Wie sich mit effizienter Fertigung Erträge steigern lassen
In den vergangenen Jahren hat sich in den metallbearbeitenden Betrieben viel getan: Ein junger, leistungsfähiger Maschinenpark, zahlreiche Ansätze zur Automation und der Einsatz neuer Bearbeitungsverfahren helfen dabei, die Unternehmen fit zu machen für den globalen Wettbewerb.
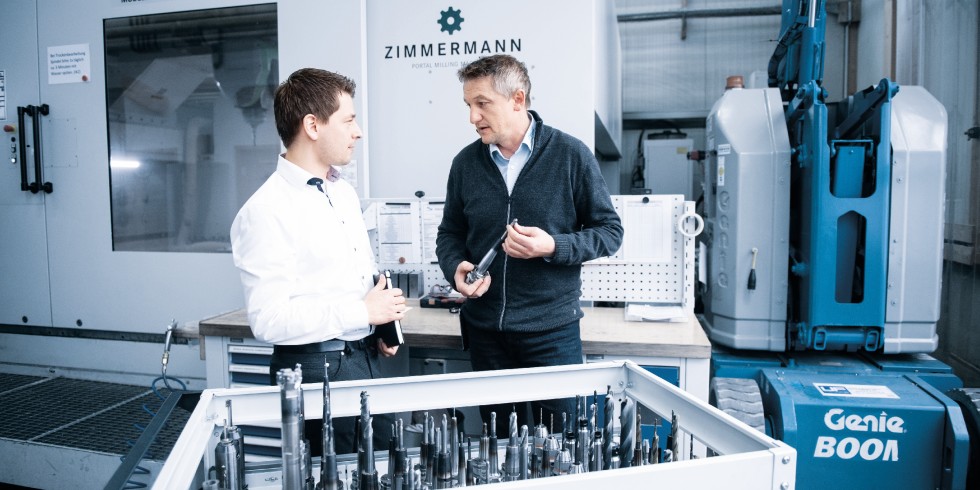
Erfahrene Berater bringen bei der Standardisierung von Fertigungsabläufen den Blick von außen mit und verringern die Gefahr, etwas Wichtiges zu übersehen.
Foto: Tebis
Trotzdem bleibt viel Potenzial ungenutzt – weil schon in der Planung oft Daten und Ansätze für eine optimale Auslegung der Prozesse fehlen. Ein Consulting-Unternehmen hat sich umfassend mit der Thematik befasst und präsentiert eine Auswahl an Lösungsansätzen, die Fertigungsbetriebe weiter bringen. „Dreh- und Angelpunkt“ sind die passenden Strategien in der Arbeitsvorbereitung.
Was hilft, wo „Excel“ an Grenzen stößt?
Wer Metall zerspant, spürt seit Jahren steigende Anforderungen in nahezu allen Bereichen. Die Materialien werden „schwieriger“ und Geometrien komplexer. Die Lose werden kleiner. Darüber hinaus wird die Terminschiene immer anspruchsvoller, die Aufträge kommen kurzfristiger – und das bei auf breiter Front bröckelnden Margen. Damit wird die wirtschaftliche, wettbewerbsfähige Bearbeitung von Aufträgen immer mehr zur Herausforderung.
