Beschichtete Zylinderlaufbahnen sind in der Automobilindustrie im Trend
Immer mehr Pkw-Modelle erhalten Motorblöcke aus Leichtmetallguss mit beschichteten Zylinderlaufbahnen. Dadurch sind sie kompakter, leichter und verursachen weniger Schadstoffemissionen. Um die Beschichtungen aufbringen zu können, werden die Zylinderbohrungen gezielt präpariert. Ein Aufrauwerkzeug mit PKD (polykristalliner Diamant)-Schneideinsatz hat sich für diese Bearbeitung bewährt, da es am wirtschaftlichsten ist.
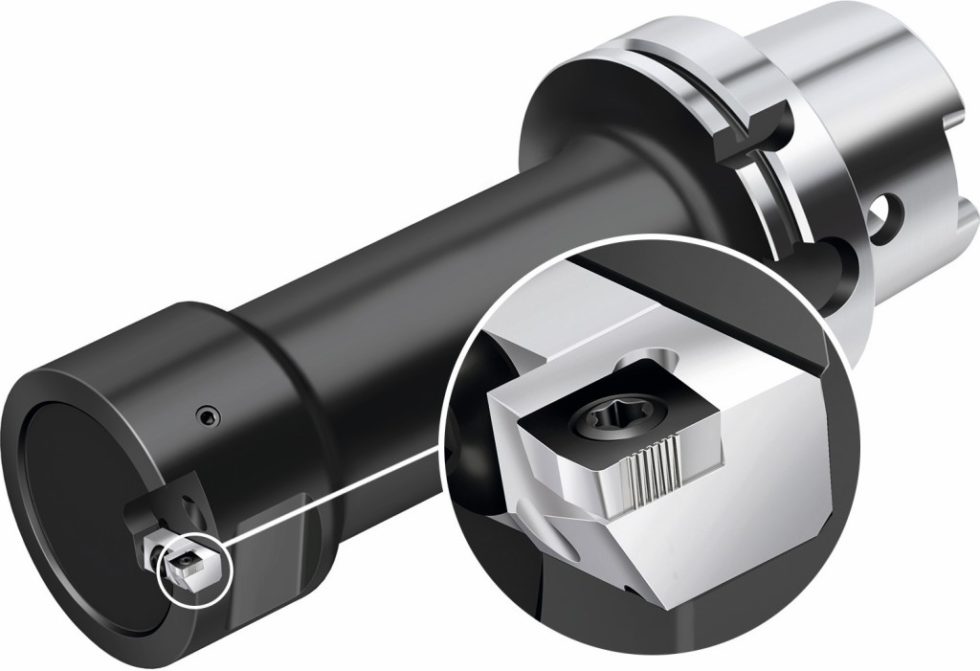
Ein neues Werkzeugkonzept „revolutioniert“ die Bearbeitung beschichteter Zylinderlaufbahnen in Leichtmetall-Motorblöcken. Bild: Walter
Lange Zeit war Grauguss (GG) das Material für Motorblöcke schlechthin. Bei Nutzfahrzeugen ist dies immer noch der Fall. Allerdings wird Aluminiumguss als Alternative immer beliebter, denn der Trend geht hin zum „Downsizing“ und zu leichten Bauweisen. In einem Leichtmetall-Motorblock, Bild 1, kommt Grauguss in der Regel nur noch in Form von Zylinderlaufbuchsen zum Einsatz. In der nächsten Motorengeneration wird diese Kombination durch Beschichtungen ersetzt.
Vorteile von Beschichtungen
Während bei GG-Buchsen mit Wanddicken von 3 mm bis 4 mm zu rechnen ist, sind Beschichtungen nur 0,3 mm bis 0,4 mm dick – das entspricht etwa dem Faktor 10. Beschichtete Kurbelgehäuse lassen sich daher kompakter und noch leichter bauen. Außerdem sind die Beschichtungen verschleißfester und verringern die Reibung zwischen Kolben und Zylinderwandung. In der Konsequenz reduzieren sich die Schadstoffemissionen einmal mehr. Ein Pkw auf dem derzeit höchsten Öko-Standard hat demzufolge einen Motorblock mit beschichteten Zylinderlaufbahnen.
