Zuverlässiges Messen in Drehbearbeitungszentren
Werkstücke für die Automobilindustrie automatisiert in Drehzentren zu messen, ist anspruchsvoll. Schließlich sind die eingesetzten Messsysteme ständig Späneflug, Kühlschmiermittel und Vibrationen ausgesetzt, denen sie trotzen müssen, ohne dass Ergebnisse verfälscht werden.
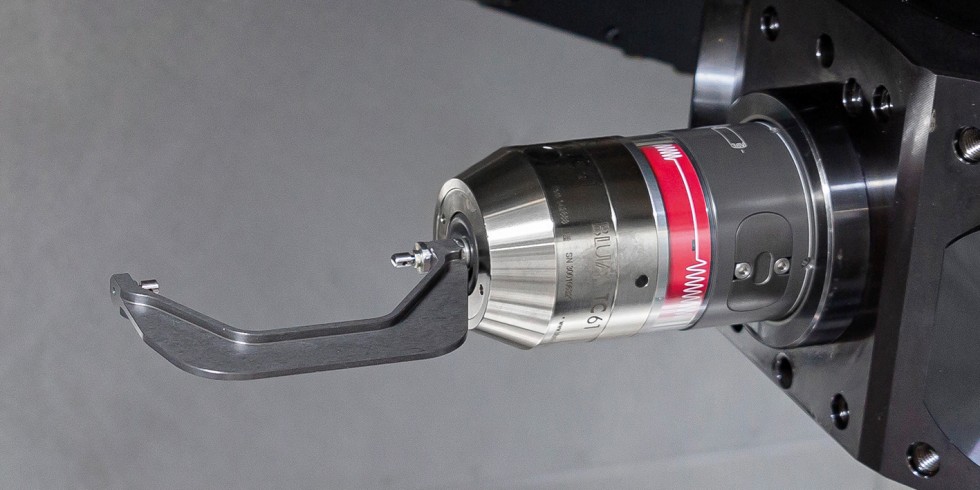
Das weltweit einzigartige bidirektionale Messwerk macht es möglich, den Messtaster mit relativ schweren Tasteinsätzen, in diesem Fall einem Messbügel, auszustatten.
Foto: Blum
Man merkt schnell: in solch „feindlicher“ Umgebung präzise Ergebnisse zu erhalten, ist eine Aufgabe für Spezialisten. Und so nutzt der Drehmaschinenhersteller Schuster aus Denklingen die langjährige Expertise eines bewährten Anbieters für das Messen im Bearbeitungsraum.
Das Ziel: Bearbeitung rund um die Uhr
Die Schuster Maschinenbau GmbH wurde vor über 40 Jahren in Denklingen, südlich von Landsberg am Lech, gegründet. Das erste Produkt waren Maschinen für die Herstellung von Gesteins- und Hammerbohrern. Über die Jahre hinweg wurden verschiedene Drehmaschinen entwickelt, beispielsweise 2003 die flexible Drehzelle F40. Gemeinsam ist allen Maschinen die Optimierung im Hinblick auf die Großserienfertigung: Die Maschinen sind dafür gebaut, rund um die Uhr in höchster Taktzahl zu produzieren.
