Wärmepumpe für Werkzeugmaschinen
Es kann sowohl heizen als auch kühlen – ein neues thermoelektrisches System ermöglicht jetzt eine bedarfsgerechte Temperierung von Motorspindeln und kürzt die „Warmlaufphase“ ab. Infolgedessen erhöht sich auch die Präzision von Werkzeugmaschinen.
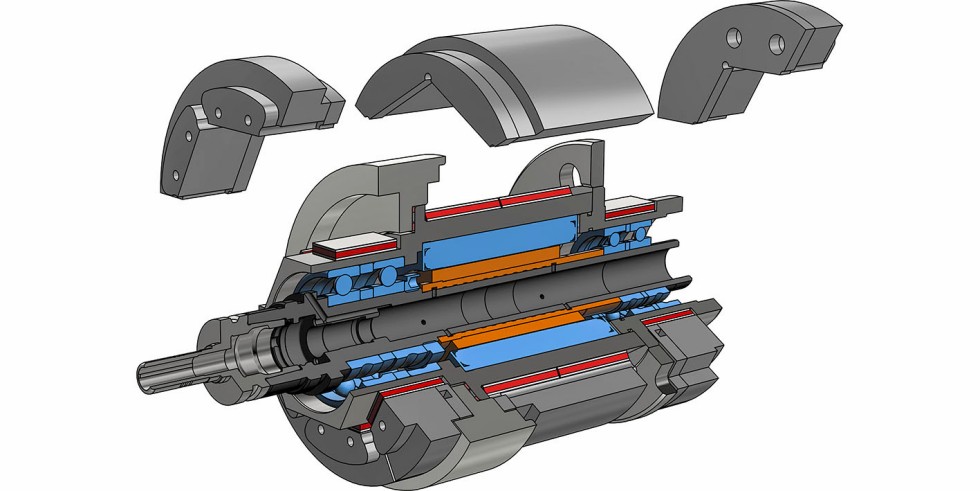
Schnittdarstellung der thermoelektrisch temperierten Fräs-Motorspindel. Das Ziel der Untersuchungen lautet: Hochleistungsfertigung dank einer Reduzierung der Warmlaufzeiten von Motorspindeln, beispielsweise für Anwendungen im Automobilbau. Grafik: Fraunhofer IPK
Ob Glaslinsen für Kameras, Spiegel für die Luft- und Raumfahrt oder Zahnräder für Uhren – in der Präzisionsfertigung kommt es auf höchste Genauigkeit an. Schon kleinste Fehler oder Unebenheiten können die Funktionalität der Gegenstände beeinträchtigen. Daher müssen die Bauteile mikrometergenau gefräst oder geschliffen werden. Der Bedarf an derart spanend bearbeiteten Bauteilen im Bereich der Optik, Messtechnik, des Automobilbaus sowie der Informations- und Kommunikationstechnik wächst stetig. Um der Nachfrage in Zukunft nachkommen zu können, ist eine hochproduktive Präzisionsfertigung notwendig.
Das Problem: Die dafür aktuell eingesetzten Werkzeugmaschinen haben eine lange Warmlaufzeit, was die Produktivität einschränkt. Die notwendigen Zeiten für den Warmlauf resultieren aus der hohen Anforderung an die Arbeitsgenauigkeit in der Präzisionsfertigung, die einen stabilen Zustand der thermisch bedingten Verlagerungen erfordert. Auf thermisch bedingte Verlagerungen lassen sich bis zu 75 Prozent der geometrischen Bauteilfehler zurückführen.
Ziel: Produktivität und Präzision optimieren
Die Motorspindeln, in die beispielsweise ein Fräswerkzeug eingespannt wird, sind die kritische Komponente einer Werkzeugmaschine: Sie haben aufgrund ihrer Nähe zum Werkzeugwirkpunkt einen erheblichen Einfluss auf die Arbeitsgenauigkeit. Die Antriebe und Lager von Motorspindeln stellen signifikante Wärmequellen dar. Durch elektrische sowie mechanische Verlustleistungen kommt es zu einer Erwärmung von Spindelgehäuse und -welle. In der Folge dehnen sich diese Komponenten aus und sorgen für eine Verlagerung des Werkzeugmittelpunkts.
Um diesen Effekt zu reduzieren, werden nach aktuellem Stand der Technik in Motorspindeln Fluidkühlungen eingesetzt, die einen Großteil der induzierten Wärmeströme abführen. Konventionelle Fluidkühlsysteme reagieren allerdings nicht auf Änderungen der Wärmeströme, die beispielsweise durch eine Variation der Drehzahl aufgrund von Werkzeugwechseln hervorgerufen werden. Schon eine kurze Stillstandszeit einer Motorspindel im Zuge eines Werkzeug- oder Werkstückwechsels führt zu einer thermischen Störung, die eine erneute Warmlaufzeit notwendig macht. Eine Energieverschwendung, die es nicht nur aus Gründen der Produktivität, sondern auch des Klimaschutzes zu vermeiden gilt.
Die Lösung: thermoelektrische Temperierung der Motorspindel
Um das thermoelastische Verhalten von Motorspindeln zu verbessern und insbesondere die Warmlaufzeit nach einem Spindelstillstand zu reduzieren, haben Forschende am Institut für Werkzeugmaschinen und Fabrikbetrieb (IWF) der Technischen Universität Berlin gemeinsam mit dem deutschen Motorspindelhersteller Alfred Jäger eine thermoelektrisch temperierte Fräs-Motorspindel entwickelt. Kernkomponente des Temperiersystems sind sogenannte Peltier-Module: elektrisch in Reihe geschaltete, winzig kleine Würfel aus dem Halbleiterwerkstoff Bismuttellurid, die zwischen zwei Keramikplatten angeordnet werden. Legt man eine Spannung an, transportieren die Halbleiter Wärme von einer zur anderen Seite. In Summe kann so eine Wärmestromdichte von bis zu 15 Watt pro Quadratzentimeter erreicht werden.