Die gängigen Beschichtungstechnologien sind das Atmosphärische Plasmaspritzen (APS), das Lichtbogen-Drahtspritzen (LDS) und das Plasma-Transferred-Wire-Arc-Verfahren (PTWA). Auf glatter Oberfläche funktionieren diese Verfahren nur unzureichend, die Beschichtungen würden den Belastungen nicht Stand halten. Damit die aufgespritzte Metallschicht eine sichere Verbindung mit dem Grundwerkstoff eingeht, ist bei allen drei Verfahren eine aufgeraute Oberfläche als Basis notwendig
Leicht integrierbar
Lange Zeit verwendeten die Automobilhersteller Strahlverfahren mit Wasser oder Korund, um die Oberflächen entsprechend zu aktivieren. Diese Technologien werden zwar immer noch eingesetzt, doch inzwischen gibt es eine Alternative, die wirtschaftlicher ist und die auch vom Werkzeugspezialisten Walter bevorzugt wird: die mechanische Vorbearbeitung mit einem speziellen Aufrauwerkzeug, Bild 2.
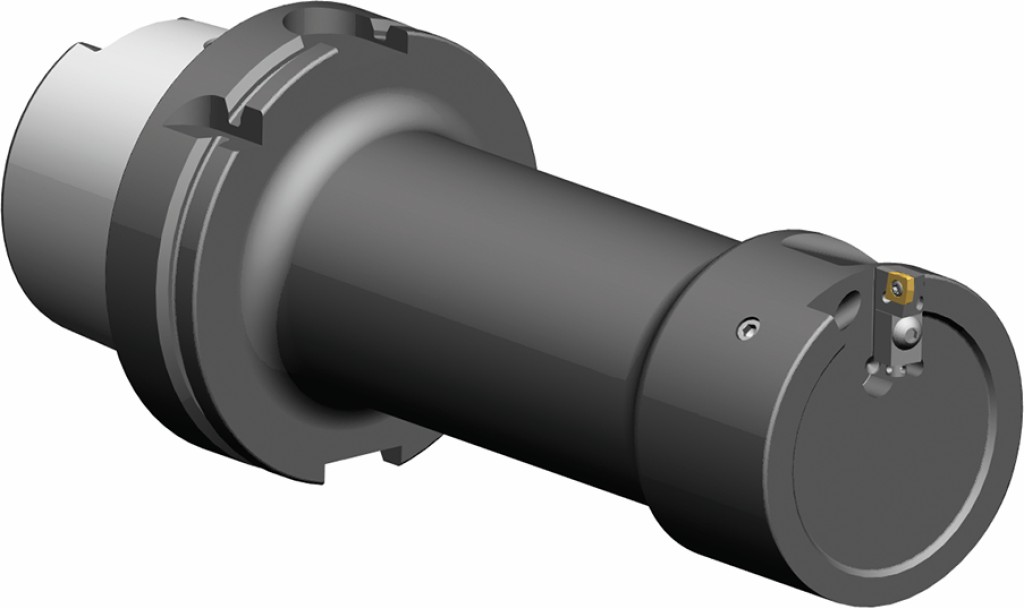
Bild 2. Für die Zylindervorbearbeitung wird ein Aufbohrwerkzeug mit einem Schneideinsatz verwendet. Der Einstellaufwand verringert sich damit ganz erheblich. Bild: Walter
Dieser Zerspanungsprozess ähnelt dem Aufbohren beziehungsweise dem Gewindeschneiden. Vorteil: Das Kurbelgehäuse braucht nicht in eine spezielle Anlage transportiert zu werden; es kann auf dem Bearbeitungszentrum, auf dem ohnehin schon gebohrt und gefräst wird, bleiben. Das Aufrauen der Zylinderbohrung wird damit zu einem integrierten Prozess in der vorhandenen Fertigungsstraße.
