Instationäre Prozessstellgrößengestaltung zur Optimierung von Drehprozessen
Moderne Drehprozesse sind durch komplexe Einsatzbedingungen gekennzeichnet. Gezeigt wird, wie der Verschleiß der hochwertigen Werkzeuge reduziert und ihre Standzeit gesteigert werden kann. Dies gelingt Forschenden am IFW mithilfe einer Modulation der Prozessstellgrößen.
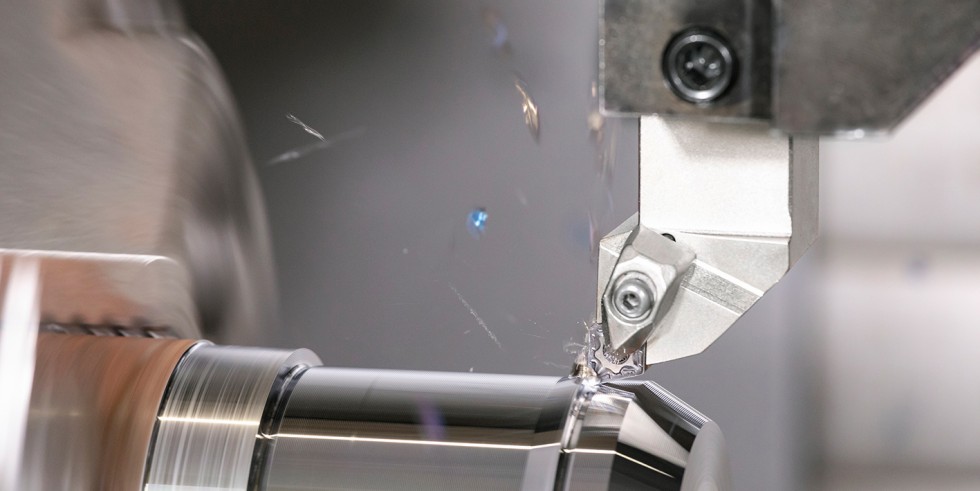
Drehwerkzeuge für das Außen- und Innendrehen: Modulationen der Schnittgeschwindigkeit sind geeignet, den Verschleiß bei der Zerspanung zu reduzieren. Einflüsse gehen zudem vom Werkstück-Werkstoff und dem Kühlschmierstoffeinsatz aus.
Foto: Iscar
Moderne Drehprozesse zeichnen sich beispielsweise durch aufwendige Werkzeuggeometrien sowie mehrachsige Vorschubbewegungen aus. Hierdurch können vorteilhafte Spanungsgrößen erzielt werden, wodurch sich die Schneidkeilbelastung verringert und eine Leistungssteigerung der Prozesse möglich ist. Einen weiteren Ansatz, die Werkzeugstandzeit zu erhöhen, bieten modulierte Prozesse. Unter welchen Randbedingungen diese Prozessführung geeignet ist, wird am Institut für Fertigungstechnik und Werkzeugmaschinen (IFW) der Leibniz Universität Hannover untersucht.
Stationärer im Vergleich zum modulierten Bearbeitungsprozess
Bei der klassischen Drehbearbeitung sind die Prozessstellgrößen zumeist stationär. Das bedeutet, dass Vorschub und Schnittgeschwindigkeit für eine spezifische Bearbeitungsaufgabe nicht verändert werden. Werden diese jedoch im Prozess kontinuierlich variiert, liegt eine modulierte Bearbeitung vor. Die Modulation wird durch die Form, das Intervall und die Amplitude definiert, siehe Bild 1. Da stets um einen Mittelwert von Schnittgeschwindigkeit und/oder Vorschub moduliert wird, ist die mittlere Produktivität vergleichbar zu Referenzuntersuchungen bei stationären Bedingungen.
