Hybridwerkzeuge optimieren Zerspanung des Leichtbauwerkstoffs Aluminium
Die Aluminiumbearbeitung ist und bleibt ein Wachstumsmarkt. Damit die begehrten Komponenten aus dem Leichtbaumaterial rasch und effizient entstehen können, setzt ein Technologieführer auf Hybridwerkzeuge für sicheres, wirtschaftliches Zerspanen.
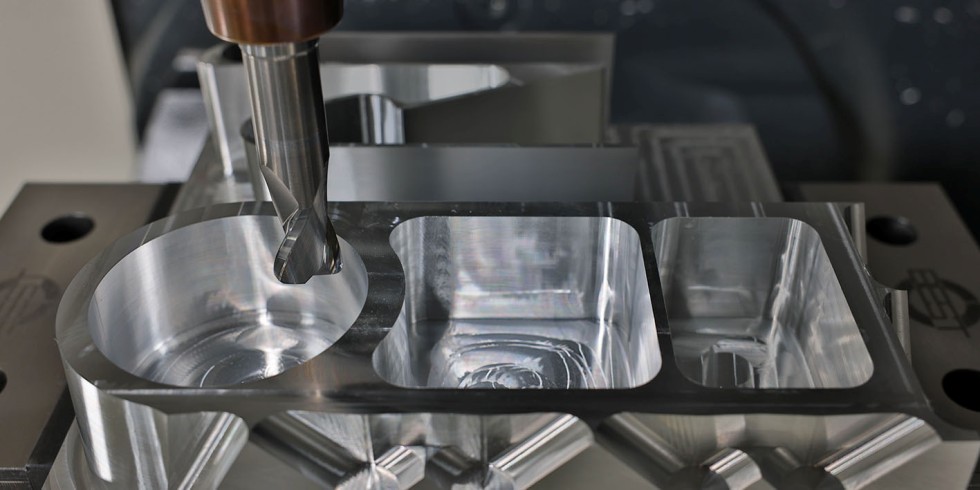
Aluminiumlegierungen finden sich aufgrund ihres Leichtbaupotentials zunehmend in allen Bereichen der Automobil- und Flugzeugindustrie. Für ihre Zerspanung sind spezielle Werkzeuglösungen gefragt, die Prozesssicherheit und Wirtschaftlichkeit verbinden.
Foto: Walter
Auch wenn die Aluminiumherstellung energieintensiv und nur bedingt klimafreundlich ist, gehören Aluminiumwerkstoffe zu wichtigen Elementen bei der Dekarbonisierung der Mobilitätsindustrie, aber auch beim Ausbau der Windenergie. Die Bilanz verbessert sich zudem noch massiv, wenn recyceltes Aluminium genutzt wird.
Was kann Aluminium zur Dekarbonisierung beitragen?
Nur durch den großen Gewichtsvorteil von Aluminiumbauteilen lässt sich das Gewicht und damit der Treibstoffverbrauch von Fahr- und Flugzeugen signifikant reduzieren. Auch bei elektrisch betriebenen Fahrzeugen ist das Gewicht ein zentraler Faktor: Je leichter das Auto, desto höher die Reichweite der Batterie. Außerdem gehört Aluminium zu den Werkstoffen, die fast zu 100 Prozent recyclebar sind. Damit lassen sich tatsächlich weitgehend geschlossene Kreislaufwirtschaftsprozesse aufbauen. Das ist bei vielen anderen Legierungen, vor allem aber auch bei Verbundwerkstoffen nur bedingt der Fall. Werkstoffe wie geschmiedete Aluminium-Knetlegierungen oder duktile Aluminium-Gusslegierungen mit niedrigem Siliziumgehalt finden sich deswegen zunehmend in allen Bereichen der Automobil- und Flugzeugindustrie.