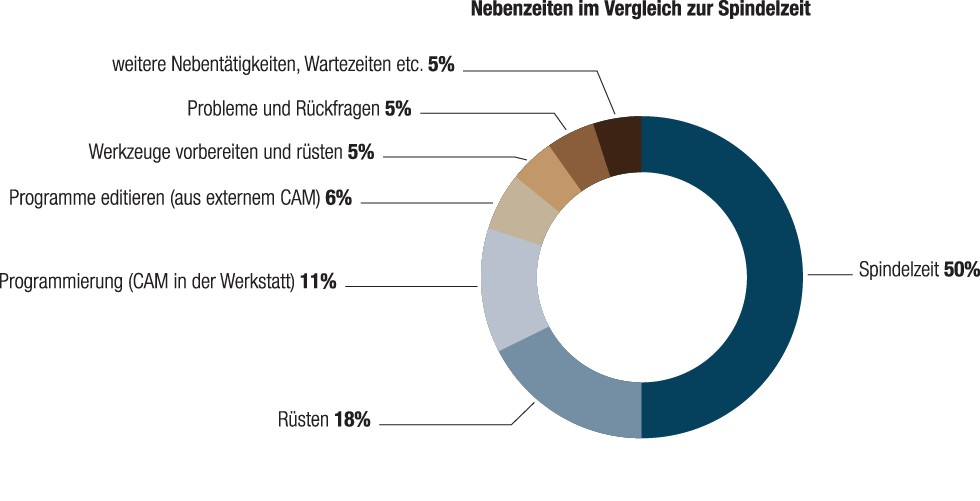
Im Durchschnitt fallen genauso viele Nebenzeiten an, wie produktive Spindelzeiten erreicht werden. Der größte Aufwand liegt beim Rüsten, gefolgt von Aufwänden an den NC-Programmen. Grafik: Tebis Consulting
Inzwischen stoßen viele Unternehmen an ihre Grenzen. Geplant wird noch oft und gern mit Excel-Tabellen, aber die sind steigernder Komplexität schnell nicht mehr gewachsen, sind insbesondere starr und unflexibel bei unvorhergesehenen Ereignissen. Die Konsequenz: Viele Einflussfaktoren wie Rüsten oder Programmieren bleiben unberücksichtigt. Teilweise sind sie sogar mangels Daten den Verantwortlichen unbekannt.
Haupt- und Nebenzeiten als Gradmesser
Die Folge der fehlerhaften Planung: Die Spindelzeiten der Maschinen sind bei weitem nicht so hoch, wie sie sein könnten – im Idealfall nämlich in der Nähe der maximal jährlich verfügbaren 8760 h/Jahr. Davon sind die meisten Unternehmen indes weit entfernt. Die Maschinenstundensätze sind damit oft nicht mehr wettbewerbsfähig.
Das liegt auch am großen Anteil der Nebenzeiten auf den Maschinen. Ein Großteil davon geht meist ins Rüsten. Ein weiterer Anteil entfällt auf Klärung fehlender oder falscher Informationen oder auf Wartezeiten, weil wieder einmal das Rohteil oder das Spannmittel nicht verfügbar ist, wichtige Werkzeuge fehlen oder der aktuelle Stand der CAD-Daten nicht freigegeben ist. Oder aber, weil die Programme sogar erst an der Steuerung der Maschine nachbearbeitet und „gängig gemacht“ werden müssen.
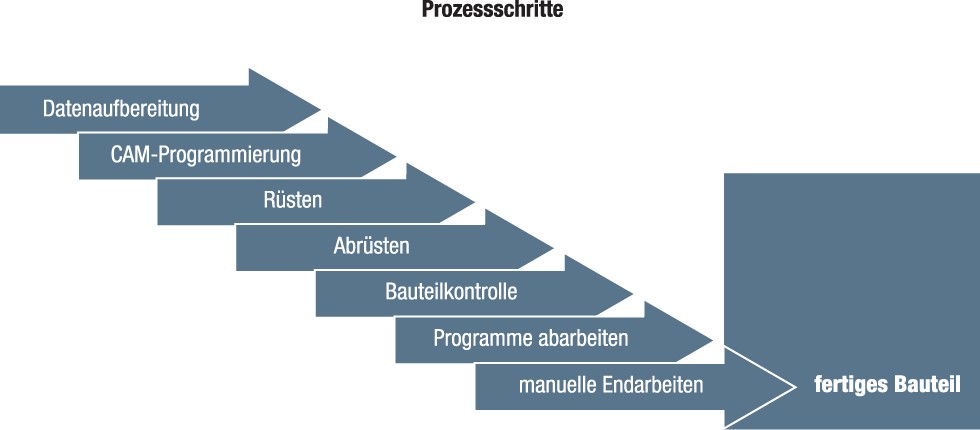
Bei der Standardisierung müssen alle Prozessschritte zusammenpassen, damit die Fertigung reibungslos läuft. Grafik: Tebis Consulting
Standards in der Arbeitsvorbereitung sichern Potenziale
Ursache ist oft eine Arbeitsvorbereitung, die ihre Möglichkeiten aufgrund fehlender Standards und Daten nicht ausschöpfen kann. Programme, die fehlerhaft sind, machen den Maschinenbedienern das Leben unnötig schwer. Oft fehlt auch ein in den allgemeinen Datenfluss im Unternehmen eingebundenes Werkzeugmanagement – die Folge ist Wildwuchs bei der Werkzeugvielfalt. Auch wer die Spannmittelplanung erst an der Maschine vornimmt, verschenkt wertvolles Potenzial.