Aus den Arbeiten des IFW ist bekannt, dass Modulationen der Schnittgeschwindigkeit geeignet sind, um den Verschleiß bei der trockenen Zerspanung von niedriglegierten Stählen zu reduzieren [1]. Daher wurde diese Strategie auf das Drehen unterschiedlicher Werkstoffe mit Verwendung von Kühlschmierstoff (KSS) übertragen. Erfolgreich ist diese Strategie bei der Zerspanung von Werkstoffen wie X40CrMoV5–1 und Ti6Al4V, bei denen trotz Einsatz von KSS ein erhöhtes Temperaturniveau vorliegt. Steigt die thermische Werkzeugbelastung an, beispielsweise durch ein erhöhtes Niveau der mittleren Schnittgeschwindigkeit, wird die Verschleißreduktion vergrößert.
Bei Prozessen mit vergleichsweise geringer Temperatur, wie bei der Zerspanung von 42CrMo4+QT mit KSS, liegen keine Vorteile der Methode vor. Hierbei stellt sich bei der Modulation ein Werkzeugverschleiß ein, der vergleichbar zum Verschleiß unter stationären Bedingungen ist. Entscheidend für die Standzeitsteigerung durch die Modulation sind die thermischen Werkzeugbelastungen. Liegen besonders hohe Temperaturen im Schneidkeil vor, wie beispielsweise beim trockenen Drehen hochlegierter Stähle oder Titan, versagt die Methode der Modulation. Bei mittler Temperaturbelastung, wie die Zerspanung niedriglegierter Stähle, wird jedoch auch bei der Trockenzerspanung eine Verschleißreduktion erreicht.
Welche Strategien führen zum Erfolg?
In den Anwendungen, in denen Schnittgeschwindigkeitsmodulationen grundsätzlich zur Verschleißreduktion eingesetzt werden können, zeigte sich, dass Strategien vorteilhaft sind, bei denen die Schnittgeschwindigkeit mit zunehmender Einsatzzeit linear reduziert wird, siehe Bild 2. Zurückzuführen ist dies auf den Widerstand des Werkzeugs gegen die thermische Belastung. Dieser ist in der ersten Phase der Einsatzzeit (hohe Schnittgeschwindigkeit, hohe Temperatur), bedingt durch den intakten Schneidstoff beziehungsweise der Beschichtung, auf einem hohen Niveau. Die zusätzliche thermische Last, bedingt durch die erhöhte Schnittgeschwindigkeit, verfügt daher in diesem Prozessfenster über keine signifikanten Effekte auf die Verschleißrate.
Bei fortschreitender Einsatzzeit wird die thermische Belastung durch Verringerung der Schnittgeschwindigkeit im modulierten Prozess reduziert, wodurch sich die Verschleißrate gegenüber dem stationären Prozess verringert. In Summe ergibt sich daher – gegenüber der Verwendung von konstanter Schnittgeschwindigkeit – eine Verschleißreduktion. Allerdings ist die Amplitude der Modulation auf den werkstoffspezifischen Verschleißwiderstand des Werkzeugs abzustimmen, um eine initiale Überlastung zu vermeiden.
Ziel: Zeitspanvolumen und Produktivität konstant halten
Neben Schnittgeschwindigkeitsmodulationen können kombinierte Modulationen aus Schnittgeschwindigkeit und Vorschub eingesetzt werden. Diese lassen sich so gestalten, dass ein konstantes Zeitspanvolumen und somit konstante Produktivität vorliegt, Bild 3. Realisiert wird dies, indem der Vorschub als Funktion der Schnittgeschwindigkeit moduliert wird. Derartige Modulationsstrategien können bei Prozessen mit geringer thermischer Werkzeugbelastung eingesetzt werden. Dies wurde beispielsweise bei der Anwendung an 42CrMo4+QT unter Hochdruckkühlschmierung nachgewiesen, bei der die thermische Werkzeugbelastung auf ein Minimum reduziert wird. Der eigentliche Vorteil dieser Strategie wird dabei nicht durch die veränderte Schnittgeschwindigkeit, sondern durch den modulierten Vorschub erzeugt. Dies konnte auch in Untersuchungen bei ausschließlicher Vorschubmodulation gezeigt werden.
