Machine Learning unterstützt Überwachung von Schleifprozessen
Der Verschleiß von Schleifscheiben hat einen maßgeblichen Einfluss auf die Qualität geschliffener Oberflächen. Bislang ist für die Überwachung des Schleifscheibenverschleißes jedoch eine zusätzliche Sensorik notwendig. Erläutert wird eine neue, alternative Möglichkeit zur Optimierung des Schleifprozesses.
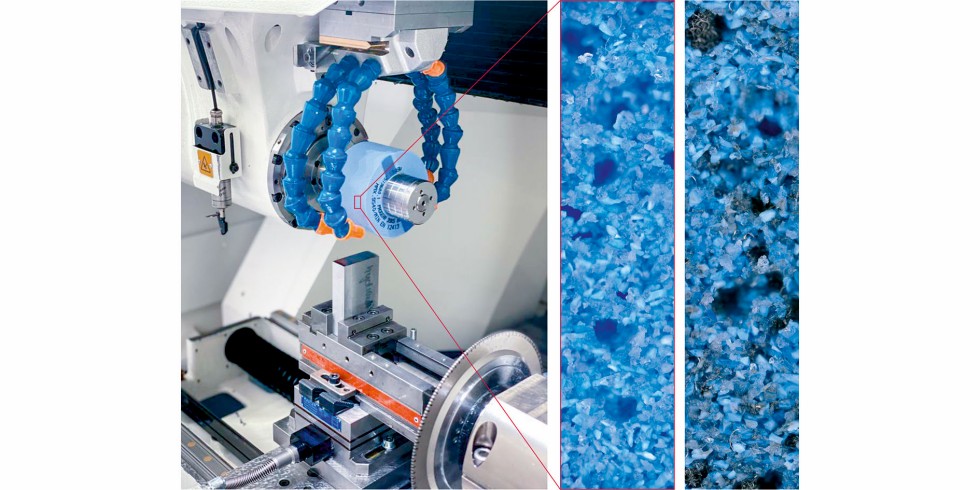
Schleifprozesse stehen in aller Regel am Ende der Prozesskette und sind ausschlaggebend für die Oberflächenqualität der Werkstücke. Um kritischen Verschleiß rechtzeitig zu erkennen und die Standzeit der Werkzeuge auszureizen, wird an Methoden zur Prozessüberwachung (inklusive Machine Learning) geforscht. Grafik: IFW
Am Institut für Fertigungstechnik und Werkzeugmaschinen (IFW) der Leibniz Universität Hannover wurde eine Überwachungsmethode auf Basis von Antriebssignalen entwickelt, die einen geringeren Aufwand bedeutet. Die Auswertung der ermittelten Signale findet mithilfe des Maschinellen Lernens (ML) statt.
Bisherige Verfahren und ihre Defizite
Schleifprozesse stehen oftmals am Ende der Prozesskette. Sie sind somit hauptverantwortlich für die Oberflächenqualität der produzierten Werkstücke. Durch zu hohen Schleifscheibenverschleiß kann es jedoch zu Prozessfehlern kommen, die sich z. B. in zu hoher Oberflächenrauheit oder Schleifbrand äußern [1]. Um kritischen Verschleiß rechtzeitig zu erkennen und gleichzeitig die Standzeit der Schleifscheibe optimal auszunutzen, wird an Methoden zur Prozessüberwachung geforscht. Dabei wird nach heutigem Stand der Technik vorrangig auf Signale von Körperschallsensoren (engl.: acoustic emission – AE) zurückgegriffen [2]. Diese führen allerdings zu einem zusätzlichen Rüstaufwand und die Qualität der Signale ist stark abhängig von Faktoren wie der Sensorplatzierung.
Hingegen ist weitgehend unbekannt, welches Potential steuerungsinterne Signale (Antriebsströme) für die Prozessüberwachung haben. Der Vorteil von Antriebssignalen ist, dass sie an jeder CNC-Maschine zur Verfügung stehen. Bislang werden Antriebssignale jedoch nicht für die Verschleißüberwachung genutzt, da sie nur einen sehr begrenzten Frequenzbereich abdecken [2] und zudem Störeinflüsse wie Reibung der Führungen oder Trägheit der Maschinenkomponenten auf die Antriebe der Maschine einwirken [3].
Um das Potential der Antriebssignale beim Flachschleifen zu untersuchen, wurde am IFW in Hannover eine Methode zur Verschleißüberwachung, basierend auf maschinellem Lernen, entwickelt. Dabei wird das Standzeitvolumen der Schleifscheibe aus den Antriebssignalen vorhergesagt. Anschließend wurde ein Vergleich mit einem Ansatz auf Basis der Kraftmessung mittels Dynamometer durchgeführt.
