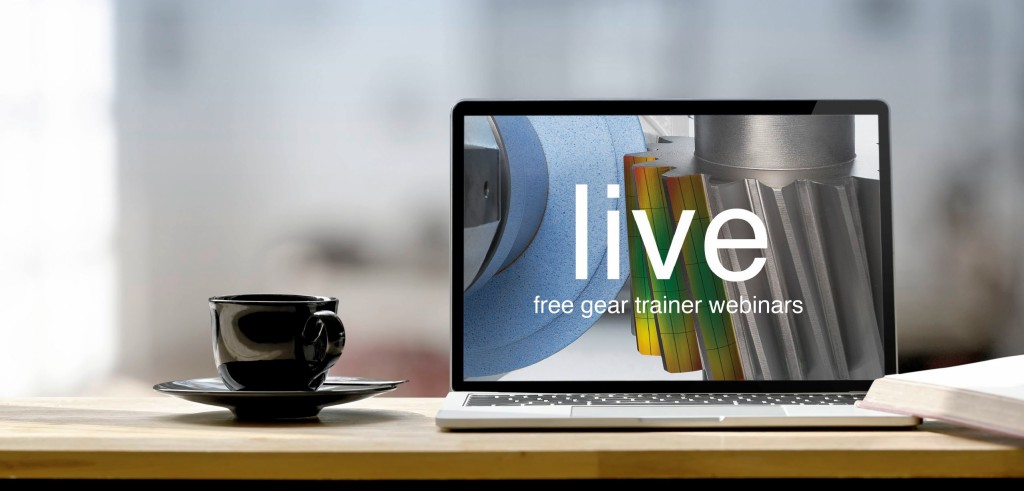
Die Verzahnungsexperten gehen in einer Webinar-Reihe den Themen, die die Kunden bewegen, auf den Grund.
Foto: Gleason
Das könnte Sie auch interessieren:
Pressenlinie im XXL-Format bei Volkswagen
Präzision durch adaptive Produktion
Beschichtete Zylinderlaufbahnen sind in der Automobilindustrie im Trend
Birgit Etmanski, promovierte Maschinenbauingenieurin, ist Chefredakteurin der Zeitschrift VDI-Z.