Wie lässt sich das Produktionsausfallrisiko von verketteten Maschinen verringern?
Maschinen und Anlagen mit komplexen verketteten Maschinen sollten besonders gut gegen Ausfälle geschützt werden, denn diese sind besonders teuer. Gezeigt wird, wie sich Produktionsunterbrechungen mit proaktiver Instandsetzung vermeiden lassen.
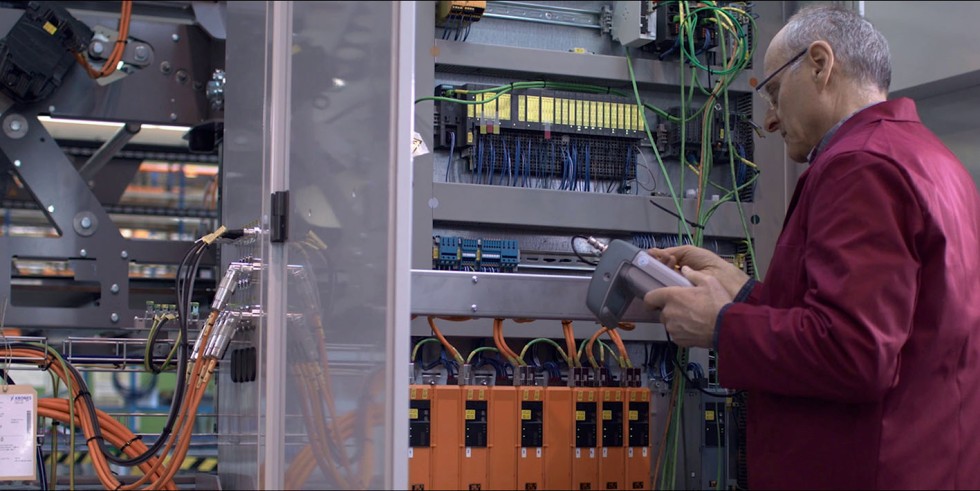
Prüfer bei der Arbeit: Häufig wird die EMV (Elektromagnetische Verträglichkeit) in einem späteren Entwicklungsstadium einer Maschine oder sogar erst in der Produktionsphase geprüft, was zu höheren Kosten und Verzögerungen führen kann.
Foto: J. Schmitz GmbH
Durch die Verkettung mehrerer Betriebsmittel zu Fertigungsstraßen sind die Folgekosten im Falle eines Produktionsstillstands besonders hoch. Im Störfall nur einer integrierten Maschine belaufen sie sich auf 1.000 Euro und bis zu 20.000 Euro – z.B. in der Chipfabrikation oder in der Automobilproduktion. Schon bei einer Anzahl von Störfällen pro Jahr im unteren einstelligen Bereich mit Stillstandszeiten von zwei bis drei Stunden pro Reparatur summieren sich die Kosten auf über 300.000 Euro pro Jahr.
Aufgrund der höheren Komplexität durch die große Anzahl eingebauter Komponenten steigt die Anzahl von Beeinflussungspfaden in Hightech-Betriebsmitteln auf 10³. Und durch die gesteigerte Frequenz von Zyklen – sowohl in der Antriebstechnik als auch der Datenverarbeitung – nimmt die Wahrscheinlichkeit eines Störfalls zu. Grund ist das Zusammentreffen von zyklischen Störamplituden durch Leistungsspitzen mit störempfindlichen Abschnitten in der Datenverarbeitung.
Elektromagnetische Verträglichkeit der Betriebsmittel im Blick
Rein algorithmisch gesehen, erhöht sich somit die Störwahrscheinlichkeit auf die Größenordnung 10³ gegenüber Einzelgeräten in einem Stand-alone-Betrieb. Abhilfe schafft hier eine umfassende elektromagnetische Verträglichkeit der Betriebsmittel. Sie ermöglicht die Minimierung der Lebenszyklus- und Stillstandskosten durch eine verfügbarkeitsorientierte Konstruktion.
Hersteller sind bei der Entwicklung von elektronischen Systemen häufig gezwungen, andere Faktoren als die elektromagnetische Verträglichkeit (EMV) in den Fokus zu stellen. So müssen die Komponenten wirtschaftlich herstellbar sein, eine hohe Leistungsfähigkeit aufweisen und den Anforderungen der Anwendung entsprechen. Zudem wird die EMV oft erst in einem späteren Entwicklungsstadium oder sogar in der Produktionsphase geprüft, was zu höheren Kosten und Verzögerungen führen kann, falls Nachbesserungen notwendig werden.
