Taktzeiten einsparen: Multifunktionale Prüfkammer für große Baugruppen
Die Automatisierung sorgt auch in der Qualitätssicherung für höhere Prozesssicherheit und -genauigkeit. Ein modernes Labor geht neue Wege und testet ab sofort auch großvolumige Baugruppen für Automobile in einer neuen Multifunktions-Prüfkammer auf Korrosion.
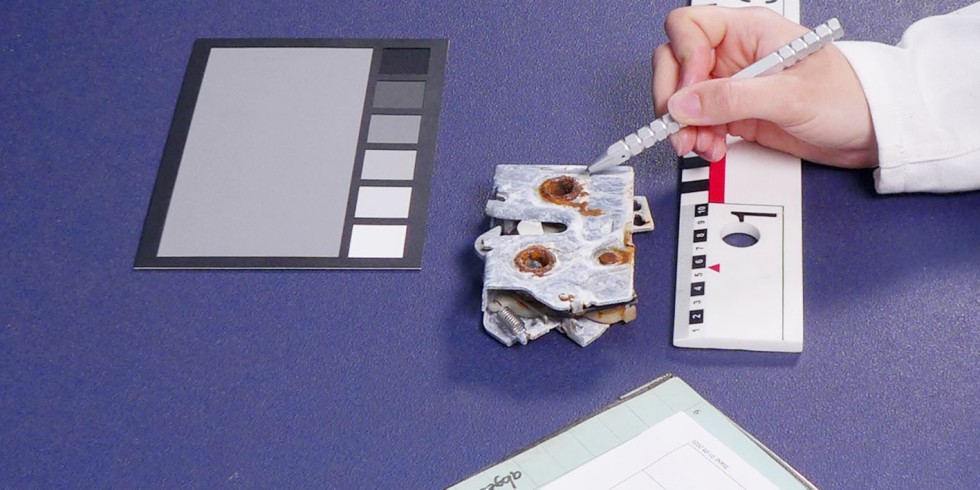
Korrodiertes Prüfteil: Durch die Simulation der einzelnen Phasen im Wechsel ist das Prüfobjekt einem Witterungswechsel ausgesetzt, der den realen Bedingungen im späteren Betrieb gleicht. So lässt sich ein mögliches Korrosionsverhalten vorhersagen.
Foto: Igos
Die in der Automobilindustrie eingesetzten Substrate Stahl, verzinkter Stahl und Aluminium müssen sich durch eine hohe Widerstandsfähigkeit auszeichnen, um korrosionsbedingte Ausfälle der Fahrzeugtechnik zu verhindern. Unabhängige Materialprüfungen sollen dies sicherstellen und in möglichst kurzer Zeit eine Bandbreite an Witterungseinflüssen simulieren. Jedoch variiert das Prüfergebnis der zahlreichen Prüflabore – trotz normierter Anforderungen – in Bezug auf Prüftiefe und Analyseservice erheblich.
Keine Umlagerung von Werkstücken mehr
Zudem werden die verschiedenen Korrosions- und Witterungsprüfungen oftmals im Wechsel nacheinander in unterschiedlichen Prüfkammern durchgeführt, sodass ein aufwendiges Umlagern der Bauteile notwendig ist. Derartige Unterbrechungen können jedoch die Prüfergebnisse negativ beeinflussen. Beim Institut für Galvano- und Oberflächentechnik Solingen (IGOS) ist dies ab sofort ausgeschlossen: Mit einer neuen Korrosionsprüfkammer lassen sich jetzt Korrosions- und Umweltsimulationen vollautomatisch ohne Umlagern der Prüfteile in derselben Kammer durchführen.

Das Prüfinstitut hat seine Ausstattung jüngst um eine neue Universalprüfkammer erweitert, die den kompletten Vorgang der Korrosionsprüfung auf einer Maschine erlaubt.
Foto: Igos
Die Anlage mit einer Kammergröße von zwei Kubikmetern sowie die flexible Steuerung ermöglichen eine noch konstantere Nachbildung natürlicher Korrosionsvorgänge. Das IGOS ist ein akkreditiertes Prüflabor, das offiziell von Mercedes-Benz für werkstofftechnische Erstbemusterungen nach WEB 2020+ zugelassen ist, und wird in der Liste V100 als freigegebenes Labor geführt.
Normen für sicherheitskritische Bauteile erfüllen
Korrosionsbedingte Bauteilausfälle können schlimmstenfalls die Betriebsbremsen oder andere sicherheitstechnische Funktionen im Fahrzeug lahmlegen. Daher sehen sich Hersteller immer wieder mit Rückrufaktionen aufgrund potentieller Mängel konfrontiert. Deshalb sind entsprechende Materialprüfungen während der Entwicklung und dem Fahrzeugbau von großer Bedeutung. „Der Prüfrahmen wird dabei durch eine Vielzahl an Normen und Regularien vorgegeben, die jedoch Veränderungen unterliegen. Wie die Bauteile selbst, erfahren auch sie eine Entwicklung, der sich die Prüflabore rechtzeitig stellen müssen“, erklärt Dipl.-Ing. Josef Andrek, Geschäftsführer des Instituts für Galvano- und Oberflächentechnik Solingen GmbH & Co. KG (IGOS).