Für die entwickelte Motorspindel bedeutet dies, dass theoretisch ein Wärmestrom von bis zu 2,5 Kilowatt zur Verfügung steht – das ist vergleichbar mit der Kühlleistung einer Klimaanlage für einen größeren Raum. Bei einer konventionellen Spindel, die mit Wasser gekühlt wird, lässt sich hingegen nicht bestimmen, wie viel Wärme abgeführt wird. Durch den Einbau der Peltier-Module ist es damit möglich, den Wärmestrom gezielt zu regeln und die Temperatur der Spindel bedarfsgerecht anzupassen. So kann beispielsweise am vorderen Lager eine Temperatur von 25 Grad Celsius eingestellt und diese unabhängig von Drehzahländerungen gehalten werden. Durch eine Umkehrung der angelegten Stromrichtung lässt sich die Spindel auch vorwärmen, um unproduktive Warmlaufzeiten zu verkürzen. Man kann es sich wie eine Wärmepumpe für Maschinen vorstellen: Durch die Richtungsumkehr ist sowohl Kühlung als auch Heizung möglich.
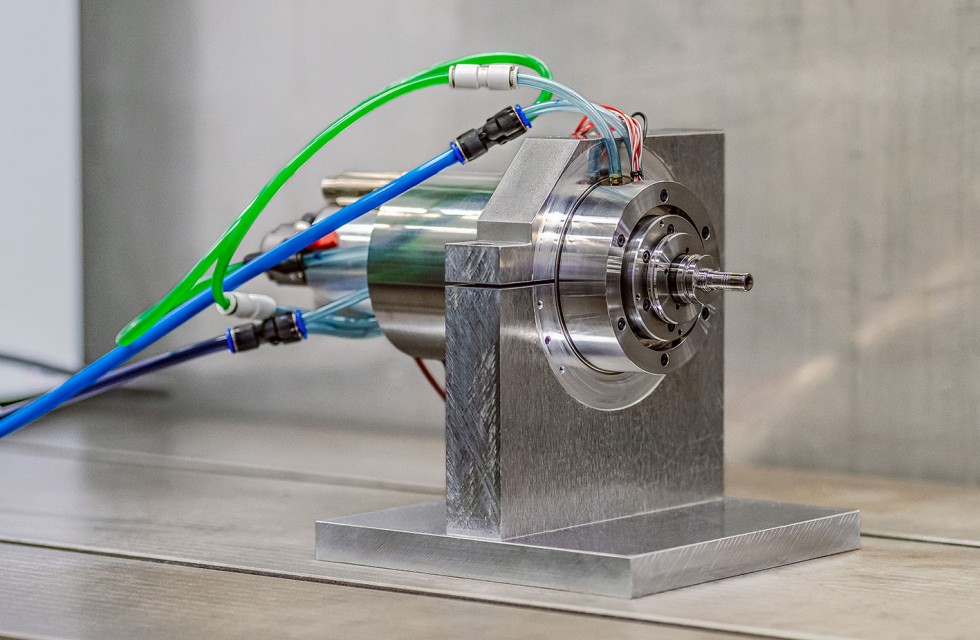
Versuchsaufbau zum Betrieb der thermoelektrisch temperierten Fräs-Motorspindel. Durch eine geregelte Wärmezufuhr sinken die Wellenverlagerung im Stillstand sowie die Warmlaufzeit des Prototypen signifikant. Grafik: Fraunhofer IPK / Larissa Klassen
Messungen belegen zahlreiche Vorteile
Um das Potenzial des thermoelektrischen Temperiersystems zu testen, wurden Vergleichsmessungen zwischen dem Prototyp und einer kommerziell verfügbaren Referenzspindel durchgeführt. Dabei wurden die Motorspindeln in einem Prüfstand mit einer Drehzahl von 55.000 Umdrehungen pro Minute betrieben und für eine Stillstandszeit von 300 Sekunden angehalten, was einen Werkstückwechsel simulieren sollte. Die Messungen zeigen: Durch eine geregelte Wärmezufuhr sinken die Wellenverlagerung im Stillstand sowie die Warmlaufzeit des Prototyps signifikant. Daraus ergibt sich ein erhebliches Produktivitäts-Steigerungspotenzial in der Präzisionsfertigung. Fazit: Die thermoelektrisch temperierten Fräs-Motorspindeln können nicht nur das Risiko von Bauteilfehlern reduzieren, sondern auch eine positive Auswirkung auf die Energieeffizienz der eingesetzten Werkzeugmaschinen haben.
Das könnte Sie auch interessieren:
Sensorische Schwenkspannelemente: Garant für sicheres Spannen
Softwarelösung für intelligente Pumpen
Onlinefähiges Ratter-Frühwarnsystem erkennt Prozessinstabilitäten

Florian Triebel ist wissenschaftlicher Mitarbeiter in der Gruppe Werkzeugmaschinentechnologie im Fachgebiet Werkzeugmaschinen und Fertigungstechnik am Institut für Werkzeugmaschinen und Fabrikbetrieb IWF der Technischen Universität Berlin. Sein Schwerpunktthema ist das thermische Verhalten von Werkzeugmaschinen.Foto: IWF
Adrian Lobe ist freier Journalist für verschiedene Medien im deutschsprachigen Raum (u.a. Die Welt, Neue Zürcher Zeitung, taz) und befasst sich schwerpunktmäßig mit digitalen Technologien und ihren Auswirkungen auf die Gesellschaft.