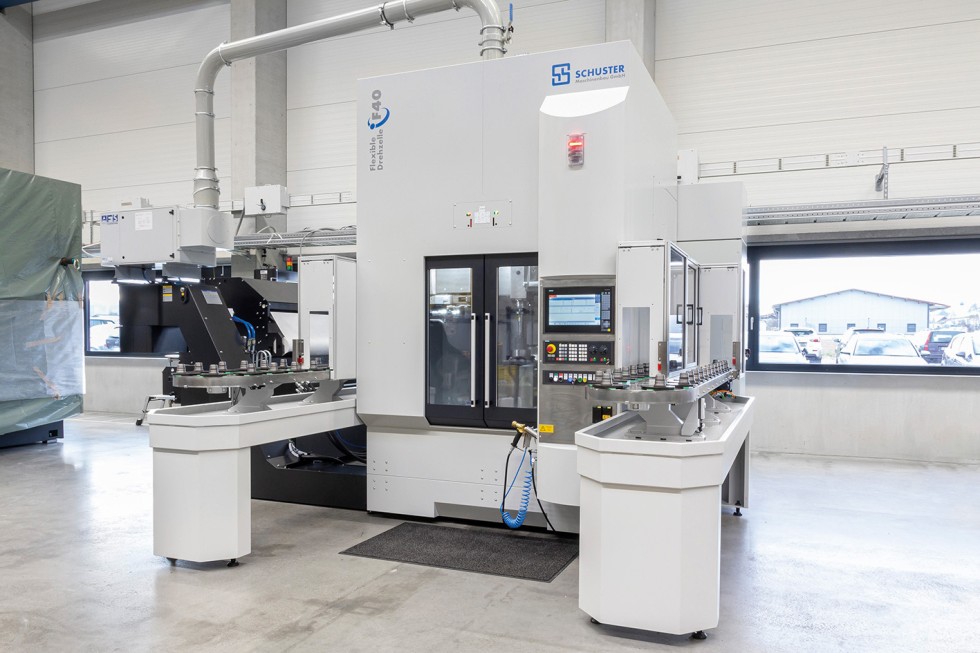
Schuster Maschinenbau setzt bereits seit vielen Jahren auf die Fertigungsmesstechnik aus Grünkraut. Auf der flexiblen Drehzelle F40 kommt beispielsweise der Messtaster TC61 zum Einsatz.
Foto: Blum
Im Jahr 2010 lieferte das Unternehmen die ersten Dreh- und Wälzfräszentren sowie Transferlinien für die Wellenkomplettbearbeitung, die den gesamten Prozess von Drehen, Fräsen und Schleifen über das Messen bis hin zum automatisierten Handling zwischen den Stationen umfassten. 2019 erreichte Schuster Maschinenbau die Marke von 100 Mitarbeitern. Die Anwender der Anlagen finden sich neben anderen Industrien auch im Automotive-Bereich. Gefertigt werden Getriebewellen, Nocken- und Ausgleichswellen, aber auch komplexe Motorwellen für Elektroantriebe. Meist werden die Wellen in mehreren miteinander verketteten Stationen bearbeitet, die an Beginn und Ende der Linie manuell be- und entladen werden.
Industrie 4.0 benötigt ganzheitlichen Lösungsansatz
Christian Moser, Projektleiter von Schuster Maschinenbau erläutert: „Mit der Transformation zur Industrie 4.0 verändern sich auch die Anforderungen an die Metallbearbeitung. Deswegen liefern wir nicht nur standardisierte Drehmaschinen. Wir realisieren innovative Zukunftslösungen in engster Kooperation mit unseren Kunden aus den metallbearbeitenden Industrien, um diese ganz individuell nach vorne zu bringen. Dafür hinterfragen wir permanent den Status Quo und streben nach ständiger Weiterentwicklung.“
Die Schuster-Maschinen arbeiten immer mit einer vertikal stehenden Werkstückspindel, je nach Aufgabe kommen Hauptspindel, Gegenspindel oder ein Mittendrehaggregat zum Einsatz. Je Arbeitsraum werden bis zu zwei Revolver oder auch Fräs- sowie Schleifaggregate eingesetzt, sodass Dreh-, Fräs- und Schleifbearbeitung in einer Aufspannung durchgeführt werden können. Die Maschinen sind immer mit X- und Z-Achse ausgestattet, welche sich abhängig vom Maschinentyp in der Spindel oder dem Revolver / Aggregat befinden. Die Spindel hat im Regelfall auch eine C-Achse. Die Y-Achse ist bei Bedarf als Option verfügbar und damit wie im Drehbereich üblich bei vielen Maschinen nicht vorhanden.