Ein qualitätsorientiertes Verfahren für die konstruktive EMV und eine Prüfung der internen EMV vor dem Inverkehrbringen der Komponenten und Maschinen sind ein „nötiges Übel“. Doch sie bieten auch viel Potential, um die gesamte Effizienz eines Betriebsmittels besonders in der Nutzungsphase langfristig zu steigern. Abhilfe schafft hier eine Software wie „ESMA“. Mit ihr ist ein softwaregestützter „QM-Prozess EMV“ möglich, die den Hersteller wie Anwender mithilfe eines Assistenzsystems an verschiedenen Stellen im Planungs- und Produktionszyklus wichtige Parameter erfassen und analysieren lässt. Auf diese Weise werden Produzenten von Betriebsmitteln durch Risikoanalyse und skalierbaren Einsatz von konstruktiven Maßnahmen bereits in der Designphase bei Konstruktion und Kostenplanung unterstützt.
Steigerung der Produktionseffizienz durch Intra-EMV-Typprüfung
Die Verfahrensschritte der Konstruktion werden Schritt für Schritt abgefragt. Dabei sind projektspezifische Maßnahmen zu definieren. Auf der Basis dieser Vorarbeit werden aus der Datenbank Risikoprioritäts-Minderungs-Faktoren aktiviert und hierarchisch algorithmisch bewertet. Für jeden Verfahrensschritt sind für je sechs Beeinflussungsmöglichkeiten im System die Minderungsfaktoren differenziert gespeichert. Dabei wird die jeweilige Wirkungskette betrachtet, z.B. Gerät (G) zu Gerät, Gerät (G) zu Leitung (L) oder Fernfeld (F) auf Gerät. Die über 400 Verfahrensschritte – multipliziert mit je sechs Beeinflussungspfaden und je drei Wirkungsfaktoren der Auftretenswahrscheinlichkeit, Fehlererkennung und Schadensfolge nach FMEA – ergeben über 7.000 Faktoren in der Datenbank. Dies zeigt die Exaktheit der aus Multiplikation der projektbezogenen Faktoren errechneten Risikopriorität.
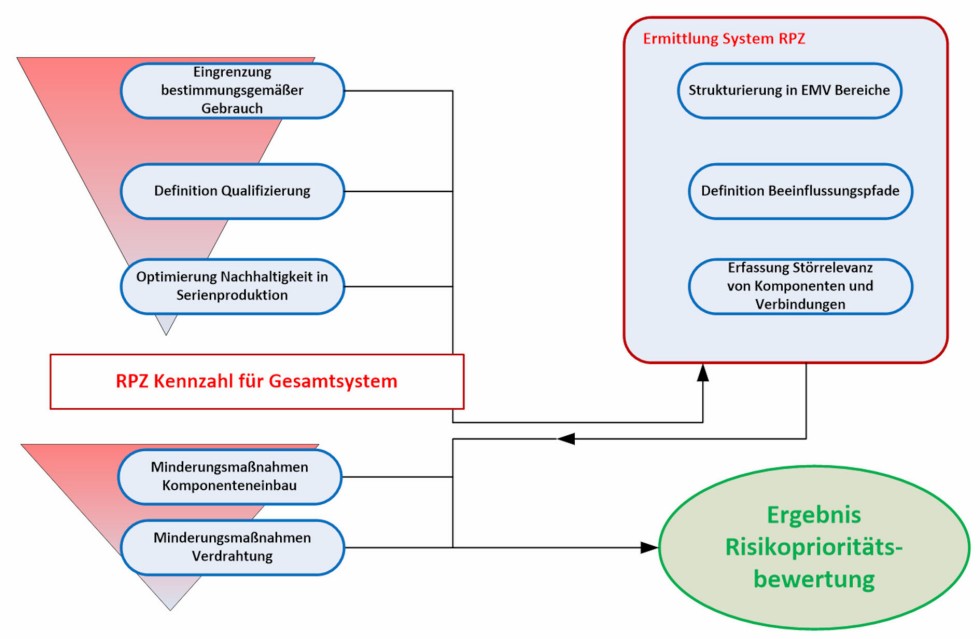
Die Verfahrensschritte der Konstruktion werden durch die Software „ESMA“ Schritt für Schritt abgefragt. Dabei sind projektspezifische Maßnahmen zu definieren. Das Ergebnis ist eine Risikoprioritäts-Bewertung auf der Grundlage verlässlicher Daten. Grafik: J. Schmitz GmbH
Relevante Messwerte lassen sich zudem mit dem „LogAmp“-Messverfahren zur Validierung von elektromagnetischen Parametern im Nahbereich innerhalb von Betriebsmitteln erfassen. Der Vorteil des Messgeräts besteht in der Möglichkeit der problemlosen und kostengünstigen Anwendung durch Instandsetzungspersonal auch ohne spezielle EMV-Kompetenz. Es genügt bereits ein einfacher Vergleich der „Markerwerte“ bei Typprüfung, Wartung sowie Instandsetzung und mit Sollwerten aus der Datenbank in ESMA, angelehnt an die Norm EN 61000–4–39, mit definierten Störfestigkeits- Kategorien. Dies ermöglicht eine „Gut/Schlecht“-Analyse vor Ort.
