Hobelwerkzeug in Extrem-Leichtbauweise optimiert Produktivität und CO2-Footprint
Leichter, schneller, hochpräzise, energie- und materialeffizient: Dies sind die Vorzüge eines neuen Werkzeugs in extremer Leichtbauweise, das jetzt für seine besondere Eigenschaftskombination prämiert wurde. Was macht die Neukonstruktion so bemerkenswert?
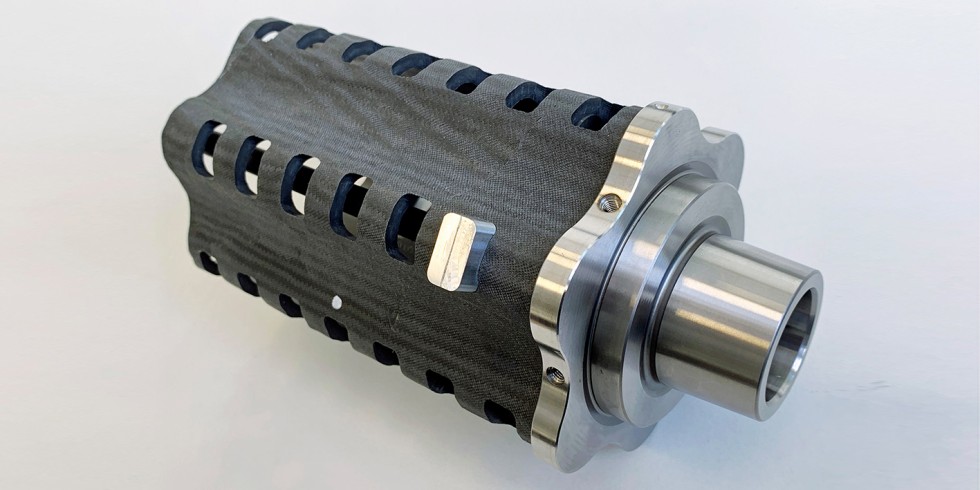
Demonstrator in Leichtbauweise mit CFK (kohlenstofffaserverstärkter Kunststoff)-Außenhaut und speziell konstruierten Metallteilen im Inneren: Das innnovative Konzept wurde mit dem "ThinKing"-Award des Monats Mai 2022 ausgezeichnet.
Foto: Leitz
Das Hobeln in der maschinellen Längsbearbeitung von Holzprodukten hat heute nichts mehr mit dem rhythmisch schleifenden Geräusch in einer Tischlerei zu tun. Moderne Hobelwerkzeuge, deren Köpfe – die Umfangsplanfräser – in Hochgeschwindigkeit rotieren, tragen die Oberfläche des Holzes präzise auf wenige Mikrometer genau ab.
Welche Vorteile bietet die Leichtbau-Innovation?
Nur halb so schwer und um die Hälfte schneller sollen die Hobelwerkzeuge für die Holzbearbeitung dank Extrem-Leichtbau werden. Mit Hilfe von numerischer Simulation bauen die Forschenden an den DITF – Deutschen Instituten für Textil- und Faserforschung Denkendorf – das Werkzeug von Grund auf neu auf. Die zum Patent angemeldete Konstruktion des modularen Baukörperkonzepts auf Basis von CFK (carbonfaserverstärktem Kunststoff) wird ganz aktuell mit dem „ThinKing“ ausgezeichnet.
Die Landesagentur für Leichtbau Baden-Württemberg präsentiert diese Innovation als herausragendes Leichtbau-Beispiel im Monat Mai 2022. Mit dem Label ThinKing gibt die Leichtbau BW GmbH monatlich innovativen Produkten oder Dienstleistungen in dieser Kategorie, die aus Baden-Württemberg stammen, eine Plattform und möchte sie in der Öffentlichkeit bekannter machen.
Die Merkmale der Werkzeugkonstruktion auf einen Blick
- Leichter: 50 Prozent weniger Gewicht bringt das Leichtbau-Hobelwerkzeug „auf die Waage“.
- Schneller: Das sehr leichte, hochfeste Werkzeug führt zu deutlich geringerer Maschinenbelastung und ermöglicht eine 1,5-fache Produktionsgeschwindigkeit.
