Software pusht Maschinenauslastung – weil jede Minute zählt
Softwarelösungen sind für die Firma Deutz ein wichtiger Hebel zur Kostensenkung und Effizienzsteigerung. An einem Fertigungsstandort gelang es dem renommierten Maschinenbauer nun, die Auslastung signifikant zu verbessern – indem der Vorschub automatisch an die Schnittbedingungen angepasst wird.
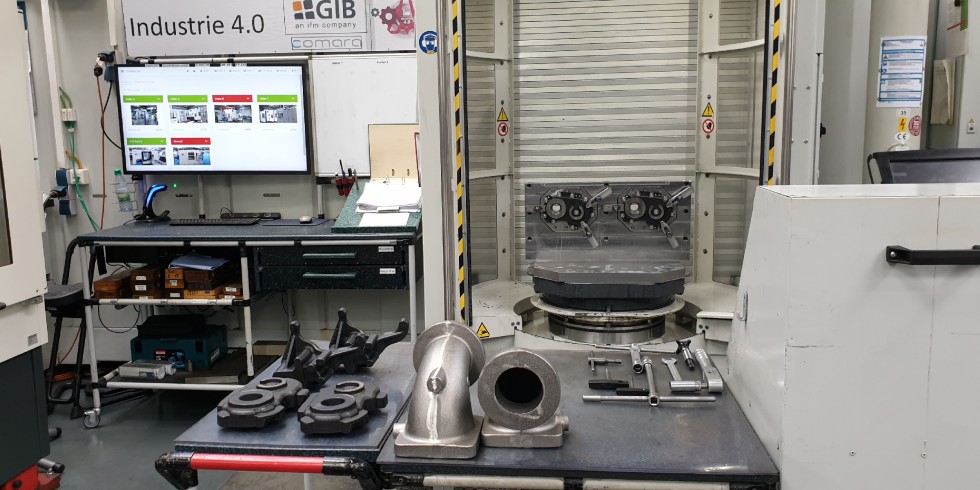
Als Problemlöser fungiert bei Deutz in Herschbach seit Kurzem eine Software, die den Vorschub automatisch an die Schnittbedingungen anpasst.
Foto: Deutz/Comara
Trotz aller globalen Verwerfungen konnte der weltweit führende Hersteller innovativer Antriebssysteme für den sogenannten „Off-Highway-Bereich“ seinen Wachstumskurs auch im ersten Quartal 2022 fortsetzen. Und nicht nur das: Auch die Profitabilität hat sich weiter verbessert. Dieser Erfolg hängt laut Jan Marth, Betriebsingenieur bei Deutz Herschbach, eng damit zusammen, dass „wir in der Fertigung nach jeder Minute suchen, die wir bei der Bearbeitung einsparen können“.
In Herschbach im Westerwaldkreis befindet sich das Kompetenzzentrum für Anbauteile – wie Nebenabtriebe, Ventilsteuerungen und Thermostatgehäuse. Mit rund 130 fachkompetenten, qualitätsorientierten Mitarbeitern läuft dort die Bearbeitung und Vormontage dieser Bauteile für die Kölner sowie die Ulmer Montagewerke ab – mit direkter Anlieferung an die Montagebänder sowie die angrenzenden Servicebereiche. Am Standort setzt das Unternehmen dazu seit Kurzem auf eine neue Software zur Fertigungsoptimierung. Auf den Maschinen, die in die Lösungen eingebunden wurden, werden seitdem deutlich mehr Teile gefertigt.