Wie maschinelles Lernen für die Prozessüberwachung genutzt werden kann
Für die ML-basierte Vorhersage des Standzeitvolumens sind drei Schritte erforderlich: Datenakquise, Datenvorverarbeitung und Training des ML-Modells. Alle Schritte werden sowohl für die Steuerungssignale als auch für die Kraftmessungen vorgenommen.
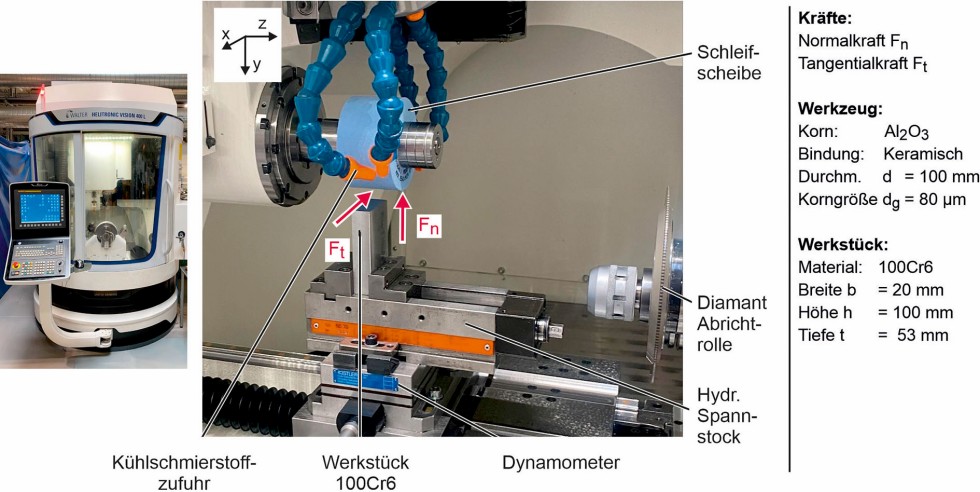
Versuchsufbau mit Walter-Schleifmaschine, hydraulischer Werkstück-Spannung, Korund-Schleifscheibe, Kühlmittelzufuhr und Dynamometer. Grafik: IFW
Für die Daten-Akquise kam am IFW eine „Helitronic Vision 400L“-Schleifmaschine der Firma Walter aus Tübingen für die Flachschleifprozesse zum Einsatz. Wie in Bild 1 dargestellt, wurde ein Werkstück aus 100Cr6 mittels hydraulischem Spannstock eingespannt. Die genutzte, keramisch gebundene Korund-Schleifscheibe hatte einen Durchmesser von 100 mm und eine Korngröße von 80 µm. Die Kräfte wurden für das Training und die Validierung der ML-Modelle während der Bearbeitung mit einem „29527B“-Dynamometer von Kistler, Winterthur/CJ, gemessen. Zudem wurden die steuerungsinternen Signale der Fanuc-Steuerung über die „Servo Guide“-Anwendung des Steuerungsherstellers mit einer Frequenz von f = 1.000 Hz aufgezeichnet. Die aufgezeichneten Signale sind in Tabelle 1 aufgelistet.
Insgesamt wurden Prozesssignale von 310 Flachschleifprozessen aufgezeichnet, wobei sechsmal abgerichtet wurde. Das Erreichen der Verschleißgrenze, ab der neu abgerichtet werden muss, wurde als der Zeitpunkt definiert, an dem erstmalig Schleifbrand durch Verschleiß auftritt. Dabei war insbesondere das Zusetzen der Schleifscheibe und Kornabstumpfung ausschlaggebend für das Standzeitvolumen. Für die einzelnen Prozesse wurde das Werkstück jeweils über die gesamte Breite (20 mm) mit einer Schnitttiefe von ae = 0.5 mm geschliffen. Die Vorschubgeschwindigkeit beträgt dabei vf = 300 mm/min und die Schnittgeschwindigkeit vc = 20 m/s.
Vorgehensweise zur Ermittlung eines Merkmalsvektors
Die aufgezeichneten Signale wurden für jeden einzelnen Prozess auf die gleiche Weise vorverarbeitet und jeweils dem entsprechenden Standzeitvolumen zugeordnet. Das Ziel der Vorverarbeitung ist es, aus den Zeitreihen einen Merkmalsvektor zu berechnen, der wiederum als Eingangsvektor für das ML-Modell genutzt werden kann. Dazu wurden insgesamt vier Schritte durchgeführt.
Schritt 1 – Bereinigung der Signale
Hierfür wurde der Signaldrift aus den aufgezeichneten Kräften entfernt und ein „Butterworth“-Tiefpassfilter mit einer Grenzfrequenz von fg = 2 kHz angewandt, um einen Einfluss der Eigenfrequenzen der Kraftmessplattform auszuschließen. Bei den Steuerungssignalen wurden die Prozessnebenzeiten aus den Signalen entfernt und somit gleichzeitig die Prozesse vereinzelt (Bild 2a).