- Präzise: Das sehr steife Werkzeug mit vorteilhaftem Schwingungsverhalten ermöglicht auch bei hohen Drehzahlen eine hohe Bearbeitungsqualität.
- Energiesparend: Der Prozess verbraucht weniger Antriebsenergie, da die zu beschleunigende Masse geringer ist.
- Materialeffizient: Der durch numerische Simulation konstruktiv optimierte Aufbau benötigt weniger Material.
- Skalierbar: Die Leichtbauweise ist auf größere, rotierende Werkzeuge sowie weitere Branchen übertragbar, wobei der Gewichtsvorteil mit dem Durchmesser zunimmt.
Materialsubstitution ist nur der halbe Leichtbau
Leichtere und steifere Werkzeuge könnten durch höhere Drehzahlen und ein optimiertes Schwingungsverhalten noch bessere Oberflächenqualitäten und Produktionsgeschwindigkeiten ermöglichen und außerdem Energie einsparen. Doch die derzeit auf dem Markt verfügbaren Umfangsplanfräser sind aus Aluminium gefertigt und haben ihr Leichtbaupotenzial weitgehend ausgeschöpft.
In einem öffentlich geförderten IGF-Vorhaben in enger Zusammenarbeit mit dem Institut für Werkzeugmaschinen (IFW) der Universität Stuttgart und weiteren Partnern aus der Industrie nahmen sich die Forschenden der DITF der Aufgabe an, das Gewicht der Umfangsplanfräser zu reduzieren, um die Produktionseffizienz wesentlich zu verbessern. „Uns war schnell klar, dass wir neben der reinen Materialsubstitution von Metallteilen durch faserverstärkte Kunststoffe nur mittels der numerischen Simulation risikobehaftete, dafür aber optimal faser- und lastgerechte Konstruktionskonzepte entwickeln können“, erklärt Hermann Finckh, stellvertretender Leiter des Kompetenzzentrum Stapelfaser, Weberei & Simulation und Leiter der Numerischen Simulation an den DITF. „Unser Ziel war, das Werkzeug von Grund auf neu aufzubauen und zu konstruieren. Leichtbau und Präzision waren dafür unsere Leitlinien.“

3D-gedrucktes Funktionsmuster, das den inneren Aufbau des Leichtbaukonzepts für das Hobelwerkzeug zeigt. Hier wird deutlich, wie wichtig geringe Toleranzen in der Fertigung sind.
Foto: DITF
Optimale Lastverteilung ist de Schlüssel zum Erfolg
Das Risiko hat sich gelohnt. Äußerlich zum Verwechseln, ähnlich beinhaltet das Leichtbaukonzept nicht nur den Materialwechsel zum carbonfaserverstärkten Kunststoff, sondern auch ein neues Gestaltungsprinzip für die „inneren Werte“ des Hobelwerkzeugs. Mit den Möglichkeiten der numerischen Simulation an den DITF gelang ein modulares Konzept: im Inneren einer Außenhülle sind dreieckige Elemente angeordnet. Diese waren an ihren Ecken in der ersten Version durch Metalleinsätze verbunden, die später durch Fixierstifte aus CFK ersetzt wurden. Diese senkrecht zu den Dreiecken angeordneten Fixierungen dienen zudem als Halterung für die Schneidenträger, welche wiederum die Wendeschneidplatten aufnehmen.
Durch das modular aufgebaute Gestaltungsprinzip werden die wirkenden Kräfte optimal auf die einzelnen Elemente verteilt. Die Fliehkraft wird von den CFK-Dreieckelementen aufgenommen. Für alle anderen Belastungen – Dreh- und Biegemoment, Normalkraft – sind die CFK-Außenhülle und die Stangen „zuständig“. „In der Fertigung von Grundkörper und Dreiecken können wir die einzelnen Teile jetzt fasergerecht entlang der Lastpfade auslegen. So ist eine optimale Lastaufnahme der Kohlenstofffasern möglich, die zu einer maximalen Gewichtseinsparung bei größtmöglicher Steifigkeit führt“, erklärt Hermann Finckh.