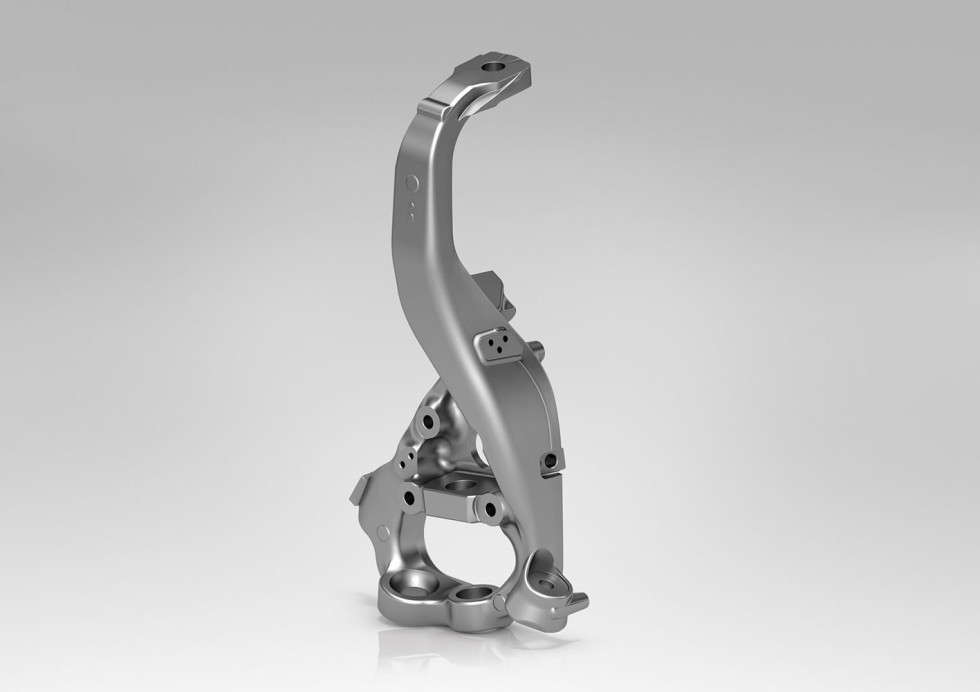
Ein Bauteil für den Automotive-Sektor ist der gezeigte Achsschenkel mit Kegelsitzbohrung: Hybridwerkzeuge kommen hier häufig zum Einsatz.
Foto: Walter
Wie lassen sich komplexe Bohrungen wirtschaftlich herstellen?
Vor allem das Einbringen von Vollbohrungen stellt bei der Fertigung von Fahrwerkskomponenten aus Aluminiumlegierungen eine technische und wirtschaftliche Herausforderung dar. Während bei größeren Bohrungen, wie zum Beispiel der Radnabenbohrung am Radträger, häufig vorgeschmiedete Vertiefungen aufgebohrt werden, entstehen kleinere Bohrungen – wie am Querlenker – dagegen durch das Einbringen ins volle Material. Dazu kommen die oft hohe Komplexität der zu bohrenden Konturen sowie die sehr hohen Anforderungen an die Genauigkeit der Bohrung und an die Oberflächenqualität.
Meist dienen die kleineren Bohrungen zur Aufnahme von Gleitlagern und Dämpfern. Das heißt, es ist mehr als das schlichte Setzen einer Bohrung gefragt: Zum Beispiel müssen auch definierte Planflächen oder Fasen angebracht werden, um im nächsten Produktionsschritt Lagerbuchsen oder Dämpfungselemente einbauen zu können. Pro Bohrung fallen so schnell bis zu fünf Bearbeitungsschritte an.
Welche Zerspanungskonzepte kommen in Frage?
Mehrere Bearbeitungsschritte an einer Bohrung erfordern ein besonderes Zerspanungskonzept, denn Werkzeugwechsel kosten nicht nur Zeit. Sie erhöhen auch das Risiko, die Vorgaben bei Passgenauigkeit und Oberflächenqualität zu verfehlen. Mit dem Konzept des Hybridwerkzeugs bieten Zerspanungsspezialisten wie Walter ihren Kunden eine auf die konkrete Aufgabe optimierte Lösung, die sich durch höchste Prozesssicherheit und Ergebnisqualität auszeichnet – und sich somit auszahlt.
