Onlinefähiges Ratter-Frühwarnsystem erkennt Prozessinstabilitäten
Das Auftreten von regenerativem Rattern verringert erheblich die Produktivität von Bearbeitungsprozessen. Durch ein Ratter-Frühwarnsystem an der Werkzeugmaschine kann die Prozessauslegung optimiert und die Ausschussquote gesenkt werden.
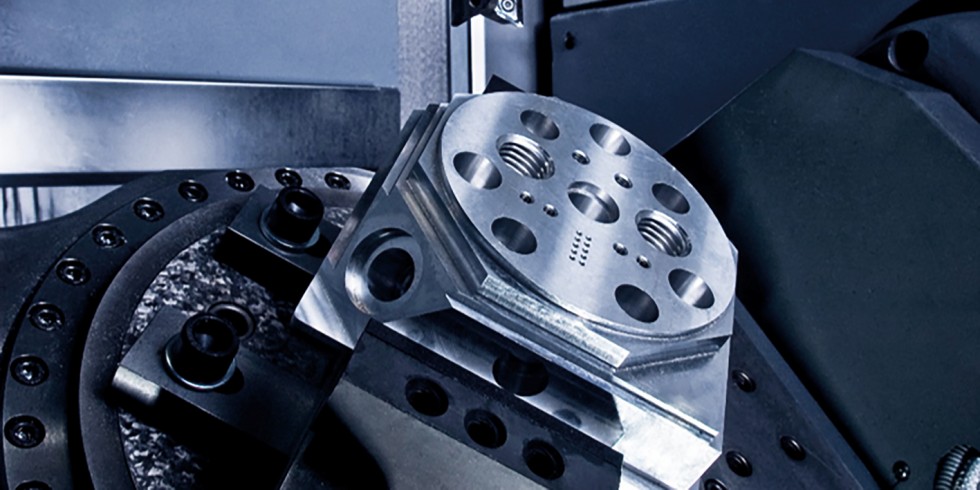
Entwicklungsziel ist ein System zur Rattervermeidung in Werkzeugmaschinen. Hierzu setzen die Forschenden auf die modellbasierte Identifikation von Prozessinstabilitäten mit prozessparalleler Datengrundlage. Die Genauigkeit des Frühwarnsystems wird anschließend in Zerspan-Versuchen bestimmt und soll den Zielkonflikt zwischen Produktivität und Bauteilqualität lösen.
Foto: WZL
Ein zentrales Ziel zur Steigerung des Nachhaltigkeitsbeitrags von Produktionsanlagen ist die effizientere Nutzung von Werkzeugmaschinen. Wird die Produktivität der Maschine gesteigert, beispielsweise durch eine verringerte Ausschussquote oder eine optimierte Prozessauslegung, kann die Anzahl erforderlicher Maschinen zur Erfüllung der Produktnachfrage reduziert werden. Bei der Auslegung von Bearbeitungsprozessen führt ein zentraler Zielkonflikt aus Produktivität und Bauteilqualität bisher jedoch häufig zu einer „konservativen“ Prozessplanung, wobei die Leistungsfähigkeit der Maschine nicht ausgenutzt wird.
Lösungsansatz: Prozessauslegung mit Stabilitätskarten
Insbesondere das Auftreten von selbsterregten und sich regenerativ selbstverstärkenden Schwingungen (Rattern) limitiert die Produktivität. Die mit den Ratterschwingungen verknüpften Prozessinstabilitäten haben eine Vielzahl von negativen Auswirkungen auf den Bearbeitungsprozess. Dazu zählen eine verringerte Oberflächengüte, erhöhter Werkzeugverschleiß, eine Beeinträchtigung der Maßhaltigkeit und eine starke Lärmentwicklung. Um das volle Potential einer Werkzeugmaschine auszuschöpfen, wird ein System zur Rattervermeidung benötigt, welches hohe Produktivität bei gleichzeitiger Gewährleistung der Bauteilqualität sicherstellt. Am Werkzeugmaschinenlabor (WZL) wird dazu an der modellbasierten Identifikation von Prozessinstabilitäten mit prozessparalleler Datengrundlage gearbeitet.
