Was leisten Industrieroboter in der mechanischen Fertigung?
Noch sind Werkzeugmaschinen tonangebend in Sachen Genauigkeit. Doch Industrieroboter holen immer mehr auf – unter anderem dank Künstlicher Intelligenz.

Ein Forscherteam der TU Berlin hat eindrucksvoll belegt, dass der Einsatz Künstlicher Intelligenz die Positionierfehler von Industrierobotern in Fertigungsprozessen kompensieren kann. Die Produktqualität lässt sich deutlich verbessern.
Foto: PantherMedia
Ohne Roboter keine Automatisierung – kamen Industrieroboter bislang vorwiegend bei Pick-and-Place- und Montagearbeiten zum Einsatz, übernehmen sie im Zuge der flexiblen Fertigung mehr und mehr auch die Tätigkeiten von Werkzeugmaschinen. Gezeigt wird, wie sich dank KI die bisher noch bestehenden Nachteile beim Robotereinsatz in spanenden oder umformenden Fertigungsprozessen kompensieren lassen.
Vorteile: Vielseitigkeit und optimale Zugänglichkeit
Die Vorteile liegen auf der Hand: Verbesserte Bewegungsachsen ermöglichen mittlerweile das Erreichen jeder möglichen Position sowie jedes beliebigen Winkels, und universelle Endeffektoren sind kompatibel mit allen erdenklichen Werkzeugen – seien es Fräser, Bohrer, Scanner oder Sägen. Industrieroboter können dadurch immer kniffligere Aufgaben ausführen und komplexe Bauteile aus einer Vielfalt an Materialien wie Holz, Kunststoff oder Metallen fertigen. Während der Arbeitsbereich einer CNC-Maschine auf wenige Meter beschränkt ist, kommt der Roboter auch an schwer zugängliche Bauelemente. Diese Wandlungsfähigkeit ist ein entscheidender Pluspunkt, wenn es darum geht, auch bei kleinen Losgrößen und hoher Variantenvielfalt effizient und kostengünstig zu produzieren.
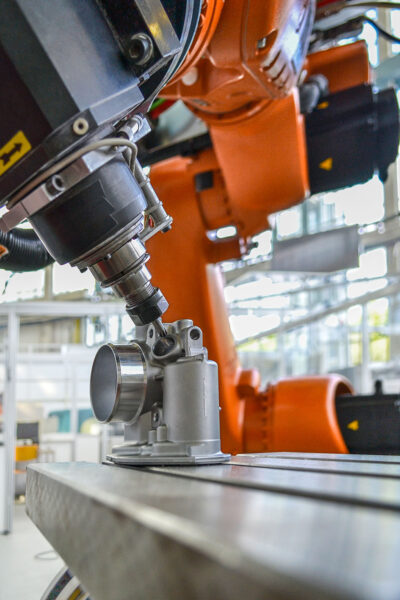
Bild 1: Roboterbasierte Bearbeitung: Zahlreichen Vorteilen stehen auch einige Nachteile gegenüber, vor allem die geringere Steifigkeit.
Foto: Fraunhofer IPK / Ksenia Gaillard
Schwachstelle: die geringe Steifigkeit
Und dennoch: An die hohe Präzision einer Werkzeugmaschine, die beispielsweise Metallteile bis in den Mikrometerbereich genau bearbeitet, kommen die flexiblen Alleskönner nicht heran. Denn ein klassischer Industrieroboter – wie der am häufigsten verwendete sechsachsige Knickarmroboter – besitzt nur eine vergleichsweise geringe Steifigkeit. Das liegt vor allem daran, dass die Roboterglieder eine sogenannte offene kinematische Kette bilden. Bei Tätigkeiten mit hohen einwirkenden Kräften wie dem Fräsen oder der Umformung gibt die Roboterstruktur nach und die gewünschte Position wird nicht exakt angefahren. Die dadurch entstehende Werkzeugabdrängung ist je nach Anwendung unterschiedlich, hat aber fast immer Einfluss auf die Fertigungsgenauigkeit. Entsprechend kommen Roboter überwiegend dort zum Einsatz, wo die hohe Genauigkeit einer Werkzeugmaschine nicht benötigt wird.
