Automobilindustrie profitiert von fertigungsnaher Messung
Eine neue smarte Test-Lösung erledigt die Qualitätsprüfung direkt vor Ort am Objekt – und das schnell und zuverlässig. Davon profitieren nun auch die E-Mobilität sowie der Erbauer einer Sportwagen-Ikone.
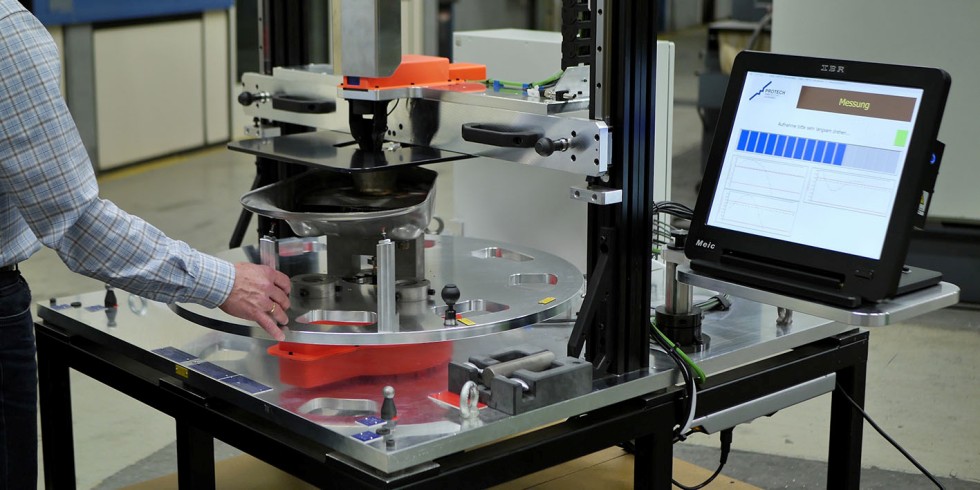
Statt mit einer Maschine im Messraum lassen sich Bauteile jetzt rasch vor Ort mit der neuen "Smart Testing Solution" prüfen. Die "messende Lehre" erledigt dies über die gesamte Laufzeit einer Komponente.
Foto: Wolpert
Ein Dienstleister für Lehrenbau und Qualitätssicherungsaufgaben hat eine „Smart Testing Solution“ (STS) entwickelt, mit der Bauteile „vor Ort“ direkt in der Fertigung vermessen und geprüft werden können. Die „messende Lehre“ ist die digitale Alternative zu einer Messmaschine in einem Messraum oder zur händischen Messung mit Messuhren in der Fertigung. Ergebnisse der 100-Prozent-Prüfungen stehen unmittelbar und vor Ort zur Verfügung. Nachbearbeitungen und Ausschuss entfallen. Davon profitieren auch verschiedene Bereiche der Automobilindustrie, vor allem der Bereich Karosseriebau.
Wie funktioniert die Messung?
„Zusammenbringen was zusammenpasst“ – so lautet das Motto der Firma Protech Lehrenbau aus Bad Friedrichshall. Und was zusammenpassen soll, muss vorher geprüft werden. Dafür konstruiert und fertigt der Betrieb alle Arten von Vorrichtungen. Das reicht vom Fügemeisterbock über Messaufnahmen bis zur hochmodernen messenden Prüflehre. Die werden heute bereits im Prototypen- und Konzeptteilbau eingesetzt, um Rückverfolgbarkeit zu gewährleisten. Das weiß auch eine süddeutsche Sportwagenschmiede zu schätzen.

Für einen Prüfauftrag der besonderen Art hat der Spezialist eine messende Lehre für das Targa-Dach des Porsche 911 entwickelt und gebaut.
Foto: Wolpert
„Qualitätsanforderungen und Kostendruck erlauben heute weder Ausschuss noch aufwendige Messverfahren. Unser STS-System spart nicht nur Zeit und Kosten, es entlastet auch den Messraum und reduziert Messfehler“, betont Bernd Schluchter, Geschäftsführer der Protech GmbH. Das Tochterunternehmen der Wolpert Gruppe hat ein digitales Messverfahren entwickelt, das in der Produktion vor allem Karosserieteile zu einhundert Prozent messen kann.