Arbeitsschritte einsparen durch fertigungsbegleitende Messung
„Das Messen im Arbeitsraum ist ein integraler Bestandteil unserer Bearbeitungsprozesse“, stellt Christian Moser fest. „In vielen Produktionsprozessen wird ein Durchmesser zunächst mit Aufmaß vor-bearbeitet und dann auf Endmaß geschliffen oder gedreht. Dazu ist es erforderlich, zwischen den beiden Schritten den aktuellen Durchmesser automatisiert zu messen und den Schleif- bzw. Drehvorgang entsprechend anzupassen. Um nicht etwaige Rundlauffehler oder den Temperaturgang der Maschine mit zu messen, ist hier eine Zweipunktmessung – ähnlich wie bei einer Bügelmessschraube – notwendig.“
Moser setzte sich mit dieser nicht alltäglichen Anforderung mit Uwe Fischer vom Messtechnikanbieter Blum-Novotest in Grünkraut in Verbindung. Beide Firmen verbindet bereits eine jahrelange Zusammenarbeit. Der 1968 gegründete Spezialist mit Sitz in Ravensburg gehört zu den weltweit führenden Herstellern qualitativ hochwertiger Mess- und Prüftechnologie für die internationale Werkzeugmaschinen-, Luftfahrt- und Automobilindustrie. Das Familienunternehmen beschäftigt heute über 600 Mitarbeiter an insgesamt neun Standorten in Europa sowie in den USA, Mexiko, Brasilien, China, Japan, Taiwan, Singapur, Korea, Indien und Thailand.
In den Drehmaschinen des Denklinger Herstellers wurden – je nach Kundenanforderung – schon diverse Blum-Messtaster und Lasermessgeräte installiert. „Früher hatten wir meist Messtaster mit Infrarot-Übertragung im Einsatz, heute sind die Taster in unseren Maschinen überwiegend per Funk mit der Steuerung verbunden. Diese lassen sich einfacher in die Maschinen integrieren, da keine Sichtverbindung zwischen Messtaster und Empfänger erforderlich ist“, ergänzt Moser.
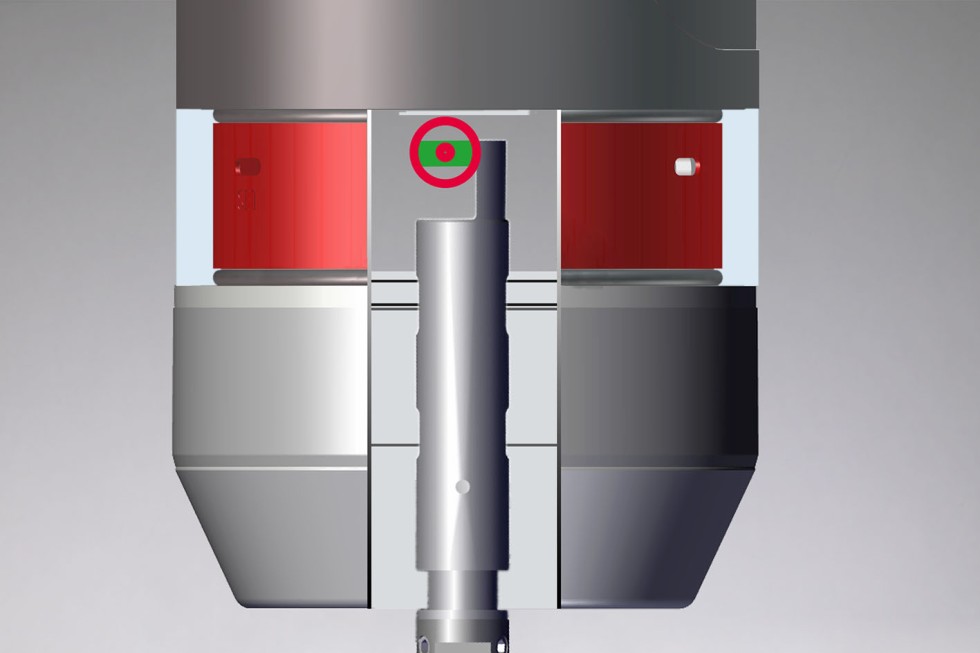
Das in zwei Achsen geführte, bidirektionale Messwerk garantiert eine verschleißfreie, optoelektronische Schaltsignalgenerierung. Grafik: Blum
Konstruktive Besonderheiten erweitern das Spektrum an Messmöglichkeiten
Da viele Schuster-Anlagen nicht mit einer Y-Achse ausgestattet sind, entfällt die Möglichkeit, das Werkstück mit einem Standard-Tasteinsatz vorn und hinten an zwei Punkten anzutasten, um den aktuellen Durchmesser zu erfassen. Es musste also eine andere Lösung gefunden werden. Diese wurde in Form des Messtasters TC61 und eines speziell entwickelten Tasteinsatzes präsentiert.