Ein Lösungsansatz liegt in der gezielten Vermeidung von Prozessinstabilitäten durch eine geeignete Wahl der Bearbeitungsparameter für den Prozess. Für die optimale Wahl der Prozessparameter stellen sogenannte Stabilitätskarten, die Stabilitätsgrenzen in Abhängigkeit von Schnitttiefe und Drehzahl darstellen, ein wichtiges Hilfsmittel dar (Bild 1).
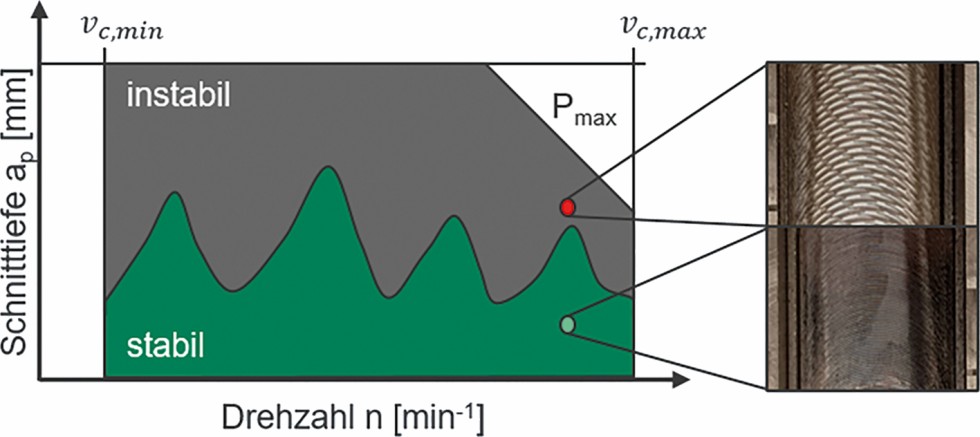
Bild 1. Schematische Darstellung einer Stabilitätskarte (links) und Auswirkung auf die Oberfläche ‧eines bearbeiteten Werkstücks unter instabilen sowie stabilen Parametern. Grafik: WZL
Das Vorgehen zur experimentellen Ermittlung von Stabilitätskarten wurde in den letzten Jahren zwar optimiert [1], ist für eine Anwendung in der Kleinserienfertigung dennoch zu aufwendig und nicht wirtschaftlich, da für jede Kombination aus Werkzeug, Werkstück und Maschine eine neue Stabilitätskarte in Vorversuchen ermittelt werden muss. Mit dem Trend einer nachhaltigen und ressourceneffizienten Produktion ist dies nicht vereinbar.
Was leistet die modellbasierte Stabilitätsberechnung?
Um die hohen Aufwände von Versuchsreihen zu umgehen, können Stabilitätsgrenzen modellbasiert ermittelt werden. Dabei erfolgt die Ermittlung der Stabilitätsgrenzen auf Basis eines analytischen Modells, welches die Wechselwirkung zwischen Maschine und Prozess beschreibt. Wesentlicher Nachteil des modellbasierten Ansatzes ist eine unsichere Datengrundlage, die sich auf Vorversuche und tabellierte Werte stützt.
In diesem Beitrag wird ein neues Konzept zur modellbasierten Online-Identifikation und Frühwarnung vor Prozessinstabilitäten für einen Fräsprozess vorgestellt. Der Nachteil einer unsicheren Datengrundlage wird durch die Nutzung prozessparallel aufgezeichneter Maschinendaten eliminiert. Das Frühwarnsystem liefert ein Werkzeug, um den vorliegenden Zielkonflikt zwischen Produktivität und Bauteilqualität zu lösen. Die prozessparallele Überprüfung der Stabilitätsgrenze unterstützt dabei insbesondere „First-Part-Right“ Ansätze zur Fertigung aufwendiger und teurer Einzelteile in einem ressourcenschonenden Ansatz. Die Methodik des Ratter Frühwarnsystems ist in Bild 2 dargestellt und umfasst fünf zentrale Bausteine.