Darüber hinaus ist der Automatisierungsgrad in der Fertigung vieler Unternehmen viel zu gering, und es gibt immer noch Fälle, in denen entsprechende Projekte mangels transparenter Einbeziehung und Beteiligung der Mitarbeiter von der Belegschaft mit Misstrauen und Ängsten beäugt werden. Hier gibt es viele Ansatzpunkte, die eigene Effizienz und damit auch ganz direkt die eigenen Erträge zu verbessern. Es ist wichtig, dass die Unternehmensführung bei allen beschlossenen Maßnahmen eine klare Linie aufzeigt und das Vereinbarte auch konsequent vorlebt und umsetzt.
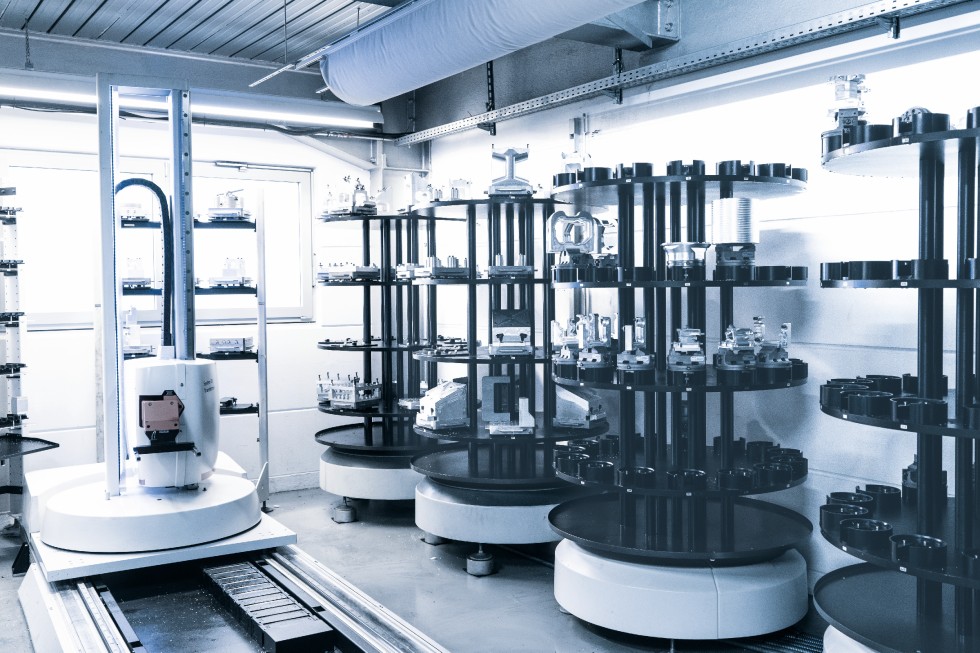
Beim Einsatz von Handlingssystemen muss das gesamte Know-how, das vorher der Maschienenbediener in die Zerspanung eingebracht hat, bereits im NC-Programmierprozess in die Bearbeitung einfließen.
Foto: Tebis
Wer die Abläufe in seinem Unternehmen rationell ausrichten will und so gezielt die Wirtschaftlichkeit erhöhen möchte, beginnt am besten beim Thema Standardisierung. Damit ist nicht immer eine Standardisierung der Produkte gemeint – hierzu gehört auch, sich über standardisierte Abläufe, Standards in der Konstruktion, Programmierung, standardisierte Zerspanungswerkzeuge und vieles mehr Gedanken zu machen. Zugegeben, nicht gerade einfach im laufenden Tagesgeschäft. Zumal die gewohnten Abläufe, Gegebenheiten und Denkmuster oft nahezu unvermeidbar den Blick auf Wesentliches verstellen.
