Unfallursache Zeitdruck
Wer sich mit der Auswertung von Unfallereignissen befasst, der wird ganz sicher irgendwann zur Einschätzung gelangen, dass die Unfallursache „menschlicher Fehler“ eigentlich der Normalfall ist. Unter Zuhilfenahme psychologischer Arbeiten zum Thema „Human Error“ wird dem Statistiker auch sehr schnell die Hoffnung genommen, dass sich dies einmal ändern könnte. Das „Fehlermachen“ ist uns scheinbar einprogrammiert, selbst die klügsten Köpfe sind davor nicht gefeit. Aus diesem Grund wurde mit dem Entstehen der industriellen Massenproduktion viel darüber nachgedacht, warum Fehler begangen werden, wie sie entstehen und letztlich, wie sie verhindert werden können. Die einfachsten Methoden waren zunächst die Kontrolle und Überwachung. Durch neue Techniken, schnellere Taktzeiten und ausgereizte Zeitkalkulationen hat sich die Arbeitswelt enorm verändert. Dadurch sind neue Fehlerquellen entstanden, z. B. durch Stress und Reizüberflutung. Es ist zu vermuten, dass viele Fehlhandlungen durch einen „Zeitdruck“ verursacht wurden. Zeit zu sparen, bzw. Handlungsabläufe zeitlich zu optimieren, ist oftmals der einzige Ausweg eine reglementierte Zeitvorgabe einzuhalten. Im folgenden Beitrag werden einige spektakuläre Fälle vorgestellt.
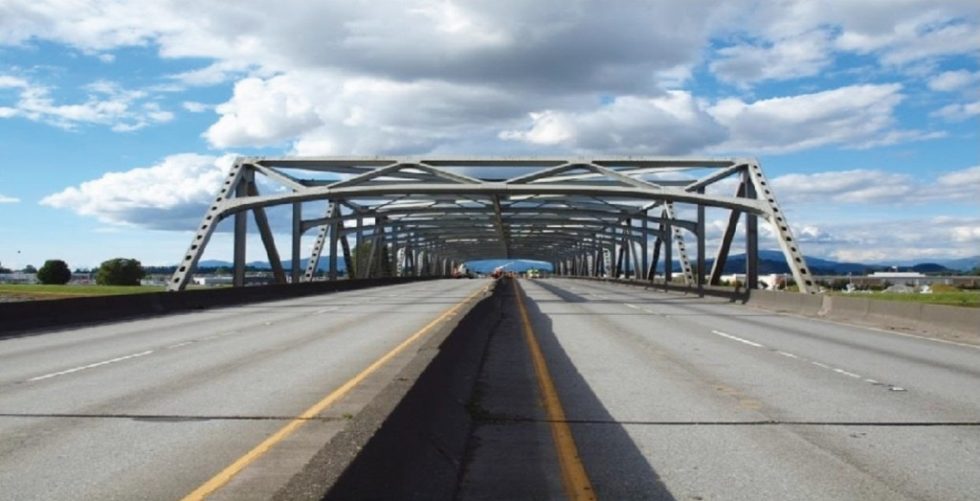
Quelle: R.Konersmann
Im umgangssprachlichen Gebrauch spricht man von einem Fehler, wenn etwas nicht so geklappt hat, wie man sich das vorgestellt hat, bzw. wenn eine Tätigkeit so ausgeführt wurde, dass das Ziel nicht erreicht wurde. Kürzer und knapper definiert eine DIN-Norm einen Fehler als „Nichterfüllung einer Anforderung“ [1].
In der Arbeitspsychologie wird noch feiner unterschieden, und zwar nach Denk-, Planungs- und Handlungsfehlern. Die Bandbreite des menschlichen Fehlverhaltens ist sehr groß, sie reicht vom einfachen Lapsus bis zum unglücklichen, zeitlich zusammentreffenden Fehlverhalten mehrerer Personen. In diesen Fällen pflanzt sich ein Fehler als Fehlerkette fort und führt oftmals zu katastrophalen Folgen, z. B. Tankerhavarien, Flugzeugabstürze oder Kernschmelzen. Einfachen Montagefehlern kann man durch eine Formcodierung vorbeugen, die den Zusammenbau nur in einer vorbestimmten Weise erlaubt, z. B. bei elektrischen Steckverbindungen. Fehler innerhalb einer automatisierten und computergestützten Montagekette können zwar während des Herstellungsprozesses identifiziert werden, z. B. wenn sich Materialfehler eingeschlichen haben, trotzdem wird oftmals eine abschließende Funktionsprüfung vorgenommen.