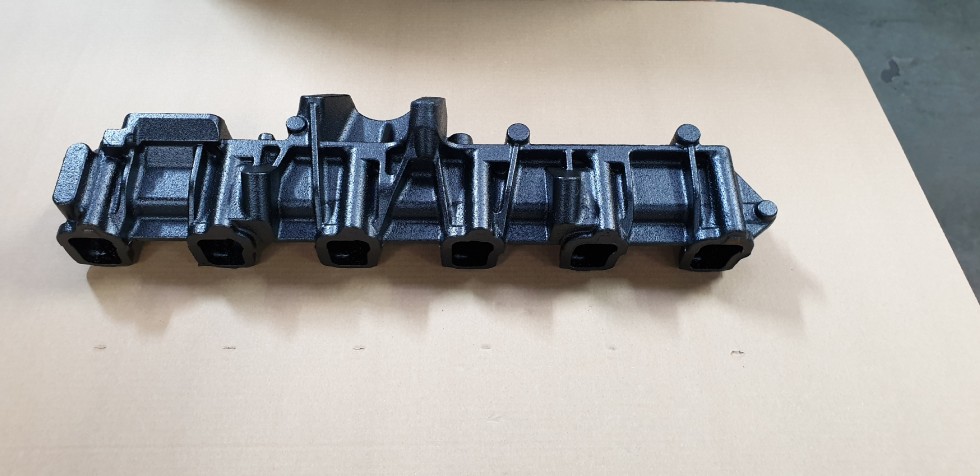
Das Kompetenzzentrum für Anbauteile mit rund 130 fachkompetenten Mitarbeitenden dient der Bearbeitung und Vormontage von Komponenten, die an die Kölner sowie die Ulmer Montagewerke geliefert werden.
Foto: Deutz/Comara
Ein „Insider-Tipp“ mit Folgen
Als der Werksleiter der spanischen Deutz-Niederlassung 2019 die Comara-Lösung als Effizienzsteigerungstool empfahl, „waren wir ganz Ohr“, erinnert sich Marth, der vor seinem Studium bei Deutz Zerspanungsmechaniker gelernt hatte. Denn auch die in Herschbach gefertigten Motorenkomponenten müssen in puncto Qualität und Preis, global gesehen, wettbewerbsfähig sein. Der Druck, der auf dem Produktionsstandort mit seiner Fertigung lastet, ist dementsprechend hoch. Der spanische Werksleiter war im Jahr 2019 von einem Mitarbeiter der Walter AG, einem Werkzeugspezialisten, auf die Software aufmerksam gemacht worden. „Die Lösung erschien uns deshalb eine vielversprechende Möglichkeit zu sein, um produktiver zu fertigen und einen wirtschaftlichen Einsatz von Werkzeugen zu gewährleisten“, so Marth, der seit mittlerweile 12 Jahren bei Deutz beschäftigt ist und alle Abläufe genau kennt.
Testlauf offenbart vielfältige Chancen
„Ein Versuch wiegt mehr als 1000 Worte“, so die Meinung von Marth. Deshalb startete Deutz von Ende 2019 bis Anfang 2020 zunächst einen Testlauf. Um die Software „Comara iCut“ sowie „Comara appCom“ auf den zwei Bearbeitungszentren zu implementieren, reiste ein Mitarbeiter des Softwarespezialisten nach Herschbach. „Das Tolle war: Wir konnten so vorab prüfen, ob die Lösungen für uns passen und die anvisierten Einsparungen erbringen“, so der Ingenieur.
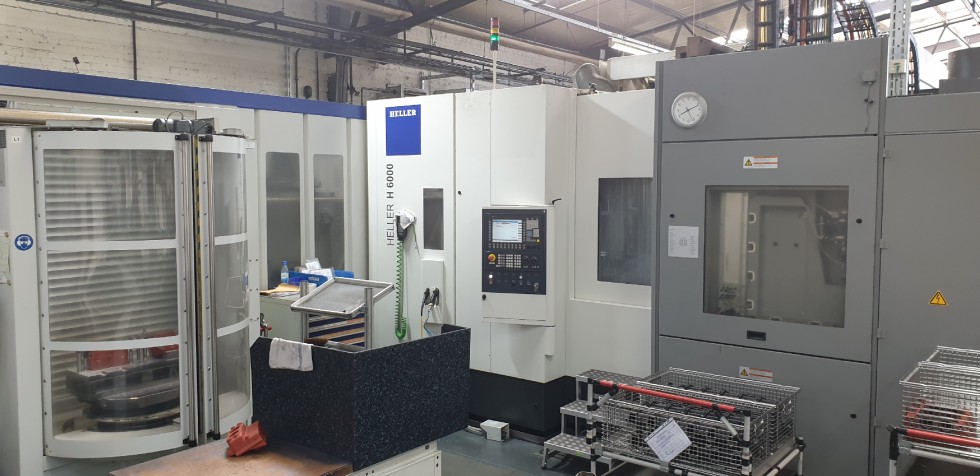
Moderne automatisierte Fertigungstechnik dominiert die Werkshallen am Standort Herschbach.