So wurde beispielsweise vor einigen Jahren der VDA-Korrosionswechseltest VDA 233–102 obligatorisch, der die Beurteilung von Bauteilen durch ein zeitraffendes Testverfahren vorgibt. Dabei werden Salzsprühnebelphasen mit anderen klimatischen Bedingungen zyklisch kombiniert. In vielen Laboren wird diese Testreihe in unterschiedlichen Kammern durchgeführt, was ein manuelles Neupositionieren der Bauteile erforderlich macht. Auch beim IGOS mussten die Komponenten bisher dreimal pro Woche für drei Stunden zwischen Klimaschrank und einer Salzsprühnebelkammer umgelagert werden. Solche manuellen Eingriffe in die Prüfphase und die unweigerliche Veränderung der Prüflage können unter Umständen zu einer Verfälschung der Ergebnisse führen.
Um dies zu vermeiden, hat das IGOS seine Prüfausstattung jüngst um eine neue Kombinationsprüfkammer – speziell für diesen VDA-Test – erweitert, die den kompletten Vorgang der Korrosionsprüfung in einer Maschine ermöglicht. Gleichzeitig sind nun mehr Kapazitäten in den anderen Kammern frei, die sonst für einen Prüfvorgang belegt gewesen wären. Die automatisierte Anlage ermöglicht die Erstellung reproduzierbarer Korrosionsbilder. Diese visualisieren die Schwachpunkte in Beschichtungen oder die entsprechende Angreifbarkeit des Materials, ohne das Prüfobjekt während der Testzyklen neu ausrichten zu müssen.
Salzsprüh-, Feuchte-, Temperatur-und Gefrierphasen in einer Kammer
Mit dieser neuen Prüfkammer ist eine Kombination verschiedener Einflussfaktoren – wie Salzsprüh-, Feuchtigkeits-, Temperatur- und Gefrierphasen – möglich. Das Gerät wird komplett automatisch betrieben. Durch die Simulation der einzelnen Zyklen im Wechsel ist das Prüfobjekt einem Witterungswechsel ausgesetzt, der den realen Bedingungen im späteren Betrieb gerecht wird, was das spätere Korrosionsverhalten präziser darstellen lässt. Die Qualität der Beschichtung kann nach diesem Test durch ergänzende Auswertungen an künstlichen Verletzungen wie Ritz-, Gitterschnitt-, Kratz- oder Steinschlagprüfungen effizienter und genauer beurteilt werden. Zu Beginn muss das Bauteil nun lediglich einmal positioniert und das gewünschte Prüfprogramm ausgewählt werden. Ist die Kammertür geschlossen, führt die Anlage alle Zyklen eigenständig durch.

Die Versorgung mit Prozesswasser und Sole ist durch ein Rohrsystem mit verschiedenen Druckluftanschlüssen sichergestellt.
Foto: Igos
„Manuelle Eingriffe, die eine Verfälschung der Ergebnisse hervorrufen könnten, sind nicht mehr notwendig, so dass wir eine wesentlich höhere Prozesssicherheit und Analysegenauigkeit gewährleisten können“, so Andrek. Die entsprechende Versorgung mit Prozesswasser und Temperatur übernehmen hochwertige Heiz- und Kühlkreise, die wiederum mit einem Solebehälter und verschiedenen Druckluftanschlüssen verbunden sind. Dank eines installierten Klimamoduls sind Prüfungen im Temperaturspektrum von –15 °C bis +60 °C möglich. „Diese Funktionserweiterung ist vor allem für Korrosionswechseltests nach VDA 233–102 erforderlich, da hierbei eine Kältephase bei –15 °C durchlaufen wird“, ergänzt Andrek.
Protokolle automatisiert erstellen
Der Innenraum der Kammer ist mit einem speziellen witterungsbeständigen Kunststoff ausgelegt und verfügt über ein besonders großes Volumen (B x H x T = 2 x 1 x 1 Meter), sodass Prüfobjekte unterschiedlicher Größe und selbst komplette Baugruppen den Tests unterzogen werden können. Auch bei der Steuerung wurde Wert auf Flexibilität gelegt: Im Schaltschrank, der über ein praktisches Touchpanel bedienbar ist, sind verschiedene Prüfprogramme hinterlegt.
Die Kammer besitzt einen integrierten Rechner auf dem ein Programm für die Bedienung der Prüfkammern aufgespielt wurde. Über dieses Programm lassen sich neue Prüfungen programmieren oder bestehende abändern. Zudem können neue vom Hersteller vorprogrammierte Prüfungen aus dem Speicher heruntergeladen werden.