Zeitbasierte Fehler entstehen immer dann, wenn es während eines Transports oder einer Produktherstellung nicht gelingt, Zeitpläne, Fahrpläne oder vertraglich vereinbarte Liefertermine einzuhalten, um nur einige Gründe zu nennen. Sie könnten vermieden werden, wenn Zeitfenster vorhanden wären, die es erlaubten, eine Zeitvereinbarung oder Terminplanung zu korrigieren. Wir leben jedoch in einer Epoche, in der die Zeit mit Geld verglichen wird. Das legendäre Bonmot Benjamin Franklins „Zeit ist Geld“ wurde 1748 aufgeschrieben und hat nach über 260 Jahren noch nichts von seiner Aussagekraft eingebüßt. Seinerzeit prangerte Franklin jedoch zuallererst die unproduktive Zeitverschwendung an. Heutzutage wird die Zeit im Zusammenhang mit der Geschwindigkeit definiert. Wir hören ständig von zeitnahen Entscheidungen, prompten Lieferungen und schnellem Internet.
Der Zwang zur Eile
Anfang der 1970er-Jahre kamen findige Automobilbauer auf die Idee, dass man viele Kosten sparen kann, wenn die Zulieferer von Einzelbauteilen einem Kunden ihre Waren direkt dort hin liefern, wo sie zur weiteren Verarbeitung benötigt werden und zwar zu dem Zeitpunkt, an dem sie gebraucht, also verbaut werden. „Just in Time“ ist die dafür gängige Beschreibung. Dadurch wurden große Materiallager überflüssig und die Lagerhaltungskosten konnten gespart werden. Dieses Verfahren funktioniert jedoch nur dann reibungslos, wenn die Lieferkette nicht unterbrochen wird, z. B. durch Verkehrsunfälle. Zwei eindrucksvolle Beispiele dafür sind der Unfall des Tankmotorschiffes „Waldhof“ auf dem Rhein am 13. Januar 2011 [2] und der Unfall auf der Wiehltalbrücke der Bundesautobahn 4 am 26. August 2004 [3].
Der Kenterunfall des Tankmotorschiffes „Waldhof“ verursachte eine Blockade des Binnenschiffsverkehrs über 32 Tage und den zwangsbedingten Stopp von 450 Binnenschiffen. Die Schäden für Transportunternehmer durch Umdisponierung auf andere Verkehrsträger und die Schäden bei Warenempfängern infolge verzögerter Lieferung waren immens. Eine ungefähre Abschätzung des monetären Schadens ist nicht bekannt. Die Reparatur der Wiehltalbrücke dauerte fast zwei Jahre und war mit einer Schadenssumme von 32 Mio. € der bis dato teuerste Autounfall Deutschlands.
Diese Unfälle verdeutlichen insbesondere die Risikosituation zwischen Zulieferer und Empfänger: Eine jahrelang reibungslos funktionierende Transportkette kann plötzlich durch die Einwirkung Dritter unterbrochen werden, sodass ernsthafte wirtschaftliche Probleme entstehen können.
Derartige Unterbrechungen können i. d. R. kurzfristig kompensiert werden, es sei denn, dass, wie im Fall der „Waldhof“, ein „Nadelöhr“ betroffen ist, dessen Umfahrung nicht ohne weiteres möglich ist.
Die Risiken der „Just-in-Time“-Methodik extensivieren sich auf viele Parteien, je nach Grad ihrer Einbindung in den Gesamtprozess. Für die Zulieferer, die den riskanten Transportprozess sicherstellen müssen, ergeben sich daraus mitunter auch unerwünschte Abhängigkeiten. Die Erwartungshaltung, einen Zulieferauftrag unter allen Umständen pünktlich erfüllen zu müssen, kann zu einem Zeitdruck führen, der zu Überreaktionen führt, z.B. zu Geschwindigkeitsüberschreitungen, aggressiven Fahrweisen und Vorschriftenmissachtung. Planungsfehler werden also durch Zeit kompensiert, indem man schneller transportiert, vermeintliche Prüfungen verkürzt oder gänzlich weglässt.