Die Smart Testing Solution fungiert wie eine „messende Lehre“. Sie vermisst definierte Punkte und Merkmale über die gesamte Laufzeit einer Komponente. Unabhängig vom Material des Bauteils – Stahl oder Aluminium, Kunststoff (1-Komponenten- oder 2-Komponenten-Material) sowie Glas – stellt es Messergebnisse sofort vor Ort in der Fertigung zur Verfügung. Bei Toleranz-Änderungen des Bauteils lassen sich die Werte bequem über die Software einstellen.
Messende Lehren für passgenaue Bauteile innerhalb der Toleranz
Auf Wunsch können mobile und flexible Messeinrichtungen bis zu einer Größe von 4000 x 1600 x 2100 Millimetern (X,Y,Z) gebaut werden. Erfasst werden die Messwerte entweder taktil (mit Messtastern, die mit Prüfgeräten der Marke Tesa kompatibel sind) oder berührungslos über gängige Mess- oder Kamerasensoren. Die Messsensoren erfassen dabei auch labile und kritische Bereiche. Mit den Kamerasensoren lassen sich zum Beispiel Löcher – sowohl auf ihre Position als auch auf ihre bloße Existenz – überprüfen. Die Messvorgänge können dabei sowohl teil- als auch vollautomatisiert durchgeführt werden.
Gemessen werden die Werte (von 1 bis X) entweder auf Knopfdruck oder Touch, alle auf einmal oder nacheinander. Die Messergebnisse lassen sich über verschiedene Formate ausgeben. Neben der grafischen Darstellung der Werte und einem Bild des Bauteils lassen sich auch Ampeldarstellungen ausgeben. Die ermittelten Daten werden statistisch erfasst und können bei Bedarf sofort ausgewertet werden.

Unabhängig vom Material des Bauteils stehen die Messergebnisse sofort in der Fertigung zur Verfügung. Bei Toleranz-Änderungen lassen sich die Werte bequem über die Software anpassen.
Foto: Wolpert
Gesammelte Werte lassen sich in den in der Automobilbranche gängigen Datenformaten exportieren und übergeben. Vor dem Vermessen wird die messende Lehre über verschiedene Referenzen kalibriert. Dabei sind auch Temperaturanpassungen durch entsprechend vermessende Referenzteile möglich.
Beispiel: Komplexes Glasdach für eine Sportwagenikone
Mit der beschriebenen Vorgehensweise spart die STS neben Zeit und Kosten vor allem die ewige Rennerei zwischen Produktion und Messraum. Bei sehr komplexen Bauteilen ist es darüber hinaus hilfreich, dass die Messergebnisse sofort in der Produktion bereitstehen. Für einen Prüfauftrag „der ganz besonderen Art“ hat Protech eine messende Lehre für das Targa-Dach des „Porsche 911“ entwickelt und gebaut. Bei dieser Prüfung ermitteln insgesamt 60 integrierte Messtaster in einer 100-Prozent-Einzelprüfung die Glasgeometrie vor dem Zusammenbau mit dem Rahmen. Dank des modernen Lehrenbaus freuen sich inzwischen Sportwagenfahrer in aller Welt über ein perfekt funktionierendes, elektrisches Targa-Dach.
Lieferant für deutsche OEMs und 1st-tier-Zulieferer
Die Wolpert-Gruppe besteht aus acht eigenständigen Unternehmen und stellt Prototypenwerkzeuge und Serienwerkzeuge sowie Prüfmittel und Serienteile her. Keimzelle des Firmenverbundes ist die Wolpert Modell- und Formenbau GmbH in Bretzfeld. 1991 gegründet, ist das Unternehmen durch technologische Entwicklungen und Firmenzukäufe stetig gewachsen. Mit der 3-Komponenten-Veredelungstechnologie und der Hybrid-Technologie für das Umspritzen von Stahlteilen mit Kunststoff bieten die Spezialisten einzigartige Verfahren an. Nicht zuletzt durch Termintreue, Präzision und Preiswürdigkeit genießt der Technologieführer das Vertrauen vieler deutscher OEM (Original Equipment Manufacturer) und 1st-tier-Zulieferer. Zuletzt wurden mit rund 300 Mitarbeitern 40 Millionen Euro Umsatz erzielt.
Das könnte Sie auch interessieren:
Faserverbundstoffe bei Tiefsttemperaturen prüfen