Je größer das Werkzeug, desto intensiver ist der Gewichtsvorteil
So ist das Leichtbau-Hobelwerkzeug nur noch halb so schwer wie das Original – statt etwas mehr die acht Kilogramm des Referenzwerkzeugs bringt die CFK-Variante nur noch etwa vier Kilogramm auf die Waage. Konstruktiv bedingt steigt sogar bei zunehmendem Werkzeugdurchmesser der Gewichtsvorteil gegenüber Werkzeugen aus Stahl oder Aluminium sogar noch weiter an.
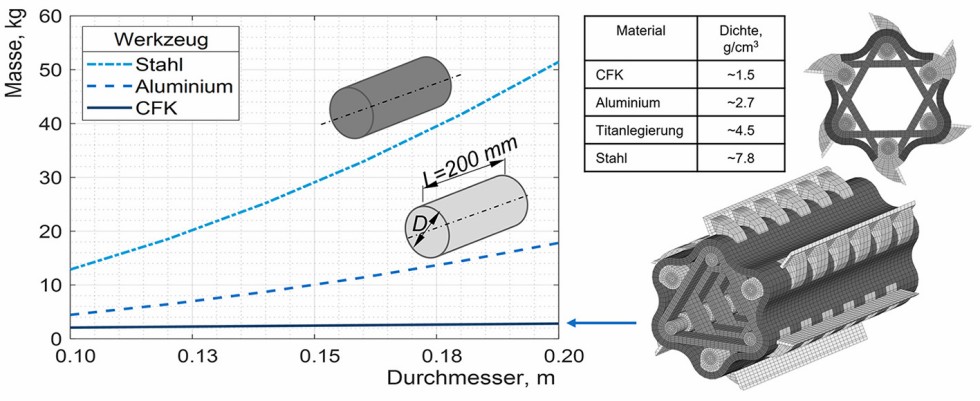
Je größer der Werkzeugdurchmesser wird, desto höher ist das Masseneinsparungspotenzial durch das modulare Grundkörperkonzept.Grafik: DITF
Die Demonstratoren wurden unter Verwendung von Carbonfaser-Rovings beziehungsweise -Gewebe mit Standardverfahren hergestellt: Wickeln und Vacuum Assisted Resin Infusion „VARI“. Auch andere bekannte Prozesse wie Flechten, das Verarbeiten von Prepregs oder RTM (Resin Transfer Moulding) sind denkbar. „Eine Herausforderung bei der Fertigung der Leichtbauwerkzeuge werden die Toleranzen der ineinandergreifenden Radien sein. Doch das ist eine lösbare Aufgabe“, ist sich Hermann Finckh sicher. „Es gibt für das Extrem-Leichtbauwerkzeug aber auch noch weitere sehr spannende Forschungsthemen zu bearbeiten, die für eine erfolgreichen Einsatz von Bedeutung sind. Dazu zählen das Versagens- und Langzeitverhalten, die Skalierbarkeit, die Präzisions- und Drehzahlmaximierung und die Funktions- und Sensorintegration. Diese Anforderungen können über sich anschließende Forschungsprojekte gelöst werden.“
50 Prozent leichteres Werkzeug sorgt für 1,5-fache höhere Produktivität
Erste Fräsversuche mit einem Demonstrator an MDF-Platten bei 12.000 Umdrehungen in der Minute zeigen, dass die Holzoberfläche der mittels konventioneller Hobelwerkzeuge erzeugten Qualität entspricht. Durch die Extrem-Leichtbauweise sollten 18.000 Umdrehungen in der Minute und mehr möglich werden. Bedingt durch die hohe Steifigkeit ist das Leichtbauwerkzeug auch bei hohen Drehzahlen präzise. Die Messer verlassen ihren berechneten Flugkreis trotz hoher Fliehkräfte nur minimal.
Bezogen auf die Produktionskosten ist das nicht der einzige Vorteil: neben einer höheren möglichen Produktionsgeschwindigkeit verbrauchen die Werkzeuge dank Leichtbau weniger Energie. Und wenn die Produktionskapazität an einer Maschine um 50 Prozent gesteigert wird, kann eine zweite Maschine möglicherweise eingespart und so ein relevanter Beitrag zur Reduzierung von CO2-Emissionen und mehr Nachhaltigkeit geleistet werden.