Foto: Deutz/Comara
Für den Testlauf wurden Maschinen ausgewählt, die für eine mittelschwere und schwere Zerspanung ausgelegt sind. Also ideale Voraussetzungen, um zu prüfen, welche Effizienzgewinne sich mit Comara iCut, einer Software, die den Vorschub automatisch an die Schnittbedingungen anpasst, erzielen lassen. Unter bestimmten Umständen können die Einsparungen bei der Bearbeitungszeit laut Comara bis zu 25 Prozent betragen. Bei Deutz wurden während des Testlaufs acht Prozent eingespart. Dies ist für Marth „kein Pappenstiel“. Vor allem überraschte den Ingenieur, dass die realisierten Einsparungen sich so einfach und schnell erzielen lassen.
Großer Nutzen, geringer Aufwand
Zwar lässt sich Comara iCut breit einsetzen, aber die meisten Zeitgewinne werden in der Regel bei Schruppfräs- und Bohrbearbeitungen generiert. Um die Bearbeitungszeit – so wie im Testlauf – verkürzen zu können, misst Comara iCut bis zu 500-mal pro Sekunde die Spindelleistung und passt den Vorschub auf die jeweiligen Schnittbedingungen an. Das heißt, die Software registriert über die Spindellast, dass beispielsweise der Bohrer aufgrund von Aufmaßabweichungen des Werkstücks noch keinen Kontakt zur Oberfläche hat und beschleunigt in diesem Fall den Vorschub. Dieser Prozess wiederholt sich während des Bearbeitungszyklus mehrfach. Je komplexer dabei das Werkstück und je zahlreicher die Bearbeitungsschritte sind, desto mehr Gelegenheiten findet die Software, den Vorschub und damit die Bearbeitungszeit entsprechend zu optimieren.
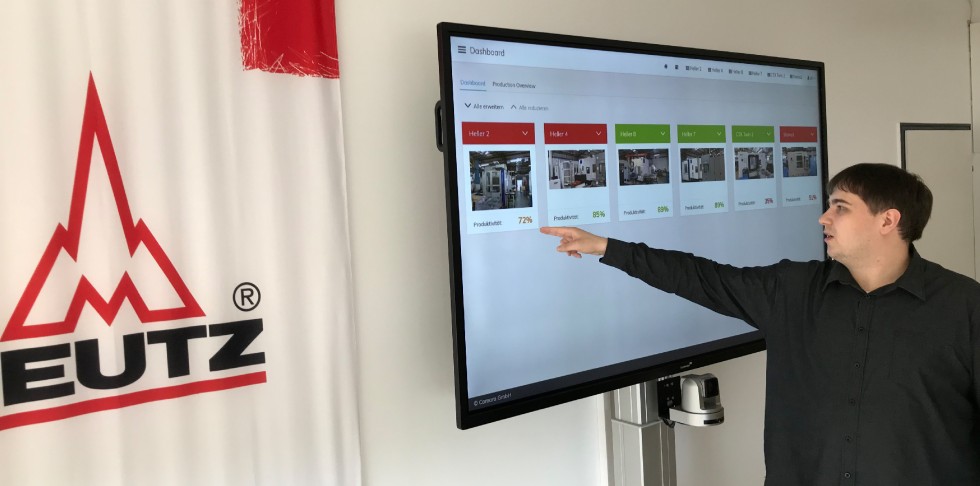
Proaktive Problembehebung: Informationen zu den Lauf- bzw. Stillstandzeiten der Maschinen werden regelmäßig in Shopfloor-Gesprächen diskutiert.
Foto: Deutz/Comara
Flexibel und schnell trainiert
Damit die steuerungsbasierte Software das kann, muss sie entsprechend „trainiert“ werden – und zwar für jedes auf der Maschine gefertigte Werkstück. Während dieser Lernphase gibt der Bediener für die verwendeten Werkzeug am Anfang und am Ende eines Bearbeitungsschrittes einen Befehl in die Maschinensteuerung ein. Anschließend braucht in der Software nur noch definiert werden, um wie viel Prozent die Vorschubgeschwindigkeit erhöht werden soll, wenn die registrierte Spindellast gering ist. So einfach und schnell die Anlernphase war, so unkompliziert ist laut Marth auch die Installation der Software. Im Vorfeld musste Deutz lediglich ein Comara-Formblatt zum Softwarestand der Maschinensteuerung ausfüllen und auch das Aufspielen der Software war „kein Akt“.