Der „Blick von außen“ hilft – was Berater leisten können
Deshalb ist es vorteilhaft, jemanden hinzu zu ziehen, der schon reichlich Erfahrung aus vergleichbaren Projekten einbringen kann. Der Blick von außen eröffnet zudem neue Horizonte – und die Gefahr, etwas Wichtiges zu übersehen, ist mit erfahrenen Partnern deutlich geringer als bei einem unternehmensinternen „Alleingang“. Sinnvoll ist, zu Beginn gemeinsam mit Experten die eigenen Prozesse und Abläufe auf den Prüfstand zu stellen. Dazu gehört auch die Überlegung, welche Aufträge man künftig bearbeiten möchte und welche nicht – etwa, weil sie nur viel Arbeit und kaum Ertrag bringen oder nur mit großem Aufwand durchgeschleust werden können. Eine tragfähige Kernkompetenz muss „sauber“ definiert werden.
Für einen systematischen und damit skalierbaren Ansatz sollten dann klare Fertigungsstandards definiert werden – in Teams, die entlang der neu definierten Prozesskette ausgerichtet sind. Dabei ist es sinnvoll, möglichst alle Betroffenen aktiv in den Prozess mit einzubeziehen. Ziel ist immer, alle Mitarbeiter „abzuholen“ und entsprechend zu motivieren. Wichtig bei allem ist ein transparentes, konsequentes und klares Handeln der Führungskräfte.
Im Mittelpunkt steht das „intelligente Bauteil“
Auch wenn es letztlich auf den ganzheitlichen Ansatz ankommt – meist lassen sich mit einigen wenigen Maßnahmen aus dem Gesamtpaket bereits „Quick-wins“ erzielen, die die Situation schnell spürbar verbessern können. Das können beispielsweise Konstruktionsstandards sein, die die Werkzeugvielfalt spürbar begrenzen. Aber auch die Schnittstellen hinsichtlich des Informationsgehalts müssen konsistent und durchgängig sein – und deutlich weiter in die Details gehen als bisher in den meisten Systemen üblich. Zwischenergebnisse, Features und Abzugskörper sind nur einige Informationen, die hier relevant sind.
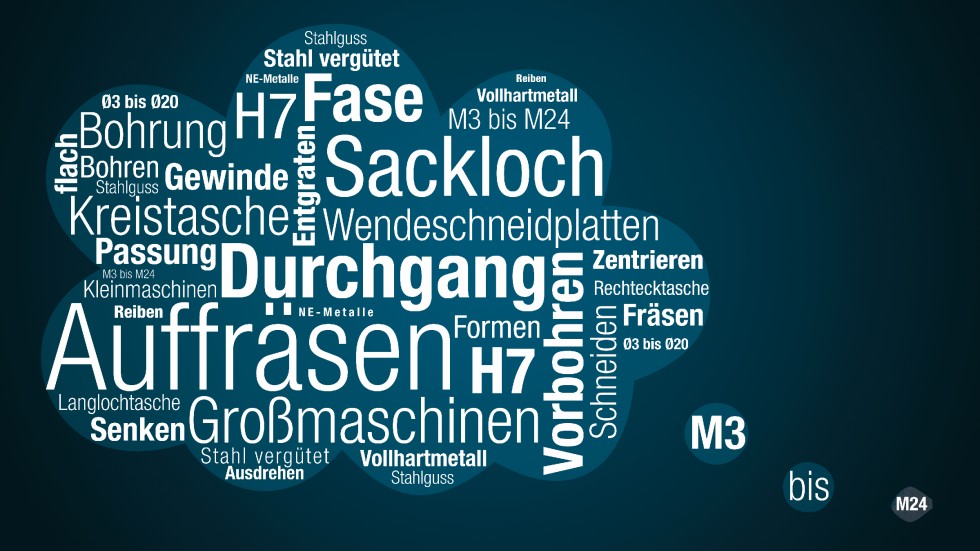
Beim Aufbau von Bearbeitungstemplates (Technologiepakete) müssen viele Informationen regelbasiert verknüpft werden, wie Geometrien und Formen, Fertigungstechnologien, Werkzeuge, Materialien oder Fähigkeiten von Maschinen. Grafik: Tebis
Ein großer Schritt ist die Möglichkeit, softwareseitig wiederkehrende Tätigkeiten systemisch zu automatisieren – mit Hilfe von Templates und spezifischen Konfigurationen. Den größten Schritt indes schafft eine konsequente Umsetzung der Datendurchgängigkeit im Unternehmen, die Mehrfacheingabe immer der gleichen Informationen ins System erübrigt und damit Fehlerquellen eliminiert. Ziel ist die nahtlose Übernahme aller fertigungsrelevanten Informationen aus dem intelligenten Bauteil.