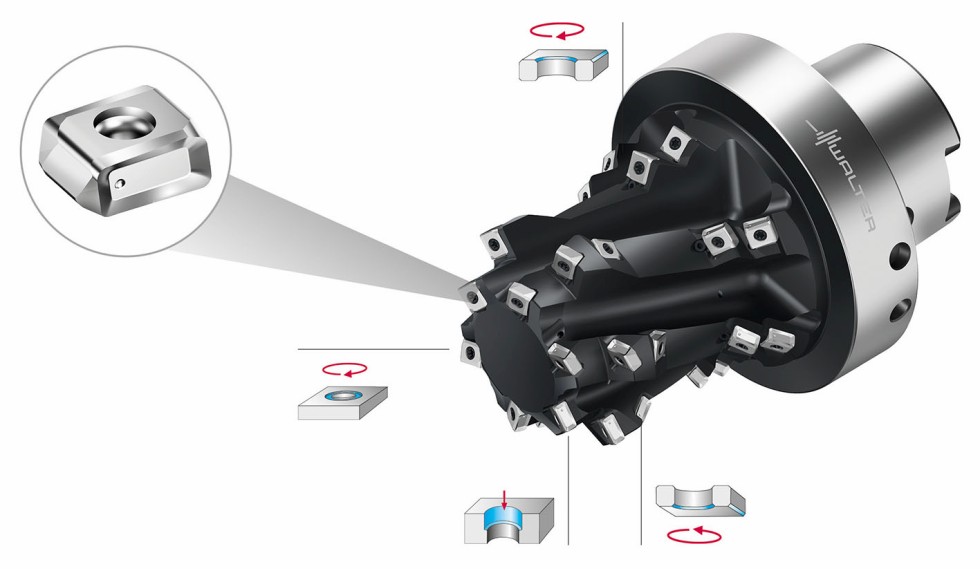
Vielfältige Bearbeitungen in einem Werkzeug sind mithilfe der tangential-lateralen Aufbohrplatte P4460 möglich: Wenn zuvor tangential eingebaute Wendeplatten in einen lateralen Sitz montiert werden, können bis zu 4+4 Schneidkanten genutzt werden.
Foto: Walter
Hybrid heißt, dass ein Werkzeugkorpus unterschiedliche Zerspanungsschritte möglich macht – also eigentlich verschiedene Werkzeuge in einem vereint. Dabei werden jedoch nicht einfach nur Wendeschneidplatten unterschiedlicher Form eingesetzt: Hybridwerkzeuge verbinden einen Bereich mit austauschbaren Wendeschneidplatten und fest eingelötete PKD (polykristalliner Diamant)-Schneiden – und damit zwei unterschiedliche Werkzeugtypen.
Der Bereich für schnell verschleißende Anwendungen wie das Schruppen arbeitet dabei mit Wendeschneidplatten, die leicht vom Kunden selbst gewechselt werden können, ohne dass das gesamte Werkzeug zum Reconditioning eingeschickt werden muss. Das Schlichten gemäß exakter Passungsmaße mit kleinsten Winkeltoleranzen und hohen Anforderungen an die Oberflächenqualität wird dagegen mit fest eingelöteten PKD-Schneiden durchgeführt. PKD-Schneidstoffe zeichnen sich durch ihre hohe Verschleißfestigkeit und die so erreichbaren Standzeiten aus. Eingesetzt werden Hybridwerkzeuge vor allem beim „Voll“-Bohren sowie bei Kegelsitz- und Kugelsitzbohrungen.