Dabei wird der durch einen Logarithmier-Baustein im Gerät erfasste Amplituden-Verlauf und Äqivalentwert zum Energiegehalt der Amplitudendichte als sogenannter „Markerwert“ ausgegeben. Die Messung erfolgt in den drei relevanten Frequenzbereichen für den Nahbereich (10 kHz bis 150 kHz, 150 kHz bis 1 MHz, 1 MHz bis 10 MHz).
Vermeidung von Produktionsstopps mit minimalem Wartungsaufwand
Da ein Stillstand unbedingt vermieden werden muss, sollten Abweichungen von EM-Parametern bereits vor Eintritt einer Störung erkannt werden. EMV-Prüfungen in einem weiten zeitlichen Abstand durch externe Prüfer können dies nur bedingt leisten. Vielmehr sollte ein eigenes Wartungsintervall etabliert werden, das sich an den vorab definierten Ausfallwahrscheinlichkeiten der einzelnen EM-relevanten Anlagen und Komponenten orientiert. Dadurch können die Wartungsaufgaben beispielsweise mit geplanten Produktionspausen synchronisiert werden.
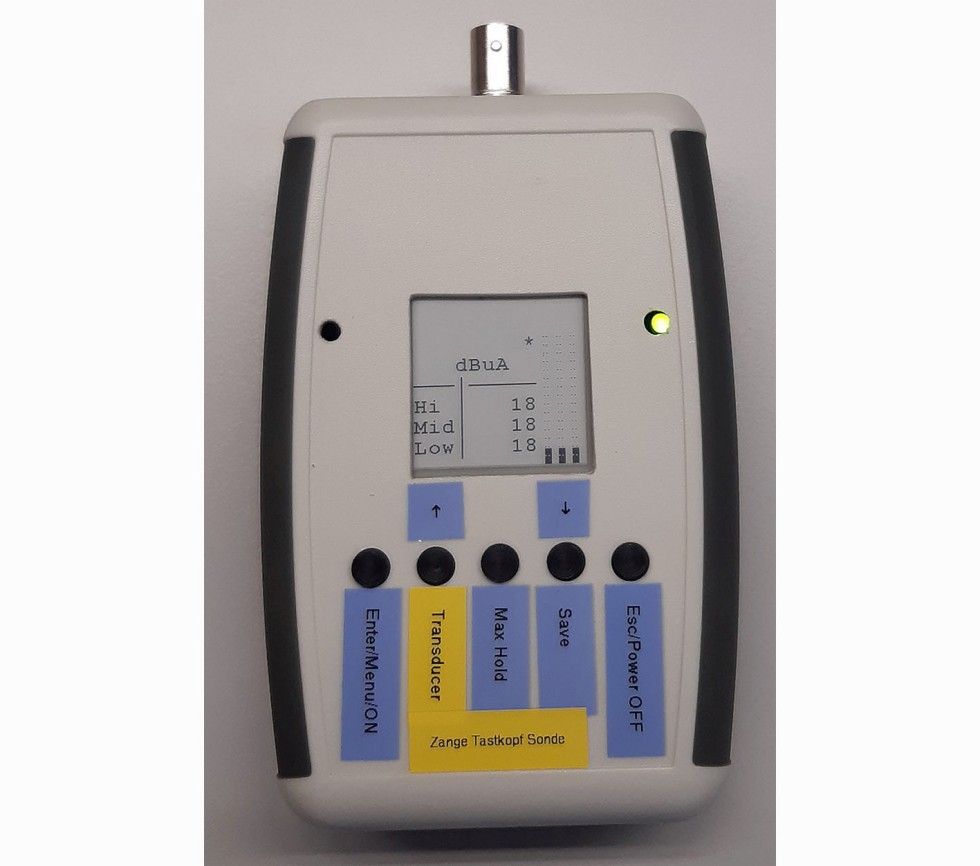
Regelmäßige Intra-EMV-Prüfungen mit mobilen Messgeräten sind Pflicht: Eine Veränderung nur eines EM-Parameters deutet bereits auf eine Degradation beziehungsweise Ermüdungserscheinungen von mechanischen oder elektrischen Baugruppen hin.