Die Verbesserung der Positioniergenauigkeit von Industrierobotern – und damit die Erweiterung ihres Einsatzgebiets – ist daher seit Jahren ein wichtiges Forschungsfeld. Dabei werden unterschiedliche Ansätze verfolgt, die entweder die Konstruktion, die Steuerung oder die Kalibrierung der Roboter in den Mittelpunkt stellen. Durch die fortschreitende Vernetzung von Maschinen und die damit einhergehende Verfügbarkeit großer Datenmengen gewinnen jedoch vor allem Methoden der Künstlichen Intelligenz, insbesondere des überwachten Maschinellen Lernens zunehmend an Bedeutung.
Mit KI die Werkzeugabdrängung vorhersagen
Das Besondere beim überwachten Lernen ist, dass das KI-Modell auf Basis eines Datensatzes lernt, bei dem die korrekten Antworten bereits existieren. Das Modell erhält also sowohl Eingaben als auch passende Ausgaben. Sobald der Algorithmus ein Muster zwischen diesen erkennt, können neue Eingaben hinzugefügt werden, und die KI prognostiziert die Ausgaben.
Entsprechend bildet ein KI-Modell zur Vorhersage von Werkzeugabdrängungen die sechs Gelenkwinkel des Roboters sowie die Kraft- und Momentkomponenten am Werkzeug als Eingangsparameter auf die Werkzeugabdrängung als Ausgangsparameter ab. Ein derart trainiertes Modell kann zur Vorhersage von Werkzeugabdrängungen für beliebige Aufgaben verwendet werden.
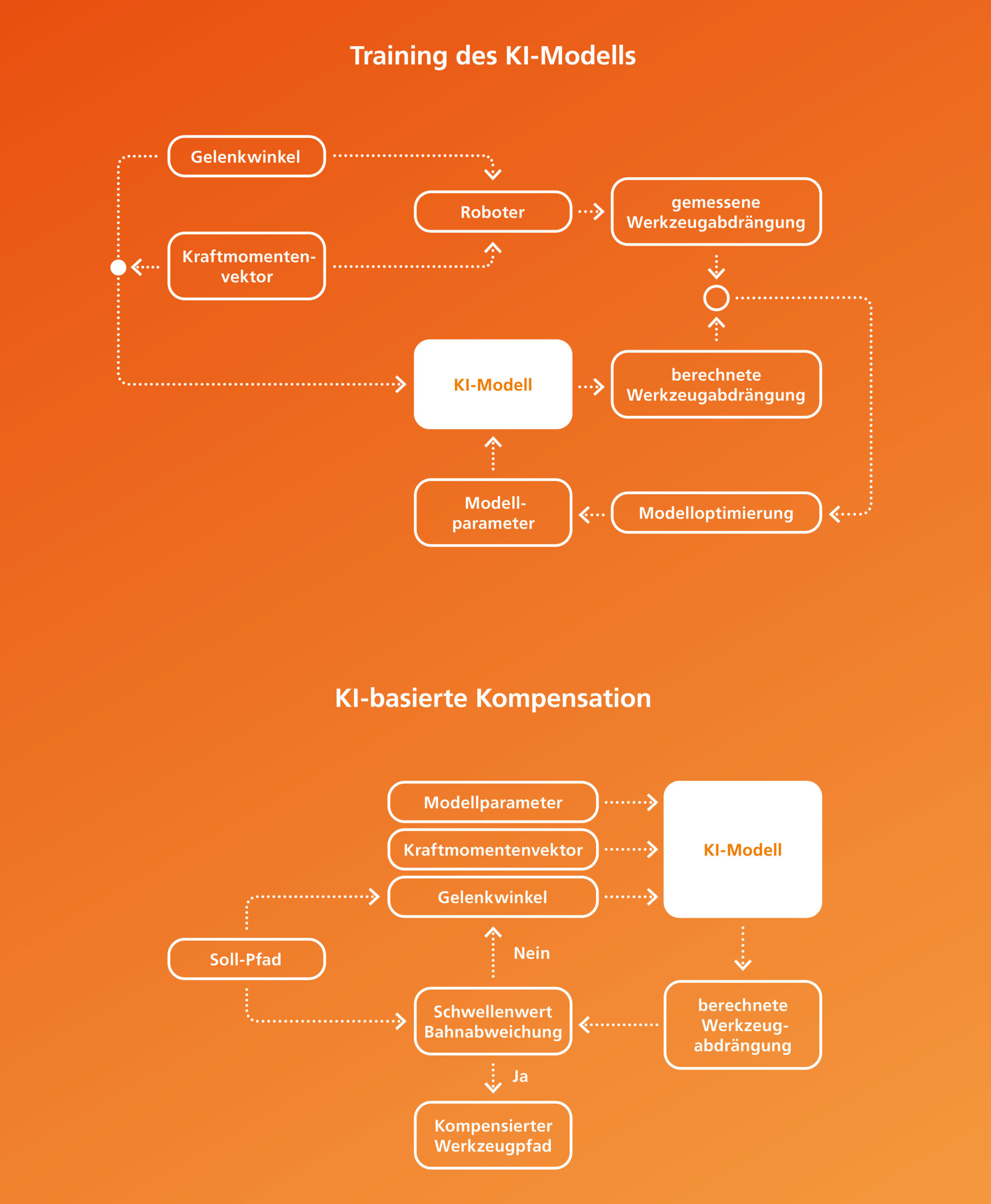
Bild 2: Training des KI (Künstliche Intelligenz)-Modells für die roboterbasierte Bearbeitung. Grafik: IWF der TU Berlin
Anwendungsbeispiel: Blechteile in kleinen Stückzahlen zu geringen Kosten
Forschende am IWF der TU Berlin haben zur Validierung dieser Trainingsmethode mit einem Industrieroboter einen sogenannten „inkrementellen Kragenziehprozess“ realisiert. Das Kragenziehen ist ein Zugdruckumformverfahren, bei dem vorgelochte Bleche zu einem Flansch aufgeweitet werden. Es ist Teil der Prozesskette zur Herstellung vieler Blechbauteile, zum Beispiel im Automobilbau.
Die Erweiterung des konventionellen Kragenziehens um einen inkrementellen Ansatz, bei dem das Blech schrittweise durch ein generisches Werkzeug entlang eines Werkzeugpfades aufgeweitet wird, ermöglicht die Flexibilisierung und Kostenreduzierung durch das Einsparen aufwendiger Umformwerkzeuge. Die Verwendung von Industrierobotern erhöht diese Flexibilität weiter und bietet zudem die Möglichkeit, Kragen in schwer zugänglichen Bereichen mit neuartigen Verfahren zu formen.