Schritt 2 – Segmentierung
Die Zeitreihen wurden in drei Segmente unterteilt: Ein Start-Segment vom ersten Kontakt zwischen Schleifscheibe und Werkstück bis zum Erreichen des vollen Eingriffs, ein Mittel-Segment, bei dem die Eingriffsbedingungen konstant bleiben und ein End-Segment, bei dem das Zerspanvolumen bis zum Materialaustritt kontinuierlich abnimmt. Für die Segmentierung wurde die Ableitung des bereinigten Spindelmoments berechnet, da Änderungen des Spindelmoments ein geeigneter Indikator für den Segmentübergang sind. Auf den berechneten Verlauf wurde ein Grenzwert angewandt, der sich aus dem Grundrauschen des Signals ergibt. Für jedes Durchlaufen der Grenzen wurde ein Index gespeichert, der Anfang bzw. Ende eines Segments markiert, Bild 2b und 2c. Analog dazu wurden die Kraftverläufe segmentiert. Anstelle des bereinigten Spindelmoments wurde die Kraft in Y-Richtung verwendet.
Schritt 3 – Merkmalsberechnung
Für jedes Segment wurden verschiedene, statistische Merkmale berechnet. Dies waren unter anderem der Mittelwert, die Standardabweichung oder die Schiefe. Die Merkmale wurden anschließend über alle drei Segmente zu einem Merkmalsvektor zusammengefasst, der einen einzelnen Prozess repräsentiert.
Schritt 4 – Merkmalssortierung
Die Merkmale wurden hinsichtlich ihrer Relevanz für das Standzeitvolumen sortiert. Dazu wurde, basierend auf dem F-Test, ein univariates Merkmalsranking durchgeführt, das jedem Merkmal einen Score zuordnet. Dabei bedeutet ein höherer Score einen höheren Informationsgehalt des entsprechenden Merkmals. Die Ergebnisse des Merkmalrankings sind in Bild 3 zu sehen.
Mit den vor-verarbeiteten Signalen konnte ein ML-Modell „trainiert“ und ein geeignetes Modell ausgewählt werden. Dazu wurden im Rahmen der Arbeit am IFW verschiedene Modelle optimiert und miteinander verglichen. Berücksichtigt wurden „Gaussian-Process Regression“, „Support Vector Machines“ und „Ensemble“-Methoden mit unterschiedlichen Hyperparametern. Im Rahmen der Hyperparameter-Optimierung kamen unter anderem unterschiedliche Kernel-Funktionen zum Einsatz. Zudem wurde die Dimension der Eingangsgrößen unter Berücksichtigung des Merkmal-Scores variiert.
Für die Hyperparameter-Optimierung wurde ein separater Datensatz (Validierungs-Datensatz) genutzt. Bei der abschließenden Auswertung kam hingegen ein weiterer Datensatz zum Einsatz (ein Test-Datensatz), der bei den vorherigen Schritten unangetastet bleibt.
Ergebnisse: Eignung der Verfahren und Chancen zur Steigerung der Genauigkeit
In Bild 4 sind die Ergebnisse des ML-Modells auf Basis der Antriebssignale und des ML-Modells auf Basis der Kräfte einander gegenübergestellt. Die Modellauswahl beruht jeweils auf der Optimierung der Hyperparameter hinsichtlich des Standzeitvolumens, unter Berücksichtigung der Variation der Eingangsgröße und der Art des Modells. Der Vorhersagefehler ergibt sich aus der Wurzel der mittleren quadratischen Abweichung (RMSE) zwischen tatsächlichem und vorhergesagtem Standzeitvolumen. Zusätzlich wird das Bestimmtheitsmaß R² für die Auswertung herangezogen.
Unabhängig davon, ob Kräfte oder Steuerungssignale als Eingang verwendet wurden, wird mit einem Gaussian Process Regression-Modell der geringste Fehler erzielt. Kernel-Funktion und Größe des Eingangsvektors unterscheiden sich jedoch in beiden Fällen. Für die Antriebssignale erreicht ein Modell mit Matern 5/2 Kernel und 50 Merkmalen den geringsten Fehler von RMSE = 104,9 mm³ (bezogen auf 1,0 mm Schleifscheibenbreite) und R² = 0.98. Übertragen auf die Standzeit, ergibt sich bei einer Vorschubgeschwindigkeit von vc = 300 mm/min und einer Schnitttiefe von ae = 0,5 mm eine Abweichung von circa 42 s, verglichen mit der tatsächlichen Standzeit, die bei den durchgeführten Versuchen im Mittel 30 Minuten entsprach.