Automatisierung in der Fertigung
Wird schließlich hardwareseitig automatisiert, etwa mit Handlingsystemen oder Robotern und den dazu gehörenden automatisierten Spannmitteln, müssen diese Möglichkeiten auch in der Programmierung berücksichtigt und entsprechend umgesetzt werden. Auch hier müssen Prozesse neu gedacht werden – das gesamte Know-how, das früher der Bediener in den Zerspanungsprozess eingebracht hat, muss jetzt bereits beim Programmieren in die Bearbeitung einfließen.
Das bewirkt, dass die Bearbeitung nicht mehr von der Anwesenheit des Bedieners abhängt. Hier liegt der Schlüssel zu einer optimalen Auslastung der Maschinenspindeln: Wenn ein Handlingsystem nur noch bereits vor-gerüstete Werkstücke im Arbeitsraum platziert und nach der Bearbeitung wieder entnimmt, wird die Laufzeit im Prinzip nur noch vom Werkstückspeicher, den rüstbaren Werkzeugen und der Kapazität der Programmierer begrenzt. Damit lässt sich die reine Laufzeit der Bearbeitungszentren sehr weitgehend optimieren.
Voraussetzung sind stabile NC-Prozesse
Ein wichtiger Schritt ist die Einführung von „Quality Gates“ in der Fertigung. Es ist unerlässlich, dass für ein optimales Ergebnis die Bearbeitungsabschnitte in der Abfolge auf einem entsprechend guten Ergebnis des vorherigen aufbauen können. So ist es wichtig, dass beispielsweise fertige, optimierte Programme auf die Maschine kommen, die mit Poti-Einstellung „100 Prozent“ ablaufen. Dafür sorgt eine verlässliche NC-Verifikation und Simulation. Sie bietet extrem hohe Sicherheit und noch dazu – quasi nebenbei – stabilere Prozesse, verlässlichere Termine und auch eine höhere Bauteilqualität.
Quality Gates sorgen für eindeutige Informationen
Quality Gates garantieren optimale Abläufe der einzelnen Prozessschritte und sorgen für einen konsistenten und definierten Informationsfluss über die Schnittstellen einzelner Verantwortlichkeiten hinaus. Sie sind ein wichtiger Bestandteil der Wertschöpfungskette und im Informationsfluss. In der Regel ist der Gesamtprozess in der Produktion eines Bauteils in einzelne Teilaufgaben gegliedert, die logisch aufeinander oder parallel erfolgen. Zwischen diesen Teilaufgaben sorgen Quality Gates dafür, dass erst alle im Prozess vordefinierten Bedingungen erfüllt sein müssen, bevor der nächste Abschnitt beginnen kann.
Ist etwa der Meilenstein „Konstruktion fertig“ mit allen Vorgängen erreicht, können diese Folgevorgänge (Beschaffung, Programmierung, Werkzeugbereitstellung …) freigegeben und gestartet werden. Hier kann ein Manufacturing Execution System (MES) den Anwender in seinen Aufgaben nachhaltig unterstützen. Darüber hinaus wird ein MES automatisch stets den aktuellen Fertigungsfortschritt anzeigen und auch Abweichungen oder fehlende Informationen transparent darstellen. Aber auch ohne ein MES kann mit einem gezielten Shopfloor-Management einiges an Transparenz geschaffen werden, um Fortschritte und mögliche Abweichungen klar darzustellen.