1. Identifikation der Maschinendynamik
Für die modellbasierte Simulation liegt die zentrale Problematik in einer effizienten Abbildung der veränderlichen Dynamik des Maschine-Werkzeug-Werkstoff-Systems. Diese wird durch neue Erkenntnisse auf dem Gebiet der Substrukturkopplung gelöst [2]. Ein einmalig eingemessenes Modell der Werkzeugmaschine wird mit analytischen Werkzeugmodellen gekoppelt, um die experimentellen Messaufwände auf ein Minimum zu reduzieren. Das Vorgehen hierbei zeigt Bild 3.
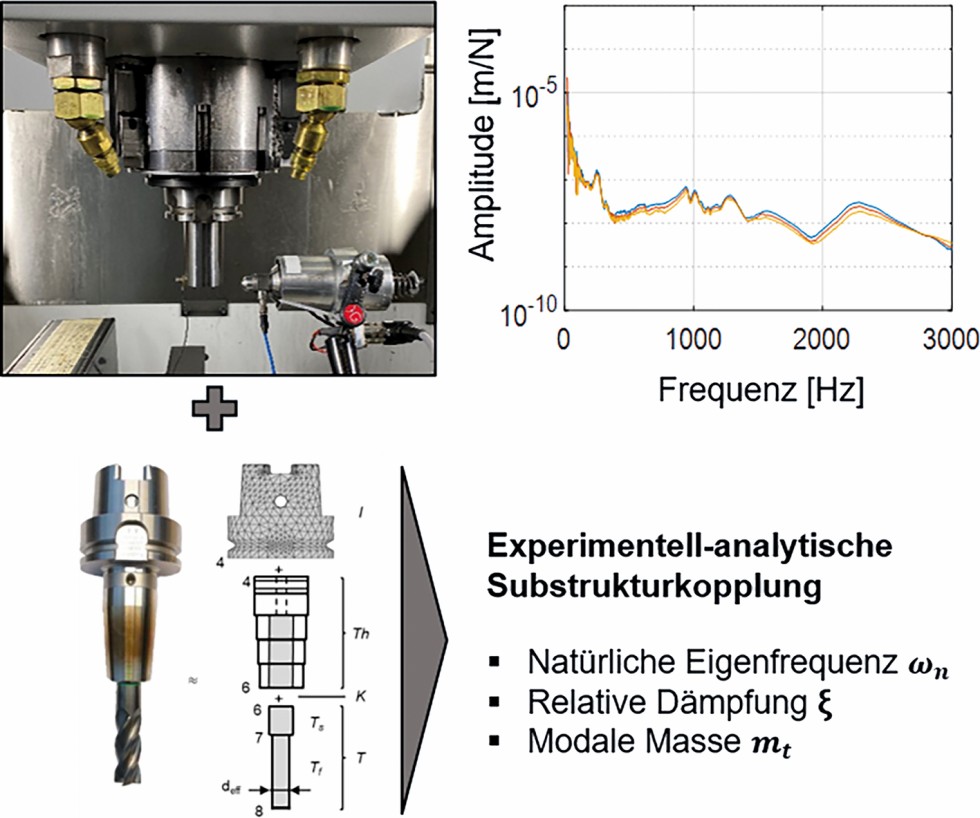
Bild 3. Messtechnische Erfassung der Maschinendynamik mit einem automatischen Impulshammer mit anschließender Ankopplung eines anayltischen Werkzeugmodells zur Identifikation der System‧parameter. Grafik: WZL
2. Ermittlung der Zerspanungsparameter
Mit einer Durchdringungssimulation auf Basis eines 3D Modells des Rohteils und dem NC-Code können Apriori die Zerspanungsparameter identifiziert werden. Hieraus können die für die Stabilitätssimulation erforderlichen Prozessgrößen wie beispielsweise die Schnitttiefe (ap) und das radiale Schnitttiefenverhältnis (ae) bezogen auf die unterschiedlichen Bearbeitungsschritte extrahiert werden. Es folgt eine Segmentierung des Bearbeitungsprozesses anhand unterschiedlicher Werkzeuge und programmierter Prozessparameter. Anhand dieser Datengrundlage können die jeweils kritischsten Bearbeitungsparameter für unterschiedliche Segmente des Prozesses identifiziert werden.