Voraussetzung: hohe Kompetenz bei Schneidgeometrie und Beschichtung
Die vor allem im Fahrwerksbereich häufig eingesetzten schmied- und warmaushärtbaren Aluminium-Knetlegierungen mit Magnesium und Silizium als Hauptlegierungselemente stellen durch ihr Zerspanungsverhalten hohe Anforderungen an die Schneide selbst: Bei der Bearbeitung bilden sich Aufbauschneiden, die zu einem schnelleren Verschleiß der Schneidkante führen. Durch die Veränderung der Schneidkantengeometrie wirken höhere Prozesskräfte auf das Bauteil ein, sodass die gewünschten Maße und Winkel oder die Oberflächenqualität nicht mehr eingehalten werden. Aluminium-Knetlegierungen bilden zudem lange Späne oder sogar Fließspäne, die einen reibungslosen Zerspanungsprozess erheblich gefährden können. Werden diese Risiken für die Prozesssicherheit nicht beherrscht, sinken auch die Effizienzgewinne deutlich, die sich durch ein Hybridwerkzeug erreichen lassen.
Worauf kommt es bei den Wendeschneidplatten an?
Die von Walter für die Aluminiumbearbeitung entwickelten Wendeschneidplatten verfügen aus genannten Gründen über eine besondere Geometrie und Beschichtung. Speziell auf die Aufgabe ausgelegt sind die Sorten „P2840“ und „P4840“, darüber hinaus „P6004“ für Vollbohroperationen sowie „P4460“ zum Aufbohren.
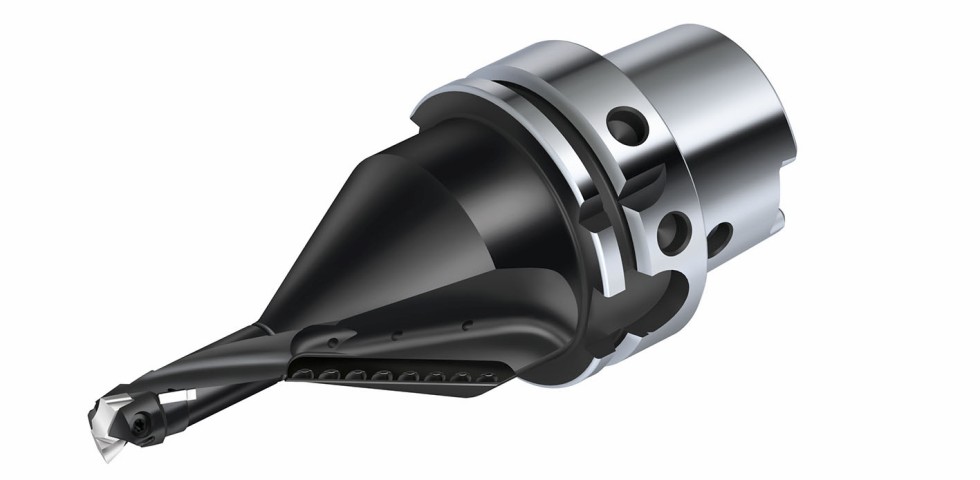
Wirkungsweise des Spanbrechers: Die gelaserte Spanbrechergeometrie im Kombinationswerkzeug ist der Schlüssel für eine prozesssichere Bearbeitung.
Foto: Walter
Eine spezifische Oberflächengeometrie gewährleistet eine optimale Spankontrolle. Die bei der Bearbeitung entstehenden Späne brechen so kurz, dass sich Fließspäne oder Spanknäuel nicht bilden können. Bei fest eingelöteten PKD-Schneiden wird, sofern nötig, durch gelaserte Spanformer- oder Spanbrechergeometrien für die entsprechend gute Spankontrolle gesorgt.