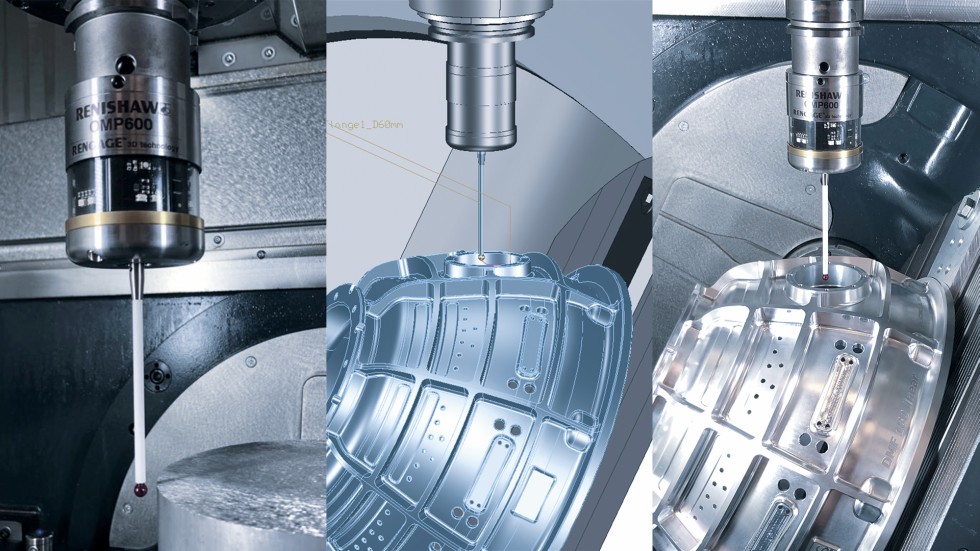
Werden Messaufgaben in den Fertigungsprozess integriert, steigt die Sicherheit und es lassen sich Korrekturen noch in der gleichen Aufspannung vornehmen.
Foto: Tebis
Zusätzliche Sicherheit bringen auch „Features“ wie beispielsweise das Messen auf der Bearbeitungsmaschine. Damit lassen sich nicht nur Korrekturen noch in der gleichen Aufspannung vornehmen. Diese Messungen auf der Maschine ermöglichen auch ein automatisches Optimieren der Prozesse. Und ganz nebenbei kann aus den gemessenen Daten automatisch die umfassende Dokumentation erstellt werden, auf die immer mehr Kunden großen Wert legen.
Fazit
Mechanische Bearbeitung ist komplex, es greifen viele Teilaspekte ineinander und müssen entsprechend berücksichtigt werden. Je früher ein Fertigungsbetrieb ein derartiges Optimierungsprojekt angeht, desto besser. Und mit kompetenter Hilfe von fachkundigen und erfahrenen Experten sowie dem nötigen Fingerspitzengefühl für die Sorgen, Ängste und Wünsche der eigenen Mitarbeiter ist bei solchen Projekten der Erfolg auf dem Weg zu höheren Erträgen in den meisten Fällen vorprogrammiert.
Wichtig bei jeder Veränderung ist, dass sie messbar ist: Die Verantwortlichen müssen festlegen, welche Messwerte wichtig und auch relevant sind. Es muss sichergestellt sein, dass diese Messwerte unabhängig sind von externen Einflüssen, auf die man keinen oder nur einen geringen Einfluss ausüben kann. Sinnvoll sind beispielsweise Indikatoren wie Fertigungszeiten nach Bauteilklasse oder das Verhältnis von Arbeitsgängen wie Rüsten, Programmieren oder Maschinenbedienung zu den produktiven Spindelstunden.
Das könnte Sie auch interessieren:
Hohe Anlageneffizienz durch intelligent geplante Rüstvorgänge
Wie funktioniert „Sandstrahlen“ mit Licht?
Wie Technologie industrielle Arbeit in der Industrie 4.0 unterstützt
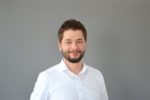
Tomek Kawala ist seit 2017 im Team von Tebis Consulting tätig. Der Maschinenbau-Ingenieur und gelernte technischer Zeichner verfügt durch seine 15-jährige Tätigkeit im Werkzeug- und Formenbau über tief greifendes Prozess- und Projektmanagementwissen. Seine Kernkompetenz besteht in der Analyse von Arbeitsprozessen und der Ermittlung von Prozess- und Produktivitätslücken. Seit 2017 engagiert er sich als Dozent an unterschiedlichen Hochschulen im Bereich Digitalisierung und Projektmanagement. Foto: Tebis