3. Online-Kraftmodell-Parametrierung
Neben der Maschinendynamik ist die Kenntnis der Schnittsteifigkeiten erforderlich. Aufgrund der großen Fortschritte im Bereich der echtzeitfähigen Erfassung von Prozesskräften, bspw. durch spindelintegrierte Sensorik [3], können die Schnittsteifigkeiten prozessparallel parametriert werden. Dies erfolgt auf Basis eines Vergleichs von gemessener und simulierter Prozesskraft mit einem „Ensemble Kalman Filter“, welcher bereits für die Anwendung einer kontinuierlichen Parameteridentifikation analytischer Kraftmodelle im Fräsprozess etabliert wurde [4].
Durch eine prozessparallele Identifikation der Schnittsteifigkeiten können die für die Stabilitätssimulation erforderlichen Eingangsgrößen anhand der reellen Randbedingungen des laufenden Prozesses ermittelt werden. Dies bietet einen Vorteil gegenüber konventionellen modellbasierten Ansätzen, die die Stabilitätsgrenze Apriori simulieren und deren Datengrundlage sich auf Vorversuche oder tabellierte Werte stützt.
4. Bedarfsgerechte Stabilitätsberechnung
Die Stabilitätsgrenzen werden prozessparallel innerhalb einer bedarfsgerechten Simulation ermittelt. Bedarfsgerecht bedeutet, dass nur die aktuell relevanten Drehzahlen und Schnitttiefen des laufenden Bearbeitungsschrittes für die Stabilitätssimulation ausgewertet werden. Anders als bei konventionellen modellbasierten Ansätzen zur Stabilitätssimulation wird daher nicht die gesamte Stabilitätskarte, sondern nur ein Bereich um den aktuell relevanten Arbeitspunkt berechnet. Die erforderlichen Eingangsgrößen zur Stabilitätsberechnung sind in Bild 4 dargestellt. Mit diesem Ansatz können die für den prozessparallelen Ansatz erforderlichen schnellen Rechenzeiten gewährleistet werden.
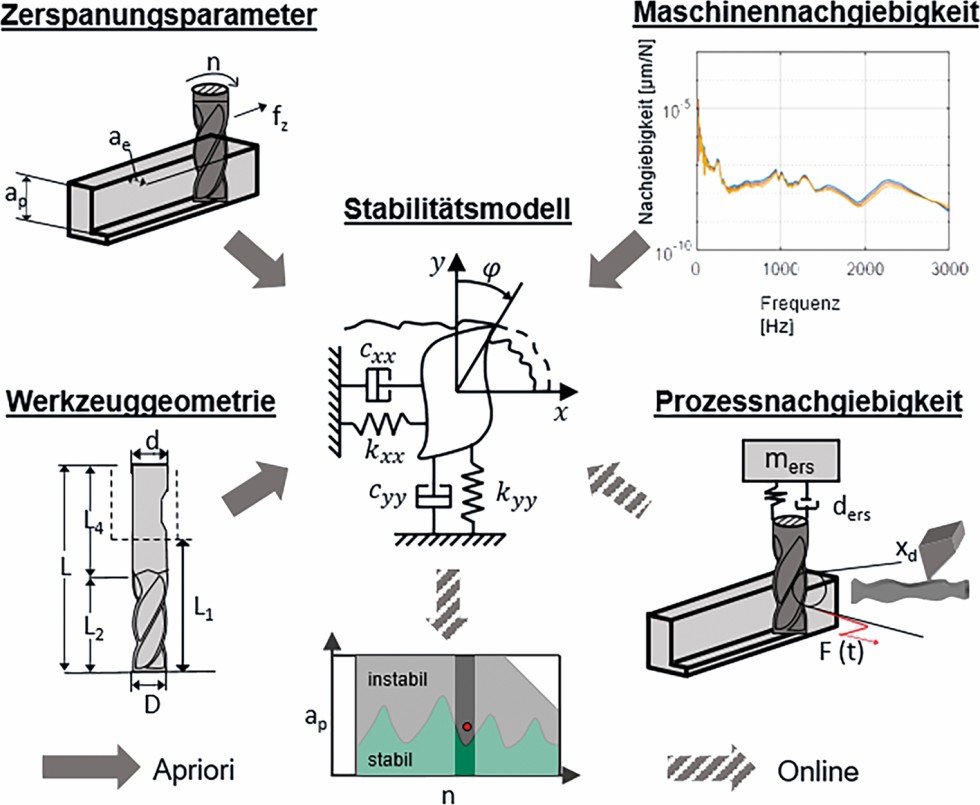
Bild 4. Übersicht der Eingangsgrößen für die Stabilitätsberechnung zur Auswertung der Stabilität um den aktuellen Arbeitspunkt. Grafik: WZL
5. Frühwarnsystem
Auf Basis der berechneten Stabilitätsgrenze können zukünftige Bearbeitungsschritte in einer Art „Look-Ahead Funktion“ auf eine Überschreitung der Grenze geprüft werden. Das Frühwarnsystem stellt eine online Funktionalität bereit, die während einer Bearbeitung vor potentiellen Prozessinstabilitäten im weiteren Bearbeitungsverlauf warnt. Die Aussage des Frühwarnsystems kann innerhalb von 5 Sekunden bereitgestellt werden. Anhand der Warnung kann das Auftreten von Prozessinstabilitäten durch einen Eingriff des Bedieners verhindert werden.