Zeitersparnis durch Geschwindigkeit
Seit jeher müssen fast alle Produkte vom Ort der Herstellung zum Verbraucher transportiert werden, z. T. über beachtliche Distanzen. Um diese Plackerei einigermaßen kraftsparend und wirtschaftlich zu gestalten, ersannen unsere Vorfahren viele Hilfsmittel – Rutschen, Schlitten und schließlich Räder. Das Rad war seinerzeit wahrscheinlich ebenso revolutionierend wie heutzutage das Internet, von der Computertechnik ganz zu schweigen. Es ließen sich noch viele Beispiele anführen. Wie die Entwicklung der Transportmittel inzwischen vonstatten ging, bedarf keiner Erläuterung, nur soviel – alles wurde schneller, schwerer und auch größer. Da der Straßengüterverkehr besonders dominant ist, wird dem Straßenbau (Querschnitte, Raumbedarf) hohe Aufmerksamkeit gewidmet. Besondere Nadelöhre stellen Tunnel- und Brückenbauwerke dar. Sie wurden/werden für eine lange Lebensdauer konzipiert und können nicht nachträglich wesentlich verändert werden. Während die Transportmittel ständig modifiziert werden, z. B. hinsichtlich Größe, Gewicht und Achslasten, bleibt eine Brücke hinsichtlich ihrer Tragfähigkeit bestenfalls konstant. Dazu kommt, dass das Verkehrsaufkommen im Laufe der Jahre ständig wächst und dadurch die berechneten Sicherheitsreserven erschöpft werden. Neben den Schwingungsbelastungen tragen auch Korrosionswirkungen zum Bauwerksverschleiß bei. Dies ist ein Grund, warum Brückenbauten einer ständigen Aufsicht unterliegen. Ein Brückeneinbruch oder eine zeitweilige Sperrung verursacht einen katastrophalen Verkehrskollaps und sehr hohe wirtschaftliche Folgekosten, wie zahlreiche Beispiele aus den USA belegen (z. B. Minneapolis, 1. August 2007 [4]).
Problem Schwerguttransporte und Übergrößen
Hin und wieder kommt es vor, dass ein spezielles, sehr großes Maschinenteil oder ein Behälter auf einer Straße nur in einem Stück transportiert werden kann. Der Transport eines übergroßen Bauteils stellt eine besondere Herausforderung dar. Der Transportweg muss hinsichtlich seiner Eignung genauestens untersucht werden. Mitunter müssen Bäume gefällt, Verkehrszeichen, Ampelanlagen, Oberleitungen, Fußgängerbrücken usw. demontiert werden. Es dürfte Konsens darüber bestehen, dass diese gut organisiert sind und in der Regel komplikationslos ablaufen, also eigentlich völlig normal sind. Es kann aber auch sein, dass alles ganz anders kommt.
Nadelöhr Brücke
Im Mai 2013 musste ein übergroßes Bauteil von einem Hersteller in British Columbia (Kanada) zu seinem Verladeort, dem Hafen von Vancouver, US-Staat Washington, transportiert werden, d. h. über eine Strecke von ca. 1 000 km. Hierfür mussten Genehmigungen eingeholt und die genaue Transportstrecke beschrieben werden. Die Genehmigungsbehörde, das Washington State Department of Transportation (WSDOT), gab seine Zustimmung., jedoch versehen mit dem Hinweis: „The Department does not guarantee height clearances; therefore, on any route where the height is in question, a front escort vehicle with a heigh pole should be used.” Des Weiteren mussten die Abmessungen des Transports genauestens ermittelt werden. Interessant ist in diesem Zusammenhang die Ermittlung der Transporthöhe. Der Fahrer verwendete dazu ein zweiteiliges Teleskoprohr, das jedoch im ausgefahrenen Zustand nur 4,57 m maß und somit zu kurz war. Der Messstab wurde darum durch ein Stahlmaßband verlängert, das infolge abgegriffener Maßzahlen kaum ablesbar war. Der Fahrer stellte mit diesem Messverfahren eine Transporthöhe von 4,8 m fest, was sich im Nachhinein als falsch herausstellte. Die tatsächliche Höhe wurde durch das NTSB mit 4,85 m ermittelt [5]. Diese Höhendifferenz von wenigen Zentimetern sollte noch eine eindrucksvolle Bedeutung erlangen. Die Besonderheit bestand auch darin, dass das „Oversize combination vehicle“ in allen Dimensionen die Normalgrößen übertraf (Bild 1).