Der Weg zu guten Daten
Die für das Umformen notwendige hohe Krafteinwirkung verursacht jedoch Werkzeugabdrängungen, die Einfluss auf die Formgenauigkeit der Kragen haben. Um diese Abdrängungen mithilfe des überwachten Maschinellen Lernens vorhersagen zu können, haben die Forschenden einen Trainingsdatensatz generiert, für den der Industrieroboter auf verschiedenen kreisförmigen Werkzeugpfaden mit einer Gasdruckfeder belastet wurde. Dabei wurden die Gelenkwinkel des Roboters ohne Belastung sowie unter Einwirkung der externen Kräfte an mehreren Punkten erfasst und jeweils mit einem Lasertracker gemessen. Insgesamt wurden auf diese Weise 352 Datenpunkte ermittelt. Die Werkzeugabdrängung ergibt sich aus der Differenz zwischen der belasteten und der unbelasteten Position.
Formgenaue Kragen: eine runde Sache
Das Ergebnis: Die Formgenauigkeit der Kragen verbesserte sich um 75 Prozent, was einer Reduzierung der maximalen Abweichung auf 0,6 mm entspricht. Gleichzeitig wurden die Unterschiede zwischen dem minimalen und maximalen gemessenen Kragendurchmesser verringert und dadurch die Rundheit der Kragen gesteigert. Das Forscherteam hat somit eindrucksvoll gezeigt, wie der Einsatz von KI Positionierfehler bei Industrierobotern kompensieren und die Produktqualität deutlich verbessern kann. Doch die entwickelte Methode ist keineswegs auf das Kragenziehen beschränkt: Unter Berücksichtigung weiterer Faktoren wie dynamische Parameter und Temperaturen wird bereits daran gearbeitet, Industrieroboter künftig für beliebige Anwendungen im Hochgenauigkeitsbereich zu befähigen.
Das könnte Sie auch interessieren:
Schnell und einfach: Produktionsprozesse mit Industrierobotern

Julian Blumberg ist wissenschaftlicher Mitarbeiter für Industrierobotik im Fachgebiet Werkzeugmaschinen und Fertigungstechnik am Institut für Werkzeugmaschinen und Fabrikbetrieb IWF der Technischen Universität Berlin. Foto: IFW
Martina Rennschmid arbeitet als freie Redakteurin und schreibt vorzugsweise über Wissenschafts- und Forschungsthemen.