Während Strahlverfahren ein völlig willkürliches Relief erzeugen, schneidet das Aufrauwerkzeug eine genau definierte Profilrille – ähnlich einem Gewindegang – in die Zylinderbohrung, Bild 3.
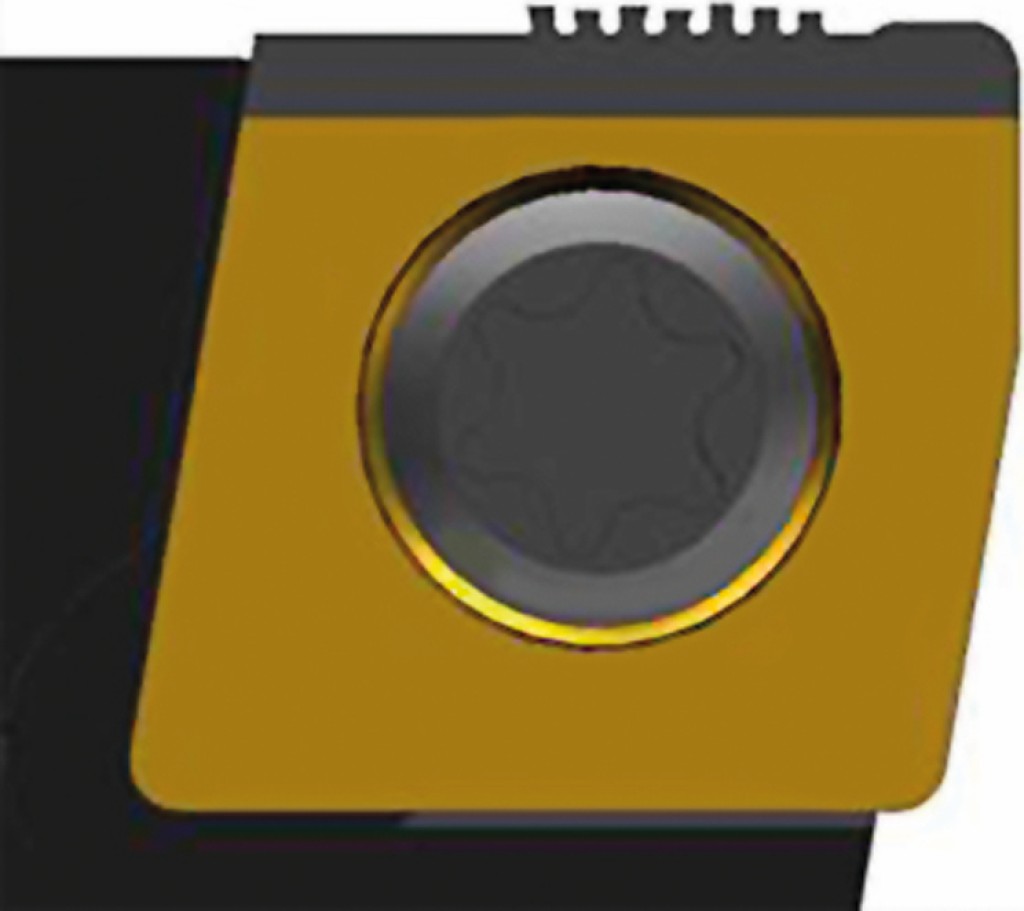
Bild 3. Der Schneideinsatz für das Aufrauwerkzeug verfügt über filigrane PKD-Zähne, die ein Profil mit Hinterschnitten erzeugen (links). Nach der Bearbeitung ist die Zylinderbohrung mit einem Schwalbenschwanzprofil überzogen – eine ideale Basis, um die Oberfläche zu beschichten (rechts). Bild: Walter
Das Profil der Rille ist schwalbenschwanzartig, um einen Formschluss zwischen Beschichtung und Grundmetall zu gewährleisten. Neben dem wirtschaftlichen bedeutet das auch einen technologischen Vorteil. Die übliche Rillenbreite und -tiefe beträgt weniger als 0,2 mm, die Steigung und damit der Vorschub des Werkzeugs bewegt sich zwischen 0,25 mm bis 0,35 mm.