„Das Besondere am TC61 ist das in zwei Achsen geführte, bidirektionale Messwerk. Im Gegensatz zu sonst typischen Messtastern können dadurch nicht nur drückende, sondern auch ziehende Messungen hochpräzise durchführt werden. Zudem erfolgt die Schaltsignalgenerierung per Abschattung einer Miniaturlichtschranke im Inneren des Messtasters, was ihn verschleißfrei und somit sehr langlebig macht,“ erklärt Fischer.
Dieses außergewöhnliche Messwerk macht es möglich, den TC61 mit relativ schweren Tasteinsätzen – in diesem Fall einem Messbügel – auszustatten. Soll nun wie bei Schuster Maschinenbau der Durchmesser einer Welle erfasst werden, lässt sich dies ganz einfach per Zweipunktmessung durchführen. Dazu wird der sich im Revolver befindende TC61 horizontal eingeschwenkt und über die X-Achse je eine Messbewegung ziehend und drückend durchgeführt. Zusätzlich wird in manchen Anlagen eine Tastkugel am äußersten Ende des Bügels angebracht, um beispielsweise Längen, Nullpunkte oder Stufen messen zu können. Die Messbügel gibt es ab 35 Millimeter maximalem Messdurchmesser in diversen Abstufungen bis hin zu 73 Millimeter. Bis 50 Millimeter Nenndurchmesser bestehen die Bügel aus Stahl, die größeren Versionen dann aus Aluminium, um die Kräfte auf das Messwerk nicht zu groß werden zu lassen.
Ziel erreicht: Fertigungspräzision optimieren
„Das Messen des Durchmessers beim Aufmaßschleifen ist die Voraussetzung für die Einhaltung der wirklich engen Toleranzen“, berichtet Moser. „Wir setzen an den X-Achsen hochpräzise Glasmaßstäbe ein, um den Taster möglichst präzise positionieren zu können. Die Messungen werden in der Aufwärmphase der Maschinen öfter vorgenommen. Sobald sich die Temperaturen stabilisiert haben, wird seltener gemessen – auch so lassen sich die Taktzeiten insgesamt kurz halten. Die Zweipunktmessung lässt sich sehr schnell durchführen und wir erreichen eine Wiederholgenauigkeit auf der Maschine von 1,5 bis 2 Mikrometern.“