Bei Wendeschneidplatten reduzieren scharf präparierte Schneidkanten die Prozesskräfte, sowie hochpolierte Spanflächen und eine spezielle Beschichtung außerdem die Bildung von Aufbauschneiden: Die so erzeugten sehr glatten Oberflächen an der Wendeschneidplatte bieten dem Werkstoff wenig Angriffsfläche. Die Wendeschneidplatten verfügen so über deutlich höhere Standzeiten als nicht-optimierte Typen.
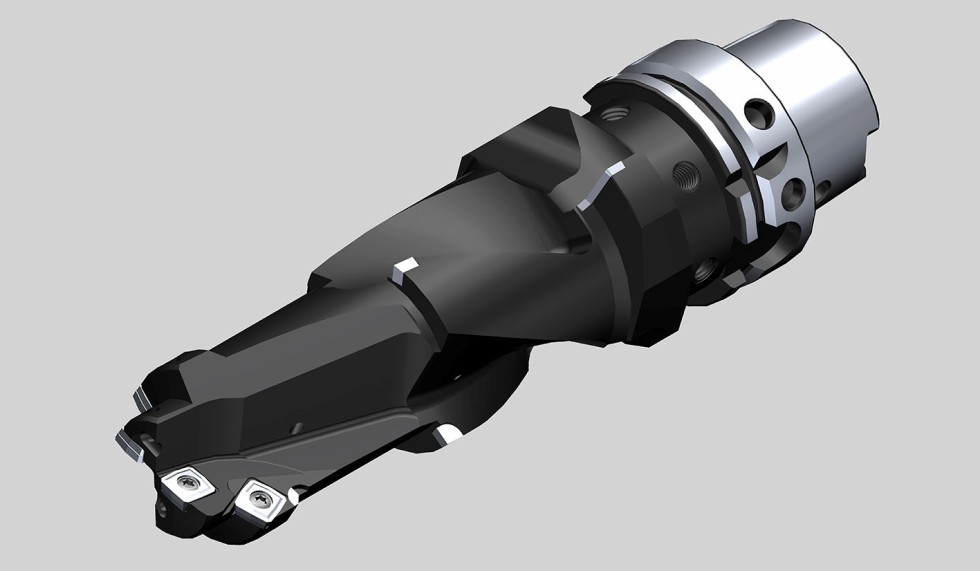
Werkzeug mit Wendeschneidplatten (hier P2840) in der Bohr- und Aufbohrstufe sowie eingelöteten PKD-Schneiden für die Bearbeitung des Fertigdurchmessers (Auf- bzw. Feinbohren).
Foto: Walter
Das Resultat: hohe Schnittdaten und ideale Prozesssicherheit
Bei Walter werden Hybridwerkzeuge für den Einsatz im konkreten Prozess konzipiert und gefertigt. Der Werkzeugkorpus ist deswegen im Prinzip eine Sonderanfertigung. Durch die hohe Produktivität, die sie im Fertigungsprozess bringen, „rechnen“ sich die Werkzeuge schnell. Ein namhafter Kunde der Tübinger konnte beim Einbringen von Bohrungen in einen Querlenker mit einem Walter-Hybridwerkzeug beispielsweise in der Bohrstufe Schnittgeschwindigkeiten (vf) von über 1.300 Metern in der Minute bei einem Umdrehungsvorschub (fu) von 0,11 Millimetern erreichen, beim nachfolgenden Auf- bzw. Feinbohren ein vf von 850 Metern in der Minute bei einem Zahnvorschub (fz) von 0,12 Millimetern. Die Effizienz in der Aluminiumbearbeitung ist damit bestens sichergestellt.
Das könnte Sie auch interessieren:
Das intelligente Werkzeug schafft Visionen
Hobelwerkzeug in Extrem-Leichtbauweise optimiert Produktivität und CO2-Footprint
Wie transferierbare künstliche Intelligenz die Zerspanung voranbringt
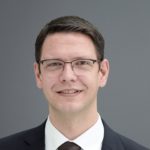
Fabian Hübner ist Component & Project Manager Transportation bei Walter in Tübingen. Foto: Walter