Foto: J. Schmitz GmbH
Unter Verwendung der Messwerte der „Intra EMV Typprüfung“ – als Soll-Vorgabe für die Nutzungsphase – ist es Anlagenbetreibern möglich, mithilfe eines digitalisierten Assistenzsystems sowie mobiler Messgeräte ein regelmäßiges, engmaschiges Condition Monitoring durchzuführen. Aufgrund der besseren, digitalisierten Datengrundlage lässt sich schließlich eine proaktive Instandsetzung ohne Produktionsunterbrechung durch unerwartete Störfälle gewährleisten. Eine Veränderung eines EM-Parameters wie magnetisches Nahfeld, Störstrom oder Störspannung sind bereits ein Indikator für Degradation bzw. Ermüdungserscheinungen von mechanischen oder elektrischen Baugruppen. Dies können Komponenten wie ESD-Ableitbürsten, Wellenlager, PE-Verbindungen, Leitungs-Schirmauflagen oder EMV-Verschraubungen sein. Werden die Abweichungen regelmäßig überprüft und rechtzeitig erkannt, lässt sich ein Ausfall besser vorhersagen und gleichzeitig die Ersatzteilbeschaffung effizienter gestalten.
Minimierung der „Life cycle costs“ von der Nutzungsphase bis zur Obsoleszenz
Die Störresilienz ist in der gesamten Nutzungsphase bis hin zur Obsoleszenz zu betrachten. Sie hängt von der Degradation der EM-Parameter der eingesetzten Komponenten ab. Dies wird beeinflusst durch die Einsatzbedingungen im Betrieb – wie Umgebungstemperatur, Luftfeuchte, Korrosivität und Netzqualität.
Das Auftreten einer Störung ist prospektiv nicht deterministisch vorhersehbar. Der Weg zur unterbrechungsfreien Produktion hingegen ist das Erkennen einer EM-Abweichung, was dann zu einer proaktiven Wartungsmaßnahme mit Vorgabe einer akzeptablen Terminierung führen kann. Ein digitales Assistenzsystem – bestehend aus der Software ESMA mit korreliertem Messsystem LogAmp – gibt dem Hersteller und später dem Nutzer die Möglichkeit, ein RCM (Reliability centered maintainance management) firmenintern einzuführen und in der Nutzungsphase ein vorhersagbares Wartungskonzept zu verfolgen. Dadurch werden eine risikoanalytische Bewertung von skalierbar einsetzbaren EM-Detail-Konstruktions-Maßnahmen und ein skalierbarer Wartungsaufwand im Hinblick auf die Instandhaltungskosten möglich. Ebenso gelingt die Sicherstellung der Langzeitnutzbarkeit der Anlage – dank der Reparierbarkeit nach einer Obsoleszenz von Original-Ersatzteilen. Dies ist möglich durch die Definition der EM-Einbaubedingungen bei Ersatz durch alternative Komponenten.
