Flexible Fertigung von Profilbauteilen ab Losgröße 1
Konventionelle Blechumformtechnologien sind bei geringen Stückzahlen häufig unwirtschaftlich. Roboterbasiertes Rollformen ist ein inkrementelles Verfahren zur flexiblen Fertigung von Profilbauteilen ab Losgröße 1. Die Umformung erfolgt mit einem Rollenkopf, der durch einen Roboterarm zugestellt und über das Werkstück bewegt wird. Durch die kinematische Gestalterzeugung können Werkzeugkosten gesenkt und kleine bis mittlere Stückzahlen wirtschaftlich gefertigt werden.
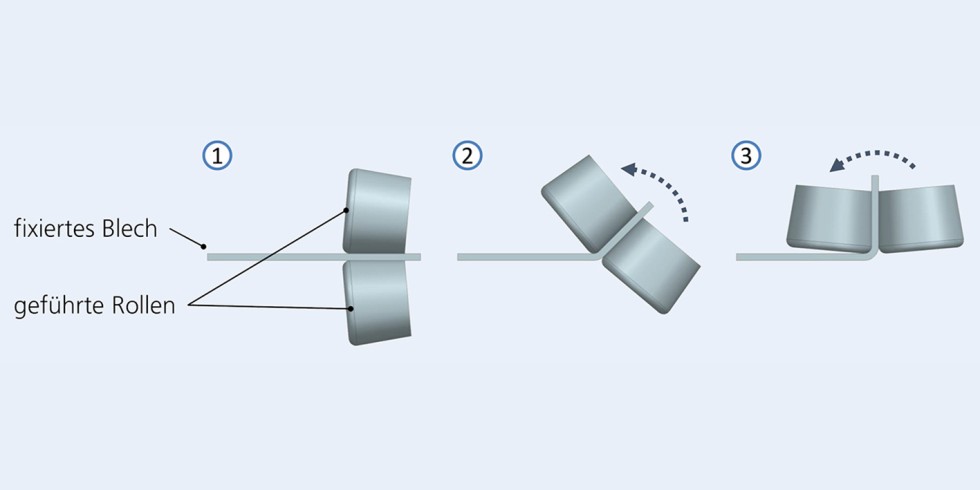
Bild 1. Verfahrensprinzip des roboterbasierten Rollformens. Grafik: Fraunhofer IWU
Ausgabe 10-2021, S. 709
1 Motivation
In der Fertigung von Blechbauteilen ist eine verstärkte Ausrichtung auf eine Vielfalt an kundenangepassten Varianten erkennbar, die individuelle Lösungen erfordert. Konventionelle Umformtechnologien, wie Tiefziehen oder Walzprofilieren, sind jedoch in der Regel auf große Stückzahlen ausgelegt und durch den hohen Formspeichergrad der Werkzeuge selbst bei mittleren Serien unwirtschaftlich. Einer Flexibilisierung des Bauteilspektrums steht der Anlagen- und Werkzeugaufwand entgegen. Für eine wirtschaftliche und sehr gut automatisierbare Erzeugung von Profilbauteilen in Kleinserien bis hin zu einer Einzelteilfertigung sind Fertigungstechnologien, wie etwa das Abkanten mit formgebundenen Werkzeugen [1], das inkrementelle Abkanten mit Dorn [2], der StaBiFü-Ansatz [3] oder das 3D-Rollforming-Center von data M [4] verfügbar. Die Flexibilität in der Bauteilfertigung ist auch bei diesen Verfahren durch die hohe Formbindung in den verwendeten Werkzeugen und Spannkonzepten begrenzt.
Am Fraunhofer-Institut für Werkzeugmaschinen und Umformtechnik IWU wird mit dem roboterbasierten Rollformen eine Technologie entwickelt und erprobt, die das Potenzial bietet, mit geringer Werkzeugbindung flexibel Profilbauteile unterschiedlicher Komplexität zu fertigen.
2 Profilherstellung durch roboterbasiertes Rollformen
Die Formgebung erfolgt mit einem auf definierten Bahnen geführten Rollenpaar. Dieses ist Teil eines Endeffektors, der von einem Roboter manipuliert wird. In die Systematik der Fertigungsverfahren nach DIN 8586 [5] ordnet sich die Technologie (analog zum konventionellen [6] und flexiblen Walzprofilieren [7–9]) in die Biegeumformverfahren mit drehender Werkzeugbewegung ein. Die Realisierung einer definierten Biegefolge („Profilblume“) erfolgt durch das inkrementelle Anstellen des Roboterarmes oder durch die Aktorik des Endeffektors (Bild 1).