Für die Kraftmessungen erzielt eine rational-quadratische Kernel-Funktion den geringsten Fehler (RMSE = 61,3 mm³, R² = 0.99). Dabei werden alle 135 Merkmale als Eingang verwendet. Mit den geänderten Eingangsgrößen erhöht sich die Genauigkeit und die Abweichung lässt sich für die genannten Prozessparameter auf 25 s senken. Die Ergebnisse zeigen daher, dass Antriebssignale für die Vorhersage des Schleifscheibenzustands, speziell des Standzeitvolumens, geeignet sind. Unter Berücksichtigung des Merkmal-Rankings wird deutlich, dass insbesondere der Strom des Antriebs in Normalrichtung (orthogonal zum Vorschub) (Iq1) eine hohe Signifikanz bezüglich der Vorhersage des Standzeitvolumens hat.
Fazit: Nutzung von Antriebssignalen bietet gute Option
Mithilfe der vorgeschlagenen Methode kann erfolgreich das Standzeitvolumen einer Schleifscheibe, basierend auf den Antriebssignalen und ohne zusätzliche Sensorik, abgeschätzt werden. Es wird ein R²-Wert von 0,98 erreicht. Dadurch lässt sich das Standzeitvolumen mit einer Abweichung von 104,9 mm³ pro mm Schleifscheibenbreite vorhersagen. Dies entspricht einer Abweichung von 42 s bei einer mittleren Gesamtstandzeit von 30 Minuten.
Es wurde ein Vorgehen entwickelt, um Prozesssignale von Flachschleifprozessen zu segmentieren und darauf aufbauend einen Merkmalsvektor zu berechnen. Der resultierende Vektor dient anschließend als Eingang für ein ML-Modell. Die Ergebnisse zeigen, dass Modelle, die auf der Gaussian Process Regression basieren, für diesen Anwendungsfall die geringsten Fehler erzielen. Neben diesem ML-Modell wurde ein weiteres ML-Modell trainiert, wobei der Eingangsvektor aus Messungen einer Kraftmessplattform berechnet wird. Der Vergleich der beiden ML-Modelle zeigt, dass mithilfe die Kraftmessung die Genauigkeit der Vorhersage des Standzeitvolumens geringfügig steigt. So kann mit der Kraftmessung ein R²-Wert von 0,99 anstatt von 0,98 erreicht werden.
Um Schleifbrand aufgrund kritischen Verschleißes sicher zu vermeiden, muss bei einer Überwachung mit Antriebssignalen die Schleifscheibe im Mittel 17 Sekunden früher gewechselt werden, als bei einer Überwachung mit gemessenen Kräften. Verglichen mit der mittleren Gesamtstandzeit von etwa 30 Minuten, ist die Verbesserung durch die Kraftmessung in der Praxis daher unwesentlich. Insgesamt zeigen die Ergebnisse ein hohes Potential von Antriebssignalen als Eingangsgröße für die Überwachung von Schleifscheibenverschleiß.
Förderhinweis: Die Arbeiten wurden gefördert durch die Deutsche Forschungsgemeinschaft (DFG) – 421461390.
Literatur
- Puerto, P.; Fernández, R.; Madariaga, J.;, Arana, J.: & Gallego, I.: Evolution of surface roughness in grinding and its relationship with the dressing parameters and the radial wear. Procedia Engineering 63 (2013), 174–182.
- Pandiyan, V.; Shevchik, S.; Wasmer, K.; Castagne, S.; & Tjahjowidodo, T.: Modelling and monitoring of abrasive finishing processes using artificial intelligence techniques: A review. Journal of Manufacturing Processes 57 (2020), S. 114–135.
- Grimmert, A.; & Wiederkehr, P.: Indirect Force Measurement Using Spindle Currents for Grinding Processes in Aerospace Industry. In Proceedings of the Machining Innovations Conference for Aerospace Industry (MIC), Dezember 2021.
Das könnte Sie auch interessieren:
Forschung und Industrie fokussieren gemeinsam die nachhaltige Produktion
Assistenzsystem bringt Mensch und Maschine in der Fertigung zusammen
Sensorische Schwenkspannelemente: Garant für sicheres Spannen
Einstellbar-gedämpfte Bohrstange schont Werkstück und Werkzeug
Prof. Dr.-Ing. Berend Denkena leitet seit 2001 das Institut für Fertigungstechnik und Werkzeugmaschinen (IFW) am Produktionstechnischen Zentrum der Leibniz Universität Hannover.
Dr.-Ing. Heinrich Klemme ist seit 2021 Leiter des Bereichs Maschinen und Steuerungen am IFW.
Dennis Stoppel, M. Sc., ist seit 2019 wissenschaftlicher Mitarbeiter am IFW im Bereich Maschinen und Steuerungen.