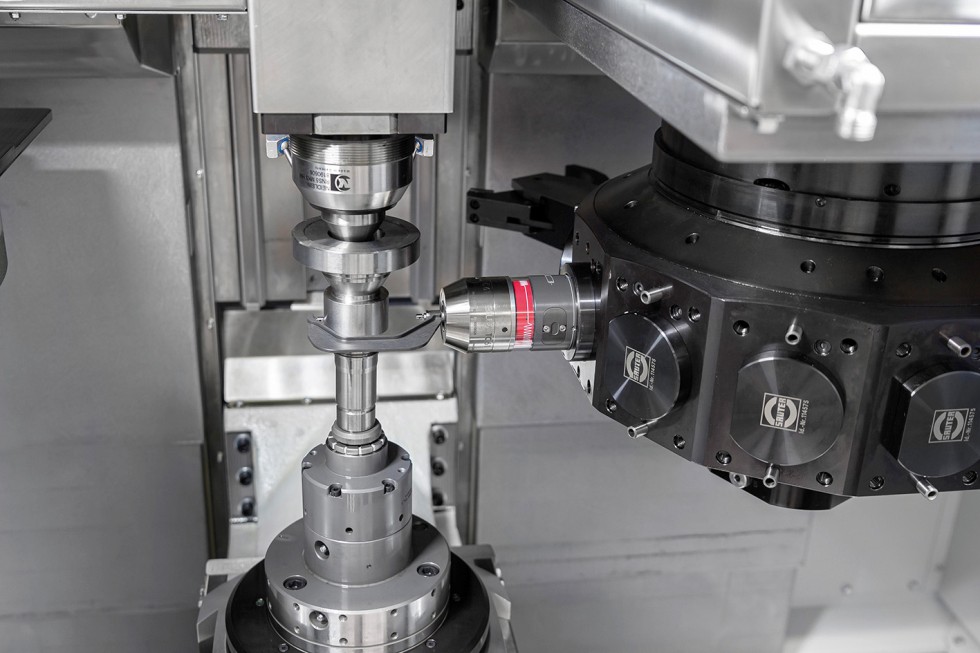
Vermessung der Drehteile in der Maschine: Dazu wird der im Revolver befindliche TC61 horizontal eingeschwenkt und über die X-Achse je eine Messbewegung ziehend und drückend durchgeführt.
Foto: Blum
Die Messungen mit dem Taster ermöglichen die Kompensation des Temperaturgangs ebenso wie der unvermeidbaren Abnutzung der Schleifscheibe. „In der Serienfertigung darf es keinen Ausschuss geben“, unterstreicht Moser, „da muss jeder Bearbeitungsvorgang über Monate und Jahre und Tausende von Werkstücken in der Toleranz bleiben. Das lässt sich nur mit laufender, prozessbegleitender Messung erreichen.“
Raue Bedingungen sind für robuste Technik unproblematisch
Dabei wird der Messtaster im Bearbeitungsraum nicht „geschont“. Während der Bearbeitung beträgt der Kühlmitteldruck bis zu 60 bar – dieser Strahl trifft indirekt auch den Messtaster im Revolver gegenüber. „Wir nehmen keine Rücksicht auf den Taster“, schmunzelt Moser. „Auch Späne und Schleifstaub bekommt er ab, das ist in Drehzentren einfach anders als in Fräszentren, in denen die ungenutzten Werkzeuge sicher im Werkzeugmagazin untergebracht sind.“ Auch die Bewegung des Revolvers selbst, der bei jeder Positionierung des Werkzeugs in einer Verzahnung fixiert wird, erzeugt nicht unerhebliche Schläge auf den gesamten Revolver und damit auch auf den Taster. Das „verkraftet“ dieser jedoch problemlos.
„Wir sind mit den gewählten Messtastern absolut zufrieden. Sie halten den widrigsten Bedingungen stand und erzeugen auch mit dem neu entwickelten Messbügel hochpräzise Messergebnisse. So fertigen unsere Kunden hochproduktiv, bei gleichzeitig geringsten Ausschussquoten“, fasst Moser seine Erfahrungen zusammen. „Die Ansprechpartner sind außerdem äußerst kompetent und bieten auch für komplexe Anforderungen ,schlaue‘ Lösungen – wie in unserem Fall den Messbügel.“
Das könnte Sie auch interessieren:
Kugelgewindetriebe auf dem Prüfstand