Zusammenfassung und Ausblick
Im Beitrag wurde eine neue Methodik für ein Online-Ratter-Frühwarnsystem vorgestellt. Die Kombination aus effizienter Ermittlung der Maschinendynamik und der prozessparallelen Datengrundlage bietet Vorteile gegenüber konventionellen Ansätzen zur modellbasierten Bestimmung von Stabilitätsgrenzen. Die Auswertung der Stabilität um den aktuellen Arbeitspunkt ermöglicht schnelle Rechenzeiten, die für den onlinefähigen Ansatz erforderlich sind. Eine Aussage des Warnsystems kann bereits nach wenigen Sekunden stattfinden. In einem nächsten Schritt wird die Genauigkeit des Frühwarnsystems anhand von Zerspan-Versuchen untersucht. Die Versuche umfassen sowohl unterschiedliche Werkzeuge als auch Werkstoffe.
Funding Acknowledgements: Gefördert durch die Deutsche Forschungsgemeinschaft (DFG) – Projektnummer 467600151.
Literatur
- Brecher, C.; Chavan, P.; Epple, A.: Effiziente Ermittlung von Stabilitätskarten beim Fräsen. In: Fräsen und Bohren, 2018b, Nr. 5, S. 56–57.
- Brecher, C.; Chavan, P.; Fey, M.: Efficient joint identification and fluted segment modelling of shrink-fit tool assemblies by updating extended tool models. In: Production Engineering, 15. Jg., 2021, Nr. 1, S. 21–33.
- Brecher, C.; Eckel, H.-M.; Fey, M.; Butz, F.: Prozesskraftmessung mit spindelintegrierter Sensorik. In: ZWF Zeitschrift für wirtschaftlichen Fabrikbetrieb, 113. Jg., 2018a, Nr. 10, S. 660–663.
- Schwenzer, M.; Stemmler, S.; Ay, M.; Bergs, T.; Abel, D.: Continuous identification for mechanistic force models in milling. In: IFAC-PapersOnLine, 52. Jg., 2019, Nr. 13, S. 1791–1796.
Das könnte Sie auch interessieren:
Kleinkraftwerke: Schlüsselkomponenten fix bearbeitet
Bedienerlose Fertigung mit Werkzeugmanagement-Lösung realisiert
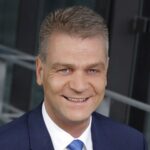
Prof. Dr.-Ing. Christian Brecher ist Inhaber des Lehrstuhls für Werkzeugmaschinen am Werkzeugmaschinenlabor WZL der RWTH Aachen. Foto: WZL
Dr.-Ing. Marcel Fey ist Oberingenieur und Leiter der Abteilung Maschinendatenanalyse & NC-Technik am WZL der RWTH Aachen.
Marcel Wittmann, M. Sc. RWTH, ist wissenschaftlicher Mitarbeiter am Institut für Werkzeugmaschinen am WZL der RWTH Aachen in der Abteilung Maschinendatenanalyse & NC-Technik.