Das Wartungskonzept „Reliability centered EMC maintainance“
Durch die in der Konstruktionsphase bereits definierten EM-Sollwerte im Inneren des Betriebsmittels – und mit der Anwendung des Messverfahrens LogAmp und der begleitenden Risikobewertung durch die Software ESMA – können in der Nutzungsphase die Verfügbarkeit aufrechterhalten und eine Produktionsunterbrechung durch Störfälle vermieden werden. Ein Weg dazu ist der konsequente Einsatz eines Wartungskonzeptes mit Condition Monitoring mit kurzen Wartungsintervallen – während und sofort nach der Inbetriebsetzung. Durch die algorithmische Bewertung der Ergebnisse jeder Wartung wird das Intervall bis zur Folgewartung adaptiert. Greift man auf die digital hinterlegten Vorab-Analysen der Bauteile zurück und ergänzt sie durch ein engmaschiges Netz aus Prüfintervallen, lassen sich Stillstandzeiten reduzieren und die Wartung besser planen. Mithilfe eines solchen Wartungskonzepts, das sich nicht an Herstellerangaben, sondern an der Störresilienz und wahrscheinlichen Materialermüdung orientiert, wird der Wartungsaufwand skalierbar, wodurch langfristig Kosten gespart werden.
Wirkungsvolle Unterstützung durch Dienstleister
Durch die schnellen Innovationszyklen oder unterbrochenen Lieferketten in der heutigen Zeit sind Originalersatzkomponenten mit identischen EM-Parametern nicht immer beschaffbar – und eine exakte Störresilienz nach dem Austausch nicht vorhersehbar. Wenn die EM-Schnittstellen-Parameter von Komponenten und Baugruppen bereits bei Konstruktion oder der Inbetriebnahme im Assistenzsystem hinterlegt werden, kann bei algorithmisch aus Wartungsergebnissen berechneten akzeptablen Zeitspannen bis zur proaktiven Reparatur in Produktionspausen rechtzeitig Ersatz organisiert werden.
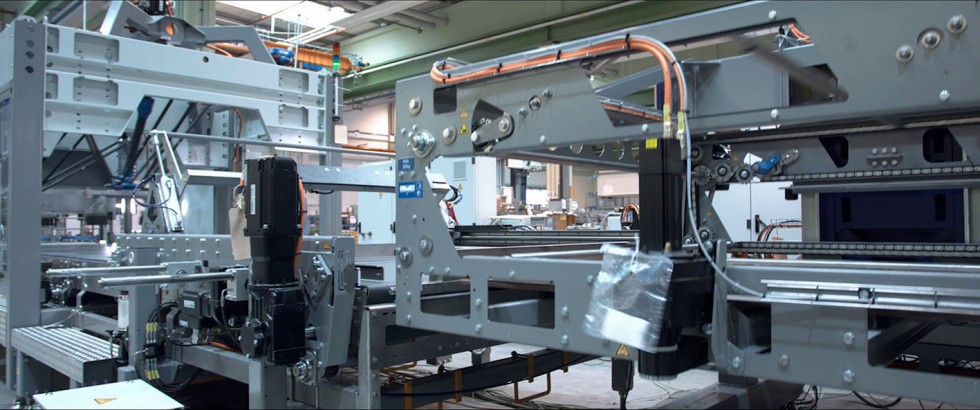
Prüfanordnung in der Werkhalle: Qualifizierte Dienstleister analysieren kleine Baugruppen in eigenen Prüfräumen, große Maschinen und -anlagen werden mit transportablem Equipment direkt beim Kunden geprüft.
Foto: J. Schmitz GmbH
Hilfestellung bietet die J. Schmitz GmbH, ein inhabergeführtes Kompetenzzentrum rund um die EMV. Das Dienstleistungsportfolio umfasst u.a. ein akkreditiertes Messlabor für den CE-Konformitätsnachweis sowie eine kompetente EMV-Beratung für Hersteller in Bezug auf die Qualifikation ihrer Produkte sowie die Begleitung von Neuentwicklungen. Ebenso führt das Prüflabor Qualifizierungen und Validierungen nach Stand der Technik durch. Die Prüfung kleiner Baugruppen erfolgt in den drei Prüfräumen in Rosenheim. Große Maschinen und -anlagen sowie Fahrzeuge werden mit transportablem Messequipment vor Ort beim Kunden geprüft.
Das könnte Sie auch interessieren:
Zukunftssicheres Maschinen-Upgrade mit KI und Edge Computing
Lebendiges Qualitätsmanagement für Maschinenbau-Unternehmen
Neue Maschinenverordnung: wichtige Änderungen für Hersteller und Betreiber
Josef Schmitz ist Gesellschafter der J. Schmitz GmbH in Rosenheim.