Im Routenverlauf lag auch eine Brücke über den Skagit- River. Diese Brücke weist jedoch eine Besonderheit auf. Sie wurde in einer Fachwerk-Kastenträger-Bauweise ausgeführt und verfügt über keine statischen Reserven, d. h. eine Beschädigung würde mit großer Wahrscheinlichkeit sofort zum Integritätsverlust führen. Außerdem hat sie durch diese Bauweise nur eine begrenzte Durchfahrtshöhe, auf die kein Warnschild hinwies, sowohl vor der Einfahrt zur Brücke als auch am Brückenportal (Bild 2).
Auch aus diesem Grund wurde der Transport von einem vorausfahrenden Escort-Fahrzeug begleitet. Dieses Fahrzeug war mit einem fest montierten Messstab ausgerüstet (wie vom WSDOT empfohlen), an dessen oberen Ende ein Gummiball befestigt war, der wahrscheinlich dem Fahrer die erforderliche Durchfahrtsfreiheit signalisieren sollte (Bild 3).
Die Fahrerin des Escort-Fahrzeuges entnahm den Transportpapieren die Höhenangabe von 4,8 m und addierte dazu noch einen Sicherheitszuschlag von ca. 13 cm, sodass die „Sicherheitshöhe“ von 4,93 m eine ungehinderte Passage sicherstellen sollte. Die Skagit-Brücke hat zwei zweispurige Richtungsfahrbahnen, jede weist zwischen den Fahrbahnmarkierungen eine Breite von exakt 3,45 m auf. Eine weitere Besonderheit dieser Brücke ist, dass die Höhe über den Fahrspuren nicht konstant ist (Bild 4).
Aus diesem Grund wurde am Ecsort-Fahrzeug die Messstange mit einem seitlichen Versatz von 0,64 m angebracht. Die Idee war, dass, wenn das „Messfahrzeug“ mit dem rechten Reifen strikt auf der rechten Fahrbahnbegrenzung fährt, der Oversize-Truck dadurch eine Orientierung erhält, die eine Kollision mit dem Querverband der Brücke sicher ausschließen sollte. Es stellt sich nun die Frage, warum nicht von vornherein die linke Fahrspur benutzt wurde. Die umständliche und wacklige Messeinrichtung wäre dadurch überhaupt nicht notwendig gewesen. Dieser Tross, vorab das Escort-Fahrzeug mit Messstange, ca. 120 m dahinter der Truck, fuhr in das Brückenportal mit der zulässigen Höchstgeschwindigkeit von 60 mph ( 96 km/h) ein.
Es wäre beispielsweise vorstellbar gewesen, vor der Passage des Brückenportals, die Geschwindigkeit deutlich zu verringern, schon um die Spur besser zu halten, quasi besser „zielen“ zu können, auch mit dem Wissen, dass die übergroße Ladung gerade so durch das Portal passt. Aber scheinbar war dies für das Gespann das geringste Problem. Zu allem Unglück wurde, gerade in diesem Augenblick, der Oversize-Truck auf der linken Fahrspur von einem anderen Truck überholt. Der Fahrer gab später dem NTSB die Auskunft, dass er sich dadurch eingeengt bzw. bedrängt fühlte (Bild 5).
Sehr wahrscheinlich ist, dass der Fahrer des Oversize-Fahrzeugs das Lenkrad reflexartig nach rechts zog und mit der Oberkante der Ladung zwei seitliche Brückenspanten durchschlug. Die Folge war, dass ein ca. 25 m langes Segment abknickte und in den Fluss fiel. Der Oversize-Truck erreichte noch das andere Ufer, drei weitere Fahrzeuge, die sich auf gleicher Höhe befanden, stürzten in den Fluss (Bild 6).
Der Lastzug auf der linken Überholspur bemerkte vom Unfall nichts und konnte erst später ausfindig gemacht werden. Zahlreiche Farbabschürfungen bewiesen, dass dieser dem Oversize-Truck zu nahe gekommen war.