Einfaches Handling
Aufgrund der geringen Abmessungen der feinen Profile müssen Aufrauwerkzeuge sehr präzise arbeiten. Sie lassen sich entweder als Ein- oder als Mehrschneider konzipieren. Bei Walter wird ein einschneidiges Konzept bevorzugt – eine stabile Bohrstange mit einem Schneideinsatz. Dabei besteht der Schneideinsatz aus einer Hartmetallbasis mit aufgelötetem PKD-Plättchen. Der Vorteil: der Aufwand für die Justierung des Werkzeugs beschränkt sich auf den Durchmesser. Bei Lösungen mit mehreren Schneideinsätzen sind diese nicht nur radial, sondern auch axial exakt aufeinander einzustellen. Geht der Einrichter nicht mit höchster Sorgfalt vor, besteht die Gefahr, das Rillenprofil zu verschneiden. Unter Umständen fehlen die Hinterschnitte, wodurch die Haftung der Beschichtung nicht mehr zu garantieren wäre. Aus diesem Grund bietet das einschneidige Konzept auch die höhere Prozesssicherheit.
Die PKD-Schneidplatte selbst verfügt über eine Reihe filigraner Zähnchen mit unterschiedlicher Tiefe und Schräglage (Bild 3) – dadurch können die Anwender das Profil in Stufen schneiden. Die Toleranzen im µm-Bereich machen die Fertigung der PKD-Platten anspruchsvoll. Walter hat dafür alle Techniken und das Know-how im eigenen Hause. Eine Kerntechnologie ist das Drahterodieren. Hierbei kommt es auf absolut korrekte Prozessparameter an, denn der Draht ist extrem dünn und unterliegt Abdrängeffekten. Diese auszugleichen, erfordert Erfahrung. Hinzu kommt, dass die unterschiedlichen Beschichtungsverfahren auch unterschiedliche Profile verlangen. Walter kann sämtliche Varianten realisieren und auf spezielle Kundenanforderungen schnell reagieren.
Vereinfachte Qualitätssicherung
Ein wichtiger Prozess ist abschließend die Qualitätskontrolle per Messmikroskop. Das empfindliche Gerät vergleicht dabei die Ist- mit einer Sollkontur. In der Kurbelgehäusefertigung beschränkt sich die Qualitätskontrolle auf eine Überprüfung des PKD-Schneideinsatzes – auch das ist ein großer Vorteil. Sind nach der Bearbeitung der letzten Zylinderbohrung alle Zähne vorhanden, muss auch die profilierte Oberfläche „in Ordnung sein“. Überprüfen lässt sich dies beispielsweise mithilfe einer Kamera. Kameras sind ebenfalls leicht in einen Gesamtprozess integrierbar und die Bilder vollautomatisch auswertbar.
Grundsätzlich lässt sich mit diesem Konzept die Wirtschaftlichkeit im Vorfeld der Beschichtung um einiges steigern. Doch nach dem Beschichten ist vor dem Fertigbearbeiten. Die Werkzeugentwickler richten ihre Blicke inzwischen auch auf diese Arbeitsschritte – das heißt auf die Beschichtungswerkstoffe. Für deren Endbearbeitung sind über kurz oder lang weitere Werkzeuglösungen verfügbar, die – noch produktiver als bislang – eine optimale Grundlage für das abschließende Fertighonen beschichteter Zylinderbohrungen schaffen.
www.walter-tools.com
Dipl.-Ing. (FH) Burkhard Krauß ist Component Manager bei der Walter AG in Tübingen und verantwortlich für Strategie, Weiter- und Neuentwicklung von Bearbeitungslösungen für Kurbelgehäuse.