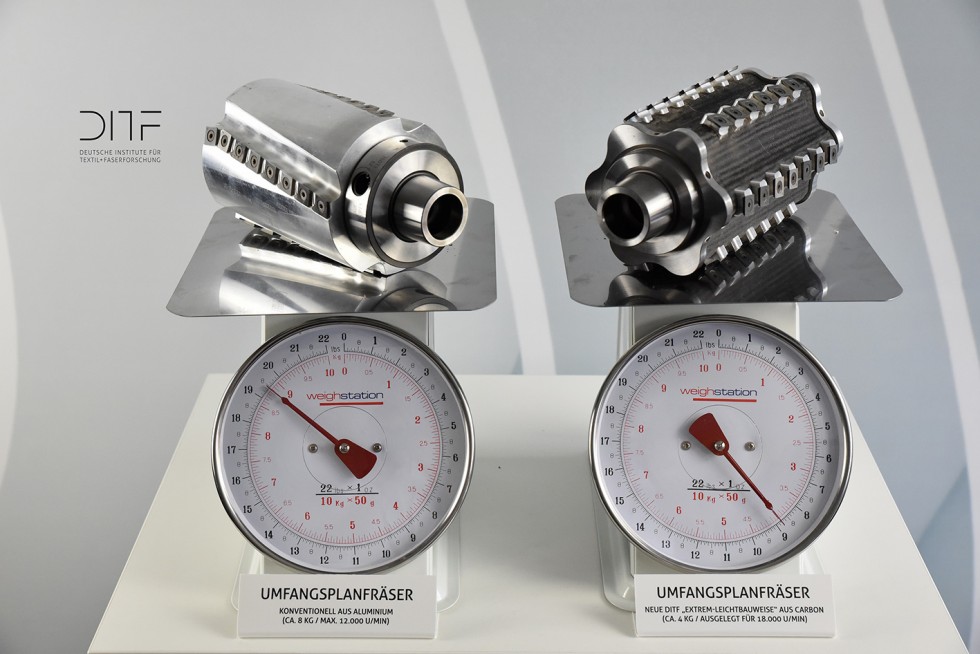
Die beiden Hobelwerkzeuge im Vergleich auf der Waage: Rechts ist das Leichtbauwerkzeug in der optimierten Ausführung mit CFK zu sehen, links die konventionelle Ausführung.
Foto: DITF
Die zum Patent angemeldete Extrem-Leichtbauweise des DITF für rotierende Werkzeuge für die Holzverarbeitung ist prinzipiell auch auf andere Anwendungen in der Automobilindustrie, der Luft- und Raumfahrt sowie im Maschinenbau übertragbar.
Über die Deutschen Institute für Textil- und Faserforschung Denkendorf (DITF)
Die Deutschen Institute für Textil- und Faserforschung Denkendorf sind eine vom Land unterstützte Forschungseinrichtung und Mitglied der Innovationsallianz Baden-Württemberg (innBW). Mit mehr als 250 Beschäftigten auf einer Fläche von über 25.000 Quadratmetern betreiben sie national und international vernetzt anwendungsbezogene Forschung über die gesamte textile Wertschöpfungskette. Die hier vorgestellten Arbeiten wurden im Rahmen des IGF-Forschungsprojekts Nr. 20128 N/1+2 „Entwicklung hochdynamisch belastbarer leichter Werkzeuggrundkörper für die Holz- und Holzwerkstoffbearbeitung“ – gefördert durch das Ministerium für Wirtschaft und Klimaschutz (BMWK) aufgrund eines Beschlusses des Deutschen Bundestages – erarbeitet. Die Projektteilnehmer danken dem BMWK für die gewährte Förderung, eingereicht über die Forschungsplattform Holzbearbeitungstechnologie (FPH).
Das könnte Sie auch interessieren:
Werkzeuge werden produktiver und nachhaltiger
Getriebe für den Luftverkehr werden leichter und langlebiger
Funktionsbauteile aus dem 3D-Druck erfolgreich Laserstrahlschweißen