Auch wenn der Testlauf die Erwartungen übertraf, „um die für uns beste Lösung zu finden, haben wir uns nach dem Test noch mal sehr genau ähnliche Lösungen von verschiedenen Anbietern angeschaut“, so Marth. Dass die Entscheidung wieder für Comara iCut fiel, hatte vor allem zwei Gründe. Zum einen ist damit auch die Anbindung älterer Maschinen möglich. Das war bei den von Deutz in Betracht gezogenen Konkurrenzlösungen laut Marth so nicht möglich. Das heißt nun, keine Maschine am Standort Herschbach muss aus Altersgründen von einer Optimierung ausgeschlossen werden.
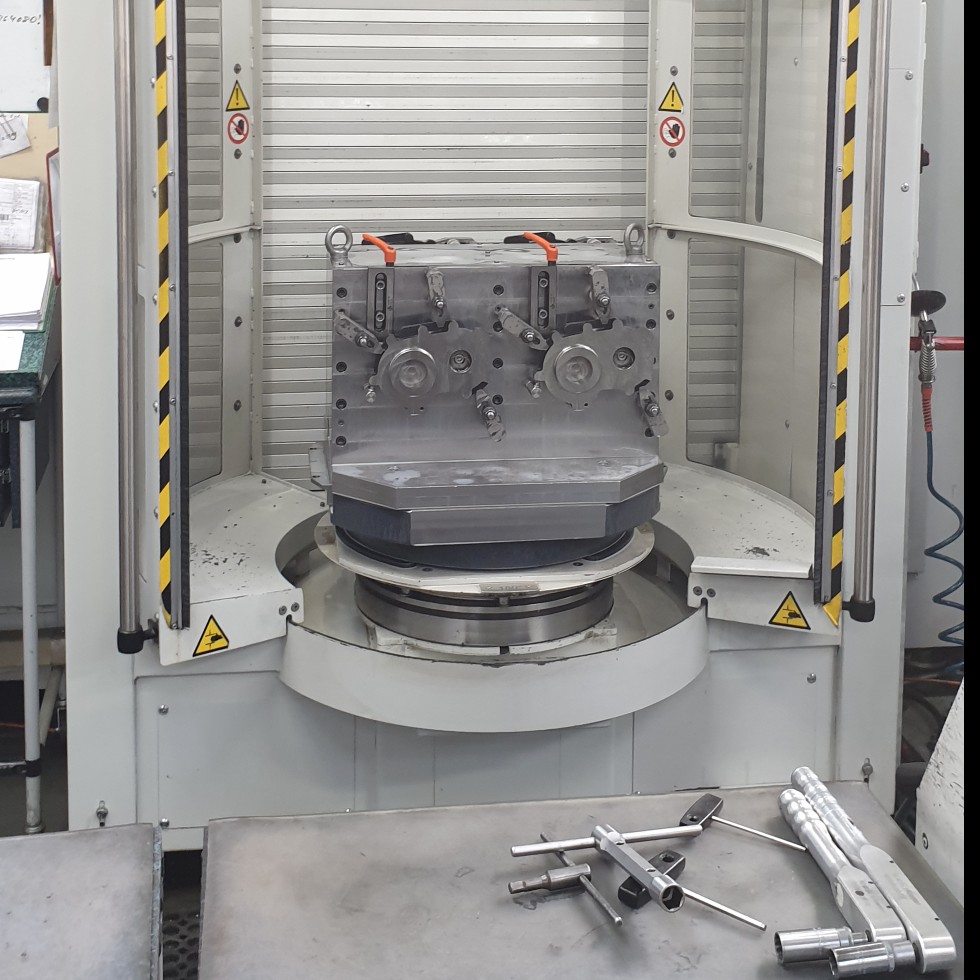
Blick in den Bearbeitungsraum: An zwei Maschinen wurde die neue Lösung zur Vorschubanpassung erprobt und konnte auf Anhieb überzeugen.