Der Wirkmechanismus dieser Strategie beruht darauf, dass – bedingt durch die Veränderung des Vorschubs – die maximalen Schneidkantenbelastungen im Bereich an der Schneidkante verschoben werden. Somit ergibt sich eine Lastverteilung entlang des Eingriffsbogens. Der Verschleißwiderstand gegenüber thermischer und mechanischer Belastung lässt sich daher auf einem hohen Niveau halten. Die Strategien mit kombinierter vc/f-Modulation konnten genutzt werden, um bei linearer Modulation eine Verschleißreduktion von bis zu 20 Prozent zu erreichen.
Die erreichbare Verschleißreduktion hängt von dem Niveau der Schnittgeschwindigkeit beziehungsweise der Temperatur ab. Vorteilhaft ist eine reduzierte Schnittgeschwindigkeit, bei der das Auftreten initialer thermisch bedingter Schneidstoffschädigungen minimiert wird und das Werkzeug der erhöhten Belastung infolge des zunehmenden Vorschubs standhält.
Weiterhin kann diese Strategie genutzt werden, um sinusförmige Modulationen von Schnittgeschwindigkeit und Vorschub einzusetzen (vgl. Bild 1). Bei niedriger Schnittgeschwindigkeit kann auf diese Weise die Standzeit der Werkzeuge, bei gleichem Zeitspanvolumen, gegenüber dem Referenzprozess um 100 Prozent gesteigert werden (Bild 4). Um dies zu erreichen, muss die Schneidkeiltemperatur beziehungsweise Schnittgeschwindigkeit jedoch weiter reduziert werden, sodass es zu keiner thermischen Überlastung der Werkzeugschneide kommt.
Fazit
Der Verschleiß kann mittels Prozessstellgrößenmodulation reduziert und die Standzeit gesteigert werden. Gleichzeitig wurde gezeigt, dass die Modulationen nicht für beliebige Kombinationen aus Prozessstellgrößen, Werkstoff und Kühlstrategie geeignet sind. Nach den derzeitigen Erkenntnissen liegt dies an einem begrenzten Prozessfenster aus thermischer und mechanischer Werkzeugbelastung, in denen ein entsprechender Verschleiß des Schneidstoffs erfolgt. Um hierbei die zugrunde liegenden Wechselwirkungen zu erforschen, werden in Spanbildungssimulation die Spannungen und Temperaturfelder im Werkzeug berechnet, um hieraus kritische Belastungen abzuleiten. Somit soll ein Verständnis für die Wirkweisen von Prozessstellgrößenmodulationen geschaffen und Auslegungsmethoden erarbeitet werden, die zu einem breiten Einsatzspektrum dieser Methoden führen.
Danksagung: Die Autoren bedanken sich bei dem Bundesministerium für Wirtschaft und Klimaschutz (BMWK) und der Allianz industrieller Forschungsvereinigungen (AIF) für die Förderung des Vorhabens „Auslegung von Prozessstellgrößenmodulationen für die Stahlbearbeitung mit Kühlschmierung“ (IGF 21754). Weiter Dank gebührt der Deutschen Forschungsgemeinschaft (DFG) für die Förderung des Projekts „Grundlagen der Verschleißmechanismen und Verschleißmodellierung für instationäre Drehprozesse“ (DE447/250–1).
Literatur
- Denkena, B.; Krödel, A.; Hess, U.; Relard, A.: Performance increase by process parameter variation during turning of AISI 4140. Procedia CIRP 101, 2021, S. 21–25
Das könnte Sie auch interessieren:
Zukunftssicheres Maschinen-Upgrade mit KI und Edge Computing
Onlinefähiges Ratter-Frühwarnsystem erkennt Prozessinstabilitäten

Prof. Berend Denkena ist Leiter des Instituts für Fertigungstechnik und Werkzeugmaschinen (IFW) der Leibniz Universität Hannover. Foto: IFW
Dr.-Ing. Benjamin Bergmann leitet am IFW den Bereich Fertigungsverfahren.
Arnd Heckemeyer ist am IFW Abteilungsleiter der Zerspanung.