Statt wie beim Walzprofilieren zahlreiche Walzgerüste mit formgebundenen Rollen zu durchlaufen, ist das Werkstück ortsfest und wird wiederholt durch das Rollenpaar passiert. Durch den gegenüber etablierten Prozessvarianten signifikant reduzierten Anlagen- und Werkzeugaufwand weist das Verfahren eine deutlich gesteigerte Flexibilität bei realisierbaren Bauteilvarianten auf, für die im Wesentlichen nur die Bewegungsbahnen definiert und programmiert werden müssen. Durch eine gezielte, lokal adaptierte Variation des Schwenkwinkels können technologisch bedingte Formabweichungen kompensiert werden. Diese werden durch verschiedene Geometrieparameter (wie Blechdicke, Biegeradius, Flanschhöhe, Biegeinkremente) und Werkstoffparameter (zum Beispiel Verfestigungsverhalten, E-Modul) bestimmt. Das anvisierte Bauteilspektrum reicht von einfachen Profilen und Maschinenverkleidungen mit Biegekanten bis hin zu komplexen, räumlich gekrümmten Profilbauteilen. Die Prozessentwicklung und -auslegung erfolgt mit experimentellen und numerischen Untersuchungen.
3 Prozessentwicklung und -auslegung
3.1 Experimentelle Untersuchungen
Für die experimentellen Untersuchungen wird ein Endeffektor genutzt, dessen Rollen passiv mitlaufen. Um unterschiedliche Blechdicken umzuformen, kann der Rollspalt manuell zwischen 0,5 mm und 5,0 mm variiert werden. Geführt wird der Endeffektor von einem Industrieroboter („KR150 R2700 Extra“ von Kuka). Im derzeitigen prototypischen Versuchsaufbau (Bild 2) wird das Blech durch Spanneisen zwischen Niederhalter und Grundplatte fixiert.
Um eine Kollision von Niederhalter und Endeffektor zu vermeiden, ist der Niederhalter mit einer 65°-Fase versehen. So kann er für Biegewinkel ≤ 60° direkt an der Biegekante positioniert werden. Biegewinkel > 60° sind durch eine Positionierung mit einem größeren Abstand zur Biegekante realisierbar. Zur Prozesscharakterisierung werden zusätzlich zur Aufzeichnung der wirkenden Umformkräfte die Bauteile nach einzelnen Umforminkrementen mit einem optischen Messsystem („T-Scan CS“ von Steinbichler) vermessen.
Die Umformstrategie beeinflusst die Bauteilqualität und die Zykluszeiten für die Profilherstellung signifikant. Variationsparameter sind zum Beispiel die Biegeinkremente je Durchgang und die konkrete Durchführung des Schwenkvorgangs inklusive Festlegung der Bewegungspunkte des Roboters. Hier hat sich gezeigt, dass vor allem mit kleinen Biegeinkrementen, etwa 10°-Schritten, selbst höherfeste Stahlbleche umgeformt werden können. Beim Schwenken können je nach Anwendungsfall verschiedene Strategien eingesetzt werden: Dazu gehört das Anstellen über eine kurze Wegstrecke oder an einem Ort und das Weiterfahren der Bahn mit konstanter Anstellung sowie das gleichmäßige Anstellen des Endeffektors um ein definiertes Biegeinkrement über die gesamte Bauteillänge. Ein bidirektionales Anstellen der Rollen, bei dem auf der Rückwärtsbahn bereits das nächste Biegeinkrement zugestellt wird, ist genauso möglich wie ein unidirektionales.
Rückfederungseffekte und Formabweichungen, etwa durch die last- und positionsabhängige Steifigkeit des Industrieroboters, können durch gezielte Bahnmanipulation bauteilspezifisch korrigiert werden. Dazu wurden verschiedene Richtstrategien erprobt, bei denen auf Basis optischer Messergebnisse ein lokal angepasstes Überbiegen erfolgt. Dieser Prozess lässt sich durchlaufzeitneutral in den Umformprozess integrieren. Trotz des minimalen Werkzeugaufwandes konnten so maß- und formhaltige Bauteile hergestellt werden.