Foto: Deutz/Comara
Zudem überzeugte die Entscheider die Lösung auch in puncto Parametrisierung. Denn anders als Varianten, die die Anpassungen vorgeben, können Anwender in Comara iCut selbst festlegen, um wie viel Prozent der Vorschub erhöht werden soll. „Wir können damit unsere ganze Erfahrung, unser Know-how einbringen und damit den größten Vorteil für uns rausholen.“
Einsparungen erhöhen Profitabilität
Als die Entscheidung getroffen war, implementierte Deutz die Lösung auf zwei weiteren Bearbeitungszentren. Die erzielten zeitlichen Einsparungen liegen derzeit über alle Maschinen und Werkstücke hinweg bei sechs Prozent. „Das ist richtig gut“, findet Marth. Denn weil die Maschinen bereits rund um die Uhr laufen und die Auftragsbücher voll sind, bedeutet die beschleunigte Bearbeitungszeit, dass „wir in der Lage sind, Kapazitätsspitzen in der eigenen Produktion abzudecken“. Auch wenn sich eine Implementierung auf weiteren Maschinen nach individueller Betrachtung der Maschinen und Effekte am Standort Herschbach derzeit nicht lohnt, so ist sich der Betriebsingenieur sicher, „bei uns wird künftig kein Bearbeitungszentrum mehr angeschafft, auf dem Comara iCut nicht läuft“.
Software zur Maschinenüberwachung
Marth, zu dessen Aufgaben es gehört, in der Fertigung am Standort Herschbach Optimierungschancen zu erkennen und entsprechende Lösungen einzuführen, testete 2019 auf den zwei Maschinen nicht nur Comara iCut, sondern auch Comara appCom – eine Software, die verschiedene Maschinen- und Fertigungsdaten erfasst, visualisiert und auswertet. Da diese mit unterschiedlichen Maschinensteuerungen interagieren kann, lässt sie sich breit einsetzen. „Mit dem Testlauf wollten wir prüfen, ob wir Maschinenstillstandszeiten in wertschöpfende Zeiten umwandeln können“, erinnert sich Marth.
Auch das Aufspielen dieser Anwendung auf die Maschinen ist im Grunde genommen sehr einfach. Bei Deutz dauerte es Ende 2019 nur deshalb einige Tage, weil das in den Testlauf eingebundene Bearbeitungszentrum damals so neu war, dass die Entwickler die Lösung erst entsprechend aktualisieren mussten. Und auch wenn die Testphase am Ende zu kurz war, um konkrete Einsparungen zu erzielen, das Effizienzsteigerungspotential stand außer Frage. „Wir können ja nur das ändern, was wir sehen – und ohne Comara appCom bekommen wir diese Transparenz nicht.“
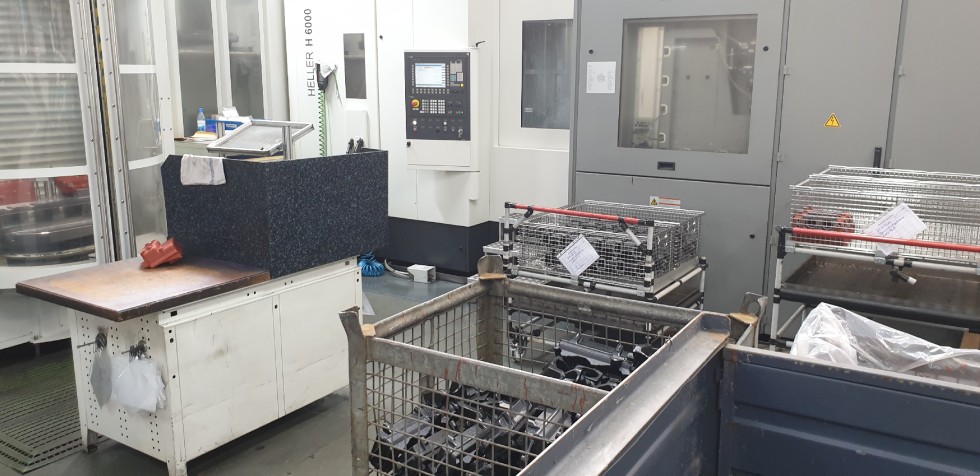
Die Auslastung in der Fertigung wurde dank der neuartigen Softwareunterstützung signifikant gesteigert.