Die Insassen der in den Fluss gestürzten Fahrzeuge kamen mit dem Schrecken davon, niemand wurde ernsthaft verletzt. Der Gesamtschaden belief sich auf fast 20 Mio. US-Dollar. Die Untersuchungsbehörde, das NTSB, rügte vor allen Dingen die schlechte Fahrtvorbereitung/Streckenerkundung durch die Fahrerin des Begleitfahrzeugs. Bei der Unfalluntersuchung kam des Weiteren heraus, dass die Fahrerin während der Fahrt ein Mobiltelefon benutzte und dadurch abgelenkt wurde. Es wurde auch bemängelt, dass vor der Brückenpassage nicht auf die linke Fahrspur gewechselt wurde. Die für einen Oversize-Transport ungewöhnlich hohe Fahrgeschwindigkeit bei der Brückeneinfahrt von 60 mph wurde nicht als Unfall begünstigend erwähnt. Vielmehr wurde darauf hingewiesen, dass auf den Interstates, auch im Staat Washington, für gewöhnlich eine mittlere Geschwindigkeit von 68 mph (> 100 km/h) gefahren wird. Als Fazit bleibt festzustellen, dass bei diesem Transport einiges dem Zufall überlassen wurde, d. h. nicht alle möglichen Begleitumstände bedacht worden sind, z. B. das Überholen des Transports im Brückenbereich. Eine rückwärtige Absicherung des Transports, die einen Überholvorgang möglicherweise verhindert hätte, wurde nicht vorgenommen. Zu bedenken ist außerdem, dass die Fracht zur Verschiffung zum Hafen Vancouver transportiert werden sollte. Die für einen derartigen Transport hohe Transportgeschwindigkeit lässt den Verdacht aufkommen, dass der Transport unter Zeitdruck stand. Dies würde auch erklären, warum keine zusätzlichen Sicherungsmaßnahmen, z. B. polizeiliche Absperrungen im Brückenbereich, eingeplant wurden.
Schneller, besser, billiger
Ein weiteres Konzept zur Minimierung von Kosten und Aufwand wird von der Weltraumindustrie verfolgt. Die wirtschaftlichen Aufwendungen für die bemannte Weltraumfahrt und für die Erforschung des Weltraums durch Raumsonden sind enorm. Aus diesem Grund wird die unbemannte Raumforschung konsequent der „Faster-better-cheaper“-Philosophie unterworfen, was bedeutet, dass der Kosten- und Zeitrahmen nicht überschritten werden darf. Der erste Versuch muss unter allen Umständen gelingen! Die Konsequenz dieser Strategie ist, dass ein Entwicklungsteam in vielen Fällen permanent unter dem Damoklesschwert des Missionsabbruchs arbeiten muss. Ein plötzlich auftretendes Problem führt zu Stressreaktionen und zu Überlegungen, wie das Große/Ganze doch noch gerettet werden kann. Die einzige „Reserve“, die in solchen Fällen angezapft werden kann, ist der Zeitfaktor. Zeit sparen durch Weglassen. In der Regel sind dies notwendige Funktionsüberprüfungen von Steuerungen oder Notabschaltsystemen, um nur einige zu nennen. Man hofft, dass es schon gut gehen wird. Aber oftmals steckt der Teufel im Detail, wie das nächste Beispiel zeigt.
NASA-Mission Genesis
Die Raumsonde Genesis (Gesamtgewicht 636 kg, ca. 2 x 2,3 m groß, mit Solarpanelen von ca. 8 m Länge [6]) wurde am 8. August 2001 gestartet. Die Rückkehr erfolgte am 8. September 2004, also nach einem dreijährigen Einsatz.
Ziel der Mission war u. a. die Untersuchung von Sonnenwindpartikeln, die in einer speziellen Rückkehrkapsel aufgefangen und durch äußere Einflüsse unverfälscht und behutsam zur Erde zurückgebracht werden sollten. Aus diesem Grund sollte die an einem Fallschirm zur Erde sinkende Sonde noch in der Luft, mithilfe von Hubschraubern, abgefangen werden. Man wollte unter allen Umständen verhindern, dass die Probekapsel bei der Landung irgendwelchen äußeren Belastungen ausgesetzt wird oder die wertvollen Materialproben beschädigt oder verunreinigt werden.