3.2 Numerische Untersuchungen
Zur Vertiefung des Prozessverständnisses werden die experimentellen Arbeiten von umfassenden numerischen Untersuchungen im FEM (Finite-Elemente-Methode)-Programm „MarcMentat“ begleitet. Zunächst wurden verschiedene Modellierungsansätze hinsichtlich der Elementtypen (Volumenelement, Solid Shells und Shells) und -größen untersucht und die FE-Ergebnisse anhand der optischen Messergebnisse der Versuchsteile validiert. Das resultierende Modell dient nun zur Optimierung der Umformstrategie und Roboterbahn sowie zur Analyse experimentell schwer erfassbarer Effekte wie dem Spannungszustand in der Umformzone und dem Umformgrad (Bild 3).

Bild 3. Zwischenstufe bei der FEM (Finite-Elemente-Methode, dargestellt Umformgrad φ). Grafik: Fraunhofer IWU
Wie bei den etablierten Walzprofiliervarianten gilt es auch beim roboterbasierten Rollformen, kritische Bandkantendehnungen nicht zu überschreiten, da dies zu Welligkeiten führt. Die numerische Analyse der Bandkantendehnung ermöglicht die Identifizierung kritischer Biegeinkremente und die Optimierung der Umformstrategie. So können Profilbauteile mit unterschiedlichen Geometrien zügig umgesetzt werden. Die Ermittlung der wirkenden Werkzeugbelastungen durch FEM dient der Weiterentwicklung und Auslegung lastangepasster Endeffektoren.
4 Zusammenfassung und Ausblick
Roboterbasiertes Rollformen ist eine innovative Fertigungstechnologie zur kosteneffizienten Herstellung von Profilbauteilen unterschiedlicher Komplexität auch in geringster Stückzahl.
Experimentelle und numerische Untersuchungen lassen darauf schließen, dass mit minimalem Werkzeugaufwand maßhaltige Bauteile realisierbar sind. Die systematische Weiterführung der Arbeiten zielt auf die Erhöhung der Form- und Maßhaltigkeit sowie auf die Umsetzung variabler Blechdicken.
Die Projekte FlexHyBat (Förderkennzeichen 19I20019F) und AVAIL (Förderkennzeichen 20W1906F) werden gefördert vom Bundesministerium für Wirtschaft und Energie aufgrund eines Beschlusses des Deutschen Bundestages.
Literatur
- Klocke, F.; König, W.: Umformen. Berlin: Springer-Verlag 2006
- Voswinckel, D. H.: Abkanten und Kragenziehen mit der inkrementellen Blechumformung. Dissertation, RWTH Aachen, 2017
- Werner, M.: StaBiFü® – efficient manufacturing of structural parts. Presentation held at 5. Automotive Photonics Konferenz, Ditzingen/Germany, 2019
- Sedlmaier, A.; Dietl, T.: 3D roll forming center for automotive applications. Procedia Manufacturing 15 (2018), pp. 767–774
- DIN 8586: Fertigungsverfahren Biegeumformen – Einordnung, Unterteilung, Begriffe. Ausgabe September 2003
- Halmos, G. T.: Roll forming handbook. Boca Raton: Taylor & Francis 2006
- Istrate, A.: Verfahrensentwicklung zum Walzprofilieren von Strukturbauteilen mit über der Längsachse veränderlichen Querschitten. Dissertation, TU Darmstadt, 2002
- Woo, Y. Y.; Han, S. W.; Oh, I. Y. et al.: Shape Defects in The Flexible Roll Forming of Automotive Parts. International Journal of Automotive Technology 20 (2019) 2, pp. 227–236
- Abeyrathna, B.; Abvabi, A.; Rolfe, B. et al.: Numerical analysis of the flexible roll forming of an automotive component from high strength steel. IOP Conference Series: Materials Science and Engineering 159 (2016), p. 12005
Dipl.-Ing. Karsten Richter
Dr.-Ing. Thoralf Gerstmann
Ph.D. Valentin Richter-Trummer
Antje Ahrens, M. Sc.
Tina Abdolmohammadi, M. Sc.
Dr.-Ing. Matthias Nestler
Dipl.-Ing. Markus Werner
Prof. Dr.-Ing. habil. Verena Kräusel
Fraunhofer-Institut für Werkzeugmaschinen und Umformtechnik IWU
Reichenhainer Str. 88, 09126 Chemnitz
Tel. +49 371 / 5397-1106
karsten.richter@iwu.fraunhofer.de
www.iwu.fraunhofer.de