Foto: Deutz/Comara
Das „A und O“ für die Akzeptanz: Bediener einbeziehen
Derzeit läuft die Software auf sechs Fertigungsmaschinen. Natürlich spüren auch die Maschinenbediener Erleichterungen. Denn anstatt die Gründe für Maschinenstillstände handschriftlich aufnehmen zu müssen, drücken sie jetzt Buttons auf dem Display der Maschine. Doch nicht nur für die Mitarbeiter auf dem Shopfloor ist das ein Gewinn. Auch Marth profitiert. Denn zu seinen Aufgaben gehörte die Übertragung der handschriftlich erfassten Daten in Excel-Dateien. Dies erforderte nicht nur viel Zeit, der manuelle Vorgang war auch eine mögliche Fehlerquelle mit Auswirkungen auf die Datenqualität.
Einfache Problemerkennung
Mit Comara iCut hat sich die Datengüte deutlich erhöht. Denn anstatt darauf angewiesen zu sein, dass die Bediener exakt beschreiben, warum die Maschine gerade nicht in Betrieb ist, erhalten diese jetzt auf dem Bedienpanel der Fertigungsmaschine eine Aufforderung, einen Stillstandgrund auszuwählen. Das geht schnell und sorgt dafür, dass alle Stillstandzeiten erfasst werden. „Damit haben wir jetzt eine Stellschraube, um Probleme zu sehen und zu beheben“, so Marth.
Beispielsweise wurde so erkannt, dass bei einem 3-Maschinen-Bedienarbeitsplatz die Werkstückbelegung auf einer Maschine suboptimal war. „Das hätten wir ansonsten niemals mitbekommen.“ Denn der Stillstand aufgrund der Bauteilaufspannung betrug ja jeweils immer nur wenige Minuten. Am Ende des Monats kamen so jedoch 20 Stunden zusammen. Gelöst wurde dieses Problem durch eine Neubelegung der Maschine. Bauteile, die aufgrund ihrer Bearbeitungszeit auf dem Mehr-Maschinen-Bedienarbeitsplatz zu vielen kurzen Stillstandzeiten führten, werden mittlerweile auf einer anderen Maschine gefertigt. Doch nicht nur die Stillstandzeiten wurden so eliminiert. Die Umbelegung entlastete auch die Bediener an diesem Arbeitsplatz. „Sie können die Maschinen jetzt effizienter bestücken.“
Etabliertes Frühwarnsystem
Aber mit Comara appCom lassen sich nicht nur Stillstandzeiten entdecken und entsprechend abstellen. Durch das Zusammenspiel der beiden Lösungen implementierte Deutz auch ein gewisses „Frühwarnsystem“. Denn durch das regelmäßige Prüfen der in Comara appCom aufgenommenen Alarmmeldungen aus Comara iCut lassen sich beispielsweise Rückschlüsse auf Materialveränderungen ziehen. Wenn bei der Bearbeitung beispielsweise festgelegte Belastungsgrenzen überschritten werden, dann „zeigt uns das, dass etwas anders ist“ – so Marth. Ein möglicher Grund könnte beispielsweise sein, dass die Oberfläche der Gussteile härter als gewohnt ist. In jedem Fall hilft der Hinweis auf eine Veränderung, dass früh adäquate Maßnahmen getroffen werden können.
Verbesserungen proaktiv angehen
Auch wenn Deutz in Herschbach derzeit nur die Basisversion nutzt, „sie hilft uns bereits, effizienter an den Lösungen zu arbeiten“. Um alle in die Problembehebung einzubeziehen, werden die Informationen zu den Lauf- bzw. Stillstandzeiten der Maschinen beispielsweise jeden Freitag auf den Shopfloor-Gesprächen diskutiert.
Doch nicht nur aktuelle Probleme kommen hier auf den Tisch. „Wir suchen auch proaktiv nach Verbesserungen“, so Marth. Aktuell werden die Daten aus Comara appCom dahingehend analysiert, ob bzw. bei welchen Bearbeitungen Duplo-Werkzeuge auf den Maschinen Zeiteinsparungen bringen und wie deutlich dies den Fertigungsprozess optimieren könnte. Dies ist eine Aufgabe, der sich am Standort Herschbach nicht nur der Betriebsingenieur Marth, sondern die ganze Belegschaft „voll und ganz verschrieben hat“.
Das könnte Sie auch interessieren:
KI optimiert die Drehteile-Fertigung
Hohe Anlageneffizienz durch intelligent geplante Rüstvorgänge
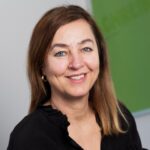
Syra Thiel ist Senior Editor bei der Agentur Storymaker in Tübingen. Foto: Storymaker