Nach dem Abtrennen von der Genesis-Muttersonde und dem Wiedereintritt der Kapsel in die Erdatmosphäre sollte daher diese, nach Erreichen einer Abbremsung von 3 g ( 29,4 m/s²), an einem Fallschirm mit einer Geschwindigkeit von ca. 13 km/h, zur Erde sinken. Der Plan sah vor, die herabsinkende Kapsel mit zwei Hubschraubern „einzufangen“. Dazu wurde an einer 5,6 m langen Stange ein Haken befestigt, der ein Fallschirmseil greifen sollte. Mit Keflarseilen sollte dann die Sonde arretiert und zu einem vorbereiteten, mit Stickstoff gefüllten Reinraum transportiert werden. Es war an alles gedacht, doch die extra geschulten Stuntmen konnten nur fassungslos zusehen, wie die Sonde mit ca. 311 km/h an ihnen vorbeirauschte und sich in den Wüstenboden grub.
Ursachenuntersuchung
Zur Analyse der Absturzursache wurde die Fehlerbaumanalyse verwendet. Auf das Wesentliche zusammengefasst ergab diese, dass keine komplizierte Ereigniskette zum Scheitern führte, sondern ein simpler Einbaufehler, den man hätte erkennen können, wenn man sich die Zeit dazu genommen hätte [7].
Es stellte sich heraus, dass zwei Beschleunigungssensoren, ein Bauteil von ca. 4 mm Durchmesser und 10 mm Länge auf einem Relaismodul seitenverwechselt montiert wurden (Bild 7).
Diese Sensoren hatten die Aufgabe, bei Erreichen einer Abbremsung von 3 g, die Initialisierung des Landemodus auszulösen, der letztlich zum Heraussprengen des Bremsfallschirms führen sollte. Zum Test der Beschleunigungssensoren werden im Allgemeinen Zentrifugentische verwendet. Auf diesen Test wurde aber aus Zeitgründen verzichtet. Es setzte sich die Auffassung durch, dass eine optische Kontrolle und ein Vergleich mit Konstruktionszeichnungen ausreichend seien. Darüber wurde jedoch vergessen, dass diese Sensoren eigentlich nur mechanische Schalter sind, bei denen eine Masse gegen eine Feder drückt und dadurch einen Kontakt herstellt (Bild 8).
Der beauftragte Ingenieur konnte anhand der Übersichtszeichnung keine Fehler feststellen. Auf die Orientierung bzw. Einbaurichtung gab es auf der Platine keinen Hinweis. Der Montagefehler hätte nur dann erkannt werden können, wenn man Ingenieure des Herstellers, die die Funktionsweise des Sensors kannten, mit der optischen Kontrolle beauftragt hätte. Da dies aus Zeit- und Kostengründen unterlassen wurde, wurde als Hauptfehlerursache ein zu rigides Zeitmanagement festgestellt.
Die Diktatur des Fahrplans
Alle Tätigkeiten, bei denen eine bestimmte Uhrzeit einzuhalten ist, können bei Fehlplanungen, Unachtsamkeiten, Reizüberflutungen usw. zu Stressreaktionen führen, die einen Zeitdruck verursachen, der, je nach (eingebildeter) Wichtigkeit, nur mit Schnelligkeit kompensiert werden kann. Im öffentlichen Leben spielen Fahrpläne und vereinbarte Liefertermine eine große Rolle. Beim Schienentransport sind Fahrpläne, d. h. verbriefte An- und Abfahrtzeiten eine Notwendigkeit zur Abwicklung der Transportaufträge. Verspätungen sind daher ärgerlich, aber nicht auszuschließen. Niemand kann vorhersehen, dass eine Viehherde außer Kontrolle gerät, ein Baum auf die Gleise stürzt oder ein Langholztransporter auf dem Bahnübergang stehen bleibt. Derartige Ereignisse werden unter dem Oberbegriff „höhere Gewalt“ abgebucht, sich darüber aufzuregen lohnt nicht.
Es gibt jedoch auch Fälle, bei denen die Pünktlichkeit zur Betriebsphilosophie erhoben wurde, z. B. bei Eisenbahnunternehmen. In vielen Teilen der Welt wird dies moderat gehandhabt, sodass nicht jede Fahrplanverspätung zum Drama wird, es gibt jedoch auch Ausnahmen. Durch ein schweres Zugunglück in der japanischen Stadt Amagasaki am 25. April 2005 wurde bekannt, dass der Fahrer eines Vorortexpresszugs versucht hatte, eine Verspätung von 90 s (!) aufzuholen [8]. In diesem Unternehmen wurde die Fahrplantreue gegenüber den Kunden quasi zur Religion erhoben. Jeder Verstoß gegen eine Missachtung des Fahrplans wurde aufmerksam registriert, Verspätungen wurden nicht akzeptiert und geahndet. In einem derartigen Arbeitsklima war es nicht überraschend, dass der Führer des Unglückszugs versuchte, die Verspätung durch eine erhöhte Geschwindigkeit zu kompensieren. Anstelle der erlaubten Geschwindigkeit von 70 km/h wurden mehr als 130 km/h gefahren [9]. In einer Kurve rissen die Fliehkräfte zwei Wagen aus der Kurve, die in ein Wohnhaus prallten. Die Folgen waren mehr als 100 Tote und zahlreiche Verletzte.