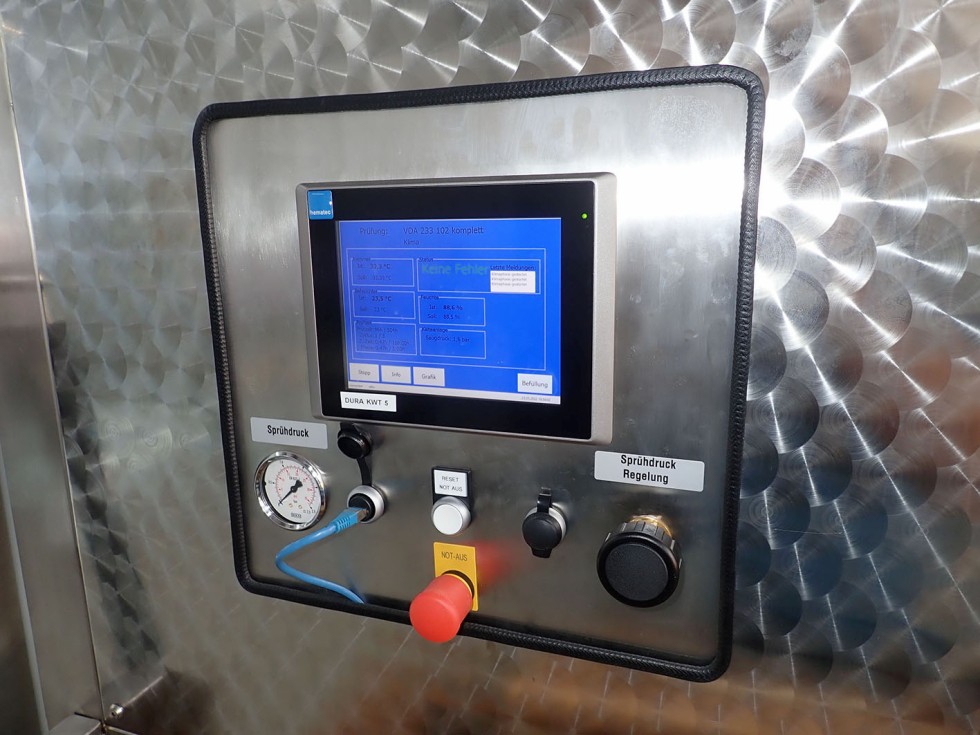
Im Schaltschrank, der über ein praktisches Touchpanel bedienbar ist, sind verschiedene Prüfprogramme hinterlegt.
Foto: Igos
Während einer Prüfung werden alle Werte automatisch aufgezeichnet und abgespeichert, so dass sie später leicht in ein entsprechendes Analyseprotokoll übertragen und archiviert werden können. Ein praktisches Prüfprotokoll gewährleistet die Rückverfolgbarkeit jedes einzelnen Prüfzyklus.
Offiziell zugelassenes Prüflabor für Baumusterfreigaben
Die neue Prüfkammer ist die jüngste Ergänzung zum umfassenden Gerätepool, den das Institut bei seiner täglichen Arbeit nutzt. Dank der Multifunktionskammer ist anderes Equipment weniger häufig für Korrosionsprüfungen gebunden und kann zeitgleich für andere Korrosionssimulationen genutzt werden. Neben den Korrosionsprüfungen werden am IGOS ergänzende chemische Material- und Schichtanalysen sowie diverse Prüfarten im Rahmen der Galvano- und Lackiertechnik durchgeführt. Auch deshalb ist das IGOS eines von den wenigen akkreditierten Laboren, die von Mercedes-Benz als offizielles Prüflabor für Baumusterfreigaben gemäß werkstofftechnischer Erstbemusterungsrichtlinien (WEB 2020+) zugelassen ist und in der Liste für Laboratorien V100 bei Mercedes-Benz geführt wird. „Mit der neuen Prüfkammer sehen wir uns nun noch besser gewappnet für die verschiedenen Herausforderungen und Prüfszenarien, die uns im Fahrzeugbau sowie anderen Bereichen begegnen“, resümiert Andrek.
Das Institut für Galvano- und Oberflächentechnik Solingen GmbH & Co. KG (www.igos.de) wurde 1993 als unabhängiges Institut gegründet und ist seit Ende 2006 akkreditiert nach DIN EN ISO 17025. Das Unternehmen verfügt über umfassende Kenntnisse in den Bereichen Galvano- und Beschichtungstechnik, Materialwissenschaft, Chemie sowie Korrosionsschutz, die sich in den zahlreichen Prüftechniken im Unternehmensportfolio widerspiegeln. Darüber hinaus bietet das Institut unabhängige Prüfberichterstattung für verschiedene Branchen sowie die Erstellung von Gutachten und Sachverständigenberichte für Gerichte und Versicherungen.
Das könnte Sie auch interessieren:
Faserverbundstoffe bei Tiefsttemperaturen prüfen
Felix Herbstritt arbeitet für den ABOPR Pressedienst in München.