Auch an Bahnübergängen sind Unfälle, für die als Ursache Zeitdruck ermittelt wurden, nicht selten. In vielen Ländern, z. B. in den USA, Kanada und Australien, sind die Übergänge lediglich durch blinkende Warnlichter gesichert. Oftmals sind auch die Sichtverhältnisse nicht ideal, z. B. in Waldgebieten oder in Kurven. Die Verführung ist daher groß, zu versuchen, trotz blinkenden Lichts, noch schnell „durchzuhuschen“ und das Reiseziel, z.B. einen wartenden Kunden doch noch zeitnah zu beliefern, zu erreichen. Manchmal gelingt dies jedoch nicht [10].
Fazit
Die vorgenannten Beispiele zeigen, dass Arbeiten unter zeitlicher Anspannung dazu führen können, dass sich Fehler einschleichen. Die Feststellung der Fehlerursache „menschlicher Fehler“ ist in solchen Fällen aber unbefriedigend und scheint die Ursache nicht richtig bzw. nur unvollständig widerzuspiegeln. Interessant wäre es zu wissen, wie dieser „Druckaufbau“ zustande kommt, wer oder was dafür verantwortlich ist. In einem hier geschilderten Fall wurde als Unfallursache „Zeitdruck“ eindeutig nachgewiesen. In vielen Fällen kann dieser klare Nachweis nicht oder nur unvollständig erbracht werden. Es besteht der Verdacht, dass dies auch daran liegen könnte, das dies in den meisten Fällen nicht hinterfragt wird und/oder es den unmittelbar Beteiligten nicht bewusst ist. Es darf auch vermutet werden, dass auch arbeitspsychologische Aspekte einwirken, z. B. Erwartungshaltungen, Ehrgeiz, personelle Abhängigkeiten usw. Dies ist jedoch nicht nur ein Problem der unmittelbar Beteiligten sondern auch der Personen, die für das Zeitmanagement verantwortlich sind. TS 530
Literaturverzeichnis
[1] DIN EN ISO 9000: Qualitätsmanagementsysteme – Grundlagen und Begriffe. Berlin: Beuth Verlag 2005.
[2] Untersuchungskommission TMS „Waldhof“ bei der Wasser- und Schifffahrtsdirektion Südwest. Mainz 8. Januar 2013, S-312.4/016.
[3] https://de.wikipedia.org/wiki/Wiehltalbr%C3%BCcke
[4] Highway Accident Report (NTSB/HAR-08/03): Collapse of I-35W Highway Bridge Minneapolis, Minnesota, August 1, 2007, National Transportation Safety Board, Washington, D.C.
[5] Highway Accident Report (NTSB/HAR-14/01): Collapse of the Interstate 5 Skagit River Bridge Following a Strike by an Oversize Combination Vehicle, Mount Vernon, Washington May 23, 2013, National Transportation Safety Board, Washington, D.C.
[6] www.bernd-leitenberger.de/genesis.shtml.
[7] GENESIS-Mishap Investigation Board Report, Vol. I. Ed.: National Aeronautics and Space Administration (NASA). Washington, D.C. 2005.
[8] www.Spiegel.de/panorama/Zugunglück-Lokführer soll aus Angst zu schnell gefahren sein. 29. April 2005.
[9] Ende einer Höllenfahrt. Berliner Zeitung vom 26. April 2005.
[10] Rail Safety Investigation QT2459, Fatal Collision between the Cairns Tilt Train and B-Double Truck Rungoo Level Crossing, Queensland, 27. November 2008, Final Report. Queensland Government, Department of Transport and Main Roads 2009.
Dr.-Ing. Rainer Konersmann, ehemals Bundesanstalt für Materialforschung und -prüfung (BAM), Berlin.